
개선된 플렉시블 패킹 링을 통한 증기터빈 로터의 진동 저감에 관한 연구
Copyright © The Korean Society for Precision Engineering
This is an Open-Access article distributed under the terms of the Creative Commons Attribution Non-Commercial License (http://creativecommons.org/licenses/by-nc/3.0) which permits unrestricted non-commercial use, distribution, and reproduction in any medium, provided the original work is properly cited.
Abstract
Steam turbines of thermal power plants are installed in such a way that packing ring surrounds the entire turbine rotors in order to reduce the amount lost due to a leak of steam and to improve performance. However, the conventional packing ring cannot affect positively fluid velocity of the direction of steam, so it does not have the power to reduce vibration of the rotor. In this research, a study was conducted to reduce it by lowering the rotational speed of steam in the rotor. Anti-swirl teeth which changes rotational speed of steam into axial speed of it, designed in front of the conventional packing rings, and their numbers, twist angles. The characteristics of the rotor and the anti-swirl teeth were chosen as design factors to reduce vibration of the rotor. Through the finite element, the improved packing ring designed with the optimal anti-swirl teeth was developed.
Keywords:
Packing ring, Anti-swirl, Vibration reduction, Leakage, Finite elements analysis키워드:
패킹 링, 안티 스월, 진동 저감, 누설, 유한요소해석1. 서론
화력발전소의 터빈은 전기 생산에 중추적인 역할을 하는 매우 중요한 설비이다. 터빈의 효율 증대를 위하여 설계 개선 및 신소재 개발 등이 요구되지만, 상당한 시간과 비용이 소모되기 때문에, 기존 터빈의 효율 저하 요인을 분석하고 이를 개선하여 효율을 향상시키는 것이 효과적이다. 터빈 효율 저하의 주요 요인으로는 유체 흐름부의 손상 및 누설로 인한 증기의 손실 등이 있으며, 이중 누설 손실이 전체의 50%를 차지하고 있다. 특히, 누설 손실 중 패킹 링에서 발생하는 누설이 22.3%이므로,1 이에 대한 연구가 필요한 실정이다. 기존 터빈의 패킹 링에 관한 연구에서 Kim 등은 패킹 링에 플렉시블 씰(Flexible Seal)을 설치하고, 플렉시블 씰과 로터 사이의 간극을 감소시켜 누설량이 저감된 모델을 제안하였다.1 U. Yucel 등은 증기터빈에 설치되는 패킹 링과 로터 사이의 누설량을 유량 계수를 활용한 무 차원 변수로 나타내어, 입구 부와 출구 부의 압력 비에 따른 연구를 수행 하였다.2 Heo 등은 투스 날의 각도에 따라 유체가 흐르는 유로의 폭을 줄일 수 있는 투스를 가진 패킹 링을 제시 하였다.3 이처럼, 기존에는 로터와 투스의 간극을 조절하거나 투스의 형상 변경에 따른 누설량 제어에 관한 연구는 다양하게 수행되어 왔으나, 로터에 의한 유체의 로터 회전 방향 흐름과 이에 의한 로터의 진동에 미치는 영향에 대한 연구는 미흡한 실정이다. 실제 터빈에 적용되고 있는 기존 패킹 링은 누설량 감소에는 효과가 있으나, 로터 회전 방향에 대한 유체의 속도 제어가 불가능하기 때문에 로터의 진동이 발생하여 투스에 마모가 발생하는 문제점이 있다.
이에 본 논문에서는 증기의 로터 회전 방향 속도에 의해 발생하는 로터의 진동 저감을 위한 플렉시블 패킹 링에 대한 연구를 수행하였다. 기존의 누설 저감을 위한 플렉시블 씰이 장착된 패킹 링에 유체의 흐름을 인위적으로 바꾸는 안티 스월 투스(Anti-Swirl Tooth)를 설계하였으며, 안티 스월 투스의 비틀림 각도, 개수 및 로터와의 간극을 설계인자로 선정하고, 유동해석으로부터 도출된 유체의 로터 회전 방향 속도를 비교하여 진동이 저감된 최적의 안티 스월 투스 형상을 선정하였다. 또한, 선정된 진동이 저감된 모델의 유한요소해석을 수행하여 누설 저감 성능 및 구조 안전성을 검증하였다.
2. 플렉시블 패킹 링의 진동 저감
2.1 플렉시블 패킹 링의 구조 및 역할
증기터빈은 보일러에서 생산된 고온고압의 증기를 팽창시켜 열 에너지를 속도 에너지로 바꾸고, 속도 에너지를 가진 증기를 회전 날개에 충돌시켜 기계적 에너지로 변환 시킨다. 증기터빈은 노즐의 역할을 하는 고정 날개와 속도 에너지를 기계적 에너지로 전환시키는 회전 날개로 구성 되어 있다. 이 때 고정 날개와 회전 날개를 통과하여 로터를 회전시키는 고온고압의 증기가 로터와 고정 날개의 틈새로 누설 되는 것을 막기 위하여 증기의 누설을 감소시키는 패킹 링이 고정 날개의 끝에 Figs. 1(a)와 1(b)와 같이 설치되어 있다. 로터와의 간극(Clearance)을 줄여 유체가 흐르는 유로를 좁히거나 투스의 각도 변경을 통하여 기밀성을 향상시킨다. 본 연구의 패킹 링은 Fig. 2(a)와 같이 몸체의 홈 부에 플렉시블 씰, 그 상단에 플렉시블 씰의 충격을 흡수하는 스프링, 몸체의 앞쪽에 안티 스월 투스로 구성되어 있으며, 이를 조립하면 Fig. 2(b)와 같다.
기존 패킹 링의 경우, 투스의 날 형태가 양날(Double Edge Tooth)이며 로터와의 간극이 전 구간에서 0.3 mm로 동일하다. 반면에 개선된 패킹 링은 진동 감소를 위한 안티 스월 투스가 입구부에 설치되어 있으며, 좁은 간극(0.15 mm)을 가지는 플렉시블 씰로 인하여 간극이 다른 일반 투스 부분보다 좁다. 플렉시블 씰은 Fig. 3과 같이 패킹 링의 바디에 장착되며, 플렉시블 씰과 패킹 링 사이에 판 스프링(Plate Spring)이 설치되어 있다.
터빈 구동 시, 로터와 플렉시블 씰 사이의 간극(0.15 mm)이 패킹 링 투스와의 간극(0.3 mm)보다 작아 로터의 진동이 발생하였을 때, 플렉시블 씰이 로터에 먼저 닿기 때문에 플렉시블 씰을 제외한 다른 투스에서는 마모가 발생하지 않고, 플렉시블 씰 또한 상단의 스프링으로 인하여 마모량을 대폭 감소시킬 수 있다. 또한, 간극을 줄일 수 있으므로,1 기존 대비 기밀성(Tightness)을 향상시킬 수 있다. 편날 형태의 투스(Single Edge Tooth)가 적용되어 기존의 양날일 때 보다 유체의 흐름이 로터 방향으로 유도되어 유로가 좁아짐에 따라 누설량이 감소하는 장점이 있으며,4 이를 Table 1 및 Fig. 4에 나타내었다.
2.2 증기터빈 로터의 진동 저감 방안
증기터빈의 로터는 정상 상태에서 약 3,600 rpm의 속도로 회전하는데, 로터와 직·간접적으로 마찰을 일으키는 패킹 링에서 증기의 유동은 Fig. 5(a)와 같다.
이 때, 축의 고속 회전에서 기인한 전단력에 의해 발생되는 힘으로 인하여 축과 패킹 링 사이의 유동 공간에서 증기의 로터 회전 방향 속도 및 불안정성(Instability)을 증가시킨다. 축이 고속회전함에 따라 축과 패킹 링 틈새에서 증기의 로터 회전 방향 속도는 증가하게 되며, 이 때 증기의 전단력에 의하여 감쇠 효과가 작아지고 로터가 받는 반력이 증가하여 로터의 진동도 커지게 된다.5-8
증기의 로터 회전 방향 속도 감소에 따른 로터의 진동 저감을 위해 패킹 링의 앞 부분에 안티 스월 투스를 설치하였다. 안티 스월 투스를 통과하기 전 유체는 로터의 회전 방향으로 흐르지만 Fig. 5(b)와 같이 안티 스월 투스를 장착하여 축 방향으로 흐르게 유도함으로써, 회전 방향 속도를 줄여 증기의 불안정성에 의한 로터의 진동을 저감한다.9
3. 유한요소해석
3.1 유동해석을 통한 안티 스월 투스 형상 설계
개선된 패킹 링은 로터의 회전축을 중심으로 대칭인 형상이므로, 유한요소 해석 시간 단축을 위하여 Fig. 6(a)와 같이 1/18(20o) 부분 모델링을 수행하였으며, 모델링 형상은 Fig. 6(b)와 같다.
최적의 안티 스월 투스 개선 설계를 위하여 투스의 개수, 비틀림 각도 및 로터와의 간극을 설계 변수로 선정하였다. 현장에서는 45o의 각도를 가진 180개의 안티 스월 투스가 설계되었으며, 이를 토대로 Fig. 7과 같이 투스의 개수를 150개, 180개 및 210개, Fig. 8과 같이 비틀림 각도를 30o, 45o 및 60o, Fig. 9와 같이 로터와 간극을 1.2 mm, 1.4 mm 및 1.6 mm로 나누었다.10 설계인자가 로터의 진동 저감에 미치는 영향도 파악을 위하여 Table 2와 같이 총 7가지의 개선된 패킹 링의 해석 모델(Models 1-7)과 기존 패킹 링(Model 8)에 대하여 유동해석을 수행하였다. Models 1-3은 비틀림 각도와 간극을 고정시키고 투스 개수만을 변화시켰고, Models 2, 4 및 5는 투스 개수와 간극은 고정시키고 비틀림 각도만을 변화시켰으며, Models 2, 6 및 7은 개수와 비틀림 각도는 고정시키고 간극만 변화시켰다.
상용 소프트웨어인 ANSYS Workbench 17.0 CFX를 이용하였으며, 유동해석에는 유로 부 모델이 필요하므로 ANSYS Design Modeler의 Fill 기능 이용하여 Fig. 6의 3D 모델링에서 패킹 링과 로터 사이의 유동영역을 Fig. 10(a)와 같이 추출하였다. 유체의 거동에 대한 발달을 고려하기 위해 입구부와 출구부에 각각 높이 5배의 유동영역을 생성하였고, 유동 영역을 Fig 10(b)에 나타내었다.
해석의 정확성을 위하여 유동영역의 벽면에 Fig. 11(a)와 같이 인플레이션 격자(Inflation Mesh)를 생성하여 유체의 점성을 고려하였다. 또한, 밀어내기 기법(Sweep Method)으로 회전체의 특성을 정확하게 구현하도록 하였으며, Fig. 11(b)와 같이 약 340 만개의 요소를 생성하였다.
본 해석 모델의 경우 벽면 부 및 좁은 틈새에서의 유동과 완전 발달한 유동 영역이 존재하므로 SST 난류 모델을 선정하였고,1 경계 조건의 경우 실제 터빈에서 측정하여 얻은 입구 및 출구 압력인 23.82 MPa 및 3.96 MPa을 각각 적용하였다. 또한, 터빈의 회전속도는 정상 상태에서의 속도인 3,600 rpm이며 작동 유체는 이상 기체이며, 이를 Table 3에 나타내었다.4,9,11
기존 패킹 링과 안티 스월 투스가 장착된 개선된 패킹 링의 유동해석을 수행하여, 그 결과를 비교하였다. 기존 패킹 링의 경우 Fig. 12(a)와 같이 입구측의 유체가 로터의 회전 방향으로 흐른다. 반면, Fig. 12(b)와 같이 안티 스월 투스를 장착하게 되면 투스의 비틀림 각도에 의해 유체의 방향이 바뀌는 것을 알 수 있다.
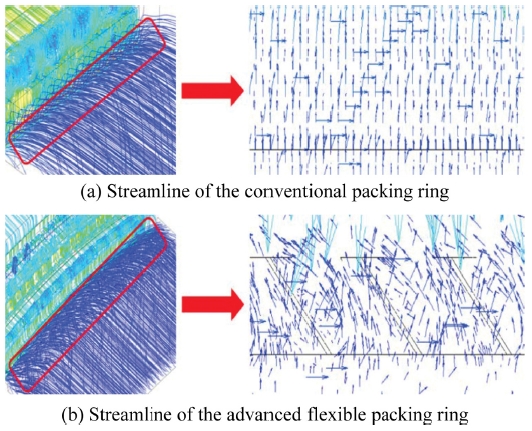
Comparison of streamlines of the conventional packing ring with that of the advanced flexible packing ring
진동 저감 여부을 판단하기 위하여, 각 모델의 최대 로터 회전 방향 속도를 Table 4에 나타내었다. 기존 패킹 링(Model 8)은 모든 개선된 모델(Models 1-7)보다 속도가 높게 도출되어, 안티 스월 투스가 로터 회전 방향 속도를 줄여 증기의 불안정성 감소로 인한 로터의 진동 저감에 효과적임을 알 수 있다.5 안티 스월 투스의 개수만을 변경한 Models 1-3의 결과를 비교해보면, 안티 스월 투스의 개수가 많을수록 유체의 로터 회전 방향 속도가 낮아지는 경향을 보인 반면에, 로터와 안티 스월 투스 사이의 간극만을 변경한 Models 2, 6 및 7에서는 로터와 안티 스월 투스의 간극이 좁을수록 속도가 낮아지는 경향을 보였다. 또한 로터와 안티 스월 투스의 비틀림 각도만을 변경한 Models 2, 4 및 5를 비교해 보면, 각도가 45o인 경우 유체의 진행 방향과 안티 스월 투스가 이루는 각이 수직에 가까워져 속도가 가장 크게 저감됨을 알 수 있었다.12
상기의 결과로부터 Models 1-7 중 로터 회전 방향 속도가 가장 낮은 Model 3에 대하여 누설량 비교 및 구조안전성 검증을 수행하였다. 기존의 패킹 링과 개선된 플렉시블 패킹 링의 누설량을 비교하기 위해 출구 측에서의 유량이 시간에 따라 일정한 값을 보이는 안정화된 시점에서의 값을 도출하였다. Table 5 및 Fig. 13에 의하면, 1.089 kg/s에서 0.985 kg/s로 약 9.56% 누설량이 감소되었는데, 이는 플렉시블 씰을 장착함으로써 투스와 로터와의 간극을 기존보다 더 좁게 할 수 있었기 때문이다.
3.2 안티 스월 투스가 설계된 플렉시블 패킹링의 구조 해석
유동해석을 통해 얻은 최적의 결과인 비틀림 각도 45o, 투스 개수 210개 및 로터와의 간극 1.2 mm인 개선된 플렉시블 패킹 링의 구조 안전성을 판단하기 위하여 구조 해석을 수행하였다. 패킹 링의 소재인 SUS410의 기계적 물성치는 Table 6과 같다. 가장 가혹한 조건에서의 구조해석을 위하여, 유동 해석의 결과에서 도출된 유동영역의 최대 압력인 23.82 MPa을 Fig. 14와 같이 부여하였다.
개선된 패킹 링의 구조해석 결과, Fig. 15(a)와 같이 응력이 분포하는 것을 확인하였으며, Fig. 15(b)와 같이 패킹 링과 안티 스월 투스가 맞닿는 부분에서 가장 높은 값인 267.83 MPa의 등가응력이 발생하였다. 이는 소재(SUS410)의 항복강도인 721 MPa 보다 낮으므로, 구조적으로 안전할 것으로 사료된다.
4. 결론
본 연구에서는 화력 발전소 증기터빈의 진동 저감을 위해 안티 스월 투스를 장착한 개선된 플렉시블 씰이 장착된 개선된 패킹 링을 개발하였다. 증기의 로터 회전 방향 속도 제어를 통한 진동 저감을 위하여 안티 스월 투스 비틀림 각도, 개수 및 로터와의 간극을 설계 인자로 선정하여 유동 해석 및 구조해석을 수행하였고, 그 결과를 요약하면 아래와 같다.
(1) 기존의 패킹 링의 로터 회전방향 속도가 18.93 m/s인데 비하여 안티 스월 투스가 장착된 패킹 링의 비틀림 각도(45o), 투스의 개수(210개) 및 간극(1.2 mm)일 때, 유체의 로터 회전 방향 속도가 12.65 m/s로 크게 저감되어 로터의 진동 저감에 효과적임을 알 수 있었다.
설계 인자의 영향도를 분석한 결과, 안티 스월 투스 개수나 로터와의 간극보다는 안티 스월 투스의 비틀림 각도를 변경하였을 때, 속도가 가장 크게 변화하여 비틀림 각도의 영향도가 가장 큰 것을 확인하였다.
유동해석을 수행한 결과, 플렉시블 씰로 인하여 로터와 투스 사이의 간격이 저감된 개선된 패킹 링의 누설량이 기존 패킹링 보다 약 9.56% 낮음을 확인하였다.
유동해석으로부터 도출된 최대 압력을 개선된 패킹 링의 구조에 적용한 결과, 패킹 링과 안티 스월 투스가 맞닿는 부분에서 가장 높은 등가응력(267.83 MPa)이 패킹 링 소재(SUS410)의 항복 강도(721 MPa)보다 낮으므로 구조적으로 안전함을 확인하였다.
본 연구에서 제안된 안티 스월 투스를 장착한 개선된 플렉시블 패킹링을 적용하여, 증기터빈의 효율을 증대 시키고 진동 저감으로 인한 내구수명 증가 누설량 감소가 기대된다.
Acknowledgments
이 논문은 2015년 중소기업청 구매조건부신제품개발사업의 일환으로 수행하였음(S2337069).
REFERENCES
-
Kim, J. H., Bae, J. H., Lee, C.-R., and Kim, C., “Development of Flexible Packing Ring in Steam Turbine for Reduction of Leakage by using CFD Flow Analysis,” Journal of the Korean Society for Precision Engineering, Vol. 30, No. 7, pp. 741-748, 2013.
[https://doi.org/10.7736/KSPE.2013.30.7.741]
-
Yucel, U. and Kazakia, J., “Analytical Prediction Techniques for Axisymmetric Flow in Gas Labyrinth Seals,” Journal of Engineering for Gas Turbines and Power, Vol. 123, No. 1, pp. 255-257, 2001.
[https://doi.org/10.1115/1.1340630]
- Hur, J., Ahn, J., Park, J., Moon, S., Lee, J., et al., “Analysis of Leakage through Labyrinth Seal in a Steam Trubine due to Modification the Teeth Angle,” Proc. of the Society of Air-Conditioning and Refrigerating Engineers of Korea Winter Conference, pp. 313-318, 2009.
- Ha, T.-W. and Kang, J.-H., “Leakage Analysis of Angled-Labyrinth-Packing-Ring Seal for Steam Turbine Using CFD,” Journal of the Korean Society of Tribologists and Lubrication Engineers, Vol. 25, No. 5, pp. 298-304, 2009.
-
Yang, S.-H., Kim, Y.-S., Nah, U.-H., and Park, J.-G., “Root Cause and Countermeasure on the Spike Vibration of a 550 MW Class USC (Ultra Super Critical) Steam Turbine,” Transactions of the Korean Society for Noise and Vibration Engineering, Vol. 17, No. 12, pp. 1238-1245, 2007.
[https://doi.org/10.5050/KSNVN.2007.17.12.1238]
-
Lee, G. J. and Kim, J. H., “Study for Fracture in the Last Stage Blade of a Low Pressure Turbine,” Transactions of the Korean Society of Mechanical Engineers A, Vol. 40, No. 4, pp. 423-428, 2016.
[https://doi.org/10.3795/KSME-A.2016.40.4.423]
-
Youn, H.-C., Woo, C.-K., and Hwang, J.-K., “Investigation of the Cause of High Vibration in a Low Pressure Turbine Casing with Manufacturing Defects by Frequency Response Analysis,” Journal of The Korean Society of Manufacturing Technology Engineers, Vol. 24, No. 4, pp. 463-468, 2015.
[https://doi.org/10.7735/ksmte.2015.24.4.463]
- Ethos Energy, “How to Improve Steam Turbine Head Rate and Increase Output,” https://www.slideshare.net/MargaretHarrison1/smart-seal-power-magazine-webinar-final, (Accessed 31 MAY 2018)
-
Lim, S., Kim, M., Kang, Y., and Park, W., “Honeycomb Labyrinth Seal Leakage Characteristic Analysis with Actual Operating Conditions on the Compressor of Gas Turbine,” Journal of Computational Fluids Engineering, Vol. 20, No. 4, pp. 102-108, 2015.
[https://doi.org/10.6112/kscfe.2015.20.4.102]
-
Gamal, A. J. and Vance, J. M., “Labyrinth Seal Leakage Tests: Tooth Profile, Tooth Thickness, and Eccentricity Effects,” Journal of Engineering for Gas Turbines and Power, Vol. 130, No. 1, Paper No. 012510, 2008.
[https://doi.org/10.1115/1.2771571]
-
Hirano, T., Guo, Z., and Kirk, R. G., “Application of Computational Fluid Dynamics Analysis for Rotating Machinery—Part II: Labyrinth Seal Analysis,” Journal of Engineering for Gas Turbines and Power, Vol. 127, No. 4, pp. 820-826, 2005.
[https://doi.org/10.1115/1.1808426]
-
Kang, S. Y., Jang, H. J., Lee, J. J., Kim, D. S., Park, S. J., et al., “Rediction of Stage Efficiency Variation of a USC High Pressure Steam Turbine by Computational Fluid Dynamics,” The Korean Fluid Machinery Association, Vol. 20, No. 2, pp. 17-25, 2017
[https://doi.org/10.5293/kfma.2017.20.2.017]