
전기화학 미세가공기술의 현황
Copyright © The Korean Society for Precision Engineering
This is an Open-Access article distributed under the terms of the Creative Commons Attribution Non-Commercial License (http://creativecommons.org/licenses/by-nc/3.0) which permits unrestricted non-commercial use, distribution, and reproduction in any medium, provided the original work is properly cited.
Abstract
Electrochemical micromachining (ECM) processes use anodic dissolution of metals to remove workpiece materials. ECM processes including electrochemical milling and drilling, wire electrochemical machining and electrochemical etching offer a better alternative in manufacturing complex features and nano-pattern surface. Electrochemical discharge machining (ECDM) uses high temperature of electrochemical spark, which is suitable process for micro machining of hard brittle and non-conductive materials such as glass and ceramic. In this paper, the state of the art in electrochemical micro machining technologies was reviewed. Also, some hybrid machining methods are introduced.
Keywords:
Electrochemical machining, Electrochemical etching, Electrochemical discharge machining, Electrochemical oxidation assisted machining키워드:
전해가공, 전해에칭, 전해방전가공, 전기화학적 산화보조가공1. 서론
최근 전기, 기계 부품의 초정밀, 고성능화에 따라 여러가지 재료에 대한 미세 가공 수요가 증가하고 있으며, 이를 충족시키기 위해 정밀 기계적 가공뿐만 아니라 초음파가공, 레이저가공, 방전가공, 전해가공 등 다양한 가공기술이 연구되고 있다.
기계적 가공은 높은 형상정밀도, 고속가공 등의 장점을 갖지만 절삭력에 의한 공구 소형화의 어려움, 공구 마모 등의 한계가 있다. 레이저가공은 일반적으로 빠른 가공 속도로 다양한 재료를 가공할 수 있지만 낮은 형상 정밀도, 높은 열에 의한 가공물의 변형 등의 단점이 있다. 방전가공은 도전성의 재료를 경도에 무관하게 가공할 수 있다는 장점이 있지만 상대적으로 느린 가공속도와 전극마모가 심하다는 단점이 있다. 기계가공, 레이저 가공, 방전 가공 등 각기 다른 재료 제거 메커니즘을 갖고 있으며 서로 상호 보완적인 특징을 갖고 있다.
전기화학가공 또한 재료 제거를 위해 전기화학반응을 이용한 가공법이다. 전해액 속에 금속재료를 넣고 전류나 전압을 인가하면 전해액과 금속 사이에 화학 반응이 일어나고 이러한 금속 재료의 전해(Electrochemical Dissolution) 반응을 원하는 영역에 국부적으로 일어나게 함으로써 원하는 형상을 가공할 수 있다. 또한 화학반응을 적절히 조절하면 금속 표면에 높은 전기화학적 스파크이 발생되어 이를 이용하면 비전도성 재료도 가공할 수 있다.
전기화학가공(Electrochemical Machining)은 전해밀링, 전해드릴링, 와이어전해가공, 전해에칭, 전해방전가공, 산화응용가공 등 다양한 기술을 포함하고 있으며 본 논문에서는 다양한 전기화학가공(Electrochemical Machining)기술의 최근 연구 동향을 소개하고자 하며 특히 마이크로 가공 분야에 그 초점을 두었다.
2. 전해가공(Electrochemical Machining)
전해가공은 금속 재료의 전해반응을 이용한 가공으로서, 금속의 경도나 강도 등 기계적 성질에 무관하게 가공이 가능하고 가공물에 열변형, 잔류응력, 버 등이 발생하지 않아 표면 품질이 우수하고 정밀한 미세 형상 가공에 적합하다. 화학가공(Chemical Machining)과 비교할 때 큰 차이점은 전해 가공에서는 전압이나 전류를 인가한다는 것이다. 마이크로 전해가공에서는 전압(또는 전류) 조절을 통해 화학반응을 제어함으로써 가공 정밀도를 향상시킬 수 있는 장점이 있다. 하지만 가공 영역 전반에 균일한 전류 밀도를 갖도록 신경써야 하고, 반응 전류는 전극의 위치나 모양에도 영향을 받기 때문에 이에 대한 고려가 있어야 한다.
2.1 전해가공 원리 및 장치 구성
전해가공은 국부적으로 전기화학반응을 집중시켜 양극(Anodic)이 연결되어 있는 가공물의 이온이 전해액으로 용해(Anodic Dissolution)되는 현상을 이용하는 가공법이다.
일반적으로 양극성의 가공물과 음극성의 공구가 전해액에 담가진 상태에서 전원을 공급하면 각각의 전극 표면과 전해액 사이에서 화학반응이 일어난다. 이 때 전해액은 양극 용해가 일어나기 용이한 수용액이 사용되며 대표적으로 염화나트륨(NaCl), 질산나트륨(NaNo3) 수용액이 이용되지만, 가공물 종류에 따라서 염산(HCl), 불산(HF), 황산(H2SO4)용액 등이 사용될 수 있다. 특히 스테인리스 강의 마이크로 전해 가공에서는 황산, 불산, 염산의 강한 산성용액이 많이 사용된다. 전해액의 농도는 높을수록 가공속도가 증가하지만 그만큼 공구와 가공물 사이의 간극이 커져 가공정밀도가 떨어진다. 미세 가공에서는 전해액의 순환도 중요하며 전해 반응 시 발생하는 기포가 가공을 방해하기도 하기 때문에 진동을 부가하여 전해액의 순환을 돕고 기포를 제거하려는 연구가 있다. 다만 가공량이 많은 경우 전해액 자체를 순환시켜 새로운 용액을 공급할 필요도 있다. 공구와 가공물 사이에 인가하는 전압 또는 전류는 가공물의 용해 속도를 증가시키는 역할을 하며 전압이 높고 전류 밀도가 높을수록 반응이 빠르게 일어난다. 이 또한 반응이 빠른 만큼 가공 정밀도가 떨어지므로 적절한 조건 선정이 필요하다. 미세 형상 가공에서는 가공 정밀도를 높이기 위해 펄스 형태의 전압을 인가하며 서브 마이크로 미터의 가공 정밀도를 얻기 위해 수 ns에서 수십 ns 폭의 펄스전압을 인가하기도 한다. 한편 음극성의 공구에서는 환원반응이 일어나며 수소기체가 발생한다. 양극에서 발생하는 용출 현상이 없기 때문에 공구는 이론적으로 마모가 되지 않는다. 공구 재료는 화학적 안정성이 높은 금속재료가 유리하며, 미세 가공에서는 백금, 텅스텐, 스테인리스 강, 초경합금 등이 공구 재료로 많이 쓰인다. 백금은 화학적으로 매우 안정적이며 지름 수 마이크로의 와이어 형태로 얻을 수 있기 때문에 10 μm 전후의 미세 홈 등의 형상 가공에 유리하다. 텅스텐도 수 마이크로 미터의 와이어나 핀 형태로 사용되며 특히 텅스텐은 전해 에칭을 통해 끝반경이 서브 마이크로의 바늘 모양으로 가공가능하여 나노 크기의 형상 가공에도 이용될 수 있다. 미세 가공을 위한 미세 공구는 공구의 강성이 필요하며 그런 이유로 텅스텐, 초경합금, 스테인리스 강이 미세 전해 가공의 공구재료로 이용된다. 이들 공구는 많은 경우 와이어 방전가공, 전해에칭 방법으로 제작된다.
Fig. 1은 전해가공 시스템의 개략도이다. 전해가공 장치의 기본 구성은 공구, 가공물, 전해액, 전원공급장치이다. 전원공급장치로부터 직류 전압이나 펄스 전압이 공급되며, 음극은 공구에 연결되고 양극은 공작물에 연결된다. 전해액에 공구와 공작물을 담근 상태로 가공하거나 가공 영역에 전해액을 뿌려주는 방식이 사용되며 가공물 재료에 따라 적절한 전해액을 사용한다. 공구 형상과 이송 방법에 따라 전해 드릴링, 밀링, 와이어 전해가공 등으로 나눌 수 있다.
2.2 전해밀링(Electrochemical Milling)
전해밀링은 공구를 적절한 경로로 이송시켜 원하는 형상을 가공하는 방법이며, 가공하고하는 영역 외에서 발생하는 전해반응(Stray Corrosion)을 억제 시킴으로써 형상정밀도를 높이기 위한 연구가 이루어지고 있다.
Chen et al.1은 전해 밀링으로 미세 채널을 가공할 때 형상정밀도를 향상시키기 위해 이중 전해액 분사 시스템을 이용했다. 한방향으로만 전해액을 분사하는 방식은 편향된 전해액의 흐름 때문에 채널과 같은 가공 형상 옆벽의 형상정밀도가 낮아지는 문제가 있다. 이를 해결하기 위해 양방향에서 전해액을 분사함으로써 채널 옆벽의 형상정밀도가 향상되었으며, Fig. 2와 같이 수직에 가까운 옆벽 가공이 가능했다.
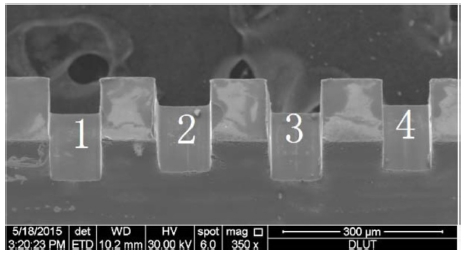
Micro groove-array fabricated by micro ECM1 (Workpiece: 304 stainless steel, Electrolyte: H2SO4) (Adapted from Ref. 1 on the basis of open access)
Zeng et al.2은 방전가공과 전해가공을 이용한 미세 형상 가공에 대해 연구하였다. 방전 표면은 재응고층(Recast Layer)에 의해 형상 정밀도 및 표면 품질이 떨어지지만 재응고층을 전해가공으로 제거함으로써 표면거칠기를 Ra 0.707 μm에서 Ra 0.143 μm으로 감소시키고 형상정밀도를 향상시켰다.
Ghoshal et al.3은 채널 형상을 제어하기 위해 공구 형상, 전해액 농도, 진동 부가에 따른 영향에 대해 연구하였다. 역테이퍼(Reverse Taper) 공구를 사용하여 채널 옆면의 경사를 2도까지 감소시켰으며, 적절한 전해액 농도 조건과 진동 부가에 의해 표면거칠기 Ra 0.02 μm 의 가공 면을 얻었다.
2.3 와이어 전해가공(Wire Electrochemical Machining)
와이어 전해가공은 미세한 와이어를 이용하여 특수한 형상을 쉽게 가공할 수 있는 장점이 있지만 높은 형상정밀도를 얻기 위해서는 와이어와 가공물 사이의 화학적 반응이 균일하고 안정적으로 일어날 수 있도록 해야 한다. 미세한 와이어를 사용하는 경우 와이어 주변의 전해액에서 국부적으로 이온이 감소하여 균일하고 안정적인 화학반응을 얻기 힘들어진다. 이를 해결하기 위해 Zeng et al.4은 와이어 전해가공에서 와이어 전극의 진동, 전해액순환(Flushing) 및 와이어 이송 속도가 가공에 미치는 영향에 대해 연구했다. 이와 같은 기술은 전극과 가공물 사이의 전해액 순환에 영향을 미치며 가공 안정성, 가공 속도, 가공 품질 등을 향상시켰다.
Fang et al.5은 와이어에 진동을 부가하는 방법을 이용하였다. 0.5-7.5 mm의 비교적 큰 진폭을 적용했으며, 와이어의 진동 진폭이 커질수록 공구와 가공물 사이의 기포가 효과적으로 제거되어 가공 속도가 증가하는 결과를 보였다. 또한, Fang et al.6은 다중 와이어 전극과 초단펄스를 이용한 연구도 수행했다. 3개의 와이어전극을 이용해 Fig. 3과 같은 형상을 두께 100 μm 스테인리스강에 가공했다.
2.4 전해드릴링(Electrochemical Drilling)
크기가 작고 깊은 구멍 가공에서는 가공 깊이가 깊어질수록 자연적으로 전해액이 순환되기 어렵기 때문에 가공 효율이 떨어지는 문제가 있다. 또한, 전해가공의 특성상 화학반응이 용이한 구멍의 입구가 출구보다 크게 가공되는 문제도 있다.
Koyano et al.7는 다공성의 전극을 이용하여 가공 형상 및 가공 효율을 향상시키기 위한 연구를 수행했다. 레이저 소결 기술을 이용하여 다공성 전극을 제작하고 공구의 미세한 구멍을 통해 전해액을 공급하는 방식을 이용했다. 다공성의 전극을 사용함으로써 가공 속도를 증가시키고 평평한 바닥면을 갖는 구멍을 가공했다. Koyano et al.8는 다른 연구에서 공구 끝부분에서는 전해 반응이 일어나도록 초단펄스를 적용하였다. 이를 이용하여 스테인리스강에 지름 55 μm, 깊이 54 μm의 구멍을 가공했다. 인가 전압 조건, 펄스 조건, 이송 속도가 미치는 영향을 분석하고 날카로운 모서리와 수직벽을 갖는 구멍을 가공했다.
전해 드릴링에서는 원활한 전해액 공급을 위해 구멍이 뚫려있는 공구를 통해 전해액을 공급하는 방식을 사용한다. 하지만 이때 구멍을 통해 나온 전해액이 난류를 만들어 가공을 불안정하게 만드는 요인이 된다. Zhu et al.9는 이런 문제를 해결하기 위해 공구의 옆면이 절연된 공구를 사용함과 동시에 공구를 통해 전해액을 토출하는 방식이 아니라 전해액을 빨아들이는 추출 방식을 이용했다. 동일한 조건에서 전해액을 토출하는 방식보다는 추출하는 방식이 가공안정성면에서 더 좋은 결과를 보였다. 또한, Zhu et al.10는 전해연삭 복합 가공을 이용한 스테인리스강의 구멍 가공에 대해 연구하기도 했다. 다이아몬드 입자가 코팅된 공구를 사용하였으며 공구회전속도, 전압, 공구이송속도가 가공 형상에 미치는 영향을 분석해 최적조건을 제시하고, 버가 없고 날카로운 모서리를 갖는 구멍을 가공했다.
2.5 전해가공을 이용한 마이크로 핀 제작
전해가공은 미세 형상 외에 고정밀, 고세장비의 마이크로 핀제작도 가능하다.
Fan et al.11은 전해가공을 이용해 텅스텐 마이크로핀을 제작했다. 전해가공 변수로서 인가 전압, 펄스 주기, Duty Factor, 온도가 가공에 미치는 영향을 분석하고, 지름 100 μm 고세장비의 마이크로핀을 제작해서 전해드릴링에 사용했다.
Han et al.12은 중성전해액과 초단펄스를 적용하여 고세장비의 미세 텅스텐 마이크로핀을 제작했다. 전해액 농도, 공구 이송 속도, 펄스 전압, 펄스 폭이 가공에 미치는 영향을 분석하였으며, 직경 7.1 μm, 세장비 14의 마이크로핀을 제작했다.
Wang et al.13은 다양한 형상의 미세 핀 가공을 위해 방전 가공으로 형상을 가공한 뒤, 전해가공으로 마무리 가공을 수행하였다. Fig. 4는 방전 전해 복합 공정을 이용해 지름 6 μm 마이크로핀과 지름 15 μm의 팁을 갖는 스타일러스(Stylus)를 가공한 예이다.
3. 전해에칭(Electro Chemical Etching)
3.1 전해에칭을 이용한 미세형상 가공
전해에칭은 대면적 가공에 적합한 가공법으로서 선택적인 가공을 위해 가공물 표면에 마스크가 필요하며, 가공 효율을 향상시키기 위해 다양한 마스킹 기술을 이용한 연구가 이루어지고 있다.
Jain et al.14은 전해 반응을 가공하고자 하는 영역에 집중시키기 위해 마스크를 이용했다. 마스크는 두께 50 μm의 투명한 시트를 사용했으며 레이저를 이용하여 제작했다. 마스크를 가공물 표면에 올려 놓고 전해 가공을 함으로써 형상정밀도를 향상시켰으며, 아크, 화살표, 갈지자형과 같은 다양한 형상을 쉽게 가공할 수 있었다.
Lei et al.15는 Photo-Assisted 전해에칭을 이용한 실리콘의 Wall Array 가공에 대해 연구했다. 전해액으로는 불산을 사용했으며 인가 전압, 전류 밀도가 미치는 영향에 대해 연구했다. 적절한 조건 선정을 통해 Fig. 5와 같이 폭 5.6 μm, 깊이 55 μm의 Wall Array를 가공했다.
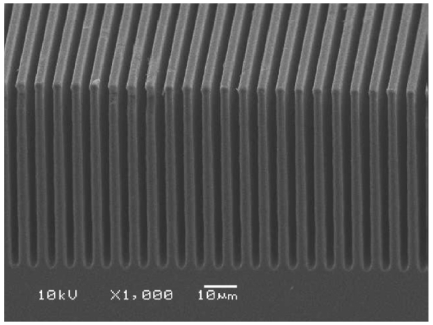
Micro wall array fabricated by photo-assisted electrochemical etching15 (Silicon wafer) (Adapted from Ref. 15 on the basis of open access)
Kikuchi et al.16는 아노다이징, 레이저, 전해에칭 공정을 이용해 알루미늄에 미세 형상을 가공했다. 아노다이징 공정에 의해 알루미늄 표면에 형성된 산화막을 레이저로 제거한 후, 전해에칭 공정을 수행했으며, 폭 60 μm, 깊이 25 μm의 채널을 포함하는 마이크로 챔버를 제작했다.
Shin et al.17은 레이저를 이용해 마스크가 필요없는 전해에칭 공정을 개발하였다. 먼저 스테인리스 강 표면에 레이저를 조사함으로써 금속 표면에 산화층을 형성하고 이 산화층은 상대적으로 전해반응이 더디게 만들기 때문에 결국 마스크와 같은 역할을 하게 된다. 이 방법은 기존의 마스크를 도포하는 공정이 필요 없고 선택적 마스킹(산화층 형성)이 가능하기 때문에 다단 구조물 가공도 가능하다.
그 밖에도 에칭률(Etching Rate)을 향상시키거나 깊은 형상을 가공하기 위한 연구도 이루어지고 있다.
Huang et al.18은 Metal-Assisted 전해에칭을 이용해 실리콘에 나노구조물을 가공했다. 은(Ag)과 구리(Cu)와 같은 금속은 전해반응을 촉진시키기 때문에 더 빠른 가공이 가능해진다.
Long et al.19은 에칭율을 향상시키기 위해 엑시머 레이저(Excimer Laser) 전해에칭을 이용했다. 전해에칭과 레이저에칭의 에칭율을 비교 연구했으며, 동일한 시간 동안 가공 깊이가 대폭 향상되는 결과를 보였다.
3.2 전해에칭을 이용한 표면 가공
전해에칭을 특정 재료에 적용하면, 재료 표면에 나노 단위의 다공성 표면을 만드는 것이 가능하다. 이러한 다공성 표면을 통해 투과율이나 반사율과 같은 재료의 광학 특성을 제어할 수 있어, 이에 대한 연구가 이루어 지고 있다.
Al-Heuseen et al.20은 UV-Assisted 전해에칭을 이용해 질화갈륨(GaN)의 발광량(Photoluminescence)을 향상시켰다. 전류 밀도의 변화에 따라 구멍의 크기 및 형상이 달라졌으며 전류 밀도가 증가할수록 발광량이 증가하는 결과를 보였다.
Lv et al.21은 실리콘 웨이퍼에 Fig. 6과 같이 다공성 피라미드(Porous-Pyramid) 패턴 표면을 만들어 반사율(Reflectance)을 감소시켰다. 일반적인 피라미드 패턴에 비해 다공성 피라미드 패턴의 반사율이 대폭 감소하는 결과를 보였다. 이는 빛을 더 잘 흡수할 수 있음을 의미하며 이를 이용해 태양전지의 효율을 향상시킬 수 있다.
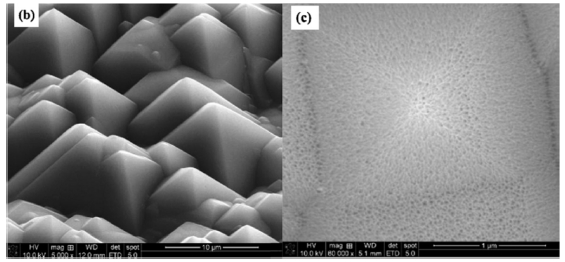
Porous-Pyramids structure fabricated by electrochemical etching21 (Adapted from Ref. 21 on the basis of open access)
Garralage Rojas et al.22는 전해에칭으로 게르마늄 웨이퍼에 이중층(Double Layer) 다공성표면을 만들었다. 이중층 구조를 만들기 위해서 양극과 음극을 바꾸는 방법을 이용하였다. 다공성은 전류 밀도와 전해액 농도에 의해 결정되며 각 층의 조건을 다르게 적용함으로써 서로 다른 다공성을 갖는 이중층 구조를 만들 수 있다.
4. 전해방전가공(Electrochemical Discharge Machining)
4.1 ECDM 원리 및 장치구성
전해방전가공(Electrochemical Discharge Machining, ECDM)은 유리와 같은 비전도체 가공에 효과적인 공정이다. 전해방전(Electrochemical Discharge)은 전해액에 담겨있는 전극에 적절한 전압을 인가했을 때 전극 주위에서 스파크를 발생하는 현상이다. 이 때 전극 주위에 발생한 수소 기체가 막을 형성하게 되는데, 이 막이 절연막의 역할을 하게 되어 방전을 유도하게 된다. 일정 전압 이상으로 인가 전압이 높아지면 절연막이 파괴되면서 전극 주위로 높은 열에너지를 가진 스파크를 발생시킨다. 이 때 스파크의 열에너지가 유리 표면을 일부 녹이면서 가공이 진행된다. 방전가공과 유사하게 공구가 재료에 접촉하지 않기 때문에 전극 마모가 거의 발생하지 않는 장점이 있다. 또한 전해방전가공 공정은 전극의 크기, 형상을 제어함으로써 다양한 3차원 구조물 제작이 가능하다는 점에서 유리 미세가공 공정으로써 많은 연구가 진행되고 있다.23-25
일반적으로 전해방전가공 장치는 방전가공시스템과 유사하다. Fig. 7은 일반적으로 알려져 있는 전해방전가공 실험 장치의 개략도이다. 전해방전가공 장치는 일반적인 3축 가공시스템과 유사하지만, 전해액 수조가 있어 가공물을 전해액에 담그고 가공을 진행하게 된다. 스핀들에는 음전극을 연결하기 위해 전압을 인가할 수 있는 브러시와 같은 구조를 장착한다. 음전극은 주로 초경 합금(WC-Co Alloy), 황동(Brass) 등을 사용하며 전해액은 KOH 또는 NaOH를 주로 사용한다. 카운터 전극(Counter Electrode)은 양극으로 화학반응에 안정적인 백금(Platinum)을 주로 사용한다.
4.2 전해방전가공 연구동향
전해방전가공의 가공 효율을 높이기 위한 연구가 활발히 진행되고 있다. 공정최적화를 통해 가공 효율을 높이는 연구는 지속적으로 발표되고 있으며, 최근에는 취성 및 내열성이 높아 가공이 어려운 석영(Quartz) 가공에도 공정 최적화를 통해 미세구조를 성공적으로 제작하는 등 전해방전가공 응용 연구가 활발히 진행되고 있다(Fig. 8).26 본 논문에서는 전해방전가공의 다양한 연구 중 가공 효율 및 형상 정밀도 향상을 위한 연구와 다른 기계가공과의 융합 연구를 주로 소개하고자 한다. 전해방전가공의 가공 효율 향상을 위해서 전극 형상, 전해액의 종류 등이 미치는 영향을 비교한 사례가 있다.
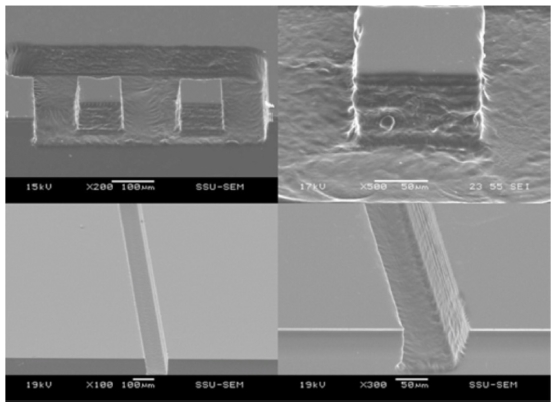
Micro column and grooves machined on quartz (30 V pulse voltage, 10 V offset voltage, 0.5 ms pulse on-time, 0.5 ms pulse off-time)26 (Adapted from Ref. 26 with permission)
전해방전가공에서 전극 형상은 전해방전이 발생하는 임계 전압과 밀접한 관계가 있어 가공 효과를 높이기 위한 다양한 전극 연구가 발표되었다. Yang et al.27은 홀 가공에서 형상정밀도를 높이기 위해 구형 전극(Spherical Tool Electrode)을 제안하였다. 원통형 전극(Cylindrical Electrode)을 사용하면 가공 깊이가 증가함에 따라 가공 시간과 직경이 증가하는 문제가 있다. 이를 개선하기 위해서 위 연구에서는 끝이 구형인 전극을 사용하였다. 전극 직경이 감소함에 따라 방전 스파크는 끝 단의 구 형상에 집중되어 가공 깊이가 깊어지더라도 전극 상단에서 발생하는 스파크 빈도를 감소시켜 형상 정밀도를 높일 수 있다. 이를 이용하여 일반 원기둥 형태의 전극에 비해 가공 홀의 직경이 65% 작아져 형상정밀도가 높아졌으며, 가공 시간 또한 83% 감소하는 효과가 있었다. Tang et al.28은 옆면 에서의 스파크 발생을 억제하기 위해 고안된 절연공구가 완벽한 절연막의 역할을 못하는 한계를 보완하기 위해 얇은 다이아몬드 막으로 완벽하게 절연된 공구를 제안하였다. 제안한 공구를 이용하여 목표 직경에 비해 넓은 직경의 홀이 가공되는 현상을 감소시킬 수 있음을 실험적으로 확인했다. 하지만 옆면 에서의 스파크 방전이 억제됨에 따라 가공 속도는 현저히 느려지는 단점이 있다.
전극 옆면에서의 방전을 이용하여 가공 효율을 높이는 연구도 진행되고 있다. Han et al.29은 전극 표면을 거칠게 제작한 전극(Surface Textured Tool)을 사용하여 가공 효율을 높였다. 사용된 공구는 방전가공을 이용하여 표면 거칠기(Ra) 1.5 μm 수준의 거친 면을 전극 표면에 구현한 것이다. 전해방전이 안정적으로 발생하는 임계 전압을 비교했을 때 표면 거칠기(Ra) 0.1 mm 수준의 매끄러운 공구에 비해 거친표면을 갖는 공구가 낮은 전압에서도 안정적인 방전이 가능함을 확인했다. 또한, 소다라임 유리(Soda-Lime Glass)의 2D 가공 실험을 통해 표면이 거친 공구를 이용했을 때, 표면이 매끄러운 공구를 사용한 결과에 비해 표면거칠기가 크게 개선되는 효과를 확인했다. 또한, 2D FEM 시뮬레이션을 이용하여 공구 표면의 미세 돌출부에 전기장이 집중되는 것을 확인했다.30 일반 전극은 전극 끝 단에 전기장이 집중되어 주로 스파크가 발생하는데 비해 표면이 거친 공구에서는 전극 표면에서 고르게 스파크가 발생함을 실험적으로도 확인할 수 있었다. Han et al.은 이를 이용해 1 : 4의 고세장비를 갖는 미세 홈을 가공하였으며, 홈 격벽의 각도 또한 3o 이내로 기존 전극에 비해 형상 정밀도를 높일 수 있었다.
또 다른 연구들로는 전해방전이 낮은 전압에서 발생할 수 있도록 하기 위해서 수소 기체 절연막을 얇게 하는 시도들이 있다. Jiang et al.31은 전해방전가공에서 수소 기체 절연막 형성의 수학적 모델을 제시하고 실험을 통해 검증하는 연구를 진행하였다. 모델을 통해 전해질의 농도나 표면 장력이 수소 기체 절연막 두께에 영향을 줌을 확인하였고, 수소 기체가 얇게 형성될수록 임계 전압과 통전 전류가 낮아져 방전이 쉽게 발생하는 것을 확인했다. 뿐만 아니라 임계 전압과 통전 전류 감소로 스파크의 과도한 열에너지로 인한 오버컷(Over-Cut) 현상을 줄일 수 있다는 결과를 알아냈다. 얇은 수소 기체 절연막을 형성하기 위한 방법으로 전해액에 계면활성제를 혼합하여 표면장력을 작게 만드는 연구가 있다(Fig. 9).32,33 Sabahi et al.32은 계면활성제의 종류와 농도를 달리하면서 미세 채널을 가공하였으며 혼합전해액을 사용함으로써 열변형부(Heat Affected Zone, HAZ)가 감소함을 실험적으로 확인하였다. Laio et al.33도 전해방전 드릴링에 계면활성제를 혼합하여 가공 속도를 높이고 구멍의 테이퍼가 작아지는 효과를 구현했으나, 구멍의 직경이 커지는 단점이 있었다.
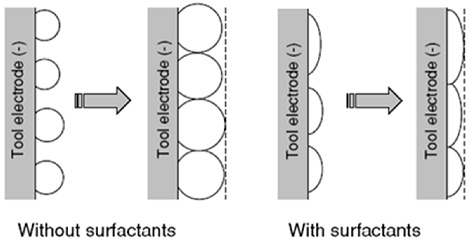
The air bubble linking modus with and without the surfactant33 (Adapted from Ref. 33 on the basis of open access)
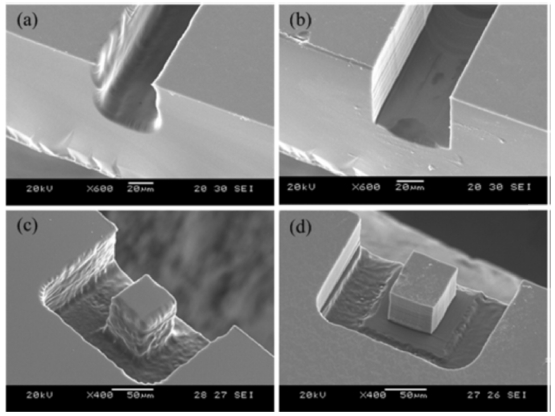
Micro structures machined by (a,c) ECDM and (b,d) then ground by a PCD tool35 (Adapted from Ref. 35 with permission)
Hajian et al.34은 전해방전 공정 중에 전극 주변에 자기장을 인가함으로써 수소 기체의 움직임을 조절하는 방법을 제안하였다. 자기장의 방향, 세기 그리고 전해액의 농도에 의해 수소 기체의 이동성을 변화시키면서 가공 깊이와 표면거칠기를 평가하였다. 자기장을 인가함으로써 표면거칠기의 개선 및 가공 깊이 향상이 가능함을 확인했다.
ECDM과 다른 기계 가공과 융합하는 연구도 활발히 진행되고 있다. Cao et al.35은 전해방전가공과 미세 연삭을 결합하여 전해방전가공에 비해 가공 시간을 단축하고 높은 표면 품질를 구현하였다. 스파크 열에너지가 유리 표면을 유화시켜 쉽게 가공되는 특징을 이용하였다. 위 논문에서는 전해방전가공과 연삭의 복합 가공을 이용하여 크랙 없이 유리 가공이 가능함을 실험적으로 확인하였다. Razfar et al.36은 전극에 진동을 가해 가공 효율이 높아지는 효과를 발표하였다. 원기둥 형태의 전극에 진동을 가해 재료 제거율과 가공 깊이가 증가함을 보였다. 하지만 고주파수(400 Hz 이상)의 진동을 가할 경우 수소 기체 절연막이 파괴되어 전해방전 효과가 감소하면서 가공 효율이 악화된다. 전해방전가공 공정을 선반 가공에 적용한 연구도 있다.
Furutani et al.37은 선반 형태의 전해방전가공 장치를 가속도 센서에 필요한 봉 형태의 PZT 가공에 활용하였다. 회전하는 PZT 봉에 전극을 일정 압력으로 접촉시키면서 가공했으며, 그 결과 Fig. 11과 같이 직경 3 mm 이내의 미세 홈을 가공할 수 있었다.
이 외에도 가공 깊이 한계를 극복하기 위해서 와이어를 전극으로 활용하는 연구가 진행되고 있다. Jain et al.38은 이송 와이어(Traveling Wire, TW) 방식을 전해방전가공에 적용하여 재료 제거율 및 오버컷 등의 가공 효율을 실험적으로 비교하였다. Bhuyan et al.39은 전해방전가공 중 와이어의 움직임이 스파크 열 에너지를 감소시켜 와이어의 끊어짐을 억제하는데 효과가 있음을 실험적으로 확인했다. Peng et al.40은 TW-ECDM을 유리 절단 공정에 적용하는 연구를 발표했다. Kuo et al.41은 KOH 전해액이 물방울 형태로 천천히 떨어지고 있는 상태(Titrated Flow)에서 WECDM (Wire Electrochemical Discharge Machining)을 통해 석영을 가공하는 방법에 대한 연구를 진행하였다. 전극과 와이어가 한 방울 안에 있을 때, 방울 속에서는 소용돌이가 형성되어 칩과 전해질의 Resultants를 제거하게 된다. 전해액은 지속적으로 흐르기 때문에 전해액 방울의 농도는 언제나 일정하고, 가스막으로 인한 절연 효과 또한 보장될 수 있다. 가공 과정에서 기존보다 더 적은 양의 전해액이 소모되고, 비용절감 또한 가능하였다. 최근 와이어 전극을 이용한 방해방전가공 공정의 가공 효율을 높이기 위해서 연삭 공정과 결합하는 연구도 활발히 진행되고 있다. Yang et al.42은 SiC를 혼합한 전해액을 이용하여 와이어 전해방전 공정을 구현했으며, 실험결과 전해방전의 열에 의해 국부적으로 용융된 표면을 연삭으로 제거함으로써 미세 크랙을 줄이고 표면거칠기를 개선하는 효과가 있음을 확인했다.
5. 전기화학적 복합가공
5.1 전기화학적 산화 보조 가공(Electrochemical Oxidation Assisted Machining)
전기화학적 산화 보조 가공은 글래시카본(Glassy Carbon, GC)과 같은 고경도 전도성 소재의 미세가공을 위해 제안되었다. 전기화학적 산화반응을 이용해 가공물의 표면을 유화시킴과 동시에 기계적인 가공을 인가하는 복합 가공 공정이다. Fig. 12는 전기화학적 산화 응용 가공 메커니즘이다. 재료에 전압을 인가하기 되면 표면에 산화막이 생성된다. 공구에 의한 기계 가공이 시작되면 산화막이 제거되면서 새로운 재료 표면이 전해질에 노출되게 된다. 노출된 재료는 인가 전압에 의해 다시 산화반응을 일으키게 되며, 산화-제거-재산화의 반복 공정으로 가공이 진행된다. 이러한 전기화학적 산화 및 기계적 재료 제거의 반복 메커니즘은 Jang et al.43에 의해 자기유변유체 연마 공정에 적용하여 글래시카본 금형 표면 연마에 활용되었다. Lee et al.44은 복합 가공 메커니즘을 3축 밀링 가공시스템에 적용하여 글래시카본 미세 가공 연구를 수행하였다.
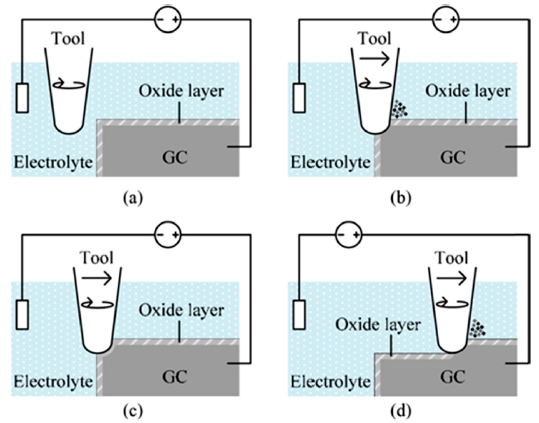
Electrochemical oxidation assisted micromachining processes: (a) formation of oxide layer before machining, (b) removal of GC substrate with its oxide layer, (c) regeneration of oxide layer and (d) machining of GC workpiece by the repetition of the (b) and (c)44 (Adapted from Ref. 44 with permission)
전기화학적 산화 보조 가공 장치는 전기화학적 산화 반응을 인가하기 위해 수조 형태의 가공물 고정 방식을 고안하였다. Fig. 13과 같이 X-Y 스테이지 위에 수조를 설치하고, 시편 표면만 전해질에 노출될 수 있게 하였다. 전압 인가 및 가공 중 전류 측정은 일정전위기(Potentiostat)를 이용하였으며, 정확한 전압 인가 및 전류 측정을 위해 3전극 방식을 사용하였다. 공구의 부식을 방지하기 위해 세라믹 소재인 지르코니아(ZrO2)를 공구 형태로 제작하여 가공에 사용하였다.
전기화학적 산화 보조 가공의 복합 가공 메커니즘은 두 가지 공정에 적용되었다. 먼저 Jang et al.43은 자기유변유체 연마 공정 제안한 복합 가공 메커니즘을 융합하여 나노미터급 표면거칠기를 갖는 글래시카본 미세 구조를 제작하였다. 글래시카본의 높은 취성으로 인해 기계가공 후 크랙이 발생하기 때문에 연마 공정이 반드시 필요하다. 저자는 자기유변유체 연마 공정의 낮은 연삭력으로 고경도 글래시카본을 연마하기 위해 전기화학적 산화반응을 융합하였고, 그 결과 Ra 11 nm 수준의 표면거칠기를 갖는 구조물을 제작할 수 있었다.
Jang et al.45은 전기화학적 산화와 기계적 마모의 복합 가공 메커니즘을 실험적으로 분석하였다. 제안한 전기화학 산화 응용 연마 공정을 모사하기 위해 Tibocorrosion Test 장비 종류 중 Block-on-Ring 시스템을 설계하였다. 지르코니아 링(Zriconia Ring)의 회전에 의해GC 산화막이 제거됨에 따라 측정되는 전류 및 임피던스(Impedance)를 분석하여 공정 메커니즘을 Fig. 14와 같이 설명하였다. 또한, 위 연구에서 인가 전압과 수직 하중을 조절함으로써 재료 제거량을 비교하였다.

Electrochemical impedance spectra before and during tribocorrosional experiment: (a) measured data shown in Nyquist diagrams; (b) equivalent circuit model and sketches of the oxidized surfaces with and without wear45 (Adapted from Ref. 45 with permission)
Lee et al.44은 전기화학적 산화 반응을 3축 밀링 공정에 적용하여 후처리 없이 나노미터급 표면거칠기를 갖는 3차원 구조물 제작이 가능한 공정을 제안하였다. 3축 밀링 공정에 전기화학 산화 반응을 응용하여 글래시카본 미세 가공에 적용하였다. 실험을 통해 제안한 공정의 적정 인가 전압과 수직 하중을 도출하였으며, 적정 가공 조건을 이용하여 나노미터급 표면거칠기를 갖는 미세홈을 가공할 수 있었다(Fig. 15).
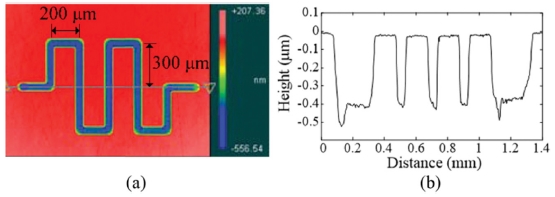
Line pattern machining result: (a) white light interferometer image and (b) depth profile45 (Adapted from Ref. 45 with permission)
Nam et al.46은 산화응용가공에 의해 취성 재료의 Critical Chip Thickness가 달라짐을 실험적으로 확인하였다. 3축 밀링 공정에 산화반응을 응용한 공정에서 크랙 발생이 감소하는 효과에 대해 분석하기 위해 일반적인 취성 재료 가공 연구에서 다루는 Critical Chip Thickness 분석을 진행하였다. Critical Chip Thickness는 취성 재료의 기계적 가공 시 크랙이 발생하지 않는 공구의 최대 절입량을 의미하는 것으로 재료의 물성 및 공정 변수의 영향을 받는다. 저자는 GC의 Critical Chip Thickness를 이론적으로 계산하였고, 전기화학 산화 반응의 적용에 따라 Critical Chip Thickness가 증가함을 실험적으로 확인하였다. 그 결과, 전기화학적 산화를 통해 Cirtical Chip Thickness가 약 3배 증가함을 확인했다. 또한, Critical Chip Thickness 분석을 바탕으로 GC의 전기화학적 산화응용 가공에서 크랙이 생기지 않는 적정 절입량과 이송 속도를 선정하기 위한 관계그래프를 도출하였다(Fig. 16).
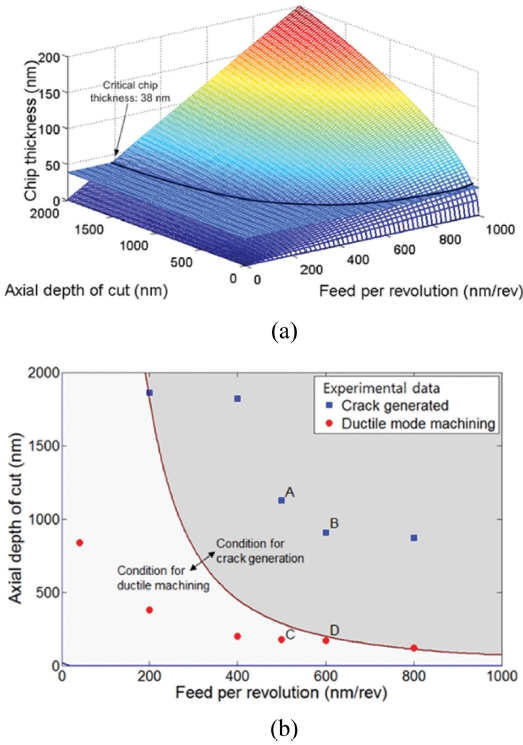
Two plots of chip thickness value; (a) 3D surface plot of the chip thickness values using Eq. 2, (b) experimental result of the effect of oxidation on the chip thickness (b) plot for occurring ductile mode micromachining below the critical chip thickness plane on the surface46 (Adapted from Ref. 46 with permission)
Nam et al.47은 전기화학 산화 속도에 따른 재료 제거량 변화를 실험적으로 확인했다. 전기화학적 산화 속도를 높이기 위해서 위 연구에서는 전해액의 수소이온농도(pH)를 달리하였다. 재료의 전기화학적 거동을 분석하는 방법 중 하나인 분극 실험을 이용하여 전해질의 수소이온농도에 따라 GC 산화를 위한 인가 전압 조건이 달라짐을 확인하였다. 이 분석을 통해 산성 전해액에서 고전압 환경에서도 산화막이 생성됨을 알 수 있었고, 그 실험 조건에서 가공시스템의 임피던스가 작아짐을 확인했다. 이로 인해 산화막 생성이 빨라졌을 것으로 예상하고 재료 제거량이 산성 전해액에서 증가함을 실험적으로 확인하였다.
6. 결론
전기화학적 반응을 이용한 최신 미세 가공 기술에 대해 살펴보았다. 전기화학가공은 금속의 양극 용출을 이용한 전해 가공과 전기화학적 스파크를 이용하여 비전도성 재료를 가공할 수 있는 전해방전가공, 전기화학반응과 기존 가공 기술을 접목한 복합 가공으로 나눌 수 있다.
전기화학적 가공은 다른 가공 기술보다 가공환경에 민감하여 전해액의 농도, 온도, 이온의 순환 등에 영향을 많이 받는다. 가공물 재료에 따라 전해액의 종류도 달리 선정해야 하며 보통 전해액은 부식을 유발하기 때문에 전해액 후처리에도 신경을 써야 한다. 또한 인가 전압, 전류도 가공에 큰 영향을 끼치기 때문에 적절한 가공 조건 선정이 중요하다.
하지만 전기화학적 가공은 다른 가공법에 비해 가공물 경도와 상관없이 가공이 가능하며 공구가 직접 가공물에 닿지 않아 공구마모에 대한 우려가 적다. 원자단위로 금속이 제거되기 때문에 마이크로미터에서 서브 마이크로 미터 크기의 형상까지도 가공 가능하다. 기계적, 열적 잔류응력이 발생하지 않으며 동시에 대면적 가공이 가능하여 대량생산에 적용할 수 있다. 전해방전가공의 경우 기존 가공법으로 어려운 유리의 미세 형상 가공도 가능하다.
전기화학적 가공법은 유럽, 일본뿐만 아니라 중국에서 매우 많은 연구가 되고 있으며 실제 생산에 적용하기 위한 가공 공정에 대한 연구가 주류를 이루고 있다. 전기화학적 반응의 복잡성으로 인해 현상의 명확한 규명이 매우 어렵지만 앞서 설명했듯이 다른 가공 기술에는 없는 장점이 많아 보다 많은 연구가 필요하다.
Acknowledgments
“이 논문은 2015년도 정부(교육부)의 재원으로 한국연구재단의 지원을 받아 수행된 기초연구사업임(NRF-2015R1D1A1A01060646).”
REFERENCES
-
Chen, C., Li, J., Zhan, S., Yu, Z., and Xu, W., “Study of Micro Groove Machining by Micro ECM,” Procedia CIRP, Vol. 42, No. pp. 418-422, 2016.
[https://doi.org/10.1016/j.procir.2016.02.224]
-
Zeng, Z., Wang, Y., Wang, Z., Shan, D., and He, X., “A Study of Micro-EDM and Micro-ECM Combined Milling for 3D Metallic Micro-Structures,” Precision Engineering, Vol. 36, No. 3, pp. 500-509, 2012.
[https://doi.org/10.1016/j.precisioneng.2012.01.005]
-
Ghoshal, B. and Bhattacharyya, B., “Investigation on Profile of Microchannel Generated by Electrochemical Micromachining,” Journal of Materials Processing Technology, Vol. 222, pp. 410-421, 2015.
[https://doi.org/10.1016/j.jmatprotec.2015.03.025]
-
Zeng, Y.-B., Yu, Q., Wang, S.-H., and Zhu, D., “Enhancement of Mass Transport in Micro Wire Electrochemical Machining,” CIRP Annals-Manufacturing Technology, Vol. 61, No. 1, pp. 195-198, 2012.
[https://doi.org/10.1016/j.cirp.2012.03.082]
-
Fang, X., Zou, X. H., Chen, M., and Zhu, D., “Study on Wire Electrochemical Machining Assisted with Large-Amplitude Vibrations of Ribbed Wire Electrodes,” CIRP Annals, Vol. 66, No. 1, pp. 205-208, 2017.
[https://doi.org/10.1016/j.cirp.2017.04.135]
-
Xiaolong, F., Peng, L., Yongbin, Z., and Di, Z., “Research on Multiple Wires Electrochemical Micromachining with Ultra-Short Voltage Pulses,” Procedia CIRP, Vol. 42, pp. 423-427, 2016.
[https://doi.org/10.1016/j.procir.2016.02.225]
-
Koyano, T., Hosokawa, A., Igusa, R., and Ueda, T., “Electrochemical Machining Using Porous Electrodes Fabricated by Powder Bed Fusion Additive Manufacturing Process,” CIRP Annals, Vol. 66, No. 1, pp. 213-216, 2017.
[https://doi.org/10.1016/j.cirp.2017.04.127]
-
Koyano, T. and Kunieda, M., “Micro Electrochemical Machining Using Electrostatic Induction Feeding Method,” CIRP Annals-Manufacturing Technology, Vol. 62, No. 1, pp. 175-178, 2013.
[https://doi.org/10.1016/j.cirp.2013.03.107]
-
Zhu, D., Wang, W., Fang, X., Qu, N., and Xu, Z., “Electrochemical Drilling of Multiple Holes with Electrolyte-Extraction,” CIRP Annals-Manufacturing Technology, Vol. 59, No. 1, pp. 239-242, 2010.
[https://doi.org/10.1016/j.cirp.2010.03.135]
-
Zhu, D., Zeng, Y. B., Xu, Z., and Zhang, X., “Precision Machining of Small Holes by the Hybrid Process of Electrochemical Removal and Grinding,” CIRP Annals-Manufacturing Technology, Vol. 60, No. 1, pp. 247-250, 2011.
[https://doi.org/10.1016/j.cirp.2011.03.130]
-
Fan, Z.-W., Hourng, L.-W., and Wang, C.-Y., “Fabrication of Tungsten Microelectrodes Using Pulsed Electrochemical Machining,” Precision Engineering, Vol. 34, No. 3, pp. 489-496, 2010.
[https://doi.org/10.1016/j.precisioneng.2010.01.001]
-
Han, W. and Kunieda, M., “Fabrication of Tungsten Micro-Rods by ECM Using Ultra-Short-Pulse Bipolar Current,” CIRP Annals, Vol. 66, No. 1, pp. 193-196, 2017.
[https://doi.org/10.1016/j.cirp.2017.04.131]
-
Wang, J. and Sheu, D. Y., “Developing a Process Chain with WEDG Technology and Pulse ECM to Fabricate Ultra Micro Pins,” Procedia CIRP, Vol. 42, pp. 815-818, 2016.
[https://doi.org/10.1016/j.procir.2016.02.325]
-
Jain, V. K., Kalia, S., and Sidpara, A. M., “Some Aspects of Fabrication of Micro Devices by Electrochemical Micromachining (ECMM) and Its Finishing by Magnetorheological Fluid,” The International Journal of Advanced Manufacturing Technology, Vol. 59, Nos. 9-12, pp. 987-996, 2012.
[https://doi.org/10.1007/s00170-011-3563-4]
-
Lei, Y., Zhao, Z., Guo, J., Li, J., and Niu, H., “Disordered Wall Arrays by Photo-Assisted Electrochemical Etching in N-Type Silicon,” Journal of Semiconductors, Vol. 37, No. 10, Paper No. 106001, 2016.
[https://doi.org/10.1088/1674-4926/37/10/106001]
-
Kikuchi, T., Wachi, Y., Sakairi, M., and Suzuki, R. O., “Aluminum Bulk Micromachining through an Anodic Oxide Mask by Electrochemical Etching in an Acetic Acid/Perchloric Acid Solution,” Microelectronic Engineering, Vol. 111, pp. 14-20, 2013.
[https://doi.org/10.1016/j.mee.2013.05.007]
-
Shin, H., Park, M., and Chu, C., “Electrochemical Etching Using Laser Masking for Multilayered Structures on Stainless Steel,” CIRP Annals, Vol. 59, No. 1, pp. 585-588, 2010.
[https://doi.org/10.1016/j.cirp.2010.03.134]
-
Huang, Z. P., Geyer, N., Liu, L. F., Li, M. Y., and Zhong, P., “Metal-Assisted Electrochemical Etching of Silicon,” Nanotechnology, Vol. 21, No. 46, Paper No. 465301, 2010.
[https://doi.org/10.1088/0957-4484/21/46/465301]
-
Long, Y., Shi, T., and Xiong, L., “Excimer Laser Electrochemical Etching N-Si in the KOH Solution,” Optics and Lasers in Engineering, Vol. 48, No. 5, pp. 570-574, 2010.
[https://doi.org/10.1016/j.optlaseng.2009.12.001]
-
Al-Heuseen, K., Hashim, M. R., and Ali, N. K., “Enhanced Optical Properties of Porous Gan by Using Uv-Assisted Electrochemical Etching,” Physica B: Condensed Matter, Vol. 405, No. 15, pp. 3176-3179, 2010.
[https://doi.org/10.1016/j.physb.2010.04.043]
-
Lv, H., Shen, H., Jiang, Y., Gao, C., Zhao, H., and Yuan, J., “Porous-Pyramids Structured Silicon Surface with Low Reflectance Over a Broad Band by Electrochemical Etching,” Applied Surface Science, Vol. 258, No. 14, pp. 5451-5454, 2012.
[https://doi.org/10.1016/j.apsusc.2012.02.033]
-
Rojas, E. G., Terheiden, B., Plagwitz, H., Hensen, J., Baur, C., et al., “Formation of Mesoporous Germanium Double Layers by Electrochemical Etching for Layer Transfer Processes,” Electrochemistry Communications, Vol. 12, No. 2, pp. 231-233, 2010.
[https://doi.org/10.1016/j.elecom.2009.11.033]
-
El-Haddad, R. and Wüthrich, R., “A Mechanistic Model of the Gas Film Dynamics During the Electrochemical Discharge Phenomenon,” Journal of Applied Electrochemistry, Vol. 40, No. 10, pp. 1853-1858, 2010.
[https://doi.org/10.1007/s10800-010-0141-7]
-
Han, M.-S., Min, B.-K., and Lee, S. J., “Modeling Gas Film Formation in Electrochemical Discharge Machining Processes Using a Side-Insulated Electrode,” Journal of Micromechanics and Microengineering, Vol. 18, No. 4, Paper No. 045019, 2008.
[https://doi.org/10.1088/0960-1317/18/4/045019]
-
Wüthrich, R. and Fascio, V., “Machining of Non-Conducting Materials Using Electrochemical Discharge Phenomenon—An Overview,” International Journal of Machine Tools and Manufacture, Vol. 45, No. 9, pp. 1095-1108, 2005.
[https://doi.org/10.1016/j.ijmachtools.2004.11.011]
-
Nguyen, K.-H., Lee, P. A., and Kim, B. H., “Experimental Investigation of ECDM for Fabricating Micro Structures of Quartz,” Int. J. Precis. Eng. Manuf., Vol. 16, No. 1, pp. 5-12, 2015.
[https://doi.org/10.1007/s12541-015-0001-9]
-
Yang, C.-K., Wu, K.-L., Hung, J.-C., Lee, S.-M., Lin, J.-C., and Yan, B.-H., “Enhancement of ECDM Efficiency and Accuracy by Spherical Tool Electrode,” International Journal of Machine Tools and Manufacture, Vol. 51, No. 6, pp. 528-535, 2011.
[https://doi.org/10.1016/j.ijmachtools.2011.03.001]
-
Tang, W., Kang, X., and Zhao, W., “Enhancement of Electrochemical Discharge Machining Accuracy and Surface Integrity Using Side-Insulated Tool Electrode with Diamond Coating,” Journal of Micromechanics and Microengineering, Vol. 27, No. 6, Paper No. 065013, 2017.
[https://doi.org/10.1088/1361-6439/aa6e94]
-
Han, M.-S., Min, B.-K., and Lee, S. J., “Micro-Electrochemical Discharge Cutting of Glass Using a Surface-Textured Tool,” CIRP Journal of Manufacturing Science and Technology, Vol. 4, No. 4, pp. 362-369, 2011.
[https://doi.org/10.1016/j.cirpj.2011.06.007]
-
Han, M.-S., Chae, K. W., and Min, B.-K., “Fabrication of High-Aspect-Ratio Microgrooves Using an Electrochemical Discharge Micromilling Process,” Journal of Micromechanics and Microengineering, Vol. 27, No. 5, Paper No. 055004, 2017.
[https://doi.org/10.1088/1361-6439/aa64b9]
-
Jiang, B., Lan, S., Wilt, K., and Ni, J., “Modeling and Experimental Investigation of Gas Film in Micro-Electrochemical Discharge Machining Process,” International Journal of Machine Tools and Manufacture, Vol. 90, pp. 8-15, 2015.
[https://doi.org/10.1016/j.ijmachtools.2014.11.006]
-
Sabahi, N., Razfar, M. R., and Hajian, M., “Experimental Investigation of Surfactant-Mixed Electrolyte into Electrochemical Discharge Machining (ECDM) Process,” Journal of Materials Processing Technology, Vol. 250, pp. 190-202, 2017.
[https://doi.org/10.1016/j.jmatprotec.2017.07.017]
-
Laio, Y. S., Wu, L., and Peng, W., “A Study to Improve Drilling Quality of Electrochemical Discharge Machining (ECDM) Process,” Procedia CIRP, Vol. 6, pp. 609-614, 2013.
[https://doi.org/10.1016/j.procir.2013.03.105]
-
Hajian, M., Razfar, M. R., and Movahed, S., “An Experimental Study on the Effect of Magnetic Field Orientations and Electrolyte Concentrations on ECDM Milling Performance of Glass,” Precision Engineering, Vol. 45, pp. 322-331, 2016.
[https://doi.org/10.1016/j.precisioneng.2016.03.009]
-
Cao, X. D., Kim, B. H., and Chu, C. N., “Hybrid Micromachining of Glass Using ECDM and Micro Grinding,” Int. J. Precis. Eng. Manuf., Vol. 14, No. 1, pp. 5-10, 2013.
[https://doi.org/10.1007/s12541-013-0001-6]
-
Razfar, M. R., Behroozfar, A., and Ni, J., “Study of the Effects of Tool Longitudinal Oscillation on the Machining Speed of Electrochemical Discharge Drilling of Glass,” Precision Engineering, Vol. 38, No. 4, pp. 885-892, 2014.
[https://doi.org/10.1016/j.precisioneng.2014.05.004]
-
Furutani, K. and Kojima, S., “Prototyping of Acceleration Sensor by Using Lathe-Type Electro-Chemical Discharge Machine,” Procedia CIRP, Vol. 42, pp. 772-777, 2016.
[https://doi.org/10.1016/j.procir.2016.02.317]
-
Jain, V. K., Rao, P. S., Choudhary, S., and Rajurkar, K., “Experimental Investigations into Traveling Wire Electrochemical Spark Machining (TW-ECSM) of Composites,” Journal of Engineering for Industry, Vol. 113, No. 1, pp. 75-84, 1991.
[https://doi.org/10.1115/1.2899625]
-
Bhuyan, B. K. and Yadava, V., “Experimental Study of Traveling Wire Electrochemical Spark Machining of Borosilicate Glass,” Materials and Manufacturing Processes, Vol. 29, No. 3, pp. 298-304, 2014.
[https://doi.org/10.1080/10426914.2013.852216]
-
Peng, W. Y. and Liao, Y. S., “Study of Electrochemical Discharge Machining Technology for Slicing Non-Conductive Brittle Materials,” Journal of Materials Processing Technology, Vol. 149, No. 1-3, pp. 363-369, 2004.
[https://doi.org/10.1016/j.jmatprotec.2003.11.054]
-
Kuo, K.-Y., Wu, K.-L., Yang, C.-K., and Yan, B.-H., “Wire Electrochemical Discharge Machining (WECDM) of Quartz Glass with Titrated Electrolyte Flow,” International Journal of Machine Tools and Manufacture, Vol. 72, pp. 50-57, 2013.
[https://doi.org/10.1016/j.ijmachtools.2013.06.003]
-
Yang, C. T., Song, S. L., Yan, B. H., and Huang, F. Y., “Improving Machining Performance of Wire Electrochemical Discharge Machining by Adding SiC Abrasive to Electrolyte,” International Journal of Machine Tools and Manufacture, Vol. 46, No. 15, pp. 2044-2050, 2006.
[https://doi.org/10.1016/j.ijmachtools.2006.01.006]
-
Jang, K.-I., Seok, J., Min, B.-K., and Lee, S. J., “An Electrochemomechanical Polishing Process Using Magnetorheological Fluid,” International Journal of Machine Tools and Manufacture, Vol. 50, No. 10, pp. 869-881, 2010.
[https://doi.org/10.1016/j.ijmachtools.2010.06.004]
-
Lee, W., Nam, E., Lee, C.-Y., Jang, K.-I., and Min, B.-K., “Electrochemical Oxidation Assisted Micromachining of Glassy Carbon Substrate,” Int. J. Precis. Eng. Manuf., Vol. 16, No. 3, pp. 419-422, 2015.
[https://doi.org/10.1007/s12541-015-0057-6]
-
Jang, K.-I., Nam, E., Lee, C.-Y., Seok, J., and Min, B.-K., “Mechanism of Synergetic Material Removal by Electrochemomechanical Magnetorheological Polishing,” International Journal of Machine Tools and Manufacture, Vol. 70, pp. 88-92, 2013.
[https://doi.org/10.1016/j.ijmachtools.2013.03.011]
-
Nam, E., Lee, C.-Y., Jun, M. B., and Min, B.-K., “Ductile Mode Electrochemical Oxidation Assisted Micromachining for Glassy Carbon,” Journal of Micromechanics and Microengineering, Vol. 25, No. 4, Paper No. 045021, 2015.
[https://doi.org/10.1088/0960-1317/25/4/045021]
-
Nam, E., Lee, C.-Y., Min, J., Lee, S. J., and Min, B.-K., “Effect of Electrochemical Conditions on Material Removal Rate in Electrochemical Oxidation Assisted Machining,” Journal of the Electrochemical Society, Vol. 164, No. 2, pp. E23-E28, 2017.
[https://doi.org/10.1149/2.0061704jes]