
표면 코팅을 통한 소다라임 유리의 가공성 향상
Copyright © The Korean Society for Precision Engineering
This is an Open-Access article distributed under the terms of the Creative Commons Attribution Non-Commercial License (http://creativecommons.org/licenses/by-nc/3.0) which permits unrestricted non-commercial use, distribution, and reproduction in any medium, provided the original work is properly cited.
Abstract
Advanced engineering ceramics have been highlighted mainly owing to their superior hardness, corrosion/wear resistance, and thermal insulation performances. However, they are usually very difficult-to-cut because of their high brittleness. In light of this, ultra-precision machining has been studied to perform ductile-regime cutting in the machining of ceramics. Ductile-regime cutting can feature a smoother surface, and lower subsurface damage as the dominant material response during cutting showed ductile behavior. Researchers have investigated promoting ductile-regime cutting to improve the machinability of ceramics. In this study, various coating materials were applied to the workpiece surface, and their effects on machinability improvements were explored. A total of 6 surface coatings and lubricants were applied to soda-lime glass. The critical depth of cut (CDC), the depth where the ductile-brittle transition (DBT) occurred, was increased in all coatings and lubricants, with an improved ductile cutting regime. Experimental results showed that solid coatings were more effective than liquid lubricants in enhancing the ductile cutting regime. It was thought that solid coatings induced an additional downward force by resisting material deformation and chip evacuation, thus contributing to suppression of crack opening. It is expected that this research can contribute to the machinability improvements of brittle materials.
Keywords:
Soda-lime glass, Ductile-brittle transition, Ultra-precision machining, Coating, Lubricant키워드:
소다라임 유리, 연성-취성 전이, 초정밀가공, 코팅, 윤활제1. 서론
공학 세라믹 재료는 높은 내열성, 내마모성, 내부식성, 경도 등의 장점으로 첨단 재료로서 주목받아 왔다. 재료의 우수한 기계적 물성 및 안전성으로 자동차 스파크 플러그, 절연재, 절삭공구, 항공우주 부품의 피복 등 다양한 산업 분야에서 활용되고 있다[1].
그러나 이처럼 다양한 장점과 넓은 활용 분야를 가졌음에도, 세라믹은 가공이 어려운 소재로 간주된다. 특히 취성이 매우 높아 수 μm 이하의 절삭 깊이에서도 균열(Cracks)이 크게 발생하여 일반적인 기계가공 수행에 어려움이 있다.
한편 세라믹 가공 시 여러 가공조건에 따라 재료가 연성 거동을 보이기도 한다[2-5]. Fig. 1은 1 μm 이하 깊이 범위에서 초정밀가공을 수행할 때 절삭 깊이에 따라 재료 거동이 연성 영역(Ductile Region)과 취성 영역(Brittle Region)으로 나뉜 사례를 보여준다. 연성 영역 가공(Ductile Cutting Regime)에서는 재료가 연성 파괴(Ductile Fracture)에 의해 제거되는 것으로 사료되며, 일반적인 취성 영역 가공보다 우수한 표면 품질, 높은 구조적 정밀성, 낮은 표면 손상 등 여러 장점을 갖는다[6]. 또한 취성 영역 가공에서는 균열 발생에 의한 진동 등 절삭 공구에 가해지는 부하가 증가하므로[7], 공구 수명의 관점에서도 연성 영역 가공이 유리하다.
이에 보다 다양한 가공 조건에서 연성 가공을 수행하고자 여러 연구가 진행되었으며, 국소 가공 면적을 가열하는 레이저 보조 가공[8,9], 공구에 미세한 진동을 가해 가공성을 향상하는 초음파 보조 가공[10-12], 아크 방전을 이용하는 방전 가공[13,14] 등이 활용되었다.
한편으로는 위와 같이 추가적인 가공 장비를 요구하는 방법과는 다르게 피삭재에 코팅(Coating)을 적용해 연성 영역 가공이 일어나는 절삭 깊이를 증가시켜 가공성을 향상하고자 하는 연구가 이루어진 바 있다[7,15,16]. 피삭재 코팅은 고가의 추가 장비 없이 쉽게 적용할 수 있다는 장점이 있으며 코팅이 세라믹 재료 가공성에 미치는 영향을 분석하고자 여러 시도가 이루어지고 있다.
연구에 따라 코팅의 역할은 다양하게 분석되며, 표면 코팅에 관한 한 연구[15]에서는 고체 코팅이 세라믹 표면에 추가적인 압축력을 가함으로써 연성 가공 영역이 확대됨을 관찰하였다. 단결정 실리콘에 왁스 코팅을 적용한 연구[16]에서는 왁스의 윤활 효과와 칩 브레이커(Chip Breaker)로서의 역할이 연성 영역 가공 확대에 기여하는 바를 분석하였다. 단결정 사파이어에 대한 선행 연구[7]는 다양한 코팅재료가 갖는 역할을 절삭력과 추력 관점에서 분석하였다.
이에 본 연구에서는 특히 다양한 물성을 갖는 코팅 재료의 가공성 향상 효과를 알아보고자 총 6종류의 코팅을 선정, 세라믹 가공에 적용하고 그 영향을 분석하였다. 코팅 재료 및 코팅 방법은 일반적으로 구하기 쉬운 코팅 재료와 적용하기 쉬운 코팅 공정을 선정함으로써 경제적인 가공성 향상 방법을 연구하고자 하였다. 피삭재로는 건물의 창문, 자동차 전면 유리, 유리병 등 널리 사용되는 세라믹 재료 중 하나인 소다라임 유리(Soda Lime Glass)를 선정하였다. 결정 방향에 따라 성질이 달라지는 사파이어와 달리, 소다라임 유리의 경우 비정질(Amorphous) 재료이다. 또한 사파이어에서의 선행 연구[7]는 절삭력의 관점에서 가공 결과 분석이 이루어진 반면, 본 연구에서는 코팅의 물성, 특히 경도와 마찰계수 관점에서 결과를 분석하고자 하였다.
소다라임 유리의 가공성에 영향을 주는 요인으로 표면 코팅이 절삭력/추력에 미치는 영향, 마찰계수 변화에 따른 윤활 변화 등이 고려되었다. 따라서 표면 코팅의 경도가 높을수록 소재에 가해지는 압축력을 증가시켜 연성 가공 영역 확대에 기여할 것이라는 가설을 세우고, 이를 검증하기 위하여 실험을 수행했다. 한편으로는 마이크로 그라인딩 연구[17]를 참조하여 마찰계수가 낮을 수록 연성 가공 영역이 확대될 것으로 추정하였다.
이에 여러 코팅 재료의 마찰계수와 Berkovich 경도를 측정하고 연성 가공 영역 향상 효과와 비교하였다. 마찰계수는 미끄럼 실험을 통해, 경도는 나노인덴테이션 실험을 통해 측정하였다. 그 후 선행 연구[18]와 유사하게 초정밀가공을 수행하고 연성가공 영역의 깊이 한계를 측정하여 비교하였다.
실험 결과 특히 고체 코팅이 연성 영역 가공이 가능한 절삭 깊이 향상에 효과적이었다. 연구를 통해 다양한 코팅이 소다라임 유리 가공성 향상에 미치는 효과를 확인하였으며, 메커니즘에 대한 분석 및 이해를 통해 연성 영역 가공 향상에 기여할 것을 기대한다.
2. 실험 상세
2.1 코팅 및 코팅의 물성치 측정
코팅 재료로 쉽게 구할 수 있는 액체 코팅 2종과 고체 코팅4종을 선정하였다. 액체 코팅으로는 서로 다른 마찰계수를 갖는 세제(1 : 1 비율 수용액)와 초정밀 가공에 사용되는 절삭유(Zubora 77 S Ultra, Zeller+Gmelin Co., Germany)를 선정하였다. 고체 코팅으로는 다양한 경도를 시험해 볼 수 있도록 왁스(Shiftwax 7607, Nikka Seiko Co. Ltd., Japan), 고무코팅제(K-980, Nabakem, Korea), 서로 다른 경화제(Curing Agent): 주제(Base Agent) 비율(5 : 1, 9 : 1)을 갖는 PDMS (Sylgard 184, Dow Silicones Co., USA) 2종을 선정하였다. 액체 코팅은 마이크로피펫을 이용하여 피삭재에 도포 하였으며, 왁스와 PDMS는 Flow Coating 공정[19]을 응용하여 코팅재를 피삭재에 부은 후 피삭재를 수직으로 1시간 이상 세워놓는 방법으로 도포하였다.
고무코팅제는 스프레이 형태의 제품을 사용하였고 Hydrographic Printing 공정[20]을 이용, 물에 도포한 후 피삭재로 떠내는 방법으로 코팅하였다.
Fig. 2에 코팅된 표면을 나타내었다. 관찰 결과 고체 코팅이 고르게 잘 도포된 것을 확인할 수 있다. PDMS 2종의 경우 약 30 μm의 두께를 보였으며, 왁스 코팅이 약 10 μm의 두께를 보였다. 고무코팅제의 경우 측정 장비 분해능의 한계(10 μm)로 단순히 10 μm 이하의 두께를 갖는 것으로 추정하였다. 각 코팅의 두께는 코팅 위의 임의의 위치에서 10회 측정하였으며 측정 간 큰 편차가 존재하지 않았다.
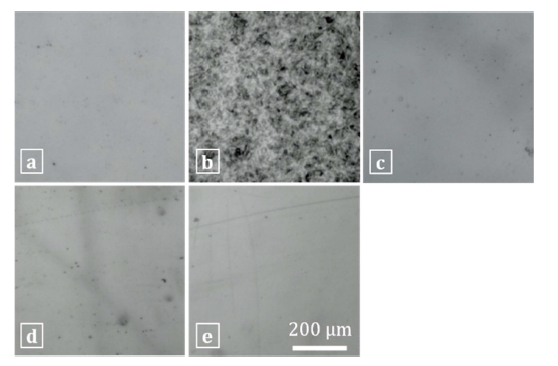
Optical images of the coatings (a. original, b. wax, c. Rubber spray, d. PDMS (5 : 1), e. PDMS (9 : 1))
코팅 간 상대적 마찰계수 비교를 위해 15 × 15 mm 크기의 코팅을 적용한 피삭재를 금속판에 고정된 평평한 사파이어 웨이퍼(2 Monocrystalline Sapphire Wafer (C-plane), Hansol Technics Co., Ltd., Korea) 위에 놓고, 점진적으로 웨이퍼를 기울이며 처음 미끄러짐이 발생한 각도를 측정하였다(Fig. 3). 코팅의 마찰을 제외한 다른 마찰을 최소화하기 위해 Ra 값이 0.019 μm 인 표면이 평탄한 사파이어 웨이퍼를 사용하였다. 마찰계수의 변환식은 식(1)과 같으며, 10회 측정 후 평균값을 사용하였다. 그 후 나노인덴테이션 실험(UNHT3, Anton Paar, Austria)을 통해 Berkovich 경도를 측정하였다. 매 측정은 3 μm min-1의 속도로 0.7-10 μm 깊이를 압입하여 5회 측정 후 평균값을 사용하였다.
(1) |
2.2 실험 제원 및 방법
초정밀 직교 절삭을 위해 3축 모터(L-509.1ASD00, PI GmbH & Co. KG, Germany)와 제어기(SMC Hydra CM & C-663.12, PI GmbH & Co. KG, Germany)로 구성한 가공 시스템을 사용하였다(Fig. 4).
실험에 사용된 모터의 최소 이송분해능은 0.02 μm이며, 단방향 이송정밀도(Unidirectional Repeatability)는 0.1 μm이다. 절삭공구는 인선 반경(Nose Radius) 500 μm의 다이아몬드 공구(Sinjin Diamond Industrial Corp., Korea)를 사용하였다. 피삭재로는 15 × 15 mm 크기로 절단된 소다라임 유리(DSA2-3748, Erie Scientific Corporation, USA)를 사용하였으며 왁스를 사용해 가공 시스템에 고정하였다. 고정된 피삭재의 기울기를 다이얼 게이지(543-561k, Mitutoyo, Japan)로 측정하여 10 × 10mm 면적 내에서 유리 표면이 1 μm 이하의 높이 차이를 갖도록 조정하였다.
기울기 조정을 완료한 후, 가공 시스템에서 유리 표면 높이를 특정하도록 광학현미경을 통해 공구를 관측하였다. 절삭 가공은 속도 5 mm min-1, 기울기 1/500으로 진행되었고, 최대 절삭 깊이는 1 μm로 선정하였다(Fig. 5). 고체 코팅의 경우 피삭재 표면이 드러나지 않기 때문에 가공 시작 전 코팅 일부를 벗겨내고 코팅이 없는 부분에서 유리의 높이를 특정한 후 코팅 위에서 가공을 수행하였다. 액체 코팅의 경우 매 절삭 시 에탄올로 피삭재를 세척하여 이전 실험의 코팅을 제거하였다. 동일 실험 조건에서 절삭 실험을 4회 반복하였으며 절삭 형상을 관찰하여 계획한 바와 같이 절삭이 정확하게 수행되었음을 확인하였다.
3. 실험 결과
3.1 가공 실험 결과
본 연구에서 가공성 향상의 결과로 연성 가공 영역의 한계 깊이 증가를 관찰하고자 하였다. 이에 연성 가공 영역과 취성 가공 영역의 구분점이 되는 지점의 가공 깊이인 임계절삭깊이(Critical Depth of Cut, CDC) [21]를 측정 및 비교하였다.
임계절삭깊이는 균열이 발생하기 시작한 점의 절삭 폭으로부터 식(2)를 이용해 계산하였다. Fig. 6에 임계절삭깊이의 개념과 각 코팅을 사용했을 때의 가공 결과 예시 사진을 함께 나타내었다.
(2) |
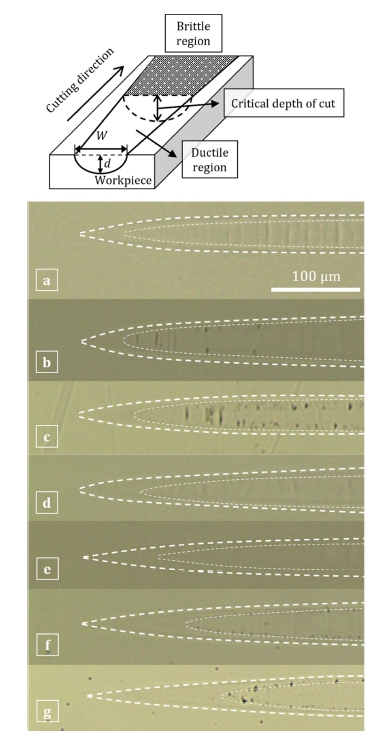
Schematic and optical images of the cutting experiment (a. original (without any coating), b. cutting fluid, c. detergent, d. rubber spray, e. wax, f. PDMS (5 : 1), g. PDMS (9 : 1))
절삭 깊이가 변화함에 따라 가공 중 주재료 거동이 연성 영역에서 취성 영역으로 전이되는 것을 관찰할 수 있으며 임계절삭깊이는 각 코팅 별로 값이 상이하였다.
아무런 코팅이 적용되지 않은 일반 소다라임 유리(Original)와 코팅 및 윤활 조건이 적용된 소다라임 유리의 임계절삭깊이 측정 결과를 Fig. 7에 비교하였으며, 다른 절삭공정의 절삭깊이[14]와 직접 비교는 어렵지만 모든 코팅에서 임계절삭깊이가 증가하여 가공성이 크게 향상됨을 확인할 수 있다. 일반적으로 액체 코팅(세제, 절삭유)에 비해 고체 코팅(왁스, 고무코팅제, PDMS (5 : 1), PDMS (9 : 1))에서 우수한 임계절삭깊이 증가를 관측하였다.
윤활제 중 절삭유가 약 0.101 μm의 임계절삭깊이로 가장 낮은 임계절삭깊이 증가를 보여주었으며, 뒤이어 세제가 보다 높은 임계절삭깊이 증가를 보여주었다. 고체 코팅 중에서는 고무 코팅제가 0.158 μm의 임계절삭깊이로 가장 낮은 임계절삭깊이 증가를 보여주었으며 그 후 왁스, PDMS (5 : 1), PDMS (9 : 1) 순으로 높은 임계절삭깊이의 증가를 보인다.
3.2 코팅 물성치 측정 결과 및 임계절삭깊이 비교 분석
Fig. 8에 코팅 6종과 일반 소다라임 유리의 마찰계수의 측정 결과를 정리하였다. 소다라임 유리의 마찰계수 0.22에 비해 액체 코팅은 0.1 이하의 낮은 마찰계수를 보여주었다. 고체 코팅은 일반 소다라임 유리에 비해 높은 마찰계수를 보여주었다.
Berkovich 경도의 경우 PDMS 2종에 비해 왁스와 고무코팅제가 100배 이상 높은 값을 갖는다(Fig. 9). 경도 및 마찰계수 측정 결과는 의도하였던 대로 각 코팅들이 서로 상이한 물성을 가짐을 보여준다.
경도 및 마찰계수에 따른 임계절삭깊이를 각각 Figs. 10과 11에 나타내었다. 경도의 경우 임계절삭깊이 향상에 미치는 영향이 뚜렷하지 않았는데(Fig. 10), PDMS (5 : 1)과 PDMS (9 : 1)의 경우 왁스나 고무코팅제 대비 상당히 적은 경도값을 가졌으나 임계절삭깊이 향상 효과는 왁스와 고무코팅제와 비슷하였다.
마찰계수의 경우(Fig. 11) 마찰계수가 작은 절삭유에서 가장 작은 임계절삭깊이 증가 효과가 관측되었다. 단결정 재료에 코팅을 적용했던 다른 연구 사례[11]와 다르게 큰 마찰계수를 갖는 고체 코팅들이 액체 코팅 대비 큰 임계절삭깊이 향상 효과를 보여주었다.
실험 결과, 특히 고체 코팅이 가공 중 재료에 가하는 압축력이 균열 억제에 효과적이었던 것으로 생각된다. 소다라임 글래스의 압입 실험에서 균열은 내면 결함(Subsurface Defects)에 인장 응력이 가해져 발생(Crack Opening)하는 것으로 알려졌으며[22], 재료에 정수압을 가함으로써 가공 중 균열 전파를 억제한 연구 사례가 있다[23]. 이 실험에서는 고체 코팅이 특히 재료 변형에 저항하며 추가적인 압축력을 재료에 수직 방향으로 가함으로써 임계절삭깊이를 향상한 것으로 사료된다.
또한 고체 코팅은 칩 배출을 방해하는 효과가 있을 것으로 사료된다. 가공 방향을 따라 공구가 이송되면, 절삭이 이루어지며 칩이 형성된다(Fig. 12). 가공 중 사진을 보면 코팅과 유리 재료가 구분되지 않고 하나의 칩으로서 배출되는 것을 확인할 수 있으며, 코팅과 유리가 가공 중 박리되지 않고 코팅이 유지되며 가공에 영향을 미쳤음을 확인할 수 있다. 이 때 고체 코팅은 아무런 코팅이 없는 경우 대비 재료의 칩 배출을 방해하며 수직 방향으로 추력을 증가시켰을 것으로 사료된다.
실험 결과에서 PDMS 코팅이 경도가 매우 낮은 유연 재질임에도 불구하고 훨씬 경도가 높은 왁스나 고무 코팅제와 유사한 임계절삭깊이 향상 효과가 있는 것으로부터 코팅이 단순 변형 저항 효과뿐 아니라 마찰계수의 영향 등 추가적인 공정 간섭을 통해 연성 영역 가공을 증가시킴을 유추해 볼 수 있다.
다만 실험 결과가 액체 코팅류의 마찰계수가 낮을수록 임계 절삭깊이 향상 효과가 클 것이라던 가설과는 상이한데 원인을 분석하기 위해서는 절삭력 측정 및 정교한 시뮬레이션을 통해 추가 연구가 필요하다. 단결정 사파이어 가공에서 결정 방향(Crystal Orientation)에 따른 코팅의 효과를 분석한 선행 연구[8]에 의하면, 코팅이 절삭력(Cutting Force, Fc)과 추력(Thrust Force, Ft)에 다양하게 영향을 미치며 비정질 소다라임 유리의 피삭재 특성 또한 연성 영역 가공 특성과 균열 발생에 영향이 있었으리라 사료된다.
실험 결과는 코팅이 연성 가공 영역 확대에 크게 기여할 수 있음을 보여준다. 아무런 코팅이 없었을 때와 비교하면 가장 효과적인 PDMS (9 : 1) 코팅의 경우 3배 이상의 임계절삭깊이를 보여주었다. 다만 코팅의 임계절삭깊이 향상 효과가 재료별로 상이하고 마찰계수의 영향 등에 대해서는 추가 연구가 필요하다. 여러 가지 가공 조건에서 코팅이 절삭 시 응력 분포에 미치는 영향을 분석한다면 상황에 맞는 코팅 선정에 기여할 수 있을 것으로 생각한다. 지속적인 연구를 통해 임계절삭깊이 향상 효과를 증가시켜 나가고자 하며, 이 연구가 소다라임 유리의 가공성 향상과 활용분야 확대에 기여할 것으로 기대한다.
4. 결론
본 연구에서는 소다라임 유리의 초정밀가공에서 피삭재에 적용된 코팅이 연성 가공 영역 확장에 미치는 영향을 알아보았다. 특히 코팅의 물성에 따른 임계절삭깊이 증가를 관측하였다.
모든 코팅에서 임계절삭깊이 증가를 관측하였으나, 고체 코팅에 비해 액체 코팅의 임계절삭깊이 증가는 미미했다. PDMS 2종과 다른 2종의 코팅(왁스, 고무코팅제)의 경도가 100배 이상으로 큰 차이가 있었으나 가공 결과 분석에서 임계절삭깊이는 고무코팅제 기준 약 2배, 왁스와는 유사한 결과를 보였다.
실험 결과로부터 고체 코팅의 재료 변형 저항과 칩 배출 저항이 임계절삭깊이 향상에 기여하는 것으로 추정하였다. 코팅 재료의 물성치와 임계절삭깊이 향상 효과 간 뚜렷한 경향성은 확인되지 않았으나, 기존 논문과는 다르게 여러 종류의 코팅을 비교하였을 경우 높은 마찰계수를 가진 코팅이 큰 임계절삭깊이 향상 효과를 보여주기도 하였다. 향후 절삭력 측정을 통해 정량적 분석을 수행할 예정이며 이 연구가 소다라임 유리의 가공성 향상에 기여할 것으로 기대한다.
NOMENCLATURE
μ : | Friction Coefficient |
θ : | The Angle where the First Slip Occurred |
d : | Depth of Cut |
r : | Tool Nose Radius |
W : | Cutting Width |
Acknowledgments
이 연구는 2022년도 정부(과학기술정보통신부, 교육부)의 재원으로 한국연구재단의 지원을 받아 수행되었으며(Nos. NRF-2022R1F1A1063896 and 5199990714521), 이에 감사드립니다.
REFERENCES
- Kalpakjian, S., (1984). Manufacturing processes for engineering materials. Pearson.
-
Young, H., Liao, H.-T., Huang, H.-Y., (2007), Novel method to investigate the critical depth of cut of ground silicon wafer, Journal of Materials Processing Technology, 182(1-3), 157-162.
[https://doi.org/10.1016/j.jmatprotec.2006.07.025]
-
Liu, K., Li, X., Liang, S. Y., Liu, X. D., (2005), Nanometer-scale, ductile-mode cutting of soda-lime glass, Journal of Manufacturing Processes, 7(2), 95-101.
[https://doi.org/10.1016/S1526-6125(05)70086-4]
-
Yan, B., Wang, A., Huang, C., Huang, F., (2002), Study of precision micro-holes in borosilicate glass using micro EDM combined with micro ultrasonic vibration machining, International Journal of Machine Tools and Manufacture, 42(10), 1105-1112.
[https://doi.org/10.1016/S0890-6955(02)00061-5]
-
Liu, Y., Tong, H., Liu, G., Li, Y., Tan, Q., (2023), Cutting model considering damage layer thickness for ultra-precision turning of quartz glass, The International Journal of Advanced Manufacturing Technology, 126(9), 4087-4100.
[https://doi.org/10.1007/s00170-023-11366-5]
-
Antwi, E. K., Liu, K., Wang, H., (2018), A review on ductile mode cutting of brittle materials, Frontiers of Mechanical Engineering, 13(2), 251-263.
[https://doi.org/10.1007/s11465-018-0504-z]
-
Yoon, H.-S., Kwon, S. B., Kim, J.-H., Ahn, S.-H., Min, S., (2022), Effects of surface coating materials on cutting forces and ductile-to-brittle transition in orthogonal cutting of monocrystalline sapphire, Journal of Manufacturing Processes, 84, 375-382.
[https://doi.org/10.1016/j.jmapro.2022.09.046]
-
Chang, C.-W., Kuo, C.-P., (2007), An investigation of laser-assisted machining of Al2O3 ceramics planning, International Journal of Machine Tools and Manufacture, 47(3-4), 452-461.
[https://doi.org/10.1016/j.ijmachtools.2006.06.010]
-
Ito, Y., Ueki, M., Kizaki, T., Sugita, N., Mitsuishi, M., (2017), Precision cutting of glass by laser-assisted machining, Procedia Manufacturing, 7, 240-245.
[https://doi.org/10.1016/j.promfg.2016.12.058]
-
Lee, T., Zhang, J., Lau, W., (1998), Machining of engineering ceramics by ultrasonic vibration assisted EDM method, Material and Manufacturing Process, 13(1), 133-146.
[https://doi.org/10.1080/10426919808935224]
-
Yang, Z., Zhu, L., Zhang, G., Ni, C., Lin, B., (2020), Review of ultrasonic vibration-assisted machining in advanced materials, International Journal of Machine Tools and Manufacture, 156, 103594.
[https://doi.org/10.1016/j.ijmachtools.2020.103594]
-
Zhou, M., Wang, X., Ngoi, B., Gan, J., (2002), Brittle–ductile transition in the diamond cutting of glasses with the aid of ultrasonic vibration, Journal of Materials Processing Technology, 121(2-3), 243-251.
[https://doi.org/10.1016/S0924-0136(01)01262-6]
-
Puertas, I., Luis, C., (2004), A study on the electrical discharge machining of conductive ceramics, Journal of Materials Processing Technology, 153-154, 1033-1038.
[https://doi.org/10.1016/j.jmatprotec.2004.04.197]
- Doan, C. X., Kim, B.-H., Chung, D.-K., Chu, C.-N., (2011), Fabrication of PCD micro tool and its hybrid micro machining, Journal of the Korean Society for Precision Engineering, 28(6), 694-700.
-
Lee, Y. J., Chong, J. Y., Chaudhari, A., Wang, H., (2020), Enhancing ductile-mode cutting of calcium fluoride single crystals with solidified coating, International Journal of Precision Engineering and Manufacturing-Green Technology, 7, 1019-1029.
[https://doi.org/10.1007/s40684-019-00126-0]
-
Ameli Kalkhoran, S. N., Vahdati, M., Zhang, Z., Yan, J., (2021), Influence of wax lubrication on cutting performance of single-crystal silicon in ultraprecision microgrooving, International Journal of Precision Engineering and Manufacturing-Green Technology, 8(2), 611-624.
[https://doi.org/10.1007/s40684-020-00198-3]
-
Yang, M., Li, C., Zhang, Y., Jia, D., Zhang, X., Hou, Y., Li, R., Wang, J., (2017), Maximum undeformed equivalent chip thickness for ductile-brittle transition of zirconia ceramics under different lubrication conditions, International Journal of Machine Tools and Manufacture, 122, 55-65.
[https://doi.org/10.1016/j.ijmachtools.2017.06.003]
-
Yoon, H.-S., Kwon, S. B., Nagaraj, A., Lee, S., Min, S., (2018), Study of stress intensity factor on the anisotropic machining behavior of single crystal sapphire, CIRP Annals, 67(1), 125-128.
[https://doi.org/10.1016/j.cirp.2018.04.114]
-
Stafford, C. M., Roskov, K. E., Epps, T. H., Fasolka, M. J., (2006), Generating thickness gradients of thin polymer films via flow coating, Review of Scientific Instruments, 77(2), 023908.
[https://doi.org/10.1063/1.2173072]
- Yook, K. S., (2019), Hydrographic printing of polymer light-emitting diodes, KIC News, 22(3), 6-10. https://www.cheric.org/PDF/PIC/PC22/PC22-3-0006.pdf
-
Wang, M., Wang, W., Lu, Z., (2013), Critical cutting thickness in ultra-precision machining of single crystal silicon, The International Journal of Advanced Manufacturing Technology, 65(5-8), 843-851.
[https://doi.org/10.1007/s00170-012-4222-0]
-
Lawn, B. R., Dabbs, T., Fairbanks, C. J., (1983), Kinetics of shear-activated indentation crack initiation in soda-lime glass, Journal of Materials Science, 18(9), 2785-2797.
[https://doi.org/10.1007/BF00547596]
-
Yoshino, M., Ogawa, Y., Aravindan, S., (2005), Machining of hard-brittle materials by a single point tool under external hydrostatic pressure, Journal of Manufacturing Science and Engineering, 127(4), 837-845.
[https://doi.org/10.1115/1.2035695]
He is a M.S. candidate in the School of Aerospace and Mechanical Engineering and Department of Smart Air Mobility, Korea Aerospace University. His research interest is ultra-precision machining.
E-mail: jhkim96@kau.kr
He is a B.Sc. in the Department of Aerospace and Mechanical Engineering, Korea Aerospace University. His research interest is ultra-precision engineering.
E-mail: sg1559@naver.com
He is a Postdoctoral researcher in the Department of Mechanical Engineering, University of Wisconsin-Madison, USA. His research interest is ultra-precision machining and modeling ductile-brittle transition.
E-mail: kwon47@wisc.edu
He is an Associate Professor in the Department of Mechanical Engineering, University of Wisconsin-Madison, USA. His research expertise are conventional and non-conventional machining processes, manufacturing strategies, and ultra-precision nano-machining.
E-mail: sangkee.min@wisc.edu
He is an Associate Professor in the School of Aerospace and Mechanical Engineering and Department of Smart Air Mobility, Korea Aerospace University. His research interests are in smart/hybrid manufacturing, sustainable manufacturing, ultra-precision machining, micro/nano fabrication, 3D/4D printing, smart materials, and manufacturing for design.
E-mail: hsyoon7@kau.ac.kr