
탄소섬유복합재 가공용 CRD-워터젯 복합가공기의 드릴링 가공성 평가

Copyright © The Korean Society for Precision Engineering
This is an Open-Access article distributed under the terms of the Creative Commons Attribution Non-Commercial License (http://creativecommons.org/licenses/by-nc/3.0) which permits unrestricted non-commercial use, distribution, and reproduction in any medium, provided the original work is properly cited.
Abstract
Transportation industries, such as aerospace and automotive demand high efficiency using lightweight parts. Carbon Fiber Reinforced Plastics (CFRP) present promising materials for transportation industry parts due to their lightweight and high-strength properties. Forming and machining processes are required to manufacture parts from carbon fiber composite materials. The near-net shaping process forms the parts, and the final accurate shape and hole are accomplished using the machining process. However, high-strength carbon fiber chips and dust from the machining process cause cutting tool wear and low productivity. The hybrid CRD (Cutting, Routing and Drilling)/water-jet machine improves tool life and productivity because its water-jet process, employed before the mechanical machining process cuts roughly without chips and dust. In this study, the hybrid CRD/water-jet machine we developed was introduced and its machining performance was evaluated using a drilling process. The delamination factor and surface roughness of drilled holes were compared with the results from a conventional machine tool.
Keywords:
Carbon fiber reinforced plastics, Hybrid machine tool, Universal fixture, CFRP dust collector, Delamination키워드:
탄소섬유복합재, 복합가공기, 유연지그, CFRP 집진장치, 박리1. 서론
자동차·항공 등 수송산업분야에서 고효율, 진환경 제품에 대한 수요가 증가하고, 국내외에서 수송산업 제품에 대한 환경관련 규제가 증가하면서 친환경, 고효율 제품에 대한 수요가 증가하고 있다. 특히, 기존의 금속소재를 기반으로 하여 고장력 강판, 설계 최적화 방법 등으로 기존의 강도를 유지하면서 전체 중량을 최소화 하는 방법을 사용하고 있지만, 점차 새로운 특성을 가진 경량신소재를 부품으로 적용하여 경량화 부품 개발을 진행하고 있다. 탄소섬유복합재(CFRP, Carbon Fiber Reinforced Plastics)는 고강도의 탄소섬유와 플라스틱 메트릭스를 이용하여 강도를 높인 복합재료로서 탄소섬유의 높은 강도와 원하는 방향의 이방성을 정의할 수 있으면서, 동시에 플라스틱의 뛰어난 성형성을 가지고 있는 복합재료이다.1,2 탄소섬유복합재는 경량이면서 고강도, 고탄성 소재로써 과거에는 전투기, 우주왕복선 등과 같은 일부 고가의 특수분야에서만 주로 사용하였으나 최근 가격 경쟁력을 확보하면서 민간 항공기, 자동차, 신재생 에너지, 선박 등 다양한 분야에서 수요가 크게 증가하고 있다.3 탄소섬유복합재와 관련한 소재 생산에 관한 연구는 과거부터 현재까지 많은 연구가 진행되었지만, 이를 제품화 하기 위한 가공시스템 및 가공공정에 관한 연구는 현재까지도 진행되고 있는 분야이다. 탄소섬유복합재는 고강도, 경량 소재로서 우수한 기계적 성질을 가지고 있지만, 우수한 기계적 성질 때문에 최적의 가공이 어렵고 적층 성형하는 구조를 가지고 있어 가공 시 결함이 쉽게 발생하고, 기존의 금속소재와는 다른 결함이 발생하여, 가공생산성을 증가시키는데, 어려움이 있다.4 상대적으로 가격이 높은 탄소섬유복합재 소재와 성형가공공정 비용 때문에, 제품화 전단계인 가공공정에서는 상대적으로 안전한 가공조건을 설정하며, 이로 인하여 생산성이 낮아져, 탄소섬유복합재의 기계부품 적용 확산에 장애물이 되고 있다. 기존의 절삭공정을 적용할 경우, 가공특성이 기존의 메탈재료 가공특성과 달라 결함 없이 가공하기가 어렵다.5,6 따라서 본 연구에서는 고품질, 고생산성의 탄소섬유복합재 부품 가공을 위해 CRD (Cutting, Routing, and Drilling) - 워터젯 복합가공기를 개발하였으며, 드릴링 가공을 통해 개발된 장비의 가공성능을 평가하였다. 실제 항공기용 부품에 사용되는 탄소섬유복합재 소재를 이용하여 소재의 결함(박리, 뜯김)을 평가하였다.
2. 탄소섬유복합재 가공을 위한 CRD-워터젯 복합가공시스템 개발
2.1 CRD-워터젯 복합가공시스템
Fig. 1은 탄소섬유복합재의 고품질, 고생산성 가공을 위해 개발된 CRD-워터젯 복합가공시스템을 보여준다, 개발된 복합가공시스템은 폭(W) 10 m, 깊이(D) 11 m, 높이(H) 6 m의 크기를 가지고 있으며 CRD 헤드와 워터젯 헤드를 가지고 있다. 대면적의 부품을 빠른 속도로 이송하며 가공하기 위해, 최대 25,000 mm/min의 이송이 가능하며, 위치정밀도 12 μm/mm, 반복정밀도 10 μm/mm로 개발되었다. 최고속도 25,000 mm/min의 고속·고정밀 이송계는 가공 시간 단축과 가공 품질 저하 방지을 동시에 만족해야만 하는 요소로써, 겐트리 타입(Gentry Type) 공작기계의 경우 칼럼(Column)이 이송하는 칼럼 이송형과 크로스레일(Cross Rail)이 이송하는 크로스레일 이송타입이 있다. 칼럼 이송형의 경우 이송부의 무게중심이 크로스레일 이송타입보다 높기 때문에 이송시 발생하는 잔류진동이 없어지는 시간이 길다는 단점이 있다. 그렇기 때문에 본 장비는 크로스레일 이송형으로 고속·고정밀 이송이 가능하도록 설계 및 제작 되었다. 1개의 서보모터와 기어박스를 이용하여 축 이송시 백래쉬(Backlash)가 존재하게 된다. 이러한 백래쉬 제거를 위한 방법 중 더블 랙 & 피니언(Double Rack & Pinion) 방식을 이용하여 제로백래쉬(Zero Backlash)를 구현할 수 있도록 설계 하였다.
겐트리 타입 장비는 크로스레일이 이송부 상단에서 축방향 이송을 하기 때문에 크로스레일의 처짐이 발생할 수 밖에 없는 구조이다. 이러한 크로스레일의 처짐은 크로스레일이 부착되어 있는 새들(Saddle), 램(Ram) 등의 처짐으로 이어지며, 최종적으로 스핀들의 위치에도 영향을 미치게 된다. 이러한 크로스레일의 처짐을 방지하기 위하여 크로스레일 상단에 처짐방지장치를 장착하여 크로스레일의 처짐을 보상해 줌으로써, 가공정밀도를 향상시킬 수 있다.
2.2 유연지그시스템
탄소섬유복합재는 주도 항공기, 자동차 등의 외부 마감 재료 및 구조재로 사용되는데, 용도에 따라 다양한 형상의 소재가 많으며, 두께가 얇은 판재 형태의 부품 비중이 높다. 이러한 형태의 소재는 가공시 소재의 고정을 어떻게 해야 하는 것인가 하는 문제 와 연결될 수 있다. 이러한 문제를 해결하기 위해 각각의 부품의 형상을 가지고 있는 고정용 전용 지그가 아닌 다양한 자유 곡면에 대응할 수 있는 유연 지그의 개발이 필요하다. 유연 지그는 소재의 다양한 형상과 위치에 즉각 대응할 수 있으며, CFRP 뿐만 아니라 타 소재에도 사용할 수 있기 때문에 유연성이 높은 장치로 활용될 수 있다.
유연지그모듈은 지지대, 흡착컵 및 틸팅부를 포함한 흡착 틸팅부와 구동부로 이루어져 있다. 흡착 틸팅부는 기계 가공 중 공작물을 고정하기 위하여 진공 흡착컵을 사용한다. 이는 볼 조인트를 중심으로 공작물의 형상에 적합하게 수동 틸팅 한다. 흡착 틸팅부의 상단에는 지지대가 있으며 이 지지대의 중심과 공작물이 접촉하게 된다. 구동부는 z축으로 변형 가능하며, 이는 흡착 틸팅부를 공작물 형상에 맞게 이송시키는 역할을 한다. 또한 유연지그시스템의 유연성을 향상시키기 위하여, 각각의 구동부는 기존의 초기 위치에서 x축 방향으로 움직이는 것이 가능하다.
Fig. 2는 28개의 상하 이동이 가능한 모듈을 가지는 유연지그시스템을 보여준다. 유연지그는 소재의 곡면부나 높이에 따라 상·하로 16.5 mm 이동이 가능하며, 이를 이용하여 소재의 높이에 따라 필요한 부분의 지그의 높낮이를 조정하여 고정이 가능하도록 설계하였다. 이러한 유연지그는 여러 개가 하나의 부품처럼 동시에 제어가 되어야 하며, 가공물의 크기에 따라 구역별 제어도 가능하여야 한다. 유연지그는 흡착컵이 가공물에 닿은 상태에서 흡착하여 고정을 하는 진공방식(Vacuum Type)의 클램핑 장치이다. 이러한 진공장치 역시 각각의 유연지그에 적용되어 제어를 하는 형태이므로, 다양한 형상의 가공물에 대응이 가능한 것이다. 결과적으로 이러한 28개의 개별제어가 가능한 모듈을 구성하여, 5 m × 3 m 크기의 최소두께 1 mm 자유곡면 부품을 고정할 수 있다.
2.3 탄소섬유복합재 가공분진 집진모듈
탄소섬유복합재는 직경 수 μm 크기를 가지는 다수의 탄소섬유로 구성되어있어, 섬유가 절단되면서 미세한 분진 형태로 가공칩이 발생한다. 이러한 분진 형태의 칩은 절삭가공시 공구의 마모를 촉진시키며, 가공품질과 공구수명을 떨어트리는 주요한 원인이 되며, 가공시 주변 작업자와 기계장치에도 영향을 주어, 가공시 칩을 얼마나 효율적으로 집진하는 것이 중요하다. 따라서 가공시 발생한 분진의 크기를 고려하여 분진 흡입장치를 설계하였으며, 이를 이용한 분진 성능을 평가하였다.
분진 흡입장치는 분진이 발생하는 위치와 가장 가까운 곳에서 흡입하는 것이 중요하기 때문에, 가공이 발생하는 스핀들에 직접 부착하는 형태로 설계하였다. Fig. 3직경 6 mm의 드릴 공구가 최대 30,000 rpm으로 회전할 때 설계된 후드 내에서의 유동 해석결과를 보여주고 있다. 공구 주변에서 최대의 유속이 발생함을 알 수 있으며, 분진의 효과적인 집진을 위해서는 공구 주변에서 발생한 고속의 분진을 흡입할 수 있는 석션 커버가 필요함을 알 수 있었으며, 석션컵(Suction Cup)으로 스핀들을 감싸는 형태로 제작하였다. 가공시 발생하는 분진을 석션컵에서 바로 흡진하여 헤드측면에 부착된 석션호스(Suction Hose)를 통해 헤드 상부로 이동하여 석션커버(Suction Cover)에 모이게 된다. 석션커버에 모인 분진들을 다시 석션호스를 통하여 배출하는 형태로 구성되어 있다. Fig. 4는 CRD헤드 스핀들 주변에 장착된 분진흡입모듈을 보여준다. 해석을 통해 결정된 형상으로 석션 커버를 제작하였으며, 주변에 브러쉬를 장착하여 가공부위에서 발생하는 분진이 외부로 비산되지 않고, 석션 커버 내부로 흡입되도록 구성하였다. 분진흡입 방법은 2개의 석션 호스를 석션컵에 대칭으로 배치하여 흡입하는 방식으로써, 2개의 석션호스가 흡입시 석션컵 내부에 흡입력으로 인한 원심력을 발생시켜 분진 흡입시 유리한 구조를 적용하였다.
2.4 탄소섬유복합재 가공성 평가
Fig. 5는 개발된 복합가공기의 가공특성을 평가하기 위한 실험 모습을 보여준다. 4개의 유연지그를 이용하여 평면의 베이스를 올리고 그 위에 실제 항공산업에 적용되는 탄소섬유복합재를 고정하여 드릴링 가공성을 평가하였다. 탄소섬유복합재 드릴링 가공시 발생하는 대표적인 결함인 박리(Delamination)과 가공 홀 표면 뜯김(Fiber Pull-Out)을 관찰하였다. 홀 가공에 사용된 소재는 두께 15 mm의 항공용 탄소섬유복합재로 여러 개의 적층 구조로 이루어져 있다. 가장 윗면과 아랫면은 직조형태의 우븐(Wooven)층으로 구성되어 있으며, 그 아래 층은 45° 방향으로 회전하면서 적층된 구조를 가지고 있다. 탄소섬유는 Toray사의 T1000급으로 구성되어 있으며, Epoxy소재의 폴리머로 경화되었다.
본 드릴링 가공성 평가에서 사용한 공구는 Widin 사의 비코팅 초경 공구를 사용하였으며, 주축회전수는 8,000 rpm, 이송속도는 0.05 mm/rev를 사용하였다. 실험에 사용된 탄소섬유복합재의 종류와 가공조건은 Table 1에 정리하였다.
상용 공작기계(CSCAM Tapping Center, M643)와 동일한 소재, 고정방식, 가공조건을 이용하여 개발된 복합가공장비의 가공성을 비교하였다. Fig. 6는 30개의 홀을 가공하면서, 각 홀 출구부에서의 박리지수를 비교한 결과를 보여준다. 처음 10번째 가공까지는 개발된 장비에서의 박리지수가 높았으나, 10번째 이후 가공에서는 유사한 수준의 박리지수가 나옴을 알 수 있었다. Fig. 7과 같이 홀 단면의 표면 거칠기를 측정하였으며, 그 결과 홀 표면의 거칠기는 기존 상용 공작기계 5.7 μm, 개발된 복합가공기 6.5 μm로 약 14% 증가한 것을 알 수 있었다. 박리지수의 변동이 크고, 가공면의 표면거칠기가 저하된 이유는 시편 고정부의 강성 저하로 예상된다. 상용 공작기계의 경우 주철 베이스를 이용하여 클램핑 방식으로 소재를 고정하는데, 개발장비에서는 유연한 실리콘 소재의 진공 흡착컵을 이용하여 소재를 가공하여, 소재 고정부에 대한 강성이 저하될 수 있다. 따라서 향후 가공시 유연지그의 변형량에 대한 고찰이 필요할 것으로 예상된다.
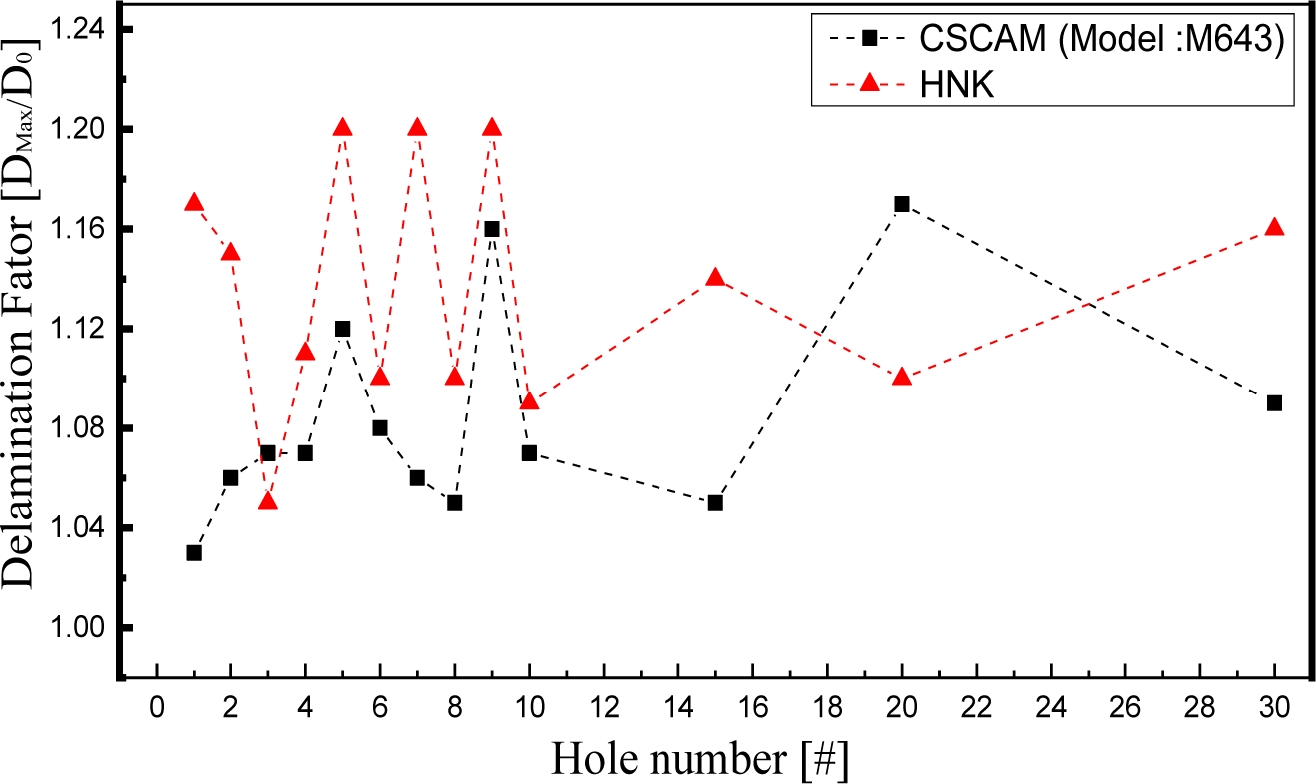
Delamination factor comparison of conventional machine tool (CSCAM) and developed machine tool (HNK)
3. 결론 및 향후 개발 방향
탄소섬유복합재는 자동차, 항공 등 수송산업 분야뿐만 아니라, 에너지, 조선 등 다양한 산업에서 경량화 소재로 수요가 증가하고, 제조업의 고부가가치화를 위한 핵심 소재이다. 본 연구에서는 가볍고 기계적 물성이 우수한 탄소섬유복합재를 고품질, 고생산성으로 절삭가공하기 위한 복합가공시스템을 개발하였고, 이를 이용하여 가공성능을 평가하였다. 실제 항공기 부품에 사용되는 탄소섬유복합재 소재를 이용하여 드릴링 가공 평가를 수행하였으며, 기존의 사용공작기계와 비교하여 박리지수는 7%, 표면거칠기는 14% 정도 높은 값으로 가공되었다. 박리지수와 가공면 표면거칠기의 차이는 개발장비의 유연지그 고정 방식에 의한 강성 저하를 원인으로 예상할 수 있다. 유연지그는 진공에 의한 흡착방식으로 시편을 고정하는데, 진공에 의한 흡착을 위해서 유연한 실리콘 재질의 흡착컵을 사용하여, 시편 고정부의 강성이 저하되었을 것으로 예상된다. 향후, 가공시 유연지그의 변형량을 측정하여, 가공 부하를 고려한 유연지그 고정부 강성 설계를 진행할 예정이다. 또한 앞으로는 현재까지 개발된 장비를 이용하여 실제 항공기 부품을 모사한 소재 및 형상을 가공하여, 다양한 가공조건 및 소재에 대한 가공데이터를 확보하고, 개발된 장비의 성능을 보완하고, 항공부품 제조업체와의 연계를 통해 개발된 장비를 이용한 안정된 양산 가공데이터를 확보할 예정이다. 또한 개발 중인 네트워크 기반의 개방형 CNC를 적용하여, 가공 중 발생하는 신호를 모니터링하여 품질과 생산성을 높이는 가공공정기술을 개발할 계획이다.
Acknowledgments
본 연구는 산업통상자원부의 기계산업핵심기술개발 사업의 일환으로 수행하였습니다. [과제번호 : 10053248, 과제명: 탄소섬유복합재(CFRP) 가공시스템 개발]
References
-
Kim, H.-Y., Kim, T.-G., Lee, S.-W., Yoon, H.-S., Kyung, D.-S., et al., “Development of Manufacturing System Package for CFRP Machining,” Journal of the Korean Society for Precision Engineering, Vol. 33, No. 6, pp. 431-438, 2016.
[https://doi.org/10.7736/KSPE.2016.33.6.431]
-
Che, D., Saxena, I., Han, P., Guo, P., and Ehmann, K. F., “Machining of Carbon Fiber Reinforced Plastics/Polymers: A Literature Review,” Journal of Manufacturing Science and Engineering, Vol. 136, No. 3, pp. 1-22, 2014.
[https://doi.org/10.1115/1.4026526]
-
Perner, M., Algermissen, S., Keimer, R., and Monner, H., “Avoiding Defects in Manufacturing Processes: A Review for Automated CFRP Production,” Robotics and Computer-Integrated Manufacturing, Vol. 38, pp. 82-92, 2016.
[https://doi.org/10.1016/j.rcim.2015.10.008]
- Gururaja, M. and Rao, A. H., “A Review on Recent Applications and Future Prospectus of Hybrid Composites,” International Journal of Soft Computing and Engineering, Vol. 1, No. 6, pp. 352-355, 2012.
-
Roberts, T., “Rapid Growth Forecast for Carbon Fibre Market,” Reinforced Plastics, Vol. 51, No. 2, pp. 10-13, 2007.
[https://doi.org/10.1016/S0034-3617(07)70051-6]
-
Benammar, A., Drai, R., and Guessoum, A., “Detection of Delamination Defects in CFRP Materials using Ultrasonic Signal Processing,” Ultrasonics, Vol. 48, No. 8, pp. 731-738, 2008.
[https://doi.org/10.1016/j.ultras.2008.04.005]
Principal Researcher at the Manufacturing System R&D Group, Korea Institute of Industrial Technology (KITECH). His research interests are machining process, machining of advanced materials (CFRP, Titanium and Inconel alloy) and micro-machining
E-mail: tgkim@kitech.re.kr
Senior Researcher at the Manufacturing System R&D Group, Korea Institute of Industrial Technology (KITECH). His research interests include design and control of precision positioning system, vibration isolation systems and robot manufacturing systems.
E-mail: kimhy02@kitech.re.kr
Principal Researcher at Korea Institute of Industrial Technology (KITECH) and an Associate Professor at University of Science and Technology (UST), Korea. His research interests are turbomachinery (Fans, compressors, pumps, hydraulic turbines, and pumpturbines) designs and developments; steady and unsteady numerical analyses; optimization methods; flow measurements and experimental techniques.
E-mail: jinhyuk@kitech.re.kr
Technician of the Manufacturing System Group at Korea Institute of Industrial Technology (KITECH). He received his M.S. (2014) degrees in the School of Semiconductor and chemical Engineering at Chonbuk University, Korea. Following a technician at KITECH in 2018. His technics involves high productivity, machining process such as turning, drilling and milling using analysis of machining mechanism, tool wear and surface integrity
E-mail: skw@kitech.re.kr
Hansol Yoon received his B.S in the School of Department of Mechanical Design Engineering at Changwon national university, Korea. He developed various machined designed technics based on manufacture the CNC machine tools in HNK Machine tool company.
E-mail: hayoon@hnkkkorea.com
Professor in the Department of Mechanical Engineering, Chung-Ang University. His research interests are Universal fixtures, Simulation-based optimization, Management of uncertainty, and Integrated materials and products design.
E-mail: hjchoi@cau.ac.kr
Principal Researcher at the Manufacturing System R&D Group, Korea Institute of Industrial Technology (KITECH). His research interests are machining process, machining of advanced materials (CFRP, Titanium and Inconel alloy) and micro-machining
E-mail: swlee@kitech.re.kr