
Design and Fabrication of a Millimeter-Scale Rotary Actuator based on the Twisted Shape Memory Alloy (SMA) Wires
Copyright © The Korean Society for Precision Engineering
This is an Open-Access article distributed under the terms of the Creative Commons Attribution Non-Commercial License (http://creativecommons.org/licenses/by-nc/3.0) which permits unrestricted non-commercial use, distribution, and reproduction in any medium, provided the original work is properly cited.
Abstract
Shape memory alloy (SMA) has been widely used for many engineering and scientific applications, because it is largely deformable with high power density, and can be actuated easily by resistive heating. It is possible to reduce the size of the actuators by integrating or embedding SMA into the structures. While many applications have been reported regarding linear or bending actuators using the SMA wire, the development of a rotary actuator remains important and challenging for the engineering applications. Here, a new type of millimeter-scale rotary actuator is proposed based on the twisted SMA wires. SMA wires are twisted, folded, and integrated into the rotary actuator, and simple change of the twist direction enables the rotary actuator to rotate in the opposite direction. By integrating the oppositely twisted SMA wires into one rotary actuator unit, bidirectional rotary motions are possible. The actuation mechanism, design, and fabrication processes of the proposed rotary actuator are presented and demonstrated with its actuation performance. The fabricated actuators had average rotary working ranges from -38.68±4.92 deg to +45.37±8.79 deg in counterclockwise (CCW) and clockwise (CW) directions. This study will leverage the practical advances in the relevant engineering and scientific applications.
Keywords:
Shape memory alloy, Rotary actuator, Twisted shape memory alloy wire, Millimeter-scale actuator키워드:
형상기억합금, 회전 구동기, 꼬인 형상기억합금 와이어, 밀리미터 스케일 구동기1. Introduction
Shape memory alloy (SMA) is a material that can be deformed at low temperature phase (twinned and detwinned martensite) and returns to its pre-deformed shape (austenite) at high temperature by application of the heat [1]. The phenomenon is called shape memory effect (SME), and it is related to a temperature-induced phase transformation [1,2]. SMA is largely deformable [2-4] with high power density [3,5], can be actuated easily by resistive heating [6], and miniaturization is possible by integrating or embedding it into the structures [1,7]. Using such characteristics and advantages, SMA has been widely used for many engineering and scientific applications; including soft robotics [3,4], biomimetics [7,8], wearable devices [9], vibration control [10], and so on. Among various forms of SMAs in wire, sheet, and tube, SMA wire is preferred in many practical applications [2-4,6], which generally undergoes 3 to 5% axial contraction with easy configuration and effective actuating force [2]. While many applications have been reported using axial contraction of the SMA wire (for linear and bending), development of a rotary actuator is still important and challenging for engineering applications of SMA [8,11,12]. Several existing works related to the SMA-based rotary actuators include, a torsion actuator driven by a pair of SMA springs applicable to a meso-scale surgical robot [13]; a rotary actuator based on the principle of wobble motor [14]; a smart soft composite composed of four SMA wires crossly connected and embedded to soft matrix (Polydimethylsiloxane, PDMS) which shows bending and twisting motions [15]; a rotary actuator based on the SMA tape [16]; and so on. However, complicated mechanisms or device configurations make them not easy for a practical application and for small scale device.
In the present study, we propose a new type of rotary actuator based on the twisted SMA wires. SMA wires are twisted, folded, and integrated into the rotary actuator, and simple change of the twist direction enables the rotary actuator to rotate in the opposite direction. By integrating the oppositely twisted SMA wires into a single rotary actuator unit, bidirectional rotary motions are possible. The actuation mechanism, design, and fabrication processes of the proposed rotary actuator are presented and demonstrated with its actuation performance.
The proposed rotary actuator is millimeter-scale, the working principle is relatively simple, bidirectional rotating motions like a conventional servo motor can be generated, and it can be fabricated in a compact form for easy integration for a practical device.
2. Design of the Rotary Actuator based on the Twisted SMA Wires
2.1 Actuation Mechanism of the Rotary Actuator
Fig. 1 shows schematic of the actuation mechanism for the proposed rotary actuator. First, we prepare the SMA wire (twinned martensite at room temperature) as two strands (1). Those strands are twisted against each other for detwinning the SMA wire (2). At this stage, two different variations are possible for the twist (detwinning) directions. We denoted those two twist directions by “inward” and “outward” as indicated in Figs. 1(a) and 1(b), respectively. It is folded after the twist (3), and by application of electric current through the electrodes (for resistive heating) the final actuator unit rotates in the opposite direction to the twist (4). Because we have two variations in the twist directions, so do the directions of rotary actuations. In this study, those two resultant directions of rotary actuations were denoted by clockwise (CW) for the inward twist and counterclockwise (CCW) for the outward twist as depicted in Figs. 1(a) and 1(b), respectively. Figs. 2(a) and 2(b) are also provided to show how the proposed twisted and folded SMA wires rotate CW and CCW, following the two different twist directions of the SMA wires.
2.2 Detail Design of the Millimeter-Scale Rotary Actuator
The rotary actuator unit was designed based on the actuation mechanism described in the previous section. As presented in Fig. 3(a) with a 3D CAD model, we designed the rotary actuator by crossing the inward and outward twisted SMA wires together. Those twisted SMA wires are folded and integrated with the electrodes into UV curable resin for the assembly. Cylindrical external covers are applied for the final device. When the electric current is applied to the inward twisted SMA wire, the rotary actuator rotates CW. In contrast, by applying electric current to the outward twisted SMA wire, the rotary actuator rotates CCW (Fig. 3(b)). In our design, the rotary actuator has 7.5 mm diameter and 20 mm length.
We note that the folding of the twisted SMA wire is one of the key advantages of the proposed rotary actuator, because 1) the two rotating axes are self-aligned by the arrangement, 2) the rotor can be freely rotated without the disturbances from the lead wires, 3) the two rotation directions (CW and CCW) can be made in the integrated form, and 4) it is beneficial for the miniaturization of the device.
In the following sections, we will provide more details on how the proposed rotary actuator was fabricated with its rotary actuation performances.
3. Results and Discussions
3.1 Fabrication of the Twisted SMA Wires
An experimental setup composed of a stepping motor and linear guides were built to fabricate the twisted SMA wires (shown in Fig. 4). At first, two ends of the SMA wire (200 μm diameter Flexinol® SMA wire with 70oC of phase transition temperature, Dynalloy, Inc.) were fixed on the moving block (denoted by pivots in Fig. 4), passing through a hook connected to the motor shaft. By the rotation of the stepping motor, the SMA wire is twisted following the rotating direction of the motor (the inward twist was depicted in Fig. 4). The moving block installed on the linear guided rail compensates the reduced distance between the hook and pivots to prevent the SMA wire snapping during the twisting process. Spring elements (rubber bands) were also installed behind the moving block to maintain the axial force to the SMA wire.
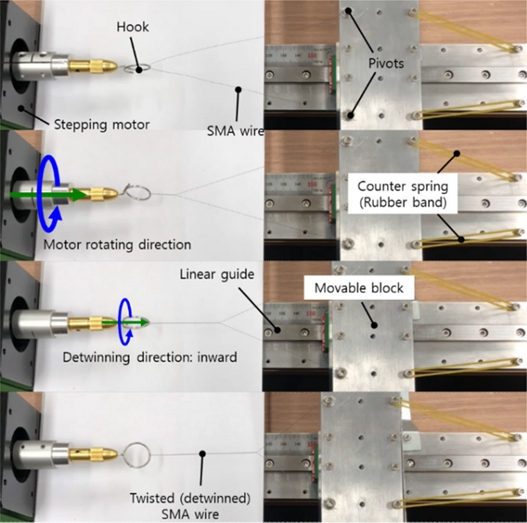
Experimental setup for fabricating the twisted SMA wire with in-situ images of the SMA wire twisting process
The twisted SMA wires (approximately 80 mm long) were fabricated using the setup in Fig. 4. We fixed the revolutions of the stepping motor to be 32 for all experiments. Fig. 5(a) presents optical images of the representative inward and outward twisted SMA wires. The resulting shape of the twisted SMA wire can be represented by a helix defined by the pitch and diameter per single revolution. Our twisted SMA wire has approximately 3 mm pitch and 0.5 mm helix diameter as shown in Figs. 5(a) and 5(b). The two different twist directions are clearly distinguishable with nearly uniform pitch along the length of the twisted SMA wires (Fig. 5(a)).
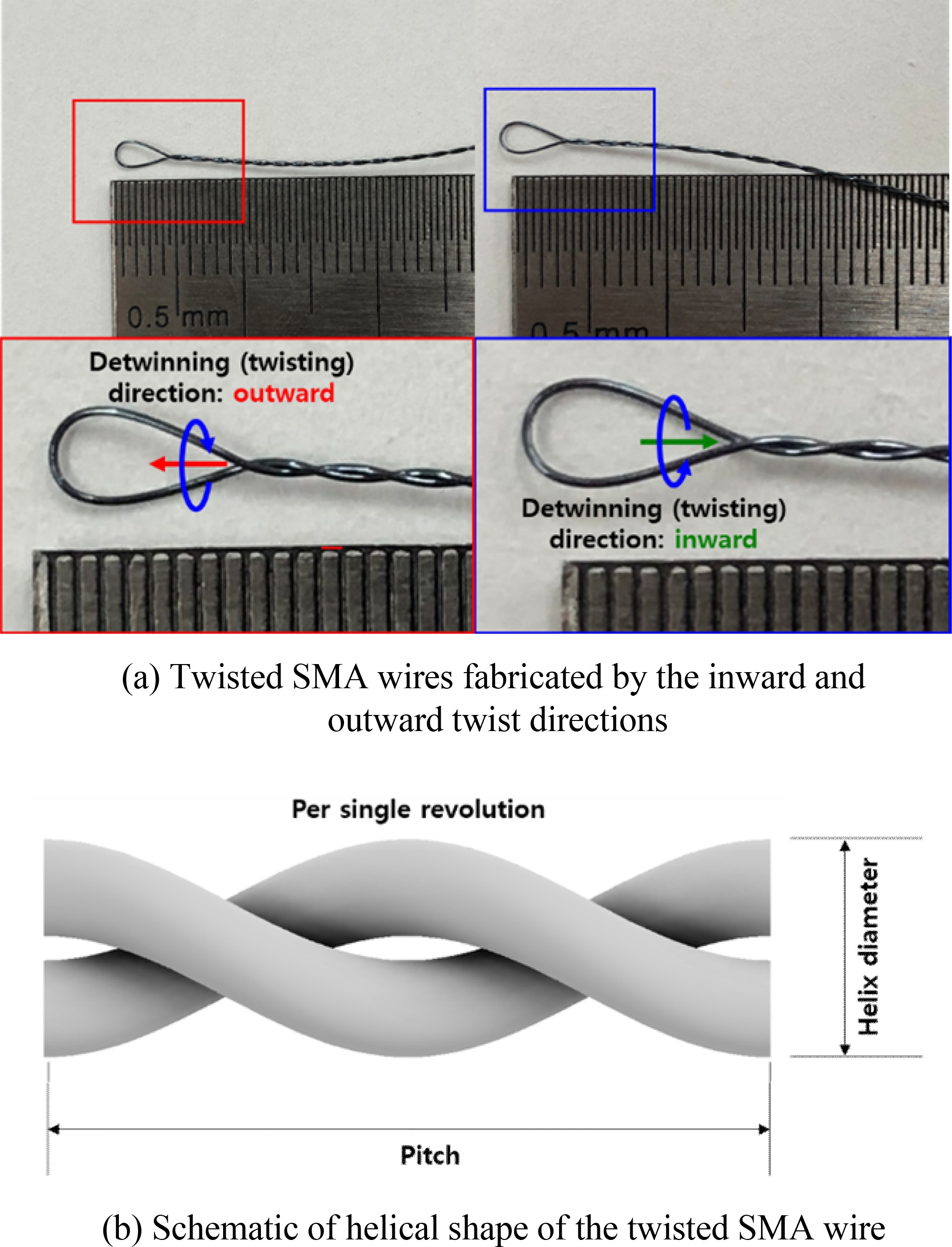
Twisted SMA wires fabricated by the inward and outward twist directions and schematic of helical shape of the twisted SMA wire
We then proposed an idea for applying the electrodes to the twisted SMA wire by winding a metal wire around the helical surface of the twisted SMA wire; it is depicted in Fig. 6. A UV curable resin (JJOMA UV resin, JJOMANHAN-MAEUL) was applied to secure the electrodes after winding the metal wire surrounding the helical surface of the twisted SMA wire.
As presented in Fig. 7, the twisted SMA wires could be easily and repeatedly fabricated with similar dimensions and qualities by the described methods.
3.2 Fabrication of the Millimeter-Scale Rotary Actuator
Fig. 8 demonstrates the fabrication processes of the rotary actuator. At first, the inward and outward twisted SMA wires (with the applied electrodes) were crossed together. We then applied the UV curable resin surrounding each twisted SMA wire along its entire length for electrical insulation. After the first applied resin surrounding each twisted SMA wire (for insulation) was cured (5 to 10 minutes), we applied the resin again at the location where the two twisted SMA wires intersect (for them to be bonded together at the intersection). Those resin application processes were conducted for electrical insulation between the two twisted SMA wires during the actuation as well as to make the twisted SMA wires stiffer. Once the two twisted SMA wires were bonded together, the wire assembly was folded and integrated with an external cylindrical cover (rotor); the cover was fabricated by a 3D printer (ABS) with 7.5 mm diameter and 5 mm length. The other ends of the twisted SMA wires (where the electrodes were created) were also bonded together by the UV curable resin. The final rotary actuator prototype was fabricated with another external cylindrical cover (stator); 3D printed (ABS) with 7.5 mm diameter and 10 mm length. As presented in Fig. 8, the rotary actuator prototype has the external dimension of 7.5 mm diameter and 20 mm length.
3.3 Step Response of the Rotary Actuator Prototype
We built a simple experimental setup shown in Fig. 9, to investigate the actuation performance of the fabricated rotary actuator. For the experiments, we installed the stator of the rotary actuator in a fixture. The rotor of the actuator was adhered to a 3D printed coupling part connected to a rotary encoder (SME360CAP, SERA) shaft. A manual stage was used to align the rotating axes of the actuator and coupling to the encoder shaft. An arrow indicator was attached on top of the coupling for better visualization of the rotation angle of the actuator.
For the actuation test, we applied step current inputs with varying the magnitude up to 1.4 A with 0.2 A increment, measuring the angular displacement of the rotary actuator using the rotary encoder.
As presented in Fig. 10 with the step responses of the angular displacement of the rotary actuator, the actuator started rotating slowly for the applied current around 0.6 A; the measured angular displacements were 0.82 and -3.26 deg, in CW and CCW directions, respectively, at 18 sec after the 0.6 A step input current was applied.
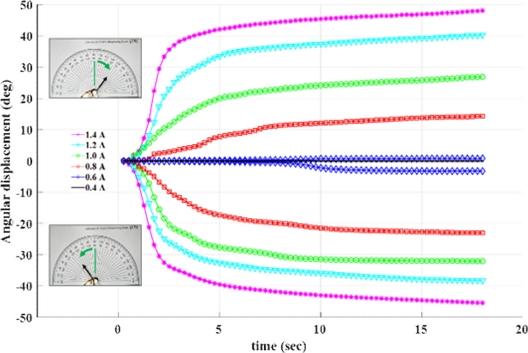
Step responses of the angular displacements of the rotary actuator with varying the step current input in CW and CCW directions
Note that the CW direction was set to be the positive direction. In our experiments, the input current equals or smaller than 0.4 A was not enough for obtaining recognizable angular displacement of the rotary actuator; it means that the temperature-induced phase transformation of the twisted SMA wire was not initiated at this current level. As we increased the input current, the actuator rotated showing larger angular displacements. The angular displacements of the rotary actuator (measured at 18 sec after the step input was applied) increased from 14.30 deg (at 0.8 A) to 48.05 deg (at 1.4 A) in the CW direction, and -23.01 deg (at 0.8 A) to -45.42 deg (at 1.4 A) in the CCW direction.
Additionally, the actuator responded faster as the input current was raised (the slope of the transient step responses increased). It is related to the increase of the rate of the resistive heating for larger current input, considering simple estimation of the electrical input power by I2RSMA, where I is the input current and RSMA is the electrical resistance of the SMA wire, neglecting the variations of electrical resistance of the SMA wire during the phase transformation and other possible heat losses.
Fig. 11 captures the in-situ rotary motions of the proposed actuator prototype when 1.4 A step input current was applied. The maximum possible angular displacements were around 50 deg in both CW and CCW directions; 48.05 (CW) and -45.42 (CCW) deg. It showed well defined and smooth rotary motions in both rotating directions.
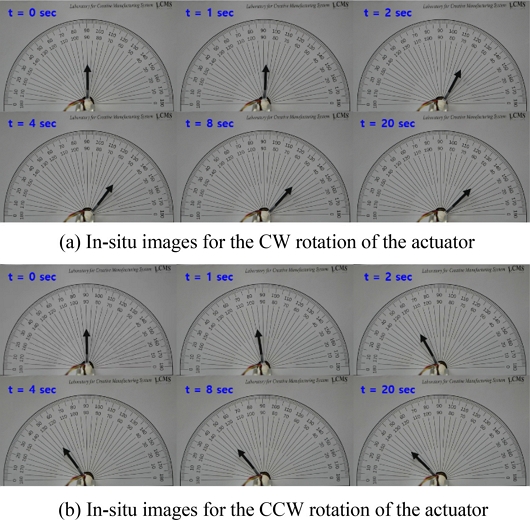
In-situ captured images of the rotary actuations of the prototype rotary actuator for 1.4 A step current applied
To evaluate the variations of the maximum possible angular displacements of the proposed and fabricated rotary actuators, we further fabricated three actuator prototypes and measured the maximum angular displacements with varying the magnitudes of the step input currents. Picture of the fabricated prototypes are presented in Fig. 12. We note that because all prototypes were hand-made, those three prototypes showed some variations in their external dimensions and qualities.
Fig. 13 plots the average maximum angular displacements (measured at 20 sec after the step input was applied where we assumed that the rotary actuation reached steady state) of the fabricated rotary actuators. The average working ranges of the rotary actuator were measured as from 0 deg (≤ 0.4 A) to 45.37±8.79 deg (1.4 A) in CW direction, and from 0 deg (≤ 0.4 A) to 38.68±4.92 deg (1.4 A) in CCW.
Based on the measured electrical resistances of the twisted SMA wire during the experiments (RSMA = 1.68±0.387 Ω), we also plot the angular displacements of the rotary actuator in terms of the power input (calculated by I2RSMA) as in Fig. 14. The rotary actuator consumed electrical power 3.29 W for its maximum angular displacement (45.37±8.79 deg in CW direction and 38.68±4.92 deg in CCW).
4. Conclusions
In conclusion, a millimeter-scale rotary actuator was proposed based on the twisted SMA wires, providing demonstrations of the actuation mechanism, exemplary design of the rotary actuator, and the fabrication techniques. Three rotary actuator prototypes were fabricated and evaluated in terms of their maximum angular displacements by the step current inputs. The fabricated actuators had average rotary working ranges from 0 deg to 45.37±8.79 deg in CW direction, and from 0 deg to 38.68±4.92 deg in CCW, by the applications of the current input up to 1.4 A (the estimated maximum power was 3.29 W). The proposed rotary actuator is millimeter-scale with relatively simple working principle, bidirectionally operable like a conventional servo motor, and it can be fabricated in a compact form for easy integration for a practical device. The further evaluations of the static and dynamic characteristics such as the stiffness of the actuator, blocking force, response time, etc., will be reported in our future works, including the repeatability of the rotary actuation performance of the proposed actuator.
Acknowledgments
This research was supported by Kumoh National Institute of Technology (No. 2019104034).
REFERENCES
-
Nespoli, A., Besseghini, S., Pittaccio, S., Villa, E., Viscuso, S., (2010), The high potential of shape memory alloys in developing miniature mechanical devices: A review on shape memory alloy mini-actuators, Sensors and Actuators A: Physical, 158(1), 149-160.
[https://doi.org/10.1016/j.sna.2009.12.020]
-
Soother, D. K., Daudpoto, J., Chowdhry, B. S., (2020), Challenges for practical applications of shape memory alloy actuators, Materials Research Express, 7(7), 073001.
[https://doi.org/10.1088/2053-1591/aba403]
-
Song, S.-H., Lee, J.-Y., Rodrigue, H., Choi, I.-S., Kang, Y. J., Ahn, S.-H., (2016), 35 Hz Shape memory alloy actuator with bending-twisting mode, Scientific Reports, 6(1), 1-13.
[https://doi.org/10.1038/srep21118]
-
Lee, J.-H., Chung, Y. S., Rodrigue, H., (2019), Long shape memory alloy tendon-based soft robotic actuators and implementation as a soft gripper, Scientific Reports, 9(1), 1-12.
[https://doi.org/10.1038/s41598-019-47794-1]
-
Abuzied, H., Abbas, A., Awad, M., Senbel, H., (2020), Usage of shape memory alloy actuators for large force active disassembly applications, Heliyon, 6(8), e04611.
[https://doi.org/10.1016/j.heliyon.2020.e04611]
-
Akbari, S., Sakhaei, A. H., Panjwani, S., Kowsari, K., Serjouei, A., Ge, Q., (2019), Multimaterial 3D printed soft actuators powered by shape memory alloy wires, Sensors and Actuators A: Physical, 290, 177-189.
[https://doi.org/10.1016/j.sna.2019.03.015]
-
Koh, J.-S., Cho, K.-J., (2013), Omega-Shaped inchworm-inspired crawling robot with large-index-and-pitch (LIP) SMA spring actuators, IEEE/ASME Transactions on Mechatronics, 18(2), 419-429.
[https://doi.org/10.1109/TMECH.2012.2211033]
-
Hu, K., Rabenorosoa, K., Ouisse, M., (2021), A review of SMA-Based actuators for bidirectional rotational motion: Application to origami robots, Frontiers in Robotics and AI, 8, 678486.
[https://doi.org/10.3389/frobt.2021.678486]
-
Jeong, J., Yasir, I. B., Han, J., Park, C. H., Bok, S.-K., Kyung, K.-U., (2019), Design of shape memory alloy-based soft wearable robot for assisting wrist motion, Applied Sciences, 9(19), 4025.
[https://doi.org/10.3390/app9194025]
-
Ghasemi, M. R., Shabakhty, N., Enferadi, M. H., (2019), Vibration control of offshore jacket platforms through shape memory alloy pounding tuned mass damper (SMA-PTMD), Ocean Engineering, 191, 106348.
[https://doi.org/10.1016/j.oceaneng.2019.106348]
-
Yuan, H., Fauroux, J. C., Chapelle, F., Balandraud, X., (2017), A review of rotary actuators based on shape memory alloys, Journal of Intelligent Material Systems and Structures, 28(14), 1863-1885.
[https://doi.org/10.1177/1045389X16682848]
-
Stroud, H., Hartl, D., (2020), Shape memory alloy torsional actuators: A review of applications, experimental investigations, modeling, and design, Smart Materials and Structures, 29(11), 113001.
[https://doi.org/10.1088/1361-665X/abbb12]
-
Sheng, J., Gandhi, D., Gullapalli, R., Simard, J. M., Desai, J. P., (2016), Development of a meso-scale SMA-based torsion actuator for image-guided procedures, IEEE Transactions on Robotics, 33(1), 240-248.
[https://doi.org/10.1109/TRO.2016.2623348]
-
Hwang, D., Higuchi, T., (2013), A rotary actuator using shape memory alloy (SMA) wires, IEEE/ASME Transactions on Mechatronics, 19(5), 1625-1635.
[https://doi.org/10.1109/TMECH.2013.2290545]
-
Rodrigue, H., Wang, W., Bhandari, B., Han, M.-W., Ahn, S.-H., (2015), SMA-based smart soft composite structure capable of multiple modes of actuation, Composites Part B: Engineering, 82, 152-158.
[https://doi.org/10.1016/j.compositesb.2015.08.020]
-
Tobushi, H., Pieczyska, E., Miyamoto, K., Mitsui, K., (2013), Torsional deformation characteristics of TiNi SMA tape and application to rotary actuator, Journal of Alloys and Compounds, 577, S745-S748.
[https://doi.org/10.1016/j.jallcom.2011.10.108]
M. S. candidate in the Department of Mechanical Engineering, Kumoh National Institute of Technology. Her research interests are smart materials, actuators, and additive manufacturing.
E-mail: ejjang@kumoh.ac.kr
M. S. candidate in the Department of Mechanical Engineering, Kumoh National Institute of Technology. Her research interests are soft robotics, shape memory alloy, smart materials and structures.
E-mail: were132@kumoh.ac.kr
B. Sc. student in the Department of Mechanical Engineering, Kumoh National Institute of Technology. His research interests are automotive engineering, robotics, and vibration.
E-mail: plaisirnuit9@kumoh.ac.kr
Assistant Professor in the Department of Mechanical Engineering, Kumoh National Institute of Technology. His research interests are integrated manufacturing system, sensors/actuators, composites, vibration, control, and additive manufacturing.
E-mail: gylee@kumoh.ac.kr