
구멍-핀 패턴 조립의 부동 개선과 과잉제약 해소를 위한 설계 방안 수치 연구
Copyright © The Korean Society for Precision Engineering
This is an Open-Access article distributed under the terms of the Creative Commons Attribution Non-Commercial License (http://creativecommons.org/licenses/by-nc/3.0) which permits unrestricted non-commercial use, distribution, and reproduction in any medium, provided the original work is properly cited.
Abstract
This paper addresses the issue of over-constrained assembly in mechanical designs using hole-pin patterns. When two hole-pin pairs are used, they can cause interference between components, leading to assembly failures. To mitigate this, designers often enlarge holes relative to pins to have a large float. However, when functional requirements do not permit significant float, field design engineers tend to add more assembly features, hoping them to mutually limit the float allowed by others. This numerical study employed two commercial tolerance analysis programs to demonstrate that these design changes could not sufficiently reduce float to justify added costs. Instead, this paper proposed an exactly-constrained design by replacing one of the holes with an elongated hole. Numerical analysis showed that this approach significantly reduced float compared to current design practices. This paper logically explains why this must be the case. It is hoped that this study contributes to the advancement of mechanical assembly design practices by adopting the exact constraint concept.
Keywords:
Hole-pin pattern assembly, Part float, Tolerance analysis, Tolerance design, Proper/Exact constraint, Over-constraint키워드:
구멍-핀 패턴 조립, 부품 부동, 공차해석, 공차설계, 적정제약, 과잉제약1. 서론
조립체의 기하품질(Geometric Quality)은 기능, 신뢰성, 심미성 등 다양한 관점에서 중요한데, 제품의 성능이 고도화되고 구매자의 요구가 까다로워지면서 그 중요도가 더욱 커지고 있다. 이에 따라 제품설계, 공정설계, 구매, 생산, 검사, 품질관리 등 제품의 기하품질에 영향을 주는 모든 부서의 전사적 협업을 통해 기하품질을 확보하도록 하는 공차공학(Dimensional Engineering/Management)이 제품 개발 프로세스의 중요 기술이 되고 있다[1].
공차공학 중 제품설계 단계에서는 부품 사이의 조립을 어떻게 할지를 결정하는 조립설계(Design of Assembly)가 중요하다. 조립설계의 주된 내용은 편차가 있어도 기하품질이 크게 저하되지 않는 강건(Robust)한 조립구조를 고안하는 것이며, 그 시작은 부품 사이의 자유도 제약 관계를 잘 결정하는 것이다[2,3]. 자유도 제약은 부품들이 가지고 있는 조립형체(Assembly Features), 즉 평면, 구멍, 핀 등의 형체들이 서로 접촉하면서 이루어지는데, 이때 과잉제약(Over-constraint)을 피하고 적정제약(Exact Constraint)을 구현하는 것이 중요하다. 이는, 과잉제약이 되면 부품들이 간섭되어 조립이 안 되거나 변형과 응력이 발생하는 등 품질 저하를 일으키기 때문이다.
본 논문에서는 가장 흔한 조립구조인 구멍-핀 패턴 조립의 과잉 제약과 부동(Float)을 다룬다. 이와 관련된 분야의 기존 연구를 살펴보면, 우선 조립형체들이 갖는 공차를 확률적으로 표현하고 그 효과를 수치 모델링하는 연구들이 있다. 예를 들어, Lee & Yi는 공차와 간극(Clearance)의 확률분포를 여러 확률분포 함수로 가정하고 몬테카를로 시뮬레이션을 수행하여 조립성을 분석했다[4]. 또 Teissandier et al.은 공차역을 정의하는 PACV라는 기하학적 개념을 개발하여 간극을 표현하는 기법을 연구하였다[5]. 다른 관련 연구로서는 로봇 등 기구설계에서 구멍-핀 조인트의 간극이 기구의 성능에 미치는 영향을 연구한 논문들이 있다[6,7]. Kim et al.은 두 개의 구멍에 최대실체조건(MMC)의 기하공차가 주어졌을 때 두 구멍 사이의 재료 두께를 확률분포로 구하는 방법을 개발했다[8]. 비교적 최근에는 Polini가 간극에 따른 부동을 좌표변환의 미소 성분 형태로 표현하고, 부동을 나타내는 변환행렬을 병진 부동 성분과 회전 부동 성분으로 표시한 후 이들의 확률분포를 가정하여 그 영향을 계산하는 방법을 개발하였다[9].
상기한 기존 연구는 모두 구멍-핀 패턴 조립의 공차해석 방법을 개발하는 데 그쳤다. 이에 반해 본 논문은 신뢰도 높은 상용 공차해석 프로그램을 이용하여 구멍-핀 조립설계에서 일어나는 자유도 제약과 부동을 상세히 고찰할 뿐 아니라, 이를 바탕으로 부동을 개선하는 설계 방안들(특히 적정제약 설계 방안)을 비교하며 연구한 점에서 차별화되는 실용 연구이다.
본 논문의 전개 순서는 다음과 같다. 먼저, 두 쌍의 구멍-핀 조립으로 이루어지는 기본 문제를 정의하고, 이 조립구조가 과잉제약임을 설명한다. 기본 문제에서 간섭을 피하고 조립성을 확보하기 위해 부동을 감수해야 함을 설명하고 그 부동량을 해석해와 수치해로 구한다. 다음으로는 부동을 줄이기 위해 현업에서 사용하는 방법, 즉 조립형체를 추가하는 방법의 유효성을 고찰한다. 마지막으로, 기본 문제에서 한 개의 구멍을 장공(Elongated Hole) 또는 슬롯(Slot)으로 변경하는 적정제약 설계 방안을 제시하고, 부동 감소 효과를 고찰한다. 단, 본 논문에서 모든 길이의 단위는 mm이며, 편의상 단위의 기입은 생략한다.
2. 기본 문제
2.1 문제 설명 및 자유도 제약
이 절에서는 본 논문에서 고찰하는 기본 문제를 정의하고 그 특성을 설명한다. 기본 문제는 Fig. 1에 보인 바와 같이 2개의 핀을 갖는 판형 부품 A와 2개의 구멍을 갖는 판형 부품 B의 조립 문제이다. 이는 흔히 사용되는 구멍-핀(또는 나사) 조립구조의 가장 간단한 형태이다. 참고로, 더 많은 구멍-핀 쌍이 포함되는 경우는 4장에서 다룰 문제의 유형으로 볼 수 있다.
Fig. 1의 두 부품 중 부품 A가 고정되어 있다고 간주하고, 부품 B가 부품 A에 조립되면서 그 자유도가 어떻게 제약되는지 고찰해 보자. 모든 형체는 CAD 모델처럼 완벽한 형상, 방향, 위치를 가지며 모든 구멍과 핀은 동일한 직경을 갖는 것으로 가정한다. 먼저, 두 부품 사이의 평면-평면 조립에 의해 부품 B의 자유도 3개, 즉 Z축 방향 병진과 X축 및 Y축 중심의 회전 자유도가 제약됨을 알 수 있다. 다음으로 2개의 구멍-핀 쌍 각각이 Fig. 1의 흰색 화살표로 표시했듯이 X축 및 Y축 방향 병진 자유도를 제약한다. 이때 Y축 방향 병진 자유도 제약의 중복은, 이 중 하나가 다른 구멍-핀 쌍을 중심으로 하는 회전 자유도를 제약하므로 과잉제약을 일으키지 않고, 자유도 제약을 완성한다. 그러나 X축 방향 병진 자유도 제약의 중복은 과잉제약을 일으키며[2], 이는 구멍-핀 쌍 각각에 의해 결정되는 부품 B의 X 위치가 서로 일치하지 않으면 조립에 실패한다는 뜻이다. 실제 문제에서는 제작 편차로 인해 구멍 사이 거리와 핀 사이 거리가 일치할 수 없으므로 항상 조립에 실패하게 된다. 참고로, Fig. 1의 문제에서 부품 B의 판이 두꺼우면 X축 및 Y축 중심 회전 자유도도 중복하여 제약되지만, 본 논문에서는 부품 B가 충분히 얇은 것으로 간주하여 이를 무시한다.
2.2 기본 문제의 설계
Fig. 1의 문제에서 구멍 사이 거리와 핀 사이 거리가 일치하지 않아도 조립이 가능하게 하려면, 구멍의 직경을 키워야 한다. 이때, 핀 사이 거리와 구멍 사이 거리의 차이가 클수록, 즉 핀과 구멍의 위치공차가 클수록 더 큰 간극이 필요하므로 구멍을 더 크게 해야 한다[10].
기하공차(GD&T) 이론[1,11]에서는, 상기 개념을 적용하여 ‘최악조건 경계(Worst Case Boundary, WCB)’를 근거로 하는 조립보장 설계 방법을 제시한다. 여기서 ‘최악조건 경계(WCB)’란 구멍(또는 핀)이 상대 부품의 핀(또는 구멍)과 조립되는 공정에 있어 조립이 가장 어려워지는 조건의 원통 경계면을 의미하는데, 그 중심은 진위치(True Position)에 있고 직경(Φ,WCB)은 다음의 식으로 구해진다.
(1) |
(2) |
식(1)과 식(2)에서 하첨자 h와 p는 각각 구멍과 핀을 의미하고, MMC는 Maximum Material Condition의 약자이므로 Φh,MMC는 구멍 직경의 최소 허용값, Φp,MMC는 핀 직경의 최대 허용값을 의미하며, TOP는 위치도를 뜻한다.
식(1)에서 구한 구멍의 WCB 직경(Φh,WCB)이 식(2)에서 구한 핀의 WCB 직경(Φp,WCB)보다 크거나 같으면, Fig. 2와 같이 핀의 원통면이 항상 구멍의 원통면 안에 있게 되므로 구멍과 핀이 간섭을 일으킬 수 없고 이들 간 조립이 보장된다. 그러나, Fig. 2에서 보듯이, 이러한 설계에서는 구멍과 핀 사이 간극이 커지게 되어 부품사이 부동이 커지게 된다. 이 논문에서는, 부동이 가능한 적도록 구멍과 핀의 WCB 직경을 같게(Φh,WCB = Φp,WCB) 설계한다. 즉, 식(1)과 식(2)를 이용하면 다음의 조건이 만족되도록 한다.
(3) |
이처럼 WCB 개념에 근거하여 기본 문제의 치수와 공차를 설계하였고, 그 결과 두 부품의 도면은 Fig. 3과 같다. 이 논문에서는 문제를 단순화하기 위해 부품 A에는 공차를 주지 않고 부품 B의 구멍에만 크기 공차와 위치도(둘 다 임의 값 0.25 mm)를 주었는데, 이는 하나의 부품에만 공차를 주어도 부품 사이 부동 현상을 관찰할 수 있기 때문이다. 또, 기하공차에서는 구멍의 위치도만큼 방향공차도 허용되는데, 문제를 단순화하기 위해 구멍의 데이텀 A에 대한 직각도는 허용하지 않았다. 이는, 부품 B의 판 두께가 얇으면 방향공차의 영향이 적어지므로, 2.1절 끝부분에 언급한 가정을 따른 셈이다.
3. 기본 문제의 부동 분석
3.1 부동의 척도
부품의 부동을 연구하기 위해 정량적인 척도가 필요하다. 본 논문에서는 Polini [3]를 따라, 두 부품이 조립된 상태에서 부품 B가 부품 A에 대해 상대적으로 보이는 면내 부동을 두 구멍 사이 중점의 면내 변위 Δx, Δy와 부품 B의 면내 회전각 Δθ로 측정한다(Fig. 4 참조).
3.2 최대 부동 범위
우선 기본 문제(Fig. 3)에서 부품 B의 부동을 나타내는 Δx, Δy, Δθ의 최대 범위를 해석적으로 구해보자. 즉, 양(+)과 음(−)의 값을 가질 수 있는 Δx, Δy, Δθ 각각의 최댓값과 최솟값의 차이를 구한다.
부동은 구멍과 핀 사이의 간극이 클수록 커지므로, 부동 범위가 최대가 되는 것은 부품 B의 구멍이 가장 크고(즉 LMC (Least Material Condition)이고) 두 구멍의 위치 오차가 없거나 동일한(즉 동일한 방향으로 동일한 크기의 오차가 있는) 경우이다. 이런 경우의 한 예가 Fig. 5에 있는데, 이때 Δx나 Δy의 최대 범위(rx, max, ry,max)는 부품 B가 회전 없이 ±x 방향이나 ±y 방향으로 최대로 병진할 때 나타나며, 식(3)을 이용하면 그 값은 다음과 같다.
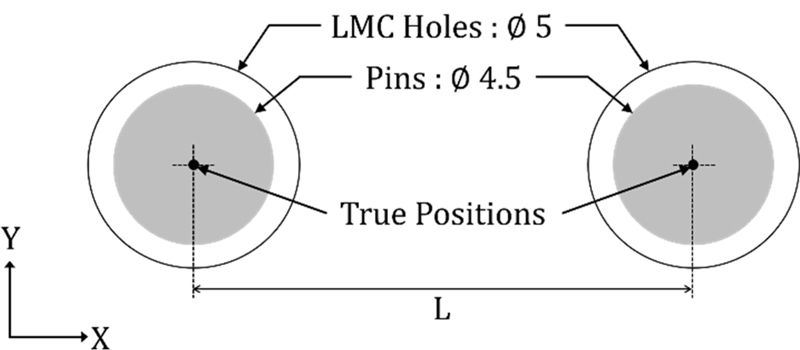
One situation enabling maximum float in the base problem with two hole-pin pairs. All numbers in [mm]
(4) |
식(4)로부터, 병진 부동의 최대 범위는 구멍과 핀의 크기공차 및 위치공차의 총합과 같음을 알 수 있고, Fig. 3의 수치를 대입하면 rx, max = ry,max = 0.5 mm가 된다.
Δθ의 최대 범위(rθ, max)는 Fig. 5의 부품 B가 Figs. 6(a) 및 6(b)와 같이 두 구멍 사이 중점 C를 중심으로 양방향 회전하여 구멍이 핀에 접하는 경우로부터 구할 수 있다. Fig. 7은 Fig. 6(a)의 좌측 핀 중심 A, 좌측 구멍 중심 B, 그리고 중앙점 C로 이루어지는 삼각형을 보여준다. 한 방향으로 발생할 수 있는 최대 회전 부동각을 Δθmax라 하면 이는 Fig. 7에서 각 ACB이다. Fig. 5에 보인 바와 같이 두 핀 사이 거리를 L로 정의하면, 선분 AC 및 선분 BC의 길이는 L/2이다. Fig. 6(a)에 보였듯이 구멍과 핀이 접하고 있으므로, 핀과 구멍의 중심 사이 거리, 즉 선분 AB의 길이 d를 구하면 다음 식과 같다.
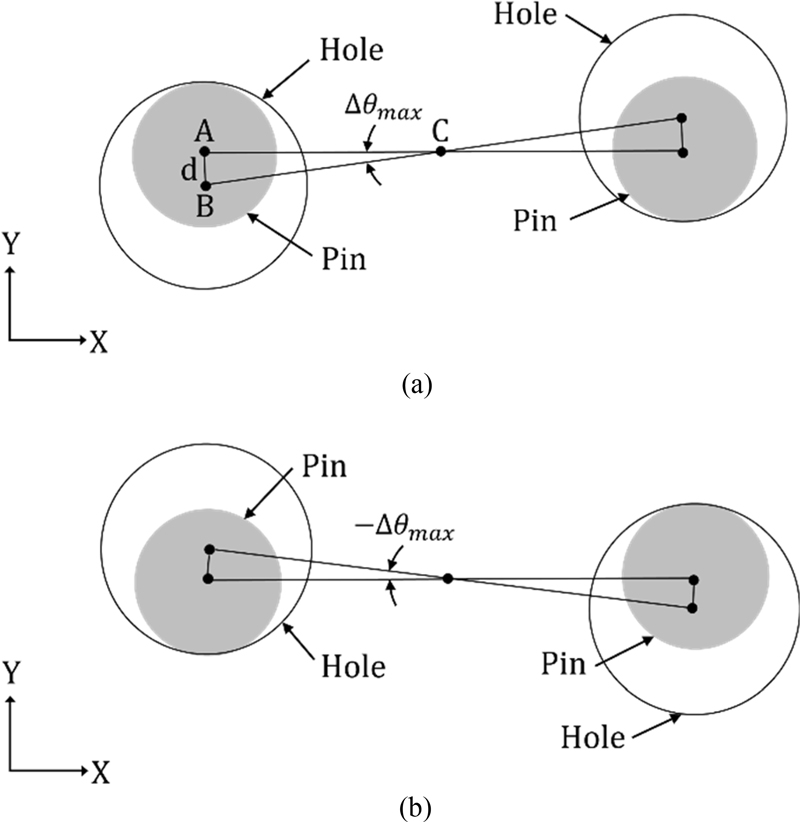
Two cases of extreme rotational float of Part B, rotated about the midpoint between the holes, with LMC holes and LMC pins and no positional errors as in Fig. 5
(5) |
Fig. 7에서 Δθmax = π - 2α = π - 2cos-1(d/L)이고, Fig. 6과 같이 양방향 최대 회전 부동각은 동일하므로 회전 부동 범위의 최댓값은 다음과 같이 구해진다.
(6) |
이 식에 기본 문제의 수치를 대입하면 rθ, max = 3.581o가 된다.
지금까지 고찰한 부동 범위의 최댓값은 하나의 특정 조립품에서 나타날 수 있는 최대 부동 범위를 의미하므로 “제품별 또는 케이스별 최대 부동 범위”라 할 수 있다. 그러나, 대량 생산의 품질 관리에서는 많은 제품에서 일어나는 부동의 산포 전체에서 구한 Δx, Δy, Δθ의 최대 범위(“양산 최대 부동 범위”)가 측정되고 관리된다. 본 연구에서는 대량 생산을 모사하는 몬테카를로(Monte Carlo) 시뮬레이션으로 수치해를 구하고 고찰할 것이므로, 지금부터는 양산 부동 범위를 고려하기로 한다.
양산 최대 부동 범위는 케이스별 최대 부동 범위보다 큰데, 그 이유를 설명하면 다음과 같다. 우선 병진 부동을 살펴보자. Fig. 5와 같이 구멍 직경이 LMC인 상태에서, 두 구멍의 위치 오차가 모두 최대한 우측으로(0.125 mm) 발생한 경우와 최대한 좌측으로(0.125 mm) 발생한 경우를 각각 Figs. 8(a)와 8(b)에 나타냈다. 각 경우에 있어 X 방향 병진 부동만 살펴보면 (a)의 경우에는 Δx = -0.375~0.125 mm가 되고 (b)의 경우에는 Δx = -0.125~0.375 mm가 된다. 따라서 두 경우 모두 케이스별 최대 부동 범위는 rx, max = 0.125 - (-0.375) = 0.375 - (-0.125) = 0.5 mm가 되어 Fig. 5의 경우와 동일하지만, 두 경우를 포함하는 양산에서 구해지는 양산 부동 범위 Rx, max는 Rx, max = 0.375 - (-0.375) = 0.75 mm가 된다. Δy의 양산 최대 부동 범위도 Δx와 마찬가지이므로 Ry, max = 0.75 mm가 된다.
유사한 방법으로, 시계 방향 또는 반시계 방향의 한 방향으로 만 최대 회전이 발생할 수 있는 경우를 고려하여 Δθ의 양산 최대 부동 범위를 구할 수 있다. 지면상 유도 과정은 생략하고, 결과만 쓰면 식(7)과 같고 수치를 대입하면 Rθ, max = 5.3720o 이 된다.
(7) |
이와 같이 얻어진 양산 최대 부동 범위들을 두 개의 상용 공이 상용 툴들은 전 세계 공차해석 프로그램 시장에서 매우 많이 사용되는 신뢰할 수 있는 프로그램이므로, 이 시뮬레이션을 통해 본 논문에서 구한 해석해를 검증할 수 있다. 양산 부동 범위의 최댓값을 수치해로 얻기 위해, 두 소프트웨어의 특수 옵션(예: 극한 분포)을 활용하여 공차 또는 부동 현상의 확률분포를 극한으로 조작하고도 시뮬레이션을 1,000,000회 이상 시행해서야 비로소 Table 1과 같이 해석해에 근사하는 값을 얻을 수 있었다. 이는 이들 최대 부동 범위가 실제로는 거의 발생하지 않는 매우 드문 값이기 때문이다.
3.3 확률 부동 범위
이 절에서는, 앞 절의 최대 부동 범위와 달리 실제 양산에서 관찰될 확률 부동 범위를 살펴보고자 한다. 이를 위해, Fig. 3의 기본 문제에서 크기공차와 기하공차를 실제 문제와 유사하게 정규분포(α 수준은 3으로 설정)로 하고 부동 변위의 확률분포는 균일분포로 하여, 100,000회의 몬테카를로 조립 시뮬레이션을 수행하였다. 그 결과로 구해진 확률 부동 범위(R, prob)를 Table 2에 나타냈는데, 상호 비교하기 쉽게 최대 부동 범위(R, max)와 함께 보였다.

Numerical solutions for maximum and probabilistic float ranges of Δx, Δy, and Δθ in the base problem with two hole-pin pairs
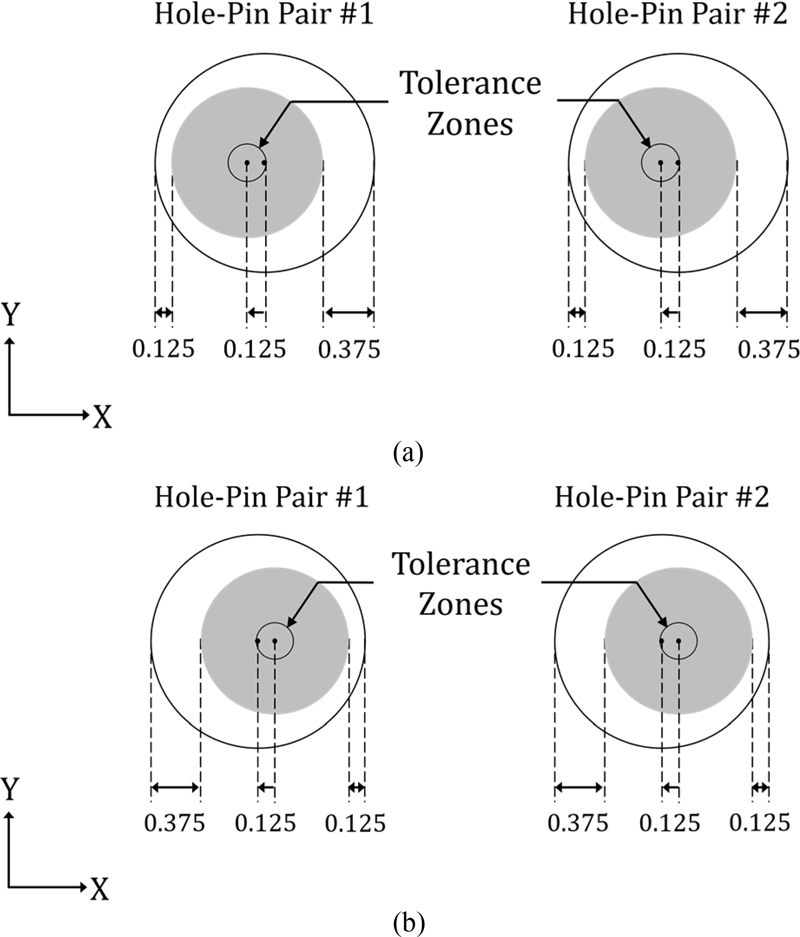
Two extreme cases among mass-produced assemblies, which allow (a) maximum possible negative Δx float and (b) maximum positive Δx float. All numbers in [mm]
Table 2에서 두 소프트웨어로부터 얻어진 수치해가 약간의 차이를 보이는 것은 이들의 알고리즘이 다르기 때문이다. 중요한 것은, 두 소프트웨어 모두 확률 부동 범위가 최대 부동 범위의 2/3 정도에 그치는 결과를 보인다는 점이다. 물론 이 부동 범위 값들은 시뮬레이션 횟수를 늘리면 다소 증가하지만 증가량은 미미하다.
확률 부동 범위가 최대 부동 범위에 비해 현저하게 작은 이유로는 두 가지를 생각할 수 있다. 첫 번째 이유는, 부품 B의 구멍 크기가 정규분포를 가지므로 구멍과 핀 사이 간극이 Fig. 5의 경우보다 현저히 작아 부동이 적게 일어나기 때문이다. 두번째 이유는, 구멍들의 위치가 서로 독립적인 확률분포를 가지므로 이들의 위치가 같은 방향으로 유사 오차를 가질 확률이 낮아 서로 부동을 방해하기 때문이다. 예를 들어, Fig. 9는 두 구멍의 위치 오차가 서로 반대 방향인 경우인데, 두 구멍의 상호 방해로 인해 |Δx|가 0.125 mm를 넘을 수 없음을 알 수 있다.
3.4 부동 감소 방안
만일 Table 2의 확률 부동 범위가 제품의 기능상 허용된다면 괜찮지만, 그렇지 않다면 부동을 줄이기 위한 대책을 강구해야한다. 부동을 줄이기 위한 설계개선 방안은 다양하지만 그중에서 중요한 것 세 가지만 살펴보기로 한다.
첫 번째 방안은 식(3)에 근거하여 핀과 구멍의 크기공차와 위치공차를 줄이는 것이다. 이 방안은 부동의 근본 원인을 억제하므로 당연히 효과가 있겠지만, 공차의 감소는 항상 비용의 증가를 초래하므로 적용하기 어려울 수 있다. 두 번째 방안은 조립 형체를 추가하는 것인데, 산업 현장에서 드물지 않게 사용되는 방법이다. 즉, 두 쌍의 구멍-핀 조립보다 더 많은 조립형체 쌍들이 조립되도록 설계함으로써 조립형체들 사이의 상호 방해로 부동이 적어지게 하는 방법이며, 4장에서 그 효과를 고찰하기로 한다. 세 번째 방안은 과잉제약을 해소하고 적정제약으로 설계함으로써 부동을 근본적으로 줄이는 방법(5장)이다.
4. 조립형체 추가 설계
4.1 조립형체를 추가한 설계안
앞 절에서 설명한 바와 같이, 기본 문제(Fig. 3)에서 발생하는 부동을 줄이기 위해 조립형체를 추가하는 설계안을 고찰해 보자.
본 논문에서 고찰하는 조립형체 추가 설계안은 Fig. 10에 보인 두 가지이다. Figs. 10(a)는 구멍-핀 쌍을 하나 추가한 것이고, 10(b)는 부품 A에 작은 벽을 두 쌍 추가하여 부품 B의 측면들이 이 벽들 사이에 끼워지도록 함으로써 슬롯-탭 쌍을 두 개 추가한 것이다.
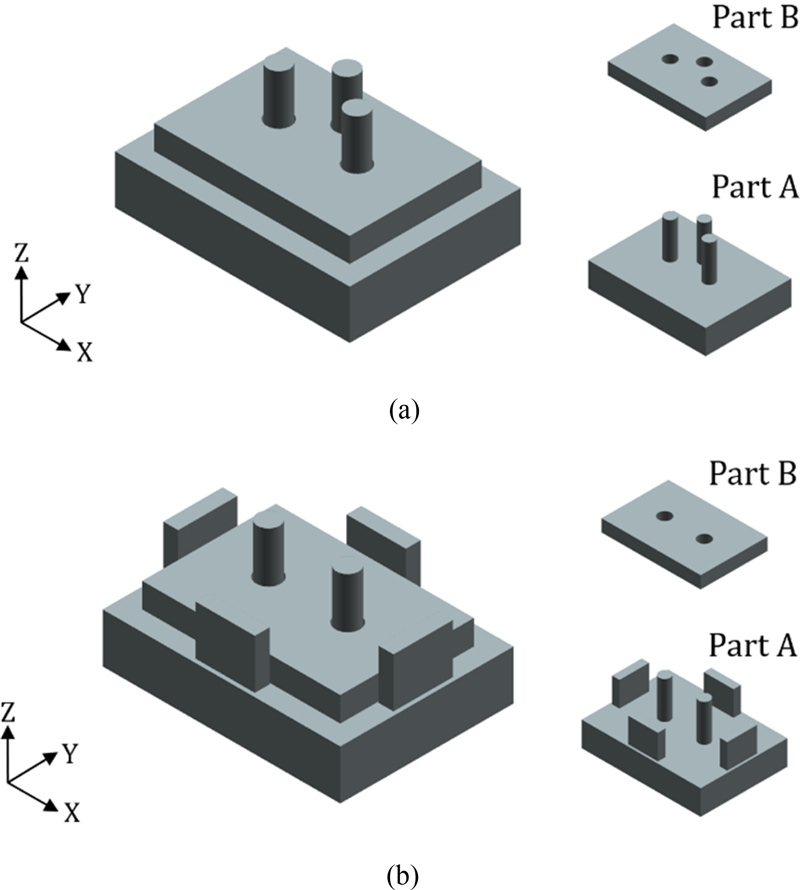
Two example designs obtained by adding extra assembly features: (a) one hole-pin pair added, and (b) two slot-tab pairs added
Fig. 10에 보인 두 가지 설계 변경안에서 추가된 조립형체들도 모두 기본 문제와 마찬가지로 WCB에 근거한 조립보장 방법(2.2절)으로 설계하였다. 이렇게 설계한 도면들이 Fig. 11에 나타나 있다. Fig. 11(b)의 경우, 부품 A에 새로 추가된 슬롯 두 쌍에 크기공차와 위치공차를 부여하였고, 이와 조립되는 부품 B의 탭(판의 가로 길이와 세로 폭)은 공차가 없는 것으로 설계하였으며, 슬롯-탭의 설계에서 WCB를 일치시켰다.
4.2 최대 부동 범위
앞 절에서 설명한 바와 같이 모든 조립형체 쌍의 WCB 크기가 같도록 설계하면, Fig. 11의 각 경우에서 발생할 수 있는 병진 부동 범위의 최댓값은 기본 문제(Fig. 3)에서의 값과 동일하다. 이는 Fig. 12(a)에 보인 바와 같이 모든 조립형체 사이의 간극이 0.25 mm로 동일하기 때문에 X축 방향이나 Y축 방향으로의 최대 병진 부동 범위에 변화가 없기 때문이다.
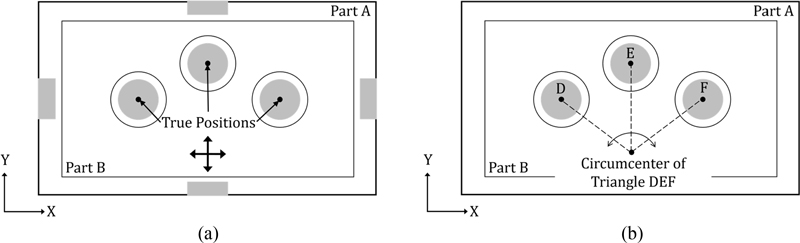
Consideration of maximum float ranges possible in the two designs in Fig. 11, with extra assembly features added: (a) Translational float only and (b) Rotational float only
그러나 회전 부동은 다소 복잡해진다. Fig. 11(a)와 같이 조립 형체가 세 쌍인 경우에는 세 구멍으로부터 동일한 거리만큼 떨어진 점(외심이라 함)이 존재하므로 그 점을 중심으로 하는 회전 부동의 최대 범위는 Fig. 12(b)에 보였듯이 기본 문제의 값과 같을 것이다. 그러나, Fig. 11(b)와 같이 조립형체가 4개 이상이면 (일반적으로 임의의 4개 이상 점으로부터 동일한 거리에 있는 점은 존재하지 않으므로[12]) 회전 부동 범위의 최댓값이 기본 문제의 값보다 작아지게 된다. 이 현상은 본 논문과 관련이 있는 주제이지만, 지엽적이므로 더 깊이 고찰하지 않기로 한다.
4.3 확률 부동 범위
Fig. 11의 두 문제에 대해, 기본 문제와 동일한 방법으로 100,000회 시뮬레이션 하여 확률 부동 범위의 수치해를 구했다. 그 결과를 Table 3에 보였는데, 비교하기 쉽도록 기본 문제의 결과도 함께 표시하였다. Table 3을 보면 조립형체 추가를 통해 어느 정도(2-16%)의 부동 감소 효과를 얻을 수 있음을 알 수 있다. 이는 추가적인 조립형체들의 위치와 크기가 독립적인 확률분포를 가지므로, 어느 한 조립형체 쌍에서 특정 방향으로 큰 부동이 발생하려고 할 때 다른 조립형체 쌍들이 이를 방해하기 때문이다. 이는 기본 문제에서 확률 부동 범위가 최대 부동 범위보다 현저하게 작아지는 이유(3.3절)와 동일하다. 이러한 이유에서 조립형체 쌍이 더 많은 Fig. 11(b)의 경우에 부동 범위가 더 많이 감소한 것으로 추정되나 두 경우의 비교만으로 결론 내리기는 어렵다.
4.4 경제성과 조립 용이성 고찰
Fig. 11의 설계들은 기본 문제(Fig. 3)에 조립형체들을 추가한 것이므로, 소재 및 제작 비용의 증가를 수반할 것이다. 비용의 증가는 공법과 소재 등에 따라 다르므로 정량적으로 논의하기는 어렵다.
한편 조립 용이성은 저하될 수 있다. 그 이유는, 조립형체 쌍의 개수가 많아져서 이들을 모두 맞추기 위한 노력이 필요하기 때문이다. 즉, 조립형체 쌍 사이의 간극이 큰 것은 각 쌍의 조립을 쉽게 해 주지만, 모든 쌍이 조립되는 위치를 찾기 위한 위치 조정 범위를 늘려 조립 작업을 어렵게 할 수 있을 것이다.
5. 적정제약 조립 설계
5.1 적정제약의 구현
지금까지 다룬 모든 설계와 달리, 이 장에서는 과잉제약이 아닌 적정제약 설계를 통해 부동을 줄일 수 있는지 고찰하기로 한다. 구체적으로는 Fig. 13에 보인 바와 같이 기본 문제에서 부품 B의 2개 구멍 중 하나를 슬롯(또는 장공)으로 변경하는 것이다. 이 조립 구조는 대표적인 적정제약 설계 방법이다[2].
Fig. 13에서 두 부품 사이의 자유도 제약을 분석해 보자. 우선 두 부품 사이 면조립에 의해 3개의 자유도가 제약되는 것은 기본 문제와 같다. 이제 구멍-핀 조립과 슬롯-핀 조립을 살펴보자. Fig. 13의 흰색 화살표가 보여주듯이, 구멍-핀 조립 쌍에 의해 X, Y 축 방향 병진 자유도가 제약되고, 슬롯-핀 쌍에 의해서는 Y축 방향 병진 자유도만 제약된다. 여기서 슬롯-핀 쌍에 의한 Y축 병진 자유도 제약은 구멍-핀 쌍 중심의 회전 자유도 제약으로 나타난다. 여기서 중요한 점은, 구멍-핀 쌍과 달리 슬롯-핀 쌍은 X축 방향으로 제약하지 않으므로, 앞의 설계들처럼 X축 방향 자유도가 중복 제약되는 과잉제약은 발생하지 않는다는 것이다. 이는 두 핀 사이의 거리에 오차가 있어도 구멍-핀 조립에 의해 X, Y 위치가 유일하게 정해지고 슬롯-핀 조립에 의해 부품이 Z축 중심으로 회전하면서 그 방향이 유일하게 결정되어 간섭 없이 조립됨을 뜻한다.
5.2 적정제약의 공차설계
Fig. 13의 적정제약 조립에서는 조립형체 쌍 사이의 상호작용에 의한 간섭이 없으므로, 각 핀이 상대방 구멍이나 슬롯보다 작거나 같으면 조립이 보장된다. 그러므로 이 적정제약 설계에서는, 기본 문제에서처럼 구멍 또는 슬롯과 핀 사이에서 WCB를 맞출 필요가 없고 다음의 두 식만 만족시키면 된다.
(8) |
이 식에서 ws, MMC는 슬롯 폭(Width)의 MMC 크기를 나타낸다. 식(8)에서 부등호 각각의 좌우 항 차이가 클수록 부동이 커지므로, 부동을 줄이기 위해 식(8)의 두 부등식에서 등호가 성립하도록 설계하기로 한다. 즉,
(9) |
공정한 비교를 위해, 기본 문제와 동일하게 핀의 크기공차는 0으로 하고 구멍과 슬롯의 크기공차 및 위치공차는 모두 0.25 mm로 정하면, 두 부품의 도면이 Fig. 14와 같이 된다. Fig. 14를 앞의 다른 도면들과 비교해 보면 부품 B의 MMC 구멍 직경이 4.5 mm로서 다른 도면의 4.75 mm보다 작은 것을 알 수 있는데, 이는 과잉제약이 해소됨으로써 구멍과 핀의 MMC 크기를 일치 시킬 수 있었기 때문이다. 그 결과, 조립형체 사이 간극이 작아지므로 부동이 감소하는 효과를 기대할 수 있다.
5.3 최대 부동 범위
적정제약 설계에서 발생하는 케이스별 부동 범위의 최댓값은, 3.2절에서 기본 문제에 대해 수행한 해석과 유사한 방법으로 구할 수 있다. 우선 Δx의 케이스별 최대 유동 범위는, Fig. 15와 같이 구멍의 직경이 최대(LMC)이고 위치오차가 없는 경우에 발생하고 슬롯-핀 쌍은 고려할 필요 없으므로 다음과 같이 된다.
(10) |
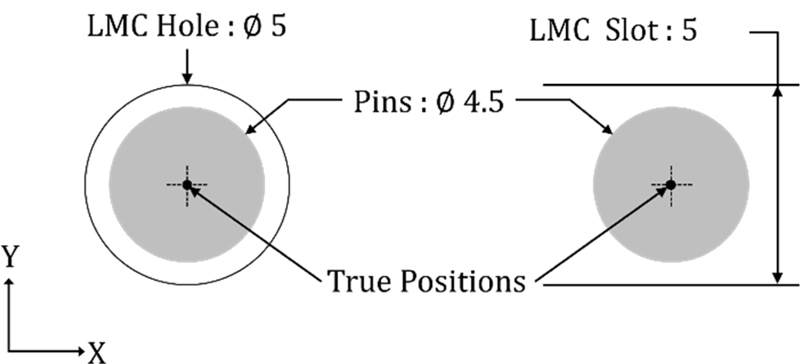
One situation enabling maximum float in the exactly constrained design with a hole-pin and a slot-pin pairs. All numbers in [mm]
식(10)의 유도 과정 중에 식(9)의 첫 번째 등식을 이용하였다. 이 식을 기본 문제에 대한 식(4)와 비교해 보면 X축 방향 부동 범위의 최댓값이 위치도만큼 감소하였음을 알 수 있는데 이 역시 적정제약의 효과이다.
다음으로 Δy의 케이스별 최대 범위는 구멍-핀 간극과 슬롯-핀 간극 중 작은 것에 의해 결정된다.
(11) |
식(10)과 식(11)에 Fig. 14의 수치를 대입하여 케이스별 최대 부동 범위를 구하면 rx,max = ry,max = 0.25 mm가 된다.
Δθ의 케이스별 최대 부동 범위를 유도하기 위해 Fig. 16을 고찰하자. Fig. 16은 Part B가 반시계 방향으로 회전하여 좌측 핀이 구멍에 접하고 우측 핀이 장공에 접하면서 한 방향의 회전 부동이 최대로 발생한 경우이다.
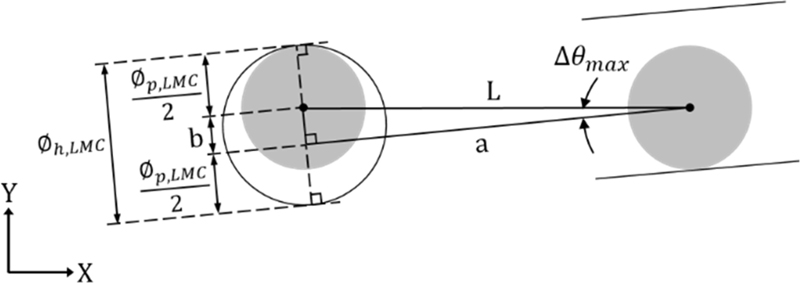
Maximum rotational float of Part B in the exactly constrained design in the situation shown in Fig. 15
두 핀 사이의 거리 L을 장공 면에 나란한 성분(a)과 수직한 성분(b)으로 분해했을 때, 최대 회전 부동은 그림과 같이 b = Φh,LMC - Φp,LMC일 때 발생한다. 따라서 회전에 따른 케이스별 최대 부동 범위는 식(12)와 같이 구해진다. 참고로, 이 문제에서 최대 회전 부동이 발생하는 경우는, 기본 문제와 달리 Part B가 두 핀 사이 중앙점으로부터 좌측으로 조금 이동한(Δx < 0) 상태에서 회전할 때이다.
(12) |
식 (12)에 Fig. 14의 수치를 대입하면 rθ, max = 1.7906o가 된다.
3.2절에서 설명한 방법에 따라, 적정제약 설계의 양산 최대 부동 범위를 구하면 Rx, max = Ry, max = 0.5 mm, Rθ, max = 3.5816o가 된다. 기본 문제와 마찬가지로 두 상용 소프트웨어를 사용하여 양산 부동 범위의 최댓값을 구했으며, 해석해와 유사한 값을 얻었다.
5.4 확률 부동 범위
Fig. 14의 적정제약 설계에서 모든 공차들이 확률분포를 가질때에 발생하는 양산 확률 부동 범위를 두 소프트웨어로 100,000회 시뮬레이션하여 구했다. 그 결과를 Table 4에 나타냈는데, 비교하기 쉽도록 앞의 결과들과 함께 표시하였다.

Comparison of numerical solutions for probabilistic float ranges of Δx, Δy, and Δθ among the base problem, two example problems with extra assembly features added, and the exactly constrained problem
Table 4를 통해 기본 문제의 구멍 1개를 슬롯 형태의 장공으로 설계함에 따라 기본 문제 대비 상당한(19-50%) 부동 감소 효과를 얻을 수 있음을 알 수 있다. 이러한 효과는, 조립형체 간 치수만 맞으면 조립이 보장되는 적정제약 설계의 특징 때문에 부동의 근본 원인인 조립형체 사이 간극이 작아져 발생한 것이다.
5.5 경제성과 조립 용이성 고찰
적정제약 설계에서는 구멍 중 하나를 장공으로 가공해야 하므로, 밀링과 같은 추가 공정이 필요하여 제조 비용이 증가할 것이다. 4장에서 고찰한 설계안들도 비용 증가를 동반하는데, 경제성 관점에서 어느 설계안이 유리할지는 소재, 공작기계, 작업자의 숙련도 등에 따라 달라질 것이다.
적정제약 설계에서는 조립형체 사이의 간극이 비교적 작으므로 조립 공정에서 조금 더 세밀하게 부품의 위치와 자세를 잡아야 한다. 그러나, 조립형체의 수가 적으므로 조립을 위한 노력의 총량은 4장의 경우들과 크게 다르지 않을 것이다.
이와 관련하여, 다수의 구멍과 다수의 핀이 패턴으로 조립되는 일반적인 문제에서 적정제약을 적용하는 방법을 설명하고자 한다. 그 방법은, 많은 구멍 중에서 두 개를 Fig. 14와 같이 구멍과 슬롯으로 설계하고 나머지 구멍들은 여유 있게 큰 확공으로 설계하는 것이다[2]. 이 설계에서 부품 B의 위치와 자세는 Fig. 14와 같이 구멍과 슬롯에 의해 정해지고, 이때 발생하는 부동의 범위 내에서 나머지 확공들은 항상 핀과 쉽게 조립되므로 부동과 조립 용이성 모두 Fig. 14의 설계와 같게 된다. 이 적정 제약 설계에서 확공들은 물론 부품이 분리되지 않도록 하는 볼트 등의 체결에 사용된다.
6. 결론
이 논문은 기계나 제품의 조립에 흔히 사용되는 구멍-핀 패턴 조립 설계를 자유도 제약과 부동 관점에서 심도 있게 고찰한 수치해석 연구이다. 구체적으로 설명하면, 과잉제약인 구멍-핀 패턴의 조립을 위해 구멍을 핀보다 크게 설계함으로써 발생하는 부품 간 부동을 고찰하고, 이를 관리하기 위한 설계 개선 방안들을 비교 연구한 것이다. 본 논문의 수치해석을 위해 두 개의 신뢰도 높은 상용 공차해석 소프트웨어를 사용하였다.
우선 두 쌍의 구멍-핀 조립 문제를 기본문제로 선정하여 이 문제에서 발생하는 부동량을 수치해석으로 구했다. 그리고, 부동을 줄이기 위해 현장 설계자들이 더러 사용하는 첫 번째 개선안으로서, 구멍-핀 패턴이나 슬롯-탭 등 조립형체를 추가하는 방안을 고찰하였다. 본 논문에서 고려한 경우들에서는 이 방안을 통한 부동 개선 효과가 2-16% 정도로 크지 않았고 재료와 가공 공정의 추가를 고려하면 경제적 타당성이 별로 없다고 판단하였다. 두 번째 설계 개선안으로서 구멍 중 하나를 장공으로 변경한 적정제약 설계에서는 부동량이 19-50%까지 감소하는 것으로 나타나, 제작 비용의 증가를 상쇄할 만한 품질 개선으로 경제적 타당성이 있을 것으로 판단하였다. 기본 문제에서 부동이 발생하는 이유가 과잉제약 때문임을 상기할 때, 적정제약 설계가 효과적인 해결책이 되는 것은 논리에 부합하는 것으로 보인다.
본 연구는 구멍-핀 패턴 조립에서 발생하는 부동 현상을 세밀하고 깊게 고찰하였을 뿐 아니라, 적정제약 설계가 부동량 억제에 있어 매우 효과적이고 타당한 방안임을 정량적으로 확인했다는 점에서 기존 연구들과 차별화되는 실용적 가치를 갖는다. 본 논문의 연구 결과가 구멍-핀 패턴의 조립을 포함하는 많은 설계에서 제품의 기하품질을 개선하는데 기여하기를 기대한다.
NOMENCLATURE
ΔΦh/p : | Size Tolerance of Hole/Pin |
Φh/p, WCB : | Worst Case Boundary Diameter of Hole/Pin |
Φh/p, MMC : | Maximum Material Condition Diameter of Hole/Pin |
Φh/p, LMC : | Least Material Condition Diameter of Hole/Pin |
rx/y,max : | Maximum Case-specific Float Range of x or y Displacement |
rθ,max : | Maximum Case-specific Float Range of Rotation |
Rx/y,max : | Maximum Float Range of x or y Displacement in Mass Production |
Rθ,max : | Maximum Float Range of Rotation in Mass Production |
Rx/y,prob : | Probabilistic Float Range of x or y Displacement in Mass Production |
Rθ,prob : | Probabilistic Float Range of Rotation in Mass Production |
TOP : | Tolerance of Position |
ws : | Width of Slot |
Acknowledgments
이 논문은 2022학년도 홍익대학교 학술연구진흥비에 의하여 지원되었음.
REFERENCES
- Yim, H., (2024), GD&T ASME Y14.5-2009: Systematic and logical illustration and applications, PubPle.
- Whitney, D. E., (2004), Mechanical assemblies: their design, manufacture, and role in product development, Oxford University Press.
-
Skakoon, J. G., (2009), Exact constraint, Mechanical Engineering, 131(9), 32-36.
[https://doi.org/10.1115/1.2009-SEP-2]
-
Lee, S., Yi, C., (1996), Statistical tolerance and clearance analysis for assembly, Proceedings of IEEE/RSJ International Conference on Intelligent Robots and Systems, 688-695.
[https://doi.org/10.1109/IROS.1996.571038]
-
Teissandier, D., Couetard, Y., Gerard, A., (1999), A computer aided tolerancing model: proportioned assembly clearance volume, Computer Aided Design, 31(13), 805-817.
[https://doi.org/10.1016/S0010-4485(99)00055-X]
-
Zhu, J., Ting, K.-L., (2000), Uncertainty analysis of planar and spatial robots with joint clearances, Mechanism and Machine Theory, 35, 1239-1256.
[https://doi.org/10.1016/S0094-114X(99)00076-2]
- Wittwer, J. W., Howell, L. L., Chase, K. W., (2001), Modeling the effects of joint clearances in planar micromechanisms, Technical Proceedings of the 2001 International Conference on Modeling and Simulation of Microsystems, 374-377.
- Kim, Y.-N., Yoon K.-H., Chang S.-H., (2005), The tolerance stack analysis of the model involving position tolerance, Journal of the Korean Institute of Industrial Engineers, 31(1), 36-43.
-
Polini, W., (2014), To model joints with clearance for tolerance analysis, Proceedings of the Institution of Mechanical Engineers, Part B: Journal of Engineering Manufacture, 228(12), 1689-1700.
[https://doi.org/10.1177/0954405414522610]
- Kim, J., (1999), Mechanical Engineering Drawing – Foundation for Creative Development of New Products, 4th ed., Moonwoondang.
- ASME, (2009), Y14.5-2009 Dimensioning and Tolerancing: Engineering drawing and related documentation practices.
- Mathematics, How to find equidistance from 4 points. https://math.stackexchange.com/questions/1797397/how-to-find-equidistance-from-4-points
B.S. student in the Department of Mechanical and System Design Engineering, Hongik University. His research interest is Design and Materials.
E-mail: jhlee0721@g.hongik.ac.kr
Professor, Department of Mechanical and System Design Engineering, Hongik University. His research interests include geometric quality, dimensional engineering and management, geometric dimensioning and tolerancing, and mechanical design.
E-mail: hjyim@hongik.ac.kr