
마그네슘 합금 판재(AZ31B)의 인장 변형에서 AE 신호 발생 특성 분석
Copyright © The Korean Society for Precision Engineering
This is an Open-Access article distributed under the terms of the Creative Commons Attribution Non-Commercial License (http://creativecommons.org/licenses/by-nc/3.0) which permits unrestricted non-commercial use, distribution, and reproduction in any medium, provided the original work is properly cited.
Abstract
In this study, acoustic emission (AE) signals associated with the behavior of materials in the magnesium alloy (Mg AZ31B) tensile test were analyzed. The AE sensor was attached with the material to measure the AE signals. During the tensile experiment, the AE sensor measured the elastic waves generated inside the specimen. The AE parameters, such as, the signal energy, duration, and frequency centroid, were studied. We also analyzed the effect of the materials size and tensile speed on the AE signals. As a result, the lowest frequency centroid value occurred at the yield and fracture points. As the width and length of the specimen increased, the number of hit counts increased and the peak frequency occurred. Other AE parameters, such as, the duration and frequency centroid, were not affected. As the tensile speed increased, the hit decreased and the frequency centroid decreased in the elastic region. It was found that in the detection of the yield and fracture deformation, the number of counts, and frequency centroid were appropriate.
Keywords:
AZ31B, Acoustic emission, Plastic deformation, AE signal키워드:
마그네슘 합금, 음향방출, 소성변형, AE 신호1. 서론
마그네슘 합금(Mg AZ31B)은 밀도가 1.74 g/cm3로, 알루미늄 합금의 2/3, 철의 1/4에 해당하며 일반적으로 쓰이는 금속 재료 중에서 비교적 가벼운 재료이다. 우수한 비강도 및 기계 가공성, 전자파 차폐 특성을 가지고 있어 항공우주 및 자동차 부품 등 다양한 분야에서 사용되고 있다[1]. 이러한 마그네슘 합금 재료는 재료의 항복점을 넘어가면 소성변형이 발생하여 본래의 역할을 수행하기 어렵다. 따라서 금속 소재의 초기 결함에 관한 검출과 파괴 거동을 파악하는 것은 매우 중요한 문제이다.
이에 따라 소성변형 및 파단점을 검출하기 위해 다양한 방법이 동원되고 있다. 그중에서 가공 공정으로 인한 재료의 거시적인 변형부터 미세한 결함까지 실시간으로 진단할 수 있는 음향 방출(Acoustic Emission) 기법이 널리 사용되고 있다[2]. 음향 방출은 고체 내부의 탄성에너지가 급격히 방출될 때 발생하는 탄성파를 의미한다. 이러한 음향 방출의 발생 원인으로는 재료에서 전위의 이동 및 균열의 진전 및 전파 등 다양하게 존재하기 때문이다. 따라서 금속 재료의 소성변형 및 파단 측정이 용이하다[3].
AE 신호는 내부 발생 신호이기 때문에 실시간 측정이 가능해 소성변형 및 균열 검출에 널리 쓰이고 있다[4]. 이에 따라 고압탄소강배관의 인장시험에서 AE 신호 분석에 관한 연구가 진행되었다. 실험 결과 탄성영역에서 항복 영역까지는 저주파수 대역(250-350 kHz)이 주로 나타났으며 소성영역에서는 저주파수부터 고주파수까지 다양하게 나타남을 확인하였다. 또한 이러한 원인을 전위의 이동, 집적 그리고 전위가 개재물이나 결정입계를 통과했을 때 나타난다고 판단하였다[5].
하지만 실제 하중은 인장 변형뿐만 아니라 압축 변형도 작용하므로 압축시험에서의 AE 신호 분석도 필요하다. 따라서 알루미늄 합금의 압축 변형 거동 분석 또한 진행되었다. 위의 연구에서는 항복 시에 가장 큰 AE 진폭 및 에너지 값이 발생하였고, 소성영역에서는 비교적 적은 값이 발생하였다[6].
더 나아가, 평직 CFRP 복합재료의 3점 굽힘 시험에서 AE 특성 분석이 진행되었다. 재료의 초기 균열이 성장하기 전에는 비교적 적은 양의 AE 신호가 발생하였고, 초기 균열이 성장하는 지점에서는 많은 양의 AE 신호가 발생하였다. 이후 하중이 감소하여 균열이 급격히 성장하는 지점에서는 누적 AE 신호 발생률이 급상승하였다[7].
구조용 재료로 쓰이고 있는 마그네슘 합금에 대해서는 연구가 미흡하다. 따라서, 본 연구는 마그네슘 합금의 탄소성변형 및 파단에서의 AE 신호 발생 특성을 분석하였다. 또한, 시편의 크기 및 인장 속도가 AE 신호에 미치는 영향을 파악하고자 마그네슘 합금 인장 실험을 진행하였다.
2. 실험 방법
2.1 장치 구성 및 시편
본 연구에서는 마그네슘 합금 판재의 기계적 거동 특성을 분석하기 위해 인장 시험을 진행하였다. 인장시험은 만능재료시험기(MINOS-020, MTDI, 대한민국)를 사용하였으며 크로스헤드 속도는 5 mm/min로 하였다. 또한, 기계적 물성을 측정하기 위해 3D-DIC (ATOS Core Optical 3D Scanner)를 사용하였고 촬영 시 DIC의 프레임의 속도는 3 Hz로 설정하여 실험을 진행하였다.
인장 시편의 규격은 Fig. 1과 같다. 시편은 ASTM E8M Subsize의 Gage Length와 폭을 참고하였으며 두께는 1 mm로 제작하였다. 추가적으로 시편의 어깨부(Grip Section)는 AE 센서 부착 위치와 지름을 고려하여 폭(W)은 20 mm, 길이(L)는 45 mm로 설정하여 제작하였다.
2.2 측정 방법
소재가 변형 및 파괴 시에 발생한 탄성파는 음향 방출 시스템에 의해 검출되며, 검출된 하나의 AE 신호는 Fig. 2와 같다. AE Hit는 임계 전압값(Threshold Voltage), HDT (Hit Definition Time), HLT (Hit Lockout Time) 등을 이용하여 정의한다. 일반적으로 AE 센서를 통해 수집된 신호는 재료의 거동에 따라 다르다고 알려져 있다[8]. 본 연구에서는 재료의 기계적 거동에 따른 신호 발생 특성 분석을 위해 Fig. 2와 같이 측정된 신호의 파형을 수집하였다. 또한 수집한 신호에서 주변 잡음을 구분하기 위해 임계 전압값 통해 하나의 Hit를 정의하고 분석하였다.
사용된 AE 센서(IDK-AES-H500-W, ㈜IDK)는 일정 주파수 대역(150 kHz)을 높은 감도로 감지하는 직경 16 mm인 공진형 센서와 넓은 주파수 대역(50-500 kHz)을 감지하는 광대역형 센서이다. 센서에 진공 그리스(MOLYKOTE 1000)를 도포하여 시편 상단 어깨부에 광대역형 센서, 시편 하단 어깨부에 공진형 센서를 부착하였다.
2.3 데이터 수집 방법
AE 신호 측정은 ㈜IDK의 일체형 측정 시스템 IDK-AET-SU8을 사용하였다. AE 센서에 의해 수집된 신호는 아주 미약하기 때문에 분석하기에 난해하다. 따라서 Pre-Amplifier에서 100배(40 dB)로 증폭하여 음향 방출 시스템으로 전송되고 DAQ Board로 수집된다. DAQ Board에서는 5 MS/s의 Sampling Rate 값을 가지고 데이터를 수집하였다. 측정된 데이터는 ㈜IDK의 AE Studio 프로그램을 사용하여 데이터를 추출하였다.
본 연구에서는 잡음을 고려하여 보다 정확한 데이터를 획득하기 위해 임계 전압은 40 dB, High Pass Filter와 Low Pass Filter는 각각 100, 1,000 kHz로 설정하였다. 신호의 해석은 크기 및 빈도수와 관계가 있는 활성도와 신호의 모양과 관련된 파형 분석에 의한 방법으로 분류된다[9]. 이에 따라 음향방출 활성도에 의한 AE 파라미터는 Hit 및 Count 수, Peak Amplitude(최대 진폭)와 Hit의 면적에 해당하는 Signal Energy로 선정하였다. 또한 파형 분석에 의한 방법은 Frequency(주파수), Rise Time, Duration 등과 같은 AE 파라미터가 발생하고, 이와 같은 파라미터들로 분석을 진행하였다. 만능재료시험기에 설치된 시편과 센서는 Fig. 3과 같다.
2.4 실험 조건
본 연구에서는 먼저, 마그네슘 합금 판재의 재료 거동에서 발생하는 변형 특성을 AE 센서를 사용하여 분석하였다. 또한 시편의 크기에 따른 AE 신호 발생 특성 차이점 분석을 위해 측정 길이 25, 50 mm와 폭 6, 12.5 mm의 조합으로 제작할 수 있는 4가지의 시편에 대한 AE 신호의 특성을 비교 분석하였다. 또한 인장 속도에 따라 AE 신호의 파라미터는 대체로 다른 경향을 보인다고 알려져 있다[10]. 따라서 변형률 속도에 따른 단축 인장 시험 중의 음향 방출 신호의 특성을 분석하고자 크로스헤드의 속도를 0.5, 5, 50 mm/min로 결정하였다. 기준이 되는 속도로 5 mm/min로 정하였으며 비교적 느린 속도 0.5 mm/min(기존 속도의 1/10배), 빠른 속도 5 mm/min(기존 속도의 10배)를 추가하여 총 3가지의 속도에 따라 실험을 진행하였다. 따라서 위의 시편의 크기와 크로스 헤드 속도의 조합으로 총 6가지의 Case로 실험을 진행하였다. Table 1은 각각의 실험 조건에 관한 표이다.
3. 실험 결과
3.1 재료 거동에 따른 AE 발생 특성 분석
마그네슘 합금의 기계적인 거동 특성과 이에 따른 AE 센서 신호 결과 분석을 위해 인장 시험을 진행하였다. 마그네슘 합금 판재의 응력-변형률 선도에 따른 Hit 수(Number of Hit)는 Fig. 4와 같다.
Hit 수는 일정 시간 동안 발생하는 AE 신호의 개수이다. Fig. 4에서와 같이 탄성영역 및 항복점에서 가장 뚜렷한 Hit 수가 발생하며 소성영역에서는 Hit 수가 급격하게 줄어드는 경향을 보이고 있다. 이후의 극한 인장강도에서부터 파단점까지의 Hit 수는 거의 발생하지 않는 것으로 나타났다. 이는 탄성영역에서 항복점까지 전위의 이동에 의한 음향 방출 신호가 가장 많이 발생하기 때문에 위와 같은 현상이 발생하는 것으로 판단된다.
Fig. 5는 마그네슘 합금의 기계적 거동에 따른 AE 파라미터 중 Signal Energy, Peak Amplitude와 Duration을 분석한 결과이다. Signal Energy(1 eu = 10-14V2sec)는 한 개의 AE 신호를 시간으로 적분한 값이며, Peak Amplitude (V)는 한 개의 AE 신호에서의 최대 진폭을 의미한다. Duration은 한 개의 AE 신호가 지속되는 시간을 의미하며, 진폭이 임계전압으로 상승한 시점부터 다시 감소하는데 소요된 시간이다. Signal Energy의 값이 크면 AE 신호가 높은 에너지를 갖는 것을 의미한다. Duration이 길수록 AE 신호가 오래 지속되는 것을 의미한다.
Signal Energy와 Peak Amplitude 같은 경우 값의 차이가 크므로 Log Scale로 그래프를 표현하였다. 또한, 변화 양상을 확인하기 위해 각각의 AE 파라미터 데이터를 이동평균으로 계산하여 빨간 실선으로 나타내었다. 그 결과 모든 파라미터가 탄성변형 구간에서 항복점까지 가장 뚜렷한 변화를 보였다. 소성변형 구간에서는 반대되는 변화 양상을 보이다가 파단점에서 가장 높은 값이 발생했다. 파단점에서는 파단과 동시에 AE 신호가 발생하였다. 이 지점에서 가장 높은 변화 양상과 밀집도를 보였다. 이 결과로부터, 재료의 항복과 파단이 발생하는 시점에서 높은 AE 에너지가 발생하고, 가장 높은 AE 신호가 파단 시점에서 발생하는 것을 알 수 있다.
Fig. 6은 마그네슘 합금의 기계적 거동에 따른 AE 파라미터 중 Frequency Centroid를 분석한 결과이다. Frequency Centroid는 AE 신호 진폭과 주파수(Frequency)를 곱한 값의 합을 진폭의 합으로 나눈 값이다. 앞서 언급한 두 파라미터와 같이 항복점에서 가장 뚜렷한 변화 양상과 밀집도를 보였다. 그러나 두 파라미터는 항복점에서 높은 값을 가지지만, Frequency Centroid 같은 경우는 낮은 값이 발생하였다. 다음과 같은 AE 파라미터의 특징을 활용하여 항복점을 예측할 수 있을 것이라 판단된다. 이는 항복점을 넘어가면 소성변형이 발생하여 본래의 역할을 수행하기 어려운 재료를 실시간으로 진단하여 소성변형을 사전에 막을 수 있다.
가장 큰 변화 양상을 보인 항복점과 파단점의 주파수 분석을 하기 위해 두 지점의 FFT (Fast Fourier Transform) 이동평균을 Fig. 7에 나타냈다. 항복점의 경우 200 kHz에서 90 dBμV로 최댓값을 보이고 이후 고주파로 갈수록 점점 감소하는 경향을 보인다. 파단점에서도 200 kHz에서 최대값을 보이는데, 그 값이 140 dBμV로 상대적으로 큰 값을 가진다. 또한, 주파수가 높은 영역에서 1,000 kHz까지 120 dBμV 값이 발생했다. 파단에서의 AE 신호는 파단과 동시에 발생한다. 이때, 재료는 2개로 나뉘어진 상태이다. 파단 시점에는 AE 신호가 높은 주파수 영역까지 신호가 분포하는 것을 알 수 있다.
3.2 시편 크기에 따른 AE 신호 발생 특성 분석
AE 센서는 다양한 인자에 영향을 받기 때문에 게이지의 크기에 따라 결과 양상이 달라질 수 있다. 이에 따라 게이지의 크기에 따른 AE 신호 결과를 분석하기 위해 4가지의 시편을 이용한 인장 시험을 진행했다. 시편의 크기 변화(폭 및 Gage Length)에 의한 AE 신호 발생 특성 결과는 Fig. 8과 같다. 게이지 길이가 증가하면 Hit 수는 약 2배 증가하는 경향을 보였다. 또한 게이지 폭이 증가하면 약 3배의 Hit 수가 증가하였다. 이는 시편의 크기가 증가함에 따라 변형 면적이 넓어져 전위의 이동이 더 많이 일어난 결과라고 판단된다.
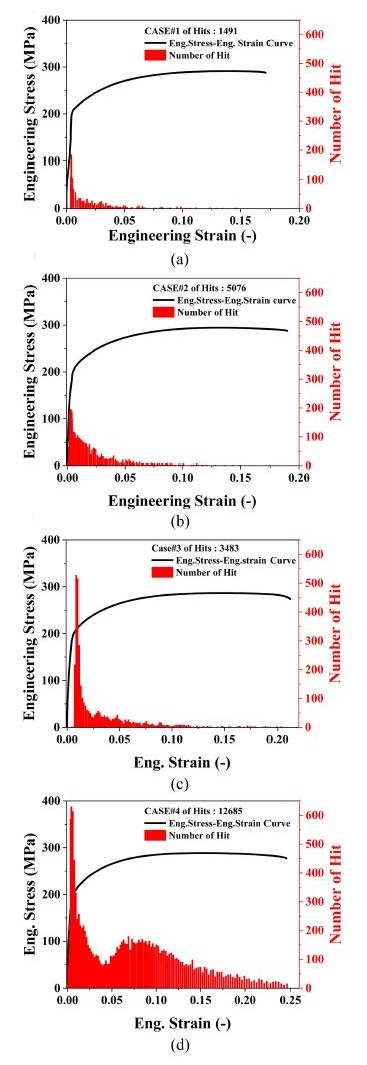
Number of hit distribution according to the material size: (a) Case 1, (b) Case 2, (c) Case 3, and (d) Case 4
Fig. 9는 시편의 크기에 따라 차이를 보이는 AE 신호 발생 특성 중 Peak Frequency를 분석한 결과이다. Case별 비교를 용이하게 하기 위해 x축은 각각의 Case의 시간에 따른 정규화를 진행하였다. 또한, y 축 같은 경우는 4 가지의 Case 중 가장 큰 파라미터값을 나타내는 Case 4를 기준으로 정규화를 진행하였다. 각각 정규화를 거친 데이터들을 이동평균으로 나타내었다. 그 결과, 게이지 길이와 폭이 증가할수록 높은 Peak Frequency가 발생하였고, 모든 Case에서 재료 거동에 따른 변화 양상은 유사하였다. 이후 시편 크기에 대해 비교한 결과는 모두 시간에 대해 정규화한 데이터를 기준으로 비교하였다.
Fig. 10은 AE 신호 발생 특성 중 Signal Energy, Duration, Peak Amplitude를 분석한 결과이다. 3가지 파라미터 모두 시편 크기에 따른 차이는 보이지 않았다. 또한, 마그네슘 합금의 기계적 거동에 따라 유사한 변화 양상을 보였다. 3가지 파라미터 모두 탄성영역 및 항복점에서 가장 큰 AE 파라미터가 발생하며, 소성영역에서는 AE 파라미터가 급격하게 줄어드는 경향을 보였다. 이후의 극한 인장강도에서부터 파단점까지의 AE 파라미터는 거의 발생하지 않는 것으로 나타났다. 위 결과를 통해 시편의 크기는 대부분의 AE 파라미터 결과에 영향을 미치지 않는 것으로 판단된다.
3.3 인장 속도별 AE 신호 발생 특성 분석
인장 시험은 인장 속도가 빨라지면 재료의 물성이 달라지기 때문에 AE 신호는 인장 속도에 따라 결과 양상이 달라질 수 있다. 이에 인장 속도에 따른 AE 센서 신호 결과를 분석하기 위해 Case 1 시편을 이용하여 3가지(0.5, 5, 50 mm/min)의 속도로 인장 시험을 진행하였다. 인장 속도에 의한 AE 신호 발생 특성은 Fig. 11과 같다. Fig. 11(a)의 총 Hit 수는 5,181개이며 항복점에서 가장 많은 Hit 수가 발생했다. 이후 소성영역에서 감소하는 경향을 보였다. Fig. 11(b)의 경우, 동일하게 항복점에서 가장 많은 Hit 수가 발생했으며 이후 소성영역에서 감소하는 경향을 보였다. 하지만 총 Hit 수는 2,843개로 Fig. 11(a)의 경우보다 더 적은 Hit 수가 검출되었다. Fig. 11(c)의 경우, 항복점에서 가장 많은 Hit 수가 발생했지만 그 분포도가 다른 2가지 경우보다 더 넓게 나타났다. 또한 총 Hit 수는 921개로 5 mm/min보다도 더 적게 검출됐다. Hit 수는 인장 속도가 빠를수록 감소하는 것을 알 수 있다.
Count는 한 개의 AE 신호에서 임계 전압을 넘는 파형의 숫자이다. Fig. 12는 인장 속도에 따른 AE 신호 발생 특성 중 Count를 분석한 결과이다. 3가지 속도 모두 마그네슘 합금의 기계적 거동에 따른 경향은 유사하다. 탄성구간에서 항복점까지 가장 뚜렷한 변화가 나타났다. 소성구간에서는 감소하는 경향을 보이다가 파단점에서 가장 높은 Count가 발생했다. 차이점으로는 인장 속도가 증가할수록 신호가 집중되어 발생한다. Fig. 12(c)에서와 같이 발생하는 Hit 수는 감소하지만, 1개의 AE 신호 내의 Count가 증가한다.
Fig. 13은 인장 속도에 따른 AE 신호 발생 특성 중 Frequency Centroid를 분석한 결과이다. 3가지 속도 모두 마그네슘 합금의 기계적 거동에 따른 경향은 유사하다. 탄성구간에서 항복점까지 가장 뚜렷한 변화가 나타났지만 Count와 반대되는 경향을 보였다. 항복점에서 최솟값이 발생하고 소성구간에서 증가하는 경향을 보인다. 속도가 빠를수록 탄성구간에서의 Frequency Centroid 값은 더 낮은 값이 발생하는 것을 알 수 있다.
3.4 AE 신호를 활용한 항복점 예측
실제 현장에서 AE 신호가 재료의 변형 거동을 확인하는 경우, 재료의 변형에 영향을 미치는 외부 요인이 달라질 수 있다. 따라서 다양한 외부의 요인과는 무관하게 재료의 변형을 실시간으로 감지를 할 수 있는 AE 신호 분석 방법이 요구된다. 본 연구에서는, 임의의 시편 크기와 인장 속도로 진행된 인장시험에서 발생한 AE 신호를 분석하여 항복 및 파단점 예측을 진행하였다. 이를 위해 시편 크기 및 인장 속도에 관계없이 항복점에서 동일한 특성을 보여줬던 Count 및 Frequency Centroid로 분석을 진행하였다. 그 결과는 Fig. 14와 같다.
5.36 s에서 높은 Count와 낮은 Frequency Centroid가 발생하였고, 이후 각 파라미터는 반대되는 경향을 보였다. 78.9 s에서는 가장 높은 Count와 낮은 Frequency Centroid가 발생하였다. 따라서 5.36 s는 해당 시편의 항복, 78.9 s는 파단이 발생한 것이라고 예측하였다. 실제 항복과 파단점을 확인하기 위해 탄성구간에서 0.2% Off-Set하여 계산한 결과 5.38 s에서 항복, 79.5 s에서 파단이 발생하였다. 이는 AE 신호로 예측한 시간과 유사했다. 이처럼 항복 및 파단점에서 뚜렷한 변화를 보이는 AE 파라미터를 이용하여 재료의 크기와 인장 속도에 관계없이 예측이 가능한 것을 확인하였다.
4. 결론
본 연구에서는 마그네슘 인장실험에서 발생하는 AE 발생 특성을 분석하는 연구를 수행하였다. 기계적 거동, 시편의 형상과 인장 속도별로 AE 파라미터 비교 분석하였다. 얻어진 결론은 다음과 같다.
재료 거동에 따른 AE 발생 특성 분석한 결과, 항복 시에 Hit, Signal Energy, Duration 및 Frequency Centroid가 피크점을 보였다. 소성변형이 진행됨에 따라 점차 반대되는 경향을 보였지만 파단 시에 Signal Energy와 Duration 같은 경우 가장 높은 값을 보였다.
시편 크기별 AE 신호 발생 특성은 게이지 폭과 길이가 증가할수록 Hit와 Peak Frequency는 게이지 길이가 증가하면 약 2배, 폭이 증가하면 3배가 증가하는 경향을 보였다. Signal Energy, Duration과 Peak Amplitude 같은 경우는 시편 크기에 따른 차이없이 유사한 변화양상을 보였다. 이는 대부분의 AE 파라미터들은 재료의 크기에 영향을 받지 않는 것이라고 판단된다.
인장 속도별 AE 발생 특성은 속도가 빨라지면 Hit는 전체적으로, Frequency Centroid 같은 경우는 탄성영역에서의 값이 감소하는 경향을 보였다. 이와 반대로 count는 인장 속도가 빨라지면 증가하는 경향을 보였다. 하지만 인장 속도가 빨라져도 재료 거동에 따라 유사한 경향을 보임을 확인하였다. 이는 인장속도를 증가시키더라도 항복 및 파단시점의 검출이 가능하다는 것을 의미한다.
본 연구에서는 AE 센서를 이용한 항복 및 파단 시점의 예측이 가능함을 확인하였다. 이에 따라 구조물의 항복점 예측이 가능하며, 성형 공정 시 소재의 파단 예측이 가능하다고 판단된다. 또한 철 재료인 스테인리스나 합금재료인 알루미늄 합금 등에서도 본 결과와 비슷한 경향을 보인다고 알려져 있다. 따라서 추가적으로 튜브, 파이프 등의 구조용 소재와 판재 성형 공정에서 발생하는 AE 신호에 대한 연구가 진행될 필요가 있다고 생각된다.
Acknowledgments
본 연구는 서울과학기술대학교 교내연구비의 지원으로 수행하였습니다.
REFERENCES
-
Park, J., Kuwabara, T., You, B., Kim, Y., (2005), Plastic deformation characteristic of AZ31 magnesium alloy sheet, Transactions of Materials Processing, 14(6), 520-526.
[https://doi.org/10.5228/KSPP.2005.14.6.520]
- Kim, H. Y., Ahn, J. H., Kim, S. R., (2005), Development of acoustic emission monitoring system for fine machining-application to cutting state monitoring in a fine fixed-abrasive machining, Journal of the Korean Society for Precision Engineering, 22(6), 109-117.
- Jeong, S.-M., Kim, J., Jeon, K. H., Hong, S., Oh, J.-S., (2020), A new method of health monitoring for press processing using AE sensor, Journal of the Korea Convergence Society, 11(11), 249-255.
- Kwon, O, Y., (1995), A study and application of acoustic emission, Journal the of Korea Institute of Electronics Engineers, 22(5), 72-82. https://scienceon.kisti.re.kr/commons/util/originalView.do?cn=JAKO199511920667477&oCn=JAKO199511920667477&dbt=JAKO&journal=NJOU00290673
- Nam, K., Lee, S., (2003), AE characteristic under tensile of carbon steel for high-pressure pipe, Journal of the Korean Institute of Gas, 7(2), 48-53.
-
Kim, J.-T., Woo, S.-C., Sakong, J., Kim, J.-Y., Kim, T.-W., (2013), Analysis of compressive deformation behaviors of aluminum alloy using a split hopkinson pressure bar test with an acoustic emission technique, Transactions of the Korean Society of Mechanical Engineers A, 37(7), 891-897.
[https://doi.org/10.3795/KSME-A.2013.37.7.891]
- Yun, Y, S., Kwak, J, H., Kwon, O, H., (2006), The evaluation of interlaminar fracture toughness and AE characteristics in a plain woven CFRP composite for 3 point bending test, Proceedings of the Spring Conference on The Korean Society for Power System Engineering, 182-186.
- Joo, Y., Im, S., Um, H., Kim, J., (2004), Generation characteristics of acoustic emission during tensile test of SA508 and SS304 materials, Proceedings of the Spring Conference on the Korean Nuclear Society. https://www.kns.org/files/pre_paper/19/472%EC%A3%BC%EC%98%81%EC%83%81.pdf
- Lee, J.-O., Ji, H.-S., Ju, N.-H., (2009), A principle and application of acoustic emission, Machine Element, 21(2), 156-164.
- Woo, C.-K., Rhee, Z.-K., (2008), Case study on the load-deflection and acoustic emission analysis of SM45C coupons with a circular hole defect under tensile loading, Transactions of the Korean Society of Machine Tool Engineers, 17(1), 50-58.
Undergraduate student in the School of Mechanical System and Design Engineering, Seoul National University of Science and Technology. His research interest in material properties and plastic processing.
E-mail: songyh9988@seoultech.ac.kr
Undergraduate student in the School of Mechanical System and Design Engineering, Seoul National University of Science and Technology. His research interest in machine fault analysis and plastic processing.
E-mail: aammss7@seoultech.ac.kr
Received M.E degree in Department of Mechanical Design and Manufacturing Engineering in Seoul National University of Science and Technology. His research interests include simulation and development of the metal forming process and lightweight materials.
E-mail: jhyu9190@seoultech.ac.kr
Professor in the Department of Mechanical System and Design Engineering, Seoul National University of Science and Technology. His research interests include simulation (FEM) and sheet metal forming.
E-mail: wjchung@seoultech.ac.kr
Assistant Professor in the Department of Mechanical System and Design Engineering, Seoul National University of Science and Technology. His research interests include simulation and development of the metal forming process and lightweight materials.
E-mail: cwlee@seoultech.ac.kr