
순차 이송형 유리 성형 공정의 다단 냉각 조건에서 렌즈 내부 온도 및 응력 분포 연구

Copyright © The Korean Society for Precision Engineering
This is an Open-Access article distributed under the terms of the Creative Commons Attribution Non-Commercial License (http://creativecommons.org/licenses/by-nc/3.0) which permits unrestricted non-commercial use, distribution, and reproduction in any medium, provided the original work is properly cited.
Abstract
Glass Molding Process (GMP) is an effective method for producing precise optical elements such as lenses. This simulation study aimed to predict the distribution of temperature and stress within a lens during a multi-stage cooling process of GMP. To develop an accurate simulation model including molds and lens, thermal contact conductance and boundary conditions were determined by analyzing experimental and simulation results. The developed model was used to investigate changes in temperature and maximum principal stress within the lens, considering variations in cooling time, speed, and method at each cooling stage. Simulation results indicated that trends of maximum temperature difference and maximum principal stress within the lens were consistent over time. Results also showed that the maximum principal stress inside the lens increased significantly with additional cooling after uneven temperature distribution caused by a relatively short cooling time. Compared to simulation results of the cooling process involving contact only with bottom surface of the mold, contact cooling with both top and bottom surfaces showed decreased residual stress at the end of cooling and maximum temperature difference within the lens. However, the maximum principal stress could be higher during the cooling process involving both surfaces.
Keywords:
Finite element analysis, Glass molding process, Process variable, Thermal contact conductance, Heat transfer distribution, Stress distribution키워드:
유한요소해석, 유리성형공정, 공정 조건, 열 접촉 컨덕턴스, 열전달 분포, 응력 분포1. 서론
유리 재료 성형 방법 중 하나인 GMP 공정은 Glass Molding Process의 약자로, 정밀 가공된 금형 사이에 유리 소재를 위치시킨 후 가열, 가압, 냉각 과정을 통해 원하는 형상의 유리 제품을 정밀하게 성형하는 공정이다[1]. GMP 공정은 단일 스테이지에서 가열, 가압, 냉각이 모두 이루어지는 일괄처리(Batch) 방식과, 일정한 온도 및 압력으로 설정된 다중 스테이지에 렌즈가 위치된 금형을 이송하며 성형이 진행되는 순차 이송형(Progressive) 방식으로 구분된다[2]. 순차 이송형 GMP 공정의 경우, 각 공정 단계의 성형 조건에 대한 개별적인 제어가 가능하여 고품질의 렌즈를 얻을 수 있으며, 다수의 렌즈를 연속적으로 성형하므로 높은 생산성을 갖는다.
GMP 공정에 관한 연구는 다양하게 진행되었다. Seo 등은 방열 블록 형상에 따른 금형 가열부 열전달 특성 및 에너지 소비에 대해 해석적 및 실험적 연구를 수행하였다[3]. Choi 등은 대구경 비구면 유리렌즈에 영향을 미치는 성형 공정 변수를 선정하고, 이에 따른 렌즈 잔류 응력을 예측하였으며, 온도 및 압력에 따라 변화하는 잔류응력 분포를 비교하여 냉각 속도가 잔류 응력에 상당한 영향을 주는 것을 확인하였다[4]. Li 등은 순차 이송형 GMP 공정에서 압축 과정에 대한 실험 및 시뮬레이션 연구를 진행하였으며, 이를 통해 압축 과정에서 마찰 계수 변화에 따른 하중 변화 및 배럴링 형상을 예측하였다[5]. Chang 등은 정밀 유리 렌즈 성형 공정 가압 및 냉각 과정에서 유리 렌즈의 잔류 응력에 대한 연구를 진행하였고, 구조 완화를 반영한 해석과 렌즈 성형 실험을 통해 성형된 유리 렌즈의 잔류 응력을 측정하여, 냉각 속도가 증가함에 따라 잔류 응력이 증가하는 임계 냉각 속도가 존재함을 규명하였다[6]. Vu 등은 유리 성형 공정 가열 및 가압 과정에 대한 실험 및 시뮬레이션을 통한 가열 시간 및 가압 하중 등의 예측에 대한 연구를 수행하였고, 시뮬레이션을 통해 예측된 최소 가열 시간 및 압축 하중은 실험 결과와 잘 일치함을 보였다[7].
GMP 공정 과정에서 렌즈 내부의 온도와 응력 분포에 대한 연구도 존재한다. Yan 등은 렌즈 성형을 위한 프리폼을 적외선 복사 방법으로 가열하는 공정에서 렌즈 내부의 온도와 응력 분포를 FEM 방법으로 시뮬레이션하여 그 결과를 고찰하였다[8]. Zhou 등은 일괄처리 방식의 GMP 전체 공정에 대한 FEM 시뮬레이션을 수행하였으며, 성형된 렌즈를 서냉하는 어닐링 과정에서 렌즈와 금형의 온도와 응력 분포, 렌즈의 부피 변화에 대한 결과를 제시하였다[9].
이외에도 GMP 공정에 대한 연구로는 성형 과정에서 응력해석 이론에 대한 연구[10,11], 가열 방법에 대한 연구[12-14], 성형에 사용되는 금형의 재료와 제작 방법에 대한 연구[15-17], 공정 변수 및 제어에 관한 연구[18-20] 등이 존재한다.
이러한 많은 연구에도 불구하고, GMP 공정 과정에 대해 제한적인 연구가 수행된 분야가 존재한다. 이러한 연구 분야의 예로는 금형과 성형 장치에서의 열 접촉 컨덕턴스에 대한 연구와 순차 이송형 방식의 GMP 냉각 공정에서 렌즈 내부 온도와 응력 분포에 관한 연구가 있다.
GMP 공정에서 가열과 냉각 과정은 매우 중요하며, 이러한 가열과 냉각 속도는 열전달과 관련된 고체면의 접촉부가 갖는 열 접촉 컨덕턴스에 따라 크게 달라진다. 특히, 금형과 이에 접촉하는 성형 장비의 가열부 및 냉각부 표면 사이와 금형과 렌즈 접촉면 사이 열 접촉 컨덕턴스를 정확히 고려하는 것은 GMP 공정 해석의 정확도를 높이는 데 중요하다. 하지만 지금까지 수행된 많은 GMP 공정 해석 논문에서 열 접촉 컨덕턴스 값은 기존 연구에서 제시한 값을 사용하는 경우[8,9,22]가 대부분이며, 이러한 접촉부의 열 접촉 컨덕턴스가 공정 해석에 미치는 영향에 대한 연구는 매우 제한적인 상황이다.
또한 순차 이송형 GMP 냉각 공정에서 렌즈 내부 온도와 응력분포에 대한 연구도 부족하다. 앞서 언급한 것과 같이 단일 스테이지의 냉각 과정에서 금형과 유리 렌즈 내부에서 온도와 응력분포에 대한 기존 연구[9]는 존재한다. 하지만, 높은 생산성을 갖는 순차 이송형 방식의 GMP에서는 각 스테이지의 냉각 조건 변화에 따라 렌즈 내부에서의 온도와 응력의 변화가 크고, 제품의 품질에 큰 영향을 줄 수 있음에도 이에 대한 연구는 거의 없는 상황이다.
따라서, 본 연구에서는 위에서 설명한 두 가지 주제에 대한 연구를 수행하고자 하였다. 먼저, 순차 이송형 GMP 장비를 모사할 수 있는 실험 장치를 구축하고, 다단의 냉각 공정을 구현하여 냉각 조건에 따른 금형 코어 내부 온도를 실험적으로 측정하였다. 이후, 냉각 공정을 FEM 방법으로 시뮬레이션 하고, 그 결과를 측정된 온도와 비교하여 실험적인 온도 변화 경향을 예측할 수 있는 열 접촉 컨덕턴스 값을 도출하였다. 또한 냉각 조건을 적용함에 있어 1단 또는 다단의 공정에서 렌즈 내부 온도와 응력의 분포를 시뮬레이션 하였다. 이를 통해 냉각 과정에서 발생하는 렌즈 내부의 응력을 특정 값 이하로 유지하면서, 공정별 시간을 줄여 생산성을 높일 수 있는 냉각 공정 조건을 제시하였다. 추가적으로 각 단계별 냉각 온도와 냉각 시간 그리고, 냉각을 위한 가열블록 접촉 여부가 렌즈 내부의 온도와 응력 분포에 미치는 영향을 고찰하였다.
2. 금형 형상 정보와 실험 장치 및 조건
2.1 금형 형상 정보
Fig. 1은 본 연구에서 사용된 금형의 외형 이미지와 1/4 단면 구조도이다. 금형은 하부 코어(A), 슬리브(B), 상부 코어(C)로 구성되었다. 정밀 가공된 비구면 곡면을 가지는 상부 코어와 하부 코어 사이에 렌즈가 위치하고, 이를 슬리브(B)가 감싸는 형태이다. 냉각 공정을 모사하기 위한 실험은 성형이 완료된 렌즈를 장착한 상태로 진행되어 렌즈와 금형은 거의 빈틈없이 밀착하여 접촉되고 있다고 가정할 수 있다. 사용된 유리 렌즈의 직경은 82 mm이다. Fig. 1(b)의 하부 코어(A)와 상부 코어(C)의 재료는 실제 금형에서는 탄화 텅스텐(WC)이지만, 본 냉각 공정 모사 실험에서는 가공의 용이성을 위해 열물성이 유사한 황동 재질로 제작되었다. 슬리브(B)와 렌즈의 재질은 실제 성형에서 사용되는 동일 재료가 적용되었다. Fig. 1(b)에서 보여주는 것과 같이 하부 코어(A), 슬리브(B), 상부 코어(C)에는 온도 측정용 열전대 삽입을 위한 직경 1 mm 구멍 (LC), (SL), (UC)가 가공되었다. 구멍 (LC)와 (UC)는 하부 및 하부 코어 내부의 온도를 측정하기 위해 코어 측면에서 각각 15와 10 mm 깊이로 가공되었으며, 구멍(SL)은 슬리브의 온도를 측정하고, 렌즈 측면 표면과 접촉하기 위해 슬리브를 관통하는 구멍이 가공되었다. 코어와 슬리브의 열전대 접촉면에는 정확한 온도 측정을 위해 Thermal Grease를 도포하여 접촉으로 인한 열저항을 최소화하였다.
2.2 냉각 공정 모사 실험 장치 및 실험 조건
본 연구에서는 금형에 대한 열 접촉 컨덕턴스를 도출하기 위해 냉각 공정 모사를 위한 실험 장치를 제작하였으며, Fig. 2는 실험 장치의 사진과 구성도를 보여준다. 실제 순차 이송형 GMP 공정장비는 모델에 따라 다르지만 가열, 성형, 냉각 공정을 위해 약 10개 내외의 다중 스테이지로 구성되어 있다. 본 연구에서는 실험실에서 일부 공정만을 모사하기 위해 3개의 스테이지로 구성된 실험 장치를 제작하였다.
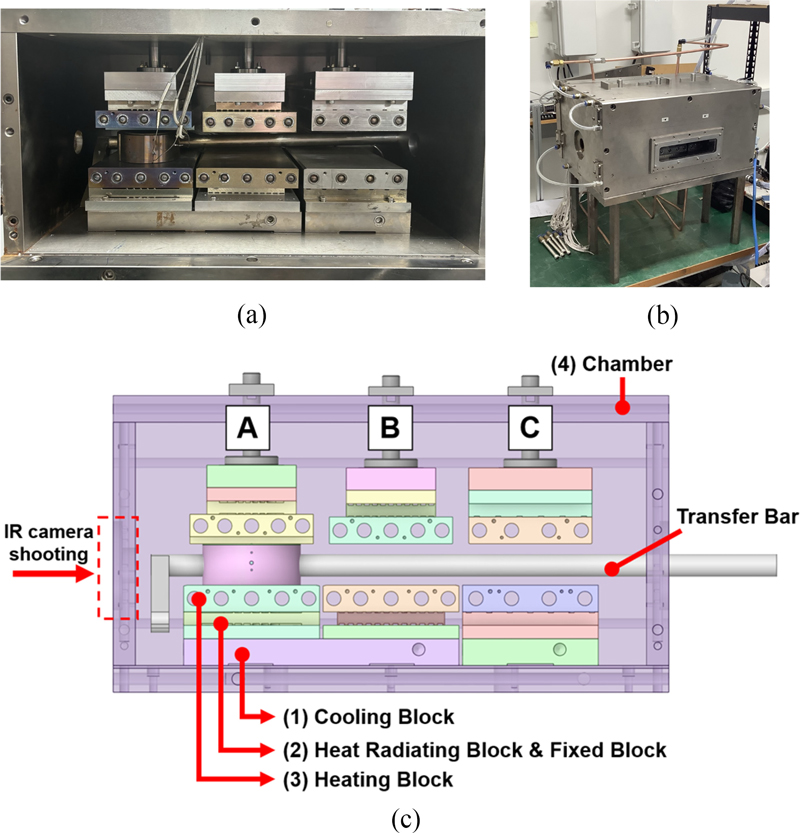
Photograph and schematic of experiment facility: (a) Photograph of the inside of experiment facility, (b) Photograph of the outside of experiment facility, and (c) Schematic of experiment facility
Fig. 2(c)와 같이 실험 장치는 3개의 공정 스테이지 A, B, C로 구성되어 있으며, 각 공정 스테이지는 금형의 가열과 냉각을 위한 상부와 하부 어셈블리를 갖는다. Fig. 2(c)는 상부 및 하부 어셈블리가 냉각블록, 방열 및 고정 블록, 가열블록으로 구성되어 있으며, 금형은 각 상부 및 하부 어셈블리의 가열블록 사이에 위치하고 있음을 보여준다. 냉각블록 내부에는 냉각수 유로가 가공되어 있어 냉각수에 의한 냉각이 수행된다. 가열블록에는 카트리지 히터가 삽입되어 있으며, 히터의 발열량을 제어하여 금형에 가해지는 공정 조건을 유지하도록 한다. 실험 장치 내부 공간에는 외부에서 지속적으로 질소를 공급하여 고온으로 인한 내부 구성품의 산화를 방지하도록 하였다. 장치 내부 공간에는 T형 열전대를 설치하여 온도를 측정하고 이를 해석 과정의 경계조건 입력에 반영하였다.
본 연구에서는 전체 공정 중 냉각 과정을 모사하기 위한 실험이 진행되었다. 일반적인 GMP 공정의 경우, 유리를 유리 전이 온도 이상으로 가열한 후 성형 단계에서 가압하여 원하는 형상으로 성형한다. 이후 성형이 완료된 유리를 단계별로 냉각시켜 공정을 완료한다. 본 연구에서는 가압 성형 단계에서 금형 내부의 렌즈 변형이 완료되고 약간 냉각되어 유동성을 나타내지 않는 완전한 고체 상태의 유리 렌즈가 다음 냉각 시작 단계로 이송된 이후의 과정을 실험으로 구현하였다. 실험에서 사용한 유리 소재는 D-ZLaF52LA이며 해당 소재의 유리 전이 온도는 546oC이다. 이러한 냉각 과정을 모사하기 위해, 먼저 스테이지 A에서 유리 전이 온도보다 낮은 500oC를 유지하는 가열블록에 의해 렌즈를 포함한 금형이 일정한 온도로 가열된다. 가열블록의 온도는 가열블록에 삽입된 K형 열전대에 의해 측정되고 이를 유지하도록 히터가 제어된다. 이후 냉각을 위해 금형이 스테이지 B로 이송막대에 의해 이동하게 된다. 이때 스테이지 B의 가열블록 온도는 460ºC로 유지된다. 냉각된 금형과 내부 유리렌즈는 다음 단계의 냉각을 위해 가열블록 온도가 200ºC로 유지되는 스테이지 C로 이송되어 추가적인 냉각이 진행된다. 냉각 실험 과정에서 금형 윗면은 상부 가열블록과 접촉하지 않고 약 1 mm 정도의 매우 작은 간격을 유지하도록 하였다. 이는 상부 표면과 접촉으로 인해 발생하는 힘에 의해 냉각과정에서 렌즈의 파손을 방지하기 위함이며, 이러한 간격의 유지는 실제 GMP 공정에서도 적용되고 있다.
위에서 설명한 실험 과정에서 Fig. 1(b)의 (LC), (SL), (UC) 지점에서 과도상태 온도가 삽입된 K형 열전대에 의해 측정되고, 금형에 관련된 열 접촉 컨덕턴스를 시뮬레이션 결과와의 측정 온도와의 비교를 통해 구하였다. 실험에서 사용된 K형 및 T형 열전대의 측정 범위와 오차는 Table 1에 제시되었다.
3. 해석 방법 및 경계조건
실험에서 가열블록의 온도가 실험 조건이므로, 해석은 Fig. 3과 같이 상부 및 하부 가열블록, 금형 및 금형 내부의 렌즈에 대해 수행되었다. 해석은 상용 프로그램인 ANSYS Workbench 2023 R2를 활용한 과도 열전달 조건으로 수행되었다. 해석을 위해 적용된 재료는 실험 결과와의 비교를 위해 동일한 재료로 고려되었다. 각 부분의 재질은 가열블록과 슬리브는 SS 304, 상부와 하부코어는 Brass (UNS C36000), 렌즈는 D-ZLaF52LA이다. 각 재질의 100oC에서 물성값은 Table 2에 제시되었으며, 온도에 따른 물성치 변화도 해석 과정에 고려되었다[21-23].
실제 유리 성형 공정에서 유리는 유리전이 온도 이상으로 가열된 후 냉각된다. 이 과정에서 유리 렌즈는 완화 현상을 겪으며 비정질 구조가 안정화되고 내부 구조 및 물리적 특성이 변화한다. 기존의 유리 성형 공정 FEM 해석 논문들은 유리 응력 완화 모델을 통해 이러한 특성을 반영하여 성형 공정을 분석하였다[4,5,9,18,19]. 그러나, 본 연구에서는 유리 전이 온도 이하에서 냉각 과정을 분석하였다. Liu 등의 연구에 따르면 유리전이 온도 부근에서 열팽창계수 및 영률 등의 물성치는 급격하게 변화하지만, 유리전이 온도 이하에서는 열팽창 계수가 거의 일정하고 영률은 완만하게 변화한다[24]. 따라서 본 연구에서는 유리 응력 완화 모델을 반영하지 않고, 열팽창 계수는 일정하게 가정하되 Young’s Modulus가 온도 범위 75-574oC에서 감소(100.34-114.76 GPa)하는 특성을 반영하여 해석하였다.
냉각 공정에 대한 정확한 열전달 해석을 위해서는 금형과 관련된 대류 및 복사 열전달, 가열블록 온도 조건, 금형 및 블록의 열 접촉 컨덕턴스 등의 경계조건을 실제 공정과 유사하게 고려해야한다. 금형 상부 표면에서 복사 열전달이 발생할 경우 경계조건은 관련 문헌을 참고하여 방사율 0.45, 복사 주변 온도는 상부 가열 블록 표면 온도로 입력되었으며 [25-27], 금형 측면 표면에서 대류 열전달 경계 조건은 자유대류 조건으로 고려하여 Churchill 등의 상관식(식(1))으로 계산 후 입력하였다[28]. 계산된 대류 열전달 계수 범위는 7.33-9.23 W/m2·K였으며, 기존 금형 가열부에 대한 연구[3]에서 제시한 3.72-12.3W/m2·K 내에 그 값이 존재하고 있어 적절한 대류 열전달 계수를 고려하고 있음을 확인하였다.
(1) |
본 연구의 해석에서는 렌즈가 가열 및 가압으로 변형이 완료되고, 금형과 렌즈가 일정 온도로 유지된 후, 다중 스테이지에 의한 냉각이 진행되는 공정을 모사하였다. 따라서 초기 조건은 냉각 시작 시점에서 금형과 가압에 의해 변형 완료된 렌즈 내부의 온도가 일정하다고 가정하였다.
순차 이송형 GMP 공정에서 금형은 냉각을 위해 상부 및 하부 가열블록이 일정한 온도로 제어되는 스테이지로 이송되므로, 각 스테이지의 냉각 시작 시점의 온도 경계조건은 가열블록 표면이 각 공정에서 주어진 온도로 일정하다고 고려된다. 이는 표면에 가까운 가열블록에 삽입된 열전대에 의해 온도가 제어되는 장비의 운전방식을 고려해 본다면 타당한 경계조건이라 할 수 있다. 첫 번째 냉각 공정에서 정해진 시간 동안 과도 열전달 해석된 금형과 내부 렌즈는 추가적인 냉각을 위해 다음 스테이지로 이동하게 되는데, 이때 다음 냉각 공정을 위한 온도 경계조건 역시 해당 공정에서 가열블록 표면온도가 일정하다고 가정하였다. 첫 번째 냉각 공정의 해석 결과에서 금형과 렌즈 내부에서 온도와 응력은 일반적으로 불균일하게 분포한다. 이러한 조건은 다음 단계 냉각의 초기 조건으로 고려되어 최종 해석 결과에 영향을 미치게 된다.
4. 열 접촉 컨덕턴스(TCC) 해석 결과
금형 및 블록의 다양한 접촉면에는 열전달에 대한 접촉 열저항 발생하며, 이는 기존의 연구에서 단위 면적당 열 접촉저항의 역수인 열 접촉 컨덕턴스(Thermal Contact Conductance, TCC[W/m2·K])로 고려되고 있다. Fig. 1이 보여주는 것과 같이 본 연구에서 고려된 금형의 경우 상부코어, 하부코어, 렌즈 사이에 각각 면 접촉하는 부위와 Fig. 3의 하부 가열블록과 금형의 하부 코어, 하부 가열블록과 슬리브와 접촉면에서 열 접촉 컨덕턴스가 존재하게 된다. 본 연구에서는 Yan 등이 수행한 웨이퍼 유리 성형 공정 시뮬레이션에서 제시한 금형 내부 열 접촉 컨덕턴스값으로[8] 모든 열 접촉 컨덕턴스가 일정하다고 초기 가정하였으며, 실험을 통한 금형 온도 측정값과 비교를 통해 수정되었다.
본 연구에서 고려해야 하는 열 접촉 컨덕턴스는 Table 3에서 정리한 것과 같이 총 7개이며, 모든 값을 시뮬레이션을 통해 구하는 것은 매우 어렵다. 따라서 금형 내부 반경 방향 열전달에 관여하는 열 접촉 컨덕턴스(슬리브와 상하부 코어 및 렌즈와 접촉면), 금형 내부 축 방향 열전달에 관여하는 열 접촉 컨덕턴스(상하부 코어와 렌즈의 접촉면), 냉각이 발생하는 하부 가열블록과 금형 사이 열 접촉 컨덕턴스(하부 가열블록과 하부 코어 및 슬리브와 접촉면)의 3개 그룹으로 컨덕턴스 값을 구분하였다. 3개 그룹의 열 접촉 컨덕턴스값을 300에서 500까지 25 W/m2·K 단위만큼 변경하며 반복 해석을 진행하였다.
해석 과정에서 Fig. 1의 (LC) 하부코어 온도, (SL) 슬리브 온도, (UC) 상부코어 온도를 각각 예측하였고, 그 결과를 실험에서 측정 온도와 비교하였다. Fig. 1 (LC), (SL), (UC)지점의 측정 및 예측 온도의 비교 결과는 Fig. 4에 제시되었다. 이러한 비교를 통해 측정 온도와 예측 온도가 최소의 차이를 보이는 열접촉 컨덕턴스 값을 구하였고, 결과는 Table 3과 같다.
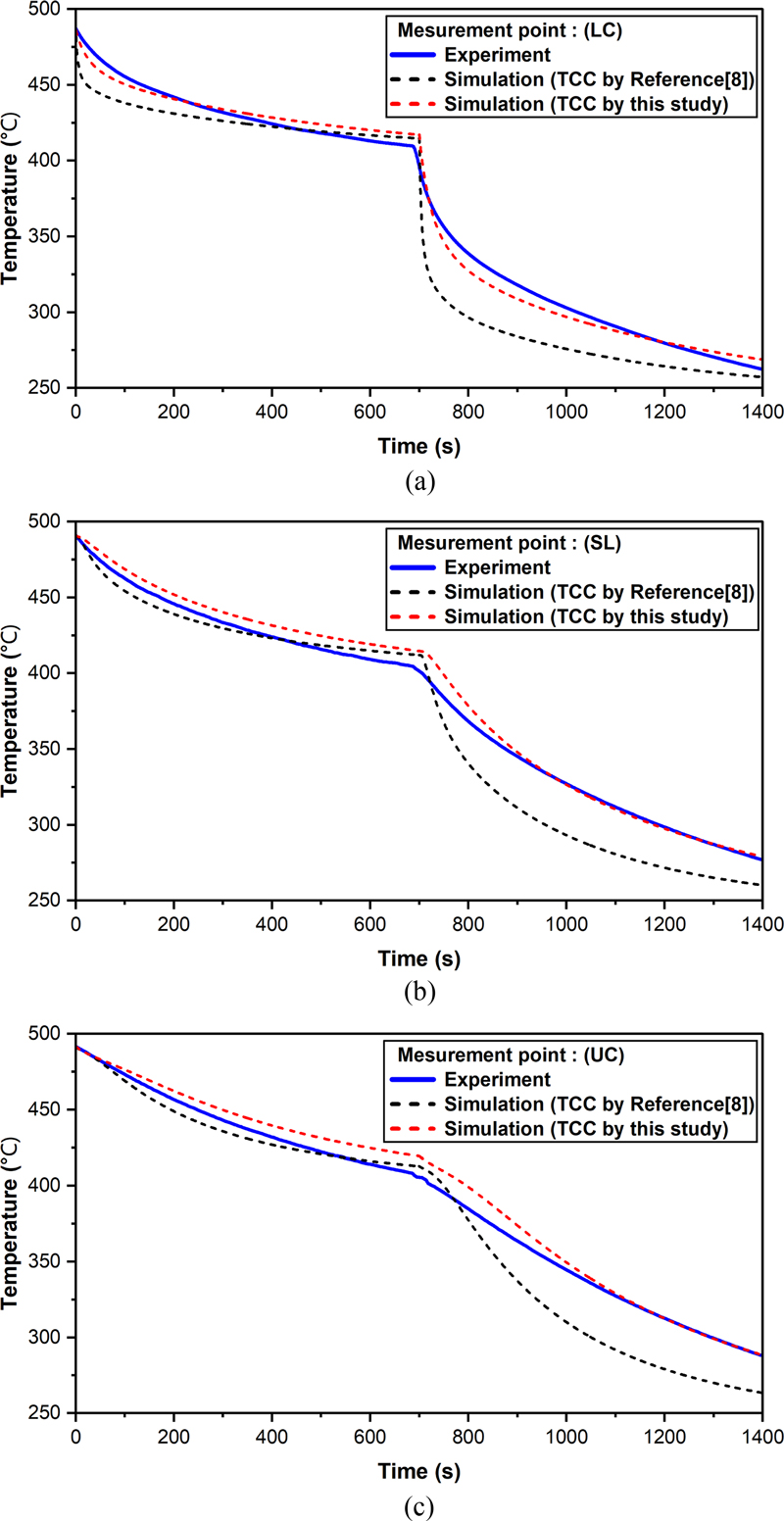
Experimental and numerical temperature comparison (a) Lower core temperature comparison, (b) Sleeve temperature comparison, and (c) Upper core temperature comparison
수치해석은 냉각 실험 조건과 동일한 경계조건으로 수행되었다. 따라서, 첫 번째 냉각 공정 단계에서 500ºC의 일정한 초기 온도를 갖는 금형 및 내부 유리 렌즈에 냉각을 위한 가열블록의 온도를 460ºC로 일정하게 유지한 상태로 700 s 동안 냉각을 수행하는 조건을 고려하였다. 두 번째 단계 냉각 공정은 200ºC를 유지하는 가열블록 온도 조건에서 700 s 동안 냉각하는 공정을 시뮬레이션하였다.
Fig. 4에서 검은색 점선의 시뮬레이션 결과는 모든 열 접촉 컨덕턴스 값을 기존 연구[8]에서 제시한 2,800 W/m2·K 으로 입력한 해석 결과이며, 특히 두 번째 냉각 공정에서 실험 결과보다 훨씬 빠른 냉각 속도 경향을 보여주고 있다. 이는 기존 연구의 열 접촉 컨덕턴스 값이 본 실험에서 존재하는 값에 비해 더 크다는 것을 보여준다. 이러한 열 접촉 컨덕턴스의 차이는 금형에 가해지는 압력의 차이에 의한 것으로 판단된다. 기존 연구는 성형을 위한 가압 조건을 포함한 해석이므로 열 접촉 컨덕턴스 역시 가압 조건의 값을 고려하였다. 반면, 본 실험에서 냉각은 가압이 없는 금형의 하부 가열블록과 접촉에 의한 냉각을 고려하는 공정이므로, 금형 및 가열블록과의 접촉 부에서 더 작은 열 접촉 컨덕턴스 값을 갖게 된다.
Fig. 4는 1의 (LC), (SL), (UC) 지점에서 측정된 온도와 시뮬레이션 예측 온도의 비교 결과를 보여준다. 본 연구에서 구한 열접촉 컨덕턴스 값을 적용한 시뮬레이션 결과는 (LC), (SL), (UC) 지점에서 실험 결과와 비교하여 각각 21.7, 16.6, 14.6oC의 최대 온도 차를 보여준다. 반면, 기존 문헌[8]의 값을 적용한 결과는 동일 지점에서 실험결과와 최대 온도 차가 각각 49.7, 34.4, 35.8oC였다. 이는 본 연구에서 구한 열 접촉 컨덕턴스를 적용한 경우 실험과 시뮬레이션 결과의 최대 온도 차를 51.7에서 59.2% 감소시켜 더 정확한 온도의 예측이 가능함을 보여준다.
시뮬레이션 결과로 얻은 열 접촉 컨덕턴스 값은 Table 3에서 보여주는 것과 같이 375에서 500 W/m2·K으로 기존 연구[8]에서 고려한 열 접촉 컨덕턴스 값인 2,800 W/m2·K에 비해 13.4에서 17.9% 정도의 값을 보여준다. 가해지는 압력의 크기에 따라 열 접촉 컨덕턴스 값이 10배 정도의 차이를 보이는 기존 문헌[27]의 결과를 고려한다면, 본 연구가 제시하는 열 접촉 컨덕턴스 값은 타당한 범위 내에 존재함을 알 수 있다. 계산된 접촉 컨덕턴스 값은 추가적인 렌즈 내부 온도와 응력 분포 해석에서 입력 값으로 고려되었다.
Fig. 4에서 첫 번째와 두 번째 단계 냉각 공정에서 예측 온도의 변화 경향을 보면, 고려된 열 접촉 컨덕턴스 값에 따른 측정 온도와의 차이가 두 번째 냉각 공정에서 두드러지게 나타남을 알 수 있다. 이는 두 번째 냉각 공정의 냉각 속도가 첫 번째에 비해 훨씬 빠르기 때문이다. 이러한 결과는 냉각 속도가 빠른 공정에서 적절한 열 접촉 컨덕턴스 고려가 과도 열전도 해석 및 정확한 온도 변화 예측에 더욱 중요하다는 것을 보여준다.
5. 렌즈 내부 온도 및 응력 분포 조건 및 해석 결과
5.1 열전달-구조 연계 해석 방법 및 해석 조건
본 연구의 주요 목적 중 하나는 순차 이송형 GMP 공정에서 생산성 향상을 위해 냉각 공정 시간을 되도록 줄이면서, 냉각 과정 중 렌즈 내부에 발생하는 응력이 특정 값을 초과하지 않는 공정 조건을 제시하는 것이다. 이를 위해 과도 열전달-구조 연계 해석을 수행하였다. 가열 부와 금형 형상의 대칭성을 고려하여 모델의 1/4에 대한 해석을 수행하였으며 해석 대상 형상은 Fig. 5와 같다. 1/4 형상 해석을 위한 대칭면에서는 단열 조건을 부여하였다. 열전달 해석을 위한 경계 조건은 3장에서 설명하였다.
본 냉각 공정 해석은 실제 생산 공정에서의 조건을 모사하기 위해 상부 및 하부 코어의 재질을 탄화 텅스텐(WC)로 고려하였으며, 사용한 WC 소재의 100oC에서 물성치는 Table 2에 제시되었다[29]. 금형 내부 및 금형과 접촉하는 가열블록에서의 열 접촉 컨덕턴스는 전술한 실험-해석결과 비교를 통해 구한 값을 적용하였다. 황동과 텅스턴의 열전도율은 100oC 조건에서 각각 115, 108.7 W/m·K 로 차이가 크지 않고, 접촉면이 유리 렌즈 가공이 완료된 이후 매끄러운 상태로 접촉되어 두 표면의 거칠기에 큰 차이가 없기 때문에, 동일한 열 접촉 컨덕턴스를 고려하는 것은 타당할 것으로 판단되었다.
금형의 냉각을 위한 가열블록의 접촉 조건은 두 종류로 고려하여 각각 시뮬레이션을 수행하였다. 첫 번째 접촉조건은 실험과 동일하게 금형 아랫면이 하부 가열블록과 접촉하고, 금형 윗 면은 상부 가열블록과 약 1 mm 간격을 유지한 상태이다.
두 번째 접촉 조건은 금형의 윗면과 아랫면 모두 각각 상부와 하부 가열블록과 접촉한 상태이며, 이러한 조건에서는 금형 및 렌즈를 고르게 냉각시키는 것이 가능하다. 본 연구에서는 가열블록이 금형에 가하는 압력 없이 단순 접촉만 하고 있는 조건으로 시뮬레이션을 수행하였다. 상부 가열블록과 금형 윗면 사이의 열 접촉 컨덕턴스는 아랫면과 동일한 값인 375 W/m2·K을 적용하였다.
과도 구조 해석은 열전달 해석에서 구한 금형 및 렌즈의 온도 분포, 즉 열하중을 반영하여 해석한다. Fig. 5와 같이 두 가열블록의 고정 면에 좌표가 고정된(Fixed) 조건을 부여하여 y축 변위를 구속하고, 상부 가열블록 아랫면에도 동일 조건으로 수직 변위를 구속하였다. 가열블록이 금형의 윗면에 접촉한 조건에서는 상부 코어 및 슬리브 윗면과 상부 가열블록이 단순 접촉한다. 상부 가열블록과 금형 윗면 접촉면의 y축 변위를 고정하여 금형 자체에 가하는 압력을 0으로 설정하였고, 금형 자체에 의한 하중을 고려하기 위해 표준 지구 중력 조건을 반영하였다.
냉각 공정에서는 냉각 속도에 따라 렌즈 내부의 온도분포가 변하며, 국소 지점에서의 변형률 차이가 발생하며 재료내부 응력 분포를 유발한다. 이러한 영향을 분석하기 위해 냉각 시간과 냉각 공정 단계를 다르게 하여 시뮬레이션을 수행하였다.
Table 4는 냉각 공정을 해석하기 위한 설정 변숫값을 보여준다. 고려된 공정 변수는 냉각 공정 단계 수와 각 공정에서의 가열블록의 온도, 각 공정 단계에서 냉각 시간, 상부 가열블록과 금형 접촉 여부로 설정하였다. 공정 단계 수의 경우 2-4단계; 각 냉각 단계에서 공정 시간은 400, 700, 그리고 1,000 s로 해석 조건을 정하였다. 상부 가열블록과 금형 윗면의 접촉 및 비접촉 여부를 고려하였으며, 접촉 조건에서는 가열블록이 금형에 가하는 압력 없이 단순 접촉하는 조건에서 해석을 수행하였다. 주어진 해석 조건은 실제 유리 렌즈 생산에 사용되는 순차 이송형 GMP 장비에서 구현되는 성형 공정 조건을 참고하여 설정되었다.
유리 렌즈는 대표적인 취성 재료이므로 압축 응력에 비교적 강하지만, 인장 응력에 취약한 특성을 갖는다. 따라서, 본 연구에서는 냉각 공정에서 공정 변수에 따라 변하는 값을 갖는 렌즈 내부 최대 주응력(σmax) 값을 분석하였다. Yi등에 따르면 일반적인 유리의 파손 인장응력은 약 75 MPa로 알려져 있다[30]. 따라서 인장응력에 대한 안전율을 고려하여, 렌즈 내부에 허용 가능한 최대 주응력 기준값을 40 MPa로 설정하고, 이를 초과하지 않는 냉각 공정 조건을 제시하고자 하였다.
5.2 금형 윗면 비접촉 조건에서 공정시간 변화에 따른 해석 결과
Fig. 6(a)와 6(b)는 3단계 냉각 공정을 적용한 경우 각 공정 냉각 시간 변화에 따른 렌즈 내부 최대 주응력, σmax의 변화와 렌즈 내부 최대 온도 차 변화를 보여준다. 여기서 렌즈 내부 최대 온도 차는 임의 시간에서 렌즈 내부의 최대 온도와 최소 온도를 뺀 값이다. 각 단계에서 상부 및 하부 가열블록의 온도는 Table 4와 같이 400, 200, 50ºC이며, 금형과 렌즈의 초기 온도는 520ºC이다. 순차 이송형 GMP 공정의 특성상, 일정한 냉각 시간을 갖는 냉각 단계가 순차적으로 수행되는 특징을 갖는다. 하나의 연속 공정에서 단계별 냉각 시간을 400, 700, 1,000 s의 세 가지 조건으로 고려하였다.
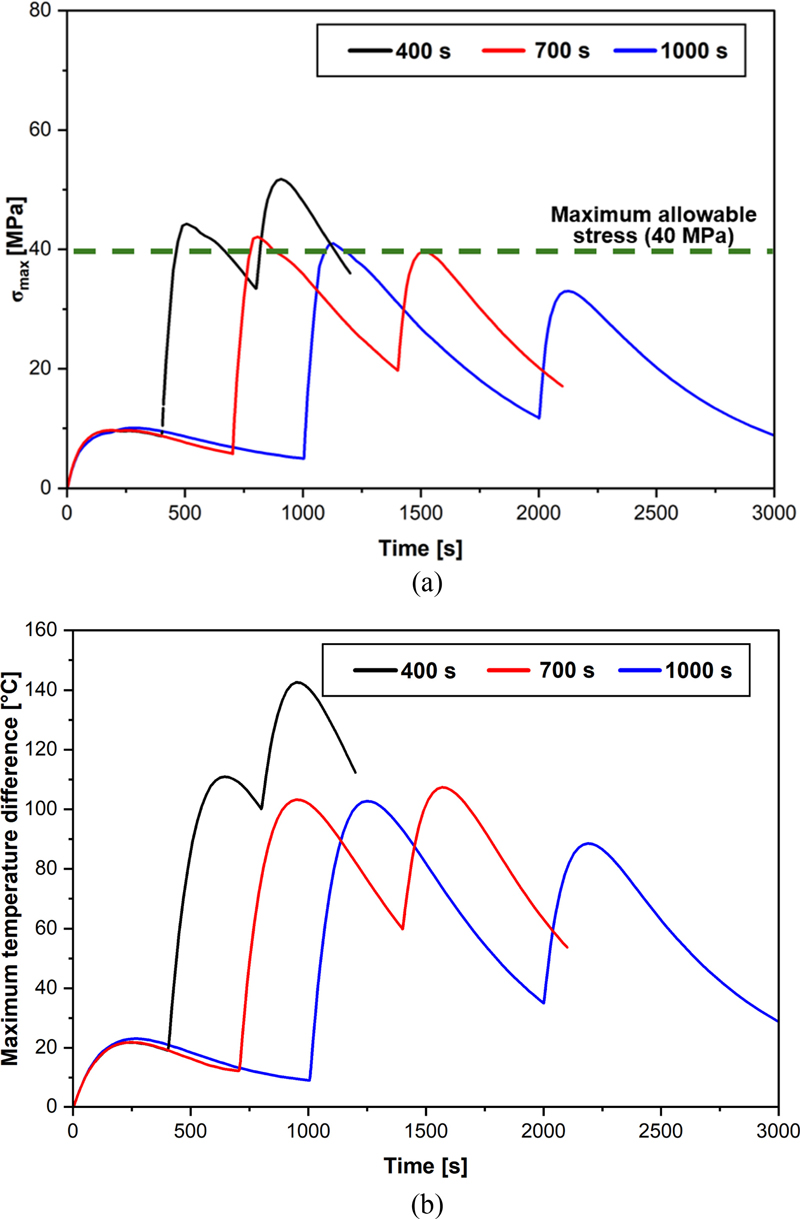
Simulated stress and temperature change of lens with the change of process time (a) Maximum principal stress and (b) Maximum temperature difference
Fig. 6(a)에서 각 단계의 냉각 시간이 400 s인 경우 첫 번째 냉각 공정에서 렌즈 내부 σmax의 최댓값은 약 9.7 MPa이지만, 냉각을 위한 접촉 가열블록 온도가 크게 낮아지는 두 번째 냉각 공정에서는 σmax의 최댓값이 약 44.3 MPa로 크게 높아지는 경향을 확인할 수 있다. 이후 세 번째 냉각 공정에서 σmax의 최댓값의 크기가 최대 51.8 MPa까지 증가하게 되는데 이는 Fig. 6(b)가 보여주는 것과 같이 렌즈 내부 최대 온도 차가 커지기 때문이다. 다시 말하면 각 공정의 냉각 시간이 400 s인 조건에서는 두 번째 공정에서 내부까지 충분히 냉각되지 않은 상태에서 세 번째 냉각 공정으로 이송되면서, 렌즈 내부와 표면의 온도차는 다시 커지게 되고, 이러한 온도의 불균일 분포 심화는 렌즈 내 σmax 값을 증가시키게 된다. Fig. 6는 렌즈 내부에서 최대 온도 차와 σmax의 변화 경향이 거의 일치하고 있음을 보여준다.
Fig. 6(a)의 렌즈 내부 σmax의 변화 곡선 중 일부 구간에서 불연속적인 선의 분포를 확인할 수 있다는데, 이는 렌즈 내부에서 σmax의 최댓값이 발생하는 지점이 고정되지 않고 시간 경과에 따라 조금씩 이동하며 σmax 최댓값이 불연속적으로 변하기 때문이다.
각 공정 단계의 냉각 시간을 400에서 700과 1,000 s 로 증가시키면, 첫 번째 냉각 공정 종료 후 렌즈 내 σmax 값은 점점 감소하게 된다. 이는 렌즈가 냉각 시간의 증가에 따라 내부 온도 분포가 점점 균일해지기 때문이며, 이는 Fig. 6(b)의 렌즈 내 최대 온도분포 차를 보여주는 그래프를 통해 확인할 수 있다. 두 번째 냉각 공정이 시작되면 렌즈 내부 온도 차가 커지며 σmax 역시 크게 증가함을 확인할 수 있고, 냉각 시간을 700과 1,000 s로 증가시켜도 두 번째 냉각 공정에서의 σmax의 최댓값의 크기는 각각 42.1과 40.7 MPa로 큰 차이가 없었다. 이는 두 번째 냉각 공정에서 가열블록 온도가 이전 공정의 460에서 200oC로 크게 감소하기 때문이다. 이는 렌즈 내부의 σmax 최댓값이 냉각 속도에 의해서도 크게 달라진다는 것을 보여준다.
Fig. 6(b)에서 냉각 공정 시간이 400 s 조건인 경우 렌즈 내부의 최대 온도 차이는 공정이 진행될수록 누적되어 증가한다. 또한 마지막 냉각 단계 직후 렌즈 내부 최대 온도 차이는 112.4oC로 충분한 냉각이 이루어지지 않아, 내부의 온도가 균일하지 않음을 알 수 있다. 반면 공정 시간이 1,000 s인 경우, 마지막 냉각 단계 직후 내부 최대 온도 차이는 28.8oC로 상대적으로 충분한 냉각이 진행되었음을 확인할 수 있다. 이러한 온도 분포는 냉각 공정시간이 충분하지 않을 경우 렌즈 내부 불균일한 온도 분포가 심화되며 렌즈 잔류 응력은 증가한다는 것을 보여주고 있다.
Fig. 6(a)는 세 번째 냉각 단계의 과정 및 냉각 종료 시점에서 σmax 값이 냉각 시간에 따라 크게 달라짐을 보여준다. 냉각 시간이 400, 700, 1,000 s일 때, 세 번째 냉각 공정 단계에서 가장 큰 σmax 값은 각각 51.8, 39.6, 그리고 33 MPa이었으며, 각 단계의 냉각 공정이 완료된 후 σmax 값은 36, 17, 그리고 8.8 MPa이었다. 이러한 σmax 값의 차이는 두 번째 냉각 조건이 완료된 이후 렌즈 내부에 분포하는 σmax 값과 온도 균일성의 차이가 세 번째 냉각 공정에서의 응력분포에 영향을 주었기 때문이다. 이러한 해석 결과는 마지막 냉각 단계의 냉각 시간 증가는 냉각 종료 시점에서 잔류하는 σmax의 크기를 감소시킬 수 있지만, 냉각 과정 중 발생하는 σmax의 최댓값의 크기는 냉각 시간보다는 이전 공정의 종료 시점에서 존재하였던 σmax에 크게 영향받음을 보여준다.
5.3 금형 윗면 비접촉 조건에서 공정 단계 세분화에 따른 해석 결과
Fig. 8(a)와 8(b)는 각 공정 단계의 냉각 시간을 700 s로 고정한 상태에서, 초기 조건과 마지막 단계의 경계 조건을 동일하게하고, 냉각을 최소 2 단계, 최대 4단계로 구성하는 경우 렌즈 내부에 발생하는 렌즈 내부 σmax 와 렌즈 내부 최대 온도 차 변화를 보여준다. Table 4에서 보여주는 것과 같이, 모든 공정에서 초기조건은 금형과 렌즈가 520oC로 일정하게 가열된 것으로 가정하였으며 마지막 냉각 공정은 50oC로 유지되는 가열블록으로 냉각되는 것으로 해석하였다.
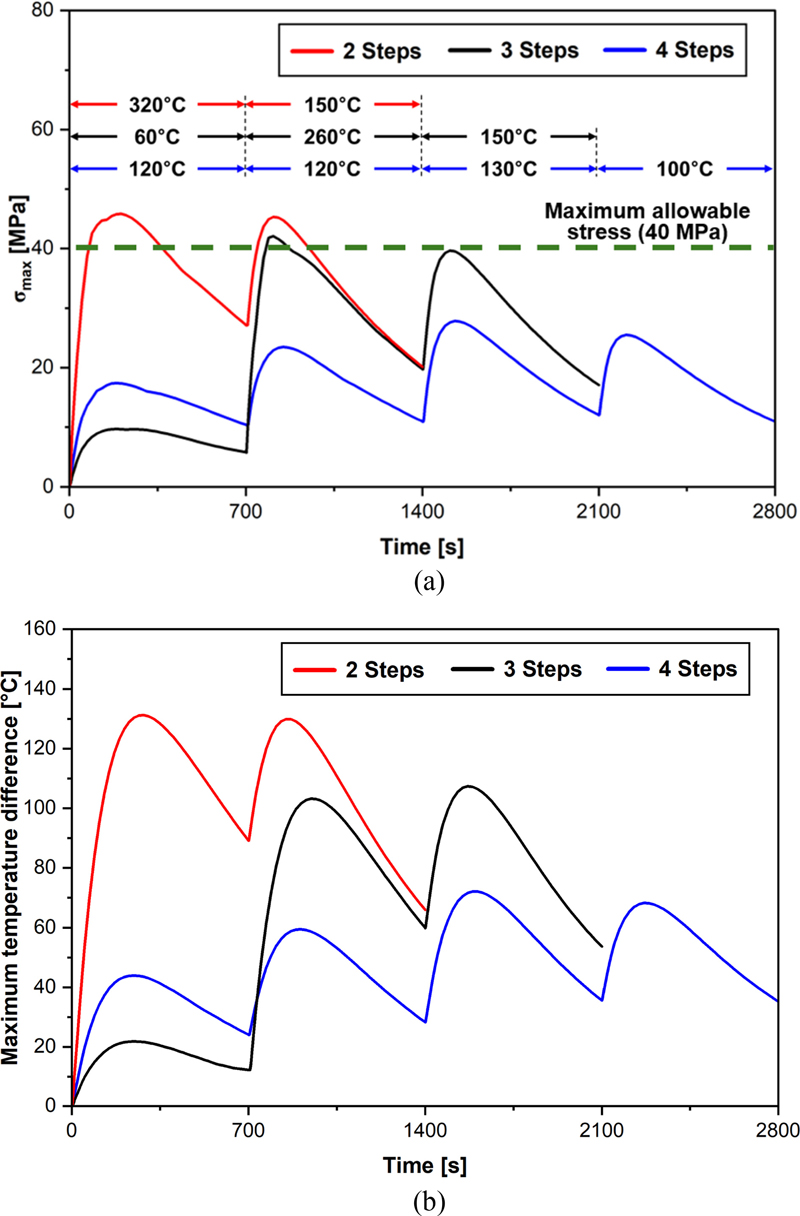
Simulated stress and temperature change of lens according to the number of process steps (a) Maximum principal stress (b) Maximum temperature difference
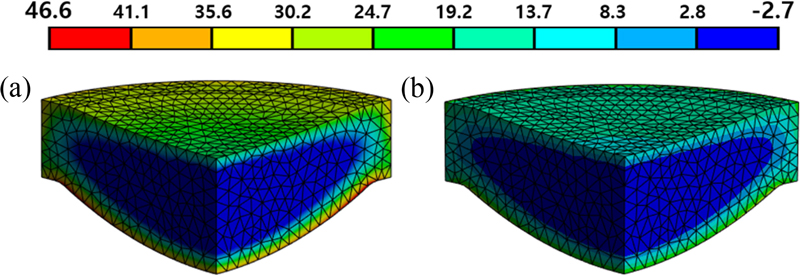
Maximum principal stress distribution lens (unit: MPa): (a) Maximum principal stress under the 2 steps condition, (b) Maximum principal stress under the 4 steps condition
Fig. 8(a)에서 표시된 온도들은 각 냉각 단계에서 이전 공정과 해당 공정에서 가열블록 온도 차를 나타낸다. 각 단계에서 동일한 냉각 시간을 설정하였으므로, 높은 온도 차는 해당 공정에서 냉각 속도가 더 빠르다는 것을 의미한다. Fig. 8의 결과는 각 냉각 공정에서 발생하는 렌즈 내부 σmax의 최댓값이 공정 단계별 온도 차가 가장 큰 과정, 즉 냉각 속도가 가장 빠른 과정에서 발생함을 보여주고 있다. 이는 공정 단계를 세분화하여 냉각 속도를 감소시킬 경우 렌즈 내부 σmax의 최댓값을 감소시켜 냉각 과정 중 발생할 수 있는 렌즈의 손상을 방지할 수 있음을 의미한다.
냉각 공정을 2개 단계로 구성한 경우, 단계별 온도 차이는 각각 320, 150ºC이며, 렌즈 내부 최대 주응력의 가장 큰 값은 첫 번째 냉각 공정에서 46.6, 두 번째 냉각 공정에서 45.1 MPa을 보여준다. 이는 너무 짧은 시간 동안 빠르게 냉각과정을 수행하는 경우 렌즈의 냉각 과정에서 렌즈가 파손될 수 있음을 보여주는 결과이다. 냉각 공정을 3개 단계로 구성하고 각 단계에서의 온도 차이를 60, 260, 150ºC로 설정하여 해석을 수행하면, 전체 냉각과정 중 발생하는 가장 큰 최대 주응력 값은 두 번째 단계에서 42.1 MPa로 예측되었다. 이 결과는 σmax 발생이 공정 온도 차보다, 공정에서의 냉각 속도 차이에 크게 영향받고 있음을 보여준다.
냉각 공정을 4개 단계로 구성하고, 각 단계별 온도 차이를 120-130ºC로 큰 차이 없이 설정하여 해석을 수행하게 되면, 전체 냉각 과정에서 발생하는 냉각 단계별 σmax의 최댓값은 17-28 MPa였으며, 전체 냉각과정에서 σmax 값이 안전율을 고려한 유리의 파손 인장응력 40 MPa 이하로 예측되었다.
Fig. 7(a)와 7(b)에 공정 단계를 2개 단계로 구성한 경우, 4개 단계로 구성한 경우에서 σmax 의 최댓값 발생 시점((a) 207 s, (b)1,528 s) 에서의 렌즈 내부 최대 주응력 분포를 나타내었다. 공정 단계를 2개 단계로 구성한 경우, 렌즈 내부 최대 주응력이 최대 46.6 MPa로 나타나며, 렌즈 하단면에서 그 값이 나타남을 확인할 수 있다. 반면 공정 단계를 4개 단계로 구성한 경우, σmax이 최대 28 MPa 이하로 나타나며 공정 단계를 2개 단계로 구성하였을 때에 비해 σmax이 전반적으로 작게 나타남을 확인할 수 있다. 또한 해석 결과는 냉각 과정에서 렌즈의 파손을 방지하기 위해 냉각 공정을 4개 단계로 구성하는 것이 적절함을 보여준다. 만일 냉각 공정을 3개 단계로 구성해야 하는 경우에는 각 단계의 냉각 시간을 크게 하여 냉각 속도를 늦추는 것이 필요할 것으로 판단되었다.
5.4 금형 윗면과 상부 가열블록의 접촉 여부에 따른 해석 결과
본 연구에서는 상부 가열블록 접촉 여부가 렌즈 내부의 응력 및 온도분포에 미치는 영향을 추가적으로 해석하였다. 전술한 것과 같이 금형이 상부 가열블록과 접촉하게 되면, 금형의 상하부 코어가 동시에 냉각되므로 냉각 과정 중 렌즈 내부의 온도 균일성을 높이는데 유리하다. 상부 가열블록이 금형과 접촉하는 경우, 금형에 압력을 가하지 않고 단순 접촉하는 것으로 해석하였다.
Fig. 9(a)와 9(b)는 Table 4의 3개 단계로 구성되며, 각 단계의 냉각 시간이 700 s 인 공정 조건에서 상부 가열블록 접촉 여부에 따른 렌즈 σmax 및 렌즈 내부 최대 온도 차의 변화를 보여준다. Fig. 10(a)에서 알 수 있듯이, 렌즈 내부 σmax은 상단 가열 블록과 금형이 닿아있는 접촉 조건에서 1 mm 간격을 갖는 비접촉 조건에 비해 두 번째 냉각단계에서 최대 16 MPa 더 크다는 것을 보여준다. 이는 상단 가열블록의 접촉에 따라 렌즈 내부 열 변형 차이가 심화되며 나타난 결과이다. 여기서 주목할 점은 Fig. 9(b)에서와 같이 두 번째 냉각 단계에서 렌즈 내 최대 온도 차는 접촉조건에서 더 작다는 것이다. 이는 렌즈 내 최대 σmax 값이 온도 차뿐 아니라 두 냉각 면의 냉각 능력에 의해서도 영향을 받는다는 것을 의미한다.
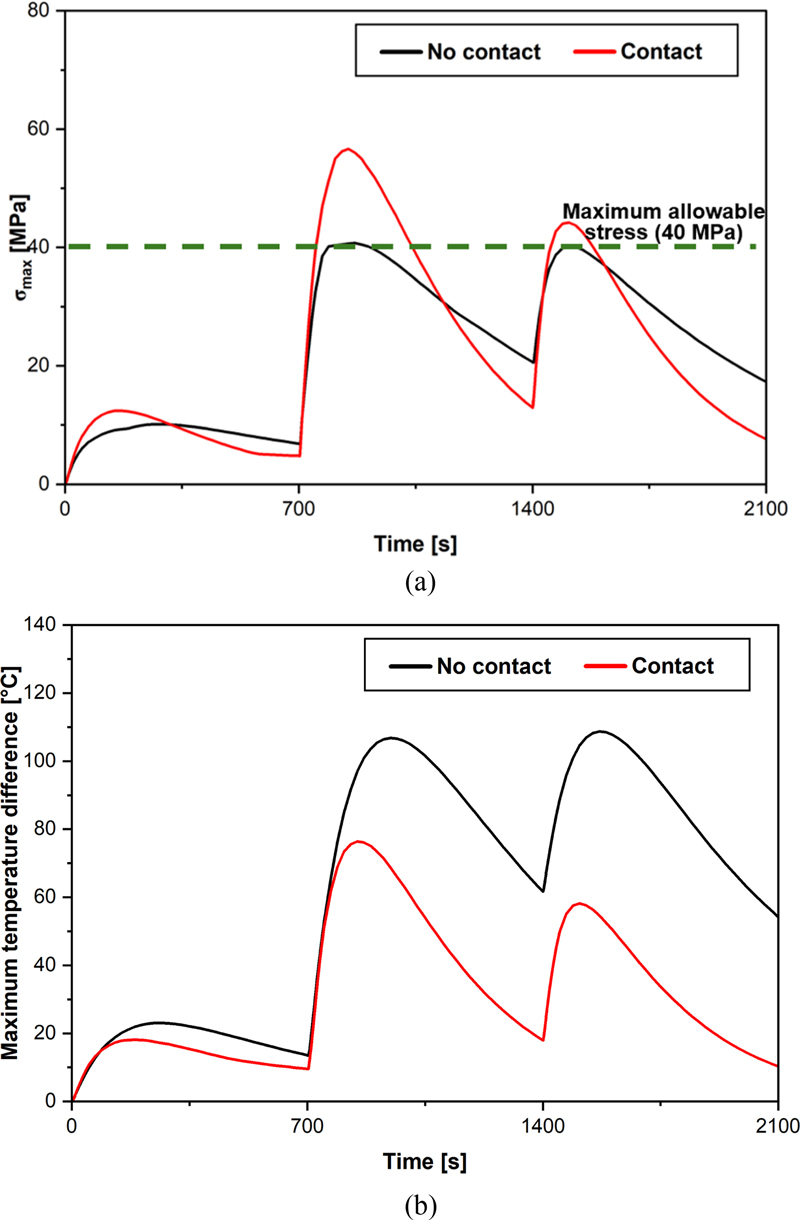
Simulated stress and temperature change of lens with the difference of contact condition (a) Maximum principal stress and (b) Maximum temperature difference
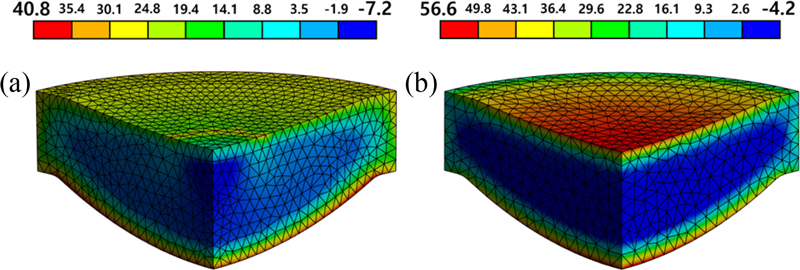
Stress distribution lens (unit: MPa): (a) Maximum principal stress under the no contact condition and (b) Maximum principal stress under the contact condition
냉각 과정에서 온도가 빠르게 변화하는 렌즈 겉면과, 비교적 느리게 변화하는 렌즈 내부의 열 변형 차이로 인한 응력이 발생한다. 두 번째 냉각 단계에서 접촉 조건의 경우 렌즈 내부의 열이 윗면과 아랫면으로 동시에 전달되어 열 변형 차이가 심화되어 응력이 크게 나타난다. 비접촉 조건의 경우 렌즈 내부의 대부분의 열이 아랫면으로 전달되기 때문에 렌즈 내부 단위 길이 당 온도 차 및 온도 구배가 작아져 이에 따른 렌즈 내 열 변형 차와 최대 주응력은 최대 온도 차에 비해 작게 나타날 수 있다.
Fig. 9(b)는 렌즈 내부 최대 온도 차가 비접촉 조건에 비해 접촉 조건에서 최대 60oC 작게 나타나며, 이는 상부 가열블록을 금형에 접촉시킬 경우 금형 및 렌즈를 균일하게 냉각시킬 수 있음을 준다. 비접촉 조건의 경우, 금형 및 렌즈의 대부분 열이 하부 가열블록을 통해 이동하므로 렌즈 내부 온도 분포는 불균일하게 나타나며 냉각 공정이 진행될수록 불균일한 온도 분포가 심화되며 렌즈 내부에서 분포하는 응력은 증가한다. 이에 따라 냉각 공정이 종료된 시점(2,100 s)의 σmax 값은 비접촉 조건에 비해 접촉 조건에서 9.7 MPa 작게 나타난다.
Fig. 10(a)와 10(b)는 응력 최댓값 발생 시점((a) 848 s, (b) 868 s)에서 상부 가열블록과 금형 윗면 접촉 여부에 따른 렌즈 내부 최대 주응력 분포를 보여준다. 비접촉 조건의 경우 렌즈의 아랫면, 비접촉 조건의 경우 렌즈의 윗면과 아랫면 부근에서 동시에 높은 σmax 이 나타난다. 또한 두 조건 모두에서 렌즈 내부에 압축응력이 나타나는 것을 알 수 있다. 이는 냉각과정에서 불균일한 온도 분포에 따른 열 변형 차이에 의해 나타난 결과이다.
렌즈 표면이 빠르게 냉각되며 온도가 렌즈 내부 온도 이하로 떨어질 때, 내부 층이 표면의 수축을 방해하게 되며 이에 따라 렌즈 내부에 압축 응력, 렌즈 표면에 인장 응력이 나타나게 된다. 이는 기존의 연구[9,31]에서 제시하는 냉각 과정에서 렌즈 냉각 시 응력 분포 경향성과 유사한 결과이다. Yin은 냉각 과정에서 냉각이 빠르게 진행되는 렌즈 표면과 렌즈 내부의 변형 속도 차이로 인해 냉각이 빠르게 진행되는 렌즈 표면에서 인장응력, 느리게 냉각되는 렌즈 내부에 압축 응력이 발생하게 된다 [31]고 언급하였다. 접촉 조건의 경우 렌즈 윗면과 아랫면에서 냉각 속도가 빠르게 나타나므로 내 측에서 수축을 방해하는 정도가 크며 이에 따라 렌즈 겉면의 인장 응력은 더욱 증가한다. 따라서 냉각 과정 중 인장응력에 의해 유리렌즈의 파손이 발생한다면, 그 위치는 렌즈의 윗면 또는 아랫면 부근임을 예측할 수 있다. 또한 렌즈 내부에서 인장이 발생하는 부분과, 압축이 발생하는 부분의 변형률 차이로 인한 파손 위험이 클 것으로 예상되며, 이러한 변형률의 차이는 렌즈 내부에서의 파단 발생 원인으로 작용할 수 있을 것으로 판단된다.
6. 결론
본 연구에서는 순차 이송형 GMP 냉각 공정을 실험 및 해석적 방법을 통해 분석하였다. 각 단계별 냉각 온도, 냉각 시간 그리고 냉각을 위한 가열블록 접촉 조건이 렌즈 내부 온도 및 응력 분포에 미치는 영향을 고찰하였으며 이를 통해 얻은 결론은 다음과 같다.
- 1. 냉각 공정 실험과 해석을 통해 렌즈를 포함한 금형 내부 및 표면의 열 접촉 컨덕턴스를 구하였으며 그 값은 375-500 W/m2·K였다.
- 2. 냉각 시간이 빠를수록 과도 열전도 해석 결과에 대한 열 접촉 컨덕턴스의 영향이 크게 작용하였다.
- 3. 다단의 GMP 냉각 공정에서 냉각 시간이 충분하지 않을 경우, 렌즈 내부 불균일한 온도 분포는 공정이 진행될수록 심화되어 렌즈 내부 잔류 응력이 증가하였다.
- 4. 냉각의 마지막 단계에서 냉각 시간의 증가는 냉각 종료 후 잔류 응력의 크기를 감소시킬 수 있지만, 냉각 공정 중 발생하는 최대 주응력의 크기는 이전 공정 종료 시점의 최대 주응력에 크게 영향받았다.
- 5. 공정 단계를 세분화하여 냉각 속도를 감소시킬 경우 렌즈 내부의 최대 주응력이 갖는 최댓값을 감소시켜 냉각 과정 중 발생할 수 있는 렌즈 손상을 방지할 수 있음을 확인하였다.
- 6. 냉각 방법이 동일한 조건에서는, 렌즈 내 최대 온도 차의 변화와 최대 주응력 값의 변화 경향이 일치하였다.
- 7. 금형의 윗면과 아랫면이 가열블록과 접촉하여 냉각되는 경우, 금형의 아랫면만 접촉하여 냉각되는 조건에 비해 렌즈 내부 온도 분포가 더 균일하여 냉각 종료 시 렌즈 내부 잔류 응력은 최대 9.7 MPa 감소하지만, 전체 냉각 과정에서 렌즈 내부 응력의 최댓값은 16 MPa 더 크게 발생하였다.
- 8. 빠르게 냉각되는 렌즈 표면에 인장 응력, 상대적으로 느리게 냉각되는 렌즈 내부에서 압축 응력이 나타나므로, 인장 응력에 취약한 유리 재료의 특성을 고려하였을 때 렌즈 표면과 인장 응력과 압축 응력이 발생하는 경계면에서 변형률 차이로 인한 파손 위험이 높을 것으로 판단되었다.
NOMENCLATURE
α : | Coefficient of Thermal Expansion |
E : | Young’s Modulus |
ν : | Poisson’s Ratio |
σ : | Principal Stress |
Acknowledgments
본 연구는 산업통상자원부의 재원으로 한국산업기술진흥원 및 한국산업기술기획평가원의 지원으로 수행되었으며 이에 감사드립니다(산업기술혁신사업 No. 20010775, 2024년 산업혁신 인재성장지원사업 No. P0012744).
REFERENCES
-
Jung, T.-S., Park, K.-S., Yoon, G.-S., (2011), A study on the optimal molding conditions for aspheric glass lenses in progressive gmp, Journal of the Korea Academia-Industrial Cooperation Society, 12(3), 1051-1057.
[https://doi.org/10.5762/KAIS.2011.12.3.1051]
-
Choi, J., Tamang, S., Park, H., (2024), A study on numerical analysis for determination of glass molding process conditions for glass lenses, Journal of the Korean Society for Precision Engineering, 41(3), 207-214.
[https://doi.org/10.7736/JKSPE.023.136]
-
Seo, B. M., Jung, D. Y., Park, K., Park, C. Y., (2022), A study on the heat transfer characteristics of a glass lens mold heating block according to design of a heat radiating block, Journal of the Korean Society for Precision Engineering, 39(7), 493-500.
[https://doi.org/10.7736/JKSPE.022.058]
-
Chen, Y., Yi, A. Y., Su, L., Klocke, F., Pongs, G., (2008), Numerical simulation and experimental study of residual stresses in compression molding of precision glass optical components, Journal of Manufacturing Science and Engineering, 130(5), 0510121-0510129.
[https://doi.org/10.1115/1.2950062]
-
Li, K., Gong, F., (2019), Numerical simulation of glass molding process for large diameter aspherical glass lens, IOP Conference Series: Materials Science and Engineering, 490(5), 052018.
[https://doi.org/10.1088/1757-899X/490/5/052018]
-
Chang, S. H., Lee, Y. M., Jung, T. S., Kang, J. J., Hong, S. K., Shin, G. H., Heo, Y. M., (2007), Simulation of an aspheric glass lens forming behavior in progressive GMP process, AIP Conference Proceedings, 908, 1055-1060.
[https://doi.org/10.1063/1.2740950]
-
Vu, A. T., Vu, A. N., Liu, G., Grunwald, T., Dambon, O., Klocke, F., Bergs, T., (2019), Experimental investigation of contact heat transfer coefficients in nonisothermal glass molding by infrared thermography, Journal of the American Ceramic Society, 102(4), 2116-2134.
[https://doi.org/10.1111/jace.16029]
-
Yan, J., Zhou, T., Masuda, J., Kuriyagawa, T., (2009), Modeling high-temperature glass molding process by coupling heat transfer and viscous deformation analysis, Precision Engineering, 33(2), 150-159.
[https://doi.org/10.1016/j.precisioneng.2008.05.005]
-
Zhou, J., Shi, T., Hu, Y., Ji, Y., Li, M., Shen, L., (2013), Numerical simulation in compression molding of glass lens, Proceedings of the 2013 IEEE International Conference on Automation Science and Engineering (CASE), 669-674.
[https://doi.org/10.1109/CoASE.2013.6653894]
-
Zhou, T., Yan, J., Masuda, J., Oowada, T., Kuriyagawa, T., (2011), Investigation on shape transferability in ultraprecision glass molding press for microgrooves, Precision Engineering, 35(2), 214-220.
[https://doi.org/10.1016/j.precisioneng.2010.09.011]
-
Tao, B., He, P., Shen, L. G., (2014), Measurement of residual stresses in molded glass lenses, Advanced Materials Research, 902, 144-147.
[https://doi.org/10.4028/www.scientific.net/AMR.902.144]
-
Nguyen, L. P., Wu, M. H., Hung, C., (2019), Finite element analysis of ultrasonic vibration-assisted microstructure hot glass embossing process, Australian Journal of Mechanical Engineering, 17(3), 199-208.
[https://doi.org/10.1080/14484846.2017.1339300]
-
Mosaddegh, P., Ziegert, J., Iqbal, W., Tohme, Y., (2011), Apparatus for high temperature friction measurement, Precision Engineering, 35(3), 473-483.
[https://doi.org/10.1016/j.precisioneng.2011.02.011]
-
Tsai, Y.-P., Hung, J.-C., Yin, L.-C., Hung, C., (2012), Ultrasonic vibration-assisted optical glass hot embossing process, The International Journal of Advanced Manufacturing Technology, 60, 1207-1213.
[https://doi.org/10.1007/s00170-011-3669-8]
-
Brand, J., Gadow, R., Killinger, A., (2004), Application of diamond-like carbon coatings on steel tools in the production of precision glass components, Surface and Coatings Technology, 180, 213-217.
[https://doi.org/10.1016/j.surfcoat.2003.10.138]
-
Dambon, O., Wang, F., Klocke, F., Pongs, G., Bresseler, B., Chen, Y., Yi, A. Y., (2009), Efficient mold manufacturing for precision glass molding, Journal of Vacuum Science & Technology B: Microelectronics and Nanometer Structures Processing, Measurement, and Phenomena, 27(3), 1445-1449.
[https://doi.org/10.1116/1.3056171]
-
Zhou, T., Liu, X., Liang, Z., Liu, Y., Xie, J., Wang, X., (2017), Recent advancements in optical microstructure fabrication through glass molding process, Frontiers of Mechanical Engineering, 12, 46-65.
[https://doi.org/10.1007/s11465-017-0425-2]
-
Ananthasayanam, B., Joseph, P. F., Joshi, D., Gaylord, S., Petit, L., Blouin, V. Y., Richardson, K. C., Cler, D. L., Stairiker, M., Tardiff, M., (2012), Final shape of precision molded optics: Part i—computational approach, material definitions and the effect of lens shape, Journal of Thermal stresses, 35(6), 550-578.
[https://doi.org/10.1080/01495739.2012.674830]
-
Tao, B., He, P., Shen, L., Yi, A., (2014), Quantitatively measurement and analysis of residual stresses in molded aspherical glass lenses, The International Journal of Advanced Manufacturing Technology, 74, 1167-1174.
[https://doi.org/10.1007/s00170-014-6058-2]
-
Cha, D. H., Park, H. S., Hwang, Y., Kim, J.-H., Kim, H.-J., (2011), Experimental study of glass molding process and transcription characteristics of mold surface in molding of aspheric glass lenses, Optical Review, 18, 241-246.
[https://doi.org/10.1007/s10043-011-0049-4]
-
Feli, S., Aalami Aaleagha, M. E., Foroutan, M., Borzabadi Farahani, E., (2012), Finite element simulation of welding sequences effect on residual stresses in multipass butt-welded stainless steel pipes, Journal of Pressure Vessel Technology, 134(1), 011209.
[https://doi.org/10.1115/1.4004571]
- AMS Technologies, D-ZLaF52LA Glass Datasheet. https://shop.amstechnologies.com/
- MatWeb, Free-Cutting Breass, UNS C36000. https://www.matweb.com/search/DataSheet.aspx?MatGUID=bae961d2d6ed497a9096986641162def&ckck=1
-
Liu, W., Ruan, H., Zhang, L., (2014), Revealing structural relaxation of optical glass through the temperature dependence of young’s modulus, Journal of the American Ceramic Society, 97(11), 3475-3482.
[https://doi.org/10.1111/jace.13179]
-
Ozaki, Y., Zee, R. H., (1995), Investigation of thermal and hydrogen effects on emissivity of refractory metals and carbides, Materials Science and Engineering: A, 202(1-2), 134-141.
[https://doi.org/10.1016/0921-5093(95)09793-7]
-
Xu, Y., Zhang, K., Tian, Z., Tong, R., Yu, K., Liu, Y., (2022), Comparison research on spectral emissivity of three copper alloys during oxidation, Infrared Physics & Technology, 126, 104344.
[https://doi.org/10.1016/j.infrared.2022.104344]
- Incropera, F. P., DeWitt, D. P., Bergman, T. L., Lavine, A., (2017), Incropera's principles of heat and mass transfer, Wiley.
-
Churchill, S. W., Chu, H. H., (1975), Correlating equations for laminar and turbulent free convection from a vertical plate, International Journal of Heat and Mass Transfer, 18(11), 1323-1329.
[https://doi.org/10.1016/0017-9310(75)90243-4]
-
Reeber, R. R., Wang, K., (1999), Thermophysical properties of α-tungsten carbide, Journal of the American Ceramic Society, 82(1), 129-135.
[https://doi.org/10.1111/j.1151-2916.1999.tb01732.x]
-
Chow, W. K., Gao, Y., (2008), Thermal stresses on window glasses upon heating, Construction and Building Materials, 22(11), 2157-2164.
[https://doi.org/10.1016/j.conbuildmat.2007.09.004]
-
Yin, S., Li, C., Fang, H., Ma, Q., (2024), Effects of annealing on thermal stress generation during the cooling process of large-size silica glass, Journal of Non-Crystalline Solids, 628, 122857.
[https://doi.org/10.1016/j.jnoncrysol.2024.122857]
M.Sc. candidate in the Department of Mechanical Design and Robot Engineering, Seoul National University of Science & Technology. Her research interest is experimental and numerical heat transfer.
E-mail: ghd4274@seoultech.ac.kr
M.Sc. candidate in the Department of Mechanical Design and Robot Engineering, Seoul National University of Science & Technology. His research interest is experimental and numerical heat transfer.
E-mail: hong980923@seoultech.ac.kr
CTO in R&D Center of Daeho Technology Korea Co., Ltd. His research interest is thermoforming equipment and F.A. system.
E-mail: dongyean@daehoteck.co.kr
Ph. D. and Principal Researcher at the Intelligent Optical Module Research Center. Korea Photonics Technology Institute. His research interest is design of optical system and optical lens manufacturing.
E-mail: ybkim@kopti.re.kr
Professor in the Department of Mechanical System Design Engineering, Seoul National University of Science & Technology. His research interest is finite element analysis of manufacturing processes.
E-mail: kpark@seoultech.ac.kr
Professor in the Department of Mechanical System Design Engineering, Seoul National University of Science & Technology. His research interest is heat transfer and energy system analysis.
E-mail: cypark@seoultech.ac.kr