
기계학습을 이용한 지능형 타이어의 마모도 추정
Copyright © The Korean Society for Precision Engineering
This is an Open-Access article distributed under the terms of the Creative Commons Attribution Non-Commercial License (http://creativecommons.org/licenses/by-nc/3.0) which permits unrestricted non-commercial use, distribution, and reproduction in any medium, provided the original work is properly cited.
Abstract
Tire-related crashes account for a large proportion of all types of car accidents. The causes of tire-related accidents are inappropriate tire temperature, pressure, and wear. Although temperature and pressure can be monitored easily with TPMS, there exists no system to monitor tire wear regularly. This paper proposes a system that can estimate tire wear using a 3-axis accelerometer attached to the tread inside the tire. This system utilizes axial acceleration, extracts feature from data acquired with the accelerometer and estimates tire wear by feature classification using machine learning. In particular, the proposed tire wear estimation method is designed to estimate tread depth in four types (7, 5.6, 4.2, and 1.4 mm) at speeds of 40, 50, and 60 kmph. Based on the data obtained during several runs on a test track, it has been found that this system can estimate the tread depth with reasonable accuracy.
Keywords:
Tire tread depth, Intelligent tire, Acceleration sensor, Fast fourier transform, Machine learning, K-nearest neighbor키워드:
타이어 홈 깊이, 지능형 타이어, 가속도 센서, 고속 푸리에 변환, 기계학습, K-최근접 이웃1. 서론
자율주행 기술의 발전에 따라 차량 시스템의 안전에 대한 책임이 점차 커지고 있다. 이는 차량의 고장에 대한 높은 신뢰성뿐만 아니라 다양한 사고를 방지하기 위한 기술을 요구한다[1,2]. 특히, 차량 사고는 인명사고로 이어질 높은 가능성을 가지고 있다. 그렇기 때문에 차량 주행 중 사고에 영향을 주는 요소를 인지하고 이를 처리하기 위한 기능이 필요하다[3-13].
특히, 사고를 유발하는 요소 중 타이어에 의한 차량 사고는 전체 교통사고에서 큰 부분을 차지하고 있다. 미국의 National Highway Traffic Safety Administration (NHTSA)에서는 타이어 관련 사고가 매년 약 11,000건 발생한다고 한다[14]. 그리고 NHTSA에서 차량 사고 전 단계에 인지할 수 있는 타이어 관련 요인을 압력, 온도, 트레드 깊이 등으로 정의한다. 타이어의 압력, 온도, 트레드 깊이는 타이어의 성능에 직접적인 연관이 있는 요인으로 철저한 관리가 요구된다[15,16].
타이어 온도와 압력이 적정 범위로 유지되지 못하는 경우 타이어의 손상을 유발할 가능성이 높아진다. 타이어 손상은 과도한 타이어 마모뿐만 아니라 타이어의 마찰력 감소 및 타이어 펑크를 유발하여 사고를 유발할 수 있다[17,18]. 그리고 타이어 트레드 깊이는 주행 안정성과 제동력에 큰 영향을 미칠 뿐만 아니라 우천 시 타이어와 노면 사이의 물을 배출하는 역할을 한다[19-21]. 일반적으로 타이어 트레드 깊이가 1.6 mm일 때 타이어 교체가 권장되며, 그 이하인 경우 타이어 관련 사고 확률이 약 12배 이상으로 증가한다[22].
압력과 온도 그리고 타이어 트레드 깊이에 관련된 사고를 방지하기 위해서는 주기적인 모니터링이 필요하다. 타이어의 온도와 압력은 Tire Pressure Monitoring System (TPMS)을 사용하여 주기적으로 모니터링이 가능하다[23-26]. 그러나 타이어 트레드 깊이는 운전자가 주기적으로 육안 검사로 진행하는 것이 일반적이며, 자동적으로 모니터링 하기 위한 시스템이 존재하지 않는다. 현실적으로 센서를 통해 타이어 트레드 깊이를 직접적으로 측정하기는 어렵기 때문에 이를 추정하기 위한 다양한 연구가 진행되었다. 대표적으로 모델 기반의 접근법과 Finite Element Method (FEM), 그리고 데이터 기반 접근법이 있다[27-30].
모델 기반 접근법은 수학적으로 정의된 타이어 또는 차량 모델을 사용하여 타이어, 도로, 그리고 차량 간 물리적 특성을 이용한다[27]. 그리고 FEM 기법은 타이어의 구조, 소재의 특성 등 많은 요소를 이용하여 타이어의 마모 정도를 추정한다[28]. 그러나 이러한 방법들은 복잡한 모델을 요구하며 정확하게 모델하기 어려운 편이다. 또한 주행 습관, 도로 상태와 같은 타이어 마모에 영향을 주는 외부 환경 요소를 반영하기 어려워 정확한 추정이 어렵다.
이 논문에서는 타이어 트레드의 가속도를 이용한 Tire Conditions Monitoring System (TCMS)을 제안한다. 이를 위해서 타이어 내부 바닥면에 가속도 센서가 부착된 지능형 타이어를 사용하였다. 마모도가 다른 지능형 타이어를 장착하고 시험용 트랙을 주행하면서 가속도를 측정하였고 이를 주파수 영역으로 변환하여 대역별 파워를 특징으로 추출하였다. 이를 이용하여 세 가지의 기계학습 모델을 훈련하였고 정확도를 평가하였다.
이 논문은 총 5장으로 구성되어 있다. 2장에서는 제안하는 TCMS의 구조를 설명한다. 그리고 3장에서는 가속도 센서 신호 특성에 대해 분석하고 타이어 트레드 깊이를 속도별로 추정하기 위한 알고리즘에 대해 설명한다. 그리고 4장에서는 3종의 기계학습을 사용한 타이어 트레드 깊이 추정 알고리즘의 성능을 평가하였다. 마지막으로 5장에서는 결론과 향후 연구에 대해 서술한다.
2. TCMS 개요
2.1 지능형 타이어
지능형 타이어는 타이어 내부에 센서가 설치되어 있다. 지능형 타이어는 센서 신호를 통해 타이어의 상태와 특성을 추정하여 타이어 관리와 이를 통한 안전한 차량 제어를 목표로 한다. 지능형 타이어는 Strain-Based, Deflection-Based, 그리고 Acceleration-Based 3가지 종류로 분류할 수 있다. Strain-Based는 Strain 센서로 타이어의 변형 정도를 측정하고 이를 이용해 타이어에 가해지는 힘의 방향과 크기를 추정할 수 있다[30]. Deflection-Based는 광학 센서를 사용하여 타이어 회전 시 LED 위치에 따른 광전류의 변화를 이용해 타이어에 가해지는 힘을 추정한다[31]. 그리고 Acceleration-Based는 가속도 센서로 타이어가 회전할 때 발생되는 가속도를 측정하고 이를 이용하여 타이어의 상태를 추정하는 방법이다[32-34].
Strain-Based는 Acceleration-Based에 비해 노이즈가 적은 장점이 있지만 낮은 에너지 효율과 높은 비용을 가진다. 그리고 Deflection-Based의 경우 타이어의 마찰을 측정하기 위한 방법으로 마모도 추정에 적용하기 어려운 구조를 가지고 있다. 그에 반해 Acceleration-Based는 비교적 노이즈가 많은 단점이있지만 높은 에너지 비용과 낮은 비용 등의 장점을 가진다. 따라서, 고급 신호처리 기술을 사용해 노이즈의 영향을 최소화한다면 실제 차량에 적용하기 가장 적합할 수 있다. 이전 연구에서 Acceleration-Based의 마모도 추정 가능성을 확인하였다[34]. 이 논문에서는 가속도의 특성을 사용해 타이어 트레드 깊이를 추정하기 위해 Acceleration-Based 지능형 타이어를 사용한다.
Fig. 1은 Acceleration-Based 지능형 타이어에 설치된 가속도 센서와 가속도의 벡터 방향을 보여준다. 그림과 같이 Longitudinal Acceleration (), Lateral Acceleration (), 그리고 Radial Acceleration (), 총 3방향의 가속도를 측정한다. 는 타이어 회전의 접선 가속도로 타이어 회전가속도에 따라 변화한다. 는 타이어 회전의 회전축 방향의 가속도로 차량 선회 시 변화한다. 그리고 는 타이어 회전의 구심가속도로 타이어 회전속도 변화에 따라 변화한다. 또한, 노면과 타이어가 접촉할 때 노면의 수직방향에 해당되는 진동에 따라 변화한다. 따라서, 이 논문에서는 타이어 트레드 깊이에 따라 변화되는 타이어 진동을 분석하기 위해 가속도 성분을 사용한다.
2.2 TCMS 구조
Fig. 2는 TCMS의 시스템 구조로 Equipment Module과 Processing System으로 구성된다. 타이어의 정보를 수집하기 위한 Equipment Module은 가속도 센서와 압력 센서, 온도 센서, 블루투스 모듈과 전원장치로 구성된다. Fig. 3은 타이어 내부 바닥면에 설치된 Equipment Module과 전원공급을 위한 배터리를 보여준다. 휠의 센터 캡에 배터리 지그를 설치하여 배터리를 장착한다. 배터리는 지그를 통해 타이어 내부의 Equipment Module과 연결된 전선을 사용하여 전원을 공급한다. 가속도 센서는 1 kHz의 Sampling Rate와 ±500 g의 측정 범위를 가지는 3축 가속도 센서를 사용한다. Equipment Module은 타이어 온도, 압력, 3축 가속도 데이터를 블루투스 통신을 통해 Processing System으로 전달한다.
Processing System은 블루투스를 통해 수신한 타이어 정보 데이터 중 z축 가속도를 사용해 타이어 트레드 깊이를 추정한다. 특히, 이 논문에서는 가속도의 주파수 영역에서 특징을 추출하고 이를 기계학습 모델로 타이어 트레드 깊이를 네 그룹으로 분류하여 추정한다. 그리고 타이어 압력과 온도, 추정한 타이어 트레드 깊이를 통신 디바이스를 사용해 이 정보를 필요로 하는 ECU에게 전달 가능하다. 이러한 TCMS는 차량 모니터링 Unit 또는 차량 제어기에 타이어 정보를 제공하여 타이어 상태를 고려한 차량 제어를 가능하게 도울 수 있다.
3. 타이어 트레드 깊이 추정 알고리즘
3.1 시간 영역 데이터 분석
Fig. 4는 타이어 트레드 깊이가 7, 5.6, 4.2, 그리고 1.4 mm인 타이어를 장착하고 시속 60 kmph로 마른 아스팔트 도로를 주행했을 때 얻어진 축방향 가속도() 신호를 보여주고 있다. 여기서 타이어 트레드 깊이가 7 mm인 타이어는 새 타이어이며, 1.4 mm는 트레드가 과도하게 마모된 교체 시기의 타이어다.
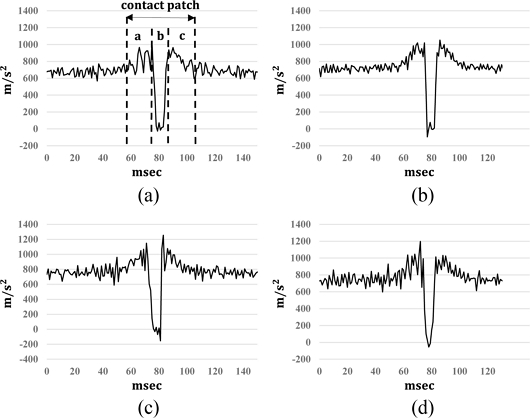
Analysis of acceleration signal in time domain; (a) 7 mm tread depth, (b) 5.6 mm tread depth, (c) 4.2 mm tread depth, (d) 1.4 mm tread depth
Fig. 4(a)에서 Contact Patch는 가속도 센서가 설치된 타이어 바닥면이 노면과 접촉했다가 떨어지는 단계이다. 노면과 접촉하기 시작하는 단계인 Contact Patch의 Fig. 4(a)에서는 타이어가 하중에 의해 눌리면서 센서가 회전축에 가까워져 구심가속도가 증가한다. 그리고 Fig. 4(b)에서는 TCMS가 설치된 타이어 바닥면이 노면과 완전 접촉을 한 상태로 평평해진 타이어의 접촉면을 따라 센서가 이동하기 때문에 구심력이 사라져서 축방향 가속도가 0에 수렴하게 된다. 그리고 Fig. 4(c)는 센서가 타이어 바닥면이 노면에서 떨어지는 단계로 Fig. 4(a) 단계와 반대로 가속도가 변화한다.
하지만 같은 속도, 같은 트레드 깊이에서도 Contact Patch의 가속도 변화는 매번 다른 형상을 보여주고 이 때문에 시간 영역의 가속도 변화로 트레드 깊이를 추정하는 것이 매우 어렵다. 따라서, 3.2장에서 시계열 데이터를 주파수 영역으로 변환하여 분석하는 것이 필요하다.
3.2 주파수 영역 데이터 분석과 특징추출 방법
시간 영역의 가속도 데이터를 주파수 영역으로 변환하여 분석하기 위해서 Fast Fourier Transform (FFT)을 사용하였다. Fig. 5는 서로 다른 트레드 깊이를 가진 타이어 4개로 각각 주행했을 때 수집한 가속도 데이터를 주파수 영역으로 변환한 결과의 예시이다. 그림에서 타이어가 많이 마모된 4.2, 1.4 mm에서 고주파 성분이 차지하는 비중이 나머지에 비해 큰 경향을 볼 수 있다. 또한 5.6과 4.2 mm일 때 50 Hz 부근에 나타나는 피크 값이 다른 두 경우에 비해 높은 것을 볼 수 있다. 이러한 차이점을 활용하면 트레드 깊이를 추정하는 것이 가능함을 시사한다.
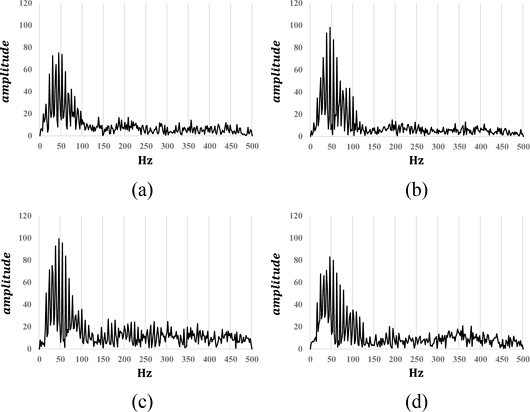
Analysis of acceleration signal in frequency domain; (a) 7 mm tread depth, (b) 5.6 mm tread depth, (c) 4.2 mm tread depth, (d) 1.4 mm tread depth
이러한 타이어 트레드 깊이에 따른 주파수 분포를 정량적으로 표현하기 위하여 0-500 Hz를 10개의 구간으로 나누어 식(1)과 같이 그 구간의 평균 파워를 산출하였다. 또한 0 Hz는 차량의 속도를 나타내기 때문에 별도로 계산하였다. Fig. 6은 60 kmph 속도로 주행하여 수집한 전체 데이터에서 식(1)로 추출한 특징의 분포를 보여준다. 그림의 타이어 트레드 깊이 별 특징은 Fig. 5보다 뚜렷하게 나타나는 것을 확인할 수 있다. 즉, 마모가 커지면 고주파 성분이 늘어난 것을 쉽게 파악할 수 있다. 따라서, 이렇게 정량화한 값을 이용한 기계학습방법을 통해 분류가 가능할 것으로 보인다.
(1) |
3.3 기계학습 기반의 트레드 깊이 추정 알고리즘
3.2절에서 60 kmph의 속도로 주행 시 획득한 데이터를 사용하여 타이어 트레드 깊이 변화에 따른 타이어 진동을 확인하였다. 특히, 식(1)로 주파수 영역에서 특징을 추출하는 경우 육안으로도 트레드 깊이 별로 분류 가능한 강력한 특징이 추출되는 것을 확인하였다. 이를 기반으로 40, 50, 60 kmph의 속도로 주행 시 타이어 트레드 깊이를 추정하는 것을 목표로 한다. 이를 위해 기계학습 모델을 사용하여 특징을 분류하여 타이어 트레드 깊이를 추정한다.
Fig. 7은 타이어 트레드 깊이 추정 알고리즘의 구조이다. 알고리즘은 그림과 같이 시계열 데이터인 가속도 센서의 데이터 500개(0.5초)를 주파수 영역으로 변환한다. 그리고 3.2절의 식(1)을 사용하여 11개의 특징을 추출한다. 그리고 나서 특징을 기계학습 모델을 사용하여 타이어 트레드 깊이를 7, 5.6, 4.2, 1.4 mm의 수치로 분류하여 추정한다. 특징을 분류하기 위한 기계학습 모델은 MLR (Multiple Linear Regression), SVM (Support Vector Machine), K-NN (K-Nearest Neighbor)을 사용해 알고리즘을 구성하고 성능을 비교 평가하여 선정하였다.
Fig. 8은 알고리즘에서 사용한 기계학습을 이용한 데이터 분류 방법을 보여준다. Figs. 8(a)는 MLR, 8(b)는 SVM, 그리고 8(c)는 K-NN을 사용한 데이터 분류를 보여 주고 있다. 각 그림은 독립 변수가 2개인 3가지 종류의 데이터를 각 기계학습방법으로 분류한 결과를 나타내고 있다. 그림에서 데이터 라벨이 ‘0’인 데이터는 동그라미, 라벨이 ‘1’인 데이터는 네모, 그리고 라벨이 ‘2’인 데이터는 세모로 표시하고 있다. 각 기계학습방법의 데이터 분류는 설명과 같다.
MLR은 입력데이터의 선형 관계로 회귀식을 모델링하고 이를 사용해 입력데이터의 Class를 분류한다. Fig. 8(a)의 3개의 점선은 각 Class의 데이터를 사용해 모델링한 회귀식이다. 데이터 Class의 수와 같은 개수의 회귀식이 설정되며, 입력데이터에 가장 가까운 회귀식에 따라 Class를 분류한다. MLR은 데이터의 분포가 선형적이고 데이터 군집 간 거리가 충분히 먼 경우 사용하기 적합하다.
SVM은 Class 별 데이터 분포에 따라 초평면 또는 커널로 차원공간을 Class 별로 분할하고 이를 사용해서 입력데이터를 분류한다. Fig. 8(b)에서 점선은 Class 영역을 분할하는 경계선이다. 이 경계선은 데이터 군집 간 분포에 의해 구성되며, 입력데이터가 위치한 영역의 Class로 데이터가 분류된다. SVM은 Class 별 데이터 분포가 겹쳐지지 않는다면 복잡한 분포 형태를 가져도 우수한 성능을 보여준다.
KNN은 Class 별 데이터로 구성된 데이터 베이스에서 입력데이터와 가장 근접한 데이터 k개 중 제일 많은 Class로 입력데이터를 분류한다. Fig. 8(c)에서는 별모양은 입력데이터로 k = 3인 상황에서 가장 근접한 데이터 3개를 선택한 결과를 보여준다. 그림에서 입력데이터와 가장 근접한 3개의 데이터 중 Class가 1(네모)인 요소가 2개로 입력데이터는 Class 1로 분류된다. KNN은 복잡한 데이터 분포에서 우수한 성능을 보이며, Class 별 데이터 분포가 겹치는 상황에서도 비교적 우수한 성능을 보여준다.
기계학습 모델 중 MLR은 옵션이 불필요한 모델이며, SVM은 분류를 위해 일반적으로 많이 사용되는 Radial Basis Function 커널을 사용하였다. 그리고 K-NN은 K개의 인접한 데이터를 찾고 인접한 데이터의 라벨을 확인하고 가장 많은 라벨로 분류하는 알고리즘이다. 그렇기 때문에 K-NN은 분류에 사용할 근접한 이웃의 개수(K)를 옵션으로 설정해 주어야만 한다. 특히, K-NN은 데이터 특성에 따라 높은 분류 정확도를 얻을 수 있는 k값이 달라진다. 따라서, K-NN을 사용하여 데이터를 정확히 분류하기 위해서는 높은 분류 정확도를 가지는 k값을 찾을 필요성이 있다.
따라서, K-NN을 사용하여 타이어 트레드 깊이를 최대한 정확하게 추정하기 위해 최적의 k값을 선정하였다. 이를 위해 가속도 센서의 데이터를 사용하여 K-NN을 학습하고 추정 정확도를 평가하여 k값에 따른 정확도를 확인하였다. Fig. 9는 k값에 따른 K-NN의 타이어 트레드 깊이 추정 정확도를 보여준다. 그래프와 같이 k값이 1인 경우 제일 높은 정확도를 보였으며, k값이 증가할수록 정확도가 낮아지는 것을 확인하였다. 이는 제일 근접한 데이터 하나만을 사용하여 특징을 분류하는 것이 최적의 결과를 도출한다는 것을 보여준다. 시험 결과에 따라 K-NN의 k값을 1로 선정하였다.
4. TCMS의 타이어 트레드 깊이 추정 알고리즘 성능평가
이 장에서는 TCMS의 타이어 트레드 깊이 추정 알고리즘에 사용할 기계학습 알고리즘을 선택하기 위해 성능 평가를 진행하였다. 성능 평가를 위한 데이터는 TCMS를 설치한 차량을 자동차 전용 시험 도로에서 주행하여 수집하였다. 시험 차량의 중량은 1,550 kg이며, 성인 두 명이 탑승하였다. 그리고 시험 차량에는 18인치 타이어가 장착되었으며, 전방 좌측 타이어에만 TCMS Equipment Module을 설치하였다. 마른 아스팔트 도로에서 40, 50, 60 kmph의 속도로 직선 코스를 주행하는 동안 데이터를 수집하였다. 타이어 압력은 39 psi로 유지하였으며, 타이어 트레드 깊이가 7, 5.6, 4.2, 1.4 mm인 타이어 4종을 교체하여 데이터를 수집하였다.
수집한 가속도 센서의 이산 시계열 데이터들을 타이어 트레드 깊이와 속도에 따라 분류하였다. 그리고 분류한 데이터를 타이어 트레드 추정 알고리즘의 입력인 0.5초(500개의 데이터) 길이의 데이터 셋들로 구성하였다. 학습과 성능 평가를 위한 데이터 셋은 약 4.5 : 5.5의 비율로 나누어 구성하였다. Table 1은 기계학습 기반의 분류모델의 학습을 위한 데이터 셋의 수를 보여주는데 총 1,008개로 구성된다. 그리고 Table 2는 학습이 완료된 타이어 트레드 추정 알고리즘의 성능 평가에 사용하기 위한 데이터 셋으로 총 1,224개이다.
제안하는 타이어 트레드 깊이 추정 알고리즘은 TCMS의 핵심 성능으로 높은 정확도가 요구된다. 또한, 실제 차량에 적용되기 위해서는 적절한 연산속도와 학습속도가 요구된다. 따라서, 이 논문에서는 TCMS의 타이어 트레드 깊이 추정 알고리즘에서 사용할 기계학습 알고리즘을 정확도와 연산속도, 학습속도를 성능지표로 고려하였다.
Tables 3, 4, 5는 Table 2의 데이터 셋을 사용하여 타이어 트레드 깊이 추정 정확도를 평가한 결과를 보여준다. Table 3은 MLR의 성능으로 전체적으로 추정 정확도가 좋지 못하며, 종합적으로 약 35.2%의 정확도를 보여준다. Table 4는 SVM의 성능으로 MLR에 비해 비교적 높은 정확도를 보여주며, 종합적으로 88.0%의 정확도를 보여준다. 그리고 Table 5는 K-NN의 성능으로 전체적으로 정확도가 양호하며, 종합적으로 96.9%의 우수한 추정 정확도를 보여준다.
결과를 정리하면 K-NN, SVM, 그리고 MLR 순으로 타이어 트레드 깊이를 정확하게 추정한다. MLR을 사용한 추정 정확도가 가장 낮은 결과는 타이어 트레드 깊이에 따른 특징의 분포가 선형적이지 않기 때문이다. 그리고 SVM보다 K-NN의 추정 정확도가 높은 결과는 타이어 트레드 깊이에 따른 특징의 분포가 완전히 공간적으로 독립되어 있지 않고 겹치는 부분이 존재한다는 것을 뜻한다. 따라서, 타이어 트레드 깊이에 따른 특징의 분포는 선형적이지 않고 공간적으로 독립되어 있지 않기 때문에 K-NN이 타이어 트레드 깊이를 비교적 정확하게 측정하는 것으로 판단된다.
Table 6은 각 모델의 학습시간과 타이어 트레드 깊이 추정 알고리즘의 실행 시간을 보여준다. 이 실험 결과는 Windows 10 64비트 운영체제와 7세대 i5 CPU를 사용하는 데스크톱에서 Python을 사용하여 얻은 것이다. 학습시간은 MLR, K-NN, 그리고 SVM 순으로 빨랐으며, 알고리즘의 실행 시간은 MLR, SVM, K-NN 순으로 빨랐다. 실행 시간은 제일 빠른 모델과 느린 모델 간의 차이가 약 0.749 ms 차이로 실행 주기인 500 ms를 고려할 경우 사소한 차이로 모델 선정 시 큰 영향을 주지 않는다. 또한, 학습 시간은 모델과 간 차이가 최대 약 5배 이상 차이가 나지만 제일 느린 모델의 학습 시간이 34.612 ms로 상당히 빨라서 모델 선정 시 큰 영향을 주지 않는다.
성능 평가 결과에 따르면 각 모델 간 학습시간과 실행 시간의 차이가 발생하였지만 TCMS에 적용 시 큰 영향을 줄 정도의 유의미한 차이가 아니었다. 하지만 학습모델의 정확도를 평가한 결과에 따르면 MLR, SVM, 그리고 K-NN을 사용하는 경우 타이어 트레드 깊이 추정 정확도 각각 35.2, 88.0, 그리고 96.9%로 확인되었다. 따라서, 이 논문에서는 정확도가 제일 높은 K-NN을 TCMS의 타이어 트레드 깊이 추정 알고리즘의 학습 모델로 선정하는 것이 타당하다.
5. 결론
타이어의 공기압과 타이어 트레드 깊이는 타이어 관련 사고를 예방할 수 있는 요소로 지속적인 모니터링이 요구된다. 특히, 자율주행의 안전을 위해 자율주행 시스템에 타이어 관련 정보가 필수적으로 요구된다. 따라서, 이 논문에서는 기계학습을 사용한 타이어 트레드 깊이 추정 알고리즘과 이를 사용한 TCMS를 제안하였다. 이를 위해서 TCMS의 가속도 센서로 수집한 데이터를 사용하여 타이어 트레드 깊이에 따른 축방향 가속도 변화의 특징을 추출하였다. 그리고 TCMS에 적합한 기계학습 모델을 선정하였다. 이 연구를 통해 얻은 결론은 다음과 같다.
첫째, 타이어 트레드 내부에 부착한 가속도 센서를 사용해서 얻은 축방향 가속도 정보를 통하여 트레드 깊이를 추정할 수 있다. 시계열 데이터에서는 타이어의 마모도를 추정하기 어려워 보이지만 주파수 영역에서 대역별 파워의 분포가 다른 점을 이용하면 트레드 깊이를 추정할 수 있는 가능성을 보여주었다.
둘째, 타이어 트레드 깊이를 추정하기 위한 세 가지 기계학습 모델 중 K-NN이 가장 적합하였다. MLR, SVM, K-NN을 학습용 데이터로 학습시킨 후 별도의 시험용 데이터로 정확도를 평가한 결과 K-NN이 가장 높은 정확도를 보였다. 또한 학습시간과 실행 시간은 기계학습 모델의 선정에 큰 영향이 없는 것으로 판명되었다.
셋째, 이 논문에서 제안된 TCMS의 타이어 트레드 깊이 추정 알고리즘은 40, 50, 60 kmph의 속도로 마른 아스팔트 노면을 달리는 경우 약 96.9%의 정확도를 갖는 것으로 평가되었다. 그리고 추정에 소요되는 시간은 약 1.530 ms로 실시간으로 처리 가능하다. 이는 실제 차량에서 타이어 트레드 깊이를 높은 정확도로 추정 가능함을 보여준다. 따라서, 과도하게 마모된 타이어로 인한 차량 미끄러짐으로 인한 사고를 사전에 예방할 수 있을 것으로 판단된다.
이 연구에는 차량의 다양한 주행 환경을 고려하지 못한 한계가 있다. 즉 젖은 도로, 콘크리트 도로, 곡선 구간 등에서 수집한 데이터를 고려하지 못했고 승용차에 탑승한 사람의 수가 변화할 때 가속도의 특성이 어떻게 변화하는지에 대한 분석이 부족하다. 또한, 타이어 내부에 장착되는 가속도 센서를 포함한 Equipment Module의 사용 전력이 커서 전원을 타이어 외부에 설치해야 하는 실정이다. 이를 해소하기 위한 저전력 설계 또는 에너지 하베스팅 기술 적용에 대한 추가 연구가 필요하다.
Acknowledgments
이 과제는 부산대학교 기본연구지원사업(2년)에 의하여 연구되었음.
REFERENCES
-
Dixit, V. V., Chand, S., Nair, D. J., (2016), Autonomous vehicles: Disengagements, accidents and reaction times, PLoS One, 11(12), e0168054.
[https://doi.org/10.1371/journal.pone.0168054]
-
Riedmaier, S., Ponn, T., Ludwig, D., Schick, B., Diermeyer, F., (2020), Survey on scenario-based safety assessment of automated vehicles, IEEE Access, 8, 87456-87477.
[https://doi.org/10.1109/ACCESS.2020.2993730]
-
He, X., Liu, Y., Lv, C., Ji, X., Liu, Y., (2019), Emergency steering control of autonomous vehicle for collision avoidance and stabilisation, Vehicle System Dynamics, 57(8), 1163-1187.
[https://doi.org/10.1080/00423114.2018.1537494]
-
Yuan, Y., Tasik, R., Adhatarao, S. S., Yuan, Y., Liu, Z., Fu, X., (2020), RACE: Reinforced cooperative autonomous vehicle collision avoidance, IEEE Transactions on Vehicular Technology, 69(9), 9279-9291.
[https://doi.org/10.1109/TVT.2020.2974133]
-
Wang, H., Huang, Y., Khajepour, A., Zhang, Y., Rasekhipour, Y., Cao, D., (2019), Crash mitigation in motion planning for autonomous vehicles, IEEE Transactions on Intelligent Transportation Systems, 20(9), 3313-3323.
[https://doi.org/10.1109/TITS.2018.2873921]
-
Yadav, R., Dahiya, P. K., Mishra, R., (2020), Comparative analysis of automotive radar sensor for collision detection and warning system, International Journal of Information Technology, 12(1), 289-294.
[https://doi.org/10.1007/s41870-018-0167-3]
-
Malinverno, M., Avino, G., Casetti, C., Chiasserini, C.-F., Malandrino, F., Scarpina, S., (2018), Performance analysis of C-V2I-based automotive collision avoidance, Proceedings of the 2018 IEEE International Symposium on “A World of Wireless, Mobile and Multimedia Networks (WoWMoM)”, 1-9.
[https://doi.org/10.1109/WoWMoM.2018.8449772]
-
Kim, T., Jeong, H.-Y., (2014), A novel algorithm for crash detection under general road scenes using crash probabilities and an interactive multiple model particle filter, IEEE Transactions on Intelligent Transportation Systems, 15(6), 2480-2490.
[https://doi.org/10.1109/TITS.2014.2320447]
- Kim, B.-K., Han, S.-C., Yi, H.-C., (2007), A study on rear lateral collision warning system of vehicle using fuzzy control algorithms, Journal of the Korean Society for Precision Engineering, 24(2), 73-85.
-
Yoon, M. Y., Choi, J. K., Jung, J. E., Boo, K. S., Kim, H. S., (2013), Development of vehicle side collision avoidance system with virtual driving environments, Journal of the Korean Society for Precision Engineering, 30(2), 164-170.
[https://doi.org/10.7736/KSPE.2013.30.2.164]
-
Baek, S., Kim, H., Boo, K., (2014), A method for rear-side vehicle detection and tracking with vision system, Journal of the Korean Society for Precision Engineering, 31(3), 233-241.
[https://doi.org/10.7736/KSPE.2014.31.3.233]
-
Yun, D., Kim, H., Boo, K., (2011), Brake performance evaluation of ABS with sliding mode controller on a split road with driver model, International Journal of Precision Engineering and Manufacturing, 12(1), 31-38.
[https://doi.org/10.1007/s12541-011-0004-0]
-
Lee, M. H., Park, H. G., Lee, S. H., Yoon, K. S., Lee, K. S., (2013), An adaptive cruise control system for autonomous vehicles, International Journal of Precision Engineering and Manufacturing, 14(3), 373-380.
[https://doi.org/10.1007/s12541-013-0052-8]
- Choi, E.-H., (2012), Tire-related factors in the pre-crash phase, (Report No. DOT HS 811 617). https://crashstats.nhtsa.dot.gov/Api/Public/ViewPublication/811617
-
Askari, H., Hashemi, E., Khajepour, A., Khamesee, M. B., Wang, Z. L., (2019), Tire condition monitoring and intelligent tires using nanogenerators based on piezoelectric, electromagnetic, and triboelectric effects, Advanced Materials Technologies, 4(1), 1800105.
[https://doi.org/10.1002/admt.201800105]
-
Tjiu, W., Ahanchian, A., Majlis, B., (2004), Development of tire condition monitoring system (TCMS) based on MEMS sensors, Proceedings of the 2004 IEEE International Conference on Semiconductor Electronics, 4.
[https://doi.org/10.1109/SMELEC.2004.1620903]
-
Liu, H., Deng, W., Zong, C., Wu, J., (2014), Development of active control strategy for flat tire vehicles, SAE Technical Paper.
[https://doi.org/10.4271/2014-01-0859]
-
Wang, F., Chen, H., Cao, D., (2015), Nonlinear coordinated motion control of road vehicles after a tire blowout, IEEE Transactions on Control Systems Technology, 24(3), 956-970.
[https://doi.org/10.1109/TCST.2015.2472982]
- Horne, W. B., Dreher, R. C., (1963), Phenomena of pneumatic tire hydroplaning, National Aeronautics and Space Administration.
-
Luchini, J., Motil, M. M., Mars, W., (2001), Tread depth effects on tire rolling resistance, Tire Science and Technology, 29(3), 134-154.
[https://doi.org/10.2346/1.2135235]
- Dijks, A., (1976), Influence of tread depth on wet skid resistance of tires, Transportation Research Record, 621, 136.
- Horne, W. B., (1962). Influence of the tire tread pattern and runway surface condition on breaking friction and rolling resistance of a modern aircraft tire, National Aeronautics and Space Administration.
-
Velupillai, S., Guvenc, L., (2007), Tire pressure monitoring [applications of control], IEEE Control Systems Magazine, 27(6), 22-25.
[https://doi.org/10.1109/MCS.2007.909477]
-
Wei, L., Wang, X., Li, L., Yu, L., Liu, Z., (2020), A low-cost tire pressure loss detection framework using machine learning, IEEE Transactions on Industrial Electronics, 68(12), 12730-12738.
[https://doi.org/10.1109/TIE.2020.3047040]
-
Leng, Y., Wenfeng, D., Peng, S., Ge, X., Nga, G. J., Liu, S., (2012), Study on electromagnetic wave propagation characteristics in rotating environments and its application in tire pressure monitoring, IEEE Transactions on Instrumentation and Measurement, 61(6), 1765-1777.
[https://doi.org/10.1109/TIM.2011.2181896]
-
Kim, S. J., Jung, H., (2013), A study on the dynamic characteristics of TPMS piezoelectric element using finite element method, Journal of the Korean Society for Precision Engineering, 30(12), 1341-1347.
[https://doi.org/10.7736/KSPE.2013.30.12.1341]
-
Jeong, D., Choi, S. B., Lee, J., Kim, M., Lee, H., (2021), Tire dimensionless numbers for analysis of tire characteristics and intelligent tire signals, Mechanical Systems and Signal Processing, 161, 107927.
[https://doi.org/10.1016/j.ymssp.2021.107927]
-
Zhang, H., Zhang, S., Zhang, Y., Huang, X., Dai, Y., (2020), Abrasion status prediction with BP neural network based on an intelligent tire system, Proceedings of the 2020 CAA International Conference on Vehicular Control and Intelligence (CVCI), 619-622.
[https://doi.org/10.1109/CVCI51460.2020.9338547]
- Karim, S. M., Rahman, Y., Hai, M. A., Mahfuza, R., (2021), Tire wear detection for accident avoidance employing convolutional neural networks, Proceedings of the 2021 NAFOSTED Conference on Information and Computer Science (NICS), 364-368.
-
Garcia-Pozuelo, D., Olatunbosun, O., Yunta, J., Yang, X., Diaz, V., (2017), A novel strain-based method to estimate tire conditions using fuzzy logic for intelligent tires, Sensors, 17(2), 350.
[https://doi.org/10.3390/s17020350]
-
Erdogan, G., Alexander, L., Rajamani, R., (2010), Estimation of tire-road friction coefficient using a novel wireless piezoelectric tire sensor, IEEE Sensors Journal, 11(2), 267-279.
[https://doi.org/10.1109/JSEN.2010.2053198]
-
Yang, S., Chen, Y., Shi, R., Wang, R., Cao, Y., Lu, J., (2022), A survey of intelligent tires for tire-road interaction recognition, IEEE Transactions on Intelligent Vehicles, 7(3), 520-532.
[https://doi.org/10.1109/TIV.2022.3163588]
-
Singh, K. B., Arat, M. A., Taheri, S., (2019), Literature review and fundamental approaches for vehicle and tire state estimation, Vehicle System Dynamics, 57(11), 1643-1665.
[https://doi.org/10.1080/00423114.2018.1544373]
- Kim, Y.-J., Kim, H.-J., Han, J.-Y., Lee, S., (2020), Classification of tire tread wear using accelerometer signals through an artificial neural network, Journal of the Korean Society of Industry Convergence, 23(2_2), 163-171.
Ph.D. candidate in the School of Mechanical Engineering, Pusan National University. His research interest is machine learning, invehicle networking, and network-based control systems.
E-mail: jyhan@pusan.ac.kr
Ph.D. candidate in the School of Mechanical Engineering, Pusan National University. His research interest is machine learning, invehicle networking, and network-based control systems.
E-mail: jhkwon09@pusan.ac.kr
Researcher in the Smart Robot Convergence and Applications Research Center at Pukyong National University. His research interest is artificial intelligence, its applications in automotive and industrial robots.
E-mail: hj.kim@pknu.ac.kr
Professor in the School of Mechanical Engineering, Pusan National University. His research interest is industrial networks, invehicle networks, and home networks.
E-mail: slee@pnu.edu