
회전경사증착 기법을 이용한 Ni-GDC 연료극이 적용된 AAO 기반의 저온작동 박막 고체산화물 연료전지의 저항 특성 연구
Copyright © The Korean Society for Precision Engineering
This is an Open-Access article distributed under the terms of the Creative Commons Attribution Non-Commercial License (http://creativecommons.org/licenses/by-nc/3.0) which permits unrestricted non-commercial use, distribution, and reproduction in any medium, provided the original work is properly cited.
Abstract
In this study, we fabricated thin film solid oxide fuel cells on nanoporous anodic aluminum oxide (AAO) substrate for low-temperature operation using the all-through sputtering method. To deposit up to a three-micrometer thick anode with both porosity and electrical conductivity, we used the glancing angle deposition and co-sputtering methods. For the anode materials, we used nickel gadolinium-doped-ceria (Ni-GDC) mixed ionic and electronic conductor (MIEC), which improved hydrogen oxidation reaction reactivity at the anode side. TF-SOFCs were successfully operated at 500oC, and 223.6 mW/cm2 was their highest measured maximum power density. We conducted structural and electrochemical analyses to figure out cells’ unique resistant characteristics; ohmic resistance through the anode thin film and polarization resistance of reaction area near the narrowed anode pores. We found how the anode thin film thickness affects the current collecting performance and the anode reactivity, and their effects were qualitatively and quantitatively compared.
Keywords:
Thin film solid oxide fuel cell, Glancing angle deposition, Ni-GDC anode, Low-temperature solid oxide fuel cell, Thickness effect, Nanoporous substrate키워드:
박막 고체산화물 연료전지, 회전경사증착, Ni-GDC 연료극, 저온작동 고체산화물 연료전지, 두께 효과, 나노다공성 기판1. 서론
고체산화물 연료전지(Solid Oxide Fuel Cell, SOFC)는 이트리아 안정화 지르코니아(Yttria Stabilized Zirconia, YSZ) 등의 고체산화물을 전해질로 사용하는 연료전지로, 고온 작동에 따른 사용 가능한 연료의 다양성, 폐열의 사용 가능성으로 인한 높은 연료 효율, 단순한 구조 등의 다양한 장점으로 인해 차세대 전력원으로 거론되고 있다[1,2]. 하지만, 고체 산화물 전해질의 이온 전도 메커니즘 상 약 700-1,000oC의 고온 영역에서 작동되어 왔으며, 그로 인한 연료전지 및 주변 설비의 열적 내구성(Thermal Durability) 이슈가 꾸준히 제기되어 왔다[1,3-5]. 이에 대한 해결방안으로, 전해질을 수 마이크로미터 이하의 박막의 형태로 제작하고, 비교적 저온 영역인 500-600oC 수준에서 작동시키는 박막 SOFC의 개념이 주목받고 있다[6-9]. SOFC의 저온구동은 전극에서의 활성화 손실(Activation Loss)의 증가 및 전해질에서의 이온전도도 감소에 따른 저항손실(Ohmic Loss)의 증가를 야기한다. 이때 박막 전해질을 SOFC에 적용하면 전해질에서의 이온 전도 경로 감소에 따라 이온 전도 저항이 감소함으로써 저온 구동 시의 저항 손실을 상쇄시키고 상대적인 저온에서도 합리적인 성능을 제공할 수 있다[6-9].
특히 박막 전해질뿐만 아니라 SOFC 구성요소를 모두 박막으로 제작하는 연구로써 비전도성 다공성 기판인 양극 산화 알루미늄(Anodic Aluminum Oxide, AAO)를 사용한 연구가 활발히 진행되어 왔다[10-14]. 이는 AAO의 고온에서의 안정성, 기공 크기 조절의 용의성, 대량생산 가능성에 기인한다. 최근 연구에 따르면, AAO 기판 상에 스퍼터링 기법을 사용하여 제작된 SOFC는 연료극 두께 증가에 따라 분극저항(Polarization Resistance)이 증가하고, 전극 면내(In-Plane) 방향으로의 옴저항(Ohmic Resistance)이 감소하는 교환관계를 가진다[13,14]. 이는 연료극 두께 증가에 따라 연료의 확산을 통한 전달이 이루어지는 기공이 닫히면서 연료전지의 반쪽반응 중 연료극 산화반응(HOR)이 일어나는 삼상계면(Triple Phase Boundary, TPB)이 감소하는 반면, 이때 발생하는 전자가 전도되는 전극의 단면적은 증가하기 때문이다. 이러한 기존 연구에 기반하여, 연료극의 기공도는 유지한 채 그 두께만 증가시킬 수 있다면, 분극저항은 그 수준을 유지하되 옴저항만 감소시킴으로써 셀의 추가적 성능 향상을 기대할 수 있다[13].
이를 바탕으로, 본 연구는 상용 기판 중 가장 큰 기공 크기(250 nm)를 가지는 AAO 기판 상에, 두꺼운 전극 물질을 증착 시에도 높은 다공성을 유지할 수 있다고 알려진 GLAD (Glancing Angle Deposition) 스퍼터링 기법을 사용하여 서로 다른 연료극 두께를 갖는 박막 SOFC를 제작하였다[15,16]. 연료극 두께의 영향만을 비교하기 위하여 전해질 및 공기극은 양 셀에서 동일한 물질 및 두께로 스퍼터링하여 증착되었다. 제작된 박막 연료전지의 구조 분석을 위해 전체 연료전지의 단면과 연료극 및 전해질 증착면에 대해 주사전자현미경(Scanning Electron Microscope, SEM) 사진을 촬영하였다. 또한, 정량적인 성능 비교 및 분석을 위해 선형주사전위법(Linear Sweep Voltammetry, LSV) 및 전기화학 임피던스 분광법(Electrochemical Impedance Spectroscopy, EIS)을 사용하여 전류-전압-전력(I-V-P) 및 나이퀴스트(Nyquist) 선도를 도출하였다. 각각의 측정결과들의 상호 연관관계를 심도 있게 분석하였으며, 이를 통해 다공성 박막 연료극의 두께 변화에 따른 박막 SOFC 성능 변화 양상에 대한 해석을 논의하였다.
2. 실험 방법(Experimental Methods)
2.1 셀 제작
박막 SOFC의 제작을 위한 기판으로 평균 지름 250 nm의 기공을 가지는 상용 AAO 기판(1 cm × 1 cm × 100 μm) (Inredox, USA)을 사용하였다. AAO 기판 상에 Ni 와 GDC를 입사각 45o로 GLAD 동시 스퍼터링하여 Ni-GDC 연료극을 증착하였다. 스퍼터링은 초기진공 6.67 e-4 Pa (5 e-3 mTorr) 및 Ar 가스 8.00 Pa (60 mTorr)의 환경에서 Ni 금속 타겟(RND Korea, South Korea)과 GDC 세라믹 타겟(20 : 80 mol %) (RND Korea, South Korea)에 각각 DC 200 W, RF 50 W의 파워를 사용하여 진행하였다.
샘플 간 증착되는 연료극 두께 조절을 위하여 각 샘플의 연료극 스퍼터링 시간을 조절하였고, 각각 800, 3,000 nm의 두께로 증착하였다. 연료극 두께로 800, 3,000 nm를 선정한 이유는 다음과 같다. 기존의 작은 기공크기(80 nm)를 가지는 AAO 기판에서의 연료극 두께에 따른 저항의 교환관계를 관찰한 기존 연구의 경우 300-1,000 nm의 연료극 두께를 사용하였으며, 최적성능은 800 nm에서 관찰되었다[14]. 본 연구는 기존 연구 대비 약 3배 더 큰 기공 크기(250 nm)를 가지는 AAO 기판을 사용함으로써 더 두꺼운 연료극에서의 분극저항 유지 및 옴저항 감소를 기대하였기 때문에 기존 연료극 두께 범위의 약 3배에 해당하는 800, 3,000 nm의 연료극 두께를 사용하였다. 해당 스퍼터링 과정의 개략도는 아래 Fig. 1과 같다.
전체 셀에 대해 전해질 및 공기극은 동일한 조건 및 두께로 증착하였다. 먼저, 전해질은 지름 2인치 Y/Zr 합금 타겟(16 mol % Y) (RND Korea, South Korea)을 이용하여 초기진공 6.67 e-4 Pa (5 e-3 mTorr), Ar/O2 혼합가스(80 : 20 vol %) 0.667 Pa (5 mTorr)의 환경에서 RF 200 W로 스퍼터링하여 800 nm 두께로 증착하였다. 이어서, 공기극은 지름 2인치 Pt 타겟(RND Korea, South Korea)을 이용하여 초기진공 6.67 e-4 Pa (5 e-3 mTorr), Ar 가스 12.0 Pa (90 mTorr)의 환경에서 DC 100W로 스퍼터링하여 150 nm 두께로 증착하였다.
최종적으로, AAO – Ni-GDC (800 nm) – YSZ – Pt의 구조를 가지는 셀과, AAO – Ni-GDC (3,000 nm) – YSZ – Pt의 구조를 가지는 셀을 제작하였으며, 각각을 ‘Ni-GDC 8’, ‘Ni-GDC 30’으로 명명하였다.
2.2 셀 구조 확인
완성된 셀의 구조적 결함 여부 및 각 층의 증착 두께 확인을 위해 셀의 단면의 집속 이온빔 주사전자현미경(Focused Ion Beam Scanning Electron Microscope, FIB-SEM) (Quanta 3D FEG, FEI Company, USA) 사진을 촬영하였다. 또한, 연료극 두께의 연료극-전해질 계면에의 영향 및 전해질에의 영향을 확인하기 위하여 AAO 기판 상에 증착된 연료극 표면과, 연료극 위에 증착된 전해질 표면의 전계방출형 주사전자현미경(Field Emission Scanning Electron Microscope, FE-SEM) (SUPRA 55VP, Carl Zeiss, Germany) 사진을 촬영하였다.
2.3 전기화학적 분석
완성된 셀의 성능 측정을 위하여 선형주사전위법과 전기화학 임피던스 분광법을 사용하였다. 측정에는 상용 전기화학 분석기기(Reference 600, Gamry Instruments, USA)을 사용하였다. 선형주사전위법은 개회로전압(OCV) - 0.3 V 사이의 전압 범위에 대해 0.01 V 단위, 0.025 V/s의 속도로 진행하였으며, 전기화학 임피던스 분광법은 0.6 V에서 진폭 30 mV 사인파로 2-1 MHz의 주파수 범위에서 측정하였다.
3. 결과 및 논의
3.1 구조 분석
아래 Fig. 2의 좌, 우측 열은 각각 Ni-GDC 8, Ni-GDC 30의 단면, 연료극 표면, 그리고 전해질 표면에서의 SEM 사진을 보여준다. 먼저, Figs. 2(a), 2(b)의 셀 단면 SEM 사진에서 각 셀의 모든 층이 박리 등의 특별한 결함없이 균일하게 증착되었음을 확인할 수 있다. 각 셀의 연료극 두께는 각각 800, 3,000 nm로 확인하였으며, 전해질과 공기극의 두께는 모두 동일하게 각각 800, 150 nm로 확인하였다.
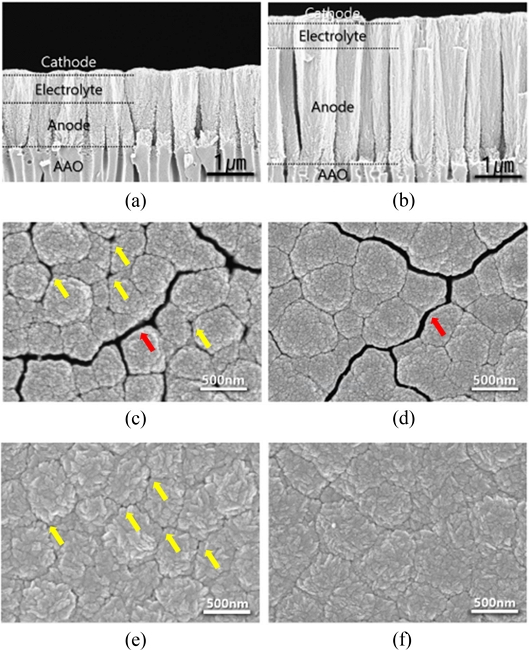
SEM picture of (a) cross section of Ni-GDC 8, (b) cross section of Ni-GDC 30, (c) anode plane of Ni-GDC 8, (d) anode plane of Ni-GDC 30, (e) electrolyte plane of Ni-GDC 8, and (f) electrolyte plane of Ni-GDC 30
연료극의 경우 Figs. 2(a), 2(b)의 SEM 단면 사진에서 결정립(Grain) 사이사이로 연료 확산이 가능한 기공들이 다수 확인 가능하다. 이들이 기존 연구에서 보고된 바와 같이 주상조직의 형태로 성장하며, 연료극의 두께가 두꺼워질수록 기둥의 지름이 커지는 것으로 관찰되었다. AAO로부터 이어지는 기공은 연료극의 두께가 두꺼워질수록 닫혀가는 것 또한 확인이 가능하다[17-19]. 이러한 현상의 영향은 Figs. 2(c), 2(d)의 연료극 표면 SEM 사진에서도 간접적으로 확인할 수 있는데, Fig. 2(c)의 Ni-GDC 8의 연료극 표면의 경우 아직 연료극의 두께가 비교적 얇아 두껍게 연결되어 있는 메인 채널(붉은 화살표 표시) 이외에도 결정립 사이사이로 미쳐 닫히지 못한 미세 기공(노란 화살표 표시)이 다수 보이는 반면, Fig. 2(d)의 Ni-GDC 30의 경우 메인 채널은 존재하나, 이외의 미세 기공은 대부분 닫혀 있는 모습을 확인할 수 있다.
전해질의 경우 Figs. 2(a), 2(b)의 SEM 단면 사진에서 연료극의 일부 기공이 이어지기는 하나, 두께 증가에 따라 기공이 닫혀 기밀성이 이루어지는 것으로 보인다. 하지만, Figs. 2(e), 2(f), 의 전해질 표면 확인 결과, 2(e)의 Ni-GDC 8의 경우 노란 화살표로 표시한 것과 같이 전해질 평면상에 미쳐 닫히지 못한 매우 미세한 기공이 일부 존재하는 것을 확인할 수 있다. 반면, Fig. 2(f)의 Ni-GDC 30의 경우 그러한 기공이 확인되지 않는다. 이는 전해질의 증착 두께가 800 nm로 비교적 얇아 Ni-GDC 8과 Ni-GDC 30의 연료극 표면구조의 영향이 전해질 표면까지 이어졌기 때문으로 추정된다.
3.2 전기화학적 분석
양 셀의 전반적인 성능 분석 및 비교를 위해 선형주사전위법을 사용하여 얻은 데이터를 바탕으로 Fig. 3의 i-V-P 곡선을 확보하였다. 구분을 위해 Ni-GDC 8의 경우 주황색, Ni-GDC 30의 경우 검정색으로 표현하였다. Ni-GDC 8, Ni-GDC 30은 각각 1.081, 1.049 V의 OCV를 기록하여 Ni-GDC 8이 미세하게 더 높은 OCV를 기록하였다. 이러한 OCV의 차이는 Figs. 2(e), 2(f)의 전해질 표면 SEM 사진을 통해 원인을 유추해 낼 수 있다. Ni-GDC 30의 경우 전해질 층에서 보다 안정적인 기체 차단이 이루어진 반면, Ni-GDC 8의 경우 연료극 표면에서 보이던 기공이 전해질 표면까지 이어져 미세한 연료 크로스오버가 발생하고 이로 인해 OCV가 낮게 측정된 것으로 추정된다.
하지만, 최대전력밀도의 경우 Ni-GDC 8, Ni-GDC 30이 각각 223.6, 181.2 mW/cm2로 Ni-GDC 8에서 약 23% 더 좋은 성능이 기록되었다. 이는 앞선 OCV의 경향성과, 서론에서 언급한 실험 설계를 고려할 때 직관적이지 않은 결과로, 이에 대한 상세 원인 분석을 위하여 전기화학 임피던스 분광법을 실시하였다.
양 셀에 대해 취득된 전기화학 임피던스 분광법 결과는 Fig. 4(a)와 같다. 측정결과를 Fig. 4(a) 좌측 상단의 등가회로모델(Equivalent Circuit Model, ECM)을 가정하고 피팅하였다. 해당 등가회로는 하나의 저항 성분과, Constant Phase Element (CPE)와 저항이 병렬로 연결된 RQ 성분 두개가 직렬로 연결된 형태이다. 각각의 RQ 성분은 연료극과 공기극을 나타내며, 저항성분은 전체 전지에서의 옴저항을 나타낸다. 그 결과로써 Ni-GDC 8, Ni-GDC 30에 대해 각각 0.587, 0.489 Ω·cm2의 옴 저항과 0.668, 1.78 Ω·cm2의 분극저항 값을 얻을 수 있었다. 이는 Fig. 4(b)의 막대그래프에서 확인할 수 있다.
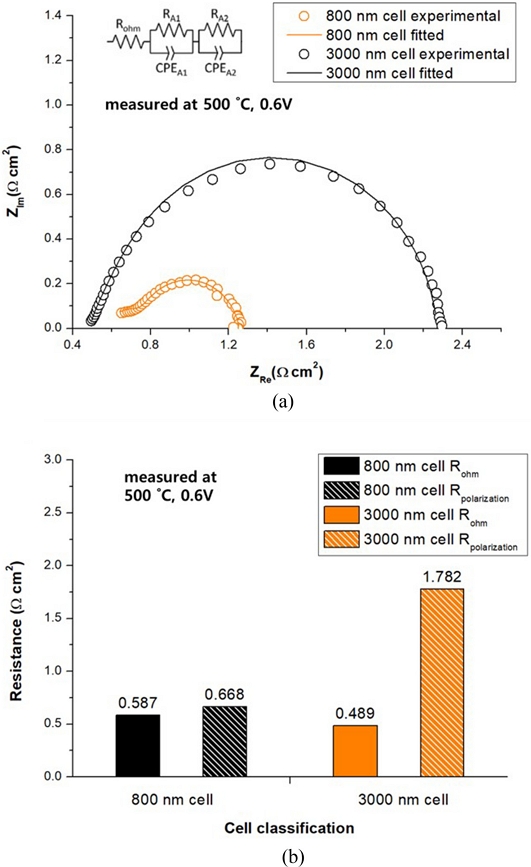
(a) EIS results of two TF-SOFCs plotted with line graphs fitted by ECM. (b) Impedance values are divided into ohmic resistance and faradaic resistance, respectively
먼저, 서론에서 예상한 바와 같이 연료극 두께 증가에 따라 옴저항이 0.598 Ω·cm2에서 0.457 Ω·cm2로 23.4% 감소하였다. 연료극 두께가 275% 증가하였지만, 옴 저항은 23.4%밖에 감소하지 않은 것은 옴 저항에 기여하는 다른 성분인 전해질에서의 이온전도 저항 및 공기극에서의 저항은 그대로 유지되었기 때문으로 추정된다. 반면, 분극저항의 경우 큰 변화 없이 유지될 것이라는 예상과 달리 66.7% 증가하였다. 이는 비교적 큰 기공 크기의 AAO(250 nm)와 GLAD 스퍼터링을 사용했음에도 불구하고 연료극의 두께가 증가함에 따라 연료극 표면에서의 미세 기공이 결국 닫히고, 이것이 연료극과 전해질 사이의 계면의 TPB 감소로 이어졌기 때문으로 추정된다. 이는 Figs. 2(c), 2(d)에서도 확인할 수 있는데, Fig. 2(c)의 Ni-GDC 8의 연료극 표면의 경우 빨간 화살표로 표시된 메인 채널 이외에도 노란 화살표로 표시된 작은 채널들이 곳곳에 존재하며 이들이 모두 TPB 형성에 기여하나, Fig. 2(d)의 Ni-GDC 30의 연료극 표면의 경우 빨간 화살표로 표시된 메인 채널 주변에서만 TPB가 생성될 것으로 예상된다. 추가적으로, 이온-전자 혼합전도체(Mixed Ionic-Electronic Conductor, MIEC) 물질인 Ni-GDC를 사용함에 따라 연료극 두께에 따른 TPB 증가의 효과도 존재하였겠지만, Ni-GDC 내 Ni의 비율이 높아 연료극 두께에 따라 미미한 TPB 향상만을 야기하였고, 결과적인 분극저항에의 영향이 기공 닫힘에 의한 TPB 감소 대비하여서는 훨씬 적었던 것으로 예상된다. 또한, 앞서 언급한 것과 같이 Ni-GDC 8의 경우 전해질에 미세한 기공이 형성되고, 이것이 연료 크로스오버를 야기하여 Ni-GDC 8에서 일부 성능저하를 야기할 것이다. 하지만, 전해질의 경우 연료극 위에 증착되므로 연료극 대비 생성되는 기공의 크기가 매우 미세하며, 이는 Fig. 2(e)에서 확인할 수 있다. 따라서, Ni-GDC 8의 전해질 상 미세한 기공에 의한 성능 감소는 Ni-GDC 30에서의 기공닫힘에 따른 TPB 감소 및 그에 따른 성능 감소 대비 그 크기가 작았던 것으로 추정된다. 결과적으로, 연료극 두께 증가에 따라 셀의 옴저항은 감소하였지만, 그 두께 증가 폭이 지나쳐 GLAD 기법 등을 사용했음에도 불구하고 기공 감소에 따른 TPB 감소 및 분극저항의 증가가 발생하였다. 이는 초기 예상과는 다르게 최대전력밀도 기준 오히려 18.9%의 성능감소를 야기하였다. 이처럼, 비전도성, 다공성 기판인 AAO 기반의 박막 SOFC의 경우 연료극 두께 증가에 따라 옴저항과, 분극저항의 경향성이 각기 다르게 나타나는 것을 다시 확인할 수 있었다. 두께 3,000 nm의 연료극을 갖는 Ni-GDC 30의 경우 감소된 전기 전도 저항보다 증가된 분극 저항의 비율이 압도적으로 높았고, 이는 결과적으로 Ni-GDC 8 셀에 비해 Ni-GDC 30 셀에서의 성능이 23% 이상 열세하게 되는 원인이 되었다. 하지만, 이전 진행된 연구 참조 시, 연료극 두께 증가에 따른 분극저항 변화는 초기 감소 이후 다시 급격하게 증가되므로[14], 만약 해당 실험에서 연료극 두께 증가가 조금 더 세밀하게 조절되어 증가되었다면 최적의 성능을 나타내는 연료극 두께를 확인할 수 있었을 것으로 판단된다.
4. 결론
이번 연구는 AAO 기판 상에 스퍼터링을 이용하여 제작된 SOFC 셀의 연료극 두께에 따른 옴저항과 분극저항 간의 교환관계를 다룬 선행연구에서 출발하여 더 큰 기공 크기를 가지는 AAO와 GLAD 스퍼터링을 사용할 시의 성능변화를 확인하였다. 본래 분극 저항은 유지되며, 옴 저항은 감소하여 셀의 성능은 전반적으로 상승할 것이라는 예상과 달리, 옴저항은 0.587 Ω·cm2에서 0.489 Ω·cm2로 23.4% 감소하였지만, 분극저항은 0.668 Ω·cm2에서 1.78 Ω·cm2로 오히려 66.7% 증가하여 전체 성능은 최대전력밀도 기준 223.6 mW/cm2에서 181.2 mW/cm2로 18.9% 감소하였다. 여기서, 옴저항의 경우 연료극 두께 증가에 따라 전자의 전도 면적이 증가함에 따라 감소하였으며, 분극저항의 경우 연료극 두께 증가에 따라 기공 닫힘 및 그에 따른 TPB 감소에 따라 증가하였다. OCV의 경우 연료극 두께 증가에 따라 오히려 미세하게 증가하였는데, 이는 연료극의 기공 닫힘이 더 많이 이루어진 상태에서 스퍼터된 전해질이 더 치밀하게 증착되었고, 그에 따라 기체 차단성능이 더 좋았기 때문인 것으로 추정된다. 이처럼 비전도성 기판 위에 제작된 박막 SOFC가 갖는 두 저항 특성에 대한 이해를 바탕으로 두 연료전지의 성능 차이의 인과관계를 파악하였다. 연료극 두께의 증가가 지나쳐 분극저항이 크게 증가하고, 전체 성능은 감소하였음을 고려할 때, 향후 추가 연구를 통해 최적 연료극 두께의 도출하고 추가적인 성능 향상이 가능할 것으로 예상된다.
Acknowledgments
This paper was presented at KSPE Spring Conference 2022
이 논문은 대한민국 정부(과학기술정보통신부)의 재원으로 한국연구재단 수소에너지혁신기술개발사업의 지원을 받아 수행된 연구임(No. 2019M3E6A1064695).
REFERENCES
-
O’hayre, R., Cha, S.-W., Colella, W., Prinz, F. B., (2016), Fuel cell fundamentals, John Wiley & Sons.
[https://doi.org/10.1002/9781119191766]
- Spiegel, C., (2007), Designing and building fuel cells, Mcgraw-hill New York.
-
Golkhatmi, S. Z., Asghar, M. I., Lund, P. D., (2022), A review on solid oxide fuel cell durability: Latest progress, mechanisms, and study tools, Renewable and Sustainable Energy Reviews, 161, 112339.
[https://doi.org/10.1016/j.rser.2022.112339]
-
Hanasaki, M., Uryu, C., Daio, T., Kawabata, T., Tachikawa, Y., Lyth, S., Shiratori, Y., Taniguchi, S., Sasaki, K., (2014), SOFC durability against standby and shutdown cycling, Journal of The Electrochemical Society, 161(9), F850.
[https://doi.org/10.1149/2.0421409jes]
-
Ju, Y.-W., Eto, H., Inagaki, T., Ida, S., Ishihara, T., (2010), Improvement in thermal cycling durability of SOFCs using LaGaO3-based electrolyte by inserting convex Sm0. 5Sr0. 5CoO3 interlayer, Electrochemical and Solid-State Letters, 13(12), B139.
[https://doi.org/10.1149/1.3494029]
-
Lee, Y. H., Chang, I., Cho, G. Y., Park, J., Yu, W., Tanveer, W. H., Cha, S. W., (2018), Thin film solid oxide fuel cells operating below 600 C: A review, International Journal of Precision Engineering and Manufacturing-Green Technology, 5(3), 441-453.
[https://doi.org/10.1007/s40684-018-0047-0]
-
Chasta, G., Dhaka, M. S., (2022), A review on materials, advantages, and challenges in thin film based solid oxide fuel cells, International Journal of Energy Research, 46(11), 14627-14658.
[https://doi.org/10.1002/er.8238]
-
Zhang, J., Ricote, S., Hendriksen, P. V., Chen, Y., (2022), Advanced materials for thin-film solid oxide fuel cells: Recent progress and challenges in boosting the device performance at low temperatures, Advanced Functional Materials, 32(22), 2111205.
[https://doi.org/10.1002/adfm.202111205]
-
Liang, F., Yang, J., Zhao, Y., Zhou, Y., Yan, Z., He, J., Yuan, Q., Wu, J., Liu, P., Zhong, Z., (2022), A review of thin film electrolytes fabricated by physical vapor deposition for solid oxide fuel cells, International Journal of Hydrogen Energy, 47(87), 36926-36952.
[https://doi.org/10.1016/j.ijhydene.2022.08.237]
-
Lim, Y., Hong, S., Bae, J., Yang, H., Kim, Y.-B., (2017), Influence of deposition temperature on the microstructure of thin-film electrolyte for SOFCs with a nanoporous AAO support structure, International Journal of Hydrogen Energy, 42(15), 10199-10207.
[https://doi.org/10.1016/j.ijhydene.2017.03.148]
-
Hong, S., Bae, J., Koo, B., Kim, Y.-B., (2014), High-performance ultra-thin film solid oxide fuel cell using anodized-aluminum-oxide supporting structure, Electrochemistry Communications, 47, 1-4.
[https://doi.org/10.1016/j.elecom.2014.07.008]
-
Kwon, C. W., Son, J. W., Lee, J. H., Kim, H. M., Lee, H. W., Kim, K. B., (2011), High-performance micro-solid oxide fuel cells fabricated on nanoporous anodic aluminum oxide templates, Advanced Functional Materials, 21(6), 1154-1159.
[https://doi.org/10.1002/adfm.201002137]
-
Lee, M. S., Lee, S., Jeong, W., Ryu, S., Yu, W., Lee, Y. H., Cho, G. Y., Cha, S. W., (2021), Nanoporous nickel thin film anode optimization for low-temperature solid oxide fuel cells, International Journal of Hydrogen Energy, 46(73), 36445-36453.
[https://doi.org/10.1016/j.ijhydene.2021.08.138]
-
Choi, I. W., Yu, W., Lee, M. S., Ryu, S., Lee, Y. H., Cha, S. W., Cho, G. Y., (2022), Tailoring 3D structured nanofibrous nickel/gadolinium-doped ceria anodes for high-performance thin-film solid oxide fuel cells, Journal of Power Sources, 531, 231320.
[https://doi.org/10.1016/j.jpowsour.2022.231320]
-
Sit, J., Vick, D., Robbie, K., Brett, M., (1999), Thin film microstructure control using glancing angle deposition by sputtering, Journal of Materials Research, 14(4), 1197-1199.
[https://doi.org/10.1557/JMR.1999.0162]
-
Hawkeye, M. M., Brett, M. J., (2007), Glancing angle deposition: Fabrication, properties, and applications of micro-and nanostructured thin films, Journal of Vacuum Science & Technology A: Vacuum, Surfaces, and Films, 25(5), 1317-1335.
[https://doi.org/10.1116/1.2764082]
-
Hong, S., Lee, D., Lim, Y., Bae, J., Kim, Y.-B., (2016), Yttria-stabilized zirconia thin films with restrained columnar grains for oxygen ion conducting electrolytes, Ceramics International, 42(15), 16703-16709.
[https://doi.org/10.1016/j.ceramint.2016.07.123]
-
Minh, N. Q., Lee, Y. H., Tran, Q. T., Ren, H., Fullerton, E. E., Wu, E. A., Meng, Y. S., (2021), Sputtered thin-film solid oxide fuel cells, ECS Transactions, 103(1), 67.
[https://doi.org/10.1149/10301.0067ecst]
-
Lee, Y. H., Ren, H., Wu, E. A., Fullerton, E. E., Meng, Y. S., Minh, N. Q., (2020), All-sputtered, superior power density thin-film solid oxide fuel cells with a novel nanofibrous ceramic cathode, Nano Letters, 20(5), 2943-2949.
[https://doi.org/10.1021/acs.nanolett.9b02344]
Ph.D. candidate in the School of Mechanical Engineering, Seoul National University. His research interest is low-temperature solid oxide fuel cell and metal-supported fuel cell.
E-mail: jw0325@snu.ac.kr
Ph.D. candidate in the School of Mechanical Engineering, Seoul National University. His research interest is thin film solid oxide fuel cell and electrochemical analysis.
E-mail: mtothes2@snu.ac.kr
Ph.D. candidate in the School of Mechanical Engineering, Seoul National University. His research interest is thin film solid oxide fuel cell and proton exchange membrane water electrolysis.
E-mail: kyjtree@snu.ac.kr
Professor in the School of Mechanical Engineering, Seoul National University. His research interest is fuel cells and energy system simulation.
E-mail: swcha@snu.ac.kr