
전기 자동차 2차 전지 셀 레이아웃에 따른 방열 성능 연구
Copyright © The Korean Society for Precision Engineering
This is an Open-Access article distributed under the terms of the Creative Commons Attribution Non-Commercial License (http://creativecommons.org/licenses/by-nc/3.0) which permits unrestricted non-commercial use, distribution, and reproduction in any medium, provided the original work is properly cited.
Abstract
This study is to investigate the cooling performance of the secondary battery in electric vehicles according to three different gaps between battery cells. To accomplish the convective cooling performance of the battery surface with three different gaps, selected local positions (X, Y, Z) for various temperature distributions were marked on the gap surface contacting the cell surface. The cooling performance of the gap of 0.5 mm was compared with the gaps of 5 mm, and 1 mm. Normalized local Nusselt number of the cooling area at the normalized width position indicated that the gap of 0.5 mm was on average 26.99% lower than that of 5 mm and 0.49% lower than that of 1 mm. At the normalized height, the gap of 0.5 mm was on average 12.12% higher than that of 1 mm. Because of the vortex at the outlet area, cooling performance at the gap of 0.5 mm was on average 13.19% higher than that of 5 mm and 0.79% higher than that of 1 mm at normalized thickness. Ultimately, the best cooling performance existed at the gap of 5 mm, but the gap of 0.5 mm was best for improving space efficiency, energy storage capacity, and vehicle-driving durability.
Keywords:
Secondary battery, Electric vehicle, Battery cooling, Battery Layout, Energy storage system, ESS, Virtual fluid dynamics, VFD키워드:
2차 전지, 전기 자동차, 배터리 방열, 배터리 레이아웃, 에너지 저장 장치, 가상유체역학1. 서론
최근 자동차 시장은 신재생에너지와 친환경적인 기술 개발을 관심사로 두고 있다. 고갈성 에너지원인 화석 연료 사용으로 인한 CO2, SO2, NOx 등이 지구 온난화와 각종 대기오염 문제에 영향을 끼치는 것을 막기 위하여 세계적인 자동차 업체들은 대표적인 재생 가능한 친환경 에너지인 전기를 활용한 전기자동차와 생산된 전기를 저장하는 시스템인 ESS (Energy Storage System) 시장으로 확산하고 있다.1 이처럼 ESS 시장이 최근 급성장하고 있지만, 잦은 화재 사고로 배터리에 대한 안전 관련 기술 확보가 시급한 상황이다.2 이러한 기술 동향 속에서 전기 자동차의 심장인 배터리 연구의 필요성은 더욱 중요시 해지고 있다. 배터리 성분은 니켈 카드뮴(Ni-Cd), 니켈 수소(Ni-MH)보다 에너지 밀도가 높고 효율이 우수한 리튬 이온(Li-ion)으로 이루어져 있다. 성능, 용량, 수명 등의 측면에서 본다면 리튬 이온 배터리가 에너지원으로 가장 적합하지만, 안전성의 문제점을 가지고 있다. 배터리는 충·방전시 전자와 원자 이온이 산화·환원 반응을 통하여 운동에너지 증가 및 화학적 에너지가 전기적 에너지로 서로 변환되면서 비가역 열과 가역 열이 발생한다.3 리튬 이온 전지는 특성상 충격과 고온에 약하기 때문에 고온에 장시간으로 노출되면 배터리의 수명이 짧아지고 심하면 열폭주 현상으로 폭발 사고로 이어지게 된다. 따라서 배터리와 같이 고전압 핵심부품들의 효율적인 열관리 기술은 전기구동 자동차에서 해결해야 할 중요한 과제이고 배터리의 내구성 향상 및 자동차 운전성 향상을 위해 전기 자동차 배터리의 방열 시스템에 대한 연구는 필수적이다. 이에 관한 기존 연구들은 원통형 배터리 팩의 냉각을 위해서 자연대류와 강제대류 방식을 비교한 연구,4 ESS의 기본 핵심 구조인 트레이 구조로 리튬이온 전지 열 유동 특성에 관한 연구,5 발열 집중 배터리에 대하여 효과적인 이유로 설계의 영향을 파악하기 위한 전기자동차용 배터리 팩 주위의 유동장 해석,6 전기자동차용 배터리 팩의 효율적인 냉각을 위하여 블로워를 이용하여 강제 송풍 시의 송풍량에 따른 냉각 성능을 배터리 모듈 입구 형상에 따라 수치 해석 연구,7 냉각판의 두께, 냉각판의 개수, 냉각판의 접촉 형태를 변수로 한 냉각 연구,8 전기자동차 배터리 냉각을 목적으로 상부 가열·하부 냉각식의 진동형 히트파이프에 대해 가열량, 냉각 온도, 충전량, 경사각 등 변수에 대한 연구,9 하우징 내부 냉각에 사용되는 유체의 유동을 분석하고 이를 원활히 하기 위해 배터리 모듈을 둘러싸는 하우징의 외형을 개선하고 공기 유입구의 위치와 팬의 위치를 조정하여 냉각 성능을 높이는 연구,10 레저용 소형차에 사용한 배터리 셀의 간격에 따른 열적 특성을 해석하여 자연대류에 의한 냉각 연구,11 배터리 셀에 자연대류 대비 강제대류 냉각 성능이 정량적으로 어느 정도 우수한지와 최적의 냉각 위치를 결정하는 연구12 등이 있지만 실제 차량용 배터리의 설계 간격에 관한 연구와 최적 간격의 배터리 방열 성능 연구는 거의 수행되지 않았다.
본 연구는 공기 블로워를 이용한 강제대류 방열 시스템에서 실제로 채택될 수 있는 배터리 셀의 간격을 5, 1, 0.5 mm 3가지로 분류하여 셀 간격별 내 온도를 수치적으로 해석하여 강제대류 열전달을 통해 위치별 방열 성능을 알아보고 방열 성능이 우수한 위치와 취약한 위치를 파악하고 또한 그 이유들을 알아내고 셀 간격에 따른 방열 성능을 비교하는 것이 이번 연구 목표이다.
2. 설계 및 수치 해석
Fig. 1은 글로벌 완성차 업체 ㈜T사 하이브리드 차량에 사용되는 Fig. 1(a)는 실제 배터리 팩 사진이고, Fig. 1(b)는 실제 배터리 셀의 사진이다. CAD 형상은 실제 차량의 배터리를 분해 및 실측하여 모델링을 하였다. Fig. 2(a)는 배터리 팩을 3D 모델링한 렌더링이며, Fig. 2(b)는 셀에 장착되는 볼팅부와 결합부, 플래쉬, 굴곡진 부분 등 유동 해석에 필요없는 부분을 제외하고 단순화시킨 형상이다. 셀 표면에 있는 플래쉬를 단순화한 이유는 최근 출시되는 배터리 셀은 가공 공정상의 복잡성과 신기술 개발 등의 이유로 방열 성능에 큰 차이가 없는 플래쉬를 제거하는 형태로 개발되기 때문에 단순화하였다. Fig. 3은 CATIA V5R21을 사용하여 모델링한 후 ANSYS V19.1로 형상을 대입한 전체 유동장과 배터리 셀의 형상이다. Fig. 3(a)의 입구와 출구 수정 형상은 입구의 안정화된 대기 유입의 표현과 출구로 방출되는 공기의 안정화 및 원활한 해석을 위해 셀 폭(X축)만큼 입구 1배, 출구 2배로 수정한 형상이며, 입·출구를 제외한 유동장과 셀 12개로 실제 형상을 나타냈다. 실제 제조 형상인 0.5 mm의 방열 성능이 어느 정도 우수한지 알아보기 위하여 실제 간격의 2배인 1 mm와 우수하게 방열될 수 있는 실제 간격의 10배인 5 mm로 분류하였고 F ig. 3 (b)는 셀 간격 5 mm, Fig. 3 (c)는 1 mm, Fig. 3 (d)는 0.5 mm(㈜S사 실제 설계 간격)이다. 좌표 방향으로는 셀 두께 방향(Y축), 셀 높이(수직) 방향(Z축), 셀 폭 (수평) 방향 (X축)으로 Figs. 3(b)부터 3 (d)와 같이 동일하게 설정하였다. 입·출구는 X축을 기준으로 동일한 수평선으로 설정하였다.
Table 1은 CATIA V5R21을 활용하여 배터리 셀을 모델링한 Fig. 2(b)와 ANSYS V19.1로 형상을 대입한 Fig. 3(a)의 제원 및 크기를 표로 나열한 것이다.
2.1 설계 조건
설계 조건은 유체 유동 및 열전달 해석을 위해서 질량 보존 법칙, 운동량 보존 방정식, 에너지 보존 법칙을 ANSYS CFX V19.1로 비압축성 유동 해석을 하였다. 배터리 셀 사이의 간격을 기준 길이로 설정하여 내부 유동의 최대 레이놀즈 수가 12,500으로 계산되어 난류 해석을 진행하였으며, 경계층 흐름에 대해 더 많은 계산을 수행하고 해석 결과의 정확도를 향상시키기 위해 k-omega standard 모델을 사용하였다.
초기 조건으로 유체(공기) 온도는 상온을 기준으로 하여 298.15 K를 부여하였고, 입구 속도는 글로벌 완성차 업체 ㈜T사의 차량 배터리 방열용 블로워 제원에서 확인한 유량 200CMH(Cubic Meter per Hour)을 활용하여 속도 8.75 m/s를 도출하였다. 출구는 대기압으로 가정하여 계기 압력 0 Pa을 부여하였다. 셀은 알루미늄 재질을 선정하였고, 표면에 점착 조건(No Slip Condition)을 주며 일정 열유속(Heat Flux) 조건을 열경계 조건으로 사용하였다. 유동장의 표면에는 Wall 조건, 점착 조건, 단열 조건을 설정하였다.
Table 2는 열 및 유동 해석을 위한 경계 조건들을 표로 나타낸 것이다.
2.2 격자 의존도 Test
배터리의 전체적인 형상에 비해 셀 간격(5, 1, 0.5 mm)은 좁으면서 점성 유동으로 인해 경계층 영역이 생기므로 조밀한 격자 생성이 중요하기 때문에 유동장을 분할하여 셀 간격들을 각각의 유동장으로 만들었다. 서로 다른 유동장의 격자를 이어주어 해석 진행에 영향이 없도록 하였다. 배터리 셀 간격의 형상은 평행 평판 유동이므로 셀 벽면에서 속도가 점착 조건으로 인해 0 m/s가 되고 셀 간격 중간에서 최고 속도가 나타난다. 속도를 나타내는 값으로 식(1)을 통해 계산할 수 있다.
(1) |
Vavg는 층류 유동에 대한 평균 속도, Umax는 X축 방향의 최고 속도이다. 간격의 속도 분포를 해석하기 위해 Vavg= 3 m/s, Umax= 4.5 m/s를 기준으로 격자 의존도 Test를 진행하였다.
격자 의존도 Test를 진행하기 위해서 셀 간격 격자를 0.5 mm에서 5, 10, 15, 20, 30개, 1 mm는 5 , 15, 20, 30, 40, 50개, 5 mm는 5 , 20, 30, 40, 50, 100개의 격자로 분류하여 진행하였다. 격자는 ANSYS Mesh를 사용하여 Edge Sizing과 Body Sizing으로 육면체 격자를 생성하여 진행하였다.
5 mm일 때, 30개 격자에서 Umax가 4.46 m/s, 오차율이 0.89%, 40개 격자는 4.49 m/s, 오차율 0.22%, 50개 격자는 4.495 m/s, 오차율 0.11%, 100개 격자는 4.498 m/s, 오차율 0.04%로 나타났다. 1 mm일 때, 20개 격자에서 Umax가 4.49 m/s, 오차율 0.22%, 30개 격자는 4.492 m/s, 오차율 0.178%, 40개 격자는 4.495 m/s, 오차율 0.11%, 50개 격자는 4.496 m/s, 오차율 0.09%로 나타났다. 0.5 mm일 때, 15개 격자에서는 Umax가 4.464 m/s, 오차율 0.8%, 20개 격자는 4.485 m/s, 오차율 0.33%, 30개 격자는 4.493 m/s, 오차율이 0.16%로 나타나며 이를 Fig. 4에 나타냈다.
이처럼 셀 간격별 격자를 비교하여 격자 의존도 Test를 진행하였다. 해석 시간 및 수렴 효율성을 고려하여 5 mm일 경우 Umax가 4.46 m/s, 오차율이 0.89%인 30개 격자, 1 mm일 경우 Umax가 4.49 m/s, 오차율 0.22%인 20개 격자, 0.5 mm일 경우 Umax가 4.485 m/s, 오차율 0.33%인 20개 격자를 선택하였다. 이때 5 mm 간격에서는 38만 개, 1 mm는 33만 개, 0.5 mm는 33만 개의 격자를 생성하여 이를 Table 3에 정리하였다.
2.3 격자 생성
배터리의 격자 생성은 ANSYS MESH를 사용하였고 격자는 셀 표면과 셀 간격 등 경계층 영역이 존재하는 곳에서는 Hexa를 사용하여 조밀하게 격자를 생성하였다. 셀 간격 부분의 유동 영역에는 Edge Sizing의 Number of Divisions로 0.5 mm에서 20개, 1 mm는 20개, 5 mm는 30개를 주고 Body Sizing으로 1.6 mm로 동일하게 주었다. 셀 주위의 유동 영역은 Edge Sizing을 5개, Body Sizing으로 1.6 mm를 주었다. 셀 간격 내의 유동 영역은 경계층 영역이므로 셀 표면에서 멀어질수록 격자의 크기가 커지도록 Bias 종류를 설정하여 생성하였다. 나머지 전체 유동장 부분은 Method에서 Tetra 격자로 설정하고 Global Size를 50 mm로 생성하였다. 그리하여 전체 배터리 유동장의 전체에 대하여 5 mm일 경우 총 1081만 개, 1 mm일 경우 총 1107만 개, 0.5 mm일 경우 총 940만 개의 격자를 생성하였고 이를 Table 4에 정리하였다. Y plus (Y+) 값은 연구 대상인 셀 간격을 기준으로 0-13.073 값을 유지하였다.
Fig. 5(a)는 배터리의 셀 단면 및 전체 유동장에 대한 격자의 형상이고, Fig. 5(b)는 셀 간격을 나타낸 격자의 형상이다.
Fig. 6(a)는 5 mm일 때, Fig. 6(b)는 1 mm일 때, Fig. 6(c)는 0.5 mm일 때, 격자 의존도 Test를 진행한 후 셀 간격 하나의 격자를 확대하여 정면도로 나타낸 형상이다.
3. 결과 및 고찰
본 연구는 배터리 셀의 형상을 단순화하고 ANSYS CFX V19.1을 활용하였고, 현재 실제 전기 자동차 배터리 제조사 국내 ㈜S사의 제품 경우 0.5 mm 간격의 배터리 팩을 글로벌 완성차 업체 ㈜B사에 적용하고 있어 0.5 mm의 방열 성능과 실제 적용이 적절한지에 대해 알아보고 다른 간격에 비해 방열 성능이 어느 정도 우수한지 수치적으로 비교하기 위해 3가지(5, 1, 0.5 mm)로 셀 간격의 크기를 분류하여 유동 해석을 진행하였다. 해석 이후 유동 해석의 경향과 신뢰성을 확인하기 위해 속도 분포, 온도 분포를 확인하였다. 방열 성능이 취약한 셀 간격과 국소적 위치를 찾기 위해 국소적 X, Y, Z 위치에서의 열전달 계수 해석을 진행하여 배터리 셀 간격별 방열 성능을 분석하고 비교하였다. 정밀한 계산을 통해 해석의 신뢰성을 높이기 위해 KISTI에서 제공하는 Intel Xeon Phi 7250(KNL) 모델 68코어 16GB*6, 6Ch per CPU의 성능을 가진 수퍼 컴퓨터를 사용하였다.
3.1 속도 분포
Fig. 7은 배터리 셀 간격별 속도 벡터 분포를 Top, Side View로 바라본 그림이며, Side View는 배터리 팩 내 12개 셀 중의 중간 셀의 속도 벡터를 나타낸 모습이다. Figs. 7(a), 7(d)는 5 mm, Figs. 7(b), 7(e)는 1 mm, Figs. 7(c), 7(f)는 0.5 mm의 속도 벡터의 모습이다.
속도 벡터는 배터리 셀 간격의 크기 따라 3가지로 분류하였고, 셀 간격 부분을 확대하여 나타냈다. 셀 간격별 최고 속도는 셀 입구 면과 출구 면에서 동일하게 발생하며 5 mm에서 37.567 m/s, 1 mm에서 57.045 m/s, 0.5 mm에서 90.907 m/s로 나타났다. 유동장 입구의 면적에서 셀과 만났을 때 면적이 급격하게 줄어들어 속도가 높게 나오는 것을 볼 수 있었다. 전체적으로 셀 간격 입구에서 공기의 흐름에 따라 셀 벽면 근처에서 마찰이 발생하여 속도가 감소하는 형상을 볼 수 있었다. 5 mm에서는 비교적 다른 간격에 비해 유동 저항의 큰 영향없이 셀 간격 입구에서부터 출구까지 원활한 공기의 흐름을 확인할 수 있었다.
1 mm, 0.5 mm에서는 좁은 셀 간격으로 인해 발생하는 유동 저항이 커서 공기가 위, 아래로 퍼져나가 셀 간격 출구 윗부분과 아랫부분에서 속도가 증가하는 형상을 볼 수 있었다. 셀 간격 0.5 mm에서는 공기가 셀 간격으로 들어가는 면적이 5 mm와 1 mm보다 작아 속도가 가장 빠른 현상을 확인할 수 있었다. 속도 벡터를 Figs. 7(d)부터 7(f)의 Side View로 봤을 때, 셀 간격이 0.5, 1 mm에서는 배터리 셀 뒷부분에 와류가 발생하는 것을 볼 수 있었지만 5 mm에서 공기가 원활하게 흘러 와류가 발생하지 않았다.
3.2 온도 분포
Fig. 8은 공기 유동에 의한 강제대류 열전달에 의해 나타난 배터리 셀 간격 내에서의 온도 분포를 나타낸 것이다. Fig. 8(a)의 5 mm에서 최저 온도는 셀 간격 입구에서 25.42oC가 나타나고, 최고 온도는 셀 간격 출구에서 31oC로 나타났다. Fig. 8(b)의 1 mm에서도 동일한 지점에서 최저 온도는 25.38oC가 나타나고, 최고 온도는 52oC로 나타났다. Fig. 8(c) 0.5 mm도 5 mm와 동일한 지점에서 최저 온도는 25.36oC, 최고 온도는 58.7oC로 나타났다. 셀 간격 입구에서는 온도 편차가 매우 작았으며 전반적으로 5 mm에서는 셀 간격이 넓어 방열이 우수하지만 1, 0.5 mm에서는 셀 간격이 좁아 유입된 공기가 방출되지 못하여 5 mm보다 높은 온도로 나타나는 것을 볼 수 있었다. 하지만 1 mm와 0.5 mm의 경우 5 mm에서 보다 온도가 높을 뿐이며, 실제 차량 주행에 있어 배터리 내구성과 전체 에너지 저장 능력에는 크게 영향을 주지 않는 온도라 판단된다. 공통적으로 셀 간격 입구에서 유입된 공기가 출구로 흐르면서 가열되어 셀 간격 출구 부분에 방열을 원활히 시키지 못하여 최고 온도가 나타나는 것을 볼 수 있고, 1, 0.5 mm의 경우 셀 간격 출구 부분에는 공기가 상하로 분산되어 출구 윗부분과 아랫부분에서는 방열이 우수한 형상을 볼 수 있었다.
Fig. 9는 셀 폭(X축)에서 방열의 편차가 가장 큰 위치에서 방열 성능을 비교하고 정량적으로 표현하기 위해 3가지의 셀 간격에 따라 온도 분포 편차가 큰 동일한 X 위치에서 수평선으로 나타냈다. Fig. 10은 셀 높이(Z축)의 방열 성능이 가장 취약한 위치인 셀 간격 출구를 집중적으로 방열 성능을 비교하고 정량적으로 표현하기 위해 3가지의 셀 간격에 따라 온도 분포의 편차가 가장 큰 동일한 셀 간격 출구 위치에서 수직선으로 나타냈다. Fig. 11은 출구면에서 봤을 때, 셀 12개의 후면을 나타낸 온도분포이다.
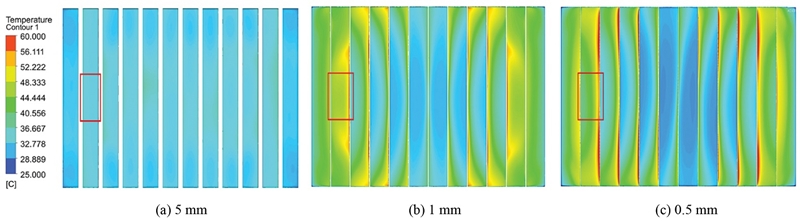
Outlet section view of temperature contours at battery pack according to three different gaps of battery pack
배터리팩 형상이 가운데 셀(왼쪽에서 6, 7번째)에 대하여 대칭을 이루고 있어 공기 유동도 대칭을 이루어 Figs. 11(a)부터 11(c) 모두 온도 분포가 대칭으로 나타났다. Fig. 11(a)의 5 mm에서는 전반적으로 12개의 셀 전부가 방열이 우수하게 나타났다. Figs. 11(b)의 1 mm와 11(c)의 0.5 mm는 Figs. 7(e)와 7(f)에서 보이는 것과 같이 속도 분포가 셀의 후면에서 와류가 발생하여 가운데 셀(Fig. 11 왼쪽에서 6, 7번째 셀)에서 방열이 우수하게 나타났다. 이를 통해 와류가 방열에 큰 영향을 미치는 것을 알 수 있었다. Fig. 12는 Fig. 11의 붉은 마킹 영역을 확대한 것으로, 셀 두께(Y축)에서 방열이 취약한 부분을 나타내는 그림이며 셀(6, 7번째 셀)의 위치에서의 방열이 가장 우수한 부분에서 방열 성능을 비교하고 정량적으로 표현하기 위해 3가지의 셀 간격에 따라 온도 분포 편차가 큰 동일한 부분에 수평선으로 나타냈다. 추가로 방열이 우수한 셀(Fig. 11 왼쪽에서 6번째)도 위와 동일하게 진행하였다.
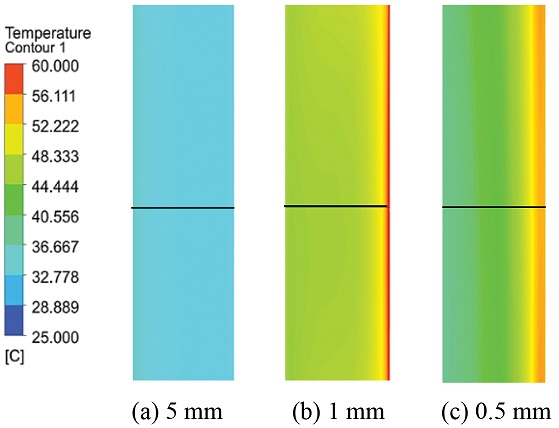
Enlarged view of temperature contours of horizontal position on the rear thickness position at the cell according to three different gaps
셀 간격의 크기에 따른 방열 성능을 정량적으로 비교하기 위해 Nusselt 수를 계산하였다. Nusselt 수는 대류 열전달에 대한 유체 내의 전도 열전달의 상대적인 비를 나타내는 무차원 파라미터로 열전달 계수(h)의 무차원 파라미터이다. 열전달 계수(h)는 아래 식(2)로 계산할 수 있다.
(2) |
여기서 q는 열 유속[W/m2], Ts는 셀의 표면 온도[K], T∞는 자유 흐름 상태의 공기의 온도[K]를 나타낸다. 방열이 취약한 곳에서 온도 분포 편차가 가장 큰 지점을 범위로 설정하여 국소적 X, Y, Z 위치에서의 Nusselt 수를 계산하여 방열 성능을 비교했다. 이러한 위치를 무차원의 기준 길이(X+, Y+, Z+)를 식(3)을 통해 계산하여 나타냈다.
(3) |
여기서 X는 셀 폭의 국소적 위치, Y는 셀 두께의 국소적 위치, Z는 셀 높이의 국소적 위치, L은 셀 폭의 전체 길이, T는 셀 두께의 전체 길이, H는 셀 높이의 전체 길이이다.
Tables 5부터 8은 Figs. 9, 10, 12의 셀 폭(X축), 셀 높이(Z축), 셀 두께(Y축)의 수평·수직선상 온도 분포를 무차원의 기준 길이(X+, Y+, Z+)의 위치에 해당하는 온도와 열전달 계수를 수치적으로 계산한 표이다. Table 5는 셀 폭(X축)의 위치에 해당하고 Table 6은 셀 높이(Z축)의 위치에 해당하고 Tables 7, 8은 셀 두께(Y축)의 위치 중 Table 7은 방열 성능이 취약한 셀(Fig. 11 왼쪽에서 2번째 셀), Table 8은 방열 성능이 우수한 셀(Fig. 11 왼쪽에서 6번째 셀)에 해당한다. Tables 5부터 8에 나타난 온도와 열전달 계수를 통해 Nusselt 수로 나타내어 셀 간격별에 따른 방열 성능을 비교하였다.

Numerical data of temperature and heat transfer coefficient for horizontal position (X) on the side surface at three different gaps

Numerical data of temperature and heat transfer coefficient for vertical position (Z) on the side surface at three different gaps

Numerical data of temperature and heat transfer coefficient for horizontal position (Y) on the rear surface of 2nd cell

Numerical data of temperature and heat transfer coefficient for horizontal position (Y) on the rear surface of 6th cell
Fig. 13은 Fig. 9의 온도 분포 편차가 가장 큰 위치에서 셀 간격별로 셀 폭(수평선)의 X+을 위치별로 Nusselt 수로 무차원화하여 레이놀즈 수(X)에 대한 방열 정도를 한눈에 파악하기 위하여 정량적으로 나타낸 그래프이다. 무차원의 기준 길이(X+)를 왼쪽에서 시작하여 오른쪽으로 0-1로 설정하였다. X+= 0은 공기가 셀 간격으로 유입되는 입구에서 가장 근접한 위치이고 X+= 1은 공기가 외부로 유출되는 셀 출구에서 가장 근접한 위치이다. Nusselt 수를 표시하여 비교해본 결과 3가지 경우 모두 공기가 셀 간격으로 유입되는 입구(X+= 0)에서 높은 방열 성능을 볼 수 있었고, Fig. 9에서 보면 셀 간격 출구로 갈수록 온도가 높아지는 것을 볼 수 있는데 셀 간격 입구에서 유입된 공기가 출구로 흐르면서 가열되어 셀 출구쪽으로 흐르고 속도 분포도 작기 때문에 셀 간격 출구 근처 위치(X+= 0.89)에서 낮은 방열 성능을 볼 수 있었다. 셀 간격별 방열 성능을 비교해보면 셀 간격 입구 근처 위치(X+= 0.11), 셀 간격 출구 위치(X+= 1)에서 0.5 mm가 1 mm에 비해 6.68, 7.66%로 높게 나타났다. 평균 방열 성능은 5 mm가 1, 0.5 mm에 비해 26.36, 26.99% 각각 높게 나타났고, 0.5 mm가 1 mm에 비해 0.49% 낮게 나타나서 방열 성능이 미미하게 차이나는 것을 알 수 있었다.
Fig. 14는 Fig. 10의 방열이 취약하고 온도 분포가 가장 높은 셀 간격 출구 부근의 위치에서 셀 간격별로 셀 높이(수직선)의 Z+을 위치별로 Nusselt 수로 무차원화하여 레이놀즈 수(Z)에 대한 방열 정도를 한눈에 파악하기 위하여 정량적으로 나타낸 그래프이다. 무차원의 기준 길이(Z+)를 위쪽에서 시작하여 아래쪽으로 0-1로 설정하였다. Z+= 0은 셀 간격 출구 부근의 가장 아래쪽에 근접한 위치이고 Z+= 1은 셀 간격 출구 부근의 가장 위쪽에 근접한 위치이다. Nusselt 수를 표시하여 비교해본 결과 3가지 경우 모두 Fig. 7을 보면 셀 간격 출구 윗부분과 아랫부분에서 속도가 증가하는 형상을 볼 수 있어 셀 간격 출구 아래쪽과 위쪽(Z+= 0, 1) 위치에서 높은 방열 성능을 볼 수 있었고, 중간 지점(Z+= 0.44, 0.55)에서 낮은 방열 성능을 볼 수 있었다. 셀 간격별 방열 성능을 비교해보면 셀 간격 출구 아래쪽과 위쪽(Z+= 0, 1) 위치에서 0.5 mm가 5 mm에 비해 35, 15.8%로 각각 낮게 나타났고, 1 mm에 비해 28.64, 48.3%로 각각 높게 나타났다. 평균 방열 성능은 0.5 mm가 1 mm에 비해 12.12% 높게 나왔고, 5 mm에 비해 2.71배 낮았다.
Fig. 15에서 셀 간격별 그래프(1)은 Fig. 11에서 온도 분포가 가장 높고 방열 성능이 취약한 셀(왼쪽에서 2번째)이고 셀 간격별 그래프(2)는 온도 분포가 가장 낮고 방열 성능이 우수한 셀(왼쪽에서 6번째, 중간)이며, 2가지를 셀 간격별로 Fig. 12와 같이 셀 두께(수평선)의 Y+을 위치별로 Nusselt 수로 무차원화하여 레이놀즈 수(Y)에 대한 방열 정도를 한눈에 파악하기 위하여 정량적으로 나타낸 그래프이다. 무차원의 기준 길이(Y+)를 왼쪽에서 시작하여 오른쪽으로 0-1로 설정하였다. Y+= 0은 셀 간격과 만나는 왼쪽 위치이고, Y+= 1은 셀 간격과 만나는 오른쪽 위치이다.
Nusselt 수를 표시하여 비교해본 결과 방열 성능이 취약한 셀(셀 간격별 그래프(1))과 방열 성능이 우수한 셀(셀 간격별 그래프(2))은 공통적으로 0.5, 1 mm에서는 셀 간격과 만나는 왼쪽 부근에서 중간 지점(Y+= 0.11-0.33)까지 높은 방열 성능을 볼 수 있었고 셀 간격과 만나는 오른쪽 지점(Y+= 1)에서 낮은 방열 성능을 볼 수 있었다. 5 mm에서는 셀 두께의 중간 지점(Y+ = 0.55, 0.66)에서 높은 방열 성능을 볼 수 있었고 셀 간격과 만나는 왼쪽 위치(Y+= 0)에서 낮은 방열 성능을 볼 수 있었다. 셀 간격별 방열 성능을 비교해보면 방열 성능이 취약한 셀(Fig. 11 왼쪽에서 2번째 셀)의 셀 간격별 그래프(1)에서 평균적으로 0.5 mm가 1 mm에 비해 9.55% 높게 나왔고 5 mm에 비해 91.28%로 낮게 나왔다. 방열 성능이 우수한 셀(Fig. 11 왼쪽에서 6번째 셀)의 셀 간격별 그래프(2)에서는 Figs. 7(e), 7(f) 속도 분포에서 0.5, 1 mm는 셀 후면에 와류가 생겨 셀 간격과 만나는 왼쪽 위치에서 중간 지점(Y+= 0-0.66)까지 0.5 mm와 1 mm가 5 mm보다 높은 방열 성능을 볼 수 있었다. 중간 지점에서 셀 간격과 만나는 오른쪽 위치(Y+= 0.77-1)까지는 5 mm가 0.5, 1 mm보다 높은 방열 성능을 볼 수 있었다. 셀 간격과 만나는 왼쪽 부근(Y+ =0.11)에서 0.5 mm가 5, 1 mm에 비해 45.43, 8.55%로 각각 높게 나타났다. 셀 간격과 만나는 오른쪽 위치(Y+= 1)에서 0.5 mm가 5, 1 mm에 비해 4.8배, 51.18%로 각각 낮게 나타났지만, 전체적인 평균 방열 성능은 0.5 mm가 5, 1 mm에 비해 13.19, 0.79%로 각각 높게 나왔다. 또한, 방열 성능이 우수한 셀(Fig. 11 왼쪽에서 6번째 셀)이 방열 성능이 취약한 셀(Fig. 11 왼쪽에서 2번째 셀)에 비해 평균 방열 성능이 0.5 mm에서 3.1배 높았고, 1 mm는 3.4배 높았고, 5 mm는 1.8% 낮게 나왔다.
방열 성능이 우수한 위치는 셀 간격 입구에서 가장 근접한 부분이고, 1 mm와 0.5 mm에서 셀 간격 출구 위쪽과 아래쪽에 국소적으로 방열이 우수하였고 셀 두께의 위치(Y위치)에서 와류로 인해 중간 셀 후면 위치(Fig. 11 왼쪽에서 6, 7번째 셀)에서 높은 방열 성능을 볼 수 있었고 방열이 원활히 되지 않는 위치는 셀 간격의 출구 위치임을 수치적으로 확인할 수 있었다. 전체적으로 셀 간격 5 mm가 방열 성능이 높았지만 셀 간격이 5 mm의 경우 배터리 레이아웃이 증가하고 배터리가 차지하는 용적이 커지게 되어 배터리 레이아웃 설계에 있어 셀 갯수를 감소시키거나 레이아웃의 크기를 증가시켜야 하므로, 그에 따라 배터리 내 에너지 저장 능력이 감소하게 되어 전기차 상용화에 가장 큰 어려움 중 하나인 1회 충전으로 주행할 수 있는 거리가 감소하게 된다. 또한, 셀 사이의 공간이 넓어지면서 고정이 어려워져 차량 운행 중 충격과 진동으로 인해 손상을 받을 수 있다. 그에 비해 0.5 mm의 경우 위의 단점을 보완할 수 있을 뿐만 아니라 셀 방열에 있어 취약 부위인 셀 후면을 와류를 통해 방열할 수 있었다.
4. 결론
본 연구는 배터리 셀 레이아웃에 따라 셀 간격을 0.5, 1, 5 mm의 3가지 경우에 대해 배터리 셀 내에서 속도 및 온도 분포를 수치적으로 해석하여 현재 실제 전기자동차에서 적용하고 있는 배터리 셀 간격인 0.5 mm의 방열 성능과 실제 적용이 적절한지에 대해 파악하고 타 간격과 방열 성능을 정량적으로 비교하는 데에 초점을 두고 연구를 하였다. 셀 간격에 방열이 취약한 부분과 우수한 부분의 편차가 가장 큰 위치를 설정하고 무차원의 기준 길이(X+, Y+, Z+)로 레이놀즈 수로 나타내어 각각의 위치에 따라 나타난 온도 분포와 열전달 계수를 통해 강제대류 열전달에 의한 방열 성능을 비교하기 위해 무차원 Nusselt 수를 계산하여 진행하였다. 이에 따른 결론을 다음과 같이 정리하였다.
(1) 셀 간격별 최고 속도는 셀 입구 면과 출구 면에서 동일하게 발생하며 유동장 입구의 면적에서 셀과 만났을 때 면적이 급격하게 줄어들어 속도가 높게 나오는 것을 볼 수 있었다. 1, 0.5 mm에서는 좁은 셀 간격으로 인해 공기가 위, 아래로 퍼져나가 셀 간격 출구 윗부분과 아래부분에서 속도가 증가하는 형상을 볼 수 있었고, 배터리 셀 출구 부근에 와류가 발생하는 것을 볼 수 있었다.
(2) 셀 간격 입구에서 유입된 공기가 출구로 흐르면서 가열되어 셀 간격 출구 부분에 방열을 원활히 시키지 못하여 최고 온도가 나타나는 것을 볼 수 있어 방열 성능이 가장 취약한 위치로 파악되었다.
(3) 셀 간격에 방열이 취약한 부분과 방열이 우수한 부분의 편차가 가장 큰 위치를 수평·수직선으로 설정하여 Nusselt 수로 나타낸 결과 셀 폭(X축)의 평균 방열 성능으로는 5 mm가 1, 0.5 mm에 비해 각각 26.36, 26.99%로 높게 나타났고, 0.5 mm가 1 mm에 비해 0.49% 낮게 나타나서 방열 성능이 미미하게 차이나는 것을 알 수 있었다. 셀 높이(Z축)의 평균 방열 성능으로는 0.5 mm가 1 mm에 비해 12.12% 높게 나왔고 5 mm에 비해 2.71배 낮았다.
(4) 배터리 셀을 출구에서 봤을 때, 셀 두께(Y축)는 방열 성능이 취약한 셀(외곽에 위치한 셀)과 우수한 셀(가운데에 위치한 셀) 2가지를 셀 간격별로 비교하였다. 와류로 인하여 가운데에 위치한 셀이 외곽에 위치한 셀에 비해 평균 방열 성능이 0.5 mm에서 3.1배 높았고, 1 mm는 3.4배 높았고, 5 mm는 1.8% 낮게 나왔다.
(5) 국소적으로 방열 성능이 우수하게 나타낸 위치는 셀 간격 입구에서 속도가 증가하여 셀 간격으로 유입되는 입구(X+= 0), 셀 간격 출구 윗부분과 아랫부분에서 속도가 증가하여 셀 간격 출구 아래쪽과 위쪽(Z+= 0, 1) 위치, 와류로 인해 방열 성능이 우수한 셀(가운데에 위치한 셀)에 셀 간격과 만나는 왼쪽 부근(Y+= 0.11)이다. 방열 성능이 취약한 위치는 셀 간격 출구 위치 부근(X+= 0.89), 셀 간격 출구 중간 지점(Z+= 0.44, 0.55), 방열 성능이 취약한 셀(외곽에 위치한 셀)에 셀 간격과 만나는 오른쪽 위치(Y+= 1)이다.
(6) 셀 간격이 5 mm의 경우 레이아웃이 증가하고 배터리가 차지하는 용적이 커지게 되어 배터리 레이아웃 설계에 있어 셀 갯수를 감소시키거나 레이아웃의 크기를 증가시켜야 한다. 그에 비해 0.5 mm의 경우 위의 단점을 보완하여 배터리 내 에너지 저장 능력을 향상시키고 배터리 셀의 차량 주행 내구성도 증대시킬 수 있으며 셀 방열에 있어 취약 부위인 셀 후면을 와류를 통하여 방열할 수 있다. 위와 같은 문제점을 해결하기 위해서는 0.5 mm가 적합하고 실제에서도 0.5 mm가 적용되고 있다.
(7) 본 연구를 기반으로 추후 연구에서는 전기자동차 배터리 간격 0.5 mm를 기준으로 하여 현재 배터리 방열에 많이 적용되고 있는 수냉식 냉각 유로의 갯수, 위치, 형태를 여러 경우로 나누어 최적 설계를 하여 수냉식의 단점인 공간 점유율을 감소시킬 것이며 방열 성능을 향상시킬 것이다. 또한, 0.5 mm 셀 간격에 방열성이 좋은 알루미늄 재질의 사각 파이프 형상인 Thermal Plate를 삽입하여 본 연구에서 확인한 공냉식 배터리 셀 간격 0.5 mm에서 존재하는 방열의 단점을 보완하고 방열 성능이 국소적으로 취약한 셀 간격 출구 부위를 보완시켜 배터리 방열 성능을 향상시킬 것이다.
REFERENCES
- Jeong, C. K., “Lithium Battery Technology Trend,” Journal of Electrical World Monthly Magazine, Vol. 480, pp. 34-35, 2016.
- Song, H. S., “Latest Trends in ESS and Battery Safety Technologies,” The Magazine of the Korean Institute of Power Electronics, Vol. 24, No. 6, pp. 66-71, 2019.
- Yoon, J. H., “Thermal Modeling of Lithium-Ion Battery Pack System,” M.Sc. Thesis, Hanyang University, 2014.
- Shin, H. J. and Lee, J. S., “Cooling CFD Analysis of a Car Batter Pack with Circular Cells,” Transactions of the Korean Society of Mechanical Engineers B, Vol. 41, No. 10, pp. 693-698, 2017.
- Kang, U. S., “A Study on Characteristics of Thermal Flow of Tray Structure for Li-Ion Battery,” M.Sc. Thesis, Pusan National University, 2017.
-
Kim, H. S., Han, B. Y., and Park, H. K., “Flow Analyses Around the Battery Pack for a NEV,” Journal of Computational Fluids Engineering, Vol. 16, No. 3, pp. 82-87, 2011.
[https://doi.org/10.6112/kscfe.2011.16.3.082]
-
Suh, H. K., “Effect of Inlet Geometry on the Cooling Performance of Battery Pack for an Electric Vehicle,” Journal of Korean Society of Mechanical Technology, Vol. 15, No. 5, pp. 679-684, 2013.
[https://doi.org/10.17958/ksmt.15.5.201310.679]
-
Baek, S. K . and Park, S. J ., “ T hermal A nalysis of a B attery Cooling System with Aluminum Cooling Plates for Hybrid Electric Vehicles and Electric Vehicles,” Transactions of the Korean Society of Automotive Engineers, Vol. 22, No. 3, pp. 60-67, 2014.
[https://doi.org/10.7467/KSAE.2014.22.3.060]
- Lee, S. H., “Li-Ion Battery Cooling System with Oscillating Heat Pipe for Electric Vehicle,” Proc. of the Spring and Fall Conference on the Korean Society of Mechanical Engineers, pp. 903-904, 2018.
- Jang, I. H., “Thermal Fluid Analysis of Battery Module for HEV,” M.Sc. Thesis, Chonnam National University, 2011.
- Jang, I. H., Choe, J. H., and Seol, S. Y., “Analysis of Cooling Efficiency Depending on Gap of Battery Packs,” Proc. of the Spring and Fall Conference on the Korean Society of Mechanical Engineers, pp. 1825-1829, 2011.
-
Lee, D. R., “A Study on the Convective Cooling Performance of the Secondary Battery in Electric Vehicle,” Journal of the Korean Society for Precision Engineering, Vol. 35, No. 12, pp. 1157-1162, 2018.
[https://doi.org/10.7736/KSPE.2018.35.12.1157]
B.S. Student in the School of Mechanical and Automotive Engineering, Catholic University of Daegu. His research interest is Electric Vehicle and Future Alternative Energy.
E-mail: gtq0125@cu.ac.kr
B.S. Student in the School of Mechanical and Automotive Engineering, Catholic University of Daegu. His research interest is Electric Vehicle and Future Alternative Energy.
E-mail: wmzl12@cu.ac.kr
B.S. Student in the School of Mechanical and Automotive Engineering, Catholic University of Daegu. His research interest is Turbo Machinery, Future Alternative Energy, and Aerospace Engineering.
E-mail: wayinuni@cu.ac.kr
Professor in the School of Mechanical and Automotive Engineering, Catholic University of Daegu. His research interest is Heat Transfer, Fluid Engineering, and Electric Vehicle.
E-mail: dlee@cu.ac.kr