
Marangoni Flow and Microstructure of Electrode Patterns in Sintering Process of Copper(I) Oxide Nanoparticles
Copyright © The Korean Society for Precision Engineering
This is an Open-Access article distributed under the terms of the Creative Commons Attribution Non-Commercial License (http://creativecommons.org/licenses/by-nc/3.0) which permits unrestricted non-commercial use, distribution, and reproduction in any medium, provided the original work is properly cited.
Abstract
Nanoparticle laser sintering is one of the vital technologies in additive manufacturing. Numerous processes such as freeform surfaces or seamless parts have been proposed for the fabrication of complex components, however, the resolution and quality of the processes do not meet the standard necessary for practical applications. Therefore, selective laser sintering is used to fabricate electrode patterns in high-precision manufacturing field. Despite the various advantages, laser sintering process generates defects on the pattern with one of the major contributing factors being the Marangoni flow. In this study, the laser sintering process was used to determine the relationship between the nanoparticle blending conditions and the microstructure of the fabricated electrode pattern through the control of the nanoparticles density and laser characteristics such as power, pulse duration, and scan speed. As a result, the conditions for Marangoni flow were analyzed in relation to the concentration of the nanoparticle solution and laser irradiation parameters. More severe Marangoni flow was produced with the solution having a low weight percent of nanoparticles, while the width of the pattern was uniform when the pulsed laser was applied using a high peak power to achieve the same total amount of energy.
Keywords:
Marangoni flow, Nanoparticle synthesis, Laser sintering, Electrode pattern키워드:
마랑고니 유동, 나노입자 합성, 레이저 소결, 전극 패턴1. Introduction
The demand for additive manufacturing is increasing along with interest in the field of 3D Printing technology. Laser-based sintering is a major fabrication method for complex three-dimensional parts and can make patterns with a width thinner than a human hair, without the need for masks. Laser-based processes, however, have some drawbacks, and a representative side effect is an indented shape owing to Marangoni flow—a phenomenon usually observed and studied in the field of inkjet printing technology, but which also occurs in laser processing technology. Marangoni flow can be calculated by droplet evaporation; Ristenpart et al. measured the relative thermal conductivities of the substrate and liquid to verify the effect on the direction of circulation in liquid evaporation.1 Marangoni flow can be controlled by the selection of the liquid, enabling the production of precise patterns. The relationship between local heating and flow of sessile water was verified by Askounis et al.2 who compared the resultant thermal patterns in terms of heating location, time, and heating power. Local heating produces four stages of thermal flow in the droplet; the flow finally converged to non-directional flow regardless of the conditions, which means that the fabricated pattern is affected more by materials than by the process. The Marangoni flow direction has been investigated in inkjet processes by Li et al., according to solvent and process parameters.3 Their research revealed that drop spacing and Z number of ink for inkjet printing determines the morphology of the dried pattern. Moreover, ethylene glycol was found to countervail the outward Marangoni flow. Hu et al. applied recirculating Marangoni flow to prevent the “Coffee Ring” effect, wherein particles are drawn from the inside to outside according to the drying time in solution.4 A uniform pattern was fabricated using a solvent with a high boiling point, which reinforces recirculation of Marangoni flow without binder material. Thokchom et al. researched how Marangoni flow in influenced by particle concentration, which affects the contact angle of the droplet.5 Specifically, when the solution has high particle concentration, the surface tension of the solution decreases because the low surface energy of the liquid–solid interface. They also investigated the effect of the substrate temperature, which determines the diameter of the evaporated droplet. Elashnikov et al.applied Marangoni flow in laser machining to make valleys that connected to each other, making a specific pattern on the substrate.6 On the other hand, Chung et al. found that in laser sintering, Marangoni flow occurs when the laser scan speed is faster than the evaporation of the solvent and the sintering of the nanoparticles, and that it has an adverse effect on the sintered pattern.7 Therefore, the effect should be controlled properly to prevent indents forming in the pattern of sintered nanoparticles, which obstruct the deposition of a dense pattern.
In the aforementioned studies, Marangoni flow was studied in various ways according to material and process, and it was found that Marangoni flow predominantly depends on the material properties and heating conditions. In spite of broad research on Marangoni flow, material dependency has not yet been revealed in laser sintering. Hence, this study focuses on nanoparticle laser sintering to analyze Marangoni flow with regard to nanoparticle concentration and heating conditions.
Laser nanoparticle sintering has been studied since 2004 using gold nanoparticles. Since then, silver, copper, and nickel nanoparticles have been applied to make electrode patterns with high electrical conductivity and stable structural properties. The process has evolved enough to fabricate high-quality patterns, but the nanoparticles show limits such as corrosion in storage and surface oxidation after sintering. Recently, copper and nickel oxides have been applied to satisfy the shortcomings in previous research. However, this still does not solve the side effects of fluidic motions such as Marangoni flow—which causes irregular pattern cross section and causes not only high electrical resistivity but also easy deterioration. For these reasons, Marangoni flow is analyzed herein with regard to its effect on the microstructure of the pattern according to the laser source and blending conditions of the metal oxide nanoparticle solution. Subsequently, the optimal conditions for producing highly conductive electrical patterns on a substrate are discussed.
2. Experimental Methods
Nanoparticles were synthesized by a hydrothermal process. Deionized (DI) water was heated to its boiling temperature, and dissolved copper ions were reacted with reduction agents. During this process, the copper ions reduce to Copper(II) oxide and then to Copper(I) oxide. The Copper(I) oxide nanoparticles were washed several times until clean and then diluted with an alcohol solvent and a surfactant. Samples were prepared by coating the solution onto a glass substrate using a spin coater, followed by laser sintering, which varied according to the laser source and concentration of the compound in solution, as shown in Fig. 1 The laser sources used were infrared (IR) Continuous Wave (CW) and pulsed lasers. The pulsed laser can be tuned in terms of pulse width, power, and repetition rate. After the laser sintering process, the fabricated copper electrode patterns were observed by Scanning Electron Microscopy (SEM). The SEM images show nanoparticles with different densities, shapes, and degrees of sintering. Oxidation and deterioration was not considered which was analyzed in previous study8 and the process was verified that organic layer protects the electrode pattern with reliable performance.
3. Results and Discussion
3.1 Photon Energy Dependency in Laser Sintering
The sintering process was carried out by irradiating with photon energy at various pulse durations and intensities. CW and pulsed laser irradiation were compared to verify the relationship between nanoparticle sintering and the irradiation intensity of the laser according to time as shown in Fig. 2 The CW-laser-irradiated pattern shows a relatively narrow pattern width, but with unsintered or recast residual nanoparticles dispersed both in and around the pattern as shown in Fig. 2(a) The Gaussian beam had a 30 μm spot size; nanoparticles outside the beam spot were sintered by heat conducted from the photon energy in the beam spot, and nanoparticles inside the beam spot were sintered by either the photon energy directly, or by heat conducted from the photon energy. Each of nanoparticle, PVP, and solvent absorb energies and the total absorbed energy is
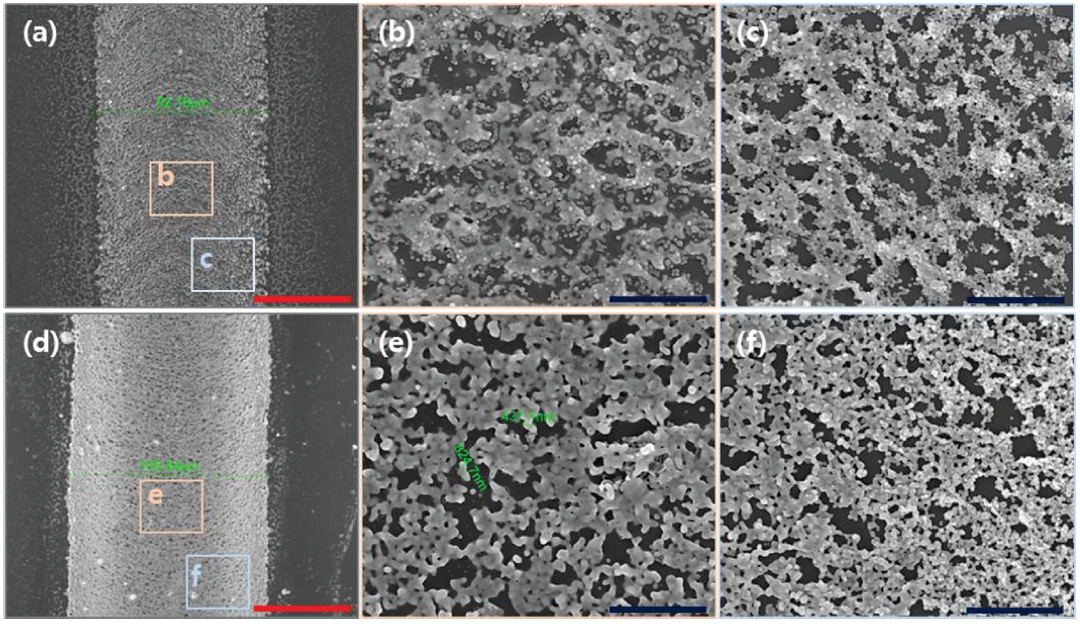
SEM images of the laser sintered copper(I) oxide nanoparticle. Copper electrode patterns made by (a) CW, (d) pulsed lasers, and detailed views in (b) and (e) the centers and (c) and (f) the boundaries as indicated (Scale bars : 50 μm, : 4 μm.)
(1) |
where M is mass, Cp is specific heat capacity, Lm is latent heat of melting, Lreaction is latent heat of chemical reaction, and Lv is latent heat of vaporization. The total energy changes to conduction energy, surface tension, and latent heat
(2) |
where κ is thermal conductivity, γ is surface tension, and A is surface tension affected area. Which means that temperature gradient and surface tension affect to the Marangoni flow of the pattern.
As shown in Figs. 2(b) and 2(c), the nanoparticles in the pattern center are sintered to a greater degree than those at the pattern edge, because the center interacts with the photon energy directly. The pattern center, however, also shows some unsintered nanoparticles, because the laser is not powerful enough to fully sinter all of them. The weak laser power is caused by both the low intensity of the CW laser and the fact that the Marangoni flow sweeps some of the nanoparticle solution away, which reduces the total amount of photon energy absorbed by the nanoparticles.
The pulsed laser-irradiated pattern also displayed differences between the center and the edge of the pattern. However, it is more densely sintered, and there are fewer residuals surrounding the pattern than with the CW laser. The CW and pulsed lasers have the same total intensity, but the CW laser continuously irradiates photon energy on the coated nanoparticle solution over time. In contrast, the pulsed laser periodically irradiates photon energy with a higher intensity and rest time between the pulses. As shown in Figs. 2(e) and (f), these intense pulses of laser power sinter all the nanoparticles, unlike the CW laser with a weaker peak power. Furthermore, the degree of sintering according to spatial distribution is the same as that of the CW laser. Hence, both the patterns (in Figs. 2(a) and 2(d)) show Marangoni flow from the center to the edge of the pattern. Marangoni flow was caused by the drastic temperature change in and around the laser beam spot, which generates a temperature gradient and pressure difference. The pressure difference creates outward flow and indents the center of the pattern, which produces concentrated nanoparticles at the edge, whereas the nanoparticles in the center are connected sparsely. The resultant pattern shape makes an inefficient electron conductor as an electrode pattern, and it does not reliably avoid contamination and oxidation.
Therefore, the nanoparticle solution was diluted to lower the Marangoni flow, and the surfactant Polyvinylpyrrolidone (PVP) was added to suppress the movement of nanoparticles from the center to the edge of the pattern by trapping effect.9
3.2 Marangoni Flow Control in Laser Sintering
To clarify the effect of nanoparticle concentration, both low- and high-weight-percent Copper(I) oxide nanoparticle solutions were prepared and irradiated with the pulsed IR laser, as shown in Fig. 3 In the case of the low-weight-percent Copper(I) oxide solution, the fabricated copper pattern has a low density, which increases from the center to the edge due to the effect of Marangoni flow. On the other hand, the high-weight-percent Copper(I) oxide nanoparticle solution gives a uniform thickness cross section, unlike the indented pattern made with the low-weight-percent solution, because the Marangoni flow was restrained by the high-weight-percent of nanoparticles and surfactant. However, it also gives an uneven pattern width, because the relatively high concentration means that the irradiated light energy cannot penetrate the pattern deeply enough to attach the nanoparticles to the substrate uniformly, and the laser power and nanoparticle coating thickness are not stable. The low-weight-percent Copper(I) oxide nanoparticle solution was tested to accentuate the Marangoni flow, to analyze its effect in detail according to laser irradiation parameters as shown in Fig. 4 The Marangoni flow increases, and the pattern widens when the laser scan speed or the laser power is higher. These are common basic phenomena of Marangoni flow in laser machining, caused by pressure differences between the laser irradiation area and the surroundings. In addition, the pattern density is lower when the laser scan speed is lower, which means that a higher energy concentration produces a lower density pattern.
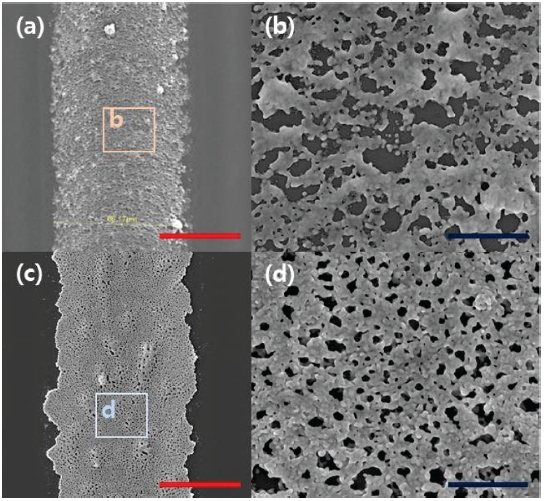
Comparison of fabricated pattern sintered by pulsed laser using nanoparticle solution with (a) low- and (c) high-weight-percent of copper(I) oxide nanoparticles, (b) and (d) detailed views as indicated (scale bar : 50 μm, : 4 μm)
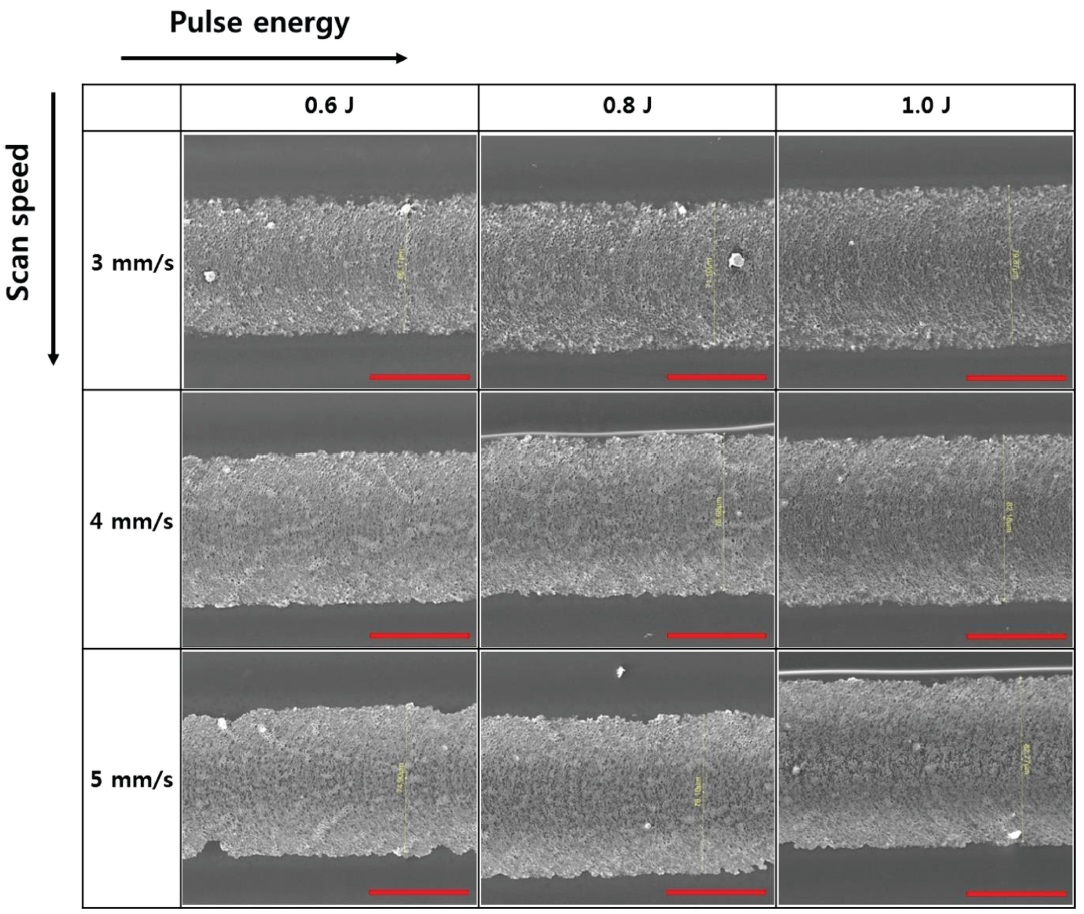
Pulsed laser irradiation of low-weight-percent copper(I) oxide nanoparticle solution according to laser pulse energy and scan speed (scale bar : 50 μm)
In conclusion, a high concentration of energy induces Marangoni flow in the nanoparticle solution as the solvent evaporates, whereas a low concentration of energy induces Marangoni flow in the nanoparticles during sintering. The laser power is therefore a major factor in determining the degree of Marangoni flow.
3.3. Relation between Peak Power and Pattern Shape in Laser Sintering
Laser sintering of low-weight-percent Copper(I) oxide nanoparticle solutions can verify the effect of Marangoni flow, but the pattern shape is not suitable for use as an electrode pattern because of its indented shape along the cross section. The high-weight-percent Copper(I) oxide nanoparticle solution was sintered according to the laser peak power as
(3) |
where the pulse energy was fixed, and pulse duration was changed from 8 ns to 200 ns, as shown in Fig. 5 Marangoni flow was restrained, and the patterns had a porous microstructure of similar size, produced by chemical residuals such as carbon dioxide gas and water vapor from the reaction between the photon energy and nanoparticle solution. The sintered pattern shows irregular width when the pulse duration is relatively short, and the laser irradiated substrate has crack damage when the pulse duration is too long. On the other hand, the fabricated pattern shows uniform pattern width and no evidence of Marangoni flow with a pulse duration of 30 ns to 100 ns. A short pulse duration means that the laser predominantly sinters nanoparticles within the spot size, with a long interval between pulses that reduces the average effect of laser irradiation spots; however, the intense pulses make a narrow pattern and suppress heat conduction in the direction normal to the laser patterning. On the other hand, a long pulse duration can cause excessive heat conduction to the substrate, without enough time to allow it to cool; it also causes unstable attachment of nanoparticles on the substrate, with thermal crack generation.
4. Conclusions
In this study, laser sintered copper electrode patterns were analyzed in terms of Marangoni flow and microstructure, according to nanoparticle density and laser irradiation. The surface tension gradient and temperature gradient are major factors in determining Marangoni flow—the flow dominates when the concentration of nanoparticles is low, and the laser power is relatively high. The surface tension of the low-weight-percent nanoparticle solution can change drastically according to temperature, and the high-power irradiation causes rapid temperature change. When the laser power is too low, the process leaves residual unsintered or weakly sintered nanoparticles in the pattern.
Marangoni flow is generated by both weak and strong laser irradiation when the nanoparticle density in solution is low. It is experienced by the nanoparticle solution as the solvent evaporates when the laser power is weak and by the nanoparticle during sintering when the laser power is strong. Hence, the nanoparticle solution should have a high concentration of nanoparticles to prevent Marangoni flow.
Laser power density is another major factor that determines the quality of the process. A short pulse duration causes non-uniform pattern width, but narrower patterns can be made than with a longer pulse duration. A long pulse duration enables high heat conduction, not only to the nanoparticle solution but also to the substrate. This helps to make wide, even patterns, but it also causes thermal damage to the substrate. Further research is needed to clarify the interaction between high-density nanoparticle solutions and ultra-short-pulse lasers.
Acknowledgments
This work was supported by research fund of Chungnam National University.
REFERENCES
-
Ristenpart, W. D., Kim, P. G., Domingues, C., Wan, J., and Stone, H. A., “Influence of Substrate Conductivity on Circulation Reversal in Evaporating Drops,” Journal of the Physical Review Letters, Vol. 99, Article No. 234502, 2007.
[https://doi.org/10.1103/PhysRevLett.99.234502]
-
Askounis, A., Kita, Y., Kohno, M., Takata, Y., Koutsos, V., et al., “Influence of Local Heating on Marangoni Flows and Evaporation Kinetics of Pure Water Drops,” Journal of the Langmuir, Vol. 33, No. 23, pp. 5666-5674, 2017.
[https://doi.org/10.1021/acs.langmuir.7b00957]
-
Li, Y., Lan, L., Sun, S., Lin, Z., Gao, P., et al., “All Inkjet-Printed Metal-Oxide Thin-Film Transistor Array with Good Stability and Uniformity Using Surface-Energy Patterns,” Journal of the Applied Materials and Interfaces, Vol. 9, No. 9, pp. 8194-8200, 2017.
[https://doi.org/10.1021/acsami.7b00435]
-
Hu, G., Albrow-Owen, T., Jin, X., Ali, A., Hu, Y., et al., “Black Phosphorus Ink Formulation for Inkjet Printing of Optoelectronics and Photonics,” Nature Communications, Vol. 8, Article No. 278, 2017.
[https://doi.org/10.1038/s41467-017-00358-1]
-
Thokchom, A. K., Zhou, Q., Kim, D.-J., Ha, D., and Kim, T., “Characterizing Self-Assembly and Deposition Behavior of Nanoparticles in Inkjet-Printed Evaporating Droplets,” Sensors and Actuators B: Chemical, Vol. 252, pp. 1063-1070, 2017.
[https://doi.org/10.1016/j.snb.2017.06.045]
-
Elashnikov, R., Fitl, P., Svorcik, V., and Lyutakov, O., “Patterning of Ultrathin Polymethylmethacrylate Films by In-Situ Photodirecting of the Marangoni Flow,” Journal of the Applied Surface Science, Vol. 394, pp. 562-568, 2017.
[https://doi.org/10.1016/j.apsusc.2016.10.074]
-
Chung, J., Bieri, N. R., Ko, S., Grigoropoulos, C. P., and Poulikakos, D., “In-Tandem Deposition and Sintering of Printed Gold Nanoparticle Inks Induced by Continuous Gaussian Laser Irradiation,” Journal of the Applied Physics A, Vol. 79, Nos. 4-6, pp. 1259-1261, 2004.
[https://doi.org/10.1007/s00339-004-2731-x]
-
Lee, H. S. and Yang, M. Y., “Copper Interconnects Based on Copper(I) Oxide Particle-Based Precursor Ink Technology-Material Composition Optimization and Reliability,” Journal of the IEEE Transactions on Device and Materials Reliability, Vol. 16, No. 4, pp. 604-609, 2016.
[https://doi.org/10.1109/TDMR.2016.2612940]
-
Semples, W., De Dier, R., Mizuno, H., Hofkens, J., and Vermant, J., “Auto-Production of Biosurfactants Reverses the Coffee Ring Effect in a Bacterial System,” Journal of the Nature Communications, Vol. 4, Article No. 1757, 2013.
[https://doi.org/10.1038/ncomms2746]
Professor in the Department of Mechanical and Materials Engineering Education, Chungnam National University. His research interest is material properties based machining and sensing.
E-mail: liber@cnu.ac.kr
Assistant Professor in the Department of Materials Science and Engineering, Chungnam National University. His research interest is alloy design and mechanical properties.
E-mail: jayhan@cnu.ac.kr