
회전형 금속와이어 공급장치에 의한 레이저응용 적층제조 기술
Copyright © The Korean Society for Precision Engineering
This is an Open-Access article distributed under the terms of the Creative Commons Attribution Non-Commercial License (http://creativecommons.org/licenses/by-nc/3.0) which permits unrestricted non-commercial use, distribution, and reproduction in any medium, provided the original work is properly cited.
Abstract
Chiefly, the metal wire-feed and laser additive manufacturing (AM) is a deposition process to produce larger mechanical parts required for aerospace, shipbuilding, automobile, and mold repair industries. The principal advantage of metal wire-feed AM is the high deposition rate compared to an assisted metal powder-feed AM, and metal powder-based fusion AM. During the wire-feed deposition process, the feed orientation is a critical parameter managed at all stages of processing. A better surface finish is attained when the melted wire flows smoothly through the process, and a wire feed direction that is utilized opposite to the deposition direction yields the best results. To improve the surface quality of metal 3D printing, we designed a rotating wire feeder, the feed direction of which varies with the direction of deposition; all free-form lines which thus exhibit identical surface qualities. Here, we use a rotating stage to orient the wire-feed direction according to the bead direction, a slip ring to supply electrical power to the feeder motor, and utilized two rotating channels on a plate to supply Ar gas and extract fumes safely during the processing stage. We evaluated the rotating wire feeder by building various parts as needed to the equipment.
Keywords:
Additive manufacturing, Rotating wire feeder, Laser assist metal deposition, Metal 3D printing키워드:
적층 제조, 회전형 와이어 공급장치, 레이저 응용 금속 증착, 금속 3D 프린팅1. 서론
금속에 의한 3D 프린팅 또는 적층 제조 기술은 다른 재질로 적층 제조하는 것보다 금속 재료가 가지는 특성에 의해 실제 산업에 쓰이는 용도가 다양하다. 이러한 금속을 적층 제조하는 방식으로는 금속을 용융시키는 열원 및 사용재료의 형태에 의해 나뉘어지며, 열원으로는 주로 레이저, 전자빔, 전기적 방전 또는 플라즈마가 사용되고 재료의 형태로는 분말 또는 와이어가 사용된다.1-4 각각의 방식은 각기 다른 장단점이 있으므로 적용 부품에 맞게 선택하여야 하며, 본 논문에서는 레이저와 와이어가 결합된 3차원 적층 제조기술에 주안점을 두었다.
레이저 응용 와이어 적층 제조는 열원에 금속 분말을 공급하여 적층 제조하는 DED (Direct Energy Deposition) 또는 금속 분말을 베드에 얇게 도포하고 원하는 부분을 스캐너를 이용하여 적층 제조하는 PBF (Powder Bed Fusion) 에 비해 정밀도는 다소 떨어지나 적층 속도가5배 이상으로 빠르고, 와이어 재료가 분말 재료보다 저렴하며 적층 공정시 분말이 비산되지 않아 작업환경이 덜 해로우며, 거의 100% 재료를 적층에 사용할 수 있어 재료 효율성이 좋다.1 이러한 장단점으로 인해 레이저 응용 와이어 적층 기술은 형상이 상대적으로 덜 복잡하고 크기가 수십 - 수백 mm인 부품제작에 유리하다고 할 수 있다.
레이저와 와이어의 용융에 의해 형성되는 비드의 품질은 다양한 실험 변수, 경로 및 제어 방식에 의해 영향을 받는다.5-10 그 중 와이어 공급 방향에 따라 적층 품질이 다르다는 사실은 기존 연구에 의해 논의 되었다.11-13 즉 와이어가 비드의 생성방향과 반대 방향에서 공급될 경우(Front Feeding)가 같은 방향에서 공급되는 경우(Back Feeding) 및 옆에서 공급되는 경우(Side Feeding)에 비해 표면이 주름지거나 기공 발생하는 것이 훨씬 덜하여 양호함을 알 수 있다. 이러한 문제를 해결하기 위해 중앙에서 와이어를 공급하고 레이저 빔을 분기해서 측면에서 조사하는 방식이 제안되었다.14 하지만 이는 내부를 채우는 공정에는 옆 벽면의 간섭에 의해 레이저가 와이어에 조사되지 못하므로 바람직하지 않다.
본 논문에서는 새로운 방식의 와이어 공급장치를 제안하여 어느 방향에서도 와이어가 항상 Front Feeding이 될 수 있도록 하였고, 이를 이용하여 몇 가지 다양한 형상을 제작하여 와이어 공급장치 사용의 가능성을 검토한 결과를 소개한다.
2. 회전형 와이어 공급 장치
양호한 적층 비드의 품질을 얻기 위해서는 Fig. 1(a)와 같이 와이어의 공급이 비드 형성방향 맞은편에서 공급되어야 한다. 직선 비드 형성의 경우에는 와이어 공급방향이 일정하므로 품질에 영향을 주지 않지만 Fig. 1(b)와 같이 타원형일 경우 비드 형성 방향에 따라 와이어의 공급 방향이 수시로 변하여야 한다. 이러한 기능을 얻기 위해 Fig. 2와 같은 개념으로 회전형 와이어 공급장치를 설계 제작하였다. 즉, 적층에 공급할 와이어를 감고 있는 스풀과 와이어를 송급 하는 이송 모터를 회전하는 중공 회전판 아래 두고 레이저는 중공 회전판의 중앙에서 모재와 와이어에 조사되도록 하였다. 회전판 아래 이송모터가 있으므로 외부에서 전원 및 신호선이 꼬임 없이 구동되어야 하는데 이를 해결하기 위해 슬립링을 사용하였다. 공정에 사용되는 보호가스와 공정 중 발생하는 흄은 회전판 내에 각각의 홈을 형성하고 오링으로 각 홈을 밀폐시켜서 회전하면서도 보호가스 공급과 흄의 제거가 원활하도록 하였다. 상기 구조로 회전판이 무한 회전한다 하더라도 전원선 및 공압선의 꼬임이 발생하지 않으며, 원하는 형상을 적층할 때 항상 와이어 공급이 비드 형성의 앞에서 이루어지도록 회전이 가능하게 하였다.
공정이 일어나는 부분은 레이저 빔의 초점위치, 회전판의 회전 중심 및 와이어의 끝점이 항상 일치하도록 정열하는 것이 중요하며 이를 위해 레이저 헤드에 미세 조정기구를 설치하여 CCD를 참고하면서 정렬을 하였고 360o 회전 결과 Fig. 3과 같이 잘 일치함을 보였다.
3. 적층 실험
3.1 레이저 사양
적층 실험에 사용된 레이저는 1,070 nm 파장을 가진 파이버레이저(IPG Photonics)이며, 600 mm 초점길이를 가진 포커싱 렌즈로 빔직경 1.5 mm를 갖도록 하였다. 초점 부근에서 레이저 빔의 진행경로에 따라 측정한 빔의 공간상 분포는 Fig. 4와 같다. 공정 초점 심도를 에너지밀도의 90%(반경이 5% 증가)로 정하면 약 ±16 mm로 측정되어 고정도로 와이어를 초점위치에 위치 시키지 않아도 된다. 다만 초점에서의 Flat Top 모드가 초점에서 벗어날수록 광 분포가 넓어지므로 주의할 필요가 있다.
3.2 적층 재료
본 실험은 적층한 부위의 내부 품질보다는 회전형 와이어 공급장치가 자유형상 적층에서도 균질한 표면 품질을 가질 수 있느냐에 맞춰져 있다. 따라서 사용 재료는 일반적으로 적층 제조에 많이 응용 되는 Ti-6Al-4V와 KP4 와이어를 사용하였으며, 모재는 와이어와 같은 재료이다. 와이어 직경은 0.9 mm이며, 외경 200 mm 스풀에 감겨 있는 와이어를 적절히 펼친 후 공급하였다.
실험 조건으로는 레이저 출력 1.5 kW, 테이블 속도 8 mm/sec, 와이어 공급 속도 40 mm/sec, 보호가스 Ar 공급량 20 l/min이고 공급각도는 45o로 고정하였다.
3.3 표면 적층
Figs. 5부터 7은 Ti-6Al-4V 와이어를 사용하였다. Fig. 5는 직경 20 mm 원을 와이어 공급 방향이 고정된 것과 회전한 것을 이용하여 적층한 사진이다. 그림에서 보는 바와 같이 고정형의 경우 Back Feeding이 이루어지는 부분에서는 주름이 발생하여 표면상태가 양호하지 못하였고, 회전형의 경우 와이어 공급이 항상 Front Feeding 상태가 되어 균일한 적층 표면을 얻을 수 있었다.
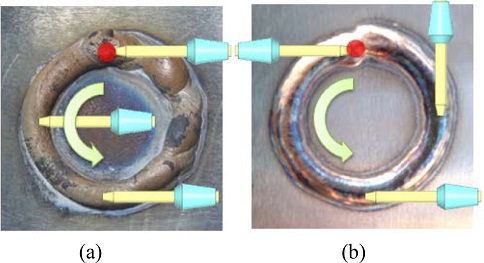
Comparison of surface quality between fixed (a) and rotation wire feeder (b) for the deposition of the circle of 15 mm in diameter
Fig. 6은 직선과 곡선이 혼합된 “ㄹ” 형상이고 Fig. 7은 스플라인으로 형성된 익형 모양의 형상으로 회전형 와이어 공급장치에 의해 모든 구간에 걸쳐 일정한 표면 거칠기를 얻을 수 있음을 확인하였다.
회전형 와이어 공급장치의 장점은 앞서 기술 하였듯이 와이어 공급용 모터의 전원 및 신호선과 보호가스 공급이나 흄 제거에 필요한 공압선의 꼬임 없이 무한 회전할 수 있다는 것이다. Fig. 8(a)는 직경 15 mm 원통 형상을 KP4 와이어(이하 동일 재료)를 사용하여 회전당 1 mm 높이로 각 5회 및 10회 적층 제조한 것이며 이를 다시 밀링 가공한 것이 Fig. 8(b)이다.
Fig. 8(b)의 10회 레이어을 적층한 원통형상을 높이 방향으로 절단하여 적층된 부분과 모재와의 경도를 0.5 mm 간격으로 측정하였으며 Fig. 9와 같이 결과를 얻었다. 고온의 레이저 열원으로 모재와 와이어가 용융되어 증착됨과 동시에 냉각이 되어 경도가 높아지는 열처리 효과를 나타낸다. 본 적층 조건의 경우 열영향부는 약 1 mm 정도로 나타났고, 와이어 적층부 상단으로 갈수록 경도가 낮아지는 경향을 보이는데 이는 하부의 적층된 재료는 상부의 적층 과정에서도 지속적으로 열이 공급되어 나타난 현상으로 생각된다. 적층된 부분의 경도는 모재에 비해 약 1.5 배 정도 높게 나타났다.
3차원 적층의 가능성을 보기 위해 Fig. 10과 같은 형상을 적층하였다. “~” 의 형상으로 앞선 방법과 동일하게 비드 형성 방향에 따라 와이어 공급장치가 회전하면서 적층 하였고, 첫번째 레이어가 끝나면 ~ 형상의 중심을 기점으로 3o 회전하고 1 mm 높이 상승해서 다음 층을 적층 하는 방식으로 총 15회 적층하였다. 옆면은 45o 기울기를 가졌고, 회전에 따른 각 층간의 최대 Offset 거리는 약 0.5 mm으로 비드 선폭 약 3 mm 위에 증착 하여도 형상이 무너지지 않고 잘 형성 됨을 알 수 있었다.
Fig. 11은 다른 형상의 3차원 적층 형상을 보여준다. 바닥직경 20 mm를 기준으로 5개 층을 Z 방향으로 기울기 약 60o 커지게 증착 하다가 다시 작아지도록 하는 형상(총 10 층), 바닥면 내부 직경이 30 mm, 외부 직경이 46 mm인 반원을 각 층마다 높이방향으로 0.5 mm씩 Offset을 주어 8번째 층에서는 서로 접합되어 삼각형의 반원 터널을 적층 제조한 형상이다.
다른 응용의 예로는 롤 표면에 적층 하는 것으로 와이어 공급이 고정형일 경우 클래딩 공정이 일반적이다. 본 회전형 와이어 공급장치의 경우 롤 커터에 적용할 수 있는 다양한 형상을 Fig. 12와 같이 롤 표면에 적층 하였고, 일부를 45o 테이퍼를 가진 밀링 공구를 이용하여 후가공 하였다. 커터부의 프로파일을 측정한 결과는 Fig. 13과 같이 거의 45o 기울기를 갖는 날을 형성함을 알 수 있다.
3.4 Infilling 적층
적층 제조기술은 모재 표면에 돌출되는 형상뿐만 아니라 오목한 부분을 적층하여 평탄하게 할 수 있어야 한다. 이는 예를 들면, 금형의 치수가 다르거나 파손이 되었을 경우 그 부분을 기계가공으로 제거한 다음 다시 채워 넣어야 할 경우, 또는 설계상 채널을 가공하고 상부를 덮어야 할 경우에 필요하다. 분말을 사용할 경우 적층 과정에서 적층에 관여하지 않고 가스에 의해 외부로 분출되지 못한 분말이 내부에 쌓일 경우 다음 적층 공정에서 이로 인해 적층 불량이 나타날 수 있다. 와이어의 경우 적층에 관여하지 않는 부분이 없이 100% 적층이 되기 때문에 분말에 비해 유리하다고 할 수 있다.
내부 적층에서는 바닥면에서의 결합 정도보다 측면에서의 결합 정도가 더 약할 수 있다. 이는 레이저 빔이 모재 내부의 측면에 의해 반사 될 수 있기 때문이다. 이를 확인하기 위해 Fig. 14와 같은 시편(40 mm × 250 mm)을 제작하여 홈(바닥면 길이35 mm, 테이퍼각도 45o, 깊이 3.5 mm)을 채우고 상면을 밀링 가공 한 후 다시 하면을 방전 및 밀링 가공으로 표준 시편을 만들어 인장 테스트를 수행하였다.
높이 간격 1 mm로 총 4개 층을 적층 하였고 각 층당 비드 간격은 양 측면을 기준으로 길이를 구한 다음 2.2 mm를 기준으로 일정하게 나누어 구하였다. 그 결과 바닥면으로부터 2.14 mm, 2.13 mm, 2.11 mm 및 4번째 층에서는 2.10 mm의 간격이 얻어졌다. 홈 내부에 적층한 결과는 Fig. 15와 같고 이를 표준 인장시편(KS B 0801) 로 제작한 결과는 Fig. 16과 같다. 상면을 밀링 가공하였어도 육안으로 적층 부위 및 열영향부를 확인할 수 있었다.
Instron 5982, 100 kN 인장시험기로 인장 시험한 결과 Fig. 17에서 보는 바와 같이 벽측 경계면에서 파단은 일어나지 않아 경계면에서도 모재와 와이어간의 융착이 양호하게 일어남을 알 수 있었다.
회전형 와이어 공급장치를 이용해 Fig. 18과 같이 금형 외부가 손상을 받았다고 가정하여 직경 15 mm, 깊이 3 mm 및 테이퍼 각도 10o의 원형 홈을 가공한 후 내부를 그림과 같은 순서로 하여 적층 하였다. 이는 원형 형상을 증착할 때 와이어가 원의 법선 방향에서 공급이 되면 홈 내부의 벽면이 와이어 공급에 장애물이 되기 때문에 이를 피하기 위해 약 35o 기울여 와이어를 공급하였다. 적층 후 표면에서 융기된 형상은 밀링 가공 하였고 그 결과는 Fig. 18(b)와 같다. 내부에 일부 기공이 보이기는 하지만 이는 공정 조건을 다소 변경하면 개선 될 수 있을 것이라 생각되며, 내부 적층 공정에도 회전형 와이어 공급장치가 유용하게 적용되는 것에 무리가 없다.
4. 결론
금속 와이어를 적층 하는데 있어 적층 품질을 높이기 위해 적층 방향에 따라 와이어 공급기가 회전하는 새로운 개념의 와이어 공급 장치를 개발 하였고, 다양한 샘플을 적층 하는데 적용하여 효용성을 검토하였다. 회전형 와이어 공급기는 고정형에 비해 품질을 향상시킬 수 있었고, 전선 및 공압선의 꼬임 없이 무한회전이 가능하여 원통 형상을 연속적으로 적층 제조할 수 있었다. 또한 자유곡선 형상, 3차원 형상 및 롤 표면에도 적용 가능함을 보였고, 롤의 경우 기계 가공을 통해 롤 커터로의 가능성을 확인 하였다. 금형 내부 수리에도 적용 가능함을 보였으며, 45o의 기울기를 갖는 홈 내부 적층시 모재 벽면과의 융착성도 양호하게 일어나 계면에서 파단이 일어나지 않음을 알 수 있었다.
Acknowledgments
이 논문은 2017년 정부(과학기술정보통신부)의 재원으로 국가과학기술연구회 금속3D프린팅융합연구단 사업(No. CRC-15-03-KIMM)의 지원을 받아 수행된 연구임.
REFERENCES
-
Ding, D., Pan, Z., Cuiuri, D., and Li, H., “Wire-Feed Additive Manufacturing of Metal Components: Technologies, Developments and Future Interests,” International Journal of Advanced Manufacturing Technology, Vol. 81, Nos. 1-4, pp. 465-481, 2015.
[https://doi.org/10.1007/s00170-015-7077-3]
-
Zhai, Y., Lados, D. A., and LaGoy, J. L., “Additive Manufacturing: Making Imagination the Major Limitation,” Journal of The Minerals, Metals & Materials Society, Vol. 66, No. 5, pp. 808-816, 2014.
[https://doi.org/10.1007/s11837-014-0886-2]
-
Sames, W. J., List, F., Pannala, S., Dehoff, R. R., and Babu, S. S., “The Metallurgy and Processing Science of Metal Additive Manufacturing,” International Materials Reviews, Vol. 61, No. 5, pp. 315-360, 2016.
[https://doi.org/10.1080/09506608.2015.1116649]
-
Williams, S. W., Martina, F., Addison, A. C., Ding, J., Pardal, G., et al., “Wire + Arc Additive Manufacturing,” Materials Science and Technology, Vol. 32, No. 7, pp. 641-647, 2016.
[https://doi.org/10.1179/1743284715Y.0000000073]
-
Abioye, T., Folkes, J., and Clare, A., “A Parametric Study of Inconel 625 Wire Laser Deposition,” Journal of Materials Processing Technology, Vol. 213, No. 12, pp. 2145-2151, 2013.
[https://doi.org/10.1016/j.jmatprotec.2013.06.007]
-
Heralić, A., Christiansson, A.-K., and Lennartson, B., “Height Control of Laser Metal-Wire Deposition Based on Iterative Learning Control and 3D Scanning,” Optics and Lasers in Engineering, Vol. 50, No. 9, pp. 1230-1241, 2012.
[https://doi.org/10.1016/j.optlaseng.2012.03.016]
-
Hagqvist, P., Heralić, A., Christiansson, A.-K., and Lennartson, B., “Resistance Measurements for Control of Laser Metal Wire Deposition,” Optics and Lasers in Engineering, Vol. 54, pp. 62-67, 2014.
[https://doi.org/10.1016/j.optlaseng.2013.10.010]
-
Ding, D., Pan, Z., Cuiuri, D., Li, H., and Larkin, N., “Adaptive Path Planning for Wire-Feed Additive Manufacturing Using Medial Axis Transformation,” Journal of Cleaner Production, Vol. 133, pp. 942-952, 2016.
[https://doi.org/10.1016/j.jclepro.2016.06.036]
-
Liu, S., Liu, W., Harooni, M., Ma, J., and Kovacevic, R., “Real-Time Monitoring of Laser Hot-Wire Cladding of Inconel 625,” Optics & Laser Technology, Vol. 62, pp. 124-134, 2014.
[https://doi.org/10.1016/j.optlastec.2014.03.007]
-
Miranda, R., Lopes, G., Quintino, L., Rodrigues, J., and Williams, S., “Rapid Prototyping with High Power Fiber Lasers,” Materials & Design, Vol. 29, No. 10, pp. 2072-2075, 2008.
[https://doi.org/10.1016/j.matdes.2008.03.030]
-
Mok, S. H., Bi, G., Folkes, J., and Pashby, I., “Deposition of Ti–6AL–4V Using a High Power Diode Laser and Wire, Part I: Investigation on the Process Characteristics,” Surface and Coatings Technology, Vol. 202, No. 16, pp. 3933-3939, 2008.
[https://doi.org/10.1016/j.surfcoat.2008.02.008]
-
Syed, W. U. H. and Li, L., “Effects of Wire Feeding Direction and Location in Multiple Layer Diode Laser Direct Metal Deposition,” Applied Surface Science, Vol. 248, Nos. 1-4, pp. 518-524, 2005.
[https://doi.org/10.1016/j.apsusc.2005.03.039]
-
Syed, W. U. H., Pinkerton, A. J., and Li, L., “A Comparative Study of Wire Feeding and Powder Feeding in Direct Diode Laser Deposition for Rapid Prototyping,” Applied Surface Science, Vol. 247, Nos. 1-4, pp. 268-276, 2005.
[https://doi.org/10.1016/j.apsusc.2005.01.138]
-
Fu, J., Gong, L., Zhang, Y., Wu, Q., Shi, X., et al., “Microstructure and Mechanical Properties of TI-6AL-4V Fabricated by Vertical Wire Feeding with Axisymmetric Multi-Laser Source,” Applied Sciences, Vol. 7, No. 3, p 227, 2017.
[https://doi.org/10.3390/app7030227]