
듀얼 모터와 단일 유성기어 기반 40 kW급 전기트랙터 시뮬레이션 모델 개발
Copyright © The Korean Society for Precision Engineering
This is an Open-Access article distributed under the terms of the Creative Commons Attribution Non-Commercial License (http://creativecommons.org/licenses/by-nc/3.0) which permits unrestricted non-commercial use, distribution, and reproduction in any medium, provided the original work is properly cited.
Abstract
The purpose of this paper was to develop a simulation model for a 40 kW electric tractor using a powertrain based on dual motors and a planetary gear. To select motor capacity and reduction gear ratio based on the power flow for agricultural work, load data for various gear conditions were acquired and analyzed using a 42 kW engine tractor of similar capacity. Modeling was conducted using MATLAB/Simulink/Simscape. Load data acquired through actual field tests were applied as load conditions for the simulation. Simulation results confirmed that the power was transmitted through the planetary gear as the clutch and brake operated according to the work mode. The developed simulation model is expected to be used for electric tractor development.
Keywords:
Electric tractor, Planetary gear, Dual motor, Simulation model키워드:
전기트랙터, 유성기어, 듀얼 모터, 시뮬레이션 모델1. 서론
최근 화석연료 사용 증가에 따른 온실가스 배출량의 상승으로 인한 기후 위기가 국제적인 문제로 대두되고 있다. 이에 대응하기 위해 세계 각국은 탄소중립을 목표로 다양한 정책을 발표하고 있으며, 국내에서도 환경을 고려하여 농기계의 내연기관을 보다 친환경적인 전동기관으로 대체하려는 연구가 진행되고 있다. 국내에서 농업용 트랙터는 연간 작업 일수가 2008년 이후 연간 약 37.5일로 주요 농업 기계 중 가장 높은 빈도로 사용되는 농업기계이다[1]. 전기트랙터는 기존의 내연기관 트랙터에 대비하여 CO2 배출량을 최대 70%까지 감소할 수 있다고 보고된 바 있다[2]. 또한 농업 인구의 고령화로 인한 노동력 감소 및 기후 변화에 따른 생산량 감소가 식량 안보 문제를 심화시키고 있다. 이러한 문제를 해결하기 위해 자율 농기계는 농업 생산성을 향상시킬 수 있는 효과적인 방법으로 제시되고 있다[3].
전기구동 방식은 온실가스와 공해물질을 줄이는 것 외에도 내연기관 방식보다 더 나은 제어 성능을 가지고 있다. 기존의 내연기관 방식의 복잡한 구동 및 변속 시스템 등은 반응 속도가 느리고 제어 정확도가 낮다. 하지만 전기구동 방식은 내연기관에 비하여 구동 및 변속 시스템이 간단하기 때문에 제어가 더 쉽고 정확하게 이루어지며 결과적으로 자율 주행 시스템의 제어 명령이 정확하게 구현될 수 있다. 자율주행 기술은 운전자의 운전 부담을 줄일 수 있으며 운전 안정성을 향상시키고 이에 따라 발생하는 사고를 줄일 수 있다[4].
기존의 내연기관 트랙터와는 다르게 전기구동 트랙터는 조밀한 구조를 가질 수 있으며, 큰 출력 밀도 강한 과부하 용량, 그리고 높은 작업 효율성을 가지고 있다. 순수 전기트랙터의 구조는 크게 단일 모터, 듀얼 모터 독립, 듀얼 모터 결합 방식이 있다[5]. 현재 대부분의 순수 전기트랙터의 파워트레인은 디젤 엔진을 배터리와 모터로 대체하고 원래의 다단 변속기를 유지하는 단일 모터를 사용한다. 단일 모터와 다단 변속기를 저부하 조건에서 사용하는 경우, 모터가 저효율 영역에서 작동하게 되어 에너지 효율성이 떨어진다[6]. 듀얼 모터 방식의 경우, 차축과 PTO(Power Take-off)에 동력을 전달하기 위해 두 모터의 출력 용량이 각각 트랙터의 목표 출력과 동일해야 한다. 하지만 현재의 배터리 팩은 디젤 연료와 비교하였을 때 부피당 에너지 밀도가 낮다. 작업 주기 동안 필요한 에너지를 제공하기 위해 더 큰 용량의 배터리와 탑재 공간이 필요하다[7]. 이러한 이유로 듀얼 모터독립 방식의 경우 공간 활용에 있어 비효율적일 수 있다. 공간활용의 문제점들을 해결하기 위해 듀얼 모터 결합 방식을 사용한 동력 전달 시스템에 관한 연구가 진행되고 있다. 단일 고출력모터 혹은 두 개의 고출력 모터를 사용하는 대신 비교적 작은 출력의 두 개의 모터를 사용함으로써 모터의 용량을 줄일 수 있다. 이는 트랙터의 공간 활용에 도움이 되며 두 모터의 작동점은 작업 및 주행 시스템의 효율을 최적화하기 위해 조정될 수 있다[6].
국내 전기트랙터 개발 현황은 소형 전기트랙터가 개발된 사례는 있으나 상용화된 사례는 없는 실정이다. 국외 전기트랙터 개발 현황은 대형급 트랙터는 상용화된 사례가 없으며 중소형급 트랙터 중 일부만 상용화 되어있다. 국내외로 중대형급 트랙터의 상용화 사례가 없는 이유는 출력이 높은 트랙터일수록 용량에 적합한 배터리를 장착하는 것이 어렵기 때문이며, 변속기를 새로 개발해야 하는데 높은 비용과 개발기간이 소요되기 때문이다. 또한 내연기관과 비교하여 상대적으로 높은 가격이기 때문에 시스템 최적화를 통해 가격을 낮출 필요가 있다.
트랙터는 다양한 농작업을 수행하는 차량으로, 각각의 농작업에 따라 주요 부품에서 발생하는 부하의 특성이 다르게 나타난다. 따라서 트랙터 구동부의 동력 전달 시스템 설계를 위해서는 주요 농작업 시 발생하는 부하 데이터를 계측하고 이를 기반으로 모터 및 감속기의 주요 사양을 선정하는 것이 중요하다[8].
본 논문에서는 단일 유성기어를 사용한 듀얼 모터 결합 방식의 파워트레인 구조를 가진 40 kW급 전기트랙터 시뮬레이션 모델을 개발하고자 한다. 듀얼 모터 용량 선정을 위해 42 kW 출력의 내연기관 트랙터를 사용하여 쟁기, 로터리, 주행 작업을 대상으로 필드 시험을 진행하여 필요한 동력을 분석하였다. 분석 결과를 통해 듀얼 모터의 용량을 선정하고, 작업에 필요한 토크 및 속도를 고려하여 유성기어 기어비 및 감속 기어비를 선정하였다. 시뮬레이션 모델에는 실제 계측한 작업별 부하 데이터를 인가하여 선정한 듀얼 모터의 용량 및 감속 기어비가 적절한지 확인하였다.
기존 연구들은 엔진을 단일모터로 대체하고 다단 변속기를 유지한다. 단일 모터와 다단 변속기를 저부하 조건에서 사용하는 경우 에너지 효율성이 떨어지기 때문에 이러한 문제를 보완하고자 듀얼 모터 결합 구조가 필요하다. 기존 연구들은 모터 관점에서 동력을 분석하였다는 한계가 있고, 이러한 한계를 극복하기 위해 본 논문에서는 타이어와 토양과의 상호작용을 수식적으로 표현하여 전체적인 트랙터의 관점에서 견인력을 계산하여 필요한 모터의 동력을 확인하였다. 이를 통해 기존 트랙터의 엔진 및 다단 변속기 구조를 듀얼 모터와 단일 유성기어로 대체할 수 있는 가능성을 확인하였다.
2. 트랙터 부하 계측
2.1 트랙터 부하 계측 시스템
40 kW급 전기트랙터의 듀얼 모터의 용량 및 감속 기어비 선정을 위한 부하 계측을 위해 비슷한 용량의 42 kW 내연기관 트랙터를 선정하였다. Fig. 1은 트랙터의 형상이며 세부사항은 Table 1과 같다.
모터 용량 선정을 위해 계측이 필요한 부분은 쟁기 작업 시 차축의 동력 과 로터리 작업 시 차축의 동력 및 PTO의 동력을 계측하여야 하며 각각의 작업 시 차량의 이동속도에 대한 계측 및 분석이 필요하다고 판단하였다. 차축의 동력 계측을 위한 휠 토크미터, 차축의 회전속도를 계측하기 위한 근접각 센서, PTO 동력 계측을 위한 PTO 토크미터, 차량의 이동 속도 계측을 위한 RTK-GPS (Rear Time Kinematic Global Positioning System)센서 및 데이터를 실시간으로 저장할 수 있도록 DAQ(Data Acquisition)를 42 kW 내연기관 트랙터에 구성하였다. Fig. 2는 구성된 트랙터 계측 시스템의 형상이며 사용된 센서의 세부 사항은 Table 2와 같다.
2.2 필드 시험지 토양 분석
필드 시험은 토양 조건에 따라 결과가 상이하기 때문에 토양 상태에 대한 정의가 필요하다. 본 연구에서는 토양의 원추 관입지수(Cone Index, CI), 토양 성분, 토양의 함수율을 대상으로 진행하였다.
동일한 필드 시험 장소 내에서도 토양 조건이 균일하지 않기 때문에 원추 관입지수가 다르게 나타난다[8]. 따라서 가로 45 × 세로 25 m 크기의 필드 시험지를 크기가 동일한 격자 형태(가로 9 × 세로 5 m)로 구분하였으며 형상은 Fig. 3과 같다.
원추관입시험은 원추관입시험기(DIK-5532, Daiki, Japan)를 사용하여 진행하였고 격자를 3회 반복 계측한 값의 평균을 사용하였으며, 견인 부하 분석 시 주로 사용되는 0-20 cm의 계측 데이터를 0-5, 5-10, 10-15, 15-20 cm 구간으로 나누어 구간별 평균 데이터를 사용하였다. 토양 성분 분석 및 함수율 측정을 위한 토양 시료 채취는 격자 부분을 100 mL의 시료원통(DIK-1801, Daiki, Japan)과 채취기(DIK-1815, Daiki, Japan)를 사용하여 시료를 채취하였다. 토양 성분 분석은 미 농무부(USDA)의 분류법에 따라 분석을 진행하였다. 수분 함량은 오븐 건조법을 이용하여 채취한 시료를 105°C에서 24시간 건조 후, 건조 전 토양 무게와 건조 후 토양 무게를 비교하여 분석하였다. Table 2는 토양 분석 결과이다.
2.3 필드 시험 조건
트랙터 부하 데이터를 얻기 위한 필드 시험의 종류로는 농작업 중 빈도가 높은 쟁기 작업 및 로터리 작업[9]과 필드 주행 시험, 아스팔트 주행 시험, 기동 토크 시험으로 선정하였다. 쟁기 작업기 및 로터리 작업기는 트랙터의 용량에 적합한 작업기를 선정하였다. Fig. 4는 선정된 작업기의 형상이며 제원은 Table 3과 같다. 트랙터의 주행 단수는 실제 사용자들의 조건을 반영하기 위해 쟁기 작업은 주변속과 부변속을 기준으로 M1(3.4 km/h), M2(5.0 km/h), M3(7.2 km/h)으로 선정하였다. 로터리 작업은 PTO 단수를 기준으로 PTO 1단(540 rpm), 2단(750 rpm), 3단(1,000 rpm), 주변속과 부변속을 기준으로 L3(2.3 km/h), M1 (3.4 km/h), M2(5 km/h)으로 선정하였다. 필드 주행 시험은 주변속과 부변속을 기준으로 M2(5.0 km/h), M3(7.2 km/h)으로 선정하였다. 아스팔트 주행시험은 트랙터의 정격 최고 속도일 때의 부하를 얻기 위해 주변속과 부변속을 기준으로 H4(30.6 km/h)로 선정하였다. 기동 토크 시험은 차량이 정지 상태에서 작동을 시작하기 위해 필요한 토크 데이터를 얻기 위해 주변속과 부변속을 기준으로 L3(2.3 km/h), L4(3.0 km/h), M1(3.4 km/h), M2 (5.0 km/h)로 선정하였다. 모든 작업 및 주행 시험은 동일한 조건에서 3회 반복 수행하여 부하 데이터를 취득하였다. Fig. 5는 실제 계측 시험 중 모습이다.
3. 동력 전달 시스템
3.1 단일 유성기어식 동력 전달 시스템
본 연구에서는 기존의 내연기관 트랙터의 엔진과 변속기를 듀얼 모터와 단일 유성기어를 사용한 변속기로 대체하고자 한다. 유성기어는 링기어, 선기어, 캐리어로 이루어져 있다. 첫 번째 모터는 PTO와 링기어에 연결되어 있는 작업 모터이고, 두 번째 모터는 선기어에 연결되어 있는 주행 모터이다. 캐리어는 차축과 연결되어 있다. 쟁기 작업 및 주행 시에는 PTO로 동력이 전달되지 않도록 PTO와 작업모터 사이에 클러치가 위치한다. PTO를 사용하는 작업 시에는 작업모터가 PTO만을 구동하고 선기어에 연결된 주행 모터만이 차량을 구동한다. 작업 모터로부터 링기어로 동력이 전달되지 않도록 작업 모터와 링기어 사이에 클러치가 위치한다. 링기어가 고정되지 않은 상태에서 선기어만 단독으로 회전하면 선기어와 링기어를 연결하는 플래닛 기어가 자전하게 되어 캐리어로 동력이 전달되지 않기 때문에 링기어를 고정하기 위한 브레이크가 필요하다. Fig. 6은 유성기어의 형상이다. Figs. 7과 8은 파워트레인 구성 및 작업에 따른 동력 흐름이다.
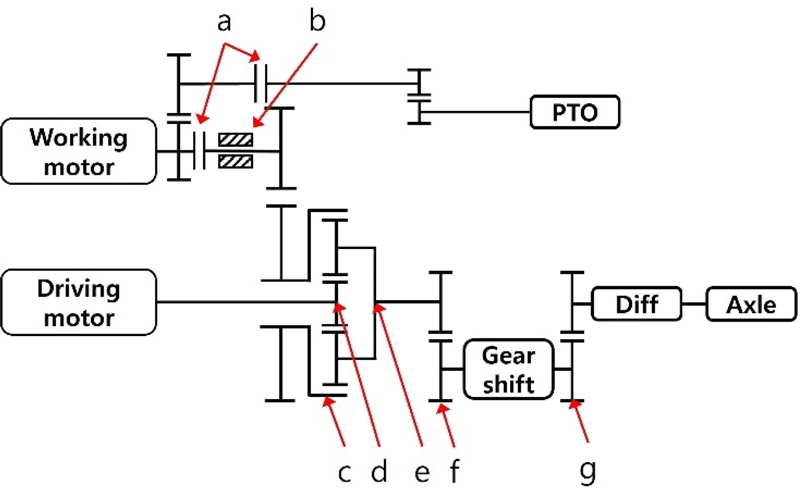
Schematic diagram of electric tractor powertrain based on planetary gear system: a. Clutch, b. Brake, c. Ring gear, d. Sun gear, e. Carrier, f. Main reduction gear, and g. Final reduction gear
3.2 모터 용량 선정
작업 모터와 주행 모터의 용량은 내연기관 트랙터를 활용한 필드 시험에서 얻은 필요 차축의 토크, 속도, 출력, PTO의 토크, 속도, 출력 데이터를 분석하여 선정하였다. 작업 모터는 로터리작업 시 PTO의 최대 부하가 측정된 PTO 3단, 주변속과 부변속은 M2 조건을 기준으로 선정하였다. PTO 3단의 평균 출력은 26.6 kW이다. 다양한 토양 환경을 고려하여 작업 모터의 용량은 30 kW로 선정하였다.
주행 모터의 용량은 로터리 작업 시 주행 모터 단독으로 트랙터를 구동해야 하는 조건과 쟁기 작업 및 주행 시 유성기어를 통해 작업 모터와 동력이 결합되는 특성을 고려하여 선정하였다. 로터리 작업 시 PTO 3단, 주변속과 부변속 M2에서 계측된 차축의 평균 출력은 5.6 kW이며, 최대 출력은 9.5 kW이다. 쟁기 작업 시 최대 차축 출력은 주변속과 부변속 M3에서 평균 24.2 kW, 최대 43.6 kW이다. 앞서 설명한 조건과 다양한 토양환경을 고려하여 작업 모터의 용량은 10 kW로 선정하였다. 선정된 모터의 제원은 Table 4와 같다.
3.3 유성기어 기어비 및 감속 기어비 선정
유성기어의 기어비 k는 선기어의 잇수와 링기어의 잇수의 비율로 표현할 수 있으며 식(1)과 같다. 유성기어의 속도 및 토크는 Lever Analogy를 통해 정의할 수 있다[10]. 식(2)는 Lever Analogy 속도 공식이며 식(3)과 식(4)는 토크 공식이다. 링기어와 선기어로 토크가 동시에 인가될 경우 식(3)을 따르고, 링기어, 선기어, 캐리어 중 어떤 하나라도 고정될 경우 식(4)를 따르게 된다.
Fig. 9는 Lever Analogy를 통한 유성기어의 속도 및 토크 관계이다.
(1) |
(2) |
(3) |
(4) |
위 식에서 Zr은 링기어의 잇수, Zs는 선기어의 잇수이다. ωc는 캐리어의 회전속도(rad/s), ωr은 링기어의 회전속도(rad/s), ωs는 선기어의 회전속도(rad/s)이다. Tc는 캐리어의 토크(Nm), Tr은 링기어의 토크(Nm), Ts는 선기어의 토크(Nm)이다.
링기어와 선기어의 회전속도와 회전방향이 정해지면 Lever Analogy 속도 공식에 따라 캐리어의 회전속도가 정해지게 된다. 캐리어의 속도는 감속기를 거쳐 감소한 속도가 차축의 속도가 된다. Lever Analogy 토크 공식에 따라 링기어와 선기어를 통해 캐리어로 전해진 토크는 감속기를 거쳐 모터의 부족한 토크를 증가시켜 차축으로 전달한다. 감속기의 기어비는 높아질수록 기어비의 비율만큼 토크가 증가하고 회전속도는 감소한다. 따라서 작업 종류에 따라 유성기어를 통해 모터의 동력이 결합하거나 분기되므로 작업 시 필요한 토크 및 주행 속도 조건을 동시에 만족하기 위한 감속 기어비를 선정해야 한다. 식(5)와 식(6)은 차축에 필요한 토크와 속도를 고려한 감속 기어비를 구하는 식이다.
(5) |
(6) |
위 식에서 RGT는 작업 시 차축의 토크를 고려한 감속 기어비이며, RGω는 작업 시 차축의 속도를 고려한 감속 기어비이다. r은 42 kW 내연기관 트랙터 후륜 타이어의 반지름으로 0.695 m이며 Vvehicle은 차량의 속도(km/h)이다.
유성기어의 링기어와 선기어의 토크는 Lever Analogy를 통해 유성기어의 기어비 비율로 더해져서 캐리어로 전달된다. 이러한 유성기어의 특징에 따라 작업 모터의 정격 토크인 72 Nm와 주행 모터의 정격 토크인 24 Nm를 충분히 활용하기 위해 두 모터의 정격 토크비를 고려하여 유성기어의 기어비 k는 3으로 선정하였다.
PTO의 감속 기어비는 작업 모터의 정격 속도인 4,000 rpm 및 PTO의 최대 회전속도인 1,000 rpm과 작업 중 평균 토크 중 가장 높은 토크인 274.1 Nm를 만족하기 위해 4로 선정하였다.
로터리 작업 시 작업 모터는 PTO로만 동력을 전달하기 때문에 주행 모터만으로 기동 토크 및 작업 수행 중 차축 토크를 이겨내며 최소 목표 작업 속도를 구현할 수 있는 감속 기어비를 선정해야 한다. 로터리 작업 시 링기어는 고정되기 때문에 Lever Analogy 속도 및 토크 공식으로부터 주행 모터의 토크는 선기어를 통해 k+1 비율인 4만큼 증가하여 캐리어로 전달되며 회전속도는 k+1비율인 4만큼 감소하여 캐리어의 속도가 된다. 기동 토크가 유지되어야 하는 시간은 짧기 때문에 주행 모터의 최대 출력을 이용한다. 기동 토크의 평균값인 6,590.1을 만족하기 위해 감속 기어비는 36.9 이상이 되어야 한다. 주행에 필요한 차축 토크의 평균 값 중 가장 큰 값인 3,925.1 Nm를 정격 토크로 만족하기 위해 감속 기어비는 40.9 이상이 되어야 한다. 주행 모터의 정격 속도인 4,000 rpm을 유지하면서 최소 목표 속도인 5.0 km/h를 만족하기 위해 필요한 감속 기어비는 49.8 이하가 되어야 한다. 위와 같은 조건으로 선정된 감속 기어비는 40.9이다. 감속 기어비를 고려하였을 경우 주행 모터의 정격 속도에서 차량의 최대 속도는 6.4 km/h, 주행 모터의 최대 속도에서 차량의 최대 속도는 9.6 km/h이다.
쟁기 작업 시 작업 수행 중에 차축 토크를 이겨내며 최소 작업 속도를 구현할 수 있도록 감속 기어비를 선정해야 한다. 작업 모터와 주행 모터의 동력이 결합되는 특징을 고려하여 쟁기 작업 중 계측된 차축 토크의 최댓값인 14,576.6 Nm를 모터의 최대 토크로 만족하기 위해 감속 기어비는 106.4 이상이 되어야 한다. 쟁기 작업 중 계측된 차축 토크의 평균값 중 가장 큰 값인 7,735.4 Nm를 모터의 정격 토크로 만족하기 위해 감속 기어비는 80.6 이상이 되어야 한다. 모터의 정격 속도인 4,000 rpm을 유지하면서 최소 목표 속도인 7.2 km/h를 만족하기 위해 필요한 감속 기어비는 138.2 이하가 되어야 한다. 위와 같은 조건으로 선정된 감속 기어비는 106.4이다. 감속 기어비를 고려하였을 경우 모터의 정격속도에서 차량의 최대 속도는 9.8 km/h이고, 모터의 최대 속도에서 차량의 최대 속도는 14.7 km/h이다.
위와 같은 과정으로 선정된 감속 기어비는 총 2단으로 1단은 106.4, 2단은 40.9이다. 2단으로 주행 시 작업 모터와 주행 모터의 정격 속도인 4,000 rpm에서 차속은 24.3 km/h이며, 차축으로 3,926.4 Nm의 토크를 전달할 수 있기 때문에 아스팔트 주행 시 최대 차축 토크인 3,175.0 Nm 이상임을 확인할 수 있다. 또한 최대 목표 주행 속도인 30.64 km/h일 때, 캐리어의 회전속도는 5,037.5 rpm이다. 작업 모터와 주행 모터의 최대 회전속도인 6,000 rpm으로 회전 시, 캐리어의 최대 회전속도는 6,000 rpm으로 최대 38.4 km/h까지 가능하다.
4. 트랙터 시뮬레이션 모델
4.1 시뮬레이션 모델링
시뮬레이션 모델은 MATLAB/Simulink/Simscape를 사용하여 개발하였다. 시뮬레이션 모델은 모터, 변속기, 차량, PTO, 타이어와 같은 주요 구성 요소들의 제원 및 성능 곡선을 반영할 수 있도록 모델링 하였다. Fig. 10은 Simulink를 사용하여 구성한 트랙터 시뮬레이션 모델이다.
작업 모드에 따라 PTO와 차축으로 모터의 동력이 적절하게 전달될 수 있도록 클러치와 브레이크가 작동하도록 하였다.
모터 모델은 변속기 모델로부터 필요한 모터의 토크와 속도 명령 값을 구해낸다. 토크-속도 선도를 사용하여 최대 토크를 제한하도록 하였다.
타이어-토양 상호작용 모델은 차량의 실제 속도와 휠의 회전속도인 이론속도를 통해 슬립을 계산하며, 계산된 슬립을 통해 차량에 작용하는 토양 추진력 공식에 사용된다. 슬립은 식(7)을 통해 구할 수 있다. 토양 추진력과 타이어의 운동저항 실험식은 미국 농공학회의 표준식(ASABE D497.4)을 사용하였으며 식(8), (9), 그리고 (10)과 같다.
(7) |
위 식에서 s는 슬립률(%), Vx는 차량의 속도(m/s), rw는 타이어의 반지름(m), ωw는 타이어의 회전속도(rad/s)이다.
(8) |
(9) |
(10) |
위 식에서 GT는 총 견인력(kN), W는 차축 부하(kN), Bn은 기동 지수, MR은 운동저항(kN), NT는 순 견인력(kN), DP는 트랙터의 견인력(kN)이다.
(11) |
위 식에서 CI는 토양의 원추 관입지수(kPa), δ는 타이어 변형량(m), h는 무부하 상태의 타이어 높이, b는 무부하 상태의 타이어 폭(m), d는 무부하 상태의 타이어 지름(m)을 의미한다.
트랙터의 동역학 모델은 트랙터의 종방향 동적 거동에 대한 모델 및 동력 전달 시스템의 회전방향 동적 거동 모델로 이루어져 있다. 식(12)는 종방향 동적 거동, 식(13)은 회전방향 동적 거동에 관련된 식이다. Fig. 11은 Simscape를 사용하여 구성한 동력전달 시스템의 회전방향 동적 거동 모델이며 동력원인 작업 모터와 주행 모터, 클러치, 브레이크, 유성기어, PTO, 타이어로 구성하였다.
(12) |
위 식에서 FGT는 총 견인력(kN), FL은 견인 부하(kN), FMR은 운동 저항(kN), M은 트랙터의 질량(kg), ax는 종방향 가속도(m/s2)을 의미한다.
(13) |
위 식에서 TWM은 작업 모터의 토크(Nm), TDM은 주행 모터의 토크(Nm), TPTO는 PTO의 토크(Nm), TAxle은 차축의 토크(Nm), iTotal은 전체 관성(kg·m2), αAxle은 전체 축의 가속도(rad/s2)이다.
5. 시뮬레이션 결과
5.1 쟁기 작업 모드 결과
42 kW 내연기관 트랙터를 이용하여 주변속과 부변속 기준 M3단에서 쟁기 작업을 통해 얻은 차축 부하 데이터를 시뮬레이션 모델의 부하 데이터로 인가 하였다. Fig. 12의 속도 그래프를 통해 트랙터가 부하를 이겨내며 속도를 유지하는 것을 확인할 수 있다. 또한 모터의 작동점이 트랙터가 정지 상태에서 구동하기 위해 정격 출력 이상의 토크가 3-5초 정도의 짧은 시간 동안 필요하지만 작업이 시작된 이후로는 정격 출력 선도 내에서 작동하는 것을 확인할 수 있다. 이를 통해 모터의 용량 및 감속 기어비가 적절하게 선정되었다고 판단된다. 또한 유성기어의 속도 및 토크 그래프를 통해 작업 모터와 주행 모터의 토크 및 속도가 유성기어 관계식에 따라 링기어와 선기어를 통해 동력이 결합되어 캐리어로 전달되는 것을 확인할 수 있다.
5.2 로터리 작업 모드 결과
42 kW 내연기관 트랙터를 이용하여 PTO 1단, 주변속과 부변속 기준 M2단에서 작업을 통해 얻은 PTO 부하 데이터 및 차축 부하 데이터를 시뮬레이션 모델의 부하 데이터로 인가하였다. Fig. 13의 결과 데이터를 통해 로터리 작업 시 주행 모터 단독으로 트랙터가 목표 속도로 주행이 가능함을 확인할 수 있었고, 작업 모터 또한 부하를 이겨내며 PTO 작업이 가능함을 확인할 수 있다. PTO 작업 시 주행 모터의 작동점은 트랙터가 정지 상태에서 구동하기 위해 정격 출력 이상의 토크가 3-5초 정도의 짧은 시간 동안 필요하지만 작업이 시작된 이후로는 정격 출력선도 내에서 작동하는 것을 확인할 수 있다. 작업 모터의 작동점은 PTO에 인가되는 부하에 따라 정격 출력 이상의 토크가 필요하지만 짧은 순간의 부하이기 때문에 모터에 큰 영향을 미치지 않는다. 모터의 작동점 확인을 통해 감속 기어비 및 PTO 기어비가 적절하게 선정되었다고 판단된다. 유성기어의 속도 및 토크 그래프를 통해 링기어의 속도 및 토크가 0인 것을 확인할 수 있고, 이를 통해 로터리 작업 모드에서 작업 모터와 링기어 사이의 클러치 및 브레이크가 작동하여 작업 모터에서 링기어로 동력 전달을 차단하고 있음을 확인할 수 있다. 또한 주행 모터의 토크 및 속도가 유성기어 관계식에 따라 선기어를 통해 증폭되고 감소되어 캐리어로 전달되는 것을 확인할 수 있다.
6. 결론
본 논문에서는 듀얼 모터와 유성기어를 사용한 동력 전달 시스템 기반의 40 kW급 전기트랙터의 시뮬레이션 모델을 개발 하였다. 유성기어를 활용한 동력 전달 시스템의 농작업에 따른 동력 전달 과정을 기반으로 모터의 용량, 감속 기어비 선정을 위해 비슷한 용량의 42 kW급 내연기관 트랙터를 활용하여 다양한 단수 조건에서 농작업별 부하를 취득 및 분석하였다. MATLAB/Simulink/Simscape를 활용하여 모델링을 진행하였고 실제 필드 시험을 통해 얻은 차량의 부하 데이터를 시뮬레이션의 부하 조건으로 인가하여 시뮬레이션을 진행하였다. 시뮬레이션 결과를 통해 작업 모드에 따라 클러치 및 브레이크가 작동하여 유성기어를 통해 동력이 적절하게 전달되는 것을 확인할 수 있었다. 향후에는 농작업 시 모터의 효율맵을 이용하여 작업 모터와 주행 모터가 고효율점에서 구동될 수 있는 제어 기법을 포함하고, 실제 듀얼 모터와 유성기어 기반 동력 전달 시스템 기반의 전기트랙터 개발을 통해 시뮬레이션 모델을 검증할 예정이다.
Acknowledgments
본 논문은 한국생산기술연구원 기업수요기반생산기술실용화사업I “[Key-Tech] 농작업 환경에서 친환경 동력원을 이용한 스마트 전기구동 플랫폼 개발(JA- 24-0006)”의 지원으로 수행한 연구임.
REFERENCES
- Korea Institute of Machinery Industry Cooperative (KAMICO) and Korean Society for Agricultural Machinery (KSAM), (2023), Agricultural Machinery Yearbook in Republic of Korea.
-
Ueka, Y., Yamashita, J., Sato, K., Doi, Y., (2013), Study on the development of the electric tractor: Specifications and traveling and tilling performance of a prototype electric tractor, Engineering in agriculture, environment and food, 6(4), 160-164.
[https://doi.org/10.1016/S1881-8366(13)80003-1]
-
Seo, D., Won, J.-H., Yang, C., Kim, G., Kwon, K.-D., Kim, K.-C., Hong, Y., Ryu, H. S., (2021), Development of boundary detection methods based on images for path following of autonomous tractor, Journal of Korean Institute of Communications and Information Sciences, 46(11), 2078-2087.
[https://doi.org/10.7840/kics.2021.46.11.2078]
-
Hang, P., Chen, X., (2021), Towards autonomous driving: Review and perspectives on configuration and control of four-wheel independent drive/steering electric vehicles, Actuators, 10(8), 184.
[https://doi.org/10.3390/act10080184]
-
Liu, M., Wei, C., Xu, L., (2020), Development of cooperative controller for dual-motor independent drive electric tractor, Mathematical Problems in Engineering, 2020(1), 4826904.
[https://doi.org/10.1155/2020/4826904]
-
Li, T., Xie, B., Li, Z., Li, J., (2020), Design and optimization of a dual-input coupling powertrain system: A case study for electric tractors, Applied Sciences, 10(5), 1608.
[https://doi.org/10.3390/app10051608]
-
Mocera, F., Somà, A., Martelli, S., Martini, V., (2023), Trends and future perspective of electrification in agricultural tractor-implement applications, Energies, 16(18), 6601.
[https://doi.org/10.3390/en16186601]
-
Jung, B. H., Park, Y. J., Park, H. K., Park, S. B., Kim, K. U., (2005), Mapping of cone index for precision tillage, Korean Journal of Agricultural Science, 30(2), 127-133.
[https://doi.org/10.5307/JBE.2005.30.2.127]
- Lee, D. H., (2011), Analysis of power requirements of tractor for field operations, M.Sc. Thesis, Sungkyunkwan University.
-
Benford, H. L., Leising, M. B., (1981), The lever analogy: A new tool in transmission analysis, SAE Transactions, 90(1), 429-437.
[https://doi.org/10.4271/810102]
M.S candidate in the Department of Bioindustrial Machinery Engineering, Jeonbuk National University, and working as a student researcher at Korea Institute of Industrial Technologies(KITECH). His research interest are modeling, controller design of special purpose vehicle.
E-mail: skskdbek@kitech.re.kr
Ph.D. candidate in the Department of Biosystems Engineering, Seoul National University, and working as a student researcher at Korea Institute of Industrial Technologies(KITECH). His research interests are modeling, controller design of special purpose vehicle.
E-mail: kkd4943@kitech.re.kr
M.S candidate in the Department of Biosystems Engineering, Seoul National University, and working as a student researcher at Korea Institute of Industrial Technologies(KITECH). His research interests are modeling, controller design of special purpose vehicle.
E-mail: lsy1014@kitech.re.kr
Professor in Department of Bioindustrial Machinery Engineering, Jeonbuk National University. His research interests are agricultural machinery, open-field smart farm.
E-mail: dckim@jbnu.ac.kr
Dr. Kim is a principal researcher at Korea Institute of Industrial Technologies(KITECH). His research interests are electric and autonomous vehicle, integrated vehicle control system.
E-mail: wgk@kitech.re.kr