
단결정 니켈기 초내열합금 CMSX-4의 고온 저주기 피로특성

Copyright © The Korean Society for Precision Engineering
This is an Open-Access article distributed under the terms of the Creative Commons Attribution Non-Commercial License (http://creativecommons.org/licenses/by-nc/3.0) which permits unrestricted non-commercial use, distribution, and reproduction in any medium, provided the original work is properly cited.
Abstract
Isothermal low cycle fatigue (LCF) behavior of a crystal nickel-based superalloy CMSX-4, a material for high-pressure turbine first stage rotor blade, was investigated at elevated temperatures. Strain-controlled LCF tests were performed under various test conditions, such as mechanical strain amplitude. Stress response and cyclic deformation were investigated, and equations of LCF life prediction were derived through the Coffin-Manson method. In addition, fatigue-induced fracture mechanism and microstructural evolution were investigated, using scanning electron microscopy (SEM). Results revealed that cyclic behavior of the CMSX-4 superalloy, was characterized by cyclic softening with increasing number of cycles at 800oC and 900oC. LCF of the CMSX-4 superalloy at 800oC and 900oC could be affected mainly by elastic damage in fatigue processing. Fatigue cracks were initiated in the surface oxide layer of the specimen. The plane of fracture surface was tilted toward <001> direction. The fatigue fracture mechanism was quasi-cleavage fracture at 800oC and 900oC. In all broken specimens, the γˊ phase morphology maintained cuboidal shape.
Keywords:
Ni-based single crystal superalloy, Low cycle fatigue, Life prediction, Microstructure키워드:
니켈기 단결정 초내열합금, 저주기 피로, 수명예측, 미세조직1. 서론
발전용 가스터빈은 연료와 압축된 공기를 연소 시 발생되는 고온·고압의 연소가스를 이용하여 터빈 블레이드를 회전시켜 발전하는 장치이다. 가스터빈을 이용한 발전설비의 경우 발전효율이 높고, 건설공기가 짧은 이점이 있다.1 또한, 최근에는 유럽과 북미지역에서 온실가스 감축과 관련된 규제가 강화됨에 따라 천연가스를 사용하는 가스터빈의 경우 친환경 발전 시스템으로써 전세계적으로 기술개발에 관심이 집중되고 있다.2 가스터빈의 발전효율 향상을 위하여 고온·고압화 추세에 따라 가스터빈의 핵심 부품들에 대한 소재의 초내열합금, 정밀가공, 열차폐 코팅 등의 다양한 기술 개발이 활발히 이루어지고 있다.3-5 단결정 초내열합금은 결정입계를 완전히 제거하여 하나의 결정으로 주조한 것으로 방향에 관계없이 동등한 수준의 물성을 갖는다. 기존의 다결정 및 일방향 응고 합금에 비하여 고온에서 변형 저항성, 크리프 저항성, 내산화 및 내부식성 등이 월등히 우수하다. 이러한 특성에 따라 단결정 니켈기 초내열합금은 터빈 블레이드, 로터 등 발전시스템의 핵심 부품 소재로서 널리 사용되고 있다.6
가스터빈의 핵심부품 중 1단 블레이드는 가동 시 초고온 연소가스의 직접적인 노출과 동시에, 3,600 rpm 정도의 고속 회전에 의해 원심력을 받게되어 기계적 피로 및 크리프, 열화 등에 의하여 결함이 발생될 수 있으며, 이러한 결함은 파손으로 이어져 블레이드의 수명을 크게 저하시킨다.7 피로파괴는 가스터빈 블레이드의 주요 파괴모드이며, 높은 하중 범위에서 반복 응력-변형률 반응과 재료의 거동은 변형률 제어 조건하에서 가장 잘 모델화시킬 수 있다. 따라서 가스터빈을 이용한 발전설비의 신뢰성을 확보하기 위하여 블레이드의 변형률 제어 조건하에서 저주기 피로 특성에 대한 연구는 매우 중요하다. 하지만, 특히 단결정 니켈기초내열합금의 저주기 피로특성에 대한 국내·외에서 선행연구는 부족한 실정이다.
본 연구에서는 가스터빈 블레이드의 작동환경을 고려하여 800°C, 900°C 온도 조건에서 단결정 니켈기 초내열합금 소재의 저주기 피로특성에 대하여 연구를 수행하였다. 다양한 변형률 진폭 조건에서 변형률 제어하 저주기 피로시험을 수행하였다. 온도별 주기적 응력 반응 및 히스테리시스 루프에 대하여 비교·분석하였으며, Coffin-Manson 식을 이용한 변형률과 피로수명과의 관계식을 도출하였다. 시험 후 파손된 시험편의 미세조직 분석을 통해 피로파괴 메커니즘과 저주기 피로에 의해 유발된 미세조직 변화에 대하여 고찰하였다.
2. 재료 및 시험방법
2.1 재료 및 시험편
본 연구에서 Re이 3% 첨가된 2세대 단결정 니켈기 초내열합금인 CMSX-4 소재를 사용하였으며, CMSX-4 소재의 화학적 조성을 Table 1에 나타내었다. 일반적으로 단결정 합금은 블레이드 회전체의 반경 방향에 재료의 결정립 성장방향을 <001> 방향으로 일치시킨다. 이는 해당방향에 대하여 다른 결정방향 대비 크리프 및 피로특성이 우수하기 때문이다.8 한국로스트왁스 사로부터 직경 23 mm, 길이 200 mm의 봉상형태로 정밀주조 및 진공 열처리하여 제작된 <001> 방위를 갖는 CMSX-4 소재를 입수하였다. 입수한 CMSX-4 소재의 결정방향을 XRD (X-ray Diffractometer)를 이용하여 분석한 결과 <001> 방위로부터 평균적으로 8° 이내의 편차를 확인하였다.
CMSX-4 초내열합금은 2가지 주요 고용강화 상 γ-Matrix와 γʹ-Precipitates이 존재한다. 두 상 모두 Face-Centered Cubic (FCC) 격자구조를 갖으며, γʹ은 Ni3 (Al, Ti) 화학양론적 조성으로 Ll2 구조로 정렬 되어있다.9 Fig. 1에 SEM (Scanning Electron Microscopy)을 이용하여 관찰한 진공 열처리 후 CMSX-4 소재의 미세조직을 나타내었다. γ-Matrix (옅은 회색)에 규칙격자 형태의 γʹ-Precipitates (진한 회색)으로 구성된 미세조직을 확인하였고, γ/γʹ의 체적 분율은 65 %이며, γ 채널의 폭은 약 30 - 70 nm, γʹ의 크기는 약 0.4 - 0.7 μm로 측정되었다.
저주기 피로 시험편은 ASTM E60610에 명시된 규격에 따라 평행부 길이 22 mm에 직경 8 mm로 설계 및 제작하였다. Fig. 2에 저주기 피로 시험편의 형상과 치수를 나타내었다. 시험편 표면의 기계 가공선 자국에 의한 균열 발생을 방지하기 위해, 저주기 피로시험 전 제작한 모든 시험편은 하중부가 방향과 평행한 방향으로 연마 가공을 하였다.
2.2 시험방법
고온 저주기 피로시험에서는 Shimadzu사의 최대 250 kN 용량 전기모터식 만능시험기(Model: AG-250 kNXplus), 고온용 세라믹형 변형률 측정 게이지, 데이터 저장용 DAQ (Data Acquisition System) 및 랩탑 컴퓨터, 고온환경을 구성하기 위한 최대 1,400°C 용량의 전용 퍼니스와 온도 컨트롤러로 구성된 시험장치를 사용하였고, 전체 시험장치 모습을 Fig. 3에 나타내었다. 시험 시작 전압축 시 버클링 현상을 방지하기 위해 우드메탈 그립을 사용하여 시험기의 하중선을 정렬하였다. K타입의 열전대를 시험편 표면에 부착하여 시험 목표온도에 도달 한 뒤 시험편 및 시험지그의 열평형을 위하여 1시간 동안 유지하였다. 가스터빈 블레이드의 실제 사용 환경조건을 고려하여 800°C, 900°C에서 변형률 진폭이 1.0 - 1.6% 범위에서 시험편 평행부에 세라믹형 변위 측정기를 장착하여 변형률 제어 방식으로 R = -1 변형률 비율로 저주기 피로시험을 수행하였다. 시험속도에 의한 영향을 배제하기 위하여 시험 주기수를 1Cycle에 소요되는 시간이 3분이 되도록 0.0056 Hz로 고정하였다. Table 2에 저주기 피로시험 조건을 정리하여 나타내었다. 저주기 피로시험 중 하중 및 변위 신호를 DAQ를 이용하여 기록하고, 시험편 파단 시 시험을 종료하고 파단수명을 기록하였다. 파손 메커니즘과 미세조직 변화를 관찰하기 위해, 피로시험 종료 후 시험편의 작용하중 방향과 평행한 방향으로 절단하였고, 기계적 연마 및 CuSO4(5 g) + HCl(25 ml) + H2O(20 ml) + H2SO4(5 ml) 용액에서 화학적 에칭 작업을 거쳐 SEM을 이용하여 시험편의 미세조직을 관찰하였다.
3. 시험결과 및 고찰
3.1 주기적 응력반응 거동
Fig. 4에 온도별 서로 다른 전변형률의 파단 사이클과 응력진폭간 관계를 나타내었다. 800°C, 900°C에서 응력진폭의 변화는 사이클이 진행될수록 응력진폭이 감소 하는 피로연화 경향을 나타내었다. 이는 재료 내부의 성질이 전위의 이동이 쉬워지는 방향으로 변하게 되는 것이다.11 800°C의 경우 모든 전변형률 조건에서 초기에 주기적 연화반응이 나타나고 이후 안정화된 응력거동이 유지된다. 900°C의 경우 모든 전변형률 조건에서 파단 될 때까지 지속적으로 주기적 연화반응이 나타났다. 동일 온도조건에서 전변형률이 클수록 연화반응 정도가 증가하였다. 800°C의 경우 모든 전변형률 조건에서 안정화된 응력거동 이후 전체 피로수명의 25% 내에서 연화현상이 일정하게 진행되다가 최대 20% 응력감소 시점까지 도달했을 때 순간적으로 파단되는 형태를 나타내었다. 900°C의 경우 모든 전변형률 조건에서 안정화된 응력거동 이후 연화현상이 일정하게 진행되다가 전체 피로수명의 10% 내에서 연화현상이 급격히 일어나 최대 37% 하중감소 시점까지 도달했을 때 파단되는 형태를 나타내었다.
3.2 히스테리시스 루프
Fig. 5에 온도별 파단수명의 절반에서 얻어진 안정화된 히스테리시스 루프를 나타내었다. 온도가 증가함에 따라 응력진폭은 감소하는 경향을 나타내었다. 이는 일정 변형률 제어식 피로하중의 경우 반복 연화현상 때문에 온도의 증가에 따라 동일 변형률 조건에서 시험편에 가해지는 응력이 감소하게 된다.
히스테리시스 루프 내의 면적을 계산하면 온도에 상관없이 모든 전변형률 조건에서 소성변형이 거의 발생하지 않아 히스테리시스 루프 내의 면적은 작지만 온도가 증가할수록 소성 변형량이 증가하면서 면적도 증가하는 경향을 나타내었다. 이를통해 900°C에서 800°C보다 피로연화 작용의 정도가 더 크게 나타남을 확인할 수 있다.
3.3 저주기 피로수명 예측
고온 저주기 피로수명 거동에 대한 수명예측 방법은 현상학적 모델(Phenomenological Model)에 의한 방법과 물리적 현상에 근거한 모델(Physically-Based Model)에 의한 방법으로 분류할 수 있다. 현상학적 모델은 매개변수 관계식이나 피로와 크리프에 의한 손상정도를 평가한다. 현상학적 모델은 손상에 대한 물리적인 의미는 없지만, 피로수명 예측 모델에 있어서 일반적이고 적용하기가 쉬운 모델이다.12 본 논문에서는 현상학적 수명예측 모델 중 저주기 피로수명을 평가하는 가장 대표적인 방법인 Coffin-Manson의 식과 Basquin의 식을 사용하였다. 식(1)과 같은 형태로 파단수명의 절반에 해당하는 반수명 에서의 안정화된 응력-변형률 선도을 이용하여 변형률을 탄성 및 소성 성분으로 나누고, 최소자승법을 이용하여 피로강도계수(b), 피로강도 지수(σf'), 피로연성 지수 (c), 피로연성 계수(εf') 등을 구하는 방법이다.13-15
(1) |
Fig. 6에 Coffin-Manson 및 Basquin식의 파라미터를 구하기 위한 탄성 및 소성 변형률-수명 선도와 전변형률-수명 선도를 나타내었으며, Table 3에 최소자승법을 이용하여 도출한 Coffin-Manson 및 Basquin 식의 파라미터 를 정리하여 나타내었다. 도출한 Coffin-Manson와 Basquin 식의 파라미터를 이용하여 피로 수명 예측식을 표현하면 800°C의 경우 식(2)와 900°C의 경우 식(3)과 같은 형태이다.
(2) |
(3) |
온도와 상관없이 전변형률 진폭이 감소할수록 소성 변형률 진폭이 눈에 띄게 줄어듬을 확인할 수 있다. 하지만, 소성 변형률은 매우 낮은 값으로 나타나 탄성 변형률이 총 변형률과 유사한 값을 나타내었다. 그러므로 탄성 변형률 선도와 소성 변형률 선도의 교차점인 천이수명은 1Cycle 미만인 수명에서 나타났으며, 이는 탄성 변형률에 의해 저주기 피로수명이 지배되는 것을 알 수 있다.
3.4 파손 메커니즘 분석
저주기 피로시험 후 파손된 시험편의 작용하중 방향과 평행한 방향에 대하여 파단면 분석을 수행하였고, 분석결과 중 온도별 대표 사진을 Fig. 7에 나타내었다. 시험온도 및 전변형률 범위에 관계없이 모든 시험편의 표면부에서 균열이 시작되어 내부로 전파하여 파단된 양상을 확인하였으며, 시험편의 표면부에 다발성 균열이 존재하는 것을 확인하였다(Fig. 7(c)). 강정구 등16은 <001> 결정방향을 갖는 CMSX-4 소재에 대한 저주기 피로시험 (R = 0) 결과 950°C에서 단결정 초내열합금의 표면산화가 급속하게 진행하게 되고, 저주기 피로균열은 내부균열 보다 표면 산화층에서 우선적으로 발생한다고 보고하였으며, 이는 본 시험 결과와 일치함을 확인하였다.
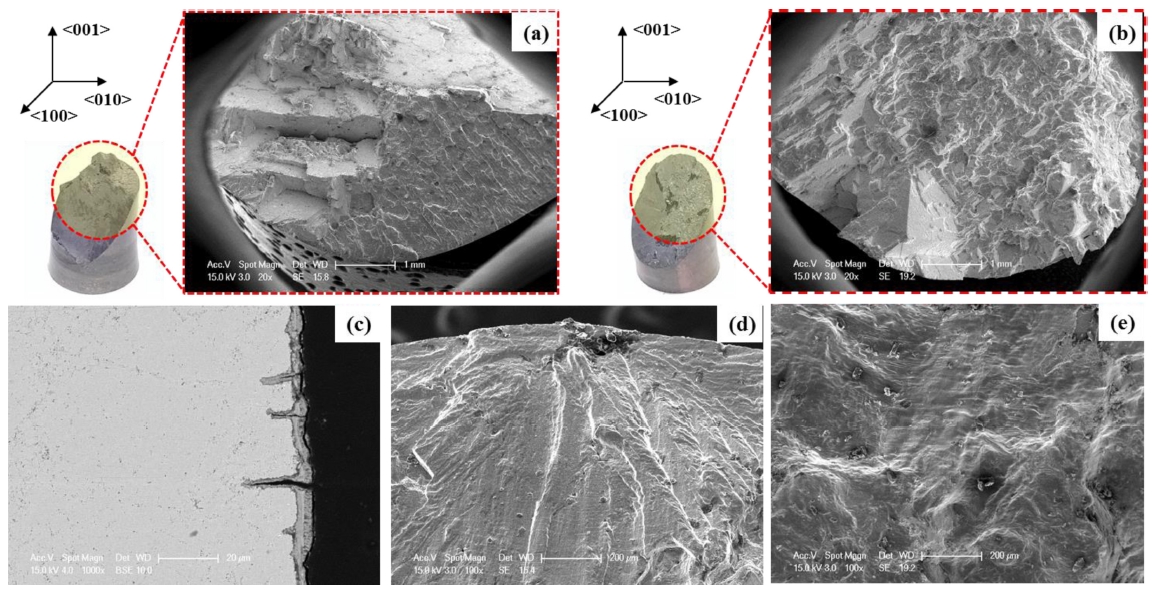
Fatigue fractographies (a) Δεt = 1.31 % at 800°C, (b) Δεt = 1.44% at 900°C, (c) surface oxide crack, (d) beach mark, (e) striation
저주기 피로시험을 통해 산화된 표면에서부터 반복 하중으로 인하여 형성되는 균열 진전의 스트리에이션이 관찰되었다(Fig. 7(e)). 800°C, 900°C에서 공통적으로 파단면에 몇 개의 평면이 관찰되었다. 이는 균열의 성장은 임계 균열길이에 도달 할 때까지 계속 되며, 처음에는 최대 인장응력이 작용하는 <100> 방향(작용하중 방향과 수직 방향)으로 γ'에 비해 강하지 않은 γ 상을 따라 전파된 뒤 다른 평면을 따라 진전하기 때문이라고 판단된다.16 소성 변형이 발생하는 동안, 단결정 초내열합금은 결정 평면상 의 슬립에 의해 변형된다.
면심입방정에 대한 3가지 주슬립 시스템(팔면체 슬립 {111}<011>, 팔면체 슬립 {111}<112>, 입방체 슬립 {100}<110>)이 있다.17 800°C, 900°C에서는 팔면체 슬립 시스템 {111}[011]에 의해 파단면의 평면은 <001> 방향으로 약 40 - 50° 기울어진 형태를 확인하였다. 또한 대부분 층상으로 취성 파괴된 파면과 연성 파면이 일부 혼재한 준 벽계파괴 특성을 나타냄을 확인하였다.
3.5 미세조직 변화
Fig. 8에 γ'의 조대화 및 구상화 등 형태 변화를 분석하기 위해 SEM을 이용하여 촬영한 파손된 시험편 종단면의 모습을 나타내었다. γ/γ'의 체적분율, γ 채널의 폭, γʹ의 크기는 저주기 피로시험 전 상태에 비해 큰 차이가 발생하지 않았다. γ'의 형태는 저주기 피로 시험 전(Fig. 1)과 비교하였을 때 온도별 시험한 모든 시험편에서 입방형태를 비교적 잘 유지하고 있다. 그리고 모든 시험편에서 작용응력 축을 따라 움직이는 전위를 효과적으로 방해하여 피로수명에 긍정적인 역할을 한다고 알려진 작용응력축에 수직인 방향으로 래프팅 현상 또한 관찰할 수 없었다. 800°C, 900°C에서 시험편의 파단면 근처에 γ' 상과 γ 기지를 전단시키는 슬립 밴드도 존재함을 확인하였다. 이러한 슬립 밴드는 주기적인 소성 변형이 연속적으로 축적됨에 따라 생성될 수 있다. 또한 피로균열 개시점에 대한 우선적인 위치가 될 수 있으며, 균열성장은 더욱 용이하게 만들 수 있다.17 본 시험조건에서 수행한 저주기 피로시험결과 소성 변형률이 매우 작게 나타나 주기적인 소형변형의 영향을 받는 γ'의 조대화 및 래프팅 현상은 확인할 수 없었다.
4. 고찰
CMSX-4 소재의 주기적 응력반응은 온도에 의존하는 거동을 보인다. Barnard 등은 <001> 결정방향을 갖는 CMSX-4에 대한 일축 인장하의 저주기 피로시험(R = -1) 결과로부터 750°C의 경우 주기적 경화현상이 지배적 이며, 950°C의 경우 주기적 연화현상이 지배적이라고 보고하였다.18 Barnard 등이 수행한 연구결과와 본 연구의 시험결과를 종합하여 첫번째 사이클에서 최대 응력진폭과 중간수명에서 최대 응력진폭을 Fig. 9에 나타내었다. 750°C에서는 첫번째 사이클 대비 중간수명에서 최대 응력진폭이 증가하는 주기적 경화현상을 나타내었다. 반면, 800°C, 900°C, 950°C에서는 첫번째 사이클 대비 중간수명에서 최대 응력진폭이 감소하는 주기적 연화현상을 나타내었으며, 온도가 증가 할수록 주기적 연화작용에 따른 최대 응력진폭 감소량은 증가하였다.
Sengupta 등은 CMSX-4 소재를 이용하여 상온 및 고온 인장시험을 통해 온도에 따른 인장특성을 평가하였다.19 Fig. 10에 CMSX-4 소재의 온도에 따른 항복강도 변화를 나타내었다. 온도가 증가할수록 항복강도는 증가하여 800°C 부근에서 최대값을 갖는다. 800°C보다 높은 온도에서는 온도가 증가할수록 항복강도는 감소하는 경향을 나타낸다.
그러므로 본 연구 결과와 Sengupta 등의 연구 결과를 종합하여 CMSX-4 소재의 경우 750°C와 800°C 사이 온도에서 주기적 경화현상과 주기적 연화현상의 천이구간이 존재함을 판단할 수 있다.
CMSX-4 소재의 온도별 기계적 변형률-파단수명 선도를 Fig. 11에 나타내었다. 온도에 상관없이 기계적 변형률이 증가할수록 파단수명이 점차 감소하는 경향을 나타내었다.
기계적 변형률이 1.5% 보다 작을 경우, 동일한 기계적 변형률에서 900°C에서 LCF 수명이 800°C보다 길게 평가되었다. 이는 일정 변형률 제어식 피로하중의 경우 주기적 연화되는 현상으로 인해 온도의 증가에 따라 작용 응력이 감소하게 되어 피로저항이 감소하기 때문이다.
CMSX-4 소재의 온도별 최대응력-파단수명 선도를 Fig. 12에 나타내었다. 선도상 동일한 최대응력 조건에서 800°C에서의 LCF 수명이 900°C보다 길게 평가되었다.
5. 결론
니켈기 단결정 초내열합금 CMSX-4에 대하여 800°C와 900°C에서 다양한 변형률 진폭 조건에서 수행한 저주기 피로특성 분석결과 다음과 같은 결론을 얻었다.
1. 800°C와 900°C에서 저주기 피로시험 동안의 응력 거동은 주기적 연화반응을 나타내었다. 선행 연구결과와 본 연구의 시험결과를 종합하여 CMSX-4 소재의 경우 750°C와 800°C 사이 온도에서 주기적 경화 현상과 주기적 연화현상의 천이구간이 존재함을 판단할 수 있다.
2. 온도별 히스테리시스 루프 내의 면적을 계산하면 800°C, 900°C에서 소성변형이 거의 발생하지 않아 면적은 작지만 온도가 증가할수록 소성변형량이 증가 하면서 면적도 증가하는 것을 확인하였다. 이를통해 900°C에서 800°C보다 피로연화 작용의 정도가 더 크게 나타남을 확인하였다.
3. 온도별 Coffin-Manson 및 Basquin식을 이용한 변형률과 피로수명과의 관계식을 도출하여 저주기 피로수명 예측식을 제시하였다.
4. 시험온도 및 전변형률 범위에 관계없이 모든 시험편의 표면부에서 균열이 시작되어 내부로 전파하여 파단된 양상을 확인하였으며, 시험편의 표면부에 다발성 균열이 존재하는 것을 확인하였다. 800°C, 900°C에서는 팔면체 슬립 시스템 {111}[011]에 의해 파단면의 평면은 <001> 방향으로 약 40 - 50° 기울어진 형태를 확인하였다. 또한 대부분 층상으로 취성 파괴된 파면과 연성 파면이 일부 혼재한 준 벽계파괴 특성을 나타냄을 확인하였다.
5. 저주기 피로에 의해 유발된 미세조직 변화는 SEM을 통하여 관찰한 γ'의 조대화 및 래프팅 현상은 확인할 수 없었다.
NOMENCLATURE
R : | Strain ratio |
Δεt : | Total strain range |
Δεe : | Elastic strain range |
Δεp : | Plastic strain range |
Nf : | Cycles to failure |
E : | Young’s modulus |
b : | Fatigue strength exponent |
c : | Fatigue ductility exponent |
σʹf : | Fatigue strength coefficient |
εʹf : | Fatigue ductility coefficient |
Acknowledgments
본 연구는 산업통산자원부(MOTIE)와 한국에너지기술 평가원(KETEP)의 지원을 받아 수행한 연구 과제입니다(No. 20161120100370). 이 논문은 2015년도 정부(미래창조 과학부)의 재원으로 한국연구재단의 지원을 받아 수행된 연구임(No. 2015R1A2A1A10055230).
REFERENCES
-
Lee, J.-M., Wee, S., Yun, J., Song, H., Kim, Y., et al., “Life Prediction of IN738LC Considering Creep Damage Under Low Cycle Fatigue,” International Journal of Precision Engineering and Manufacturing-Green Technology, Vol. 5, No. 2, pp. 311-316, 2018.
[https://doi.org/10.1007/s40684-018-0033-6]
-
Kim, Y., Lee, J.-M., Song, H., Han, K., Koo, J.-M., et al., “TBC Delamination Life Prediction by Stress-Based Delamination Map,” International Journal of Precision Engineering and Manufacturing-Green Technology, Vol. 4, No. 1, pp. 67-72, 2017.
[https://doi.org/10.1007/s40684-017-0009-y]
-
Al-Zurfi, N. and Turan, A., “LES of Rotational Effects on Film Cooling Effectiveness and Heat Transfer Coefficient in a Gas Turbine Blade with One Row of Air Film Injection,” International Journal of Thermal Sciences, Vol. 99, pp. 96-112, 2016.
[https://doi.org/10.1016/j.ijthermalsci.2015.08.005]
-
Yao, Y., Zhang, J.-Z., and Wang, L.-P., “Film Cooling on a Gas Turbine Blade Suction Side with Converging Slot-Hole,” International Journal of Thermal Sciences, Vol. 65, pp. 267-279, 2013.
[https://doi.org/10.1016/j.ijthermalsci.2012.10.004]
-
Tawancy, H., Mohammad, A., Al-Hadhrami, L., Dafalla, H., and Alyousf, F., “On the Performance and Failure Mechanism of Thermal Barrier Coating Systems Used in Gas Turbine Blade Applications: Influence of Bond Coat/Superalloy Combination,” Engineering Failure Analysis, Vol. 57, pp. 1-20, 2015.
[https://doi.org/10.1016/j.engfailanal.2015.07.023]
- Yu. Y, “Materials Information Platform 2011,” Korea Institute of Materials Science, pp. 393-404, 2011.
-
Lee, D., Kang, T., Koo, J.-M., Seok, C.-S., and Song, S.-J., “A Study of the LCF Characteristics of the NI-Based Superalloy IN738LC,” International Journal of Precision Engineering and Manufacturing, Vol. 16, No. 4, pp. 775-780, 2015.
[https://doi.org/10.1007/s12541-015-0102-5]
- Segersäll, M., “Nickel-Based Single-Crystal Superalloys: The Crystal Orientation Influence on High Temperature Properties,” Linköping University Electronic Press, 2013.
-
Kraft, S., Zauter, R., and Mughrabi, H., “Aspects of High Temperature Low Cycle Thermomechanical Fatigue of a Single Crystal Nickel Base Superalloy,” Fatigue & Fracture of Engineering Materials & Structures, Vol. 16, No. 2, pp. 237-253, 1993.
[https://doi.org/10.1111/j.1460-2695.1993.tb00755.x]
- ASTM International, “Standard Test Method for Strain-Controlled Fatigue Testing,” ASTEM E606, 2005.
-
Hwang, K. T., Kim, J. H., Yoo, K. B., Lee, H. S., and Yoo, Y. S., “Low-Cycle Fatigue in NI-Base Superalloy IN738LC at Elevated Temperature,” Transactions of the Korean Society of Mechanical Engineers. A, Vol. 34, No. 10, pp. 1403-1409, 2010.
[https://doi.org/10.3795/KSME-A.2010.34.10.1403]
- Kang, M.-S., “Low Cycle Fatigue Behavior of 12Cr Steel for Thermal Power Plant Steam Turbine,” Journal of the Korean Society for Precision Engineering, Vol. 19, No. 8, pp. 71-76, 2002.
- Coffin Jr, L. F., “A Study of the Effects of Cyclic Thermal Stresses on a Ductile Metal,” Transactions of the American Society of Mechanical Engineers, Vol. 76, pp. 931-950, 1954.
- Manson, S. S., “Behavior of Materials Under Conditions of Thermal Stress,” NACA Rep 1170, pp. 317-350, 1954.
- Basquin, O., “The Exponential Law of Endurance Tests,” in Proc. of Am Society Test Mater, Vol. 10, pp. 625-630, 1910.
-
Kang, J. G., Hong, H. U., Choi, B. G., Kim, I. S., Jo, C. Y., et al., “Deformation and Failure Behavior During Thermo-Mechanical Fatigue of a Nickel-Based Single Crystal Superalloy,” Journal of the Korean Institute of Metals and Materials, Vol. 49, No. 2, pp. 112-120, 2011.
[https://doi.org/10.3365/KJMM.2011.49.2.112]
-
Shi, Z., Wang, X., Liu, S., and Li, J., “Low Cycle Fatigue Properties and Microstructure Evolution at 760°C of a Single Crystal Superalloy,” Progress in Natural Science: Materials International, Vol. 25, No. 1, pp. 78-83, 2015.
[https://doi.org/10.1016/j.pnsc.2015.01.009]
-
Barnard, N., MacLachlan, D., Jones, N., Mason-Flucke, J., Bagnall, S.,et al., “Low Cycle Fatigue of CMSX-4 In Off-Axis Orientations and the Effect of a Multi-Axial Stress State,” Superalloys 2012, pp. 293-300, 2012.
[https://doi.org/10.1002/9781118516430.ch32]
-
Sengupta, A., Putatunda, S., Bartosiewicz, L., Hangas, J., Nailos, P., et al., “Tensile Behavior of a New Single-Crystal Nickel-Based Superalloy (CMSX-4) at Room and Elevated Temperatures,” Journal of Materials Engineering and Performance, Vol. 3, No. 1, pp. 73-81, 1994.
[https://doi.org/10.1007/BF02654502]
Ph.D. candidate in the Graduate School of Mechanical Engineering at Sungkyunkwan University. His research interests include the mechanical properties and microstructures of superalloys.
E-mail: aegulj@skku.edu
Professor in the Department of Mechanical Engineering at Sungkyunkwan University. His research interests include the prediction of fracture behavior of structural materials .
E-mail: seok@skku.edu
Ph.D. candidate in the Graduate School of Mechanical Engineering at Sungkyunkwan University. His research interests include the lifetime prediction and reliability assessment of industrial facilities.
E-mail: sinkill2@skku.edu
Vice President in the Korea Lost-Wax Corporation. His research interests include the quality control and guarantee of precision castings.
E-mail: eschung@lostwax.co.kr
R&D Team Leader in the Korea Lost-Wax Corporation. His research interests include the mold design.
E-mail: bgyun@lostwax.co.kr
Senior researcher in the Korea Lost-Wax Corporation. His research interests include the development of precision casting process.
E-mail: ksh0528@lostwax.co.kr