
레이저 변수와 분말 기공율이 SLM 공정의 분말베드내 열특성에 미치는 영향 고찰
Copyright © The Korean Society for Precision Engineering
This is an Open-Access article distributed under the terms of the Creative Commons Attribution Non-Commercial License (http://creativecommons.org/licenses/by-nc/3.0) which permits unrestricted non-commercial use, distribution, and reproduction in any medium, provided the original work is properly cited.
Abstract
Heat transfer characteristics in the vicinity of irradiated region of the beam of a selective laser melting (SLM) process affect the creation of the melted region during the deposition. The creation of the molten pool is greatly influenced by laser parameters and powder characteristics. The goal of the paper is to investigate the influence of laser parameters and powder porosity on thermal characteristics in the vicinity of the molten pool of the SLM process through repeated finite element analyses (FEAs). The power and the scan speed are chosen as the laser parameters. The laser is assumed to be a volumetric Gaussian heat flux model. Materials of the powder and the substrate are chosen as SUS17-4PH and S45C, respectively. Temperature dependent thermal properties for those material are used to perform the FEA. An appropriate efficiency of the heat flux is predicted by comparing the results of FEAs and those of experiments. The influence of laser parameters on temperature distributions in the vicinity of the melted region and the formation of the molten pool is examined. In addition, the effects of porosity of powders on heat transfer characteristics in the vicinity of the melted region are discussed.
Keywords:
Selective laser melting process, Thermal characteristics, Transient heat transfer analysis, Parameters of laser, Porosity of powders키워드:
선택적 레이저 용융 공정, 열 특성, 비정상 열전달해석, 레이저 변수, 분말 기공율1. 서론
금속 적층 제조(Additive Manufacturing, AM) 공정은 추가적인 금형 제작 없이 컴퓨터응용설계(Computer Aided Design, CAD) 데이터로부터 3차원 금속 제품을 직접 제작할 수 있는 장점을 가지고 있다.1 분말 베드 융해(Powder Bed Fusion, PBF) 공정과 직접식 에너지 적층(Directed Energy Deposition, DED) 공정은 대표적인 금속 적층 제조 공정이다.1-5 선택적 레이저 소결(Selective Laser Sintering, SLS) 공정이 개발된 후, 직접식 금속 레이저 소결(Direct Metal Laser Sintering, DMLS) 공정, 선택적 레이저 용융(Selective Laser Melting, SLM) 공정, 전자빔 용융(Electron Beam Melting, EBM) 공정 등 다양한 PBF형 금속 적층 제조 공정들이 개발되었다.1-3 SLM 공정에서는 분말 형태로 분말 베드(Powder Bed) 위에 공급된 적층 재료에 집속된 고출력 레이저 빔을 조사하여 분말을 용융시킨 후, 용융된 재료를 분말 베드 위에 부착된 기저부 또는 앞서 생성된 적층층 위에서 고화 시킴으로써 새로운 층을 생성한다.3,4,6 이 과정을 반복적으로 수행하여 3차원 금속 제품을 제작한다.3,4,6 SLM 공정에서는 분말이 완전 용융되기 때문에 충진율이 매우 높은 제품을 제작할 수 있다.3 SLM 공정에서 고출력 레이저 빔이 조사되는 영역 부근의 분말층과 기저부에 발생하는 열전달 현상은 분말층과 기저부의 급속 가열에 의한 용융 풀(Molten Pool) 생성과 용융 영역의 급속 냉각에 의한 고화층 생성에 직접적인 영향을 미친다.7,8 그러므로 SLM 공정의 제어를 위해서는 레이저 출력, 레이저 스캔 속력(Scan Speed), 기저부 예열 온도, 분말층 기공율 및 분말층 두께 등의 변수들에 따른 레이저 빔 조사 영역 주위의 비정상 열전달 거동에 대한 분석이 필요하다.6-8
Roberts 등은 SLM 공정에서 다층 스캐닝을 포함하는 실제 분말 적층 공정의 온도 이력을 예측하기 위한 3차원 유한 요소해석 모델을 개발하였다.9 Hussein 등은 SLM 공정을 이용한 SUS316 분말 단일층 적층시 분말층과 기저부의 3차원 온도 분포 예측을 위하여 비선형 비정상 유한요소해석을 수행하였다.10 그들의 연구에서는 분말의 상변화가 고려된 유효 밀도와 유효 열전도도를 3차원 열전달 해석에 적용하였다.10 Loh 등은 3차원 비정상 열전달 해석을 수행하여 레이저 출력과 스캔 속력에 따른 알루미늄 분말층 내의 용융 풀의 진전과 가열부 온도 변화율 변화를 고찰하였다.8 그들의 연구에서는 유효 열전도도를 분말의 기공율 함수로 계산되었다.8 Huang 등은 Ti-6Al-4V 분말을 이용한 SLM 공정에서 레이저 출력 및 스캔 속력이 적층부 온도 분포와 용융 풀 형상에 미치는 영향에 대한 연구를 수행 하였다.7 이 연구에서는 기공율이 고려된 온도 의존 유효 열전도도 및 밀도가 입력 데이터로 사용되었다.7 Denlinger 등은 Inconel 718 분말을 사용하는 레이저 분말 베드 융해 공정에서 열전달 현상을 고찰하기 위한 모델을 개발 하였다.11 또한 해석 결과와 실험 결과를 비교하여 제안된 모델의 효율성을 고찰하였다.11 Heeling 등은 유한 차분법(Finite Difference Method, FDM)을 이용하여 레이저 스캔 속력에 따른 용융 풀 변화와 적층부 기공율 변화를 고찰 하였다.12
본 연구에서는 3차원 비정상 열전달 해석을 이용하여 기저부와 분말층의 재료를 S45C와 SUS17-4로 사용하는 SLM 공정에서 레이저 공정 조건과 분말 기공율이 레이저 조사 영역 부근의 열특성에 미치는 영향성을 고찰하였다. 비정상 열전달 해석을 수행하기 위한 레이저 열원 모델, 온도 의존 열물성 모델, 기공율이 고려된 분말층 온도 의존 열물성 모델 및 유한 요소 해석모델을 도출하였다. 3차원 유한요소해석 결과와 실험 결과를 이용하여 열원 효율을 선정하였다. 반복적인 3차원 유한요소해석 결과를 이용하여 레이저 출력 및 레이저 스캔 속력이 용융부의 형상과 온도 분포에 미치는 영향을 분석하였다. 또한, 분말의 기공율에 따른 레이저 조사 영역 부근의 열전달 특성 변화를 고찰하였다.
2. SLM 시스템 및 3차원 유한요소해석
2.1 적용된 SLM 시스템
이 연구에서는 Fig. 1과 같이 한국생산기술연구원에서 보유하고 있는 3D Systems 사의 PROX DMP 300 장비를 사용하였다. PROX DMP 300 장비에서는 Table 1과 1,064 nm 파장(Wave Length: λ)을 가지는 파이버(Fiber) 전송 방식의 연속형 Nd:YAG 레이저를 사용하고 있다. 레이저의 횡방향 모드(Transverse Mode)와 에너지 분포는 각각 TEM00과 가우시안(Gaussian) 분포이다.9 분말 베드위 장착되는 기저부는 S45C이며, 적층을 위하여 기저부 위에 도포되는 분말 재료는 스테인레스 금속인 SUS17-4PH를 사용하였다. 기저부의 두께와 분말 도포층의 두께(ψ)는 각각 25 mm와 40 μm이다. Table 1과 같이 레이저 빔의 유효 반경(Effective Radius: re)과 분말층 침투 깊이(Penetration Depth: δ)는 각각 약 37.5 μm와 약 50 nm이다. 적층 시스템의 챔버 내부는 산소 농도가 0.1% 이하인 질소 분위기를 유지되도록 하였다. 적층 실험시 기저부는 예열을 수행하지 않았다.
2.2 유한요소해석 모델링
SLM 공정의 3차원 비선형 비정상 열전달 해석을 수행하기 위하여 Fig. 2와 같은 3차원 유한요소해석 모델을 설정하였다. x 축 방향으로 레이저 이동 시키면 단일 트랙(Single Track)의 적층 비드를 생성하는 조건에 대한 해석 모델을 도출하였다. 단일 트랙 적층 공정의 특성을 고려하여 대칭형 유한요소해석 모델을 생성하였다. 유한요소해석 영역을 도출하기 위하여 대형 모델에 대한 사전 해석을 수행하여, 적층 공정중 실제 열전달이 발생하는 영역을 대략적으로 산출하였다. 또한, 열원의 이동 방향에 수직한 방향으로 레이저 빔의 직경의 2배 이상의 폭이 되도록 모델을 설정하였다. 가장 높은 온도 분포가 발생하는 레이저 출력과 스캔 속력 조건에서 실제 열전달이 발생하는 열영향 영역의 최대 폭이 충분이 해석 모델에 포함될 수 있으며, 용융 풀이 완전히 정상 상태로 발전할 수 있는 열원 이동 거리가 될 수 있도록 해석 모델의 크기를 설정하였다. 또한, 레이저 빔 직경과 침투 깊이를 고려하여 Fig. 2와 같은 0.20 mm × 0.80 mm × 0.24 mm 크기의 유한 요소 해석 모델을 도출하였다. 해석 모델의 중앙면에서는 대칭 조건을 부여하였다. 레이저 빔이 조사되는 분말 도포층 상면에는 복사 및 대류 조건을 적용하였다. 그외 유한 요소 해석 모델의 최 외곽면에는 대류 조건을 부여하였다. 분말 도포층과 기저부의 경계면에는 접촉 열 컨덕턴스(Interfacial Thermal Conductance, G)를 적용 하였다. 유한 요소 해석에 적용된 초기 온도(Initial Temperature, Ti), 대류 계수(Convection Coefficient, h), 접촉 열 컨덕턴스 및 방사율(Emissivity, ε)은 Table 2와 같다. SUS17-4PH 재료의 방사율은 유사 재료인 SUS17-7PH 재료의 방사율 데이터를 사용하였다.13 유한 요소 격자 생성은 Fig. 2와 같이 레이저 빔 조사 영역 중심부 방향으로 집중된 바이어스 격자(Biased Mesh) 를 생성하였다. 분말 도포층과 기저부는 각각 46,080개와 30,720개의 육면체 입체 요소로 표현하였다.
레이저 빔은 식(1)과 같이 침투 깊이가 고려된 원뿔형 체적 가우시안 열원(Conical Volumetric Gaussian Heat Flux)으로 가정하였다.14 열원의 x 방향 이동을 고려한 이동 좌표계(Moving Coordinate)를 도입할 경우, 절대 좌표계와 이동 좌표계의 상관관계는 식(2) 및 식(3)과 같다. 식(1)에 이동 좌표계를 도입하면 열원은 식(4) 같이 모델링 된다. 또한, 이동 좌표계가 적용되면 3차원 열전달 방정식은 식(5)와 같이 스캔 속력의 영향을 고려할 수 있다.15 상용 프로그램인 ABAQUS를 이용하여 3차원 비선형 비정상 유한 요소 해석을 수행하였다. ABAQUS의 DFLUX Subroutine을 이용하여 열원 모델링과 열원의 이동을 프로그래밍 하였다.
(1) |
(2) |
(3) |
(4) |
(5) |
실험에 적용된 중심 적층 조건에 대하여 유한 요소 해석 결과와 실험 결과를 용융 폭 측면에서 비교하여 열원 효율을 도출하였다. 도출된 효율을 사용하여 레이저 출력과 스캔 속력에 따른 레이저 빔 조사 영역 부근의 열전달 및 용융 풀 생성 특성을 분석하였다. 실험에서 정확한 분말 기공율이 측정되지 않아 효율 선정과 레이저 공정 변수인 레이저 출력과 스캔 속력에 따른 열전달 특성 분석에서는 분말의 기공율을 고려하지 않았다. 또한, 분말의 기공율이 적층부 열특성에 미치는 영향을 정량적으로 분석하기 위하여 열원 효율 도출에 적용된 중심 적층 조건에서 분말의 기공율에 따른 레이저 빔 조사 영역 부근의 열전달 특성 변화를 고찰하였다. 3차원 비선형 비정상 열전달 해석을 수행한 조건은 Table 3과 같다. 또한 실험에 적용된 중심 적층 조건의 레이저 출력과 스캔 속력은 각각 172W와 1.6 m/s이다.
(6) |
(7) |
(8) |
(9) |
(10) |
2.3 열전달 해석을 위한 열물성
3차원 비선형 비정상 열전달 해석을 수행하기 위해 분말 도포층 재료인 SUS17-4PH와 기저부 재료인 S45C 재료의 온도 의존 열전도도, 온도 의존 비열 및 온도 의존 밀도 데이터를 문헌 조사를 통하여 Fig. 3과 같이 도출하였다.16-18 레이저 효율 예측과 레이저 출력과 스캔 속력에 따른 레이저 빔 조사 영역 부근의 열전달 특성 분석에는 Fig. 3과 같은 분말층의 기공율이 고려되지 않은 SUS17-4PH 열물성 데이터를 사용하였다.16,17
분말 도포층의 기공율에 따른 레이저 빔 조사 영역의 열전달 특성 변화 분석에서는 식(6)부터 식(10)까지 사용되었다. 기공율과 분말간 결합이 고려된 온도 의존 열전도도를 산출하기 위하여, 첫번째로 식(6)부터 식(8)과 같은 Zehner-Schlunder 모델을 이용하여 기공율만이 고려된 SUS17-4PH 분말의 온도 의존 열전도도를 예측하였다.18-20 이 예측 데이터와 SUS17-4PH의 소결 온도 이후 분말 도포층내의 분말간 결합부와 비 결합부의 혼합율(Mixing Ratio, β)가 고려된 식(9)를 이용하여 기공율과 분말간 결합상태가 고려된 SUS17-4PH 재료의 온도 의존 열전도도를 도출하였다.18 SUS17-4PH 재료의 소결 온도와 용융 온도 사이의 분말간 용융에 의한 결합부가 차지하는 혼합율은 소결 온도 이하에서는 0%이고 용융 온도에서 100%가 되도록 혼합율이 선형적으로 변한다고 가정하였다. 기공율이 고려된 SUS17-4PH 재료의 온도 의존 비열과 밀도는 식(10)과 같은 혼합 법칙(Mixing Law)를 이용하여 예측 하였다.18 SUS17-4PH 재료의 용융 온도는 약 1,425oC이며, 이 재료의 소결 온도는 용융 온도의 50%에 해당되는 약 712oC로 가정하였다.16-18 분위기 가스로 사용된 질소의 온도 의존 열전도도, 온도 의존 비열, 온도 의존 밀도 곡선들은 문헌 조사를 통하여 Fig. 4와 같이 도출되었다.21-23
3. 결과 및 고찰
3.1 열원 효율
적용된 SLM 공정의 중심 적층 조건에 대한 3차원 비선형 비정상 열전달 해석을 수행하여 Figs. 5부터 7과 같은 각 열원의 효율별 레이저 빔 조사 영역 주위의 3차원 온도 분포를 도출하였다. Fig. 5와 같은 레이저 빔의 이동 거리가 0.15 mm 이상일 경우 해석에 적용된 모든 효율에서 온도 분포와 최대 온도가 거의 일정하게 유지 되는 것을 알 수 있었다. 이 결과로부터 열원이 0.15 mm 이상 이동할 경우 정상 상태 열전달이 시작되는 것을 알 수 있었다. 정상상태 열전달 구간에서 열원의 효율에 따른 레이저 빔 조사영역 주위의 온도 분포 변화 분석을 수행하였다. Figs. 5 및 6과 같이 열원 효율이 증가할수록 최대 온도와 용융 풀의 면적과 깊이가 증가하는 것을 알 수 있었다. Fig. 7과 같이 열원 효율이 증가할 경우 용융부의 폭 증가율보다 길이 증가율이 더 크게 나타나는 것을 알 수 있었다. 이 결과로부터 열원의 효율이 증가할수록 열원의 이동 방향의 수직 방향 보다 열원의 이동 방향의 반대 방향으로 열전달이 증가하는 것을 알 수 있었다. 분말 도포층과 기저부의 결합 가능성을 분석하기 위하여 분말 도포층과 기저부 경계면의 온도 분포를 고찰하였다. 기저부의 재료인 S45C의 소결 온도는 S45C 재료의 용융 온도인 1,520oC의 50%에 해당되는 760oC로 가정하였다.16-18 해석에 적용된 전체 효율 조건에서 분말 도포층과 기저부 경계면의 온도가 S45C 재료의 소결 온도보다 높은 온도로 예측되었다. 이 결과로부터 이 해석에 적용된 모든 효율 조건에서 분말 재료인 SUS17-4PH가 기저부에 결합될 수 있는 것을 알 수 있었다.
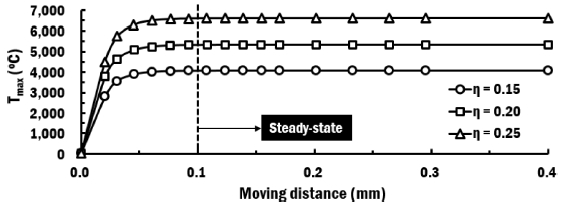
Maximum temperatures for different moving distances and efficiencies of heat flux (P = 172 W and ν = 1.6 m/s)
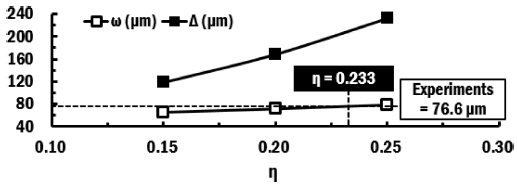
Effects of the efficiency on the width (w) and the length (D) of the molten pool (P = 172 W and ν = 1.6 m/s)
식(1)과 식(4)의 열원 모델링에 대한 열원의 효율을 예측하기 위하여 중심 적층 조건으로 실험된 결과와 3차원 열전달 해석결과를 Fig. 7과 같이 용융부 폭 측면에서 비교하였다. 실험 결과에서 취득된 각 출력별 스캔 속력과 비드 폭 상관관계를 이용하여 중심 조건의 비드 폭을 산출하였다. 그 후 이 산출된 비드 폭을 분말 도포층의 용융부 폭으로 가정하였다. 비교 결과 Fig. 7과 같이 열원이 약 0.233일 때 유한 요소 해석 결과가 용융부 폭 측면에서 실험 결과와 거의 유사하게 예측되는 것을 알 수 있었다.
3.2 공정 조건에 따른 온도 분포 및 용융부 형상 변화
3차원 비선형 비정상 열전달 해석 결과를 이용하여 레이저 출력과 스캔 속력에 따른 정상 상태에서의 최대 온도 변화를 고찰한 결과, Fig. 8과 같이 레이저 출력이 증가하고 스캔 속력이 감소 할수록 정상 상태에서의 레이빔 조사 영역에 발생하는 최대 온도가 증가하는 것을 알 수 있었다. 또한, 해석이 수행된 조건에서는 레이저 스캔 속력보다 레이저 출력이 최대 온도 변화에 미치는 영향이 더 큰 것을 알 수 있었다. 이 결과를 이용하여 식(11)과 같은 유효 열 입력량(Effective Heat Input) 을 가정할 수 있었다. 유효 열 입력량의 지수 값은 유효 열 입력량과 정상 상태 최대 온도의 상관 관계 회귀 분석(Regression Analysis)을 통하여 결정하였다. 회귀 분석에서는 지수 함수를 기저 함수로 사용하였다. 유효 열 입력량과 정상 상태 최대 온도 상관 관계는 Fig. 9 및 Table 4와 같이 도출 되었다. 도출된 유효 열 입력량과 정상 상태 최대 온도 상관 관계식에 대한 결정 계수(Coefficient of Determination)가 0.99 이상으로 도출된 회귀 분석식이 정상 상태 최대 온도와 유효 열 입력량 상관 관계를 적절히 표현 할 수 있음을 알 수 있었다.
(11) |
해석 결과를 이용하여 레이저 출력과 스캔 속력에 따른 용융부 생성 특성 변화를 분석/고찰 하였다. 이 분석은 용융부 형상이 완전히 발달되어 열원 이동에 따라 용융부 형상이 변하지 않는 열원 이동 거리 이상에서 수행 되었다. 레이저 출력이 일정할 경우, Fig. 10과 같이 스캔 속력이 증가할수록 용융부의 길이, 폭 및 깊이가 감소하는 것을 알 수 있었다. 또한, 스캔 속력이 증가할수록 용융부 선단과 열원의 위치 사이의 거리 및 용융부 깊이 방향 기울기(Slope in the Thickness Direction, θ)가 감소하는 것을 알 수 있었다. 스캔 속력이 일정할 경우, Figs. 10(b) 및 11과 같이 레이저 출력이 증가 할수록 용융부의 길이, 폭 및 깊이가 증가하는 것을 알 수 있었다. 또한, 레이저 출력이 증가할수록 용융부 선단과 열원의 위치 사이의 거리 및 용융부 깊이 방향 기울기가 증가하는 것을 알 수 있었다. 이와 같은 현상은 레이저 출력이 증가하고 스캔 속력이 감소 할수록 레이저 조사부에 부가되는 유효 열 입력량이 증가하기 때문으로 사료된다. 이 연구에서 해석을 수행한 레이저 출력과 스캔 속력 범위에서는 레이저 출력이 스캔 속력보다 용융부 생성에 더 큰 영향을 미치는 것을 알 수 있었다. 유효 열 입력량이 157 J/s0.5m0.5 이상인 경우에는 거의 모든 적층 조건에서 용융부 깊이가 분말 도포층 두께 이상으로 예측되는 것을 알 수 있었다. 이 결과로부터 유효 열 입력량이 157 J/s0.5m0.5 이상인 경우에는 분말 용융부와 기저부와 완전히 용융되어 결합되는 것을 알 수 있었다. 또한, 이 연구에 적용된 모든 해석 조건에서 기저부와 분말 도포층 경계면의 온도가 S45C 재료의 소결 온도보다 높은 온도로 예측되었다. 이 결과로부터 해석에 적용된 모든 레이저 출력과 스캔 속력 조합에서 SUS17-4PH 분말이 기저부에 결합될 것으로 사료되었다.
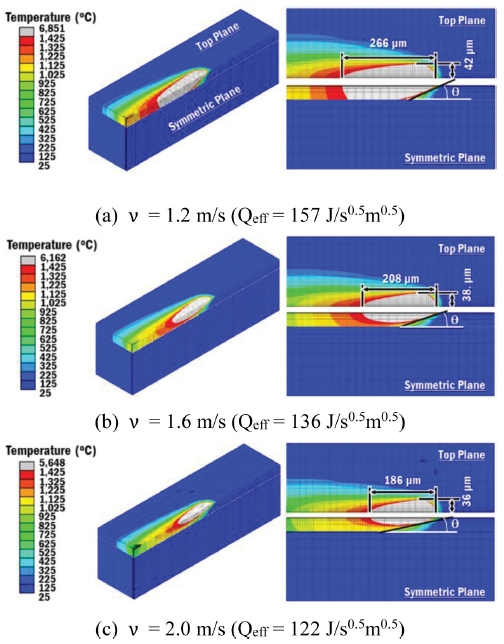
Influence of the scan speed of the laser on the temperature distribution in the vicinity of the irradiated region (P = 172W)
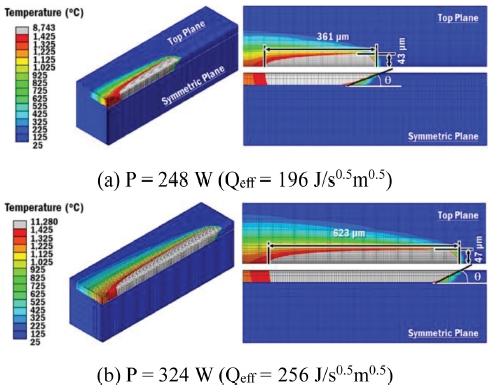
Effects of the power of the laser on the temperature distribution in the vicinity of the irradiated region (ν = 1.6 m/s)
해석 결과를 이용하여 Fig. 12 및 Table 5와 같은 식(11)의 유효 열 입력량과 용융부 폭, 길이 및 평면 형상비(In-Plane Aspect Ratio, P)의 상관 관계를 도출할 수 있었다. 용융부의 평면 형상비는 식(12)과 같이 정의 되었다. Fig. 12에서 유효 열입력량이 증가할 경우 용융부 폭의 증가율보다 용융부 길이의 증가율이 더 크게 나타나는 것을 알 수 있었다. 특히, 유효 열입력량이 증가할수록 열원 후미의 용융부가 현저히 증가하는 것을 알 수 있었다. 이 결과들로부터 유효 열 입력량이 증가 할수록 용융부의 폭 방향 열전달 보다 용융부의 길이 방향의 열전달이 더 크게 발생하는 것을 알 수 있었다.
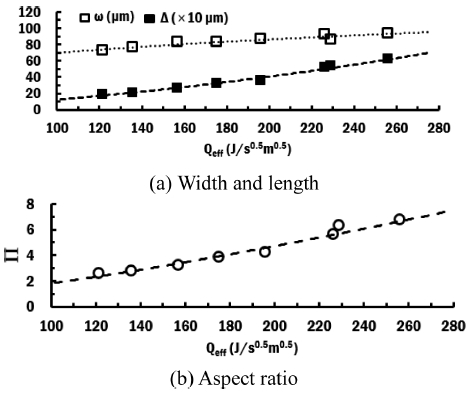
Influence of the effective heat input on the length, the width and the aspect ratio of the molten pool

Relationship between effective heat input and measures of the formation of the molten pool in steady-state
(12) |
해석이 수행된 레이저 출력과 스캔 속력 조합에서 용융부 평면 형상비가 최소 2.5에서 최대 6.7까지 증가하는 것을 알 수 있었다.
3.3 분말 기공율에 따른 열전달 특성 변화
적층 중심 조건인 레이저 출력 172 W와 스캔 속력 1.6 m/s에서 분말 기공율에 따른 레이저 조사부 주위의 열전달 특성 변화를 Figs. 10(b) 및 13과 같이 분석/고찰 하였다. 그 결과 분말 기공율이 고려된 경우와 고려되지 않은 경우 열 영향 영역(Heat Affected Region) 의 크기가 현저히 달라지는 것을 알 수 있었다. 분말 기공율을 고려한 경우 Fig. 13과 같이 분말 기공율이 고려하지 않은 경우 보다 열 영향 영역의 크기가 두드러지게 감소하는 것을 알 수 있었다. 분말 기공율이 적용된 경우 기공율이 증가하더라도 열 영향 영역의 크기는 거의 일정한 것을 알 수 있었다. 이 현상은 기공율이 고려될 경우, 기공율이 고려되지 않은 열 물성 데이터에 대비하여 분말의 밀도는 거의 변하지 않고 비열은 약 50-70% 정도 감소하지만 열전도도는 Fig. 14와 같이 소결 온도 이하에서 기공율이 고려되지 않은 열전도도의 10% 이하로 감소하여, 소결 온도 이하에서는 열 확산율이 현저히 감소하기 때문으로 사료된다.
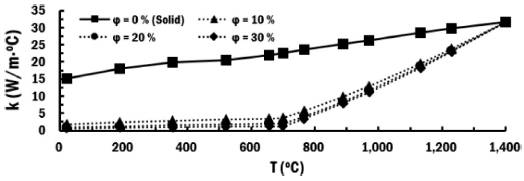
Temperature dependent thermal conductivity of SUS17-4PH considering porosity and contact status of powders
Figs. 10(b), 13 및 15(a)와 같이 분말 기공율이 증가할수록 열영향 영역내의 용융부 폭, 길이 및 깊이가 증가하는 것을 고찰할 수 있었다. 분말 기공율이 0%에서 30%로 증가할 경우, 용융부 폭과 길이의 증가량은 각각 10.8 mm와 96 mm정도였다. 또한, 분말 기공율이 증가할수록 용융부의 최대 온도가 조금씩 증가하는 것을 알 수 있었다. Figs. 10(b) 및 13과 같이 분말 기공율이 0%에서 30%로 증가할 경우 최대 온도 증가량은 약 711oC정도였다. 이 같은 현상은 분말 온도가 용융 온도 이상인 용융부에서는 열전전도가 기공율이 0%인 고체의 열전도도와 동일하고 밀도는 기공율에 따라 거의 감소하지 않으나, 기공율이 증가할수록 비열이 조금씩 감소함으로 용융부에서의 열 확산율이 증가하여 열 영향 영역 내부의 분말 용융부가 확대되는 것으로 사료되었다. Fig. 15(b)와 같이 분말 기공율이 증가할수록 용융부 평면 형상비가 거의 선형적으로 증가하는 것을 알 수 있었다. 이 결과로부터 분말 기공율이 증가할수록 용융부의 폭보다 길이가 증가하는 것을 알 수 있었다.
4. 결론
S45C 기저부 재료와 SUS17-4PH 분말 재료를 사용하는 SLM 공정의 레이저 공정 조건과 분말 기공율이 레이저 조사 영역 주위의 열 특성에 미치는 영향을 분석/고찰하여 다음과 같은 결론을 얻을 수 있었다.
(1) SLM 공정에 대한 비정상 열전달 해석 수행을 위한 3차원 체적 열원 모델, 온도 의존 열물성 데이터, 기공율과 분말 결합도가 고려된 열물성 데이터 및 유한요소해석 모델을 도출할 수 있었다.
(2) SLM 공정을 수행할 중심 레이저 출력과 스캔 속력 조건에서 열원 효율에 따른 레이저 조사부 온도 분포 변화를 고찰하였다. 용융부 폭 측면에서 실험 결과와 해석 결과를 비교하여 적정 레이저 열원 효율을 선정할 수 있었다.
(3) 선정된 레이저 열원 효율을 적용하여 레이저 출력과 스캔 속력 조합에 따른 레이저 조사부 주위의 열전달 특성 변화를 분석/고찰하였다. 유효 열 입력량에 따른 레이저 조사부 주위의 열전달 특성 및 용융부 변화를 고찰할 수 있었다. 또한, 유효 열입력량과 용융부 최대 온도, 폭, 길이 및 평면 형상비의 상관 관계를 도출할 수 있었다.
(4) 중심 적층 조건에서 분말 기공율에 따른 레이저 조사부 주위의 열특성 변화를 고찰하였다. 그 결과 분말 기공율이 고려될 경우 분말 소결 온도 이하에서는 열전도도가 기공율 0%인 분말 열전도도의 10% 이하로 감소하여 열 영향 영역이 현저히 감소하는 것을 알 수 있었다. 또한, 분말의 기공율이 고려 된 경우 분말 용융 온도 이상에서는 열전도도와 밀도는 기공율 0%인 분말과 거의 유사하지만, 기공율이 증가할수록 비열은 점점 감소하여 열 영향 영역내부에 생성되는 용융부의 폭, 길이, 깊이 및 최대 온도는 증가하는 것을 알 수 있었다.
향후, 추가적인 실험과 해석을 수행하여 3차원 유한요소해석 모델의 최적화 및 해석 결과의 타당성과 신뢰성을 향상시킬 예정이다.
NOMENCLATURE
λ : | Wave length of laser |
δ : | Penetration depth |
re : | Effective radius of laser |
ψ : | Thickness of deposited powders on the substrate |
Ti : | Initial temperature |
h : | Convection coefficient |
G : | Interfacial thermal conductance |
ε : | Emissivity |
I(x, y, z) : | Intensity distribution of heat flux |
η : | Efficiency of heat flux |
P : | Power of laser |
x, y, z : | Global coordinates |
xm, ym, zm : | Moving coordinates |
ν : | Scan speed of laser |
t : | Scan time of laser |
tm : | Scan time in moving coordinates |
: | Gradient for moving coordinates |
T : | Temperature |
k : | Thermal conductivity |
: | Heat input per time |
ρ : | Density |
Cp : | Specific heat |
φ : | Porosity of powder |
kp : | Effective thermal conductivity of powder considering porosity |
ks : | Thermal conductivity of powder at the solid state |
kf : | Thermal conductivity of nitrogen gas |
B : | Constant of Zehner-Schlunder model |
ke : | Effective thermal conductivity considering mixing ratio |
β : | Mixing ratio |
Ωe : | Effective thermal property considering porosity |
Ωs : | Thermal property of powder |
Ωf : | Thermal property of nitrogen gas |
Tmax : | Maximum temperature |
ω : | Width of the molten pool |
Δ : | Length of the molten pool |
Qeff : | Effective heat input |
Tmax,s : | Maximum temperature in the state-state |
R2 : | Coefficient of determination |
θ : | Slope in the thickness direction |
Π : | In-plane aspect ratio of the molten pool |
Acknowledgments
이 논문은 산업통상자원부 및 한국산업기술평가관리원 의 산업기술혁신사업의 지원을 받아 수행된 연구 결과의 일부임 (No. 20000201)
REFERENCES
-
Ahn, D. G., “Applications of Laser Assisted Metal Rapid Tooling Process to Manufacture of Molding & Forming Tools - State of the Art,” International Journal of Precision Engineering and Manufacturing, Vol. 12, No. 5, pp. 925-938, 2011.
[https://doi.org/10.1007/s12541-011-0125-5]
-
Guo, N. and Leu, M. C., “Additive Manufacturing: Technology, Applications and Research Needs,” Frontiers of Mechanical Engineering, Vol. 8, No. 3, pp. 215-243, 2013.
[https://doi.org/10.1007/s11465-013-0248-8]
-
Ahn, D. G., “Direct Metal Additive Manufacturing Processes and Their Sustainable Applications for Green Technology: A Review,” International Journal of Precision Engineering and Manufacturing-Green Technology, Vol. 3, No. 4, pp. 381-395, 2016.
[https://doi.org/10.1007/s40684-016-0048-9]
-
Kim, J. and Lee, C.-H., “Laser Assisted Additive Manufacturing by Rotating Metal Wire Feeder,” Journal of the Korean Society for Precision Engineering, Vol. 35, No. 9, pp. 847-852, 2018.
[https://doi.org/10.7736/KSPE.2018.35.9.847]
-
Chua, B. L., Lee, H. J., Ahn, D.-G., and Kim, J. G., “Influence of Angle of Corner Deposition on Temperature and Residual Stress Distributions in the Vicinity of the Deposited Region by a Ti-6Al-4V Wire-Feeding Type of Direct Energy Deposition Process,” Journal of the Korean Society for Precision Engineering, Vol. 35, No. 9, pp. 853-859, 2018.
[https://doi.org/10.7736/KSPE.2018.35.9.853]
-
Olakanmi, E. O., Cochrane, R. F., and Dalgaron, K. W., “A Review on Selective Laser Sintering/Melting (SLS/SLM) of Aluminium Alloy Powders: Processing, Microstructure, and Properties,” Progress in Materials Science, Vol. 74, pp. 401-477, 2015.
[https://doi.org/10.1016/j.pmatsci.2015.03.002]
-
Huang, Y., Yang, L. J., Du, X. Z., and Yang, Y. P., “Finite Element Analysis of Thermal Behavior of Metal Powder during Selective Laser Melting,” International Journal of Thermal Sciences, Vol. 104, pp. 146-157, 2016.
[https://doi.org/10.1016/j.ijthermalsci.2016.01.007]
-
Loh, L.-E., Chua, C.-K., Yeong, W.-Y., Song, J., Mapar, M., et al., “Numerical Investigation and an Effective Modelling on the Selective Laser Melting (SLM) Process with Aluminium Alloy 6061,” International Journal of Heat and Mass Transfer, Vol. 80, pp. 288-300, 2015.
[https://doi.org/10.1016/j.ijheatmasstransfer.2014.09.014]
-
Roberts, I. A., Wang, C. J., Esterlein, R., Stanford, M., and Mynors, D. J., “A Three-Dimensional Finite Element Analysis of the Temperature Field during Laser Melting of Metal Powders in Additive Layer Manufacturing,” International Journal of Machine Tools & Manufacture, Vol. 49, Nos. 12-13, pp. 916-923, 2009.
[https://doi.org/10.1016/j.ijmachtools.2009.07.004]
-
Hussein, A., Hao, L., Yan, C., and Everson, R., “Finite Element Simulation of the Temperature and Stress Fields in Single Layers Built without-Support in Selective Laser Melting,” Materials & Design, Vol. 52, pp. 638-647, 2013.
[https://doi.org/10.1016/j.matdes.2013.05.070]
-
Denlinger, E. R., Jagdale, V., Srinivasan, G. V., El-Wardany, T., and Michaleris, P., “Thermal Modeling of Inconel 718 Processed with Powder Bed Fusion and Experimental Validation Using in Situ Measurements,” Additive Manufacturing, Vol. 11, pp. 7-15, 2016.
[https://doi.org/10.1016/j.addma.2016.03.003]
-
Heeling, T., Cloots, M., and Wegener, K., “Melt Pool Simulation for the Evaluation of Process Parameters in Selective Laser Melting,” Additive Manufacturing, Vol. 14, pp. 116-125, 2017.
[https://doi.org/10.1016/j.addma.2017.02.003]
- Emissivity of Common Materials, https://www.omega.com/literature/transactions/volume1/emissivitya.html, (Accessed 17 JUL 2019)
-
Marchandise, E., Mouraux, A., Plaghki, L., and Henrotte, F., “Finite Element Analysis of Thermal Laser Skin Stimulation for a Finer Characterization of the Nociceptive System,” Journal of Neuroscience Method, Vol. 223, pp. 1-10, 2014.
[https://doi.org/10.1016/j.jneumeth.2013.11.010]
-
Ahn, D. G., Lee, S. H., and Yang, D. Y., “Investigation into Thermal Characteristics of Linear Hotwire Cutting System for Variable Lamination Manufacturing (VLM) Process by Using Expandable Polystyrene Foam,” International Journal of Machine Tools & Manufacture, Vol. 42, No. 4, pp. 427-439, 2002.
[https://doi.org/10.1016/S0890-6955(01)00144-4]
-
Rack, H. J., “Physics and Mechanical Properties of Cast 17-4 PH Stainless Steel,” SAND-80-2302, Sandia National Labs., Albuquerque, NM, USA, pp. 19-24, 1981.
[https://doi.org/10.2172/6607517]
- Fieldhouse, I. B. and Lang, J. I., “Measurement of Thermal Properties,” WADD Technical Report 60-904, Armour Research Foundation, Virginia, USA, pp. 10-49, 1961.
- Lee, H. J., “A Study on Preheating and Deposition Characteristics of Super-Alloy Powders for the Development of a Novel Metal Additive Manufacturing Process Using a Plasma Electron Beam,” Ph.D. Thesis, Chosun University, 2018.
-
Hsu, C. T., Cheng, P., and Wong, K. W., “Modified Zehner-Schlunder Models for Stagnant Thermal Conductivity of Porous Media,” International Journal of Heat and Mass Transfer, Vol. 37, No. 17, pp. 2751-2759, 1994.
[https://doi.org/10.1016/0017-9310(94)90392-1]
-
Abyzov, A. M., Goryunov, A. V., and Shakhov, F. M., “Effective Thermal Conductivity of Disperse Materials. I. Compliance of Common Models with Experimental Data,” International Journal of Heat and Mass Transfer, Vol. 67, pp. 752-767, 2013.
[https://doi.org/10.1016/j.ijheatmasstransfer.2013.08.045]
- Thermal Conductivity of Nitrogen, http://www.ddbst.com/en/EED/PCP/TCN_C1056.php, (Accessed 17 JUL 2019)
- The Engineering ToolBox, “Nitrogen-Specific Heat,” https://www.engineeringtoolbox.com/nitrogen-d_977.html, (Accessed 17 JUL 2019)
- Cengel, Y. A. and Ghajar, A. J., “Heat and Mass Transfer-Fundamentals and Applications,” McGraw Hill Education, pp. 874-875, 2012.
He is master course in the Department of Mechanical Engineering, Chosun University. His research interest is development, application and numerical analysis of a metal additive manufacturing process.
E-mail: otq_center@naver.com
He is senior researcher of Extreme Fabrication Technology Group of Korea Institute of Industrial Technology. He received Ph.D from Chosun University, Korea in 2018. His research interest includes development, application and numerical analysis of a metal additive manufacturing process.
E-mail: hlee3@kitech.re.kr
He is master course in the Department of Mechanical Engineering, Chosun University. His research interest is development, application and numerical analysis of a metal additive manufacturing process.
E-mail: gustlr8213@naver.com
He is Professor at the Department of Mechanical Engineering, Chosun University. He received his M.S. and Ph.D. degrees from KAIST, Korea in 1994 and 2002, respectively. His/Her research interest includes development, application and numerical analysis of additive manufacturing process.
E-mail: smart@chosun.ac.kr
He is senior researcher of Digital Manufacturing Process Group of Korea Institute of Industrial Technology. He received Ph.D from KAIST, Korea in 2013. His research interest includes development and application of additive manufacturing process.
E-mail: sonyong@kitech.re.kr