
용융전기방사를 이용한 두꺼운 미세섬유 매트의 제작
Copyright © The Korean Society for Precision Engineering
This is an Open-Access article distributed under the terms of the Creative Commons Attribution Non-Commercial License (http://creativecommons.org/licenses/by-nc/3.0) which permits unrestricted non-commercial use, distribution, and reproduction in any medium, provided the original work is properly cited.
Abstract
Recently, porous structures of nano/microfibers are receiving great attention because of their excellent mechanical properties, surface area to volume ratio, and permeability. In this study, thick microfiber mats were fabricated using a melt-electrospinning process in a controlled manner. A melt-electrospinning equipment including a three-axis precision motion control with pneumatic dispensing was constructed. The diameter and deposition pattern of melt-electrospun microfibers with respect to the barrel temperature and pressure were investigated. Based on identified effects of process conditions on microfiber geometry, thick microfiber mats with various properties were successfully fabricated using melt-electrospinning with snake scanning and iterative layering. Their mechanical properties and porosities were then compared and analyzed.
Keywords:
Microfiber mat, Melt-electrospinning, Buckling, Snake scanning키워드:
미세섬유 매트, 용융전기방사, 좌굴, 사행 스캔1. 서론
최근 다양한 다공성 구조물에 대한 관심이 높아짐에 따라 미세섬유 제조와 관련한 다양한 연구가 활발히 이뤄지고 있다.1-3 이러한 다공성 구조물에는 거품(Foam)구조, 입자구조, 섬유구조 등 다양한 형태가 제시되어 있으며, 이러한 구조물 중 미세섬유 구조물은 높은 부피대비 표면적, 유연성을 가지면서도 높은 강도 등의 우수한 기계적 물성치를 가지고 있어 다양한 분야에 활용되고 있다.1 최근까지 다양한 미세섬유 제조기술이 개발되고 있으며, 그 대표적인 방법으로 전기방사기술(Electrospinning), 드로잉(Drawing), 멜트-블로잉(Melt-Blowing) 등이 있다.4
용융전기방사법(Melt-Electrospinning)은 일반적인 용액전기방사법(Solution-Electrospinning)이 유기용매를 이용하는 것과는 달리 열가소성 소재를 열에 직접 녹여 액상에서 전기방사하는 차이가 있다. 이러한 점으로 인해 용액전기방사법에 비해 사용할 수 있는 소재에 제한이 있는 단점이 있으나, 인체와 환경에 영향을 미칠 수 있는 유기용매를 사용하지 않으며, 이로 인해 생산비 측면에서의 이점이 존재한다. 특히 이 방식은 최근 많은 관심을 받고 있는 용융압출(Melt-Extrusion) 3차원 프린팅과의 공정 유사성이 높고, 용융압출 3차원 프린팅에 비해 10% 이하의 작은 섬유 직경을 가지는 특징이 있다. 그러나 미세섬유의 좌굴(Buckling) 현상으로 인해 형상 제어에 어려움이 있다.5
최근까지 용융전기방사와 관련된 다양한 연구가 진행되어 왔다. Dayan 등은 콜렉터 속도, TCD, 압력 및 인가전압과 같은 파라미터에 의한 섬유 직경 모델을 제안하였다.6 Zhmayev 등은 용융전기방사의 안정된 제트 영역에서 전기적으로 충전된 점탄성 유체의 비등온(Non-Isothermal), 자유표면유동(Free Surface Flow)에 대한 모델을 개발하여 온도, 전압, 유량에 따른 노즐의 직경 변화 실험값과 비교 분석하였다.7 Wunner 등은 미세섬유의 적층된 높이에 따른 Taylor Cone의 변화와 섬유 적층 거동에 미치는 영향에 대하여 분석하였다.8 Yang 등은 저밀도 폴리에틸렌을 사용하여 용융전기방사의 온도 조건이 고분자의 유량에 미치는 영향을 연구하였다.9 Lyons 등은 다양한 용융전기방사 파라미터가 폴리프로필렌의 형태 및 섬유 직경에 미치는 영향을 연구하였다.10 Ko 등은 용융전기방사를 이용하여 원형 패턴의 생성 및 제작 조건이 원형 패턴에 미치는 영향을 분석하였다.11 Ogata 등은 CO2 레이저 용융 장치가 장착된 새로운 용융전기방사시스템을 개발하였다.12 현재까지 섬유의 거동에 대한 다양한 연구가 수행되었으나, 좌굴 형상이 포함된 미세섬유로 구성된 두꺼운 섬유 매트의 제작과 관련한 연구를 찾기 어렵다. 특히, 충분한 두께를 가지면서도 두께에 대한 제어 가능성을 제시할 경우 미세섬유로 구성되어 높은 다공성과 충분한 유연성 및 강도를 가질 수 있으므로, 조직공학의 지지체(Scaffold),13,14 골유도재생(Guided Bone Regeneration)을 위한 맴브레인,15,16 창상치료(Wound Healing)용 패치,17,18 다양한 효소의 담체19-21로 활용될 수 있는 등 그 산업적 가치가 높다.
본 연구에서는 용융전기방사법을 이용하여 미세섬유로 구성된 두꺼운 매트의 제작하고, 특성을 조절할 수 있음을 보였다. 이를 위해 용융전기방사장치를 구성하고, 공정조건에 따른 섬유의 거동을 분석하였으며, 이를 토대로 좌굴 거동을 가진 미세섬유로 구성된 약 3 mm 두께의 미세섬유 매트를 제작하고, 그 특성을 평가하였다.
2. 용융전기방사 실험
용융전기방사공정을 위한 실험 장치를 구성하였다. 개발된 장비는 배럴(Barrel)에 담긴 고분자 팰렛(Pellet)을 용융시키기 위해 배럴 외부에 원통형 히터(TCD-200 EX, Iwashita Engineering, Inc.)가 부착되어 있으며, 정밀 공압제어(AD 3000C, Iwashita Engineering, Inc.)를 통해 용융된 고분자를 노즐로 토출할 수 있도록 하였다. 사용된 노즐(Nozzle)은 스테인레스강 재질이며, 내경은 0.3 mm이었다. 이때 노즐과 집적판(Collector) 사이에는 고압의 정전기장이 고전압발생기를 통해 부가되었다. 특히 본 연구에서는 금속 배럴에 부착된 히터의 전기충격을 방지하기 위해 노즐에는 기저전압을 부가하고, 알루미늄 집적판에 양의 전압을 부가하였다. 특히 3축 자유도를 가진 직교형 이송 장치를 배럴-노즐(Z축)과 집적판(X-Y축)에 연결하고, 그 운동을 CNC(Computer Numerical Control) 제어기(PMAC2A, DeltaTau)를 이용하여 제어하였다. 특히 실험 장치는 실험 조건이 외부 온도와 습도에 영향을 적게 받을 수 있도록 아크릴 상자 내부에 설치되었다. Figs. 1(a)는 실험 장치의 간단한 구성을 보여주며, 1(b)는 연구에 사용된 연구에 사용된 실험 장치를 보여준다.
용융전기방사의 고분자는 생체적합성이며 생체흡수성 소재로 잘 알려져 생체재료 제작에 자주 사용되고 있는 팰렛 형태의 PCL (Polycaprolactone, Polyscience, USA)이었다. 사용된 PCL은 중량-평균 분자량이 43,000-50,000이었다.
본 연구에서 사용된 용융전기방사공정의 실험 조건은 Table 1과 같이 정리할 수 있다. 노즐과 집적판 사이의 거리는 15 mm이었으며, 노즐과 집적판의 전압차는 12 kV로 하였다. 노즐은 제자리에 있지 않고, 레스터 스캔 방식을 이용해 균일한 두께를 얻어질 수 있도록 하였으며, 이때 노즐의 스캔 속도는 30 mm/s이었다. 본 연구에서는 배럴의 온도와 압력에 따른 미세섬유의 직경 및 좌굴 거동을 확인하였다. 이를 위해 배럴의 온도는 90, 120, 150oC, 배럴의 압력은 150, 300, 450 kPa로 각각 세 경우였다.
3. 실험 결과의 분석
3.1 배럴 온도의 영향
Table 1의 조건에서 배럴의 압력을 300 kPa로 고정시키고, 배럴의 온도가 90, 120, 150oC일 때의 용융전기방사된 미세섬유를 분석하였다. Figs. 2(a)부터 2(c)는 세 가지 조건에서 방사된 미세섬유를 보여준다. Figs. 2(a)부터 2(c)에서 볼 수 있는 바와 같이 온도에 따라 미세섬유의 직경이 달라짐을 확인할 수 있으며, 그 경향은 2(d)에서 정리되었다. 각 조건의 평균 직경을 측정한 결과 90oC에서는 약 43 μm이고, 120oC에서는 약 39 μm, 150oC에서는 약 31 μm이었다. 각 조건에서의 섬유 직경 평균치 대비 표준편차는 1.68, 3.74, 5.77%로 확인되어 비교적 일정한 섬유가 방사되고 있음을 알 수 있었다. 이러한 현상은 배럴 온도가 낮을수록 PCL 용융액의 점도가 높고, 경화되는 시간도 짧아 섬유의 연신이 상대적으로 어렵기 때문이다.
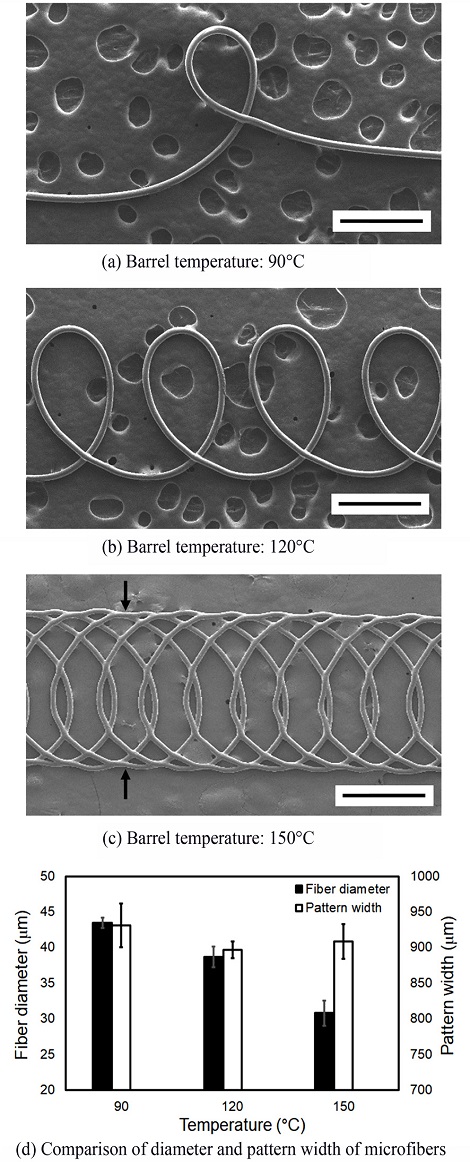
Microfibers melt-electrospun under three different barrel temperature conditions (Scale bars in (a)-(c) correspond to 500 μm. Distance between the arrowheads in (c) corresponds to pattern width)
Figs. 2(a)부터 2(c)에서 배럴의 온도 조건에 따라 섬유의 좌굴 형상이 다름을 알 수 있다. 배럴 온도가 낮을 때에 비해 높을 때 원형 형상이 보다 일정하게 나왔음을 볼 수 있다. 이는 해당 온도에서의 미세섬유의 경화도와 직경에 따라 섬유의 총 길이, 굽힘저항(Bending Resistance) 및 휘핑 운동(Whipping Motion)이 영향을 받아 원형 곡선으로 집적판에 집적되며, 집적판의 병진 방향 이동에 따라 그림과 같은 형상을 가지게 된다. 특히 Figs. 2(a)와 2(b)는 완전한 원형 곡선을 가지는데 필요한 시간보다 집적판의 병진 운동이 빨라 완전한 원형 곡선을 가지지 못했으나, 2(c)는 원형곡선이 집적되는 속도가 집적판의 병진속도에 비해 충분히 빨랐음을 알 수 있다. 그러나 각 조건별로 일관성 있게 해당 패턴이 반복됨을 확인하였다. 따라서 각 좌굴 패턴이 가지는 패턴의 폭을 측정하였으며, Fig. 2(d)에서 보인 바와 같이 배럴 온도에 상관없이 패턴폭은 비교적 유사한 수준에 있었다.
3.2 배럴 압력의 영향
배럴의 온도 조건 세 가지 중 가장 안정한 패턴 품질을 보인 150oC를 배럴의 온도로 고정하고 나머지의 조건은 Table 1의 조건을 따른 상태에서 배럴의 압력을 150, 300, 450 kPa으로 서로 다르게 가할 때의 용융전기방사된 미세섬유를 분석하였다. Figs. 3(a)부터 3(c)는 각 압력 조건에서 방사된 미세섬유를 보여주며, 이로부터 배럴의 압력 조건에 따라 미세섬유의 직경이 달라짐을 알 수 있다. 또한 그 값은 Figs. 3(d)에서 확인할 수 있으며, 3(a)부터 3(c)에서 보인 바와 같이 압력이 커질수록 직경도 증가함을 확인할 수 있다. 방사된 섬유의 평균 직경은 150 kPa에서는 약 23 μm, 300 kPa에서는 약 31 μm, 450 kPa에서는 약 37 μm이었다. 또한 각 조건의 평균 섬유 직경 대비 표준편차는 각각 4.66, 5.77, 6.51%로 측정되었다. 이는 배럴의 토출압력이 증가함에 따라 토출유량이 증가함으로 인해 방사된 섬유의 커진 것임을 알 수 있다.
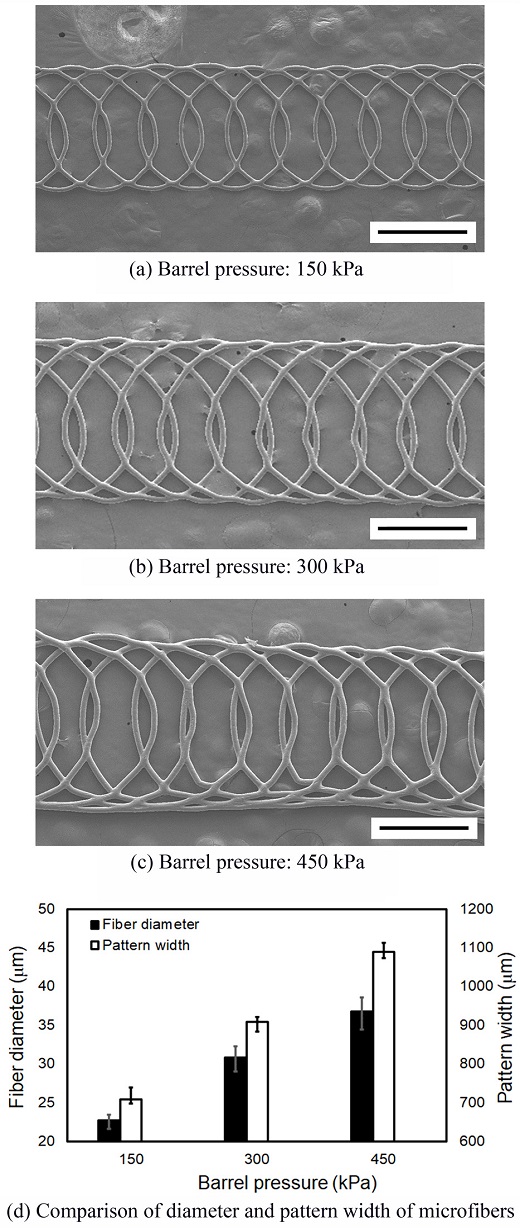
Microfibers melt-electrospun under three different barrel pressure conditions (Scale bars in (a)-(c) correspond to 500 μm)
배럴 압력에 따른 직경의 변화와 함께 Figs. 3(a)부터 3(c)는 압력 조건에 따른 섬유의 좌굴 형상도 보여준다. Fig. 3(d)에서 보인 바와 같이 배럴 압력이 증가함에 따라 섬유의 직경이 증가하는 현상과 유사한 추세를 가지며, 원형 패턴의 폭도 같이 증가하였다. 이는 배럴 압력의 증가에 따라 토출량이 증가하므로, 섬유 직경의 증가와 함께 원형 곡선의 반경도 커진 것으로 추정된다. 비록, 곡률 반경은 증가하였으나 패턴의 형상은 유사한 수준에 있음을 알 수 있다.
3.3 미세섬유 구조물의 제작
앞에서 제시한 배럴의 압력 조건(150, 300, 450 kPa)을 이용하여 3 mm의 두께를 가지는 미세섬유 구조물을 제작하였다. 이는 Fig. 3에서 보인 원형 패턴을 가진 미세섬유로 구성된 3차원 구조물을 제작하기 위한 것으로서 충분한 다공성과 함께 기계적인 물성치도 가질 수 있는 장점이 있다. Fig. 3에서 보인 패턴 특성을 유지하면서도 3 mm의 두께의 두꺼운 매트를 제작하기 위해 각 층별로 사행 스캔(Snake Scan) 방식을 이용하여 집적판을 이송하며 집적하도록 하였다. 특히 각 층은 서로 직교하도록 하였으며, 스캔피치(Scan Pitch)는 0.6 mm로 하였다. 두께는 해당 조건으로 제작하며, 두께가 3 mm가 될 때까지 반복적으로 적층하였다. 제작된 매트의 두께 편차는 3.5% 이내였다.
Fig. 4(a)는 배럴 압력이 150 kPa인 경우 제작된 미세섬유 매트를 보여준다. Fig. 4(a)로부터 제작된 매트의 모서리 부분은 구배를 가지나, 최상층은 비교적 평면의 형태를 가짐으로부터 두께가 일정한 매트가 성공적으로 제작되었음을 알 수 있다. 각 배럴 압력 조건으로 제작된 매트의 치수는 22 × 35 × 3mm3이었다. 각 조건에 따라 섬유의 직경은 서로 다르나 유사한 형상을 가짐을 확인하였다. Figs. 4(b)부터 4(d)는 각 압력 조건하에서 제작된 미세섬유 3차원 구조물의 표면을 보여준다. 그림에서 보인 바와 같이 여러 층이 적층되어 있기 때문에 복잡한 섬유구조를 확인할 수 있으나, 각 섬유는 Fig. 3에서 보인 바와 같은 원형 패턴을 유지하고 있음을 알 수 있다. 또한 많은 공극이 확인되며, 이로부터 목적한 바와 같이 미세섬유로 구성된 다공성 구조물이 제작되었음을 알 수 있다.
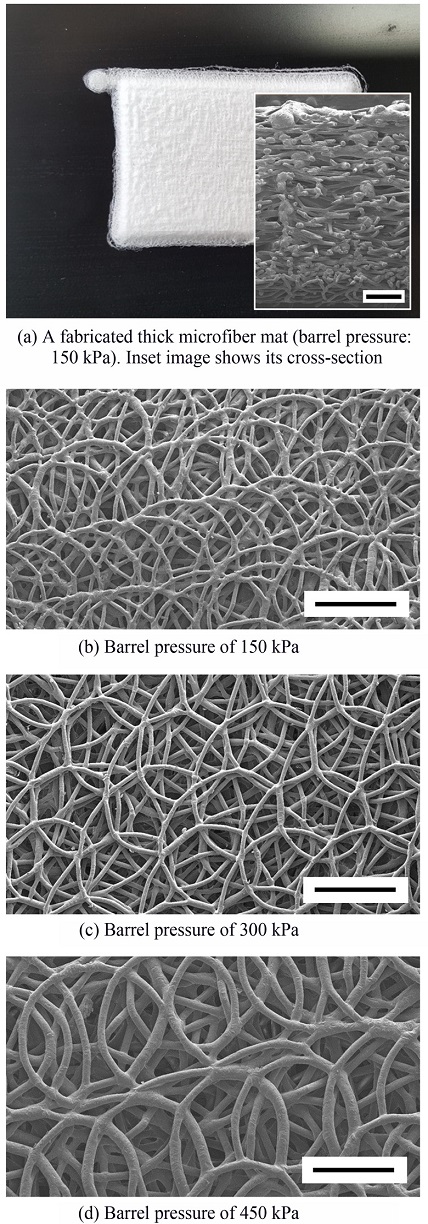
Thick microfiber mats melt-electrospun under three different barrel pressure conditions (Scale bars in (a)-(d) correspond to 500 μm)
Fig. 3에서 보인 바와 같이 각 배럴의 압력 조건에 따라 섬유의 직경과 집적 패턴이 다르므로 각 조건별로 층의 두께가 달라질 수 있다. Fig. 5는 세 조건의 미세섬유 구조물의 섬유 직경의 분포를 비교한 결과를 보여준다. Fig. 5로부터 직경분포는 압력 조건에 따라 최빈값이 구별되도록 분포되어 있으며, 일정 분포를 가지고 존재함을 알 수 있다. 이로부터 각 압력분포에 따라 섬유 직경에서 확연한 차이를 가짐을 알 수 있다. Table 2는 각 배럴의 압력 조건별로 3 mm 두께를 가진 미세섬유 구조물 제작을 위해 적층한 층의 개수 및 이로부터 계산된 평균 층 두께를 보여준다. Table 2에서 확인할 수 있는 바와 같이 단위시간당 토출량이 제일 작은 150 kPa의 배럴 압력 조건의 경우 72층을 적층하였으며, 이때 평균 층 두께는 42 μm이었다. 단위시간당 토출량이 더 큰 300, 450 kPa의 경우는 각각 56층과 32층을 적층하였으며, 평균 층 두께는 52, 94 μm이었다. 이로부터 각 조건별로 구조물의 높이에 맞는 층 개수를 조절할 필요가 있음을 알 수 있다. 층 두께의 차이로 인해 제작 시간은 배럴 압력이 증가함에 따라 감소하였다.
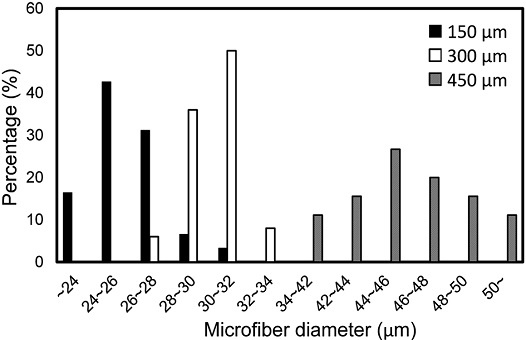
Comparison of diameter distribution of microfibers melt-electrospun under three different barrel pressure conditions

Number of layers, layer thickness, and fabrication time of microfibers melt-electrospun under three different barrel pressure conditions
제작된 매트의 기계적 특성과 공극률을 확인하였다. 기계적 물성을 조사하기 위해 소형 만능시험기(No. 3344, Instron)를 이용하여 압축 하중이 주어졌을 때의 압축계수(Compressive Modulus)를 얻었다. 또한 샘플의 부피에 대한 무게로부터 공극률을 계산하여 비교하였다. 우선 압축시험과 공극률 계산을 위해 세 가지 배럴 압력 조건 하에서 제작된 샘플을 절단(Punching)하여 직경 5, 두께 3 mm의 시편을 조건별로 5개씩 준비하였다. 압축시험 시 압축속도(Cross-Head Speed)는 0.5 mm/min으로 하였다. 공극률은 디스크 형태 시편의 공칭부피(Nominal Volume)와 시편의 무게, 사용된 PCL 고분자의 밀도를 이용하여 계산하였다.
Fig. 6(a)는 압축시험을 통해 얻어진 세 가지 종류의 매트 시편에 대한 응력-변형률 선도를 보여준다. Fig. 6(a)에서 알 수 있듯이 세 종류의 시편 모두 일반적인 고분자 압축거동을 보임을 알 수 있으며, 사용된 배럴 압력이 클수록 동일한 변형률에 대해 더 큰 응력이 요구됨을 알 수 있다. 또한 종류에 따라 다르지만 약 30%의 변형률 이상에서까지 응력과 변형률 간에 선형적인 특성을 가짐을 알 수 있다. 선형 구간에서의 응력-변형률 거동으로부터 압축계수를 얻었으며, 이는 Fig. 6(b)에서 비교하여 제시하였다. Fig. 6(b)로부터 더 높은 배럴 압력 조건에서 더 큰 압축계수를 가짐을 알 수 있다. 또한 압축계수가 높을수록 탄성저장에너지(Resilience)가 작아짐을 확인하였다. 이와 함께 압축 시험 전 미리 계산된 공극률 또한 Fig. 6(b)에서 같이 비교되었으며, 배럴 압력이 클수록 공극률이 작아지며, 동일 부피에 더 많은 고분자가 집적되어 있음을 알 수 있다. 이상으로부터 공극률이 섬유 직경과 함께 압축계수, 탄성저장에너지에 영향을 주었을 것으로 추정할 수 있다.
4. 결론
본 연구에서는 최근 많은 관심을 받고 있는 섬유 기반의 다공성 구조물 용융전기방사법을 이용하여 제작할 수 있음을 보였다. 이를 위해 3축 정밀제어와 공압식 토출 장치를 포함한 용융전기방사장치를 구성하였다. 융융전기방사에서 배럴의 온도와 압력에 따른 미세섬유의 직경 및 집적/좌굴 형상을 분석하였으며, 20-50 μm 수준의 직경을 가진 미세섬유를 방사하고, 그 형상을 조절할 수 있음을 보였다. 이를 바탕으로 정밀운동제어를 기반으로 한 미세섬유의 사행 스캔 집적 및 반복 적층을 통해 기존 연구에서 찾아보기 힘든 미세섬유로 구성된 약 3 mm 두께의 미세섬유 매트를 제작하고, 압축계수와 공극률을 비교하고 분석하였다.
Acknowledgments
이 논문은 2018, 2020년도 정부(과학기술정보통신부)의 재원으로 한국연구재단, 정보통신기획평가원의 지원을 받아 수행된 연구임(2020-0-01519, Nos. NRF2018R1A2B2009540 & NRF2020R1A4A1018652).
REFERENCES
-
Huang, Z. M., Zhang, Y. Z., Kotaki, M., and Ramakrishna, S., “A Review on Polymer Nanofibers by Electrospinning and Their Applications in Nanocomposites,” Composites Science and Technology, Vol. 63, No. 15, pp. 2223-2253, 2003.
[https://doi.org/10.1016/S0266-3538(03)00178-7]
-
Zhao, G., Gong, S., Wang, H., Ren, J., Wang, N., et al., “Ultrathin Biocompatible Electrospun Fiber Films for Self-Powered Human Motion Sensor,” International Journal of Precision Engineering and Manufacturing-Green Technology, Vol. 8, No. 3, pp. 855-868, 2021.
[https://doi.org/10.1007/s40684-020-00246-y]
-
Kim, H. C., Kim, D., Lee, J. Y., Zhai, L., and Kim, J., “Effect of Wet Spinning and Stretching to Enhance Mechanical Properties of Cellulose Nanofiber Filament,” International Journal of Precision Engineering and Manufacturing-Green Technology, Vol. 6, No. 3, pp. 567-575, 2019.
[https://doi.org/10.1007/s40684-019-00070-z]
-
Ramakrishna, S., “An Introduction to Electrospinning and Nanofibers,” World Scientific, 2005.
[https://doi.org/10.1142/5894]
-
Lee, J., Lee, S. Y., Jang, J., Jeong, Y. H., and Cho, D. W., “Fabrication of Patterned Nanofibrous Mats Using Direct-Write Electrospinning,” Langmuir, Vol. 28, No. 18, pp. 7267-7275, 2012.
[https://doi.org/10.1021/la3009249]
-
Dayan, C. B., Afghah, F., Okan, B. S., Yıldız, M., Menceloglu, Y., et al., “Modeling 3D Melt Electrospinning Writing by Response Surface Methodology,” Materials & Design, Vol. 148, pp. 87-95, 2018.
[https://doi.org/10.1016/j.matdes.2018.03.053]
-
Zhmayev, E., Zhou, H., and Joo, Y. L., “Modeling of Non-Isothermal Polymer Jets in Melt Electrospinning,” Journal of Non-Newtonian Fluid Mechanics, Vol. 153, Nos. 2-3, pp. 95-108, 2008.
[https://doi.org/10.1016/j.jnnfm.2007.11.011]
-
Wunner, F. M., Wille, M. L., Noonan, T. G., Bas, O., Dalton, P. D., et al., “Melt Electrospinning Writing of Highly Ordered Large Volume Scaffold Architectures,” Advanced Materials, Vol. 30, No. 20, Paper No. 1706570, 2018.
[https://doi.org/10.1002/adma.201706570]
-
Deng, R., Liu, Y., Ding, Y., Xie, P., Luo, L., et al., “Melt Electrospinning of Low-Density Polyethylene Having a Low-Melt Flow Index,” Journal of Applied Polymer Science, Vol. 114, No. 1, pp. 166-175, 2009.
[https://doi.org/10.1002/app.29864]
-
Lyons, J., Li, C., and Ko, F., “Melt-Electrospinning Part I: Processing Parameters and Geometric Properties,” Polymer, Vol. 45, No. 22, pp. 7597-7603, 2004.
[https://doi.org/10.1016/j.polymer.2004.08.071]
-
Ko, J., Mohtaram, N. K., Ahmed, F., Montgomery, A., Carlson, M., et al., “Fabrication of Poly (ε-Caprolactone) Microfiber Scaffolds with Varying Topography and Mechanical Properties for Stem Cell-Based Tissue Engineering Applications,” Journal of Biomaterials Science, Polymer Edition, Vol. 25, No. 1, pp. 1-17, 2014.
[https://doi.org/10.1080/09205063.2013.830913]
-
Ogata, N., Yamaguchi, S., Shimada, N., Lu, G., Iwata, T., et al., “Poly (Lactide) Nanofibers Produced by a Melt-Electrospinning System with a Laser Melting Device,” Journal of Applied Polymer Science, Vol. 104, No. 3, pp. 1640-1645, 2007.
[https://doi.org/10.1002/app.25782]
-
Moroni, L., De Wijn, J., and Van Blitterswijk, C., “3D Fiber-Deposited Scaffolds for Tissue Engineering: Influence of Pores Geometry and Architecture on Dynamic Mechanical Properties,” Biomaterials, Vol. 27, No. 7, pp. 974-985, 2006.
[https://doi.org/10.1016/j.biomaterials.2005.07.023]
-
Pham, Q. P., Sharma, U., and Mikos, A. G., “Electrospun Poly (ε-Caprolactone) Microfiber and Multilayer Nanofiber/Microfiber Scaffolds: Characterization of Scaffolds and Measurement of Cellular Infiltration,” Biomacromolecules, Vol. 7, No. 10, pp. 2796-2805, 2006..
[https://doi.org/10.1021/bm060680j]
-
Fujihara, K., Kotaki, M., and Ramakrishna, S., “Guided Bone Regeneration Membrane Made of Polycaprolactone/Calcium Carbonate Composite Nano-Fibers,” Biomaterials, Vol. 26, No. 19, pp. 4139-4147, 2005.
[https://doi.org/10.1016/j.biomaterials.2004.09.014]
-
Gentile, P., Chiono, V., Tonda-Turo, C., Ferreira, A. M., and Ciardelli, G., “Polymeric Membranes for Guided Bone Regeneration,” Biotechnology Journal, Vol. 6, No. 10, pp. 1187-1197, 2011.
[https://doi.org/10.1002/biot.201100294]
-
Hassiba, A. J., El Zowalaty, M. E., Nasrallah, G. K., Webster, T. J., Luyt, A. S., et al., “Review of Recent Research on Biomedical Applications of Electrospun Polymer Nanofibers for Improved Wound Healing,” Nanomedicine, Vol. 11, No. 6, pp. 715-737, 2016.
[https://doi.org/10.2217/nnm.15.211]
-
Rieger, K. A., Birch, N. P., and Schiffman, J. D., “Designing Electrospun Nanofiber Mats to Promote Wound Healing-A Review,” Journal of Materials Chemistry B, Vol. 1, No. 36, pp. 4531-4541, 2013.
[https://doi.org/10.1039/c3tb20795a]
-
Billiet, T., Vandenhaute, M., Schelfhout, J., Van Vlierberghe, S., and Dubruel, P., “A Review of Trends and Limitations in Hydrogel-Rapid Prototyping for Tissue Engineering,” Biomaterials, Vol. 33, No. 26, pp. 6020-6041, 2012.
[https://doi.org/10.1016/j.biomaterials.2012.04.050]
-
Coburn, J., Gibson, M., Bandalini, P. A., Laird, C., Mao, H. Q., et al., “Biomimetics of the Extracellular Matrix: An Integrated Three-Dimensional Fiber-Hydrogel Composite for Cartilage Tissue Engineering,” Smart Structures and Systems, Vol. 7, No. 3, pp. 213, 2011.
[https://doi.org/10.12989/sss.2011.7.3.213]
-
Yang, G., Lin, H., Rothrauff, B. B., Yu, S., and Tuan, R. S., “Multilayered Polycaprolactone/Gelatin Fiber-Hydrogel Composite for Tendon Tissue Engineering,” Acta Biomaterialia, Vol. 35, pp. 68-76, 2016.
[https://doi.org/10.1016/j.actbio.2016.03.004]
Ph.D. candidate in the Department of Mechanical Engineering, Kyungpook National University. Her research interests are advanced manufacturing processes and bioengineering.
E-mail: jeonghk@knu.ac.kr
M.Sc. candidate in the Department of Mechanical Engineering, Kyungpook National University. His research interest is manufacturing processes.
E-mail: shinjun1005@gmail.com
Associate Professor in School of Mechanical Engineering, Purdue University. His research interests are smart manufacturing and micromanufacturing processes.
E-mail: mbgjun@purdue.edu
Associate Professor in School of Mechanical Engineering, Kyungpook National University. His research interest is advanced manufacturing processes.
E-mail: yhjeong@knu.ac.kr