
연마가공과 자기조립단분자막 코팅 기반 다종 금속의 극소수성 표면 제작기술
Copyright © The Korean Society for Precision Engineering
This is an Open-Access article distributed under the terms of the Creative Commons Attribution Non-Commercial License (http://creativecommons.org/licenses/by-nc/3.0) which permits unrestricted non-commercial use, distribution, and reproduction in any medium, provided the original work is properly cited.
Abstract
A study about superhydrophobic surface started from the analysis of lotus leaf, and superhydrophobic surface fabrication methods have been researched. These methods cannot be used on various metals because the fabrication methods have complex and material-selective processes. In this work, we report a simple fabrication method using abrasive blasting and a self-assembled monolayer coating to produce a superhydrophobic surface. Abrasive blasting was used to create microstructures on metal surfaces. Random peak and valley microstructures were created after abrasive blasting, and a surface profile was measured to analyze the relationship between blasting pressure and a roughness parameter. A hydrophobic material coating was performed by a self-assembled monolayer method. Six kinds of metal surfaces displayed superhydrophobic properties. This utilitarian method could be applied to diverse applications.
Keywords:
Metal, Superhydrophobicity, Abrasive blasting, Self-assembled monolayer, Microstructure키워드:
금속, 극소수성, 연마가공, 자기조립단분자막, 마이크로 구조1. 서론
극소수성 표면은 물과의 접촉각이 150도 이상인 표면을 일컫는 말로써 높은 접촉각으로 인해 물이 젖지 않는 특성을 가져 항균,1 항곰팡이,2 자가세정,3,4 유수분리,3 방식,4 방빙5 등의 수분과 관련된 응용분야에의 적용이 기대되고 있다. 이러한 기능성을 다양한 재질의 표면에 구현하기 위하여 연꽃의 계층적인 구조를 분석, 모사하는 것에서 시작하여 많은 연구개발이 이루어져 왔다.6-9 특히 금속 재질의 극소수성 표면의 경우 산업에서 금속을 사용함에 따라 반드시 발생하게 되는 부식과 관련된 문제를 해결하기 위하여 연구개발이 진행되어 왔다.10-18
금속 기반의 극소수성 표면 제작방법은 크게 소수성 물질을 구조화하여 금속표면에 부착하는 방법10-13과 금속의 미세구조 형성 후 소수성 물질을 얇게 코팅하는 방법으로 나뉜다.14-20 소수성 물질을 구조화하여 부착하는 방법은 금속의 종류에 대한 제한이 없지만 소수성 물질과 표면과의 결합이 접착성질에 의해 결정되므로 내구성에 한계가 있다. 미세구조를 형성하고 소수성 물질을 코팅하는 방식은 금속에 따라 마이크로/나노 구조를 생성하는 방법이 다르기 때문에 레이저가공,14,19 산에칭,15,16 도금,17,18 양극산화20 등과 같은 다양한 미세구조 형성 방법이 사용된다. 도금과 양극산화의 경우는 복잡한 표면에 적용이 어렵고 추가 전력이 필요하다는 점, 산에칭의 경우는 유해물질의 사용 및 배출이 있다는 점, 레이저가공의 경우는 공정이 복잡하고 대면적 가공이 힘들다는 점에서 산업적인 응용이 제한적이다.
본 연구에서는 모래분사를 통한 표면연마로 간단하게 마이크로 구조 금속표면을 생성하였으며 이러한 표면에 자기조립단분자를 코팅하여 6종의 금속에 극소수성 표면을 제작하였다. 이를 통해 모래분사 압력과 표면거칠기와의 관계를 확인하고, 접촉각 측정을 통하여 표면거칠기가 극소수성에 미치는 영향을 관찰함으로써 다양한 금속에 쉽게 적용 가능한 극소수성 금속표면 제작 공법을 확립하고자 한다.
2. 시편 제작 및 실험 방법
철금속과 비철금속 중 산업에서 많이 사용되는 알루미늄, 구리, 철과 대표적인 합금 3종을 표면재질로 채택하였다. 산업용 알루미늄(순도 99.5%), 산업용 구리(순도 99.0%), 연철(탄소 0.25%)과 황동(아연 30.0%), 스테인리스강 304(크롬 18.0%, 니켈 8.0%) 그리고 스테인리스강 316(크롬 17.0%, 니켈 12.0%) 재질에 동일한 연마가공과 코팅 공법을 사용하여 극소수성 표면을 제작하였다.
2.1 표면 제작
금속표면 연마는 건식 샌드블라스팅 기기를 이용하였다. 산업에서 건식 샌드블라스팅은 10 kgf/cm2 이하의 분사 압력을 이용하며 가장 일반적으로 사용되는 4 kgf/cm2 조건을 기준으로 시험 범위를 선정하였다. 4, 6, 8 kgf/cm2로 분사 압력을 증가해가며 500 메쉬 크기의 모래(30-40 μm)를 분사하였다. 시편과 5 cm거리에서 표면 전체를 10 회 반복하여 연마한 후 시편에 남아있을 수 있는 모래를 제거하기 위하여 초순수를 사용하여 5분간 세척 후 건조하였다. 자기조립단분자막을 코팅하기 위하여, 건조된 시편을 Heptadecafluoro-1,1,2,2-Tetrahydrodecyl Trichlorosilane (HDFS)와 헥산을 1 : 1000 비율로 교반한 용액에 2시간 담궈 처리하였으며 그 후 헥산 용액에 1시간 세척하였다. 최적화된 극소수 표면 제작 공법을 이용하여 15 cm × 40 cm 면적을 가지는 스테인리스강 304에 6 kgf/cm2의 연마가공 압력 조건을 이용하여 극소수성 표면을 제작하였다. 상기의 모든 공정은 상온에서 진행하였다.
2.2 표면 분석
연마가공 후 표면의 미세구조는 전자주사현미경(FE-SEM; JEOL, JSM-7401F, NINT) 장비를 사용하여 확인하였다. LEI 모드에서 구조를 관찰하였으며 표면구조 확인과 동시에 에너지분산 분광기(EDS)를 통하여 코팅 전, 후 성분 변화를 확인하였다. 압력 조건에 따른 표면거칠기 변화는 3차원 프로파일러(Wyko Veeco NT1100)를 통해 확인하였다. 표면거칠기는 산술평균 거칠기인 Ra를 분석하여 평가하였으며 계산식은 아래와 같다.
(1) |
y값은 거칠기를 측정하고자 하는 표면의 중심 평면에서 표면까지의 수직 거리이며 산술 평균 거칠기는 y값의 절대값을 평균한 것이다. 샘플링 길이는 951 nm이며 측정한 영역은 가로 640 μm × 480 μm이다.
표면거칠기 변화를 통해 나타나는 젖음성 변화는 DSA-100 (Kr¨uss Co.) 장비를 통해 5 μl 물방울을 표면에 떨어트려 측정하는 세실 드랍 측정법을 이용하여 확인하였다. 연마공정 조건, 금속표면 재질, 코팅 유무에 따라 젖음성이 달라졌으며 각 시편마다 접촉각을 5회 측정하여 평균과 표준편차를 계산하였다.
3. 결과 및 토의
3.1 분사 압력과 표면
모래분사를 통한 연마가공은 표면의 녹, 오염, 돌출부 제거 및 접착, 도금의 전처리 등에 사용되는 가장 일반적인 방법으로 압축기에서 나오는 공기가 노즐을 통과하여 모래 입자를 분사하는 시스템으로 구성되어 있다. 이때 분사한 수많은 모래 입자의 크기, 속도 및 표면과의 충돌 방향 등이 복합적으로 작용하여 금속표면에 미세 구조를 형성하게 된다. 알루미늄 표면에 4 kgf/cm2의 연마가공 압력 조건으로 연마가공을 진행한 결과 분사된 모래 입자 크기보다 작은 딤플 구조가 중첩되어 곡선 형태의 굴곡이 이어져 있는 마이크로 구조가 형성됨을 확인하였다(Fig. 1(b)). 동일한 압력(4 kgf/cm2)으로 나머지 5종의 금속에 연마가공을 하였으며 같은 비율을 가지는 SEM과 3D 프로파일러 이미지의 비교를 통해 재질별 마이크로 구조의 형상 및 깊이를 분석하였다. 재질이 다른 금속의 경우 SEM 이미지를 통해서는 유사한 형태로 보이지만 마이크로 구조의 깊이와 밀도에서 차이가 있음을 알 수 있다(Fig. 2). 또한 3D 프로파일러를 통해 확인한 0.31 mm2 면적의 표면에 연마를 통해 생성된 마이크로 구조가 전체적으로 고르게 생성되어 있어 연마가공을 통하여 금속표면의 젖음성을 균일하게 구현할 수 있을 것으로 판단할 수 있다.
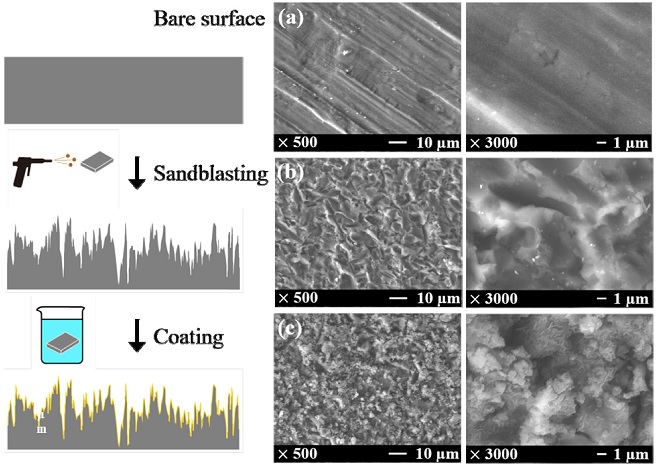
Scheme of the superhydrophobic metal surface fabrication process and SEM images of aluminum surface at each step: (a) Bare surface, (b) Sandblasted surface, (c) Sandblasted and HDFS coated surface
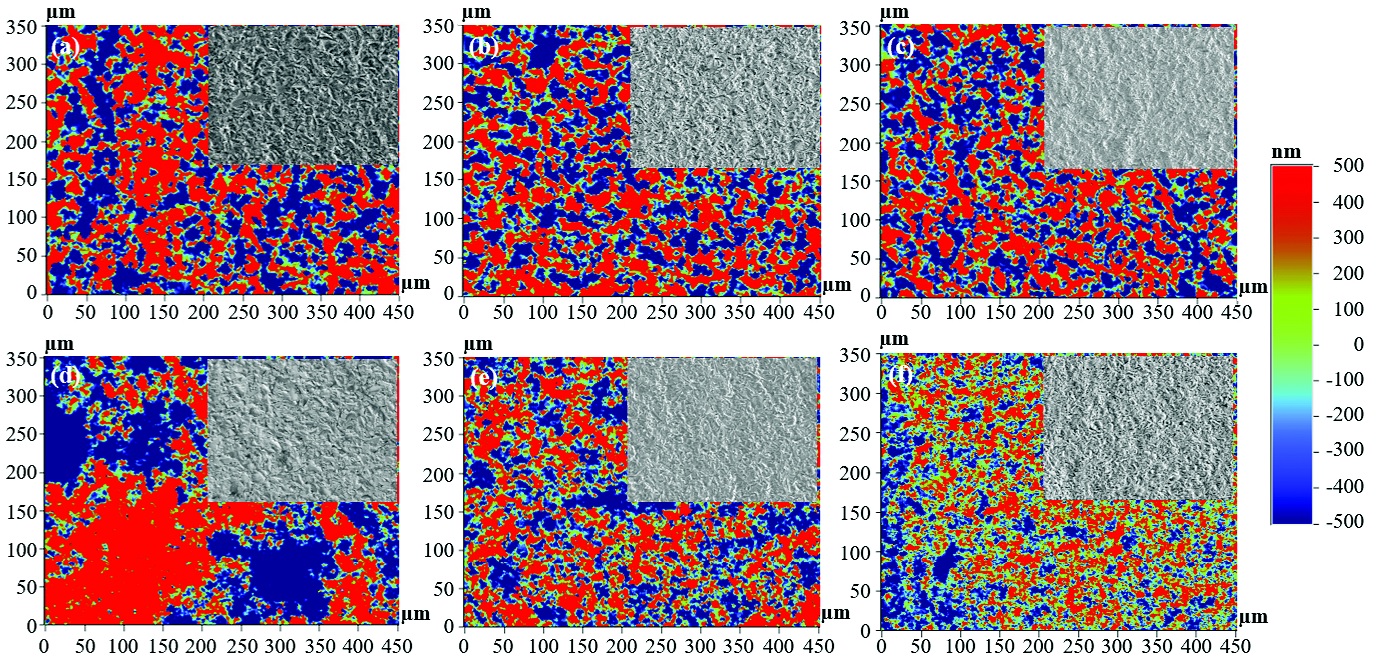
2D images of sandblasted metal surfaces after the surface profiling process and SEM images of the surfaces. The magnification of the images are same: (a) Aluminum, (b) Copper, (c) Brass, (d) Mild steel, (e) Stainless steel 304 (SUS304), (f) Stainless steel 316 (SUS316)
표면거칠기를 평가하기 위해 사용한 Ra값은 연마가공의 압력 조건이 4, 6, 8 kgf/cm2로 변화함에 따라 증가하는 결과를 보였다(Fig. 3). 압력은 모래 입자의 충돌 속도에 비례하는 효과를 주므로 압력이 커짐에 따라 평균 거칠기 값이 커지는 것으로 판단할 수 있다. 최고점과 최저점 사이의 수직 방향 거리는 알루미늄에 8 kgf/cm2의 연마가공 압력 조건으로 마이크로 구조를 형성한 경우 나타났으며 그 값은 19.4 μm이다. 연마가공을 통해 제작된 마이크로 구조는 6종의 금속에서 표면의 중심 평면에서 ±10 μm 이하의 높이로 굴곡이 형성되어 있음을 알 수 있다. 다만 재질별로 경도가 상이하기 때문에 압력에 따라 발생하는 거칠기와 압력 증가에 따른 거칠기 변화 폭은 다른 것으로 확인하였다. 동일한 압력 증가에도 불구하고 금속 중 가장 경도가 낮은 알루미늄은 연철의 평균거칠기를 역전하는 경향을 보였으며 황동과 스테인리스강 304, 316의 경우 합금의 상대적으로 높은 경도로 인해 구리, 연철에 비해 평균 거칠기가 33.3% 이상 낮게 나옴을 확인할 수 있다. 이러한 결과를 통해 모래분사 위치를 고정하여 마이크로 구조를 표면 전체에 고르게 생성할 수 있으며 압력 조절을 통해 원하는 거칠기를 선택적으로 표면에 생성 시킬 수 있음을 알 수 있다.
3.2 표면거칠기와 극소수성
모래분사를 통해 생성된 마이크로 구조에 자기조립단분자막을 코팅하면 Fig. 1(c)와 같이 마이크로 구조에 영향을 주지 않으며 소수성 구현이 가능하다. EDS를 이용한 성분 분석을 통해 자기조립단분자막 코팅 후 금속표면에서 HDFS에 포함되어 있는 플루오르 원자를 확인할 수 있으며 알루미늄, 구리, 연철 표면에 각각 19.1 wt.%, 13.5 wt.%, 9.5 wt.% 존재함을 확인하였다. 동일 시간 코팅하였음에도 불구하고 플루오르 원소의 차이가 나는 이유는 자기조립단분자의 끝에서 금속과 반응하는 실레인이 금속 원자에 따라 반응성의 차이를 가지고 있기 때문이며, 알려진 실레인과 금속 원자와의 반응성은 알루미늄, 구리, 연철 순이므로 EDS를 통해 측정된 결과값과 일치함을 알 수 있다.21
표면처리에 따른 접촉각 변화를 Table 1에 정리하였다. 연마가공을 진행하지 않은 금속표면에 자기조립단분자막 코팅으로 최소 115.4o 이상의 접촉각을 가지는 소수성 표면을 제작할 수 있으며 이러한 값은 금속의 겉보기 접촉각에서 최소 21.2o에서 최대 60.8o까지 증가된 값이다. 거칠기가 동일한 표면에서 겉보기 접촉각은 물질의 고유한 표면에너지에 의해 결정된다.22 금속표면에 자기조립단분자를 코팅함으로써 변화된 표면에너지로 인하여 접촉각이 상승하였음을 알 수 있다. 하지만 이러한 소수성 표면에서는 물방울은 접착되어 떨어지지 않으며 알려진 극소수성 표면과 달리 미세구조가 존재하지 않아 공기를 포집 할 수 없기 때문으로 판단된다.
표면거칠기와 극소수성간의 관계를 알아보기 위하여 자기조립단분자막이 코팅된 마이크로 구조 금속표면의 접촉각 측정을 통하여 소수성 변화를 확인하였다.
연마가공을 진행하여 마이크로 구조가 생성된 표면에 자기조립단분자막을 코팅하면 공기를 포집할 수 있는 구조로 인하여 자기조립단분자막 코팅만을 진행한 표면보다 소수성이 높음을 확인할 수 있다(Fig. 4). 일정 압력 조건 이상에서 극소수성 표면을 얻을 수 있으며 이는 연마가공 압력에 비례하여 표면거칠기가 증가하고, 표면거칠기가 높은 표면에서 공기를 많이 포집하고 있기 때문이다.23
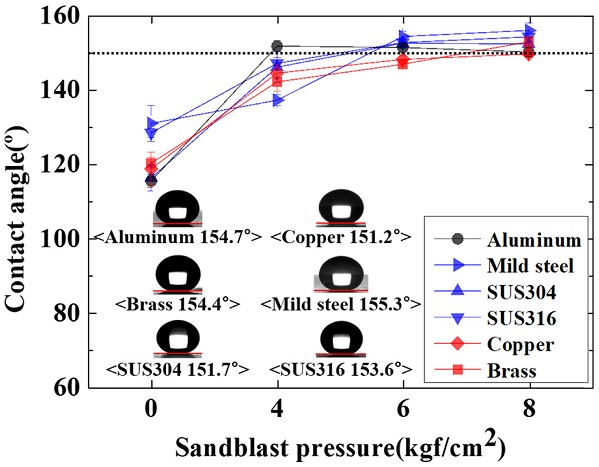
Contact angles of sandblasted metal surfaces after self-assembled monolayer coating and images of water droplet of superhydrophobic metal surfaces
재질별로 150o 이상의 극소수성이 나타나는 최소 압력 값에 차이가 있으며 Fig. 4에서 그 값을 확인할 수 있다. 알루미늄 표면은 4 kgf/cm2 조건 이상에서, 연철, 스테인리스강 304, 316 표면은 6 kgf/cm2 조건 이상에서, 구리 및 황동은 8 kgf/cm2 조건에서 극소수성 성질을 구현할 수 있다. 표면거칠기와 표면의 자기조립단분자막이 표면 소수성에 복합적으로 영향을 주며 이는 연마가공의 압력 조건 4 kgf/cm2에서 연철의 표면거칠기 값이 알루미늄에 비해 16.5% 높음에도 불구하고 알루미늄 대비 10.0% 이하의 접촉각을 보이며, 또한 연마가공의 압력 조건 6 kgf/cm2에서 극소수성을 나타내는 스테인리스강 316에 비해서 구리의 표면거칠기가 27.5% 가량 높음에도 불구하고 접촉각 150o 이하를 보이는 것에서 판단할 수 있다. 표면거칠기 및 금속표면의 플루오르 양과 표면 극소수성에 대한 상세한 분석은 앞서 제시한 연마가공의 압력 조건을 기반으로 자기조립단분자막 코팅 조건을 변화시켜가며 추가 실험하여 논의할 예정이다. 확보된 극소수성 제작 공법의 산업화 적용 가능성을 확인해보기 위하여 대면적 스테인리스강 304 표면에 극소수성을 균일하게 구현하였다.
4. 결론
연마 공정과 자기조립단분자막 코팅을 통하여 6종의 금속재질에 극소수성 표면을 제작할 수 있었다. 표면거칠기 측정 및 SEM 이미지를 통해 연마 공정을 통해 생성된 마이크로 구조가 형성됨을 확인하였으며 금속에 따라 압력과 표면거칠기는 비례관계에 있음을 알 수 있었다. 자기조립단분자막 코팅 후 소수성 표면을 제작하였으며 각각의 재질에서 극소수성을 얻을 수 있는 연마가공의 압력 조건을 확인하였다. 알루미늄의 경우 4 kgf/cm2, 연철, 스테인리스강의 경우 6 kgf/cm2, 구리와 황동의 경우 8 kgf/cm2의 압력 조건으로 형성한 마이크로 구조 표면에서 자기조립단분자막 코팅을 통해 극소수성 표면을 얻을 수 있었다. 또한 대면적 표면 제작을 통하여 산업화 가능성을 확인하였으며 다양한 금속 재질에 사용할 수 있는 단일 공정법을 확립하였다. 이러한 연구결과는 연마가공을 사용하는 금속표면 세척 및 전처리 산업에 쉽게 적용할 수 있으며, 부식 환경에서 사용할 수 있는 기능성 금속표면을 제공함으로써 응용분야를 넓힐 수 있을 것으로 보인다.
NOMENCLATURE
Ra : | Roughness average (nm) |
y : | Vertical distance from the mean plane (nm) |
SUBSCRIPT
i, j : | Index of summation |
Acknowledgments
이 논문은 2012년도 교육부와 한국연구재단의 지역혁신인력양성사업의 지원을 받아 수행된 연구임(NRF-2012H1B8A2026127).
REFERENCES
-
An, A. K., Guo, J., Lee, E.-J., Jeong, S., Zhao, Y., et al., “PDMS/PVDF Hybrid Electrospun Membrane with Superhydrophobic Property and Drop Impact Dynamics for Dyeing Wastewater Treatment Using Membrane Distillation,” Journal of Membrane Science, Vol. 525, pp. 57-67, 2017.
[https://doi.org/10.1016/j.memsci.2016.10.028]
-
Kim, Y. and Hwang, W., “Wettability Modified Aluminum Surface for a Potential Antifungal Surface,” Materials Letters, Vol. 161, pp. 234-239, 2015.
[https://doi.org/10.1016/j.matlet.2015.08.103]
-
Cao, W.-T., Liu, Y.-J., Ma, M.-G., and Zhu, J.-F., “Facile Preparation of Robust and Superhydrophobic Materials for Self-Cleaning and Oil/Water Separation,” Colloids and Surfaces A: Physicochemical and Engineering Aspects, Vol. 529, pp. 18-25, 2017.
[https://doi.org/10.1016/j.colsurfa.2017.05.064]
-
Zhang, Z., Ge, B., Men, X., and Li, Y., “Mechanically Durable, Superhydrophobic Coatings Prepared by Dual-Layer Method for Anti-Corrosion and Self-Cleaning,” Colloids and Surfaces A: Physicochemical and Engineering Aspects, Vol. 490, pp. 182-188, 2016.
[https://doi.org/10.1016/j.colsurfa.2015.11.049]
-
Bengaluru Subramanyam, S., Kondrashov, V., Rühe, J. R., and Varanasi, K. K., “Low Ice Adhesion on Nano-Textured Superhydrophobic Surfaces under Supersaturated Conditions,” ACS Applied Materials & Interfaces, Vol. 8, No. 20, pp. 12583-12587, 2016.
[https://doi.org/10.1021/acsami.6b01133]
-
Barthlott, W. and Neinhuis, C., “Purity of the Sacred Lotus, or Escape from Contamination in Biological Surfaces,” Planta, Vol. 202, No. 1, pp. 1-8, 1997.
[https://doi.org/10.1007/s004250050096]
-
Zhai, L., Cebeci, F. Ç., Cohen, R. E., and Rubner, M. F., “Stable Superhydrophobic Coatings from Polyelectrolyte Multilayers,” Nano Letters, Vol. 4, No. 7, pp. 1349-1353, 2004.
[https://doi.org/10.1021/nl049463j]
-
Kim, D., Hwang, W., Park, H. C., and Lee, K.-H., “Superhydrophobic Nano-Wire Entanglement Structures,” Journal of Micromechanics and Microengineering, Vol. 16, No. 12, pp. 2593-2597, 2006.
[https://doi.org/10.1088/0960-1317/16/12/011]
-
Erbil, H. Y., Demirel, A. L., Avcı, Y., and Mert, O., “Transformation of a Simple Plastic into a Superhydrophobic Surface,” Science, Vol. 299, No. 5611, pp. 1377-1380, 2003.
[https://doi.org/10.1126/science.1078365]
-
de Leon, A. C. C., Pernites, R. B., and Advincula, R. C., “Superhydrophobic Colloidally Textured Polythiophene Film as Superior Anticorrosion Coating,” ACS Applied Materials & Interfaces, Vol. 4, No. 6, pp. 3169-3176, 2012.
[https://doi.org/10.1021/am300513e]
-
Ishizaki, T., Kumagai, S., Tsunakawa, M., Furukawa, T., and Nakamura, K., “Ultrafast Fabrication of Superhydrophobic Surfaces on Engineering Light Metals by Single-Step Immersion Process,” Materials Letters, Vol. 193, pp. 42-45, 2017.
[https://doi.org/10.1016/j.matlet.2017.01.050]
-
Zhang, X.-F., Chen, R.-J., Liu, Y.-H., and Hu, J.-M., “Electrochemically Generated Sol-Gel Films as Inhibitor Containers of Superhydrophobic Surfaces for the Active Corrosion Protection of Metals,” Journal of Materials Chemistry A, Vol. 4, No. 2, pp. 649-656, 2016.
[https://doi.org/10.1039/C5TA07443F]
-
Isimjan, T. T., Wang, T., and Rohani, S., “A Novel Method to Prepare Superhydrophobic, UV Resistance and Anti-Corrosion Steel Surface,” Chemical Engineering Journal, Vol. 201, pp. 182-187, 2012.
[https://doi.org/10.1016/j.cej.2012.08.090]
-
Modestov, A., Emelyanenko, K., Emelyanenko, A., Domantovsky, A., and Boinovich, L., “Application of Laser Micro-and Nanotexturing for the Fabrication of Superhydrophobic Corrosion-Resistant Coatings on Aluminum,” Russian Chemical Bulletin, Vol. 65, No. 11, pp. 2607-2611, 2016.
[https://doi.org/10.1007/s11172-016-1625-3]
-
Jie, H., Xu, Q., Wei, L., and Min, Y., “Etching and Heating Treatment Combined Approach for Superhydrophobic Surface on Brass Substrates and the Consequent Corrosion Resistance,” Corrosion Science, Vol. 102, pp. 251-258, 2016.
[https://doi.org/10.1016/j.corsci.2015.10.013]
-
Varshney, P., Mohapatra, S. S., and Kumar, A., “Superhydrophobic Coatings for Aluminium Surfaces Synthesized by Chemical Etching Process,” International Journal of Smart and Nano Materials, Vol. 7, No. 4, pp. 248-264, 2016.
[https://doi.org/10.1080/19475411.2016.1272502]
-
Khorsand, S., Raeissi, K., Ashrafizadeh, F., Arenas, M., and Conde, A., “Corrosion Behaviour of Super-Hydrophobic Electrodeposited Nickel-Cobalt Alloy Film,” Applied Surface Science, Vol. 364, pp. 349-357, 2016.
[https://doi.org/10.1016/j.apsusc.2015.12.122]
-
Huang, Y., Sarkar, D. K., Gallant, D., and Chen, X.-G., “Corrosion Resistance Properties of Superhydrophobic Copper Surfaces Fabricated by One-Step Electrochemical Modification Process,” Applied Surface Science, Vol. 282, pp. 689-694, 2013.
[https://doi.org/10.1016/j.apsusc.2013.06.034]
-
Dong, C., Gu, Y., Zhong, M., Li, L., Sezer, K., et al., “Fabrication of Superhydrophobic Cu Surfaces with Tunable Regular Micro and Random Nano-Scale Structures by Hybrid Laser Texture and Chemical Etching,” Journal of Materials Processing Technology, Vol. 211, No. 7, pp. 1234-1240, 2011.
[https://doi.org/10.1016/j.jmatprotec.2011.02.007]
-
Kim, Y., Lee, S., Cho, H., Park, B., Kim, D., et al., “Robust Superhydrophilic/Hydrophobic Surface Based on Self-Aggregated Al2O3 Nanowires by Single-Step Anodization and Self-Assembly Method,” ACS Applied Materials & Interfaces, Vol. 4, No. 10, pp. 5074-5078, 2012.
[https://doi.org/10.1021/am301411z]
- Gelest, “Silane Coupling Agents: Connecting Across Boundaries,” http://www.gelest.com/wp-content/uploads/Goods-PDF-brochures-couplingagents.pdf, . (Accessed 12 JAN 2018)
-
Wenzel, R. N., “Surface Roughness and Contact Angle,” Journal of Physical Chemistry, Vol. 53, No. 9, pp. 1466-1467, 1949.
[https://doi.org/10.1021/j150474a015]
-
Cassie, A. and Baxter, S., “Large Contact Angles of Plant and Animal Surfaces,” Nature, Vol. 155, No. 3923, pp. 21-22, 1945.
[https://doi.org/10.1038/155021a0]