
공압 프린팅 시스템에서 용액의 표면 장력이 토출 액적에 미치는 영향
Copyright © The Korean Society for Precision Engineering
This is an Open-Access article distributed under the terms of the Creative Commons Attribution Non-Commercial License (http://creativecommons.org/licenses/by-nc/3.0) which permits unrestricted non-commercial use, distribution, and reproduction in any medium, provided the original work is properly cited.
Abstract
This paper presents results for effects of the liquid surface tension on the ejected droplet volume using a pneumatic printing system. The low surface tension of the solution causes the liquid wetting around the nozzle, and then the wetted nozzle also inhibits stable formation of droplets. First, we confirmed the maximum inlet pressure (i.e., balanced with capillary force on the outlet channel) corresponding to varied surface tensions of the solutions, prepared by controlling the concentration of a surfactant. The ejected droplet volumes with the surfactant concentrations was varied within approximately 7% at each maximum inlet pressure, and the volume variation decreased to a fifth as compared with a high surface tension liquid.
Keywords:
Pneumatic, Printing, Ejected droplet, Surface tension, Surfactant키워드:
공압, 프린팅, 토출 액적, 표면 장력, 계면활성제1. 서론
미량의 액적(Droplet)을 원하는 위치에 전달하는 잉크젯(Inkjet) 기술은 미세 패턴을 제작하는데 있어서, 기존의 포토리소그래피(Photolithography)를 이용한 방법에 비해 재료 사용량의 최소화 및 제작 공정 단순화와 같은 장점들을 제공할 수 있다.1 효과적인 제조 도구(Fabrication Tool)로써 잉크젯 기술을 활용하기 위해서, 다양한 기능성 재료들을 이용하여 유기 태양 전지(Organic Solar Cell),2 유기 박막 트랜지스터(Organic Thin Film Transistor),3 조직 공학 분야의 세포 구조물 제작4과 같은 응용 연구들이 활발히 진행되어 오고 있다.
프린팅 기술에서 잉크의 밀도(Density), 점도(Viscosity), 표면 장력(Surface Tension)과 같은 물성에 따라 시스템의 작동 조건이 달라질 뿐만 아니라 프린팅 성능에 영향을 미치게 된다.5 최근 다양한 기능성재료(Fuctional Materials)들을 이용한 응용 연구들이 많아지면서, 다양한 물성을 가지는 용액(i.e., 잉크)을 적용할 수 있는 프린팅 기술이 요구되고 있다. 특히, 용액의 표면 장력이 작아질 수록 프린팅 노즐에서 용액의 젖음(Wetting) 현상이 발생하게 되며, 노즐이 젖어 있거나, 노즐에 용액이 맺히게 되면 토출 액적의 직진성(Straightness), 미토출(Misfiring) 등에 영향을 주어 정상적인 프린팅이 어렵게 된다.6 일반적으로 프린팅 가능한 최소 표면장력은 약 30 mN/m으로 알려져 있다.6,7
본 연구에서는 공압 방식의 프린팅 시스템을 이용하여 다양한 표면장력을 가지는 용액들이 프린팅 노즐과 토출되는 액적에 미치는 영향에 대해서 확인하였다. 본 시스템의 노즐은 용액을 토출하는 기능과 동시에 용액이 노즐 밖으로 흐르지 못하게 모세관 밸브(Capillary Valve)와 같은 기능을 하게 된다. 계면활성제(Surfactant)를 이용하여 용액의 표면장력을 조절하였으며, 계면활성제 농도 별 모세관 밸브 기능을 할 수 있는 최대 압력을 확인하였고, 압력 조건 및 용액 표면장력 크기에 따른 토출되는 액적의 부피 변화를 확인 하였다.
2. 공압 분주 시스템과 모세관 밸브
실험에 사용된 공압 방식의 프린팅 시스템은 용액을 보관하는 저장소(Reservoir)와 솔레노이드 밸브를 포함하는 구동 부분, 그리고 용액 챔버(Liquid Chamber)와 노즐을 포함하고 있는 프린팅 헤드부분으로 구성되어 있다(Fig. 1(a)). 프린팅 헤드는 PDMS (Polydimethylsiloxane) 재질의 멤브레인을 중심으로 용액 입구와 노즐을 포함하는 실리콘 층과 압력 전달을 위한 홀을 포함하고 있는 유리 층으로 구성되어 있다(Fig. 1(b)).8
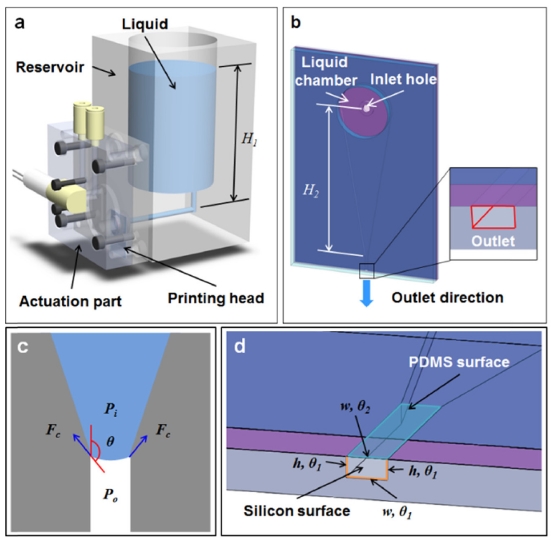
Schematic views of (a) inlet pressure caused by the liquid level in the reservoir and (b) in the dispenser, (c) the force balance between capillary and inlet pressure, (d) different contact surfaces of the liquid at the outlet nozzle
시스템은 초기 멤브레인에 가해진 음압(Negative Pressure)에 의해서 용액 입구(Inlet Hole)가 열리게 되고, 이를 통해 저장된 용액이 프린팅 헤드로 공급된다. 이때, 용액에 가해지고 있는 입구 압력(Inlet Pressure)에 의해 용액은 출구 방향으로 흐르게 되며, 노즐 부분에서 용액의 표면장력과 접촉각(Contact Angle)에 의한 모세관 힘(Capillary Force, Fc)과 용액 내부 압력(Pi)이 평형을 이루며 멈추게 된다(Fig. 1(c)). 모세관 힘의 방향이 용액이 흐르는 방향과 반대가 되기 위해서는 채널 표면과의 접촉각이 90° 이상이 되어야 한다. 사각 채널에서 평형 상태의 액체 내부와 외부의 압력 차이(ΔP = Pi − Po)는 Young-Laplace 방정식에 의해서 다음 식(1) 같이 나타낼 수 있다.9
(1) |
여기서, γ는 용액의 표면장력, θ는 용액이 채널 벽면에서 이루는 접촉각을 나타내며, h와 w는 각각 채널의 높이와 폭을 나타낸다. 일반적으로 접촉각은 움직이지 않는 평형상태의 정적 접촉각(Static Contact Angle)을 의미하며, 채널 내의 용액의 계면(i.e., 고체-액체-기체가 이루는 삼중선(Triple Line)이 움직이기 위해서는 정적 접촉각 보다 더 큰 접촉각을 이루게 되는데, 이를 전진 접촉각(Advancing Contact Angle)이라고 한다.10 따라서, 본 연구에서 접촉각은 모두 전진 접촉각을 측정하여 사용하였다.
저장된 용액은 정수압(Hydrostatic Pressure)을 받으며 프린팅 헤드로 공급되므로, 식(1)의 압력 차이는 식(2)와 같이 표현할 수 있다.
(2) |
여기서, ρ는 용액의 밀도, g는 중력 가속도, H는 용액의 중력 방향으로의 높이를 나타낸다. 노즐의 내부 벽면은 실리콘과 PDMS로 이루어져 있기 때문에, 각각의 재료 표면에서의 용액의 접촉각을 θ1(실리콘)과 θ2(PDMS)으로 구분하여 나타내었다. 용액의 높이(H)는 용액 저장소에서의 높이(H1, Fig. 1(a))과 헤드 내부에서의 높이(H2, Fig. 1(b))의 합으로 나타낼 수 있으며, 본 연구에서는 헤드 내부 높이(H2)는 1 cm으로 고정하였다.
3. 용액 표면장력과 최대 입구 압력
용액의 표면 장력에 따른 노즐의 기능과 토출되는 액적의 부피 변화를 확인하기 위해, 탈이온수(Deionized Water)에 계면활성제를 이용하여 용액의 표면장력의 크기를 조절하였다. 계면활성제는 주로 친수성(Hydrophilic) 부분과 소수성(Hydrophobic) 부분을 가지고 있는 화합물로, 용액의 표면 혹은 두 용액의 계면의 장력(Tension)을 낮춰주는 역할을 하며, 서로 다른 특성의 두 용액을 혼합 하기 위해 많이 사용된다.11
본 실험에서는 계면활성제인 Triton X-100(TX-100)을 0.04 mM에서 0.2 mM까지 첨가하여 용액의 표면장력을 조절하였다. 준비한 용액은 링 방식(Ring Method)의 표면장력 측정기(LAUDA, Ring/Plate-Tensiometer TD2)를 이용하여 상온에서 표면장력의 크기를 측정하였다. 채널 벽면 표면에서의 전진 접촉각을 측정하기 위해 실리콘과 PDMS 재료의 평판(Plate) 샘플을 준비하였으며, 일정량(Volume-6 μL)의 액적을 표면에 올려 놓고 천천히 표면을 기울이면서 액적이 움직이기 시작할 때 이미지를 분석하여 전진 접촉각을 측정하였다. 실제 프린팅 노즐은 Teflon 용액(0.1%, v/v)을 이용하여 소수성 코팅 후에 사용하였기 때문에, 측정 실리콘 샘플도 동일한 방법으로 Teflon 코팅이된 샘플에서의 전진 접촉각을 측정하였다. 계면활성제 농도별 용액의 표면장력 및 전진 접촉각 측정 결과는 Table 1에 정리하였다.
계면활성제의 농도별 노즐에서 모세관 밸브 기능을 할 수 있는 최대 입구 압력(Inlet Pressure)의 크기를 측정하였으며, 입구 압력은 용액 저장소의 수두 높이(H1)를 통하여 조절하였다. 최대 입구 압력은 용액의 연속 토출 전후에 노즐에 용액이 흘러 넘치지 않는 것을 기준으로 판단하였다.
측정 결과 농도별 최대 입구 압력은 0.5 kPa에서 1.8 kPa 범위에 있었다. Fig. 2는 입구 압력에 따른 용액의 계면의 위치 변화를 탈이온수를 이용하여 관찰한 광학 이미지들이며, 입구 압력이 증가할 수록 계면의 위치가 노즐 방향으로 이동하는 것을 확인할 수 있었다.
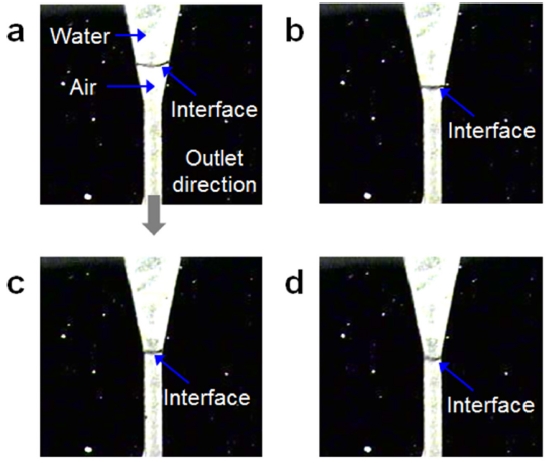
Optical images of the interface of the liquid (DI water) at the outlet with different inlet pressures: (a) 1.2 kPa, (b) 1.4 kPa, (c) 1.6 kPa, (d) 1.8 kPa
또한 식(2)을 이용하여 이론적인 최대 입구 압력을 계산하였으며, 그 결과 탈이온수를 제외하고 계면활성제가 포함된 용액의 경우 실험적으로 측정된 값보다 다소 낮게 계산되었다(Table 2).
4. 표면장력과 토출 액적
입구 압력이 토출되는 액적에 미치는 영향을 확인하기 위해서, 먼저 탈이온수를 이용하여 입구 압력을 0.5 kPa에서 1.5 kPa까지 증가시키면서 액적의 부피를 측정하였다. 토출되는 액적의 부피는 정밀 저울을 이용하여 측정하였으며, 측정 과정에서 용액의 증발로 인한 오차를 줄이기 위해서 실리콘 오일을 포함한 용기에 토출하여 전체 무게 변화를 측정하여 액적의 부피를 계산하였다. 용액을 밀어내는 압력인 양압(Positive Pressure)의 크기는 20 kPa에서 100 kPa까지 증가시켰으며, 음압(Negative Pressure, -5 kPa) 및 토출 주기(~33 Hz; Duration Time 10 ms and Delay Time 20 ms)는 일정하게 유지하였다. 토출 과정에서 멤브레인에 전달되는 압력의 시간에 따른 변화를 Fig. 3에 나타내었다. 작동 조건 및 토출 액적에 대한 자세한 내용은 이전 연구 결과에서 보고하였다.8,12
측정 결과, 양압의 크기가 증가할수록, 그리고 입구 압력이 증가 할수록 토출되는 액적의 부피가 증가하는 경향을 확인 하였다(Fig. 4). 전체 압력 범위에서 토출된 부피는 299 nL에서 715 nL로 측정되었으며, 각 측정값은 10회 이상 반복 측정하였으며, 이때 변동 계수(Coefficient of Variation, CV)는 1.04% 이내로 계산되었다. 입구 압력은 저장된 용액을 프린팅 헤드 내 용액 챔버(Liquid Chamber)로 공급하는 역할을 하기 때문에, 입구 압력이 클수록 정해진 시간(Delay Time) 내에 용액의 공급이 원활하게 이루어지며, 반대로 입구 압력이 작을 수록 공급 유량이 줄어들어 공급이 원활하지 못해, 동일한 양압 조건에도 토출 부피가 감소하는 것으로 보인다. 양얍의 크기가 20 kPa일 때, 입구 압력이 0.5 kPa일 때와 1.5 kPa일 때의 부피 차이는 약 50 nL이지만, 양압이 100 kPa일 때, 부피 차이는 약 255 nL로, 입구 압력의 영향은 양압의 크기가 클수록 더 크게 나타나는 것을 확인할 수 있었다.
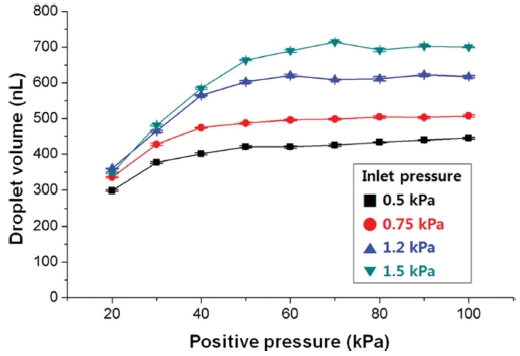
Droplet volume of DI water (without surfactant) vs. positive pressure with different inlet pressures from 0.4 kPa to 1.4 kPa (n > 10 and CV < 1.04%)
용액의 표면장력이 토출 부피에 미치는 영향을 확인하기 위하여, 계면활성제 농도를 조절하여 용액의 표면장력을 71 mN/m에서 32 mN/m까지 변화시켰으며, 각 용액의 토출 부피를 측정하였다. 또한 토출 주기에 의한 영향을 확인하기 위해서, 지연 시간(Delay Time)을 20 ms(~33 Hz)과 200 ms(~5 Hz)으로 조절하였으며, 입구 압력은 계면활성제 농도에 따라 노즐에서 용액 계면의 위치가 달라지기 때문에 용액 계면의 위치를 동일하게 하기 위해서 용액에 가해줄 수 있는 최대 입구 압력 조건으로 설정하였다. 이때 양압(100 kPa) 및 음압(-5 kPa)은 일정하게 유지하였다.
먼저 높은 토출 주기(~33 Hz) 조건에서, 계면활성제 농도 별 최대 입구 압력 조건(0.5 kPa~1.5 kPa)에서 토출된 액적의 부피는 703 nL에서 748 nL로 45 nL의 변화량을 보였으나, 계면활성제가 없는 탈이온수의 경우 동일한 입구 압력 조건에서 445 nL에서 700 nL으로 255 nL의 변화량을 보였다(Fig. 5(a)). 입구 압력의 크기에 따른 부피 차이는 계면활성제가 없는 탈이온수의 경우의 비해 계면활성제가 포함된 용액들의 경우 부피 변화량이 약 1/5 수준으로 줄어든 것을 확인 할 수 있었다. 이는 계면활성제로 인한 표면장력 및 접촉각의 감소로 인해 용액 계면이 이동할 때의 저항이 줄어든 효과로 예상 된다.13
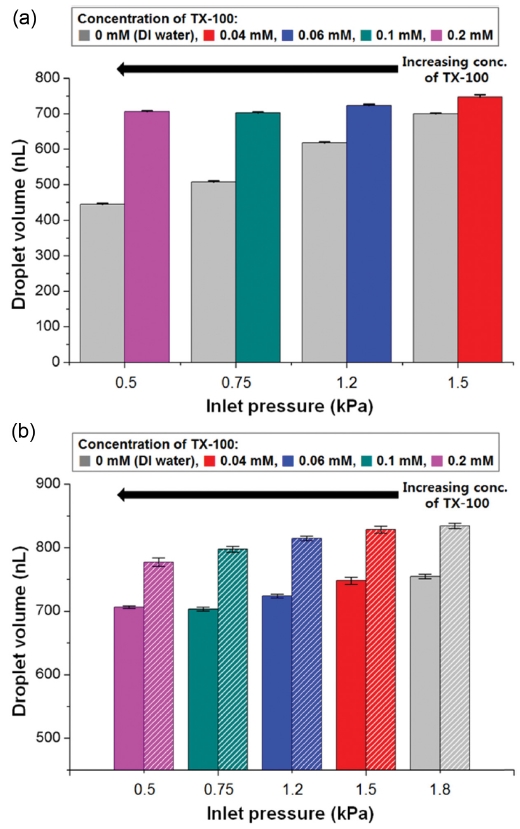
Droplet volume vs. inlet pressure with different concentrations of TX-100: (a) compared with DI water variation and TX-100 solution to inlet pressure (n > 10 and CV < 0.75%) and (b) droplet frequency was varied from 33 Hz (solid bar) to 5 Hz (patterned bar) (n > 10 and CV < 0.88%)
토출 주기에 의한 영향을 확인하기 위해서, 높은 주기(~33 Hz)에서 최대 입구 압력 조건에서 계면활성제 농도별(0 mM의 탈이온수 포함) 토출 부피는 703 nL에서 754 nL로 51 nL의 부피 변화를 보였다. 동일한 조건에서 낮은 주기(~5 Hz)의 경우 토출 부피는 777 nL에서 834 nL로 57 nL의 부피 변화를 보이는 것으로 확인 되었으며, 따라서 주기에 따른 계면활성제 농도별 부피 변화량의 차이는 크지 않은 것을 확인할 수 있었다.
전체 토출 주기에서, 계면활성제의 농도가 증가 할수록 토출 부피가 51~57 nL 정도 줄어드는 것을 확인할 수 있었다. 이는 계면활성제 농도가 증가 할수록 가해줄 줄 수 있는 최대 입구 압력의 크기가 감소하게 되며, 줄어든 입구 압력의 영향으로 토출 부피가 줄어든 것으로 예상된다. Fig. 5에서 측정된 모든 액적의 부피는 최소 703 nL에서 최대 834 nL 범위로, 모든 측정값들의 변동계수(CV)는 6.8% 이내로 계산되었다.
5. 결론
본 연구에서는 공압 방식의 프린팅 시스템을 이용하여 용액의 표면장력에 따른 토출 액적의 부피 변화에 대해서 확인하였다. 계면활성제의 농도를 조절하여 다양한 표면장력을 가지는 용액들의 모세관 밸브 기능을 할 수 있는 최대 입구 압력을 확인하였다. 먼저 계면활성제를 포함하지 않은 탈이온수를 이용해서 입구 압력에 따른 토출 부피 변화를 확인하였으며, 양압이 증가 할수록 입구 압력에 의한 공급 유량의 차이로 인한 토출 부피의 영향이 큰 것을 확인하였다. 계면활성제 농도별 토출되는 액적의 부피는 최대 입구 압력 조건에서 약 7% 정도 변하는 것을 확인 할 수 있었으며, 이는 계면활성제가 없는 경우에 비해 입구 압력에 따른 토출 부피 변화량이 1/5 수준으로 줄어든 것을 확인 하였다. 이와 같이 계면활성제를 통해 조절된 다양한 표면장력을 가지는 용액들 프린팅 노즐과 토출 부피에 대한 영향을 확인할 수 있었으며, 다양한 기능성 잉크를 개발하고 사용하는 프린팅 시스템에서 잉크의 표면장력 특성을 확인하고 이를 반영하여 토출 액적의 부피를 정밀하게 제어하는데 활용할 수 있을 것으로 기대한다.
Acknowledgments
이 성과는 2018년도 정부(과학기술정보통신부)의 재원으로 한국연구재단의 지원을 받아 수행된 연구임(No. 2017R1C1B5076710).
REFERENCES
-
Tekin, E., Smith, P. J., and Schubert, U. S., “Inkjet Printing as a Deposition and Patterning Tool for Polymers and Inorganic Particles,” Soft Matter, Vol. 4, No. 4, pp. 703-713, 2008.
[https://doi.org/10.1039/b711984d]
-
Kim, Y. H., Sachse, C., Machala, M. L., May, C., Müller Meskamp, L., et al., “Highly Conductive PEDOT: PSS Electrode with Optimized Solvent and Thermal Post Treatment for ITO Free Organic Solar Cells,” Advanced Functional Materials, Vol. 21, No. 6, pp. 1076-1081, 2011.
[https://doi.org/10.1002/adfm.201002290]
-
Kwak, D., Lim, J. A., Kang, B., Lee, W. H., and Cho, K., “Self Organization of Inkjet Printed Organic Semiconductor Films Prepared in Inkjet Etched Microwells,” Advanced Functional Materials, Vol. 23, No. 42, pp. 5224-5231, 2013.
[https://doi.org/10.1002/adfm.201300936]
-
Di Biase, M., Saunders, R. E., Tirelli, N., and Derby, B., “Inkjet Printing and Cell Seeding Thermoreversible Photocurable Gel Structures,” Soft Matter, Vol. 7, No. 6, pp. 2639-2646, 2011.
[https://doi.org/10.1039/c0sm00996b]
-
Choi, I. H., Kim, Y. K., Lee, S., Lee, S. H., and Kim, J., “A Pneumatic Drop-on-Demand Printing System with an Extended Printable Liquid Range,” Journal of Microelectromechanical Systems, Vol. 24, No. 4, pp. 768-770, 2015.
[https://doi.org/10.1109/JMEMS.2015.2433955]
-
Calvert, P., “Inkjet Printing for Materials and Devices,” Chemistry of Materials, Vol. 13, No. 10, pp. 3299-3305, 2001.
[https://doi.org/10.1021/cm0101632]
-
de Gans, B. J., Duineveld, P. C., and Schubert, U. S., “Inkjet Printing of Polymers: State of the Art and Future Developments,” Advanced Materials, Vol. 16, No. 3, pp. 203-213, 2004.
[https://doi.org/10.1002/adma.200300385]
-
Lee, S. and Kim, J., “Development and Characterization of a Cartridge-Type Pneumatic Dispenser with an Integrated Backflow Stopper,” Journal of Micromechanics and Microengineering, Vol. 20, No. 1, Paper No. 015011, 2009.
[https://doi.org/10.1088/0960-1317/20/1/015011]
-
Cho, H., Kim, H. Y., Kang, J. Y., and Kim, T. S., “How the Capillary Burst Microvalve Works,” Journal of Colloid and Interface Science, Vol. 306, No. 2, pp. 379-385, 2007.
[https://doi.org/10.1016/j.jcis.2006.10.077]
-
Gao, L. and McCarthy, T. J., “Contact Angle Hysteresis Explained,” Langmuir, Vol. 22, No. 14, pp. 6234-6237, 2006.
[https://doi.org/10.1021/la060254j]
-
Dionísio, M. and Sotomayor, J., “A Surface Chemistry Experiment Using an Inexpensive Contact Angle Goniometer,” Journal of Chemical Education, Vol. 77, No. 1, p. 59, 2000.
[https://doi.org/10.1021/ed077p59]
-
Lee, S., Choi, I. H., Kim, Y. K., and Kim, J., “Velocity Control of Nanoliter Droplets Using a Pneumatic Dispensing System,” Micro and Nano Systems Letters, Vol. 2, No. 1, 2014.
[https://doi.org/10.1186/s40486-014-0005-8]
-
Kim, A., Kim, H., Lee, C., and Kim, J., “Effective Three-Dimensional Superhydrophobic Aerogel-Coated Channel for High Efficiency Water-Droplet Transport,” Applied Physics Letters, Vol. 104, No. 8, Paper No. 081601, 2014.
[https://doi.org/10.1063/1.4866262]