
레이저 가속 플라이어의 고속 충돌을 이용한 금속표면의 마이크로 형상 가공
Copyright © The Korean Society for Precision Engineering
This is an Open-Access article distributed under the terms of the Creative Commons Attribution Non-Commercial License (http://creativecommons.org/licenses/by-nc/3.0) which permits unrestricted non-commercial use, distribution, and reproduction in any medium, provided the original work is properly cited.
Abstract
Generally speaking, the high speed forming process is suitable for the precise manufacturing of hard-to-form and high strength materials. This study conducted microscale embossing and punching experiments by establishing a forming system that uses a laser induced acceleration. The changes in the flyer velocity with the laser energy, flyer thickness, and flyer diameter were measured using a high speed camera, and the effects of the noted acceleration characteristics of flyers on processing performance were investigated. It is particularly important that in the case of punching, the advantages of high speed processing, in which the accuracy was improved by increasing the shear zone of the workpiece, were identified. Significantly in the case of embossing, it was observed that the formability improved by increasing the flyer velocity as the flyer diameter decreased. However, in the case when the flyer thickness was decreased, increased energy was consumed in the plastic deformation of the flyer, and the advantages of high speed forming could not be realized. For this reason, further research is needed to take advantage and optimize the forming process using the laser induced acceleration through experiments which are noted as considering the various process variables and materials.
Keywords:
Micro features, High-speed impact, Laser accelerated flyer, Embossing, Micro forming키워드:
미세 형상, 고속 충돌, 레이저 가속 플라이어, 엠보싱, 마이크로 성형1. 서론
최근 제품의 소형화와 경량화가 중요해짐에 따라 다양한 고강도 재료를 이용한 정밀 부품의 가공에 대한 관심이 높아지고 있다.1,2 하지만 성형 기법을 이용한 가공시 대부분의 고강도 재료는 성형성(Formability)이 낮기 때문에 기존의 성형 기술을 그대로 적용하기에는 한계가 있다.3 이러한 문제점을 해결하기 위하여 가공물을 매우 짧은 시간 동안 변형시켜 가공하는 고속성형법(High Velocity Forming)이 제안되었다.4 고속성형에서는 소재가 높은 변형률(Strain Rate) 조건에서 국부적으로 변형되면서 전단효과(Shear Effect)가 증가하고 소재의 성형성도 향상된다.5 또한 표면 주름(Wrinkling) 및 스프링백(Springback)이 감소하기 때문에 성형 품질의 향상에도 도움이 되는 것으로 알려져 있다.5,6
이러한 고속성형 공법으로는 폭발성형(Explosive Forming)이나 전자기 성형(Electromagnetic Forming)이 가장 널리 활용되고 있다. 하지만 폭발 성형의 경우 사용자의 안전에 주의가 필요하고, 전자기 성형은 가공물이 도체가 아니면 성형을 할 수 없는 단점을 가지고 있다. 또한 위의 공법들은 기본적으로 매크로 스케일(Macro-Scale) 영역에서 주로 사용되기 때문에 마이크로 크기의 정밀 부품 가공을 위해서는 새로운 고속성형 공법이 필요하다.6
레이저 유도 가속을 이용한 성형 공정은 고출력 펄스 레이저를 이용하여 박판 플라이어(Flyer)를 고속으로 가속시키고, 이를 가공물에 충돌시켜 매우 짧은 시간에 소재를 변형시키는 공법이다. 다른 공정에 비해 장비가 간단하고, 제어성, 반복성 및 가공 정밀도가 우수하기 때문에 마이크로 형상의 정밀가공에 적합하다. 따라서 이에 관한 연구가 최근 활발히 진행되고 있는데, Liu 등7은 레이저 삭마에 의해 발생하는 플라즈마의 충격파를 이용하여 금속 박판을 가속시키고, 소재를 펀칭(Punching) 가공하는 실험을 성공적으로 수행하였다. 본 연구에서는 레이저 삭마 현상으로 생긴 충격파로 인해 가속된 금속 박판이 가공물에 충돌하게 되면, 가공물은 축방향 하중을 받으면서 몰드의 형상에 따라 전단되어 펀칭 가공됨을 관찰하였다. Wang 등8은 레이저 에너지의 전달효율을 높이기 위하여 다층(Multi-Layered) 구조의 플라이어를 제작하였고, 이를 통해 삼차원 구조의 마이크로 형상을 성공적으로 가공하였다. Banishev 등9은 플라이어의 속도를 측정하기 위하여 PDV (Photon Doppler Velocimetry) 시스템을 구축하였고, 플라이어의 소재 및 형상, 레이저 에너지, 비행거리 등 다양한 공정변수가 플라이어의 가속특성에 미치는 영향을 관찰하였다.
하지만 기존의 연구들은 아직 초기단계로 레이저 유도 가속에 의한 성형 공정의 적용 가능성을 확인하는 경우가 대부분이고, 플라이어의 가속특성이 가공성능에 미치는 영향에 관한 체계적인 연구는 아직 부족한 실정이다. 따라서 본 연구에서는 고속 카메라를 이용한 레이저 유도 가속 시스템을 구축하여 가속된 플라이어의 속도와 비행특성을 동시에 확인하였고, 마이크로 엠보싱 공정에서 플라이어의 가속 특성이 가공 성능에 미치는 영향을 고찰하였다. 플라이어의 두께와 지름, 레이저 에너지, 그리고 플라이어의 속도가 엠보싱 성능에 미치는 영향을 관찰하여, 다양한 공정변수들과 가공성능 사이의 상관관계를 연구하고자 하였다.
2. 실험 방법
Fig. 1은 레이저 유도 가속을 이용한 마이크로 엠보싱 실험의 개략도를 나타내고 있다. 본 시스템에서 레이저를 작동시키면 설정한 에너지 수준을 가진 레이저 빔이 발사되고, 발사된 빔은 반사경과 집속렌즈(Focusing Lens)를 거쳐 플라이어의 표면에 도달하게 된다. 레이저 에너지가 플라이어 표면을 순간적으로 삭마(Ablation)시키면 고온, 고압의 플라즈마가 발생하게 되는데, 이 플라즈마가 급속히 팽창하면서 플라이어를 가속시키고 플라이어는 가공물에 충돌하면서 고압의 에너지를 전달하여 가공물은 몰드의 형상으로 가공된다.
에너지 원으로는 파장 1064 nm, 펄스 폭 10 ns의 Q-Switched Nd:YAG 레이저를 사용하였고, 18만 FPS (Frame Per Second)의 고속 카메라를 이용하여 다양한 공정조건에서 플라이어의 가속특성을 관찰하였다. 플라이어의 속도는 플라이어가 가속되는 초기 10 mm 구간에서 5.5 μs 간격으로 촬영한 고속 카메라의 이미지를 이용하여 그 평균값을 계산하였다. 플라이어가 소재에 충돌할 때 고온의 플라즈마에 의해 가공물에 열손상이 발생하거나, 플라이어와 소재가 용융되어 접착되는 현상이 발생하였기 때문에 가공물과 플라이어 사이에 초탄성 소재인 폴리우레탄(Polyurethane)을 삽입하여 플라이어가 가공물에 미치는 열영향을 최소화하고자 하였다. 플라이어의 상단에는 유리 소재의 구속층(Confinement Layer)을 설치하고 이를 몰드 시스템에 단단히 고정하여 플라즈마가 가공물 방향으로만 팽창할 수 있도록 하였고, 가공물 상단에는 일정한 두께의 스페이서(Spacer)를 설치하여 플라이어가 충분히 가속될 수 있는 공간을 마련하였다. 플라이어의 가속 및 가공실험은 매질에 대한 제어 없이 공기 중에서 실시하였다.
몰드의 재질은 SM45C 탄소강으로 마이크로 엠보싱 공정을 위하여 몰드의 중앙에 지름 500 μm의 원형 구멍을 EDM (Electric Discharge Machining)을 이용하여 제작하였다. 금속 플라이어는 알루미늄을 이용하여 각각 200 μm 및 300 μm의 두께와 2.5 mm, 3.5 mm, 4.5 mm의 지름으로 제작하여 다양한 형상을 가진 플라이어의 가속특성과 가공성능을 관찰하였다. 플라이어의 지름은 몰드의 크기보다 크게 제작하여 가공물에 충분한 압력을 전달할 수 있도록 하였으며, 레이저 빔의 크기는 플라이어의 지름보다 작게 설정(2 mm)하여 삭마에 의한 플라즈마가 플라이어 측면으로 빠져나가는 것을 최소화하였다.
가공물은 두께 110 μm의 알루미늄 박판을 사각형으로 절단하여 사용하였으며, 가공 후 엠보싱 혹은 펀칭된 형상은 광학현미경과 비접촉식 삼차원 형상 측정장비(Nano3D) 및 SEM을 이용하여 관찰하였다.
3. 실험 결과 및 고찰
3.1 플라이어의 속도 측정
레이저 에너지와 플라이어의 두께 및 지름에 따른 플라이어의 속도 변화를 고속카메라를 이용하여 측정하였다. Fig. 2는 두께 300 μm, 지름 3.5 mm의 플라이어가 1.6 J의 레이저 에너지에 의해 가속되었을 때 연속 촬영한 고속카메라 사진을 보여주고 있다. 사진들 사이에서 플라이어가 이동한 거리를 측정하여 플라이어의 평균속도를 계산하였다. 플라즈마가 플라이어의 중앙 부분에서 발생하기 때문에 비행 중 플라이어의 중앙 부분이 볼록하게 변형되어 있는 것을 관찰할 수 있었다. 즉 플라이어가 가공물에 충돌할 때 중앙부분이 먼저 가공물에 접촉하여 압력을 전달하고 림(Rim) 부분은 순차적으로 가공물에 접촉하게 되는 것으로 판단된다.
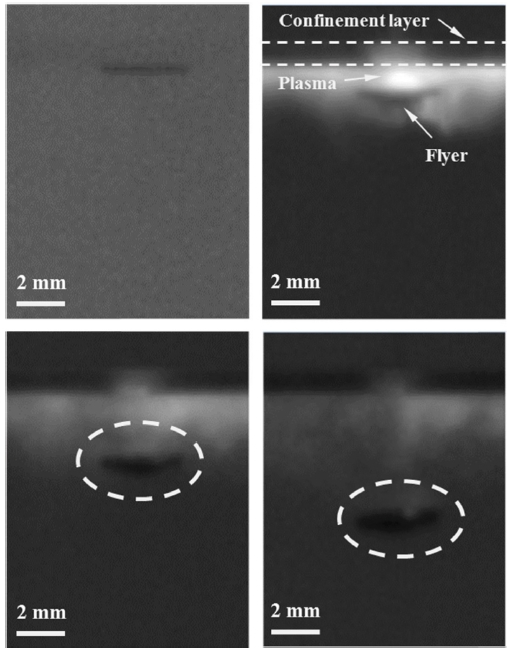
High-speed images of the launched 300 μm thick flyer with 3.5 mm diameter and 1.6 J laser energy (increasing order of time elapse of 0, 21, 42, and 63 μs)
Fig. 3에 다양한 레이저 에너지 값과 플라이어의 지름 및 두께 조건에서 플라이어의 속도를 측정한 결과를 나타내었다. 본 논문의 실험 조건에서는 플라이어의 두께 200 μm, 지름 2.5 mm에서 가장 큰 속도 값 330 m/s가 측정되었다. 플라이어의 두께와 지름이 감소하면 플라이어의 질량이 감소하기 때문에 플라이어의 속도가 증가하는 것을 확인할 수 있었다. 또한 레이저 에너지가 증가할수록 플라이어의 가속에너지가 증가하기 때문에 플라이어의 속도가 증가하는 것도 확인하였다.
한가지 주목할 점은 플라이어의 속도 측정 편차가 플라이어 지름 2.5 mm의 경우 급격히 증가한다는 것이었다. 이는 플라이어의 지름에 대한 레이저 빔의 상대적인 지름 비율이 영향을 미치는 것으로 판단된다. 이 비율이 감소하면 플라즈마에 의한 압력이 플라이어의 중앙 부분에 주로 작용하기 때문에 플라이어가 볼록한 형상을 유지하면서 비행하게 되지만, 이 비율이 증가할수록 플라즈마 압력이 플라이어 표면 전체에 작용하게 되면서 비행중 플라이어가 국부적으로 변형되기 보다는 작은 정렬오차에 대해서도 쉽게 회전하며 비행하게 된다. Fig. 4에서 플라이어의 지름이 2.5 mm인 경우 플라이어는 비행 중 수평을 유지하지 못하고 쉽게 회전하는 것을 관찰할 수 있다. 여기에서 발생하는 에너지 손실이 속도 측정의 편차를 일으키는 것으로 보인다. 또한 이 경우에는 플라이어와 구속층의 접촉상태에 따라 플라즈마 에너지가 플라이어 측면 방향으로 손실될 가능성도 높아진다.
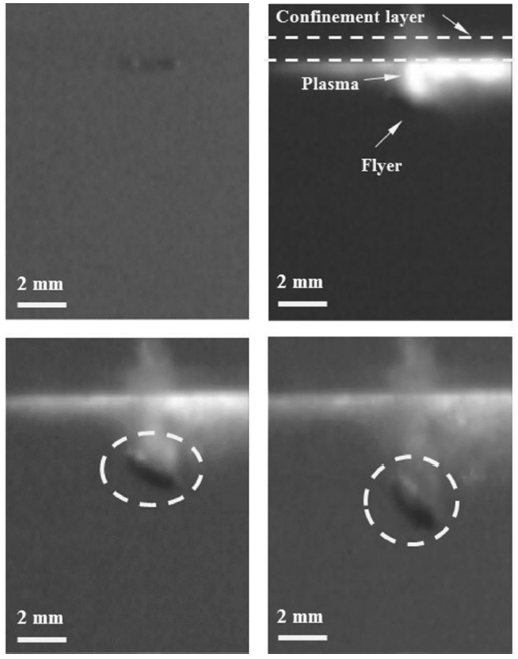
High-speed images of the launched 300 μm thick flyer with 2.5mm diameter and 1 J laser energy (increasing order of time elapse of 0, 21, 42, and 63 μs)
하지만 실제 가공 시 플라이어와 가공물의 충돌지점은 플라이 어의 비행거리가 200 μm인 초기 부분이기 때문에 이러한 회전 효과가 가공성능에 미치는 영향은 제한적이다. 속도 측정의 경우에는 데이터 수집을 쉽게 하기 위하여 인위적으로 플라이어의 비행거리를 가공 시보다 증가시켜 속도를 측정하였다.
3.2 가공성능 평가
레이저 유도 가속 플라이어를 이용한 가공 공정의 성능 평가를 위해 우선 레이저 에너지의 변화에 따른 가공 특성의 변화를 관찰하였다. 플라이어의 두께와 지름이 각각 300 μm와 4.5 mm로 고정된 경우 레이저 에너지가 2 J일 때 가공물이 성공적으로 펀칭 가공 되었고(Fig. 5), 에너지가 1 J인 경우에는 가공물이 엠보싱 가공됨을 확인하였다(Fig. 6). Fig. 5에서 펀칭된 가공물의 형상을 확인할 수 있는데 광학현미경 관찰 결과 펀칭된 구멍은 몰드의 형상에 따라 정밀하게 가공된 것을 볼 수 있다. SEM을 이용하여 파단면을 관찰하였을 때 롤오버(Roll-Over), 전단영역(Shear Zone), 버(Burr)와 같이 전형적인 펀칭 단면의 특성을 확인할 수 있었다. 또한 전단영역의 크기가 증가하여 가공 정밀도가 향상되는 고속 가공의 장점도 확인할 수 있었다.
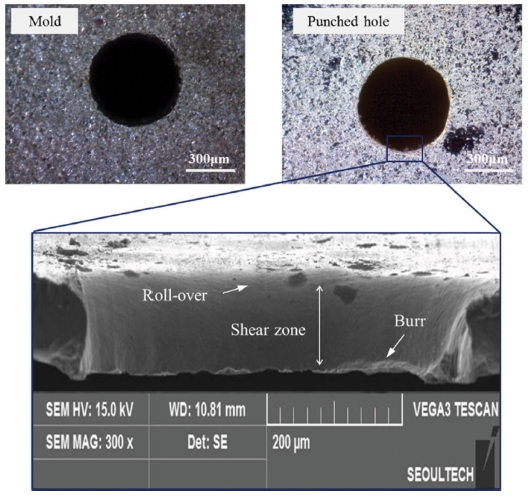
Microscopic and SEM images of punched workpiece by 300 μm thick flyer impact of 4.5 mm diameter at 2 J energy
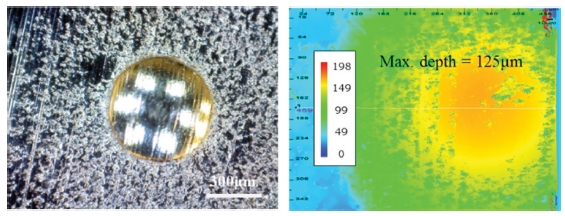
Microscopic image and deformed profile of embossed workpiece by 300 μm thick flyer impact of 4.5 mm diameter at 1 J energy
Fig. 6에서 볼 수 있는 것처럼 작은 에너지 조건(1 J)에서는 엠보싱 된 형상을 비접촉 삼차원 측정장비를 이용하여 측정하였는데, 엠보싱 형상의 대칭성을 확인할 수 있었고 최대 엠보싱 깊이는 125 μm로 측정되었다.
플라이어의 지름 변화가 가공성능에 미치는 변화를 관찰하기 위하여 레이저 에너지와 플라이어의 두께를 1 J과 300 μm로 고정한 상태에서 플라이어의 지름을 축소시켜 가공 실험을 실시하였다. 플라이어의 지름이 3.5 mm인 경우(Fig. 7), Fig. 6의 결과와 비교하였을 최대 엠보싱 깊이가 236 μm로 88% 증가한 것을 확인할 수 있었다. 플라이어의 지름을 2.5 mm로 더욱 감소시킨 경우에는 엠보싱 깊이가 깊어(즉, 300 μm이상) 측정 장비의 한계로 정확한 값을 측정할 수는 없었다. 하지만, 플라이어의 지름이 감소함에 따라 가공성이 증가하는 경향은 확인할 수 있었다.
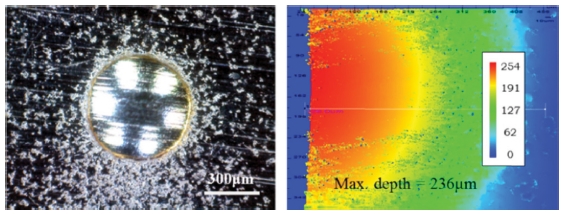
Microscopic image and deformed profile of embossed workpiece by 300 μm thick flyer impact of 3.5 mm diameter at 1 J energy
이러한 현상은 두 고체가 매우 빠른 속도로 충돌할 경우 생성되는 압력의 크기가 속도에 비례하는 고속가공의 특성에 기인하는 것으로 판단된다. Johnson10의 연구에 따르면 플라이어의 운동에너지가 가공물에 전달될 때 플라이어의 속도와 압력의 관계를 다음과 같이 모델링할 수 있다.
(1) |
여기서, 첨자 1과 2는 각각 플라이어와 가공물을 나타낸다. ρ 는 소재의 밀도이고 C는 재료의 종파 속도(Longitudinal Wave Speed)로 다음의 식으로 표현할 수 있다.
(2) |
여기서, K는 체적 탄성률(Bulk Modulus), ν는 재료의 포아송 비(Poisson’s Ratio)를 나타낸다. 식(1)과 식(2)에 따라 본 연구의 레이저 유도 가속 시스템을 통해 플라이어의 속도가 증가하면, 플라이어가 가공물에 전달되는 압력이 증가하여 가공성을 향상시킬 수 있다는 것을 확인할 수 있다.
동일한 에너지 조건에서 플라이어의 속도를 증가시키는 또 다른 방법은 Fig. 3에서 확인할 수 있는 것처럼 플라이어의 두께를 감소시키는 것이다. 따라서 플라이어의 두께를 200 μm로 감소시킨 상태에서 가공 실험을 실시하여 가공 성능의 향상 여부를 확인하였다. Fig. 8에서 확인할 수 있는 것처럼 가공물의 엠보싱 깊이는 지름 3.5 mm 플라이어의 경우 153 μm, 지름 4.5 mm 플라이어의 경우에는 93 μm였다. 앞의 실험과 동일하게 플라이어의 지름이 감소할 수록 속도가 증가하여 가공물의 엠보싱 깊이가 깊어지는 것을 확인할 수 있었다. 그러나 Figs. 6 및 7의 결과를 Fig. 8과 비교해 보면 플라이어의 두께가 감소할 때 엠보싱 깊이가 감소하는 것을 확인할 수 있었다. 이는 플라이어의 속도가 증가함에 따라 압력이 증가하게 되는 식(1)의 예측과 어긋나는 결과이다.
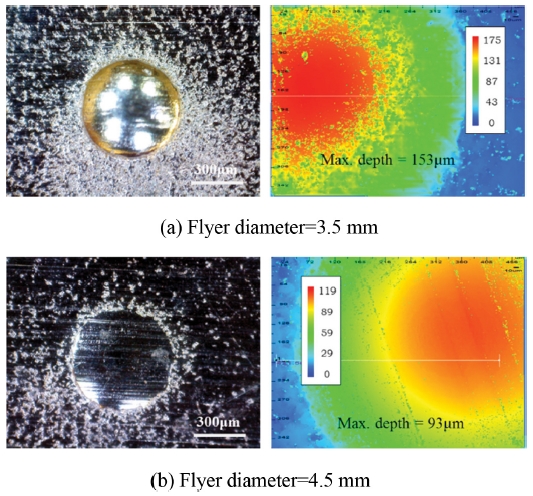
Microscopic image and deformed profile of embossed workpiece by 200 μm thick flyer impact at 1 J energy
엠보싱 깊이가 감소하는 원인은 플라이어가 가공물에 충돌 시 전달하는 압력의 전달 효율과 관련이 있는 것으로 판단된다. 즉 플라이어의 두께가 얇아지는 경우 플라이어가 가공물에 충돌할 때 플라이어에 변형이 일어나면서 에너지의 상당 부분이 플라이어의 소성 변형에 소모되는 것으로 보인다. Fig. 9로부터 200 μm 두께의 플라이어가 300 μm 두께의 플라이어보다 국부적인 변형이 심하게 발생하였음을 확인할 수 있다.
Table 1에 레이저 유도 가속 플라이어를 이용한 마이크로 엠보싱 실험결과를 정리하여 나타내었다. 결론적으로 레이저 유도 가속을 이용한 가공 공정에서 플라이어의 절대적인 속도를 증가시키는 것도 중요하지만 플라즈마 압력의 전달 효율을 높이는 것도 중요한 것으로 판단된다. 플라이어의 지름 변화는 비행특성의 변화가 적어 속도 증가가 가공 성능의 향상으로 이어졌지만, 플라이어의 두께 변화는 플라이어의 소성변형에 따라 압력 전달 메커니즘이 변화되어 가공성을 향상시키는데 한계가 있었다. 향후 다양한 공정변수에 대한 추가 실험을 실시하여 레이저 유도가속을 이용한 가공에서 최적화 된 공정조건을 찾아내는 연구가 필요하다.
4 결론
본 연구에서는 레이저 유도 가속을 이용한 고속 성형 시스템을 구축하여 마이크로 형상을 엠보싱 혹은 펀칭 가공하는 실험을 수행하였다.
(1) 고속카메라를 이용하여 레이저 에너지, 플라이어의 지름 및 두께에 따른 플라이어의 속도 변화를 관찰하였고, 플라이어의 가속 특성이 가공 성능에 미치는 영향을 고찰하였다.
(2) 레이저 유도 가속 시스템을 이용하여 가공물을 성공적으로 펀칭 혹은 엠보싱 가공할 수 있었다. 펀칭 단면 관찰 결과 전단영역이 증가하는 고속 가공의 특징을 관찰할 수 있었고, 엠보싱 가공의 경우에도 플라이어의 지름을 감소시켜 속도를 증가시켰을 때 가공성이 향상되는 것을 확인하였다.
(3) 플라이어의 두께를 감소시킨 경우에는 플라이어의 국부적인 소성변형의 증가로 고속 가공의 장점을 구현하는데 한계가 있었다. 향후 보다 넓은 범위의 소재 및 공정 조건에 대한 추가적인 연구가 필요하며, 가공 공정의 최적화를 통해 레이저 유도 가속 시스템의 적용 범위를 확대할 수 있을 것으로 기대된다.
Acknowledgments
이 연구는 서울과학기술대학교 교내 학술연구비 지원으로 수행되었습니다.
REFERENCES
-
Kim, H. S. and Nam, J. S., “Quantitative Modeling and Characterization of the Size Effects in Microscale Coining Process of Copper,” Precision Engineering, Vol. 51, pp. 490-498, 2018.
[https://doi.org/10.1016/j.precisioneng.2017.10.004]
-
Kim, H. S., “A Quantitative Study of the Tribological Size Effect in Microforming with a Multi-Region FEA Model,” Tribology International, Vol. 90, pp. 104-112, 2015.
[https://doi.org/10.1016/j.triboint.2015.04.016]
-
Nam, J. S., Lee, S. W., and Kim, H. S., “Experimental Study on the Size Effect and Formability of Sheet Materials in Microscale Deep Drawing Process,” Journal of the Korean Society for Precision Engineering, Vol. 32, No. 9, pp. 793-798, 2015.
[https://doi.org/10.7736/KSPE.2015.32.9.793]
-
Seth, M., Vohnout, V. J., and Daehn, G. S., “Formability of Steel Sheet in High Velocity Impact,” Journal of Materials Processing Technology, Vol. 168, No. 3, pp. 390-400, 2005.
[https://doi.org/10.1016/j.jmatprotec.2004.08.032]
-
Liu, H., Hu, Y., Wang, X., Shen, Z., Li, P., et al., “Grain Refinement Progress of Pure Titanium during Laser Shock Forming (LSF) and Mechanical Property Characterizations with Nanoindentation,” Materials Science and Engineering A, Vol. 564, pp. 13-21, 2013.
[https://doi.org/10.1016/j.msea.2012.11.087]
-
Wang, X., Shen, Z., Gu, C., Zhang, D., Gu, Y., et al., “Laser Indirect Shock Micro-Embossing of Commercially Pure Copper and Titanium Sheet,” Optics and Lasers in Engineering, Vol. 56, pp. 74-82, 2014.
[https://doi.org/10.1016/j.optlaseng.2013.12.012]
-
Liu, H., Wang, H., Shen, Z., Huang, Z., Li, W., et al., “The Research on Micro-Punching by Laser-Driven Flyer,” International Journal of Machine Tools and Manufacture, Vol. 54, pp. 18-24, 2012.
[https://doi.org/10.1016/j.ijmachtools.2011.12.004]
-
Wang, X., Yuan, Y., Shen, Z., Gu, C., Zhang, Q., et al., “Investigation of the Forming Pressure and Formability of Metal Foil by Laser-Driven Multi-Layered Flyer,” Optics & Laser Technology, Vol. 58, pp. 151-160, 2014.
[https://doi.org/10.1016/j.optlastec.2013.11.013]
-
Banishev, A. A., Shaw, W. L., Bassett, W. P., and Dlott, D. D., “High-Speed Laser-Launched Flyer Impacts Studied with Ultrafast Photography and Velocimetry,” Journal of Dynamic Behavior of Materials, Vol. 2, No. 2, pp. 194-206, 2016.
[https://doi.org/10.1007/s40870-016-0058-2]
- Johnson, W., “Impact Strength of Materials,” Edward Arnold Publishers Ltd., pp. 35-40, 1972.