
센터 타이로드를 적용한 대형 가스터빈 로터에서 운전 중 발생하는 타이 볼트 체결력 변동의 최소화 방법
Copyright © The Korean Society for Precision Engineering
This is an Open-Access article distributed under the terms of the Creative Commons Attribution Non-Commercial License (http://creativecommons.org/licenses/by-nc/3.0) which permits unrestricted non-commercial use, distribution, and reproduction in any medium, provided the original work is properly cited.
Abstract
The large gas turbine rotor used for power generation has a structural characteristic comprising a shaft, disk, and blade assembled to the disk. Because the start/stop is repeated, the tightening force may be reduced in the process of repeating the tightening force between the tie rod and the disk. When the tightening force falls below the threshold, changing the critical speed, increasing the vibration, or in extreme cases, the rotor may loosen and cause a major accident. Also, it is imperative to continuously maintain the proper tightening force because the thread of the tie rod is damaged when the tightening force exceeds the yield stress condition of the tie rod. In this paper, the gas turbine rotor system is modeled and simplified to identify the control variable of the tightening force of the tie rod bolts of the rotor. For verification, a simplified model of the gas turbine rotor was designed, manufactured, and verification tests were conducted to confirm the adequacy of the calculation method. As a result, the tightening force decreased as the stiffness of the pressing disk decreased, so the stiffness of the pressing disk should have a stiffness range similar to that of the tie rod.
Keywords:
Gas turbine rotor system, Center tie-rod rotor, Tightening force minimizing, Disk tightening force validation, Tightening force due to displacement키워드:
가스터빈 로터, 센터 타이로드 로터, 체결력 최소화, 디스크 체결력 검증, 변위로 인한 압착력1. 서론
발전용으로 사용되는 대형 가스터빈은 시동에서부터 전출력 상태까지 도달하는데 10-20분 정도밖에 소요되지 않기 때문에 전력 사용량의 변동이 매우 심한 현대사회의 전력 부하에 적합하다.1-9
발전용으로 사용되는 대형 가스터빈은 빠른 기동 특성, 구조적 특이성 및 높은 온도 조건으로 인해 기계설계 관점에서 매우 높은 난이도가 요구되고, 안정성이 매우 강조되는 회전 기계이다.10,11 또한, 가스터빈의 성능은 가격을 결정하는 중요한 요소이고, 이와 더불어 운전 신뢰성 및 운전 안전성도 매우 중요하기 때문에 설계 과정에서 이를 높이기 위한 여러가지 기술들을 적용한다.10-13
가스터빈의 로터는 크게 회전축(Shaft), 회전디스크(Disk), 디스크와 결합되는 회전날개(Blade)로 구성되어 있고 이들 각각의 특성에 연성 관계가 고려된 복잡한 구조를 갖는다. 이 로터의 회전축과 디스크들을 몇 가지 방법을 통해 조립하여 완전하게 구조적으로 일체화된 로터와 같은 상태로 만들어 사용해야 한다.14
대형 가스터빈에는 유럽의 원천제작사(Original Equipment Manufacturer, OEM) Siemens를 중심으로 센터타이로드(Central Single Tie Rod) 방식의 로터가, 그리고 미국의 원천제작사 GE와 일본의 원천제작사인 MHPS를 중심으로 멀티타이로드(Multiple Tie Rod) 방식의 로터가 적용되고 있다(Fig. 1).15
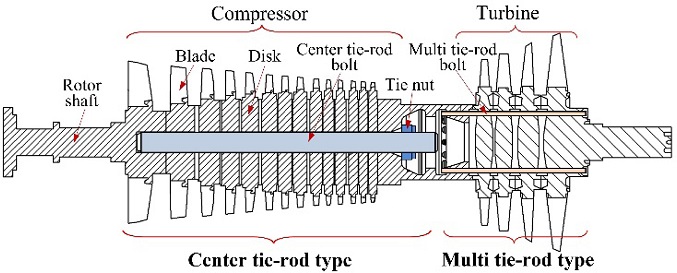
Concept of integral assembly method of rotor shaft and disks15 (Adapted from Ref. 15 on the basis of OA)
특히, Fig. 2에서 보여주는 바와 같이 기동(Start-Up)→정상운전(Steady-State)→정지(Shut-Down) 운전 과정 중에 0-3600 rpm 까지의 회전 속도 변화와 1500oC 이상까지의 온도 변화를 경험하게 된다.
이 과정 동안에 로터의 디스크, 블레이드, 고정체의 열용량의 차이와 회전 속도의 변화에 따라 시간에 따른 반경 방향(Radial)으로의 변형량과 축 방향(Axial)으로의 변형량이 서로 다르게 된다.
따라서, 로터의 블레이드를 포함한 회전부와 케이싱(Casing)에 연결된 베인(Vane)을 포함한 고정체(Stator)와의 간극은 회전 속도 및 연소기 열 출력 변화에 따라 변화하게 되므로 이를 충분히 고려하여 반경 방향 조립 간극(Radial Clearance)과 축방향 조립 간격(Axial Clearance)을 결정해야 한다.14,16,17
그런데, 기동/정지를 반복함에 따라 타이로드와 디스크 간 상대 변위 값이 최대-최소를 반복하는 과정에서 체결력이 감소할 수 있다.16-20
이 체결력이 임계치 이하로 떨어지면 위험 속도를 변화시켜 진동이 증가하거나, 극단적인 경우 로터가 풀려서 큰 사고를 유발할 수도 있다. 또한, 체결력이 증가하여 타이로드의 항복응력 조건을 넘어서면 타이로드의 나사산 또는 타이로드가 손상될 수 있기 때문에 적절한 체결력을 지속적으로 유지시키는 것이 대단히 중요하다.
기존에는 타이로드 소재의 기계적 강도 특성을 적용하여 최대 체결력 조건에서 타이로드가 항복(Yield)되지 않도록 설계하고 있으나, 실제의 경우 타이로드의 항복뿐만 아니라 나사의 풀림 현상이 우려되어 매 정비시마다 체결 상태를 확인한다.
본 논문에서는 Fig. 3에서 보여주는 바와 같은 센터 타이로드(Central Tie-Rod)를 적용하는 로터의 운전 건전성을 높이기 위해 타이볼트의 체결력에 영향을 주는 설계 변수를 도출하여, 설계 변경을 통해 체결력의 변화를 최소화하는 방안을 제시하고 그 방안의 타당성을 해석 및 실험을 통하여 검증하고자 한다.
2. 센터타이로드 로터의 체결력
2.1 체결력의 영향 요소
실제적으로 체결력의 변화는 타이로드와 전체 디스크와의 상대 변형량에 의해 결정되는데, 이 상대 변형량은 회전 속도의 변화에 따른 원심력의 변화에 기인하는 반경 방향 및 축 방향으로의 변형량과 타이로드와 디스크의 온도 차이에 의해 발생하는 열 팽창량의 변화로부터 계산할 수 있다.
그런데, 원심력에 의한 변형량은 비교적 쉽게 계산이 되지만, 열 변형량 계산의 경우는 온도 분포가 각 구성품의 위치와 역할에 따라 3차원적으로 모두 다르며, 각 운전 상황에 따른 성능 설계 및 2차 유로에 의한 냉각 설계에 영향을 받으므로, 설계 과정에서 많은 반복 계산 과정을 통해 점차 수렴되어져서 최종적으로 결정되기 때문에 계산이 결코 쉽지가 않다.
Fig. 4는 Siemens사의 V84.3A 모델(170 MW, 3600 rpm) 가스터빈에서 기동 과정에서 정지 과정까지의 운전 사이클 동안의 체결력의 변화에 따른 타이로드 응력의 변화를 나타낸 것이다. 21
Fig. 4를 살펴보면, 초기 조립시의 체결력은 대략적으로 항복응력(Yield Stress)의 50% 수준이며, 운전을 시작하면 초기에 회전 속도가 증가함에 따라 원심력에 의해 로터가 반경 방향으로 늘어나는 방향으로 변형하게 되므로 축 방향은 일시적으로 프아송 비(Poisson’s Ratio)만큼 변형하게되어 체결력이 줄어들게 되므로 응력이 5%정도 낮아진다.
이후부터는, 연소열에 의해 가열이 진행되게 되므로 열 변형이 주도적으로 작용하여 열용량의 비율만큼의 변형량 차를 발생시켜 최대 60% 정도까지 증가하게 되고, 시간이 충분히 지나서 정상 상태에 도달하면 초기값인 50% 수준으로 복귀하게 된다. 과도 운전 상태 중에 비상 정지(Trip) 되는 경우에는 65% 정도까지 증가하게 된다. 또한, 정지 과정에서는 8% 정도의 응력 감소 변동을 나타낸다.
결과적으로, 운전 사이클 과정에서 대략적으로 항복응력의 45-60% 정도까지의 체결력의 변화를 반복하게 될 것이다. 따라서, 이 응력 변화 사이클을 감안하여 타이로드의 피로 수명을 계산하여야 한다.21,22
Fig. 5는 실제 가스터빈 설계 과정 중에 계산된 결과의 일부로, 운전 과정 중에 디스크와 타이로드의 온도 차와 회전 속도의 변화에 따른 체결력의 변화를 계산한 결과중의 하나이다(온도 기준은 디스크와 타이로드의 평균온도임).
Fig. 5는 실제 270MW급 가스터빈이 운전 중에 정지하였다가 다시 기동하는 열간 기동 과정(Hot Start Condition)에서의 온도 편차의 변화와 체결력의 변화를 보여주고 있다. 실제 체결력의 변화는 운전 사이클 과정에 따라 변화하게 되며, 일반적으로 열간 기동 과정에서 가장 큰 변화를 보인다.23-25
Fig. 5의 결과는 Fig. 4의 결과와 유사한 경향을 보이고 있다. 즉, 정지 과정에서 체결력이 낮아졌다가 다시 복귀되고, 다시 기동하게 되면 원심력의 영향이 빠르게 나타났다가 열 변형의 영향이 커져서 110%까지 체결력이 증가했다가 시간이 경과함에 따라 안정하게 된다.
전체 경향성은 온도 편차가 주도적인 역할을 하고 있음을 확인할 수 있고, 3600→0 rpm , 또는 0→3600 rpm으로 급속히 회전 속도가 변화하면 그에 따라 즉시 원심력의 영향이 나타남을 알 수 있다.
전체 운전 사이클 동안 약 35%정도의 체결력 변화를 보여주고 있다.
2.2 제어 요소의 선정
타이로드의 체결력, 즉 타이로드에 걸리는 응력에 영향을 주는 요소는 회전 속도, 타이로드와 디스크의 소재의 열 특성에 직접적인 영향을 받게 되며, Fig. 6(a)에서 보는 바와 같이 구조적 관점에서는 디스크와 타이로드를 동시에 지지하는 압착디스크가 영향을 줄 수 있음을 알 수 있다.26
Fig. 6(a)의 로터 구조에서 변위와 관련한 정적(Static) 특성만을 본다면 가속도항(Acceleration Term)과 속도항(Velocity Term)을 무시할 수 있으므로 각 디스크와 타이로드의 질량(Mass)과 댐핑(Damping)은 의미가 없어지고 스프링만 남게 된다. 따라서, 질량과 댐핑을 제외하여 디스크와 타이로드를 스프링으로 간략화하면 Fig. 6(b)와 같이 모델링 할 수 있다.
여기서, 각 디스크와 타이로드는 온도와 변위가 변화 요소이므로 Fig. 7(a)와 같이 각각 온도와 변위를 가지는 스프링 요소로 모델링이 가능하다.
본 연구의 목적이 체결력의 변화를 최소화할 수 있는 방안이 무엇인지에 관심이 있으므로, 모두 동일한 온도 조건에서도 그 결과는 동일할 것이므로 온도를 동일(즉, T(i) = const.)하게 주고, 각 디스크와 타이로드의 스프링을 통합하여 등가 모델로 간주하면 Fig. 7(a)는 Fig. 7(b)와 같이 모델링의 간략화가 가능하다.
(1) |
(2) |
그런데, 각 디스크의 재질은 응력 조건과 수명 조건에 의해 결정되기 때문에 변형량 조절을 위해 임의로 바꾸는 것이 매우 어려우므로, 결국은 타이로드의 재질과 압착 디스크가 이용 가능한 제어요소가 된다.
또, 초기 체결력(Pre-Tightening Force)은 다음의 조건에 의해 결정한다.21
(1) 자중에 의한 굽힘 모멘트를 고려한 디스크 간 분리 모멘트(Separating Moment),
(2) 운전 중 블레이드 탈락(Blade Loss)에 의한 모멘트,27
(3) 발전기 SOP (Synchronization Out of Phase) 상황과 같은 과도 토크(Transient Torque),
(4) 고유진동수가 수렴(Natural Frequency Convergence)하는 조건의 체결력 조건
이렇게 결정된 체결력을 기준으로 하여 타이로드의 재질과 크기가 결정되므로, 실제적으로 타이로드 재질의 변경 과정은 쉽지 않다. 그러므로, 이미 설계된 디스크의 재질이나 타이로드의 재질을 변경하는 것을 고려 대상에서 제외해야 한다. 따라서, 본 논문에서는 체결력의 변화를 제어할 요소로 압착 디스크(Pressing Disk)를 선정하였다.
3. 체결력 변화의 최소화
Fig. 7(a)에서 xt의 변위 차가 발생하였다면, 각 디스크 변위의 총합에 압착 디스크의 변위가 더해진 값이며, 이는 타이로드의 총 변위와 같을 것이다. 따라서, 디스크에 대해서는 식(3), 타이로드에 대해서는 식(4)와 같이 표현할 수 있다.
(3) |
(4) |
여기서, α(i): i-번 디스크의 열팽창계수, αr(i): i-번 타이로드의 열팽창계수, Ta: 대기온도, m: 타이로드 수
본 연구의 목적인 체결력 변화의 최소화 관점에 집중하기 위해 디스크와 타이로드의 재질을 동일하게 하고, 온도 조건도 동일하게 해서 살펴보고자 한다.
소재와 온도 조건을 동일하게 α(i) = α = const., T(i)= T = const.하면 할 수 있는 방안이 무엇인지에 관심이 있으므로, 모두 동일한 온도 조건에서도 그 결과는 동일할 것이므로 온도를 동일하게 주면 즉, T(i) = const. 조건을 주고, 각 디스크와 타이로드의 스프링 통합하여 각각 하나의 등가 스프링(식(1), 식(2))으로 모델링을 간략화하면 Fig. 7(b)와 같다.
본 논문에서는 압착력의 변화를 줄이는 것이 설계 후에 로터의 동특성의 변동성을 줄여주는 것이므로 이 문제에 집중하여 논의한다. 즉, 이 변동성의 주원인이 운전에 의해 발생되는 원심력과 온도 차에 의해 발생되는 축 방향 상대 변위이므로, 축 방향의 상대 변위를 줄여주거나, 축 방향 상대 변위에 대응하는 강성으로 인한 압착력의 변화를 줄이면 된다. 따라서, 축 방향 상대 변위를 유발하는 온도 차와 회전 속도를 바꿀 수 없으므로, 역으로 강성을 바꾸자는 아이디어이다.
그러나, 강성 또한 디스크의 강성에 직접적인 영향을 주게 되므로 마음대로 작게 결정할 수 없다. 그래서, 핵심은 상대 변위를 줄이기 위해 다른 응력 조건이 허용하는 범위 내에서 디스크의 총 등가강성과 타이로드의 총 강성을 같은 수준으로 만들면 될 것이다.
체결력 선정의 전제 조건은 자중이나 블레이드 탈락에 의한 분리 모멘트, 발전기 고장에 의한 과도 토크, 그리고 고유진동수의 유지이다. 그리고, 타이로드의 체결에 의해 발생하는 인장응력이 항복응력의 50% 범위 내에 있도록 하는 것이다.
따라서, 이를 모두 만족시키려면 압착디스크의 강성이 타이로드의 강성과 비슷한 수준일 것이라는게 유추되는 결과이다. 현재 계산되어 설계한 타이로드는 앞의 전제 조건을 모두 만족하도록 선정되었으므로, 전제 조건에 대해서는 따로 계산하지 않고, 강성의 조절을 통해 문제를 해결해 보고자 한다.
Fig. 7(b)에서 타이로드를 유압식 볼트 조임 장치(Hydraulic Bolt Tightening Cylinder)를 이용하여 Ft를 작용시켜 xt의 변위를 주면, 디스크에도 같은 크기의 반력이 Ft의 크기로 작용하고 xt의 변위가 발생하게 된다. 이를 수식으로 정리하면 식(5)와 식(6)과 같다.
(5) |
(6) |
따라서, 볼트 조임에 의한 압착력과 반력의 크기가 서로 같아야 하고, 그 변위도 각각 동일하게 된다. 그러므로, 디스크의 등 가강성(Kdeq)과 타이로드의 강성(Krd)도 서로 같아야 하므로 식(7)과 식(8)과 같이 정리할 수 있다.
(7) |
(8) |
식(7)과 식(8)의 조건을 토대로 타이로드의 강성을 유추해보면 다음 식(9)와 같다.
(9) |
여기서, 디스크 강성과 타이로드 강성의 비율 Kds/Krd= ndr 이라면,
(10) |
(11) |
통상적으로 Kds/Krd = ndr = 5-10 정도이므로 정리하면,
(12) |
즉, ndr= 5일때, 압착디스크의 강성(Kpd)이 타이로드 강성에 비해 1.25배, ndr= 10일때는 1.1배 정도이면 상대위가 최소화가 될 것이다(식(12)).
실제 상용화된 가스터빈을 기준으로 살펴보면 각 강성 설계 기준은 Table 1에서와 같이 소재의 항복응력에 제한을 받게 되며, 대략 압착응력이 항복응력의 50% 수준임을 확인할 수 있다. 이는 각 디스크나 타이로드를 선정할 때 항복응력의 적절한 범위내에서 설계해야 함을 알 수 있다.
그런데, 실제적으로 압축기나 터빈의 디스크 각각의 강성은 타이로드의 강성에 비해 매우 큰 값을 가진다. 또한 압축기와 터빈의 디스크 전체의 등가강성(Kds)의 수준도 통상 타이로드 강성의 5배 이상으로 높으며, 일반적으로 압착력이 커지면 등가강성도 커진다.
3.1 운전 시 구성품 간 온도 차에 의한 체결력의 변동
실제적으로 체결력의 변화는 타이로드와 전체 디스크의 상대 변형량에 의해 결정되는데, 이 상대 변형량은 운전에 의해 발생되는 원심력과 온도 차에 의해 발생 되는데, 체결력 변동의 최소화 관점에서 실제 로터를 단순화한 축소 모델(Scaled Model)에 대해 해석용 모델 로터의 디스크(원통디스크, Disk Shell)에 온도 차를 발생시켜 각 압착디스크의 적용 조건별로 체결력의 변화를 해석적으로 확인해 보고자 한다. 해석용 모델은 Figs. 8과 9와 같이 실제 로터의 약 1/8 정도의 축소 모델로 타이로드, 원통디스크, 압착디스크 간의 강성비를 실제와 유사하게 모사하였다. 해석은 상용 해석 프로그램 인 ANSYS V19.2를 사용하였다.
Fig. 9에서 보여주는 서로 다른 강성을 가지는 4가지의 압착 디스크(Type A-Type D)에 대해 해석을 수행하고 실험으로 검증한다. 계산된 압착디스크 별 강성은 다음 Table 2와 같다.
Fig. 10은 해석 대상 로터의 원통디스크와 압착디스크의 온도차(기준온도 20oC와의 온도 차이)에 따른 압착력의 변화를 보여주고 있다. 즉, 압착디스크 형상에 따라서 강성이 서로 다르다. 따라서, 온도 차에 의한 변형이 같더라도 변형에 필요한 힘이 서로 다르게 되므로, 압착디스크의 강성의 변화가 압착력의 변화를 실현할 수 있음을 알 수 있다.
핵심 메커니즘은 Fig. 11에서 보여주는 바와 같이 온도 차에 의해 발생하는 축 방향 변위를 압착디스크가 변형하면서 높은 강성의 압착디스크보다는 낮은 강성의 압착디스크가 타이로드에 전달되는 변위를 줄여주기 때문에 상대적으로 강성의 변화가 적어지므로, 결과적으로 압착력의 감소 효과를 발생시킨다.
4. 실험 및 결과
해석 모델링 및 해석 결과의 정합성을 확인하기 위한 목적으로 4가지 모델(Fig. 9)의 압착디스크에서의 응력을 측정하여 해석 결과와 비교하였다. Fig. 12는 체결 응력 실험 장치를 보여주고 있다. 다수의 디스크를 등가강성을 갖는 원통으로 모사하고, 중앙에 타이로드를 설치하여 한쪽은 베이스 디스크에 고정하고 반대쪽 끝 부분에 압착디스크를 설치하여 Fig. 7(b)의 모델링과 동일하게 모사하였다. 로터 사양은 Table 3과 같다.
응력 측정을 위한 스트레인 게이지를 Figs. 8과 12에 나타낸 바와 같이 원통 중간 바깥면, 타이로드 표면과 압착디스크 평면부에 각각 설치하여 스트레인을 측정 하였고, 변위는 변위지시계(Digital & Analog Indicator)와 레이저 타입의 변위센서(Laser Displacement Sensor)를 이용하여 타이로드, 원통디스크, 압착디스크의 변위를 계측하였다. 실험에 사용한 센서 사양은 Table 4와 같다.
실험은 유압식 볼트 조임 장치의 공급 압력 변화를 이용하여 압착력을 인가할 때 각 센서 부위에서의 스트레인과 변위를 측정하는 방식으로 진행하였다.
모든 타입에 대해 실험을 실시하였으며, 모두 경향성이 유사하였다. 따라서, Table 5에 그 중 하나의 결과로 Type A의 결과만 표시하였다. 실험의 정밀도는 Table 5에 나타난 바와 같이 총 오차의 수준이 1-3%로 비교적 잘 일치하는 것으로 확인되었다.
발생 가능한 오차는 실험용 타이로드 및 디스크의 재질의 차이로 인한 소재 물성치의 차이와 기계가공 오차가 작용한 것이므로 제작 정밀도를 최대한 높이고, 제작 소재의 물성치와 해석 모델의 물성치 값을 반영하여 해석의 정밀도를 높였다. 실험 목적을 검증하기 위한 실험 정밀도 수준으로는 충분한 수준으로 판단된다.
5. 결론
발전용으로 사용되는 대형 가스터빈은 빠른 기동 특성, 구조적 특이성 및 높은 온도 조건으로 인해 운전 신뢰성 및 운전 안전성을 높이기 위한 여러가지 기술들을 적용한다. 본 논문에서는 센터 타이로드를 적용하는 로터의 운전 건전성을 높이기 위해 타이볼트의 체결력에 영향을 주는 설계 변수를 도출하여, 설계 변경을 통해 체결력의 변화를 최소화하는 방안을 제시하고 그 방안의 타당성을 해석 및 실험을 통하여 검증하였다.
센터타이로드를 적용한 로터의 운전 중 발생하는 볼트의 체결력 변동을 최소화 방법으로 압착디스크의 강성 변경을 통한 방법의 연구를 통해 다음과 같은 결론을 얻었다.
(1) 압착디스크의 형상을 변화시켜 강성 변경을 통하여 타이로드에 작용하는 압착력의 변화가 가능하다.
(2) 디스크 강성과 타이로드의 강성비가 통상 5 : 1 정도이므로 이를 고려하면 타이로드 강성과 압착디스크 강성의 비를 1 : 1.1-1.5 정도가 압착력을 최소화하는 범위로 추천된다.
(3) 해석 결과와 실험 결과가 비교적 잘 일치하므로 해석으로도 충분히 강성 변화 수준의 예측이 가능하므로 해석 결과를 적용하여 설계하여도 문제가 없다.
(4) 타이로드 압착력의 최소화를 통해 타이로드에 걸리는 최대 응력을 낮출 수 있으므로, 결과적으로 타이로드의 재질 수준을 낮추어 원가 절감이 가능하며, 타이로드의 직경을 감소시켜 터빈의 디스크 중심부에 걸리는 최대 응력을 감소시켜 설계의 유연성을 확보 측면에서 유리하다.
Acknowledgments
본 연구는 산업통상자원부(MOTIE)와 한국에너지기술 평가원(KETEP)의 지원을 받아 수행한 연구과제입니다(No. 2013101010170A).
REFERENCES
-
Pieper, C. and Rubel, H., “Electricity Storage: Making Large-Scale Adoption of Wind and Solar Energies a Reality,” Balanced Growth, pp. 163-181, 2012.
[https://doi.org/10.1007/978-3-642-24653-1_11]
-
Gülen, S. C., “Gas Turbines for Electric Power Generation,” Cambridge University Press, 2019.
[https://doi.org/10.1017/9781108241625]
- Kost, C., Mayer, J. N., Thomsen, J., Hartmann, N., Senkpiel, C., et al., “Levelized Cost of Electricity Renewable Energy Technologies,” Fraunhofer Institute for Solar Energy Systems ISE, Vol. 144, 2013.
- U.S. Energy Information Administration, “Annual Energy Outlook 2019 with Projections to 2050,” https://www.eia.gov/outlooks/aeo/pdf/aeo2019.pdf, (Accessed 12 MAR 2020)
-
Gonzalez-Salazar, M. A., Kirsten, T., and Prchlik, L., “Review of the Operational Flexibility and Emissions of Gas-and Coal-Fired Power Plants in a Future with Growing Renewables,” Renewable and Sustainable Energy Reviews, Vol. 82, pp. 1497-1513, 2018.
[https://doi.org/10.1016/j.rser.2017.05.278]
-
Lee, A., Zinaman, O., and Logan, J., “Opportunities for Synergy between Natural Gas and Renewable Energy in the Electric Power and Transportation Sectors,” National Renewable Energy Lab.(NREL), Golden, CO (United States), 2012.
[https://doi.org/10.2172/1060601]
- Byfield, S. and Vetter, D., “Flexibility Concepts for the German Power Supply in 2050: Ensuring Stability in the Age of Renewable Energies,” München: Acatech–Deutsche Akademie Der Technikwissenschaften, 2016.
- Fabiani, A., Adam, B., Bärbel, E., Duncan, G., Bozhil, Ko., Angus, M., et al., “Renewables in Cities 2019 Global Status Report,” https://www.ren21.net/wp-content/uploads/2019/05/REC-2019-GSR_Full_Report_web.pdf, (Accessed 12 MAR 2020)
-
Crabtree, G., Misewich, J., Ambrosio, R., Clay, K., DeMartini, P., et al., “Integrating Renewable Electricity on the Grid,” Proc. of the AIP Conference of American Institute of Physics, pp. 387-405, 2011.
[https://doi.org/10.1063/1.3653865]
- Bloch, H. P. and Geitner, F. K., “Practical Machinery Management for Process Plants. Volume 1: Improving Machinery Reliability,” Elsevier, 1988.
- Lee, A. S., “Rotor Dynamic Design Supervision for the Reliability of the Rotating Machinery,” Transactions of the Korean Society for Noise and Vibration Engineering, Vol. 8, No. 5, pp. 775-783, 1998.
- Kim, S. Y., Oh, G., Oh, G., Ahn, K., Cho, S., et al., “Conceptual Design of a Heavy Duty Gas Turbine Engine for Power Generation,” Korea Institute of Machinery and Materials, 1998.
- Cook, C. P., “Shop Vs. Field Corrections to Equipment,” Proc. of the 14th Turbomachinery Symposium on Texas A&M University, 1985.
-
Endres, W., “Rotor Design for Large Industrial Gas Turbines,” Proc. of the International Gas Turbine and Aeroengine Congress and Exposition of American Society of Mechanical Engineers Digital Collection, 1992.
[https://doi.org/10.1115/92-GT-273]
- Lee, S. E., “Gas Turbine with Plurality of Tie Rods and Method of Assembling the Same,” US Patent, 9951687B2, 2018.
- Bunker, R. S., “Cooling Design Analysis,” The Gas Turbine Handbook, pp. 296-308, 2006.
-
Lattime, S. and Steinetz, B., “Turbine Engine Clearance Control Systems: Current Practices and Future Directions,” Proc. of the 38th AIAA/ASME/SAE/ASEE Joint Propulsion Conference & Exhibit, p. 3790, 2002.
[https://doi.org/10.2514/6.2002-3790]
- Dean, G. J., and AccTTech, L., “Integrated Approach to Gas Turbine Rotor Condition Assessment and Life Management,” https://etn.global/wp-content/uploads/2017/11/21_EPRI_JS.pdf, (Accessed 12 MAR 2020)
-
Florjancic, S. S., Pross, J., and Eschbach, U., “Rotor Design in Industrial Gas Turbines,” Proc. of the International Gas Turbine and Aeroengine Congress and Exhibition of American Society of Mechanical Engineers Digital Collection, 1997.
[https://doi.org/10.1115/97-GT-075]
-
Fukue, I., Aoki, S., Aoyama, K., Umemura, S., Merola, A., et al., “A New High-Efficiency Heavy-Duty Combustion Turbine 701F,” Journal of Engineering for Gas Turbines and Power, Vol. 116, No. 2, pp. 389-394, 1994.
[https://doi.org/10.1115/1.2906832]
-
Janssen, M. J. and Joyce, J. S., “35-Year Old Splined-Disc Rotor Design for Large Gas Turbines,” Proc. of the ASME International Gas Turbine and Aeroengine Congress and Exhibition, 1996.
[https://doi.org/10.1115/96-GT-523]
-
Janssen, M., Seume, J., and Zimmermann, H., “The Model V84. 3 Shop Tests: Tip Clearance Measurements and Evaluation,” Proc. of the ASME International Gas Turbine and Aeroengine Congress and Exposition, 1994.
[https://doi.org/10.1115/94-GT-319]
- Han, D. W., “The Design and Experimental Verification of Rear Support Disk for Preventing Excessive Thermal Stress of Industrial Gas Turbine Rotor during Startup,” Ph.D. Thesis, Pusan National University, 2019.
- Annigeri, R. and Freeman, B., “Solution for Gas Turbine Rotor End of Life,” http://www.gten.ca/downloads/2017/papers/206paper.pdf, (Accessed 12 MAR 2020).
-
Rządkowski, R., Lampart, P., Kwapisz, L., Szymaniak, M., and Drewczyński, M., “Transient Thermodynamic, Thermal and Structure Analysis of a Steam Turbine during its Start-Up,” Proc. of the ASME Turbo Expo, 2010.
[https://doi.org/10.1115/GT2010-22813]
-
Jansen, M., Schulenberg, T., and Waldinger, D., “Shop Test Result of the V64. 3 Gas Turbine,” Journal of Engineering for Gas Turbines and Power, Vol. 114, No. 4, pp. 676-681, 1992.
[https://doi.org/10.1115/1.2906641]
-
Jiang, X. J., Zhang, Y. Y., and Yuan, S. X., “Analysis of the Contact Stresses in Curvic Couplings of Gas Turbine in a Blade-Off Event,” Strength of Materials, Vol. 44, No. 5, pp. 539-550, 2012.
[https://doi.org/10.1007/s11223-012-9412-3]
Ph.D. Principal Research Engineer in Doosan Heavy Industries. His research interest is Rotordynamics, bearing design, and vibration diagnosis of Turbomachinery.
E-mail: yeongchun.kim@doosan.com
Ph.D. Senior Research Engineer in Doosan Heavy Industries. His research interest is Machine and machine element design.
E-mail: dowon.han@doosan.com