
PBF (Powder Bed Fusion)와 DED (Directed Energy Deposition)의 연속 공정으로 적층제조된 630 스테인레스강의 마모 거동에 관한 연구
Copyright © The Korean Society for Precision Engineering
This is an Open-Access article distributed under the terms of the Creative Commons Attribution Non-Commercial License (http://creativecommons.org/licenses/by-nc/3.0) which permits unrestricted non-commercial use, distribution, and reproduction in any medium, provided the original work is properly cited.
Abstract
Hybrid additive manufacturing (AM) refers to a combination of two metal AM techniques: material deposition by powder bed fusion (PBF) and additional building by directed energy deposition (DED). This study focused on different characteristics in accordance with relative deposition directions of PBF and DED during hybrid AM production. Characteristics of the sample fabricated by hybrid AM (i.e., hybrid sample) were compared with those of the sample fabricated by PBF or DED. Ferrite was dominant in the microstructure of PBF deposits with very fine retained austenite observed locally. In contrast, lath martensite and retained austenite were formed uniformly in the microstructure of DED deposits. Different microstructures in the two processes were attributed to differences of cooling rate. In DED deposits, microhardness was significantly decreased owing to a high retained austenite fraction. However, in the hybrid sample, microhardness was rapidly increased in the HAZ owing to aging heat treatment for long-term deposition. Principal wear mechanisms of PBF and DED samples were oxidative wear and plastic deformation, respectively.
Keywords:
Powder bed fusion, Directed energy deposition, 630 stainless steel, Microstructure, Microhardness, Wear test키워드:
파우더 베드 퓨전, 직접에너지 적층, 630 스테인레스강, 미세조직, 미세경도, 마모시험1. 서론
AM (Additive Manufacturing)은 3차원의 복잡한 부품을 절삭이 아닌 소재를 Layer-by-layer 방식으로 적층하여 제조하는 공정이다. AM은 맞춤형 설계가 가능하고, 폐기되는 재료의 양이 감소하기 때문에 비싼 소재를 이용한 부품 제작에 있어서는 기존의 절삭에 의한 방식보다 경제적이다. 또한 절삭 가공으로 제작하기 어려운 형상도 제조 가능하기 때문에 AM은 제조 산업을 혁신시킬 수 있는 기술로 평가되고 있다. 이러한 이유로 AM은 자동차, 항공우주 그리고 의료 부품 제작에 다양하게 사용되고 있다[1-3].
금속을 재료로 하는 AM에는 PBF (Powder Bed Fusion)과 DED (Directed Energy Deposition)로 분류된다. PBF은 플랫폼 위에 금속 분말을 얇게 도포한 뒤 선택적으로 고출력 에너지를 조사하여 소결(Sintering) 또는 용융(Melting)시켜 3차원 형상의 단면을 Layer-by-layer 방식으로 적층하는 방식이다. DED는 금속 표면에 레이저 혹은 전자 빔을 조사하여 표면을 용융시키고, 여기에 금속 분말을 공급하여 용융 및 응고시켜 가면서 적층하는 방식이다. PBF는 DED에 비해서 높은 정밀도와 우수한 표면 품질을 가진 제품을 제조할 수 있다. 따라서, 복잡한 형상을 가진 금속 부품을 생산하는데 적합한 기술로 간주된다[4]. 하지만 생산 속도가 상대적으로 느리며, 챔버(Chamber) 크기에 따라 제작할 수 있는 제품의 크기에 제한이 있다. DED는 PBF에 비해 정밀도와 표면 품질은 덜 우수하지만, 생산 속도가 PBF에 비해 상대적으로 빠르며, 국부적인 영역에 적층이 가능한 장점을 가지고 있다. 따라서 DED는 이미 제작된 제품의 표면강화 및 사용 중 손상이 발생한 부품의 보수와 리모델링 등과 같은 응용으로 산업적 활용도가 높다[5-8]. 이러한 두 기술이 결합된 하이브리드 AM은 각 기술의 단점을 보완하고 장점을 극대화할 수 있으며, 개별 공정을 채택했을 경우 대비 더욱 광범위한 부품 제작이 가능하게 할 것이다. 또한 기존 공정 대비 생산 효율을 극대화할 수 있다.
하지만 현재 하이브리드 AM과 관련된 연구는 AM과 절삭가공이 결합된 것에 국한되어 있다. 따라서, PBF와 DED가 결합된 하이브리드 AM에 대한 연구는 미비한 실정이다. Schneider 등은 316L 스테인레스강으로 제작된 PBF와 DED 부품을 V자 이음새를 이용해 접합하여 하이브리드 샘플을 제작하였고, 미세조직과 경도를 분석하였다[9]. Kumaran 등은 PBF와 DED을 결합하여 316L 스테인레스강으로 제작된 샌드위치 구조의 특성에 대해 조사하였다[10,11]. 또한, PBF와 DED 샌드위치 구조 샘플이 각각 PBF와 DED로 제작된 샘플과 유사한 기계적 특성이 나타난다고 밝혔다. 또한, XRD 분석을 통해 샌드위치 구조 샘플에 대한 잔류 응력에 대해 조사하였으며, DED 적층부, 경계부, 그리고 PBF 적층부의 잔류 응력을 비교했을 때 경계부에서 가장 높게 나타났다고 밝혔다.
하나의 부품을 영역별로 혹은 기능별로 구분하여 PBF와 DED로 제조하는 방식의 AM 기술은 앞으로도 연구가 필요한 실정이다. PBF와 DED 각각의 적층 원리에 따른 미세조직의 차이점에 대한 깊이있는 분석이 필요하며, 이에 따른 다양한 기계적 특성에 관한 연구가 필수적이다. 또한, 적층 제조된 제품의 이방성으로 인해 PBF와 DED의 적층 방향에 따른 특성 변화에 대한 연구도 매우 중요하다고 할 수 있다.
본 연구에서는 높은 강도 및 내마모성과 내식성[12-14]으로 항공 우주, 원자력, 석유 산업 분야에서 널리 사용되고 있는 630 스테인레스강을 사용한 AM에 대한 연구를 진행하였다. 630 스테인레스강은 아크 용접에 대한 용접성(Weldability)이 우수하기 때문에 활용도가 높은 합금으로 평가받고 있으며[15], 최근에 PBF 공정에 대한 연구 주제로 많이 응용되고 있다[16-20]. 본 연구에서는 PBF로 적층 제조된 소재 위에 DED로 추가 적층하는 방식으로 샘플을 제작하였다. 특히, 샘플 제작 시에 PBF와 DED 간의 상대적 적층 방향을 다르게 하였다. 제작된 샘플을 이용해 적층부의 미세조직과 경도를 비교하였으며, 이것이 마모 거동에 미치는 영향을 분석하였다.
2. 실험 방법
2.1 재료
본 연구에서는 630 스테인레스강 분말을 이용하여 PBF를 통해 모재(Substrate)를 제작하였으며, 동일한 조성의 분말을 DED 적층에도 사용되었다. 630 스테인레스강의 특성은 석출 경화 열처리를 통해 향상될 수 있으며, 따라서 “단일 처리 마르텐사이트 강”이라고 한다. Fig. 1에 DED용 분말과 PBF용 분말을 나타내었다. 두 가지 모두 가스아토마이징(Gas Atomizing)을 통해 구형으로 제조(Carpenter Co., USA)되었다. DED용 분말의 직경은 45-150 μm이고, PBF용 분말의 직경은 20-40 μm이다. Table 1에 두 분말의 화학적 조성을 나타내었다.
2.2 DED 및 PBF 공정 원리와 사용 장비
Figs. 2(a)와 2(b)는 각각 DED와 PBF의 적층 원리 및 방법을 나타낸다. DED에서는 각 레이어(Layer)를 형성하기 위해 먼저 2차원 단면의 외부경계를 따라 비드를 적층한다(이를 “컨투어”라고 함). 컨투어 적층 후, 지그재그(Zig-zag) 패턴으로 단면 내부에 적층 비드를 채우게 된다(이를 “포켓”이라고 함). 이러한 방식으로 하나의 레이어를 만들고, 다음 레이어에서는 이전 레이어와 90o 교차하여 높이 방향으로 적층된다. 전체 3차원 적층이 완료될 때까지 이를 반복한다. PBF는 그림에서와 같이 헥사곤(Hexagon) 패턴이 사용된다. 이는 315o(홀수 번째 레이어)와 225o(짝수 번째 레이어) 사이에서 번갈아 나타난다.
본 연구의 DED 공정에는 DMT (Direct Metal Tooling) MX3 (Insstek Co., Korea)가 사용되었다. MX3는 MX-CAM 소프트웨어로 작동하는 5축 NC 장치이며, 4 kW CO2 레이저 시스템을 포함한다. 3개의 분말 호퍼와 함께, 분말과 공정 가스를 공급하기 위한 노즐로 구성된 분말 공급시스템이 있다. 공정 중 산화를 방지하고 분말을 공급하기 위해 아르곤이 사용되었다. 분말 공급 장치가 설치된 헤드에 광학 시스템이 설치되었으며, 모재 표면으로부터 9 mm 떨어진 직경 1.0 mm 노즐을 사용하였다.
PBF에는 DMP (Direct Metal Printers, ProX300, 3D Systems, USA)가 사용되었다. ProX300은 ProX DMP Manufacturing 소프트웨어로 작동하는 3축 장비이며, 500 W 파이버 레이저 시스템을 포함한다. 베드에 분말을 도포하기 위한 별도의 롤러 시스템이 있으며, Nitrogen 또는 Argon로 채워진 챔버에서 제조한다.
2.3 시편 제작 및 전처리
Fig. 3은 PBF 모재에 대하여 DED 국부 영역 적층 시 적층 방향에 따른 시편의 제작 과정을 나타내고 있다. 본 연구에서는 PBF로 제작된 부품이 사용 중 국부 파손이 발생하였을 경우, 파손 영역에 대하여 DED를 활용한 국부 적층을 통해 보수하는 과정을 가정하였다. 따라서, 먼저 PBF로 모재를 제작한 후 그루브(Groove) 가공한 뒤, 이 부분에 DED 적층하여 시편을 제작하였다. PBF와 DED의 적층 방향에 따라서 HYBRID (Parallel)와 HYBRID (Cross)로 구분하였다. 적층된 소재는 와이어 컷팅(Wire Cutting)으로 마모 시편의 형상으로 절단하였으며, 그라인딩(Grinding)을 통해 시편을 정밀하게 마무리하였다. DED와 PBF 적층부의 경계는 시편의 중앙에 위치하도록 하였다.
마모 시험은 볼온디스크(Ball-on-disk) 방식의 상온 마모시험기(Abrasion tester, R&B, Korea, 친환경선박핵심연구지원센터)를 사용했으며, 작용 하중 100 N과 회전속도 80 RPM에서 직경 18 mm의 마모 트랙을 10분 동안 알루미나 볼이 회전하는 방식으로 마모 실험을 수행하였다. 본 연구에서는 적층 샘플의 후열 처리(Post-heat Treatment)가 소재 특성에 영향을 끼칠 수 있기 때문에 적층 후에는 열처리를 하지 않았다.
3. 실험 결과 및 고찰
3.1 시편 제작 및 전처리
HYBRID (Parallel)와 HYBRID (Cross)는 Fig. 3에 나타낸 것과 같이 각각 PBF 모재의 상면(Upper Surface)과 옆면(Side Surface)에 DED 적층이 이어진다. DED 적층이 시작되는 모재의 표면 특성은 PBF와 DED 적층 경계면 특성에 영향을 미칠 수 있다. Fig. 4(a)는 PBF 모재 상면(여기에는 Layer를 생성하기 위한 적층 트랙이 형성되어 있다)과 측면(적층 Layer가 형성되어 있음)의 표면 특성을 관찰한 결과이다. 상면에서는, 레이저 스캔에 의해 형성된 트랙과 국부적인 영역에 볼링(Balling)이 확인된다. 반면에 측면에서는 주로 소결된 분말들이 다수 형성됐고, 일부 국부적인 영역에 볼링도 관찰됐다. PBF 모재의 상면과 측면에 대한 3D 형상과 거칠기(Roughness) 측정 결과, 상면과 측면은 각각 13.95 μm와 17.15 μm의 거칠기를 가지는 것으로 나타났다. 이러한 거칠기의 차이는 DED 적층 시 경계면에서의 소재 간 융합(Fusion)에 영향을 미칠 수 있다.

Surface roughness of PBF substrates and observation of defects near the interface between PBF deposits and DED deposits
두 샘플의 PBF-DED 경계면을 분석하기 위해 OM 관찰하였고, 그 결과를 Fig. 4(b)에 나타내었다. 그림에서 알 수 있듯이 HYBRID (Parallel)의 경계면에서는 결함이 발생하지 않았지만, HYBRID (Cross)의 일부 경계에서는 결함(Interfacial Defect)이 관찰되었다. 두 샘플 모두 동일한 DED 적층 조건으로 제작되었기 때문에, 결함은 PBF 적층부 표면 특성에 기인한다고 볼 수 있다. 앞서 설명한 것과 같이 PBF 적층부 측면의 표면거칠기가 상면에 비해서 더 높았으며, 따라서 측면에서 DED 적층이 시작될 경우 동일한 레이저 출력에 대한 에너지 흡수율이 상면과 비교해 낮아진다. DED 적층 시, 에너지 밀도가 낮아지게 되면 공급된 분말을 완전히 녹이지 못하기 때문에 융합부족(Lack of Fusion)에 의한 기공 결함이 발생할 수 있다.
또한, DED 적층 전 PBF 적층 모재의 측면에는 완전히 용융 되지 못한 분말들이 달라붙어 있었고, 이들은 일부 산화된 것을 확인할 수 있었다. 산화된 분말은 용융풀의 표면장력(Surface Tension)과 마랑고니 유동(Marangoni Flow)을 변화시키며 젖음성(Wettability)을 저하시킨다[15,16]. 또한, 측면의 높은 거칠기도 젖음성에 영향을 미쳤다고 판단되며, 이에 따라 HYBRID (Cross)의 경계에서 불완전한 젖음에 의한 결함이 발생한 것으로 추측할 수 있다. 이러한 결함은 HYBRID (Cross) 샘플의 경계부 일부에만 존재했지만, 하중이 작용될 경우 응력 집중(Stress Concentration)의 원인이 될 수 있다.
3.2 미세조직과 상분석
적층 샘플들의 미세조직(Microstructure)을 보여주는 SEM 사진들을 Fig. 5에 나타내었다. PBF 적층부는 용융풀(Melting Pool) 내부에 주상형 페라이트(Columnar Ferrite)가 적층 방향을 따라 형성된 것을 알 수 있다. 이미 적층된 레이어 위에 다음 레이어가 적층될 때, 응고 과정에서 새롭게 형성된 결정들(Crystals)이 이전 레이어의 결정 방향을 따라 에피택셜 성장(Epitaxial Growth, 파란색 화살표)하게 된다. 이러한 주상형 페라이트는 적층 비드 내부에 수십 μm의 길이로 형성되어 있으며, 인접한 비드로 뻗어 있는 경우 100 μm 이상으로 나타났다. 적층 비드 경계에는 국부적으로 잔류 오스테나이트(Retained Austenite)가 형성된 것을 알 수 있다. 이는 오버랩에 의한 재용융과 HAZ (Heat Affected Zone)에 의한 것으로 판단된다.
한편, DED 적층부는 오스테나이트 입계 내부에 형성된 래스 마르텐사이트(Lath Martensite)가 지배적으로 형성되었다. 하지만, DED 샘플에 형성된 래스 마르텐사이트는 전형적인 것과는 달리, 잔류 오스테나이트가 혼합되어 있다. PBF 적층 샘플에서는 주상형 페라이트가 지배적으로 형성된 반면에 DED 적층부에는 래스 마르텐사이트가 지배적으로 형성되었다. 이러한 차이는 두 공정의 냉각 속도 차이에 기인한다. DED와 PBF 공정 중 만들어지는 용융풀의 직경과 두께는 각각 1, 0.3, 0.08, 0.04 mm이다. DED 공정에서의 용융풀의 크기가 훨씬 크기 때문에 PBF에서의 용융풀 냉각속도가 높은 것이 일반적인 현상이다. 또한, DED 공정에서의 레이저 출력이 PBF에서보다 높은 반면 이송 속도는 더 느리다. 이는 DED 과정에서 훨씬 높은 에너지가 용융풀 주변에 공급되는 것을 뜻한다. 즉, DED 중 높은 에너지 공급으로 인해 입열과 열 축적이 크기 때문에 냉각 속도가 낮아질 수 있다. 일반적으로 PBF의 냉각 속도는 105-106 K/s로 알려져 있고[17], DED에서의 냉각 속도는 103-104 K/s로 알려져 있다[18,19].
XRD를 통해 상 분석을 수행하였고, 결과를 Fig. 6에 나타내었다. 630 스테인레스강은 매우 낮은 탄소 함량을 가지고 있으며, 이러한 저탄소강에서는 BCT 마르텐사이트의 격자 왜곡이 매우 작기 때문에 XRD 분석을 통해 BCC 페라이트와 BCT 마르텐사이트를 구분하는 것은 불가능하다[20]. 따라서, 본 논문에서는 BCC와 BCT 두 가지 상 모두 BCC 상이라고 가정한다. PBF 적층부와 DED 적층부 모두 BCC(페라이트 혹은 마르텐사이트) 상과 FCC(오스테나이트) 상이 존재하였다. PBF 적층부에는 BCC가, 그리고 DED 적층부에는 FCC가 지배적인 것을 알 수 있다. 하이브리드 샘플의 경우 PBF로 제작된 모재 위에 DED로 적층되었기 때문에, PBF 적층부보다 γ-iron이 높으며, DED 적층부 보다 α-iron이 증가한 것을 알 수 있다.
Fig. 7는 두 샘플의 EBSD 결과를 나타내고 있다. IPF Map을 통해 2개의 시편 모두 결정립들이 적층 방향을 따라 성장한 것을 알 수 있다. 이러한 결정립의 방향은 슬립 시스템(Slip System)과 하중(Loading) 방향과의 정렬에 영향을 미치기 때문에 이방성이 나타난다. PBF 적층부와 DED 적층부의 결정립 형태는 상이하게 나타났다. PBF 적층부는 조대한 BCC 상이 지배적으로 형성되어있고, 매우 미세한 FCC 상이 국부적으로 형성된 것을 알 수 있다. 반면에 DED 적층부는 BCC 상과 FCC 상들이 고르게 분포되어 있는 것을 알 수 있으며, PBF부에 비해 상 분율 차이가 크지 않은 것을 알 수 있다. PBF에서의 급속한 용융 및 응고는 적층된 630 스테인레스강의 오스테나이트 입자를 미세하게 만들었다[21]. 이에 비해 상대적으로 훨씬 낮은 DED에서의 냉각 속도는 오스테나이트 입자를 성장 시킬 수 있는 더 많은 시간을 제공하였다[22]. 또한, DED용 분말은 오스테나이트 안정화 원소인 N과 Cu의 원소 함량이 PBF용 분말보다 높은 것으로 확인되었다. 이러한 이유들로 DED 적층부의 FCC 상은 PBF 적층부에서보다 더욱 조대하게 형성될 수 있으며, FCC 분율도 증가하였다.
3.3 Microhardness
Fig. 8은 시편 단면에서 깊이 방향으로 측정된 미세경도(Microhardness) 분포를 나타내고 있다. PBF부와 DED부에서는 깊이에 따른 경도 변화가 크게 없이 비교적 일정하게 나타내고 있다. PBF 적층부와 DED 적층부의 평균 경도 값은 각각 347 HV와 232 HV로 나타났다. 이러한 차이는 PBF에서의 매우 빠른 냉각 속도로 인한 미세한 조직과 BCC 상에 기인한다. Hall-Petch 이론에 따르면, Grain 크기가 감소함에 따라 강도는 증가하게 된다[23]. 결정립이 미세할수록 결정립계에 인접한 전위밀도(Dislocation Density)는 더 높기 때문에 높은 경도를 나타낸다. 또한, DED부에 형성된 높은 분율의 잔류 오스테나이트는 낮은 경도의 원인이 된다.
한편, 하이브리드 시편의 경우 DED와 PBF 구간에서의 경도가 DED 샘플과 PBF 샘플에서 측정된 경도와 거의 동일하다. 하지만, PBF와 DED 적층부의 경계에서는 경도가 급격하게 상승하였다. 하이브리드 시편의 경우 PBF 적층 모재 위에 DED 적층 되었기 때문에 경계면 부근에 HAZ를 형성시킨다. 하이브리드 시편 제작 과정에서 3시간 정도의 DED 공정 동안 지속적인 입열에 의해 시편에 열 축적(Heat Accumulation)이 발생하고, 이로 인해 시효 효과(Aging)가 유발된 것으로 추측된다. 이러한 시효 효과는 용질 원자의 분리 및 침전을 발생시키기 때문에, 이로 인해 HAZ 부근에서 경도가 상승한 것으로 판단된다.
3.4 Wear Test
Fig. 9(a)는 마모 시험 후 각 시편의 PBF와 DED 영역에서 마모 폭을 측정한 결과를 나타내고 있다. HYBRID (Parallel)의 마모 폭은 PBF부와 DED부에서 각각 4.49 mm와 4.69 mm로 나타났고, HYBRID (Cross)의 경우 PBF와 DED에서 각각 4.52 mm와 4.68 mm로 나타났다. DED 적층부에서는 두 시편 모두 동일한 조건으로 적층되었기 때문에 마모 특성에 차이가 나타나지 않았고, PBF 영역에서도 방향에 따른 마모 손상의 차이가 나타나지 않았다. 반면에 PBF와 DED 적층부의 마모 폭을 비교했을 때 0.15-0.2 mm의 차이가 나타났다.
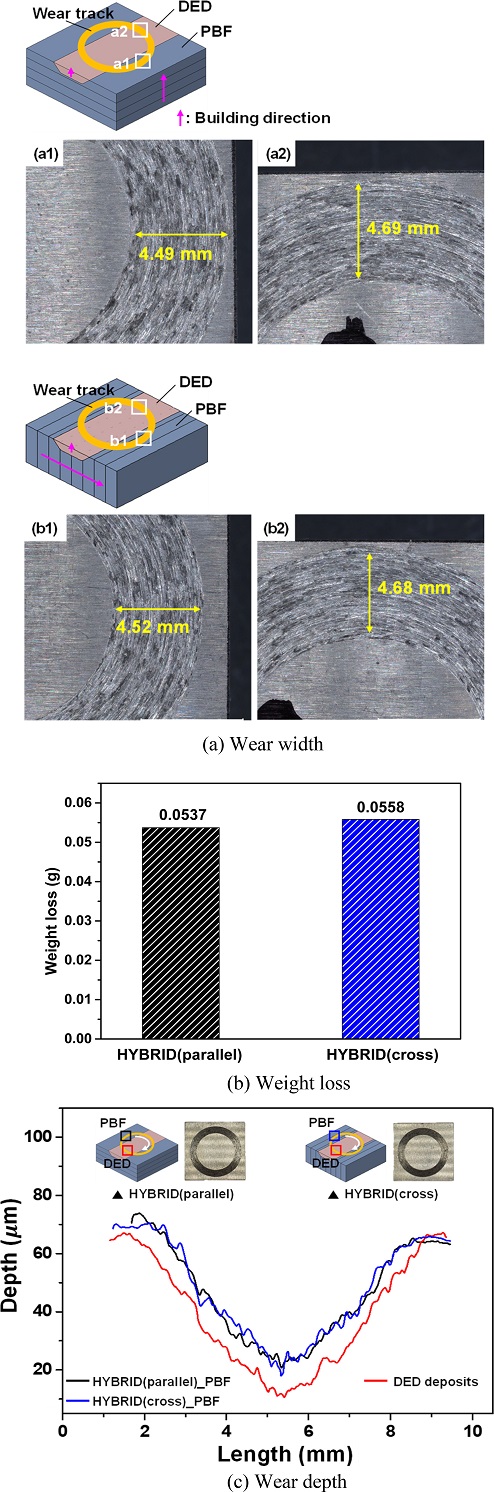
Wear width, weight loss and wear depth according to the building direction of hybrid sample after wear test
Fig. 9(b)는 마모 시험 후 감량을 측정한 결과를 나타내고 있으며, HYBRID (Parallel)와 HYBRID (Cross)의 감량은 각각 0.0537 g과 0.0558 g으로 나타났다. 마모 폭 결과와 마찬가지로 PBF 적층 모재의 표면에 따른 차이는 발생하지 않았다.
Fig. 9(c)는 마모 흔의 프로파일을 3차원 형상 측정기를 이용하여 측정한 결과를 나타내고 있다. 마모 깊이 또한 PBF 모재 방향에 따른 큰 차이는 나타나지 않았지만, PBF부와 DED부를 비교했을 때 약 10 μm의 차이가 발생했다. 위의 결과에서 모두 PBF 적층 모재의 방향에 따른 유의미한 차이는 발생하지 않았지만, PBF 적층부와 DED 적층부를 비교한다면 PBF 영역에서 마모 손상이 적게 나타났다. 이러한 차이는 앞서 설명한 미세조직과 미세경도의 결과와도 일치한다. PBF 적층부의 미세한 결정립 크기 그리고 DED 적층부 대비 낮은 오스테나이트 분율은 경도를 증가시켰고, 따라서 상대적으로 낮은 마모율로 이어졌다.
한편, 일반적으로 적층 제조된 시편의 마모 시험 시 적층 방향에 따른 이방성(Anisotropy)이 발생한다고 보고되고 있지만, 본 연구에서는 그러한 차이가 발생하지 않았다. 이는 본 연구에서 마모 시험 시, 높은 하중이 사용됐기 때문이다. Yang et al.은 SLM (Selective Laser Melting)으로 제작된 시편의 마모시험결과, 결정립 방향에 따라 낮은 하중에서는 이방성이 두드러지게 발생하지만[24], 높은 하중에서는 등방성(Isotropy)이 나타난다고 밝힌 것과 동일한 결과라고 볼 수 있다.
Fig. 10(a)는 각 샘플의 손상 표면을 나타내고 있다. 100 N의 높은 하중이 알루미나 볼에 의해 시편 표면에 반복적으로 가해졌기 때문에 심각한 마모가 나타났다. 하지만, PBF의 적층 표면에 따른 뚜렷한 차이는 발생하지 않았다. 하이브리드 샘플의 PBF 영역 표면에서는 슬라이딩 방향을 따라 연삭 마모(Abrasive Wear)와 산화막(Oxidized Layer)이 나타났다. 마모시험 중에 떨어진 미세한 파편(Fine Debris)이 표면을 긁어 얕고 미세한 스크래치를 형성시켰다. 또한, 알루미나 볼과 시편 간의 마찰에 의해 시편 표면의 온도 상승으로 인한 산화가 관찰되었다[25]. 모든 시편의 표면에서 산화층이 관찰되었으며, 이는 EDS 분석을 통해서도 확인할 수 있다.
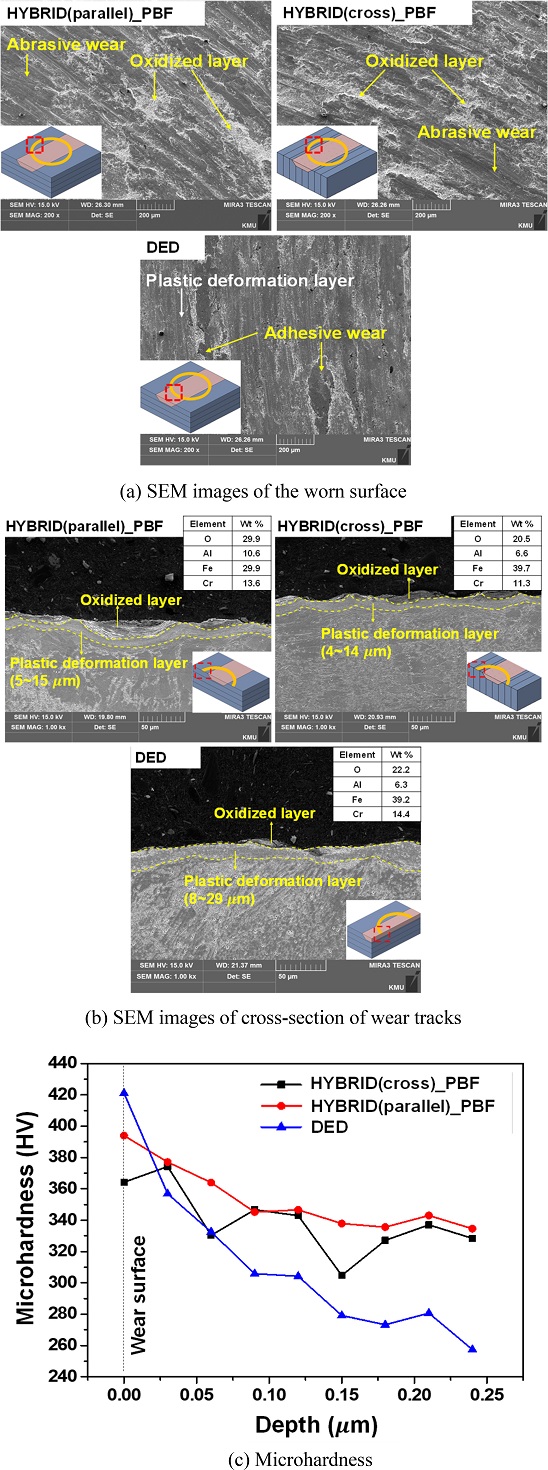
SEM images of the worn surface, SEM images of cross-section of wear tracks, and microhardness measurement of cross-section after wear test
반면, DED부의 손상 표면에는 주로 소성변형층(Plastic Deformation Layer)이 나타난 것을 알 수 있으며, 국부적으로 응착마모(Adhesive Wear)가 나타났다. DED부에서의 높은 잔류 오스테나이트 분율과 PBF 적층부 대비 낮은 경도는 내마모성을 저하시켜, 표면에서 큰 소성 변형을 유발했다고 판단된다. 또한 내마모성이 낮은 표면에서 떨어진 미세한 파편들이 볼의 회전 마찰로 인해 시편 표면에 응착마모를 발생시킨 것으로 파악된다.
Fig. 10(b)는 마모흔 단면에 대한 SEM 관찰 결과이다. 모든 시편에서 표면에 소성변형층이 형성된 것을 알 수 있다. 하지만 PBF 모재 방향에 따른 소성변형층 깊이에 차이가 거의 없지만, PBF부와 비교해서 DED 적층부의 소성변형층의 깊이가 다소 높게 나타났다. 이는 같은 하중 조건 하에서 DED 적층부의 가공경화능(Work Hardening Capacity)이 더 높은 것을 의미한다. 마모시험 후 시편 단면에서 깊이에 따른 경도를 측정했고, 그 결과를 Fig. 10(c)에 나타냈다. 적층 후 PBF부에 비해 낮은 경도를 보였던 DED부의 표면 경도가 마모시험 후에는 PBF부에 보다 증가한 것을 알 수 있다. 이로부터 DED 적층부의 높은 가공경화능을 확인할 수 있다.
이상에서와 같이, PBF부의 적층 방향에 따른 마모 거동에는 큰 차이가 없었으나, PBF와 DED 샘플의 주요 마모 메커니즘은 각각 산화 마모와 소성변형으로 서로 다른 결과를 확인할 수 있었다.
4. 결론
본 연구에서는 대표적 금속 AM 기술인 PBF와 DED 기술의 연속적인 공정으로 제작된 시편의 미세조직 및 상분석, 경도 그리고 마모 거동에 대해 연구하였다. PBF와 DED 공정에서의 용융풀 냉각 속도 차이에 의해 상이한 미세조직이 형성됐으며, PBF 샘플에서는 페라이트가 지배적으로 나타났고, 미세한 결정립이 형성되었다. DED 샘플에서는 래스 마르텐사이트와 잔류 오스테나이트가 지배적으로 나타났다. 한편, DED용 분말에는 오스테나이트 안정화 원소 함량이 PBF용 분말에서보다 높았기 때문에 잔류 오스테나이트 분율이 훨씬 높게 나타났다.
마모 거동에서는 PBF 모재의 적층 방향에 따른 이방성이 발생하지 않았다. 하지만 PBF의 미세한 조직과 낮은 분율의 잔류 오스테나이트는 경도를 상승시켰으며, 따라서 DED 적층부 대비 다소 높은 내마모성이 나타났다. PBF와 DED 샘플의 주요 마모 메커니즘은 각각 산화 마모와 소성변형으로 나타났으며, 마모 후에는 DED 적층부에서 높은 가공경화능을 확인할 수 있었다.
본 연구는 PBF와 DED 공정을 동시에 사용하는 하이브리드 AM에 대한 기초 연구로써, 두 이종 공정(PBF와 DED)의 연속공정으로 제작된 부품의 특성 연구에 초점을 맞추었다. 따라서, 두 이종 공정을 사용하여 기능성 부품을 제작하기 위한 부품 설계에 대한 기초 데이터를 제공한다. PBF, DED, 그리고 연속공정에 따라 분포되는 미세조직과 결정립이 다르게 나타났으며, 이에 의해 각 시편의 기계적 특성이 다르게 나타났다.
하지만 본 연구에서는 경도와 마모 거동에 대해서만 분석하였다. 따라서, 샘플 제작 방법에 따라 다양한 하중 조건에 대한 변형 특성을 비교해 보는 것도 흥미로운 연구 주제가 될 수 있다. 한편, 적층 제조된 샘플의 기계적 특성은 후 열처리에 의해서도 달라질 수 있다. 따라서 향후에는 열처리 조건에 따른 하이브리드 적층 샘플의 특성 변화에도 초점을 맞출 예정이다.
Acknowledgments
본 연구는 한국산업기술평가관리원(KEIT) 산업기술혁신사업(No. K-G012000875302)과 한국연구재단 개인기초연구사업(No. 2021R1A2C101197311)의 지원을 받아 수행되었음.
REFERENCES
- Sarvankar, S. G., Yewale, S. N., (2019), Additive manufacturing in automobile industry, International Journal of Research in Aeronautical and Mechanical Engineering, 7(4), 1-10.
-
Gisario, A., Kazarian, M., Martina, F., Mehrpouya, M., (2019), Metal additive manufacturing in the commercial aviation industry: A review, Journal of Manufacturing Systems, 53, 124-149.
[https://doi.org/10.1016/j.jmsy.2019.08.005]
-
Heinl, P., Müller, L., Körner, C., Singer, R. F., Müller, F. A., (2008), Cellular Ti–6Al–4V structures with interconnected macro porosity for bone implants fabricated by selective electron beam melting, Acta Biomaterialia, 4(5), 1536-1544.
[https://doi.org/10.1016/j.actbio.2008.03.013]
-
Sun, Y., Hebert, R. J., Aindow, M., (2020), Effect of laser scan length on the microstructure of additively manufactured 17-4PH stainless steel thin-walled parts, Additive Manufacturing, 35, 101302.
[https://doi.org/10.1016/j.addma.2020.101302]
-
Sridharan, N., Cakmak, E., Dehoff, R. R., (2019), Microstructure evolution during laser direct energy deposition of a novel Fe-Cr-Ni-WB hardfacing coating, Surface and Coatings Technology, 358, 362-370.
[https://doi.org/10.1016/j.surfcoat.2018.09.053]
-
Baek, G. Y., Shin, G. Y., Lee, E. M., Shim, D. S., Lee, K. Y., Yoon, H.-S., Kim, M. H., (2017), Mechanical characteristics of a tool steel layer deposited by using direct energy deposition, Metals and Materials International, 23(4), 770-777.
[https://doi.org/10.1007/s12540-017-6442-1]
-
Saboori, A., Aversa, A., Marchese, G., Biamino, S., Lombardi, M., Fino, P., (2019), Application of directed energy deposition-based additive manufacturing in repair, Applied Sciences, 9(16), 3316.
[https://doi.org/10.3390/app9163316]
-
Wilson, J. M., Piya, C., Shin, Y. C., Zhao, F., Ramani, K., (2014), Remanufacturing of turbine blades by laser direct deposition with its energy and environmental impact analysis, Journal of Cleaner Production, 80, 170-178.
[https://doi.org/10.1016/j.jclepro.2014.05.084]
-
Schneider, J., Seidel, A., Gumpinger, J., Riede, M., López, E., Brückner, F., Leyens, C., (2019), Advanced manufacturing approach via the combination of selective laser melting and laser metal deposition, Journal of Laser Applications, 31(2), 022317.
[https://doi.org/10.2351/1.5096123]
-
Kumaran, M., Senthilkumar, V., (2021), Experimental characterization of stainless steel 316L alloy fabricated with combined powder bed fusion and directed energy deposition, Welding in the World, 65(7), 1373-1388.
[https://doi.org/10.1007/s40194-021-01117-z]
-
Kumaran, M., Senthilkumar, V., Panicker, C. J., Shishir, R., (2021), Investigating the residual stress in additive manufacturing of combined process in powder bed fusion and directed energy deposition, Materials Today: Proceedings, 47, 4387-4390.
[https://doi.org/10.1016/j.matpr.2021.05.200]
-
Lashgari, H., Kong, C., Adabifiroozjaei, E., Li, S., (2020), Microstructure, post thermal treatment response, and tribological properties of 3D printed 17-4 PH stainless steel, Wear, 456, 203367.
[https://doi.org/10.1016/j.wear.2020.203367]
- Kumar, V. A., Gupta, R., Karthikeyan, M., Prasad, K. N., Sinha, P., Rao, M. N., (2007), Processing and characterization of thin sheets of 17-4PH stainless steel for aerospace application, Proceedings of the International Conference on Advanced Materials & Composites, 1-5.
-
Ping, L., Cai, Q.-Z., Wei, B.-K., Zhang, X.-Z., (2006), Effect of aging temperature on erosion-corrosion behavior of 17-4PH stainless steels in dilute sulphuric acid slurry, Journal of Iron and Steel Research, International, 13(5), 73-78.
[https://doi.org/10.1016/S1006-706X(06)60099-X]
-
Choi, S.-H., Kim, C.-S., Jhang, K.-Y., Shin, W.-S., (2011), Influence of surface roughness on morphology of aluminum alloy after pulsed-laser irradiation, Transactions of the Korean Society of Mechanical Engineers A, 35(9), 1105-1111.
[https://doi.org/10.3795/KSME-A.2011.35.9.1105]
-
Ansari, M., Mohamadizadeh, A., Huang, Y., Paserin, V., Toyserkani, E., (2019), Laser directed energy deposition of water-atomized iron powder: Process optimization and microstructure of single-tracks, Optics & Laser Technology, 112, 485-493.
[https://doi.org/10.1016/j.optlastec.2018.11.054]
-
Cheruvathur, S., Lass, E. A., Campbell, C. E., (2016), Additive manufacturing of 17-4 PH stainless steel: Post-processing heat treatment to achieve uniform reproducible microstructure, JOM, 68(3), 930-942.
[https://doi.org/10.1007/s11837-015-1754-4]
-
Gu, D. D., Meiners, W., Wissenbach, K., Poprawe, R., (2012), Laser additive manufacturing of metallic components: materials, processes and mechanisms, International Materials Reviews, 57(3), 133-164.
[https://doi.org/10.1179/1743280411Y.0000000014]
-
Ian Gibson, I. G., (2015), Additive manufacturing technologies 3D printing, rapid prototyping, and direct digital manufacturing, Springer.
[https://doi.org/10.1007/978-1-4939-2113-3]
-
Sun, Y., Hebert, R. J., Aindow, M., (2018), Effect of heat treatments on microstructural evolution of additively manufactured and wrought 17-4PH stainless steel, Materials & Design, 156, 429-440.
[https://doi.org/10.1016/j.matdes.2018.07.015]
-
LeBrun, T., Nakamoto, T., Horikawa, K., Kobayashi, H., (2015), Effect of retained austenite on subsequent thermal processing and resultant mechanical properties of selective laser melted 17–4 PH stainless steel, Materials & Design, 81, 44-53.
[https://doi.org/10.1016/j.matdes.2015.05.026]
-
Gu, H., Gong, H., Pal, D., Rafi, K., Starr, T., Stucker, B., (2013), Influences of energy density on porosity and microstructure of selective laser melted 17-4PH stainless steel, Proceedings of the 2013 International Solid Freeform Fabrication Symposium, 1-16.
[https://doi.org/10.26153/tsw/15572]
- Dieter, G. E., Bacon, D., (1976). Mechanical Metallurgy, McGraw-hill.
-
Yang, Y., Zhu, Y., Khonsari, M., Yang, H., (2019), Wear anisotropy of selective laser melted 316L stainless steel, Wear, 428, 376-386.
[https://doi.org/10.1016/j.wear.2019.04.001]
-
Dwivedi, D. K., (2010), Adhesive wear behaviour of cast aluminium–silicon alloys: Overview, Materials & Design (1980-2015), 31(5), 2517-2531.
[https://doi.org/10.1016/j.matdes.2009.11.038]
Master candidate in Department of Ocean Advanced Materials Convergence Engineering, Korea Maritime and Ocean University. His research interest is metal additive manufacturing.
E-mail: taegun0902@naver.com
Senior Researcher in Automotive Materials & Components Group at Korea Institute of Industrial Technology. His research field is engineering for additive manufacturing, especially directed energy deposition (DED).
E-mail: shin2007@kitech.re.kr
Principal Researcher in Automotive Materials & Components Group at Korea Institute of Industrial Technology. His research field is engineering for additive manufacturing, especially directed energy deposition (DED).
E-mail: kylee@kitech.re.kr
Associate Professor in Department of Ocean Advanced Materials Convergence Engineering, Korea Maritime and Ocean University. His research interests include incremental and roll forming for sheet metal, direct energy deposition (DED) and structural analysis as well as optimal design.
E-mail: think@kmou.ac.kr