
멀티 루멘 카테터 압출에서 다양한 공정 변수의 영향에 관한 연구
Copyright © The Korean Society for Precision Engineering
This is an Open-Access article distributed under the terms of the Creative Commons Attribution Non-Commercial License (http://creativecommons.org/licenses/by-nc/3.0) which permits unrestricted non-commercial use, distribution, and reproduction in any medium, provided the original work is properly cited.
Abstract
The multi-lumen catheter with complex and small cross section is widely used for interventional radiology and minimally invasive surgery. It is manufactured in the polymer extrusion process with many manufacturing parameters. The profile of the extrudate is difficult to predict because it depends on the die shape and many parameters. In this paper, the effects of the manufacturing parameters for multi-lumen catheter extrusion are studied. The commercial software ANSYS Polyflow is used to simulate the polymer flow and predict the profile of the extrudate. The optimized die shape is used to achieve the target profile of the extrudate. The extrudate profiles are investigated with respect to the puller speeds at the end of the extrudate and blowing air pressure of each lumen. Circularity and major diameter are compared for the different manufacturing parameters. The effects of the manufacturing parameters on the profile of the extrudate are examined. The target profile of the extrudate is obtained with optimized manufacturing parameters.
Keywords:
Catheter, Multi-lumen, Polymer extrusion, Polymer flow, Numerical analysis, Manufacturing parameters키워드:
카테터, 멀티 루멘, 폴리머 압출, 폴리머 유동, 수치해석, 공정 변수1. 서론
카테터는 최소침습 기반 중재 시술 의료분야에 활발히 사용되고 있는 도관 형태의 소모성 의료기기로써, 시술의 용이성 증대와 환자의 수술 위험도 및 감염률 최소화를 위하여 활발히 사용되고 있는 고분자 기반의 일회용 의료기기이다. 특히, 심혈관계 수술에서 절제 및 영상 장비와 함께 사용된다.1,2 최근 진단기술과 의료진의 시술 능력이 발전하면서, 보다 다양한 의료 목적에 부합하기 위하여 작고 복잡한 형태의 단면에 얇은 벽을 갖는 카테터의 수요가 증가하고 있다.1 이를 만족시키기 위해서는 카테터 샤프트(Shaft) 부위의 복잡한 루멘 형상과 내외경을 안정적인 공정으로 제조해야 한다. 따라서 높은 정밀도를 갖는 압출 공정이 요구된다. 폴리머 압출 공정은 다이를 사용하고 다이를 통과한 폴리머는 일반적으로 유변학적 특성으로 인하여 다이의 형상과 크기가 다르게 성형된다. 따라서, 압출물의 형상을 예측하는 것은 쉽지 않다.3 또한 다양한 공정 변수들의 영향으로 최종 압출물의 형상이 결정된다. 공정 변수들로는 용융 폴리머의 온도, 다이로 들어가는 폴리머의 유량, 다이를 통과한 압출물의 자유 표면 길이, 압출물의 냉각, 압출물을 당기는 Puller의 속도 등이 있다. 따라서 위에 나열한 공정 변수들이 압출물의 형상에 어떤 영향을 미치는지에 대한 연구가 요구된다. 실험적인 방법을 통하여 다이 형상과 공정 변수가 압출물의 형상에 미치는 영향에 대한 다양한 연구가 진행중이다.5,6 일반적으로 원하는 압출물을 얻기 위한 실험적인 설계 방법으로 다이 형상 및 공정 변수를 변경시켜 압출물을 제작하는 시행착오법이 사용된다.3 이 방법은 많은 시간과 자원을 필요로 한다. 따라서 수치해석을 이용한 설계 방법에 대한 연구도 활발히 진행중이다.3,4,7-11
Tian et al.3은 멀티 루멘 카테터 압출 과정을 Finite Element Method (FEM)를 사용하여 묘사하였다. 다이 형상의 변화가 압출물에 미치는 영향을 파악하기 위하여 다양한 형상의 다이에 따른 압출물의 형상을 수치해석적인 방법으로 예측하였다. 각 루멘의 두께비, 중공비와 편심비 등을 고려하여 원하는 압출물을 생성하기 위한 다이 설계 방법을 제시하였다. Conçalves et al.4은 복잡한 형상을 가진 카테터를 제작하기 위하여 3차원 Finite Volume Method (FVM)를 이용한 Computational Fluid Dynamics (CFD) 코드를 개발하였다. 또한 원하는 압출물을 얻기 위한 다이 형상 설계를 위해 최적화 방법을 사용하였다. 멀티 루멘 카테터의 제작을 위하여 다이 출구에서 균일한 속도 분포를 갖는 다이 형상을 설계하였다. Tian et al.7은 FEM을 사용하여 점탄성 유체의 특성을 알아보았다. 점탄성 유체를 묘사하기 위하여 Pom-Pom 모델을 사용하였고 수치해석 결과와 실험결과를 비교하였다. 다이 스웰(Die Swell) 현상을 알아보기 위하여 작은 다이 채널 크기, 폴리머의 유량 및 이완 시간 등의 서로 다른 조건에 대한 스웰 현상을 분석하였다. Jin et al.5은 싱글 루멘 카테터 압출 과정 중 공정 변수인 폴리머 온도, 다이 랜드 길이, Puller 속도와 폴리머 유량이 압출물에 미치는 영향을 실험적인 방법으로 알아보았다. 공정 변수를 변화시켜가면서 카테터의 지름과 벽 두께에 대한 영향을 측정하였다. 폴리머 온도 변화는 압출물의 형상에 큰 영향이 없었고 Puller 속도와 유량의 변화는 압출물에 큰 영향을 주고 그 변화는 비선형적이라고했다. Jin et al.6은 멀티 루멘 카테터 압출을 위한 공정 변수의 영향을 실험적으로 알아봤다. 각각의 루멘에 주입되는 공기의 체적유량의 변화에 따른 카테터와 각 루멘의 난형도를 측정하였다. 그 난형도를 바탕으로 최적화된 다이 형상을 설계하였다.
본 논문에서는 ANSYS Polyflow를 사용하여 폴리머의 유동을 해석하고 최종 압출물의 형상을 예측하여 볼 것이다. Tian et al.3의 수치해석 방법에 Puller 속도와 루멘에 주입되는 공기 압력을 적용시켜 실제적인 카테터 압출 과정을 해석할 것이다. 또한 원하는 카테터 압출물 단면을 얻기 위해 최적화된 다이 형상을 사용하여 압출 과정 중 공정 변수가 압출물의 형상에 미치는 영향에 대하여 알아볼 것이다.
2. 카테터 압출 공정
Fig. 1은 카테터 압출 공정을 간략하게 나타낸다. Nurdle 형태의 폴리머 원재료는 Hopper에서 Barrel로 공급되어진다. Barrel 안에는 회전하는 Screw가 있고 마찰열에 의해서 폴리머의 온도가 올라가고 용융된다. Screw의 회전을 조절하여 용융된 폴리머를 운반하고 유량을 제어한다. 용융된 폴리머는 다이를 통하여 압출되고 루멘의 형상을 만들기 위하여 루멘 위치에 공기를 주입한다. 압출물은 Puller에 의하여 일정 속도로 당겨져 이송된다. 그리고 일정 길이의 자유 표면을 지난 후 진공 및 냉각 탱크로 들어가 경화되어 최종 압출물의 형태를 갖는다.
본 연구에서 카테터 압출물의 목표 형상과 최적화된 다이 형상 및 크기를 Fig. 2에 나타내었다. 압출된 카테터는 4개의 루멘을 갖고 중심을 지나는 수직선을 기준으로 양쪽이 대칭인 형상을 갖고 있다. 카테터 성형에 쓰이는 다이는 각각의 루멘이 만들어지는 위치에 공기 주입구가 위치하게 된다. 공기 주입 압력과 Puller 속도에 의하여 전체 카테터와 루멘의 크기 및 형상이 결정된다.
연구에 사용된 폴리머는 Arkema Inc.의 PEBAX 4033이고 밀도는 1010 kg/m3이다. 이 소재의 유변학적 거동을 고려하기 위하여 Generalized Newtonian 모델2을 사용하였고 전단율 변화에 따른 점성 계수는 Bird Carreau 모델2을 사용하여 아래 식(1)과 같이 나타내었다.
(1) |
여기서 η∞는 무한 전단율에 대한 점성, η0는 전단율이 없을 때의 점성을 나타낸다. 또한 λ는 이완시간, n은 Power Law Index를 나타낸다. 소재의 유변학적 성질을 파악하기 위하여 온도 190°C에서 전단율의 변화에 따른 점도를 측정하였다. 전단율 10-2-105 s-1 구간의 점도를 측정하고 Bird Carreau 모델을 사용하여 Curve Fitting을 하였다. Fig. 3에 190°C PEBAX 4033의 전단율에 따른 점도를 변화를 나타내었다. 그리고 Curve Fitting 파라미터는 Table 1에서 보는 바와 같다.
3. 수치해석 모델링
폴리머 유동을 해석하기 위하여 지배방정식으로 비압축성 정상상태 Navier Stokes 방정식을 사용하였고, 중력과 관성을 무시하였다. 따라서 질량 보존식은 아래 식(2)와 같이 표현된다.
(2) |
또한 운동량 보존식은 다음 식(3)과 같이 표현된다.
(3) |
여기서 ui는 i번째 속도, p는 압력을 나타내고 Generalized Newtonian 모델을 사용한 편향 응력 텐서 τij는 아래 식(4)와 같이 표현된다.
(4) |
수치해석에 사용된 격자와 경계 조건을 Fig. 4에 나타내었다. 다이 중심을 지나는 수직선에 대칭인 형상을 고려하여 1/2 영역의 3차원 형상을 해석하였다. 다이 랜드의 길이는 10mm이고 No-Slip 조건을 부여하였다.
다이 랜드가 끝나는 부분부터 압출물의 형상을 예측하기 위하여 10 mm 길이를 가진 자유 표면 조건을 적용하였다. 다이 랜드 입구에서는 용융된 폴리머가 Z 방향의 완전발달 유동으로 들어간다. 폴리머 유량은 169.65 mm3/s이다. 자유 표면 끝에서는 Puller에 의해 압출물이 당겨지는 속도가 적용된다. 자유 표면에 위치한 루멘의 벽에는 루멘 형성을 위해 주입되는 공기에 의한 압력 조건이 주어진다. 자유 표면의 길이가 짧기 때문에 주입 공기의 압력 강하는 무시하였다. 그리고 대칭면에는 대칭 조건을 적용하였다.
수치해석에 사용된 격자는 142,538개의 노드와 128,280개의 육면체 요소로 이루어져 있다. 3개의 루멘을 구별하기 위하여 각각의 루멘에 번호를 부여하였다. 지배방정식에 수렴의 어려움을 유발하는 비선형 항들이 포함되어 있어서 Evolution Scheme을 사용하였다. 또한 Bird Carreau 모델의 Power Law Index 값이 0.7보다 작으므로 Picard Iteration을 사용하였다. 반복 계산은 지배방정식의 해가 수렴 조건 10-4을 만족할 때까지 수행하였다. 자유 표면의 형상을 예측하기 위하여 Optimesh Remeshing 방법을 사용하였다.
4. 결과 및 분석
4.1 속도 분포
Fig. 5(a)는 다이 랜드 끝부분 즉 자유 표면이 시작하는 부분에서의 속도 분포를 나타낸다. 각 루멘의 압력 조건은 1번 루멘 2239 Pa, 2번 루멘 2189 Pa 그리고 3번 루멘 2488 Pa이다. Puller 속도 0.1 m/s가 자유 표면 끝에 적용되었다. 카테터 벽 두께가 두꺼운 부분에서 다른 부분에 비해 속도가 큰 것을 알 수 있다. 다이 랜드 끝에서 압출 후 압출물은 속도가 높은 부분에서 Swell 현상이 발생한다.1 따라서 상대적으로 속도가 낮은 부분에서는 벽의 두께가 줄어드는 현상이 발생한다. 폴리머 유동이 유동 방향에 수직인 평면에 대하여 균일한 속도 분포를 갖기 위하여 속도가 큰 부분에서 벽의 두께가 두꺼워지고, 속도가 작은 부분에서 벽의 두께는 얇아진다. 이로 인해 각 루멘과 카테터의 형상이 원형을 유지하기 힘들어진다. 따라서 Swell 현상을 억제하기 위하여 Puller를 이용하여 압출물을 당겨주고 루멘을 원형으로 유지하기 위하여 공기를 주입하는 방법을 사용하는 것이다. Fig. 5(b)는 다이 랜드, 각각의 루멘과 카테터 압출물 내부의 속도 분포를 나타낸다. 폴리머는 다이 랜드 내부에서 일정한 속도 분포를 가지고 자유 표면 쪽으로 이동한다. 자유 표면에 노출되면서 Puller 속도의 영향으로 인하여 단면적이 줄어들며 Swell 현상을 억제시키는 것을 볼 수 있다. 또한 공기압의 영향으로 각 루멘의 형상이 잘 유지되는 것을 볼 수 있다.
4.2 Puller 속도의 영향
Fig. 6은 서로 다른 Puller 속도에 따른 압출물의 형상과 수직 단면에서의 속도 분포를 나타낸다. Puller 속도는 0.05, 0.1, 0.15 그리고 0.2 m/s를 고려하였다. 각 루멘의 압력 조건은 위와 같이 1번 루멘 2239 Pa, 2번 루멘 2189 Pa 그리고 3번 루멘 2488 Pa이다. 같은 유량 169.65 mm3/s 대비 Puller의 속도가 높을수록 카테터의 단면적이 적어지는 것을 알 수 있다. 또한, 속도 분포 그래프를 보면 Puller 속도 0.05m/s의 경우 자유 표면이 시작하는 부분에서 약한 Swell 현상이 발생하는 것을 알 수 있다. 반면에 높은 Puller 속도에서는 Swell 현상이 전혀 발생하지 않는 것을 확인할 수 있다. 따라서 일정 속도 이상의 Puller 속도가 Swell 현상을 억제해주는 것을 알 수 있다. Puller 속도 변화에 따른 카테터 외부의 긴 지름과 카테터와 각 루멘의 진원도를 Fig. 7에 나타내었다. 진원도는 아래 식(5)로 정의된다.
(5) |
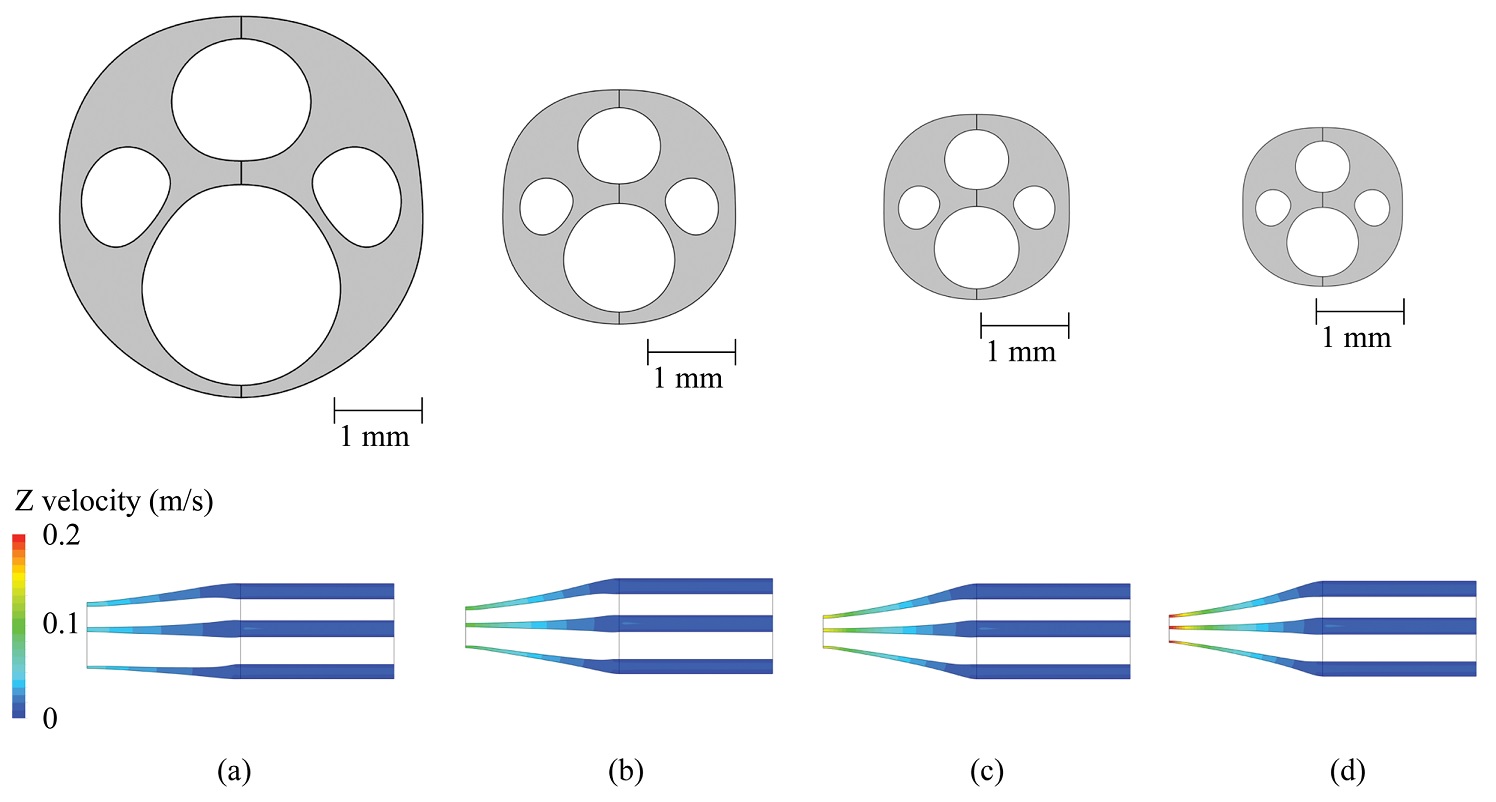
Extrudate profile and velocity contour for different puller speed (a) 0.05, (b) 0.1, (c) 0.15, and (d) 0.2 m/s
여기서 As는 카테터와 루멘의 단면적이고 P는 둘레 길이를 나타낸다. 앞에서 말한 바와 같이 Puller 속도가 높을수록 카테터 외경이 작아지는 것을 확인할 수 있다. 목표 카테터 외경은 2.7 mm이고 Puller 속도 0.1 m/s인 경우 카테터 외경은 2.77 mm인 것을 알 수 있다. 또한, 루멘 3의 진원도는 Puller 속도가 커짐에 따라 증가하는 것을 알 수 있다. 카테터 외부와 다른 루멘의 진원도는 Puller 속도 변화에 큰 영향을 받지 않는다.
4.3 압력의 영향
Fig. 8은 1번 루멘에 작용하는 공기압의 변화에 따른 압출물의 단면 형상을 나타내고 있다. 1번 루멘에 적용되는 압력은 0, 1244, 1866, 2488 그리고 3110 Pa을 고려하였다. Puller 속도는 0.1 m/s이고 다른 루멘의 압력은 2번 루멘 2189 Pa 그리고 3번 루멘 2488 Pa이다. 1번 루멘의 압력이 커짐에 따라서 1번 루멘 주변의 벽 두께가 얇아지는 것을 볼 수 있다. 그리고 다른 루멘의 중심이 카테터 중심에서 멀어지는 것을 볼 수 있다. Fig. 9는 1번 루멘 압력 변화에 따른 카테터 외부의 긴 지름과 카테터와 각 루멘의 진원도를 나타내었다. 1번 루멘의 압력이 증가함에 따라 카테터 외부 긴 지름이 증가하고 1866 Pa까지는 진원도의 변화가 없다가 그 이상부터 카테터 외부와 루멘의 진원도가 감소하는 경향을 볼 수 있다. 1번 루멘의 압력이 1866 Pa 경우에 카테터 외부 직경 목표 직경인 2.7mm과 가까운 값을 갖게 되고 전체적인 진원도도 가장 높은 값을 갖는다는 것을 알 수 있다.
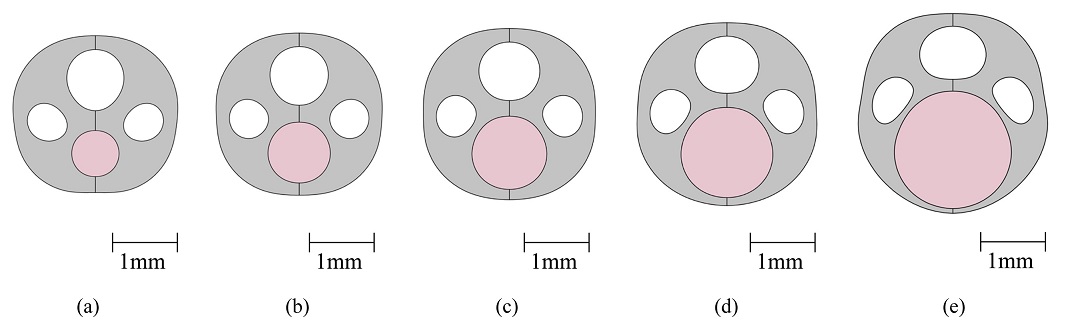
Extrudate profile for different pressure in lumen 1 (Pink region) (a) 0, (b) 1244, (c) 1866, (d) 2488, and (e) 3110 Pa
Fig. 10은 2번 루멘에 작용하는 공기압의 변화에 따른 압출물의 단면 형상을 나타내고 있다. 2번 루멘에 적용되는 압력은 0, 1244, 1866, 2488 그리고 3110 Pa을 고려하였다. Puller 속도는 0.1 m/s이고 다른 루멘의 압력은 1번 루멘 22396 Pa 그리고 3번 루멘 2488 Pa이다.
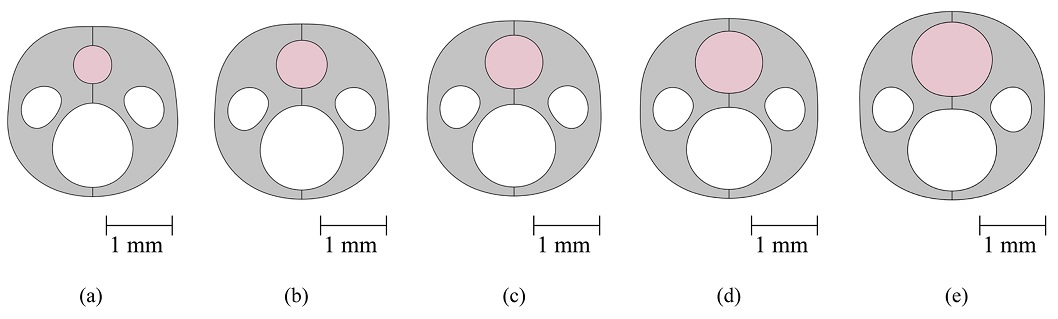
Extrudate profile for different pressure in lumen 2 (Pink region) (a) 0, (b) 1244, (c) 1866, (d) 2488, and (e) 3110 Pa
1번 루멘과 마찬가지로 2번 루멘의 압력이 커짐에 따라서 2번 루멘 주변의 벽 두께가 얇아지는 것을 볼 수 있다. 1번 루멘과 다르게 2번 루멘의 압력 변화에 의해서 다른 루멘의 크기나 형상이 많이 변하지 않는 경향을 볼 수 있다. Fig. 11은 2번 루멘 압력 변화에 따른 카테터 외부의 긴 지름과 카테터와 각 루멘의 진원도를 나타내었다. 2번 루멘의 압력이 증가함에 따라 카테터 외부 긴 지름이 증가한다. 1번과 2번 루멘의 진원도는 2번 루멘의 압력과 관계없이 거의 같은 값을 갖고 3번 루멘의 경우 2번 루멘의 압력이 증가함에 따라서 진원도도 증가하는 경향을 갖는다. 카테터 외부의 진원도는 2번 루멘의 압력이 2488 Pa경우를 제외하고 거의 같은 값을 갖는다. 루멘의 압력 변화에 따른 진원도의 변화가 복잡한 성질을 갖고 있음을 알 수 있다.
2번 루멘의 압력이 2488 Pa일 경우 전반적으로 높은 진원도와 직경이 목표 카테터 직경 2.7mm에 가까운 값을 갖음을 알 수 있다.
Fig. 12는 3번 루멘에 작용하는 공기압의 변화에 따른 압출물의 단면 형상을 나타내고 있다. 3번 루멘에 적용되는 압력은 0, 1244, 1866, 2488 그리고 3110 Pa을 고려하였다. Puller 속도는 0.1 m/s이고 다른 루멘의 압력은 1번 루멘 2239 Pa 그리고 2번 루멘 2189 Pa이다. 마찬가지로 3번 루멘의 압력이 커짐에 따라서 3번 루멘 주변의 벽 두께가 얇아지는 것을 볼 수 있다. 그리고 3번 루멘의 압력 변화에 따른 다른 루멘의 크기나 형상의 변화가 작다는 것을 알 수 있다. Fig. 13은 3번 루멘 압력 변화에 따른 카테터 외부의 긴 지름과 카테터와 각 루멘의 진원도를 나타내었다. 3번 루멘의 압력이 증가함에 따라 카테터 외부 긴 지름이 증가하지만 그 값이 이전 경우와 비교하여 작다는 것을 알 수 있다. 카테터 외부와 1번, 2번 루멘의 진원도는 3번 루멘의 압력과 관계없이 거의 같은 값을 갖지만 3번 루멘의 경우 1866 Pa 이상의 압력에서 진원도가 낮아짐을 알 수 있다. 3번 루멘의 압력이 1866, 2488 PA에서 카테터 목표 직경과 유사한 값을 갖고 전체적으로 높은 진원도 값을 갖는다.
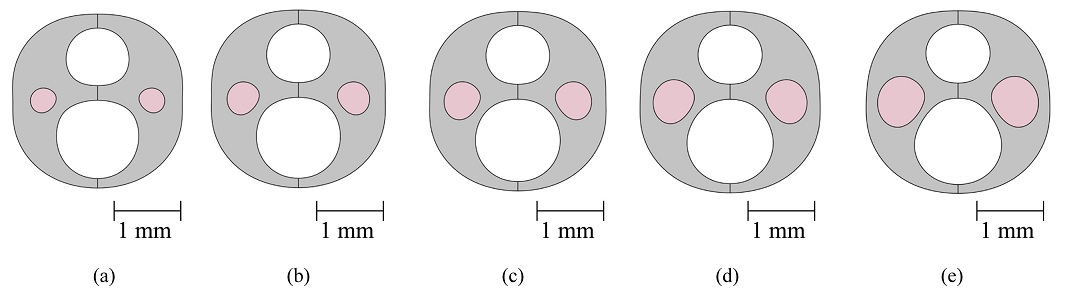
Extrudate profile for different pressure in lumen 3 (Pink region) (a) 0, (b) 1244, (c) 1866, (d) 2488, and (e) 3110 Pa
4.4 목표 형상과 예측 형상 비교
다양한 공정 변수를 적용하여 압출물의 형상을 예측한 결과 폴리머 유량 169.65 mm3/s과 Puller 속도 0.1 m/s, 각 루멘의 압력은 1번 루멘 2239 Pa, 2번 루멘 2189 Pa 그리고 3번 루멘 2488 Pa의 조건에서 목표 압출물의 형상과 가장 비슷한 형상이 만들어짐을 알 수 있었다. Fig. 14는 목표 압출물의 형상과 최적화된 공정 변수를 사용하여 예측한 형상을 비교하였다. 카테터 외경의 긴 지름은 2.77mm이고 진원도는 0.9, 1번 루멘의 긴 지름은 1.27mm이고 진원도는 0.9, 2번 루멘의 긴 지름은 0.95mm이고 진원도는 0.9, 3번 루멘의 긴 지름은 0.66mm이고, 진원도는 0.89이다. 3번 루멘의 긴 지름과 진원도가 목표 형상과 가장 큰 차이를 보인다. 1번 루멘과 카테터 외경의 중심축 편심은 크지 않지만 2번과 3번 루멘의 편심은 상대적으로 크게 발생한 것을 알 수 있다.
5. 결론
본 연구에서는 수치해석을 사용하여 멀티 루멘 카테터 압출에서 다양한 공정 변수의 영향에 관한 연구를 수행하였다. 목표 카테터 형상을 만들기 위하여 최적화된 다이를 사용하고 다양한 공정 변수의 영향을 알아보았다. 진원도와 긴 지름을 비교하여 공정 변수가 압출물의 형상에 미치는 영향을 파악하였다. 또한 Puller 속도와 루멘에 주입되는 공기 압력을 수치해석에 적용하여 정확하게 압출물 형상을 예측하였다. 최종적으로 목표 압출물과 큰 차이가 없는 카테터 형상을 만들 수 있는 공정변수를 찾아내었다.
Puller 속도의 영향이 압출물 형상에 가장 크게 작용하는 것을 알 수 있었다. 속도가 커지면 압출물의 전체적인 단면적이 작아지고 각 루멘의 크기도 작아지는 것을 알 수 있었다. 또한 루멘에 주입되는 공기압의 변화는 단순히 그 루멘의 크기가 커지는 것 외에 다른 루멘에도 영향을 주며 진원도와 긴 지름의 변화에 복잡한 성질이 있음을 알 수 있었다. 본 연구의 수치해석 방법과 공정 변수의 영향에 대한 결과가 카테터 압출 공정에 많은 도움이 될 것으로 예상된다. 향후 여러 공정 변수들을 고려하여 최적화된 다이를 설계하는 역계산법에 대한 연구와 실험을 통한 검증과정이 필요할 것으로 예상된다.
NOMENCLATURE
η : | Viscosity (Pa∙s) |
λ : | Relaxation time (sec.) |
n : | Power law index for Bird Carreau model (-) |
: | Strain rate (1/s) |
p : | Pressure (Pa) |
τ : | Shear stress (Pa) |
c : | Circularity (-) |
REFERENCES
-
Dausch, D. E., Castellucci, J. B., Gilchrist, K. H., Carlson, J. B., Hall, S. D., et al., “Live Volumetric Imaging (LVI) Intracardiac Ultrasound Catheter,” Cardiovascular Revascularization Medicine, Vol. 14, No. 3, pp. 157-159, 2013.
[https://doi.org/10.1016/j.carrev.2013.03.008]
-
Iwasawa, J., Koruth, J. S., Petru, J., Dujka, L., Kralovec, S., et al., “Temperature-Controlled Radiofrequency Ablation for Pulmonary Vein Isolation in Patients with Atrial Fibrillation,” Journal of the American College of Cardiology, Vol. 70, No. 5, pp. 542-553, 2017.
[https://doi.org/10.1016/j.jacc.2017.06.008]
-
Tian, H., Zhao, D., Wang, M., and Jin, Y., “ E ffect of Die Lip Geometry on Polymer Extrudate Deformation in Complex Small Profile Extrusion,” Journal of Manufacturing Science and Engineering, Vol. 139, No. 6, Paper No. 061005, 2017.
[https://doi.org/10.1115/1.4035419]
-
Gonçalves, N., Carneiro, O., and Nóbrega, J., “Design of Complex Profile Extrusion Dies through Numerical Modeling,” Journal of Non-Newtonian Fluid Mechanics, Vol. 200, pp. 103-110, 2013.
[https://doi.org/10.1016/j.jnnfm.2013.02.007]
-
Jin, G. B., Zhao, D. Y., Wang, M. J., Jin, Y. F., Tian, H. Q., et al., “Study on Design and Experiments of Extrusion Die for Polypropylene Single-Lumen Micro Tubes,” Microsystem Technologies, Vol. 21, No. 11, pp. 2495-2503, 2015.
[https://doi.org/10.1007/s00542-015-2426-6]
-
Jin, G., Jin, Y., Zhao, D., Dai, G., and Zhang, Q., “Cross-Section Design of Multi-Lumen Extrusion Dies: Study on the Effects of Die Swell and Gas Flow Rate of the Lumen,” Microsystem Technologies, Vol. 23, No. 10, pp. 5093-5104, 2017.
[https://doi.org/10.1007/s00542-017-3489-3]
-
Tian, H., Zhao, D., Wang, M., Jin, G., and Jin, Y., “Study on Extrudate Swell of Polypropylene in Double-Lumen Micro Profile Extrusion,” Journal of Materials Processing Technology, Vol. 225, pp. 357-368, 2015.
[https://doi.org/10.1016/j.jmatprotec.2015.06.015]
-
Müllner, H. W., Wieczorek, A., Fidi, W., and Eberhardsteiner, J., “Advances in Numerical Prediction of Extrusion Tools Used for Fabrication of Rubber Profiles,” Proceedings in Applied Mathematics and Mechanics, Vol. 8, No. 1, pp. 10633-10634, 2008.
[https://doi.org/10.1002/pamm.200810633]
-
Ngamaramvaranggul, V. and Webster, M., “Viscoelastic Simulations of Stick-Slip and Die-Swell Flows,” International Journal for Numerical Methods in Fluids, Vol. 36, No. 5, pp. 539-595, 2001.
[https://doi.org/10.1002/fld.145]
-
Huang, J. C. and Leong, K. S., “Shear Viscosity, Extensional Viscosity, and Die Swell of Polypropylene in Capillary Flow with Pressure Dependency,” Journal of Applied Polymer Science, Vol. 84, No. 6, pp. 1269-1276, 2002.
[https://doi.org/10.1002/app.10466]
-
Cho, H. S. and Lyu, M. Y., “Flow Characteristics of Polymer Melt for Die Shapes for the Extrusion of Catheter Tubing,” Polymer-Korea, Vol. 42, No. 2, pp. 197-205, 2018.
[https://doi.org/10.7317/pk.2018.42.2.197]
M.S. Student in the Department of Mechanical System Engineering, Kumoh National Institute of Technology. His research interest is polymer extrusion manufacturing.
E-mail: tmdrl0723@gmail.com
Assistant Professor in the Department of Mechanical System Engineering, Kumoh National Institute of Technology. His research interest is heat transfer and fluid flow analysis.
E-mail: euntaek@kumoh.ac.kr