
인입 거리에 따른 가변형 월 블로워의 성능 평가
Copyright © The Korean Society for Precision Engineering
This is an Open-Access article distributed under the terms of the Creative Commons Attribution Non-Commercial License (http://creativecommons.org/licenses/by-nc/3.0) which permits unrestricted non-commercial use, distribution, and reproduction in any medium, provided the original work is properly cited.
Abstract
The soot blowing performance for a wall blower, according to the entering distance of a nozzle from the boiler wall, is evaluated according to a liquid droplet impingement erosion model. This erosion model incorporated the computational fluid dynamics of a jet steam of nozzle, and it uses the pressure and velocity of a jet steam at the furnace wall for several entering distances of the nozzle. A relative erosion rate dependent on the velocity of the jet steam is also introduced. Several cases are compared, as determined according to the entering distance and the number of nozzles. The shaded erosion region, according to the entering distance of the nozzle and the co-injected region, have also been schematized. Specifically, when the entering distance of the nozzle is large, the maximum relative erosion rate is small. However, the soot blowing area is uniformly large, as compared with the case of a small entering distance. This shows that the maximum relative erosion rate is high, but the soot blowing region is small and the shaded regions occur.
Keywords:
Adjustable wall blower, Erosion model, Computational flud dynamics, Furnace wall, Nozzle jet키워드:
월 블로워, 침식 모델, 전산유체역학, 보일러 노벽, 노즐 분사1. 서론
화력발전소에서 사용하는 석탄 연료는 연소 시 회분(Fly Ash)을 배출하여 보일러 노(Furnace) 내부의 벽에 달라붙어 열교환 특성을 악화시켜 보일러의 연소효율과 연료효율에 막대한 영향을 끼치게 된다. 기존 연구에1,2 따르면 이러한 점착이 심하게 발생되는 경우 보일러 출력의 10-20%, 열효율의 10%까지 영향을 미치는 것으로 알려져있다.
일반적으로 이러한 보일러 내부 벽면에 점착된 회분을 운전 중에 제거하기 위하여 월 블로워(Wall Blower)가 사용된다. 월 블로워는 보일러 노 내부에 상시 설치 되어 분사되는 유형과 외벽에 설치되어 내부로 인입하여 부착물을 제거하는 제매(Soot Blowing) 과정을 거친 후 다시 후퇴하는 유형으로 존재한다. 상시 설치되는 형태의 월 블로워는 내부와 같이 연소 산화물의 영향을 받게 되기 때문에 인입 방식의 월 블로워가 주로 사용되고 있다. 그런데 기존 국내 발전소에서 사용하고 있는 이러한 인입식 월 블로워는 내부 인입 거리가 고정됨에 따라 제매 면적이 고정적으로 유지된다.3 인입거리가 고정되어 제매가 진행되는 경우 노면의 특정 영역에만 제매가 지속되어 노벽이 손상될 수 있으며, 제매의 음영 구역이 발생되는 문제점이 있다. 제매로 인한 노벽의 손상문제는 발전소의 보일러 수명과 직접적인 관련이 있어서 보수적인 제매 관리를 선호하고 있는 실정이다. 이러한 문제를 해결하기 위해서는 가변적으로 인입거리를 조절하는 장치개발이 중요하다.
본 연구에서는 가변적으로 인입거리를 조절하기 위한 월 블로워 장치를 개발하기 위해 그리고 월 블로워의 인입거리에 따라 발생할 수 있는 음영구역을 제거하고 보일러 노벽의 전체적으로 균일한 제매 면적을 확보하기 위한 인입거리를 구하고자 한다. 월블로워의 제매 성능에 대한 연구는 발전소 가동의 특성 상 실증적 방법으로 수행하기 어렵기 때문에 월 블로워의 스팀 분사에 대한 유체 전산모사해석을 통하여 보일러 노벽으로 분사되는 유체의 압력 및 속도를 도출하였다. 도출된 해석 결과를 분사 스팀 속도를 기반으로 한 상대 침식률 모델에 적용하여 월 블로워의 격자형 배치로 인한 공동 분사 영역에서의 제매 성능을 침식률로 도식화하였다.
2. 월 블로워의 유한요소해석
2.1 월 블로워의 노즐의 모델링
유체 전산모사해석을 위해서 Fig. 1(a)의 연구 대상 월 가변형 월 블로워 시제품을 기반으로 Fig. 1(c)와 같이 유동과 관련이 있는 영역인 노즐부 및 분사 영역에 대한 격자 모델링을 수행하였다. 기본 설계 형상에 대한 모델링을 바탕으로 인입 거리의 변화에 따른 모델을 추가로 제작하였다.
유체 전산모사해석을 위해서는 월 블로워 노즐에서 분사되는 증기가 작용할 검사 체적(Control Volume)의 지정이 필요하므로 그림에 해당하는 분사 영역을 모델링 하였다. 검사 체적의 크기는 추후 검증을 위한 실증 실험의 영역을 포함할 수 있도록 4 m × 4m × 1m로 모델링하였다. 또한 검사 체적을 유한요소로 모델링 하기 위하여 사용한 격자는 요소 36,846,217개, 절점 6,411,620개로 이루어져있다. 특히 증기가 분사되어 존재할 것으로 예측되는 부분인 벽면으로부터 1 m까지의 격자를 더 조밀하게 작성하였으며, 요소의 크기도 20 mm 이하로 유지하여 전산모사해석의 수렴성을 확보할 수 있도록 하였다.
월 블로워 관을 통해 공급되어 분사되는 작동 유체는 감압된 상태로 공급이 되어 10 bar의 압력과 300oC의 온도를 갖고 노즐로 공급되도록 하였다. 해당 조건에서의 과열 증기의 열/유체 물성치는 아래 Table 1과 같다.
월 블로워 노즐의 해석을 위해 실제로 노즐이 작용하는 환경을 모사하여 해석 조건 및 경계 조건을 선정하였다. 노즐의 분사구가 향하는 Y 방향을 분사 방향으로 설정하고 -Y 방향을 중력 방향으로 하였다. 노즐로 공급되는 유체의 압력은 포핏 밸브의 영향으로 인입 거리에 따라 변동이 되기 때문에 이에 대한 해석을 추가로 진행하여 반영하였다. 또한 분사 유체의 물성은 300도의 과열 증기 물성을 모두 이용하여 Table 1과 같은 증기의 특성을 전산모사해석에 적용하였다.
보일러 내부와 분사 증기의 성질이 매우 달라 다상(Multiphase)의 유체 용량(Volume of Fluid) 모델을 사용하였다. 유체 상의 종류는 두 개로 설정하고, 부피율 컷오프(Volume Fraction Cutoff)를 0.25로 결정하였다. 또한 난류 모델은 Realizable k-ε, 표준 벽함수(Standard Wall Function)을 이용하였다.
2.2 인입 거리에 따른 공급 압력 변화 해석
본 연구에서 입력 조건으로 사용되는 노즐로 공급되는 유체의 압력은 Fig. 2(a)에서 보여지는 포핏 밸브의 열림량에 따라 변화하게 된다. 포핏 밸브의 열림량은 인입 거리에 영향을 받게 되므로 인입 거리에 따른 공급압의 변화를 고려한 해석을 위해 사전 해석을 수행하였다. Fig. 2(b)와 같이 모델링한 포핏 밸브 내부 영역을 유체 영역으로 지정하고 노즐의 인입 거리에 따라 포핏 코어 및 로드의 위치를 변경하여 밸브 열림량을 변화시키며 해석하였다. Fig. 2(c)에서는 압력분포 결과를 보여주고 있다. 그 결과, 인입 거리 별 밸브의 출구압/입력압의 비는 Fig. 3과 같이 나타난다. 인입 거리가 45 mm에서 75 mm까지 변화될 때 나타나는 최대 압력 저하는 약 6% 정도이며 이를 분사 스팀 해석의 노즐 공급압 경계 조건으로 적용하였다.
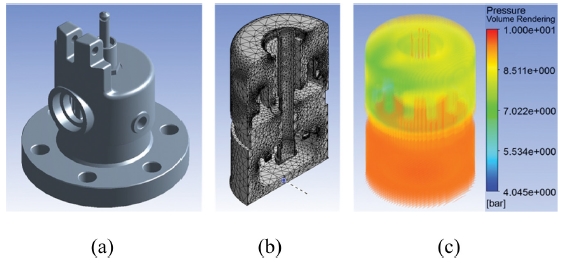
(a) A three dimensional model of a poppet valve, (b) Fluid mesh modeling in the poppet valve, (c) Steam pressure distribution in the poppet valve
2.3 인입 거리에 따른 분사 스팀 해석
2.1에서 구성한 인입거리에 따른 유체 전산모사해석 모델에 포핏 밸브 내부의 압력 감소를 해석한 결과를 토대로 인입거리에 따른 벽면에서의 분사 스팀 압력과 속도에 대한 해석을 수행하였다. Fig. 4에 해석을 통해 나타난 분사 스팀의 속도를 나타내었다. 인입거리가 증가함에 따라 노즐로부터 더 먼 거리까지 유체의 속도가 유지되는 것을 알 수 있다. Fig. 5(a)에서 보이는 것과 같이 벽면에서의 최대 압력이 약 1 bar 부근에서 나타나며 인입거리가 45 mm에서 75 mm까지 커질수록 최대 압력이 나타나는 반경 거리가 더 멀어짐을 알 수 있다.
또 벽면 부근에서의 스팀 최대 속도는 Fig. 5(b)에서 보듯이 약 350 m/s2로 나타나며 거리가 멀어질수록 감소한다. 인입 거리가 커질수록 벽면에서 속도가 형성되는 최대 도달거리 또한 커지게 된다. 인업거리가 75 mm인 경우 인입거리 45 mm일때보다 최대 도달 거리는 약 0.6 m 증가하게 된다. 이러한 최대 도달 거리의 증가로 인해 인입거리에 따른 공동 분사 영역과 해당 영역에서의 침식률의 차이가 나타나게 된다.
3. 월 블로워의 공동 분사 영역
3.1 보일러 내부 부착물의 침식률
월 블로워의 공동 분사 영역에서 노즐 분사 스팀에 의한 부착물 제거 성능을 분석하기 위하여 부착물 제거 메커니즘에 대한 연구를 수행하였다. 일반적으로 부착물 제거는 침식에 의한 영향이 크다고 알려져있다.4-6 따라서 본 연구에서는 분사 스팀에 의한 상대 침식률을 분석하여 노즐의 부착물 제거 성능을 평가하고 공동 분사 영역의 영향을 고려하였다.
고속의 증기에 섞인 액적(Droplet)이 표면에 충돌하며 손상을 입힌다. 이러한 액적충돌침식(Liquid Droplet Impingement Erosion)7 현상에 의해 배관의 감육이 일어나는 것과 마찬가지로 월 블로워의 분사 스팀에 의해 부착물의 제거가 진행된다. 기존 터빈 블레이드나 항공 산업을 대상으로 이러한 침식에 대한 연구가 지속적으로 진행되고 있고 유체의 분사 상태 및 재료 물성 등에 따른 다양한 침식률 예측 모델이 개발되었다.8-11 이러한 액적충돌침식에 의한 감육 속도는 특히 액적의 유속과 비례한다고 알려져 있다.12 본 연구에서는 인입거리가 변함에 따라 재료 물성 등의 상수가 변하지 않기 때문에 분사 속도를 기반으로 한 상대 침식률 평가모델을 적용하였다.
일반적으로 침식률 E는 아래 식과 같이 유체 속도(V), 액적의 크기(r), 재료의 경도(Hv)에 영향을 받는 것으로 알려져 있다.14,15
(1) |
여기서, k는 비례상수이며, Vjet/Vref는 액적의 상대적인 속도비이며, rjet/rref는 액적 크기의 상대적인 비이며, g(Hv)는 재료의 경도에 관한 함수이다. 여기서 액적의 크기는 유체 속도의 제곱에 반비례하므로12 rjet/rref는 다음과 같은 관계를 갖는다.
(2) |
따라서 식(1)은 다음과 같다.
(3) |
재료가 동일한 상태이므로 침식계수(k), 재료 경도(Hv)를 상수로 처리하여 무차원화하여 월 블로워 분사 스팀 속도에 의한 상대 침식률(EW.B.)을 다음과 같이 정의한다.
(4) |
여기서, 이며 기존 연구에13 따르면 상수 a는 5.1이고 b는 2이다.
위에서 도출한 월 블로워의 침식률 모델과 유체 유한요소 해석을 통해 계산된 분사 속도를 바탕으로 노즐로부터의 거리 및 인입 거리에 따른 침식률을 계산하였다. 인입거리 45 mm에서 최고 속도일 경우를 기준 침식률로 설정하여 인입거리와 도달거리에 따른 상대 침식률은 Fig. 6과 같이 나타난다. 상대 침식률은 앞서 해석을 통해 나타난 속도의 경향과 유사하며 최대 도달 거리를 벗어난 영역에서 분사 증기의 침식률은 0이 된다.
3.2 인입 거리에 따른 공동 분사 영역
월 블로워의 공동 분사 영역에서는 단독 분사 영역과는 다르게 양쪽 노즐에서 분사되는 증기에 각각 영향을 받게 된다. 본 모델에서는 한 쪽 노즐에서 분사 후 일정 시간이 지난 후 다른 노즐에서 분사가 되므로 공동 분사 영역 부분은 해당 위치에서의 양쪽 노즐 침식률을 합한 값이 된다. 이러한 공동분사 영역을 알기 위해 두 개의 노즐, 그리고 4개의 노즐이 격자를 이룬 모델에 대해 탐구한다.
따라서 발전소에서의 실제 월 블로워 간격에 따라 3.5 m 떨어진 노즐 사이의 공동분사영역을 고려한 상대 침식률은 Fig. 7과 같이 나타난다. 노즐에서 가까운 거리의 최대 침식률은 인입거리가 가장 짧은 45 mm에서 나타나지만, 짧은 도달거리로 인해 특정 영역에서의 침식률이 밀집되어 높게 나타남을 알 수 있다. 반면에 인입거리가 가장 큰 75 mm에서는 노즐 부근의 침식률이 기준 침식률의 70% 정도로 나타나는 반면에 넓은 영역에서 고른 침식률이 나타난다.
실제 보일러 내부의 월 블로워는 3.5 m 간격의 격자 형태로 배치되어 있어 상하좌우 모두 공동 분사 영역이 나타난다. 이로 인해 최대 도달 거리에 따라 음영 구역이 나타날 수 있기 때문에 격자형 배열 상태에서의 상대 침식률 분석을 수행하였다. 월 블로워 간의 간격은 이전 경우와 같이 3.5 m로 배열하여 Fig. 8과 같이 단독 및 공동 분사 영역을 도식화하였다. Fig. 8(a)는 인입거리 45 mm인 경우로 격자형 배치 한 가운데 부분이 음영 영역으로 나타난다. 이러한 음영 영역은 인입거리가 커져 최대 도달 거리가 멀어지면서 사라지며 충분한 상대 침식률이 확보된다. 앞서 분석한 바와 같이 노즐과 가까운 거리에서는 인입거리 45 mm인 경우의 침식률이 더 높게 확보되는 반면 인입거리 75 mm에서는 전체적으로 고른 침식률이 확보된다. 따라서 부착물의 분포 상태에 따라 노즐의 인입거리를 45 mm에서 75 mm로 변경함으로써 최적의 제매 성능을 확보할 수 있다.
4. 결론
본 연구에서는 월 블로워의 인입 거리에 따른 제매 능력의 분석을 위하여 유체 전산모사해석 모델을 개발하고 전산모사를 통해 도출된 분사 유체의 속도를 상대 침식률 모델에 대하여 적용하였다. 이를 통해 월 블로워 노즐로부터 가까운 거리의 부착물 제거에는 인입거리 45 mm인 월 블로워가 유리하고, 노즐로부터 먼거리의 음영 구역 제거 및 고른 제매를 위해서는 인입거리 75 mm인 월 블로워가 우수함을 밝혔다.
Acknowledgments
본 연구는 2015년도 산업통상자원부의 재원으로 한국에너지기술평가원(KETEP)의 지원을 받아 수행한 연구 과제입니다(No. 20151110100030).
REFERENCES
- Barrett, R. E., “Slagging and Fouling in Pulverized-Coal-Fired Utility Boilers: A Survey of Boiler Design Practices for Avoiding Slagging and Fouling,” Battelle Columbus Div., Report No. EPRI-CS-5523-Vol. 2, 1987.
-
Isreb, M., “Integrated Life Synthesis for Boiler Sootblowers in Fossil Power Plants,” Computers & Structures, Vol. 63, No. 6, pp. 1043-1051, 1997.
[https://doi.org/10.1016/S0045-7949(96)00407-5]
- Jang, I., Kim, J. H., and Jang, Y. H., “Optimization of Nozzle Shape Parameters for Wall-Blower,” Proc. of KSPE Autumn Conference, p. 331, 2015.
-
Zbogar, A., Frandsen, F., Jensen, P. A., and Glarborg, P., “Shedding of Ash Deposits,” Progress in Energy and Combustion Science, Vol. 35, No. 1, pp. 31-56, 2009.
[https://doi.org/10.1016/j.pecs.2008.07.001]
-
Mu, L., Zhao, L., and Yin, H., “Modelling and Measurements of the Characteristics of Ash Deposition and Distribution in a HRSG of Wastewater Incineration Plant,” Applied Thermal Engineering, Vol. 44, pp. 57-68, 2012.
[https://doi.org/10.1016/j.applthermaleng.2012.03.039]
-
Fang, Q., Wang, H., Wei, Y., Lei, L., Duan, X., et al., “Numerical Simulations of the Slagging Characteristics in a Down-Fired, Pulverized-Coal Boiler Furnace,” Fuel Processing Technology, Vol. 91, No. 1, pp. 88-96, 2010.
[https://doi.org/10.1016/j.fuproc.2009.08.022]
-
Cook, S. S., “Erosion by Water-Hammer,” Proceedings of the Royal Society A, Vol. 119, No. 783, pp. 481-488, 1928.
[https://doi.org/10.1098/rspa.1928.0107]
- Kim, K.-H., Hwang, K.-M., and Park, S.-H., “Shell Wall Thinning and Mitigation Plan and Design Modification of a Feedwater Heater Impingement Baffle,” Journal of the Korean Society for Precision Engineering, Vol. 27, No. 6, pp. 55-63, 2010.
-
Heymann, F. J., “High Speed Impact between a Liquid Drop and a Solid Surface,” Journal of Applied Physics, Vol. 40, No. 13, pp. 5113-5122, 1969.
[https://doi.org/10.1063/1.1657361]
-
Rein, M., “Phenomena of Liquid Drop Impact on Solid and Liquid Surfaces,” Fluid Dynamics Research, Vol. 12, No. 2, pp. 61-93, 1993.
[https://doi.org/10.1016/0169-5983(93)90106-K]
- Rochester, M. C. and Brunton, J. H., “Influence of Physical Properties of the Liquid on the Erosion of Solids,” ASTM International, Article No. STP567, 1974.
-
Reitz, R. D. and Bracco, F. V., “Mechanism of Atomization of a Liquid Jet,” The Physics of Fluids, Vol. 25, No. 10, pp. 1730-1742, 1982.
[https://doi.org/10.1063/1.863650]
-
Lee, B.-E., Riu, K.-J., Shin, S.-H., and Kwon, S.-B., “Development of a Water Droplet Erosion Model for Large Steam Turbine Blades,” Journal of Mechanical Science and Technology, Vol. 17, No. 1, pp. 114-121, 2003.
[https://doi.org/10.1007/BF02984292]
-
Ahmad, M., Casey, M., and Sürken, N., “Experimental Assessment of Droplet Impact Erosion Resistance of Steam Turbine Blade Materials,” Wear, Vol. 267, Nos. 9-10, pp. 1605-1618, 2009.
[https://doi.org/10.1016/j.wear.2009.06.012]
- Jeong, H.-C., Kim, D.-W., Choi, G.-M., and Kim, D.-J., “The Effect of Injection Angle and Pressure on Etch of Invar Plate Using Industrial Etch-Nozzle,” Journal of the Korean Society for Precision Engineering, Vol. 23, No. 8, pp. 47-53, 2006.