
레이저 빔 가공을 이용한 텅스텐 마이크로 니들 어레이 제작
Copyright © The Korean Society for Precision Engineering
This is an Open-Access article distributed under the terms of the Creative Commons Attribution Non-Commercial License (http://creativecommons.org/licenses/by-nc/3.0) which permits unrestricted non-commercial use, distribution, and reproduction in any medium, provided the original work is properly cited.
Abstract
Micro needle arrays have been widely used within medical contexts, such as for drug delivery and nervous electrodes, and its fabrication methods have attracted attention recently. This paper describes a novel fabrication method for micro needle arrays on a tungsten metal plate using only laser beam machining. Tungsten material was ablated as combining laser beam scanning path to control needle structure. Overlapping laser beams from the combined scanning path causes thermal accumulation phenomena which removes the material. In this paper, controlling laser scanning path (Line Interval, Line Space, Number of Lines) and machining conditions (Power, Number of Scan), and the changing length and pitch of the micro needles were measured through SEM. Moreover, the piercing force for application in drug delivery and nervous electrodes was measured with a load cell system.
Keywords:
Laser beam machining, Micro needle arrays, Tungsten, Piercing force, Micro fabrication키워드:
레이저 빔 가공, 마이크로 니들 어레이, 텅스텐, 관통력, 미세 가공1. 서론
최근 마이크로 스케일의 가공기술을 의학 분야에 응용하고자 하는 움직임이 대두되고 있다. 환자에게 약물을 투여하는 방법에는 구강으로 복용하는 방법과 직접 원하는 부위에 주사하는 방법이 있다.1 구강 복용법은 약물 주사 시에 환자가 겪는 고통이 없지만 소화액과 섞여 체내에 공급되는 과정에서 의학적인 효과가 늦게 발현된다.2 직접 주사 방법은 빠른 약물 효과가 나타난다는 장점이 있으나, 통점을 자극하여 고통을 유발하므로 주사 공포증이 있는 환자들에게는 적용하기가 어렵다.3 마이크로 니들은 통증 신경을 자극하지 않는 작은 크기의 니들 어레이를 이용하여 피부를 통해 약물을 전달하는 방식으로, 기존의 직접 주사 방법과 구강 복용법의 단점을 해결한 방법이다.4
마이크로 니들은 뇌와 중추 신경계의 신호 전달용 뇌전도(Electroencephalogram) 전극으로도 응용하고 있다. 이는 뇌 연구와 뇌 질병 원인 파악 및 치료를 위해 중요도가 높아지고 있는 연구 분야이다.5
마이크로 니들을 가공하기 위해 다양한 재료와 가공법이 사용되었다. Photolithography나 Deep Reactive Ion Etching을 이용하여 직접 니들의 형상을 노광하여 가공하거나 몰드를 선가공하고, 폴리머를 전사시켜 완성품을 얻는 방법 등이 있다.6 이러한 가공법에서 사용되는 실리콘 등의 재료는 취성을 지니고 있기 때문에 부서진 니들 조각이 인체에 남아 악영향을 끼칠 수 있으며 견실성에 단점을 갖는다. 또한 기존의 다단계 적층 공정을 이용하는 경우 대량 생산을 위한 가공 시간 및 비용적 측면에서 효율성이 낮다.7 레이저 빔 가공법을 이용하여 스테인레스 스틸 금속 표면에 마이크로 핀 어레이를 가공한 연구를 진행하고 있다.8 레이저 빔 가공은 기존의 다단계 공정법과 다르게 금속 표면을 열적으로 제거하여 가공하는 손쉬운 방법이다.9 가공속도가 빠르기 때문에 시간적 비용이 낮고, 효율적으로 모재의 대면적에 마이크로 핀을 가공할 수 있다. 또한 레이저 빔 경로를 조절하여 핀을 가공하고, 전해에칭 후공정을 진행하여 재응고층을 제거함으로써 다양한 형상의 마이크로 핀을 조각하는 기술 연구를 진행하였다.10
본 논문에서는 레이저 빔 가공을 이용하여 텅스텐 금속에 마이크로 니들을 가공한다. 레이저 빔이 조사되는 경로와 가공 조건에 따라 니들의 배열과 형상의 변화를 확인한다. 최종적으로 마이크로 니들로써의 적용성 확인을 위해 사람의 피부와 비슷한 조성의 젤라틴과 고기에 관통력을 측정하였다. 본 연구는 기존의 마이크로 니들 가공법이 지니고 있던 시간적, 비용적 문제를 단순히 레이저 스캐닝만을 이용하여 원스텝 공정으로 수행함으로써 해결하는 고효율의 방법이다. 또한 재료적 측면에서 텅스텐 금속을 모재로 사용하여 실리콘이 지니고 있던 물성적 한계를 동시에 해결하였다.
2. 배경 이론 및 실험 세부사항
2.1 마이크로 니들 어레이 제작을 위한 레이저 빔 조사 경로 조절
Fig. 1(a)는 레이저 빔 가공을 이용하여 텅스텐 마이크로 니들 어레이가 제작되는 과정을 나타낸다. 레이저 빔의 조사 경로는 화살표로 표시하고 있으며, 중첩되는 경로 이외의 비어있는 사각형 부분에서 마이크로 니들이 생성된다. 기존의 레이저 빔 가공을 이용한 마이크로 핀 어레이 가공의 경우, 스테인레스 스틸의 재료적 특성에 의하여 열적 가공으로 적층된 산화크롬 재응고층이 시편의 두께보다 높은 위치에 생성되었으나,8 본 연구에서 사용된 텅스텐은 적층되는 재응고층보다 열 가공에 의해 모재가 제거되는 속도가 빨라 시편의 아래 방향으로 니들 형상이 생성된다. 본 연구에서는 25 mm2 대면적의 마이크로 니들 어레이를 가공하고자 한다. 대면적 가공의 경우 많은 양의 레이저 빔 열에너지가 대류와 전도로 소실되어 마이크로 니들의 형상에 영향을 주므로, 빔 조사 경로와 레이저 빔 가공 조건 등의 파라미터 실험을 수행하였다. Fig. 1(b)는 레이저 빔 경로 조합에 따른 니들 가공 실험 시 변경될 파라미터이다. 라인 스페이스(Line Space)는 레이저 빔 그룹 사이에 존재하는 니들이 형성되는 공간, 라인 인터벌(Line Interval)은 각 빔 경로 사이의 거리, 라인 수(Number of Lines)는 동일 방향으로 나열된 레이저 빔들의 개수를 의미한다.
2.2 실험 장비와 환경
Fig. 2는 본 연구 수행에 사용된 레이저 가공 시스템을 보여준다. 1 μm 이송급 레졸루션을 갖는 정밀 3축 가공기를 기반으로 텅스텐 공작물은 X, Y축 스테이지에 지그와 함께 고정하여 이송되며, 레이저는 Z축 스테이지에 장착되어 초점 거리를 맞추고 가공을 수행한다. 본 연구에서는 1,064 nm 파장을 갖는 이터븀 파이버 레이저를 사용하였다. 모든 니들 가공 실험에서 스캔속도는 258.6 mm/s, 펄스 레이저의 반복률은 20 kHz의 고정값을 유지하였으며, 출력과 조사 횟수를 변경하며 파라미터 실험을 수행하였다.
3. 레이저 빔 조건 및 경로에 따른 가공 특성
3.1 레이저 빔 가공 조건에 따른 특성
레이저 빔 가공은 주로 빔의 출력과 조사 횟수를 변경하여 발생한 열에너지로 공작물을 기화시켜 가공한다. Fig. 3은 레이저의 출력을 변화시키며 가공한 텅스텐 마이크로 니들이다. 라인 스페이스는 50 μm, 라인 인터벌은 10 μm, 라인 수는 6줄의 조건으로 600회 조사하여 가공하였다. 레이저 빔의 출력이 Figs. 3(a)부터 3(c)를 보면 8에서 16 W로 증가함에 따라 가공되는 깊이(니들의 길이)는 점차 증가하였다. Fig. 3(d)의 20 W 이상인 경우에는 텅스텐 공작물 상단부터 깊이 방향으로의 전체 가공량은 증가하였으나, 생성된 마이크로 니들의 길이는 변화량이 적었다. 이는 레이저 빔 가공에서 열에너지 축적에 따른 깊이 방향 가공량이 로그함수 경향성을 띄기 때문이다.11 Fig. 3(e)에서 보는 바와 같이 가공된 마이크로 니들의 피치는 출력이 증가하여도 129 μm의 수치에서 변화가 없었다. 이는 레이저 빔의 출력이 가우시안 분포를 따르기 때문에 열에너지가 빔의 반경 방향으로 갈수록 줄어 가공 경계값(Threshold)을 넘지 못했기 때문이다. 또한 출력이 증가하여도 물리적인 빔의 조사 너비가 넓어지지 않으면 단순 출력으로 증가된 열에너지는 깊이 방향 가공을 위해 사용되기 때문이다.
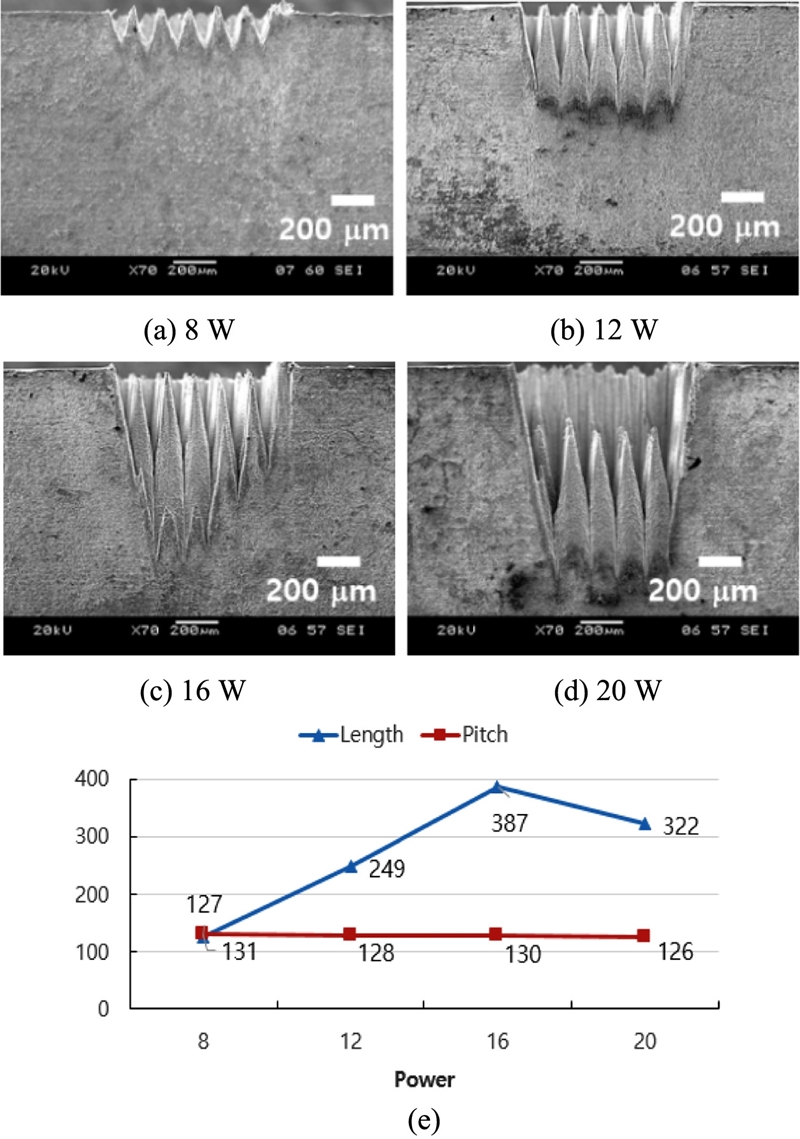
(a), (b), (c), (d) Fabricated micro needle arrays according to laser beam power, and (e) Measured specific value of needle
Fig. 4는 레이저 빔의 조사 횟수를 변경하며 가공된 마이크로 니들의 SEM 사진과 길이 및 피치를 측정한 그래프이다. SEM 사진에서 확인할 수 있듯이 빔의 조사 횟수가 증가함에 따라 텅스텐 공작물 표면에서 깊이 방향으로의 가공량이 증가함을 확인할 수 있다. 반면에 생성된 마이크로 니들의 피치와 길이는 변하지 않음을 확인할 수 있다. 1,600회 이상으로 레이저 빔이 조사된 경우, 두께 1 mm의 텅스텐 공작물을 관통하여 니들 어레이의 가공이 불가능하였다. 따라서, 공작물의 가공 경계값을 넘기 위한 레이저 빔 조사 횟수로 가공하여 열에너지를 공급하는 것이 바람직하다.
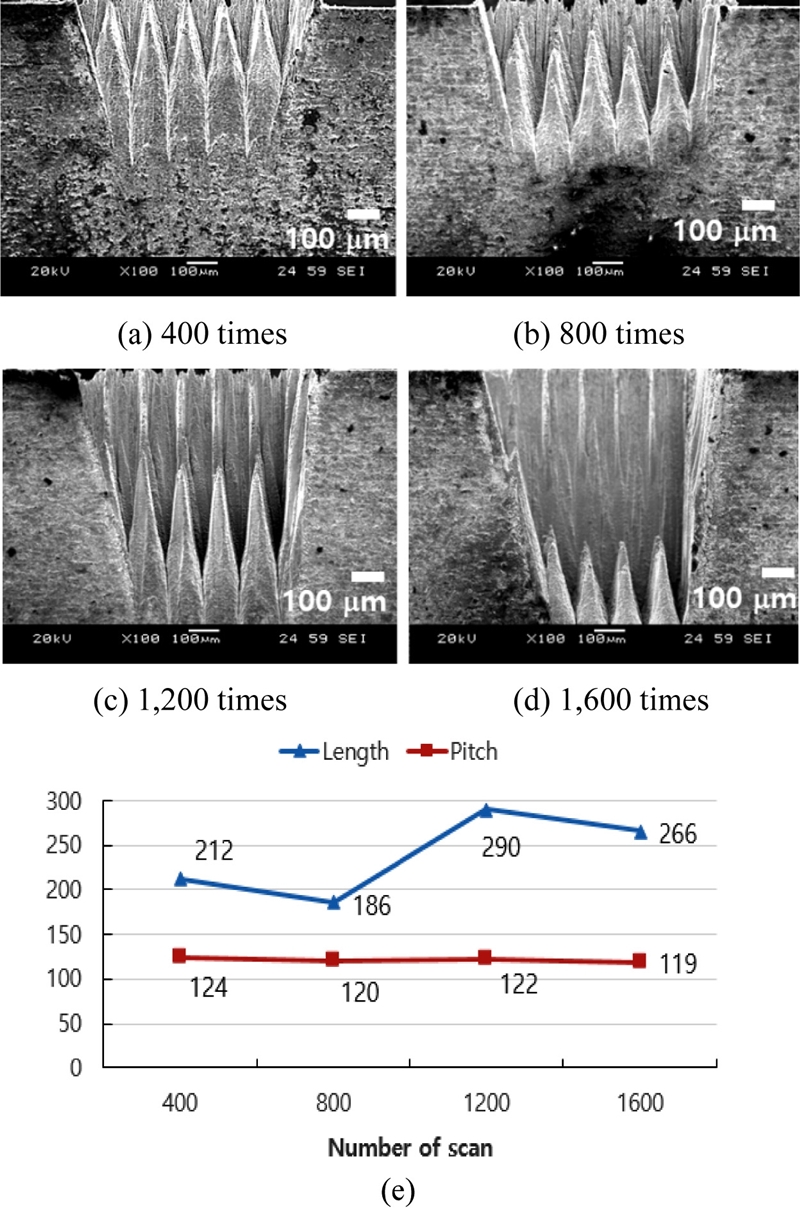
(a), (b), (c), (d) Fabricated micro needle arrays according to number of laser scan, and (e) Measured specific value of needle
레이저 빔 가공은 공작물의 부피, 열에너지의 축적 및 열전달에 따라 가공 양상이 변한다. 그러나 앞서 수행한 실험 결과로부터 레이저 빔의 출력과 조사 횟수 등 가공 조건에 변화를 주는 것만으로는 니들의 형상 조절에 한계가 있음을 확인하였다. 따라서 니들 길이와 피치를 조절하기 위해서 조사되는 레이저 빔의 경로를 조합하는 것이 반드시 필요하다.
3.2 라인 스페이스에 따른 가공 특성
라인 스페이스는 레이저 가공 경로가 지나지 않는 비어있는 곳으로 마이크로 니들이 형성되는 부분이다. Fig. 5는 라인 스페이스를 50, 100, 200 μm로 변경하며 가공한 마이크로 니들의 형상을 보여준다. 레이저 빔의 출력은 14 W를 유지하였으며, 라인 인터벌은 20 μm, 레이저 빔 라인 수는 16줄의 조건으로 350회 조사하여 가공하였다. 라인 스페이스가 증가할수록 레이저 빔의 열에너지의 영향을 받지 않는 비가공 부위가 넓어지므로 결과물의 상단부 편평한 부분 넓이가 증가함을 확인할 수 있다. Fig. 5(a)의 경우 입력된 라인스페이스 수치인 50 μm 대비하여 실제 영역의 너비가 26.3 μm로 가공률이 가장 높았다. 즉, 비가 공 영역의 너비(라인 스페이스)가 좁을수록 공작물의 부피 대비열의 축적이 높게 일어나므로 뾰족한 팁 반경의 니들을 가공하기에 용이하다.
3.3 라인 인터벌에 따른 가공 특성
Fig. 6은 각 레이저 빔 사이의 간격인 라인 인터벌을 변경하며 가공된 마이크로 니들 어레이의 사진이다. 출력 10 W, 라인 스페이스 50 μm, 라인 수 6줄의 조건으로 400회 조사하여 가공하였다. 라인 인터벌이 10에서 20 μm로 증가하면서 레이저 빔의 중첩 간격이 넓어지게 되고, 가공된 니들의 길이와 피치가 증가하게 된다. Fig. 6(c)의 라인 인터벌 30 μm 경우 완전한 니들을 가공하지 못하고, 작은 크기의 원뿔 가공 결과가 산재함을 확인할 수 있다. 이는 레이저 빔 중첩률이 낮아져서 모재 기화에 필요한 열에너지의 축적이 부족하기 때문이다. 침투용 니들에 필요한 관통 성능을 얻기 위해서는 니들의 팁 반경이 작을수록 유리하며, 라인 인터벌이 좁은 Fig. 6(a)의 경우 5.7 μm의 팁 반경으로 가장 뾰족하게 가공됨을 확인하였다.
3.4 라인 수에 따른 가공 특성
Fig. 7은 레이저 빔 라인 수를 변경하며 가공된 마이크로 니들 어레이의 사진이다. 출력 10 W, 라인 스페이스 50, 라인 인터벌 10 μm의 조건으로 400회 조사하여 가공하였다. 조사되는 레이저 빔 라인 수가 증가함에 따라 마이크로 니들간 피치가 넓어짐을 확인하였다. 라인의 수는 레이저 가공 시 필요한 열에너지의 축적량과 비례하므로 공작물의 가공 깊이가 깊어져 니들의 길이가 증가하게 된다. 관통 성능에 유리하도록 단위 면적당 압력을 높이기 위해서는 레이저 빔 라인의 수를 증가시켜 니들 사이의 피치와 길이를 증가시키는 것이 바람직하다.
4. 마이크로 니들의 관통력 측정
마이크로 니들의 전극 및 약물 주사 적용성을 확인하기 위하여 관통력을 측정한다. Fig. 8은 측정에 사용된 25 mm2의 대면적 텅스텐 마이크로 니들 어레이다. 팁 반경 2.3, 길이 507, 기둥 밑 직경 230 (세장비 2.2), 피치 310 μm로 가공하였으며 Table1의 레이저 빔 가공/경로 조건을 사용하였다. 니들이 대상물을 관통하는데 유리하도록 팁 반경을 줄이고 피치를 넓히는 조건을 선택하여 제작하였다. Fig. 9는 3축 정밀 이송스테이지를 기반으로 구축된 니들의 관통력 측정 시스템 개략도이다. X, Y축에 틸팅 스테이지를 설치하여 관통하고자 하는 대상물의 수평을 조정하도록 하였다. Z축에 로드셀 시스템을 장착하고 끝 부분에 마이크로 니들을 부착하여 수직 이송시키며 돼지고기 피부와 젤라틴 합성물의 관통력을 측정하였다. 젤라틴 합성물은 인체피부 조직을 모사하기 위하여 젤라틴과 물 1 : 5 중량비로 70°C 가열 용해 후 2시간 서냉 응고시켜 사용하였다.
Fig. 10(a)는 가공된 마이크로 니들과 젤라틴 합성물 간의 관통력과 초고속 카메라를 이용하여 관통 단계를 측정한 결과이다. Fig. 10(a)의 (i) 영역은 니들이 젤라틴의 탄성을 이겨내고, 관통이 시작되는 단계를 나타내며, 시작점으로부터 Z축 수직 지면 방향으로 약 140 μm 이송되었을 때 0.103 N의 최대 관통력을 갖는다. Fig. 10(a)의 (ii) 영역에서는 니들이 지속적으로 이송되면서 관통된 부분 이외의 젤라틴이 니들 위를 덮어가는 단계이다. 젤라틴의 항복점을 지나고 니들과 젤라틴 간의 상대적 움직임이 발생하기 때문에 관통력은 점차 감소됨을 확인할 수 있다. Fig. 10(a)의 (iii) 영역은 니들과 젤라틴 간의 상대적 움직임을 해소하고, 관통력이 평형을 유지하는 부분이며, 니들 원뿔 밑부분이 젤라틴과 접촉하는 면적이 늘어나면서 미세하게 측정 힘이 증가함을 확인할 수 있다. Fig 10(b)는 동일한 로드셀 시스템을 이용하여 돼지고기 피부와 젤라틴의 관통력을 측정한 결과이다. 돼지고기 피부의 경우, 약 180 μm 이송하였을 때 대상물과 니들 간의 관통력이 0.122 N으로 측정되었으며, 젤라틴에서 측정한 결과와 0.019 N의 차이를 보였다. 이는 젤라틴과 돼지고기 피부 간의 항복 특성 차이에 인한 결과로 볼 수 있으며, 본 연구에서 가공된 마이크로 니들의 팁 반경과 피치의 조합으로 약 0.11 N의 관통력이 발생할 수 있음을 확인하였다.
5. 결론
레이저 빔 가공법을 이용하여 텅스텐 마이크로 니들 어레이를 가공하는 연구를 수행하였다. 마이크로 니들을 제작하기 위한 기존 MEMS 및 다단계 적층 공정법과 달리 1,064 nm 파장영역의 근적외선 레이저만을 이용하여 텅스텐 니들을 가공하는 원스텝 공정을 소개하였다. 의학용 마이크로 약물 주사와 신경전극으로 사용하기 위한 마이크로 니들은 탄성을 갖는 피부 조직을 관통하기에 유리한 형상으로 가공해야 한다. 가우시안 분포를 따르는 레이저 빔의 출력 강도 경향과 열에너지 축적을 이용하여 모재를 기화시켜 가공하는 레이저 빔 가공법의 특성상 출력과 조사 횟수 등의 가공 조건을 조절하여 결과물 형상을 변화시키는데 한계가 있다. 본 논문에서는 레이저 빔 가공 조건이외에 라인 스페이스, 라인 인터벌 및 라인 수 등 레이저 빔의 조사 경로를 조절하여 마이크로 니들의 피치와 길이 변화를 확인하였다.
진행된 파라미터 실험 결과를 바탕으로 팁 반경 2.3, 길이 507, 피치 310 μm의 25 μm2 마이크로 니들 어레이를 가공하였다. 돼지고기 피부와 젤라틴 합성물 및 니들 간의 관통력을 측정하여 각각 0.122, 0.103 N의 결과를 얻음으로써, 가공된 마이크로 니들의 약물 주사 및 신경 전극으로의 적용성을 확인하였다.
Acknowledgments
이 성과는 정부(과학기술정보통신부)의 재원으로 한국연구재단의 지원을 받아 수행된 연구임(No. NRF-2019R1F1A1056012).
REFERENCES
-
Sivamani, R. K., Liepmann, D., and Maibach, H. I., “Microneedles and Transdermal Applications,” Expert Opinion on Drug Delivery, Vol. 4, No. 1, pp. 19-25, 2007.
[https://doi.org/10.1517/17425247.4.1.19]
- Lee, H. J., Jeon, H., Park, S. J., Lee, H. W., and Bae, S., “Micro Needle Array Fabrication for Drug Delivery and Drug Delivery Evaluation Test Using Optical Inspection Module,” Proc. of the International Conference on Nanotechnology and Biosensors, Vol. 2, pp. 101-104, 2011.
-
Kim, Y. C., Park, J. H., and Prausnitz, M. R., “Microneedles for Drug and Vaccine Delivery,” Advanced Drug Delivery Reviews, Vol. 64, No. 14, pp. 1547-1568, 2012.
[https://doi.org/10.1016/j.addr.2012.04.005]
-
Van Der Maaden, K., Jiskoot, W., and Bouwstra, J., “Microneedle Technologies for (Trans) Dermal Drug and Vaccine Delivery,” Journal of Controlled Release, Vol. 161, No. 2, pp. 645-655, 2012.
[https://doi.org/10.1016/j.jconrel.2012.01.042]
-
Wang, L. F., Liu, J. Q., Yan, X. X., Yang, B., and Yang, C. S., “A MEMS-Based Pyramid Micro-Needle Electrode for Long-Term EEG Measurement,” Microsystem Technologies, Vol. 19, No. 2, pp. 269-276, 2013.
[https://doi.org/10.1007/s00542-012-1638-2]
-
Ashraf, M. W., Tayyaba, S., and Afzulpurkar, N., “Micro Electromechanical Systems (MEMS) Based Microfluidic Devices for Biomedical Applications,” International Journal of Molecular Sciences, Vol. 12, No. 6, pp. 3648-3704, 2011.
[https://doi.org/10.3390/ijms12063648]
-
Yang, G., Gaines, J. A., and Nelson, B. J., “A Supervisory Wafer-Level 3D Microassembly System for Hybrid MEMS Fabrication,” Journal of Intelligent and Robotic Systems, Vol. 37, No. 1, pp. 43-68, 2003.
[https://doi.org/10.1023/A:1023982907874]
-
Lee, S. W., Shin, H. S., and Chu, C. N., “Fabrication of Micro-Pin Array with High Aspect Ratio on Stainless Steel Using Nanosecond Laser Beam Machining,” Applied Surface Science, Vol. 264, pp. 653-663, 2013.
[https://doi.org/10.1016/j.apsusc.2012.10.087]
-
Dubey, A. K. and Yadava, V., “Laser Beam Machining-A Review,” International Journal of Machine Tools and Manufacture, Vol. 48, No. 6, pp. 609-628, 2008.
[https://doi.org/10.1016/j.ijmachtools.2007.10.017]
-
Park, J. W., Kim, H., Kim, J. G., and Chu, C. N., “Fabrication of Various Shaped Tungsten Micro Pin Arrays Using Micro Carving Technology,” Precision Engineering, Vol. 47, pp. 389-396, 2017.
[https://doi.org/10.1016/j.precisioneng.2016.09.012]
-
Gómez, D. and Goenaga, I., “On the Incubation Effect on Two Thermoplastics When Irradiated with Ultrashort Laser Pulses: Broadening Effects When Machining Microchannels,” Applied Surface Science, Vol. 253, No. 4, pp. 2230-2236, 2006.
[https://doi.org/10.1016/j.apsusc.2006.04.036]
Professor in the Department of Mechanical Design Engineering, Dongyang Mirae University. His research interest is non-traditional machining.
E-mail: jongwukpark@dongyang.ac.kr
Professor in the Department of Mechanical Engineering, Dongyang Mirae University. His research interest is non-traditional machining.
E-mail: haan86@dongyang.ac.kr
Student in the School of Medicine, Kyungpook National University. His research interest is general medical therapy.
E-mail: dkdhdh@knu.ac.kr