
소재 압출 방식 3D 프린팅 출력물 삼차원 형상 치수 표준 확립을 위한 기초 연구
Copyright © The Korean Society for Precision Engineering
This is an Open-Access article distributed under the terms of the Creative Commons Attribution Non-Commercial License (http://creativecommons.org/licenses/by-nc/3.0) which permits unrestricted non-commercial use, distribution, and reproduction in any medium, provided the original work is properly cited.
Abstract
Material extrusion (ME) type 3D printing has been widely utilized through various types of systems depending on the fabrication methods, materials, and precision to fabricate complex workpieces that cannot be made with conventional methods. This study provides basic considerations in response to the current demands on performance evaluation of ME type 3D printing related to dimensions as well as the realization of the guidelines to be established in the near future. As a simple specimen for these purposes, 2D and 3D hole-plates were designed and fabricated by using a ME type entry-level 3D printer. For evaluation of dimensions on the specimen, both specimens were measured by a calibrated tool-maker’s microscope which is to length standard. The measurement parameters were the center position of the holes, the diameter of the holes, and the circularity error of the holes.
Keywords:
ME 3D printing, Dimensional standard키워드:
재료 압출 방식의 3차원 프린팅, 형상 치수 표준1. 서론
최근 3D 프린터(Three-Dimensional Printer)는 출력 방식, 출력물의 소재, 출력물의 크기, 출력 분해능에 따라 다양한 종류로 개발 및 출시되고 있으며, 장난감부터 정밀기계부품 제작에 이르기까지 널리 활용되고 있다. 3D 프린터의 기본적인 핵심 기능은 설계 도면상의 삼차원 치수 정보에 부합하는 정확한 출력물을 제작하는 것이다. 특히, 정밀공학분야에서 활용되는 3D 프린터의 경우에는, 다른 부품과의 정밀한 조립 공정을 고려하면 출력물 형상 치수에 대한 정확성 및 신뢰성 확보는 매우 중요한 요소이다.1-3
국제적으로 통용되는 형상 치수의 정확성 및 신뢰성을 확보하기 위해서는 SI 단위계를 통한 소급체계를 구축해야 한다. 측정물의 형상 치수에 대한 소급성은 길이 표준의 SI 단위인 미터(Meter)의 정의로부터 얻을 수 있으며, 안정화 레이저를 이용한 간섭계를 통해 구현할 수 있다. 일반적인 산업 현장에서는 이와 같이 복잡하고 엄격한 소급체계를 상시 유지할 수 없기 때문에, 주기적인 교정을 통해 측정물의 정확성 및 신뢰성을 확보할 수 있다. 또한, 이동이 어려운 측정 장비의 경우에는 표준 인증 물질 혹은 기준 시편을 통해 교정을 수행할 수 있다.4
3D 프린터는 기존의 전통적인 기계 가공 장비로는 제작이 어려운 복잡한 형상을 제작하는데 유용하다. 반면, 이와 같은 3D 프린터의 출력물은 내부 구조, 비정형 곡면, 거친 표면 등으로 인해 기존의 측정 방법으로는 대응하기 어려울 뿐만 아니라, 이를 통한 출력물의 객관적인 평가도 불가능하다. 이는 수많은 3D 프린터 제조사에서 제공하는 장비 제원상의 핵심 성능 지표에 대한 신뢰성을 저하시키는 결과를 가져오며, 사용자가 규격화되지 않은 제한된 성능 지표만으로 제품을 선정하게 되는 위험 요인이 발생하게 된다. 마찬가지로, 3D 프린터 제조사들도 자사 제품이 타사 제품에 비해 가지는 상대적인 성능 우위를 부각시킬 수 있는 객관적인 성능 평가 지표를 사용자에게 제시하기 어려우며, 객관화되지 않은 성능 평가 지표로는 제품 개선을 위한 연구 개발의 방향을 설정하기도 어렵다. 현재, Fig. 1과 같이 제한적으로 3D 프린터의 출력 성능을 확인하기 위해, 다양하고 복잡한 형태의 패턴들이 포함된 테스트 시편들이 널리 보급되고 있지만, 이를 통해 출력되는 출력물의 형상과 모양만을 확인할 뿐 정량적인 평가를 하기에는 한계가 있다.1,2,5
현재 다양한 3D 프린터의 출시와 함께 성능에 대한 시험평가 수요가 생겨나고 있지만, ISO와 같은 국제 표준 기구의 활발한 논의에도 불구하고, 아직 구체적으로 성능 평가를 위한 측정 방법론이 보고되지 않고 있다.6 본 연구는 1) 길이 표준으로부터 소급체계가 연결된 기존의 평가 방법을 최대한 활용하여 3D 프린터 출력물의 형상 치수 관련 시험평가에 일차적으로 대응하고, 2) 향후 확립될 3D 프린터의 형상 치수 표준을 구현하기 위한 기초 연구로서 수행되었다. 물론 기존의 소급체계를 활용함으로 인해 일반적인 3D 프린터 출력물에 대한 형상 치수 관련 모든 이슈에 대응하기는 어렵지만, 본 논문에서 제안하는 이차원 홀 플레이트(2D Hole-Plate) 및 삼차원 홀 플레이트(3D Hole-Plate) 기준 시편을 통해 홀의 중심 위치 정밀도, 홀의 지름 정밀도, 홀의 진원도에 대한 측정을 수행함으로써 3D 프린터에 대한 가장 기본적인 형상 치수 성능을 평가하고자 한다.
2. 홀 플레이트 기준 시편의 설계 및 제작
3D 프린터의 출력 성능을 평가하기 위한 출력물의 형상 치수측정 방법은 매우 다양하다. 그 중 3D 프린터의 출력물 크기와 정밀도, 측정 효율성을 고려하였을 때, 이를 측정할 수 있는 표준 장비는 공구 현미경이 가장 적합하다. 공구 현미경은 고배율 렌즈를 사용하여 얻은 시편 이미지로부터 치수를 결정하는 방법으로 측정하는 장비이다.
본 연구에서는 길이 표준 측정 장비인 공구 현미경을 활용하여, 3D 프린터 출력물의 형상 치수 측정에 대응하기 위해 Fig. 2와 같은 이차원 및 삼차원 홀 플레이트 기준 시편(이하 이차원 및 삼차원 시편)을 제안한다. 특히, 공구 현미경을 이용하여 대상물을 정확하게 측정 하기 위해서는 모서리 선정이 매우 중요한데, 상기 시편은 원형 대칭인 홀(Hole)을 이용하여 모서리 선정에서 생길 수 있는 측정 불확도를 최소화하여 중심 좌표를 측정할 수 있는 형태로 설계되었다. 선형 치수(가로 길이, 세로 길이, 높이)를 확인하기 위해 홀 중심 좌표 사이의 거리를 이용할 수 있으며, 선형 치수의 복합적인 성능(XY 평면, YZ 평면, XZ 평면)을 검증하기 위해 홀의 진원도를 이용할 수 있다.
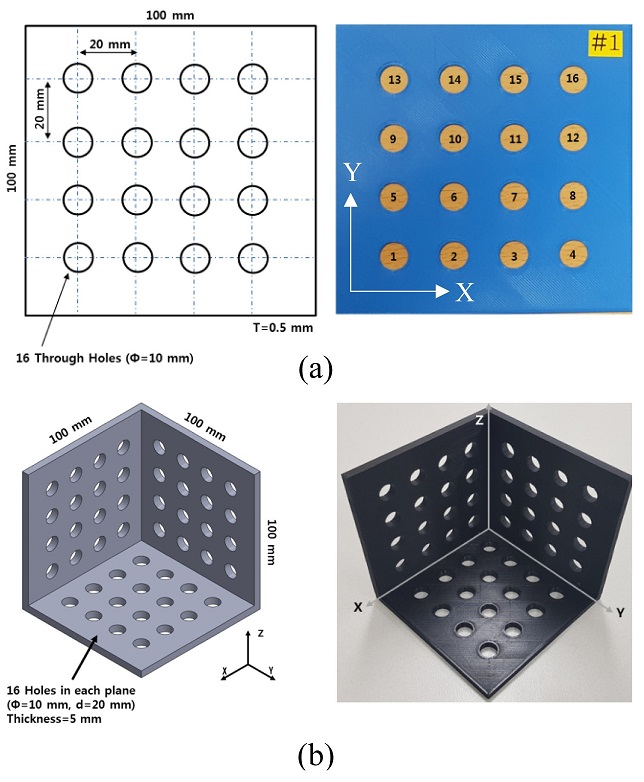
Design and fabrication results of hole-plates for estimating dimensional performance on 3D printers (a) 2D hole-plate, and (b) 3D hole-plate
우선, 홀 플레이트의 크기는 일반적으로 많이 사용되고 있는 타입의 3D 프린터에 적용 가능하도록 시판되는 3D 프린터의 출력 가능 영역을 고려하여, 이차원 시편의 경우에는 가로(X) 100 mm, 세로(Y) 100 mm로 선정하였고, 삼차원 시편의 경우 가로(X) 100 mm, 세로(Y) 100 mm, 높이(Z) 100 mm로 선정하였다. 홀의 지름 또한 보급형 3D 프린터의 출력 정밀도를 고려하여 10 mm로 선정하였다. 이는 홀의 지름이 작은 경우 3D 프린터의 출력 정밀도를 판단할 수 있는 객관적인 기준이 될 수 있으나, 일반적인 소재 압출(Material Extrusion, ME) 방식(또는 융착 조형(Fused Deposition Modeling, FDM)방식)의 3D 프린터의 출력 정밀도를 고려하여 결정하였다. 홀의 간격인 홀의 중심 좌표 사이의 거리는 가로 방향 및 세로 방향 모두 20 mm로 선정하였다. 두께의 경우, 출력 시간을 고려하여 이차원 시편은 1 mm, 삼차원 시편은 10 mm로 선정하였다. Figs. 2(a)와 2(b)에서 보듯이, 이차원 및 삼차원 시편의 각 면에서 홀의 지름 및 배열은 동일하게 설계하였다. 각 홀의 식별을 용이하게 하기 위해, Fig. 2(a)와 같이 각 면에서 좌측 아래부터 홀 번호를 1번부터 16번(우측 위)까지 부여하였다. 본 연구에서 제작된 홀 플레이트는 보급형 ME 방식의 3D 프린터(Ultimaker 3, Ultimaker)를 활용하여 출력하였고, 제조사에서 제공하는 분해능은 12.5 μm (X), 12.5 μm (Y), 2.5 μm (Z)이다. 본 논문에서 제안된 시편은 일반적인 ME 방식의 3D 프린터와 같이 와이어 형태의 재료를 사출 헤드로 압출하여 XY 평면상에 한 층씩 형태를 만들며 수직 방향(Z축)으로 적층하는 방식으로 제작되었다. 여기서 각 층은 XY 평면상에서 4겹의 컨투어(Contour)를 먼저 출력하고 45°의 래스터각(Raster Angle)으로 컨투어 내부를 채우는 방식으로 제작되었다.
3. 홀 플레이트의 측정 방법 및 측정 결과
본 연구는 기초 연구 단계로서 이차원 및 삼차원 시편 출력물의 형상 치수 성능을 평가할 수 있는 변수를 1) 홀의 중심 좌표, 2) 홀의 지름, 3) 홀의 진원도로 한정하였다. Fig. 3은 이를 평가하기 위해 사용된 공구 현미경(NEXIV VMR-H3030, Nikon)을 보여주며, 본 장비는 한국표준과학연구원 길이 표준 소급체계에 따라 교정되었다. 측정 영역은 300 mm (X), 300 mm (Y), 150 mm (Z)이다. 측정 분해능은 10 nm, 측정 정밀도는 전체 측정 영역에서 1.8 μm (X), 1.8 μm (Y), 1.9 μm (Z)이다. 그리고, 현미경 광학계로 측정할 수 있는 시야(Field of View)는 사용하는 대물렌즈의 배율에 따라 2배의 경우 2.33(X) × 1.75(Y) mm부터 30배의 경우 0.155(X) × 0.117(Y) mm까지 조절할 수 있다. 제안된 홀 플레이트의 형상 치수 변수들은 공구 현미경에서 획득된 이미지로부터 각 홀 경계 영역에서의 밝기 프로파일을 분석하여 결정됩니다.
측정 변수 중 홀의 지름과 중심 좌표의 경우, Fig. 4와 같이 서로 다른 4개의 지점(원의 좌측, 우측, 상측, 하측)에서 200개의 데이터(붉은색)를 획득하여, 총 800개의 데이터를 최소 자승법(Least Square Method)을 활용하여 원 맞춤(Circular Fitting, 파란색)을 수행하였다. 이때, 대물렌즈의 시야의 한계로 전체 원을 한번에 측정할 수 없었으며, 측정의 효율성을 높이기 위해 원의 일부 영역에서만 데이터를 얻는 것으로 연구를 진행하였다. 4개의 지점 위치는 기본적으로 홀 중심 위치를 기준으로 좌측, 우측, 상측, 하측으로 설정하였으나, 해당 위치에서 제작된 홀의 경계가 매끄럽지 않은 경우 근방으로 위치를 바꿔서 데이터를 획득하였다. 총 800개의 충분한 데이터를 바탕으로 원 맞춤에 근거하여 측정 변수를 결정하기 때문에, 일부 획득 지점 변경이 측정 변수 결정에는 큰 영향을 주지 않음을 확인하였다. 위의 방식으로 얻어진 원의 중심을 홀의 중심 좌표(Xc, Yc)로, 원의 지름을 홀의 지름(D)으로 정의하였다.
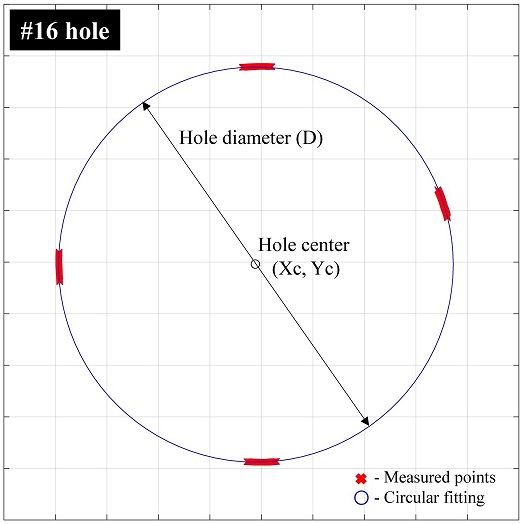
Definition of a center point and a diameter of each hole (This is an example of the #16 hole on the 2D hole-plate.)
진원도는 원이 얼마나 이상적인 원에 가까운지를 정량적으로 나타내는 값이다. Fig. 5와 같이 측정 데이터(Circular Element, 검은색)를 원 맞춤을 수행하면, 동일한 중심을 가지면서 측정 데이터를 포함하는 최소 외접원(Minimum Circumscribed Circle, 붉은색)과 측정 데이터 내에 포함되는 최대 내접원(Maximum Inscribed Circle, 파란색)이 존재한다. ISO/TS 12181에 따라, 외접원과 내접원의 반지름 차이를 진원도 오차(Circularity Error)로 정의한다.7-9
본 연구를 위해 출력물 재료로는 ME 공정에서 일반적으로 많이 사용되고 있는 PLA (Poly Lactic Acid)가 사용되었으며, 시편 제작 시 3D 프린터의 베드(Bed)에 접착제를 얇게 도포한 뒤 출력하였다. 삼차원 시편의 경우, XY 평면, YZ 평면, XZ 평면에 대해 이차원 시편을 측정하는 것과 같은 방법으로 측정을 수행하였다. 공구 현미경의 측정 원리상, 삼차원 공간 좌표 및 각 축에 대한 직각도에 대해서는 실질적으로 측정하기 어려움이 있다.
Fig. 6은 이차원 홀 플레이트 시편의 홀 중심 좌표의 위치 오차를 나타낸다. 홀 위치와 간격에 비해 오차가 매우 작은 값이기 때문에 각 홀에서의 오차는 50배 확대하여 표현하였다. 좌측 하단에 위치한 1번 홀의 중심 좌표(0, 0)를 기준으로 Fig. 4와 같이 측정된 각 홀의 중심 좌표가 설계된 위치(파란색 원의 중심)로부터 어느 정도 오차를 가지는지(빨간색 화살표)를 도식화한 결과이다. Fig. 6에 나타낸 결과에 따르면, 가장 큰 오차를 가지는 것은 우측 상단에 위치한 16번 홀이며, X, Y축 방향으로 각각 -220 μm, -78 μm의 오차를 보인다. 실제 중심 위치의 이동 거리로 환산했을 때 오차는 233 μm이며, 이는 기준인 1번 홀 중심 좌표부터 16번 홀 중심 좌표까지의 설계된 거리인 84.853 mm 대비 -0.27%에 해당한다. 이는 온도 제어가 되는 챔버가 없이 출력된 시편이 상온에서 식으면서 시편의 형상 수축이 생긴 것으로 추정할 수 있다. 본 오차가 일정한 값으로 반복적으로 발생한다면, 이를 교정하여 출력물의 형상 치수 오차를 줄여나가거나 사용하는 재료에 따라 온도 제어가 가능한 챔버가 구비된 3D 프린터를 사용함으로써 치수 오차를 줄여나갈 수 있을 것으로 판단된다.
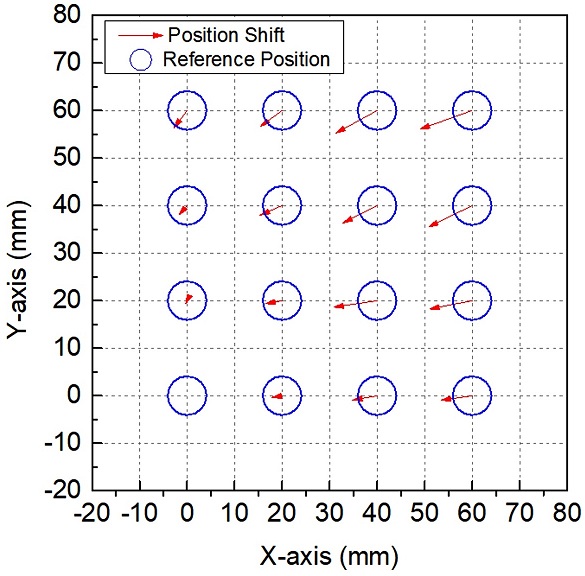
Position error map of holes on 2D hole-plate (The scale of the position error arrows was magnified 50 times.)
Table 1은 이차원 시편의 각 홀에 대한 지름과 진원도 오차를 정리한 표이다. 각 홀의 지름의 경우 설계치는 10 mm이지만, 홀의 평균 지름이 9.37 mm로 측정되었다. 따라서, 이차원 시편의 홀들은 원하는 설계치에 비해 약 0.63 mm(-6%)가 작게 출력되었으며, 이는 무시하기 어려운 수치로 해당 값을 활용하여 외각선에 대한 보상을 수행할 수 있다. 또한, 각 홀의 평균 진원도 오차는 0.069 mm로 측정되었고, 이는 10 mm인 지름의 약 0.7% 수준의 변동을 갖는 원이 출력되었음을 의미한다. 홀 지름의 경우 출력 후 시편이 상온에서 식으면서 생기는 수축에 기인한다고 예측할 수 있으며, 진원도 오차의 경우 3D 프린터의 X , Y 방향 정밀도에 의해 기인한다고 예측할 수 있다. 수축에 의한 영향이라고 가정해 볼 때, 홀의 중심 좌표나 진원도 오차보다 홀의 지름 오차가 월등히 큰 것은 보급형 3D 프린터의 한계로 볼 수 있다.
삼차원 시편의 경우, XY 평면, YZ 평면, XZ 평면에 대해 앞선 이차원 시편과 같은 방법으로 측정 및 분석을 수행하였다. Fig. 7은 Fig. 6의 결과와 같은 방법으로 삼차원 시편의 각 평면상에서 측정된 홀의 중심 좌표에 대한 위치 오차를 나타낸다. 이 그래프도 홀 위치와 간격에 비해 오차가 매우 작은 값이기 때문에 각 홀에서의 오차는 50배 확대하여 표현하였다. 각 홀의 중심 좌표의 최대 오차는 274.8 μm (XY 평면), 294.5 μm (XZ 평면), 167.2 μm (YZ 평면)이며, 이는 약 0.5% 수준의 오차이다. 이는 이차원 시편 보다 약 3배 이상의 큰 값을 가지는데, 삼차원 시편의 경우 이차원 시편에 비해 각 출력 평면의 두께가 두껍고, 세 면이 서로 연결되어 수축되면서 비교적 큰 수준의 공간적 오차를 발생시키는 것으로 판단된다.
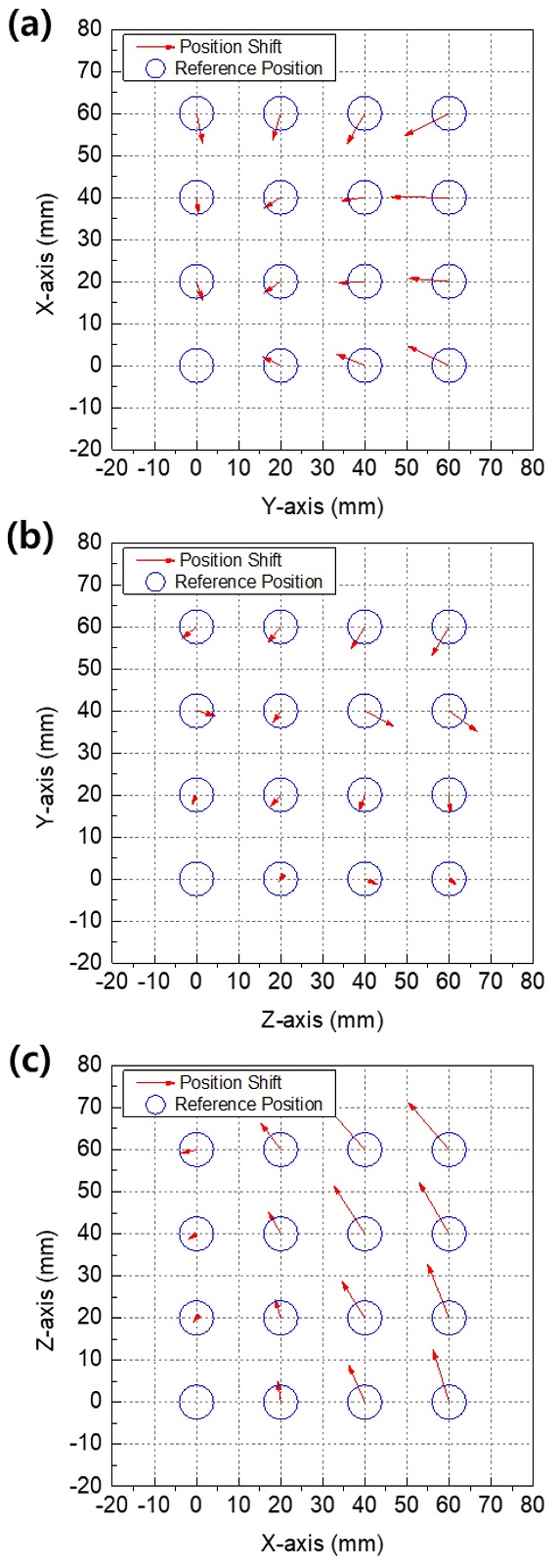
Position error map of holes on 3D hole-plate (a) XY plane, (b) YZ plane, and (c) XZ plane (The length of the position error arrows was magnified 50 times.)
삼차원 시편의 홀 평균 지름 오차는 -3.2%(XY 평면), -1.0%(XZ 평면), -1.5%(YZ 평면)를 갖고 있으며, 열 수축에 의해 모두 설계치보다 작은 값을 가진다. 특히 수직으로 쌓는 XZ 평면 및 YZ 평면보다는 수평인 XY 평면에서 약 3배 이상의 홀 지름 오차를 가지고 있었다. 이는 출력 특성상 연속적으로 제작하는 XY 평면에서 열 수축 영향이 큰 것을 알 수 있다. 진원도 오차의 경우에는 1.3%(XY 평면), 1.6%(XZ 평면), 2.5%(YZ 평면)로 나타났고, 이는 수직으로 쌓는 특성상 XY 평면보다는 XZ 평면 및 YZ 평면의 진원도가 저하되었다. 이는 Fig. 8의 삼차원 시편 상의 홀의 여러 위치에서 얻은 출력 단면으로부터 확인할 수 있다. 삼차원 시편의 경우, 4겹의 컨투어로 형성되는 XY 평면의 홀과 달리 XZ 평면, YZ 평면의 홀은 Z 방향을 따라 여러 층을 쌓아 올려 생성하기 때문에 평균 지름 오차와 진원도 오차 양상을 달리함을 확인할 수 있다.
4. 결론
본 연구는 홀 플레이트라는 하나의 예를 통해 3D 프린터의 형상 치수 구현 성능을 간단하면서도 합리적으로 평가하고 객관화시키기 위한 기초 연구로 진행되었다. 이를 위해, 이차원 및 삼차원 홀 플레이트를 기준 시편으로 제안하였고, 보급형 3D 프린터들의 출력 영역을 고려하여 각 시편들의 크기를 선정하였다. 제작된 홀 플레이트에서 홀의 중심 좌표, 지름, 진원도를 3D 프린터 성능 평가를 위한 측정 항목들로 선정하였고, 길이 표준 소급체계에 의해 교정된 공구 현미경을 사용하여 획득한 샘플 이미지 분석을 통해 각각의 항목들을 측정하였다.
측정 결과에 따르면, 이차원 시편과 삼차원 시편 모두 온도 제어용 챔버가 없는 보급형 ME 방식의 3D 프린터를 사용하여 출력하였기 때문에 열 수축으로 인한 형상 치수 변화가 가장 두드러지게 나타남을 확인할 수 있었다. 이차원 시편의 경우, 특히 홀의 지름에 대한 오차가 다른 항목에 비해 상대적으로 크게 나타났다. 삼차원 시편의 경우, 출력면에 따라 오차의 크기 차이를 보였는데, 지름 오차에 있어서 XY 평면의 오차가 XZ 평면, YZ 평면의 오차보다 3배 이상 크게 나타난 반면, 진원도 오차의 경우, XY 평면의 오차가 X Z 평면, YZ 평면의 오차에 비해 작게 나타난 것을 알 수 있었다. 이는, 3D 프린터 제작물에 있어서 열 수축 영향뿐만 아니라 출력 방향에 따른 영향이 크게 작용함을 보여주는 결과라고 판단된다.
본 연구는 추후 산업계와의 교류를 통해 보다 실용적이고 실효성 있는 3D 프린터 평가용 기준 시편을 개발하기 위한 시작점으로써, 표면 거칠기, 단차, 직각도 등에 대한 평가까지 종합적으로 고려함으로써, 국제표준기구를 통해 제정될 3D 프린터의 출력 성능 평가 및 새로운 장비/소재 개발을 위한 표준 측정법을 구현하는데 필요한 기초연구자료로서 유용하게 사용될 것으로 기대한다.
Acknowledgments
본 연구는 한국표준과학연구원 '1-2-01. 광학 측정표준기술 고도화 과제(No. 20011030) 및 산업통상자원부 산업소재기술개발사업 과제(No. 10051680)의 지원으로 수행되었습니다.
REFERENCES
-
Thompson, M. K., Moroni, G., Vaneker, T., Fadel, G., Campbell, R. I., et al., “Design for Additive Manufacturing: Trends, Opportunities, Considerations, and Constraints,” CIRP Annals, Vol. 65, No. 2, pp. 737-760, 2016.
[https://doi.org/10.1016/j.cirp.2016.05.004]
-
Adam, G. A. and Zimmer, D., “Design for Additive Manufacturing-Element Transitions and Aggregated Structures,” CIRP Journal of Manufacturing Science and Technology, Vol. 7, No. 1, pp. 20-28, 2014.
[https://doi.org/10.1016/j.cirpj.2013.10.001]
-
Choi, S., Bae, Y., Lee, I., and Kim, H., “Latest Research Trends of 3D Printing in Korea,” Journal of the Korean Society for Precision Engineering, Vol. 35, No. 9, pp. 829-834, 2018.
[https://doi.org/10.7736/KSPE.2018.35.9.829]
- Maeng, S. R., Jin, J. H., Buajarern, J., Kim, J. W., Kim, J. A., et al., “Design and Fabrication of a Step Height Certified Reference Material for Multi-Probe Inspection Instruments,” Journal of the Korean Society for Precision Engineering, Vol. 28, No. 3, pp. 323-329, 2011.
-
Moylan, S., Slotwinski, J., Cooke, A., Jurrens, K., and Donmez, M. A., “An Additive Manufacturing Test Artifact,” Journal of Research of the National Institute of Standards and Technology, Vol. 119, No. 1, pp. 429-459, 2014.
[https://doi.org/10.6028/jres.119.017]
- Jin, J., Eom, S., Park, J., “Feasibility Study on Dimensional Standards of 3D Printer,” Proc. of the Spring Conference on Korean Society for Precision Engineering, p. 126, 2019.
- ISO 12181-1:2011, “Geometrical Product Specification (GPS)-Roundness–Part 1: Vocabulary and Parameters of Roundness,” 2011.
- ISO 12181-2:2011, “Geometrical Product Specification (GPS - Roundness–Part 2: Specification Operators,” 2011.
- JCGM 100:2008, “Evaluation of Measurement Data-Guide to the Expression of Uncertainty in Measurement,” 2008.
- MakerBot Thingiverse, “Test Your 3D Printer,” https://www.thingiverse.com/thing:704409, (Accessed 26 MAR 2020)
Senior engineer in Korea Research Institute of Standards and Science (KRISS). His research interest is optical metrology.
E-mail: sheom@kriss.re.kr
Principal research scientist in Korea Research Institute of Standards and Science (KRISS). His research interest is optical metrology.
E-mail: jungjae.park@kriss.re.kr
Principal research scientist in Korea Research Institute of Standards and Science (KRISS) and Professor in University of Science and Technology (UST). His research interest is optical metrology.
E-mail: jonghan@kriss.re.kr
Principal researcher in Korea Institute of Industrial Technology (KITECH). His research interest is additive manufacturing process.
E-mail: sonyong@kitech.re.kr