
기계 가공공정 모니터링 기술의 현황
Copyright © The Korean Society for Precision Engineering
This is an Open-Access article distributed under the terms of the Creative Commons Attribution Non-Commercial License (http://creativecommons.org/licenses/by-nc/3.0) which permits unrestricted non-commercial use, distribution, and reproduction in any medium, provided the original work is properly cited.
Abstract
Monitoring technology of machining operations has a long history since unmanned machining was introduced. Lots of research papers were presented and some of them has been commercialized and applied to shop floor. Despite the long history, many researchers have presented new approaches continuously in this area. This paper presents current state of monitoring technology of machining operations. The objectives of monitoring are shortly summarized, and the monitoring methods and the unique sensor technologies are reviewed. The main objective of the monitoring technology remains same; tool condition monitoring (TCM). The general approaches also remain similar; signal processing and decision making. But, the innovative methods for every step of process monitoring are being provided to improve the performance. More powerful computing is lowering the wall of much more data from more sensors by fast calculation. This technology also introduces the novel decision making strategies such as Artificial Intelligent. New materials and new communication technologies are breaking the limitation of sensor positions. Virtual machining technology which estimates the machining physics is being integrated with monitoring technology.
Keywords:
Machining, Monitoring, Sensor키워드:
기계 가공, 모니터링, 센서1. 서론
기계 가공공정 모니터링 기술은 인류가 기계를 이용하여 원하는 물건을 만들기 시작했을 때부터 많은 관심을 받아온 분야이다. 인류가 칼 등의 공구를 이용하여 직접 물건을 제작할 경우 제작자들은 그들의 눈과 귀, 촉각 및 근육으로 전달되는 저항 등을 느끼면서 사용하고 있는 도구 및 만들고 있는 물건의 상태를 모니터링 하였다. 그러나, 인류의 근육이 모터 등으로 대체되고 모터의 힘이 인류의 안전을 위협하게 됨에 따라 제작이 이루어지는 곳, 즉 공구와 제품이 맞닿는 곳에서 무슨 일이 벌어지는지 더 이상은 인류의 눈과 귀, 혹은 촉각 등으로 느낄 수 없게 되었다. 공구와 소재가 맞닿은 곳에서 벌어지는 현상에 의해서 제작되는 물건의 품질이 결정되기 때문에, 이러한 현상을 이해하기 위한 많은 노력들이 과거로부터 진행되어 왔다. 이에 따라, 기계 가공공정을 통해 발생하는 다양한 물리적 현상을 센서를 이용하여 모니터링하는 분야는 기계 가공공정의 중요한 연구분야의 하나로 자리 잡게 되었다.
기계 가공공정 모니터링 분야에 대한 많은 연구들이 오래전부터 소개되었으며 훌륭한 연구자들에 의해서 일정 기간의 연구들은 리뷰페이퍼 형태로 정리되거나 책으로 출판되어 이 분야의 연구자들에게 많은 도움을 주고 있다.1-3 그럼에도 불구하고 기계 가공공정 모니터링 분야의 논문들은 계속해서 출판되고 있고 이를 토대로 계속해서 발전해 나갈 것으로 예상된다. 특히, 최근 국내외에서 회자되고 있는 제4차 산업혁명의 중요한 토대 중 하나가 모니터링 기술이라는 점에 있어서 기계 가공공정 모니터링 분야에 대한 현장의 요구는 지속적으로 확대될 것으로 기대된다.
본 논문은 기계 가공공정 중에 공구와 소재가 맞닿는 곳에서 발생하는 물리적인 현상들을 센서를 이용하여 모니터링 하는 최근의 연구들을 국내 연구자들에게 소개하는 것을 목적으로 작성되었다. 공구와 소재의 위치 결정을 위해서도 센서가 사용되나 본 논문에서는 제외하였으며, 물리적 현상을 검출한 이후의 공정제어부분 및 상위 시스템 연계분야도 제외하였음을 미리 밝힌다. 본 논문을 작성하기 위해 2012년 이후 출판된 기계 가공공정 모니터링분야의 논문들 중 피인용이 높은 논문들 130여 편을 1차로 선별하였다. 이러한 논문들을 목적, 즉 해결하고자 하는 문제(2장) 및 해결 방법(3장)으로 나누어 소개하고 있으며, 센서 들의 사용에 관해 독특한 점들이 있는 논문들을 4장에 소개하였다. 목적-방법-센서적용이 서로 완전히 나누어질 수 없어 중복될 소지가 있으나 각 장에서 언급한 내용은 다른 장에서 중복되지 않고 하나라도 많은 논문을 소개하기 위해 노력했다. 결론부에서는 기계 가공공정 모니터링분야의 최근 동향을 저자들의 의견을 중심으로 정리해 보았으며, 근래 자주 소개되고 있는 가상가공 기반의 모니터링 기술에 대해 간단히 소개하였다.
본 논문을 준비하면서 우선적으로 고려한 최근 논문들의 저작권확보가 어려워 많은 그림을 싣지 못하는 점에 대해 독자들의 이해를 구하고자 한다.
2. 기계 가공공정 모니터링의 목적
기계 가공 중에 발생할 수 있는 문제는 다양하다. 이러한 문제들은 가공에 관련된 장비들에 대한 관점과, 가공공정의 성능, 즉 효율에 대한 관점, 가공의 결과로 얻게 되는 제품의 관점에서 살펴볼 수 있다. 장비와 관련된 문제 발생을 최소화 하고, 가공공정은 안정적이면서 높은 효율을 갖는 상태로 관리하면서, 가공된 제품의 품질을 최상으로 유지하기 위해서 문제가 될 만한 사건의 발생을 즉시 감지하거나 발생 전에 미리 예측하는 것이 모니터링의 목적이며 최종적으로 적기에 필요한 조치를 취할 수 있도록 제어하는 것까지 포함하기도 한다.4,5
기계 가공공정 모니터링이라는 주제로 본 리뷰 논문을 준비하면서 전 세계 논문의 인용정보를 제공하는 대표적인 색인 데이터베이스인 SCOPUS에서 해당 주제로 검색하여 찾아진 논문들 중 피인용 횟수가 많은 순으로 정렬하여 상위그룹을 본 논문의 참고문헌들로 선정하였다. 본 논문의 작성시점인 2017년 말을 기준으로 직전 5년의 논문들을 대상으로 하였으며, 가장 최근 논문들의 피인용이 상대적으로 낮은 점을 보완하기 위하여 연차 별 보정을 수행하였다.
Fig. 1은 참고문헌의 저자들이 모니터링 연구를 수행하면서 관심을 갖고 접근한 분야를 조사해본 결과를 보여주고 있다. 과거에 발간된 다른 리뷰논문들과 유사하게 공구마모나 파손 등과 같은 공구 상태를 모니터링하기 위한 연구가 가장 많은 것으로 나타났다. 채터 감지를 위한 연구가 그 뒤를 이었고, 공정 상태나 절삭 메커니즘 파악을 위한 연구와 가공 장비 상태 감지를 위한 연구가 그 다음으로 조사되었다.
공구는 가공공정의 효율과 가공된 제품의 품질에 직접적으로 큰 영향을 미치는 요소이다. 절삭공정의 모니터링과 관련된 많은 수의 연구들이 공구의 마모 상태를 실시간으로 감지하거나, 선행실험을 통해 학습된 데이터를 바탕으로 공구마모 시점을 예측하는 것에 초점을 맞추고 있다. 공구의 마모나 파손을 감지하거나 발생 시점을 예측할 수 있게 되면, 작업자는 단편적인 조치로서는 적절한 시점에 공구를 교체하여 공정의 문제 발생과 제품의 품질 저하를 방지할 수 있다. 한걸음 더 나아가서는 공구의 마모 발생을 최소화하는 공정 조건을 찾아 보다 효율적인 공정 운영을 할 수 있다.
절삭공정 중에 발생하는 채터는 시스템의 안정성을 떨어뜨리고, 제품의 품질에 문제를 야기하는 위험한 현상이다. 공구의 마모 분야와 더불어 많은 연구자들이 절삭공정 중의 채터 발생을 감지하기 위하여 다양한 연구를 진행해 오고 있다.
또 다른 주요한 모니터링 관심 분야는 공정 메커니즘 파악이나 장비 상태에 대한 감지와 함께 표면 상태의 감지 및 표면 품질의 예측이다. 표면 상태의 감지 및 예측은 단일 주제로서 모니터링 연구의 대상이 되기도 하지만, 공구의 마모나 채터의 발생 등과 함께 연관 지어져 통합적인 시스템으로의 연구가 이루어지기도 한다.
기타 모니터링의 관심 분야들로는 가공공정 중의 소재의 변형상태를 파악하여 능동적으로 대처하기 위한 연구가 있으며,6 센서를 탑재한 지능형 장치 개발도 확인된다. 그리고, 최근의 컴퓨팅 기술의 발달에 힘입어 클라우드나 인공지능, 데이터 마이닝, 가상가공 기반의 모니터링 시스템 구축에 대한 연구 사례들이 있다.7-12
3. 기계 가공공정 모니터링의 방법
모니터링 행위는 데이터를 취득하고 적절히 처리하여 필요한 정보를 얻어내는 과정이다. Fig. 2는 데이터 흐름의 관점에서 모니터링 시스템을 살펴본 것이다. 데이터를 취득하기 위해서는 목적에 맞는 센서가 선정되어야 하고, 선정된 센서를 통해 취득한 신호는 노이즈를 제거하고 분석하는 과정을 거쳐서 공정의 상태를 정의할 수 있는 정보로 변화하게 된다. 이어지는 내용에서는 2장에서 언급한 주요 모니터링 목적에 대한 각각의 사례를 소개한다.
3.1 공구마모 감지
공구마모를 확인하는 방법은 현미경 등의 이미지 장치를 통해 육안으로 관찰하는 것이 가장 직관적이나, 이러한 이미지 장치를 공작기계 안에서 활용하기 위해서는 비산되는 절삭유와 칩 등의 작업환경과 공정 중단에 따른 생산성 저하도 고려해야 하기 때문에 현장에서 효율적으로 사용하는데 한계가 따르게 된다.
이런 이유로 공구의 마모 상태를 감지하기 위한 대부분의 모니터링 시스템은 힘 센서 기반으로 가공 부하 변화를 관찰하거나 가속도 센서 기반으로 시스템 진동의 변화를 관찰하는 형태의 간접적인 접근이 주로 이루어진다. 필요에 따라 센서의 종류나 개수의 적용은 달라지지만, 기본적으로 센서를 이용하여 수집된 데이터를 기초로 하여 노이즈 신호를 걸러내고, 다양한 분석 기법을 이용하여 목적에 맞게 신호를 패턴화하고 마모 상태를 분류하는 기준의 정확성을 높여서 활용성을 갖추도록 하는 연구 과정은 유사하다. 공정의 특성에 맞는 센서의 선정과 취득된 신호의 변별력을 높이기 위한 신호 처리 기술의 조합은 매우 다양하게 나타난다.
Wang et al.13은 ν-SVM (Support Vector Machine)을 사용하여 밀링공정의 공구 상태 모니터링을 구현하였다. 공구마모 상태의 다중 카테고리 분류를 실현하기 위해 진동 신호를 수집하고 WPD (Wavelet Packet Decomposition)를 기반으로 특성 벡터를 추출하는 공구 상태 모니터링 프레임 워크를 구성하였다. 제안된 방법의 효과를 증명하기 위해 티타늄 합금의 밀링 실험을 수행하였다. 결과는 NN (Nearest Neighbor) 기반 ν-SVM과 LPP (Locality Preserving Projection)의 조합이 교육 정확도를 저하시키지 않으면서 학습 샘플의 빠른 학습을 실현할 수 있음을 보여주었다. 저자들은 다른 논문을 통해 밀링공정에서 절삭력 신호를 수집하고 공구마모 상태를 여러 범주로 분류할 수 있도록 RVM (Relevance Vector Machine) 분류기를 기반으로 한 공구마모 모니터링 시스템을 소개하였다. 저자들은 RVM은 SVM에 비해 작은 수의 교육 샘플에서 더 정확한 결과를 얻을 수 있으며, 또한 분류 속도가 SVM보다 빠른 것으로 보고하였다.14 동일 저자의 또 다른 연구는 절삭력 신호로부터 추출 된 형상을 기반으로 연속 공구마모 예측을 실현하기 위해 GMR (Gaussian Mixture Regression) 모델을 제안하였다.15 위의 연구들은 동일한 연구자의 공구마모 모니터링 시스템에 대한 연구인데, 공정 상태 및 모니터링 환경의 변화에 따라 서로 다른 분류기법들이 적용되어 효과를 얻을 수 있음을 보여준다. 이외에도 공구마모 감지와 관련하여서는 아래의 내용들과 같이 많은 연구 보고들이 있다.
엔드밀 공정에서 공구마모를 모니터링하는 한 연구에서는 공구 결함을 실시간으로 감지하는 새로운 방법을 소개하였는데, 이 방법은 절삭 조건과 독립적이며 공구마모와 상관관계가 있는 힘 모델 계수의 실시간 추적을 기반으로 하였다.16 또 다른 연구에서는 절삭력을 기초로 BPNs (Back-Propagation Neural Networks)와 ANFIS (Adaptive Neuro-Fuzzy Inference System)을 사용하였다.17 이 밖에도 절삭력 기반의 공구마모 모니터링 연구사례들이 많았다.18-20 이 중 Ritou et al.21은 스핀들에 근접하게 설치한 Eddy Current 센서를 이용하여 절삭력을 추정하는 방식으로 공구마모를 모니터링 하는 연구를 수행하였다.
진동 신호를 이용한 한 연구에서는 공구마모를 분류하기 위하여 데이터 수집 및 처리를 위한 모듈, 공구마모 분류를 위한 모듈 및 의사 결정을 위한 모듈의 세 가지 모듈로 구성된 퍼지 시스템의 모델을 제시하였다.22 선삭공정을 다룬 다른 연구에서는 공구의 진동 신호를 ARMA (Autoregressive Moving Average) 모델을 사용하여 모델링하여 공구/홀더 시스템의 동적 특성과 공구의 주요 측면 마모 사이의 관계를 나타내었다.23 진동 신호를 이용한 또 다른 논문은 피쳐 선택 및 식별 방법을 공구 상태 모니터링의 핵심으로 보고, 이 두 가지 문제의 처리를 위해 다중 클래스 SVM-RFE (Support Vector Machine Recursive Feature Elimination)와 LS-SVM (Least Squares Support Vector Machines)을 제안하였다.24
절삭력이나 진동 신호 이외에도 다양한 센서를 이용한 모니터링 연구 사례들이 있다. 음향방출(Acoustic Emission, AE) 신호에 대하여 음향방출 센서나 마이크로폰을 이용한 공구마모 모니터링 시스템 구축 사례들도 보고 되었다.25-27
비전시스템을 이용하여 가공된 표면을 분석하여 공구마모를 모니터링 하는 연구사례도 보고 되었다.28 유사한 형태로 레이저 프로파일 센서를 이용하여 공구마모에 대한 기상측정이 가능하도록 구현한 모니터링 시스템에 대한 연구는 주목할 만하다.29
공작기계의 에너지 모니터링 연구는 연구자들의 노력으로 많은 발전이 이루어지고 있는데, 스핀들의 파워나 전류 변화를 통하여 공구마모를 모니터링 하거나, 공구의 충돌 여부를 감지하는 연구들이 있다.11,30-32
3.2 채터 감지
채터 발생 여부를 감지하기 위한 모니터링 시스템은 공구마모 감지와 유사하게 가속도 센서와 공구동력계를 주로 사용하여 구축된다. 채터 모니터링이 공구마모 모니터링과 다른 점은 모니터링 시스템의 구현 과정에서 신호 처리를 위한 분석 기법의 개발 비중이 두드러지게 나타난다는 것이다. 그 이유는 채터의 발생 메커니즘이 공구마모의 발생 메커니즘에 비해 공작기계와 공구 등과 같이 가공공정을 이루는 시스템 요소들 간의 상호 복합적인 영향의 결과로 나타나기 때문인 것으로 사료된다.
WPT (Wavelet Package Transform)와 HHT (Hilbert-Huang Transform)의 두 가지 첨단 신호 처리 기술에 대한 연구를 토대로 최종 밀링공정을 위한 효과적인 채터 식별 방법이 제시되었으며,33 밀링공정에서 절삭력이 절삭 안정성에 미치는 영향을 확인하기 위해 시간 영역 해석, 주파수 영역 해석 및 Wavelet 분석을 기반으로 절삭력 변동을 설명한 논문도 있었다.34 Cao et al.35은 최종 밀링공정을 위한 새로운 채터 식별 방법을 제시하였는데, 채터 특성을 이해하기 위해 다양한 채터 조건에서 생성된 진동 신호와 안정적인 절삭 신호를 연구하면서, 밀링공정에서의 채터 진동의 비선형 특성과 비정적 특성을 고려하여 EEMD (Ensemble Empirical Mode Decomposition)를 사용하여 진동 신호를 해석하고 두 개의 비선형 지표를 채터 감지에 사용하였다. 채터의 심각도가 증가함에 따라 주기적인 채터 성분이 점차적으로 우세하여 확률적 소음의 비율이 감소하므로 이 두 지표가 감소함을 확인하였다.
고속 가공공정에서의 한 사례로 절삭력 및 순간 각속도(Instantaneous Angular Speeds, IAS) 분석을 기반으로 채터 모니터링을 시도하였다. 순간 각속도를 기반으로 한 표시기는 추가 센서가 필요 없으며 제조 시스템의 비용을 높이지 않고도 실현할 수 있어서 채터 검출을 위한 저가의 모니터링 시스템을 개발하기에 적합하다는 의견을 제시하였다.36
채터 검출을 위한 신호 분석에 많이 활용되는 SLD (Stability Lobe Diagram)를 실험적인 방법으로 비교적 간단하게 활용할 수 있는 아이디어를 제시한 한 연구에서는 SSR (Spindle Speed Ramp-Up)이라고 하는 간단하고 빠른 테스트 방법을 제안하였는데, 이 방법은 절삭 깊이를 변경하는 몇 가지 테스트를 수행하여 SLD를 실험적으로 평가한다. 저자는 이 기술이 주파수 분석의 효율적인 사용을 가능하게 하여, 공정에 대한 지식이 없어도 가속도계, 동력계 또는 마이크와 같은 다양한 센서를 사용할 수 있게 한다고 밝히고 있다.37
벨트 전송을 사용하는 머시닝 센터에서 전자식 위치 및 속도제어가 활성화 된 경우와 그렇지 않은 경우의 FRF (Frequency Response Function) 커브에 중요한 차이가 있음을 발견한 연구가 보고되었는데, 스핀들에 탭 테스트를 수행할 때 전자 제어를 활성화한 상태에서 얻은 SLD 곡선이 가공 작업에서 채터 동작을 더 정확하게 예측함을 실험을 통하여 검증하였다.38
절삭력 모니터링을 이용하여 채터를 감지하는 여러 연구들이 있는데,39,40 한 연구에서는 채터 발생시 채터 억제를 용이하게 하기 위해 시계열(Time Domain) 알고리즘을 제안하여 푸리에 변환과 같은 계산이 많은 주파수 도메인 변환을 사용하지 않고 지배적인 채터 주파수를 정확하게 결정할 수 있음을 보였다.41
AE 신호의 모니터링을 통한 채터 감지 사례도 일부 보고되었다.42
위에서 열거한 사례들에서와 같이 채터 감지 및 이의 개선을 위한 학계에서의 연구들은 매우 다양하며, 최근에는 산업계에서도 이러한 모니터링 시스템을 적극적으로 채용하는 사례들이 나타나고 있다. 일례로 공작 기계 업체에서 공작 기계의 설계 및 제작 단계에 이러한 기계 진동 현상의 모니터링과 제어를 위한 시스템을 갖추어 사용자의 전문성을 보완하여 장비의 보호 및 제품의 생산성과 품질을 향상시킬 수 있도록 하고 있다.
3.3 표면 품질 예측
가공품의 표면 상태의 감지 및 예측은 단일 주제로서 모니터링 시스템 개발의 대상이 되기도 하지만, 공구마모나 채터와 함께 종합적인 문제로서 모니터링 대상이 되기도 한다.43 Balasundaram et al.44은 비전시스템을 이용하여 표면 거칠기를 모니터링 하고, 이를 통하여 공구마모와 기계 진동과의 상관관계를 살펴보았다.
절삭력과 가속도와 변위 측정을 동시에 활용한 센서 퓨전 기술로 시스템의 동적 거동을 파악하여 가공품의 표면 품질을 예측하는 연구도 수행되었다.45
표면 상태의 감지 및 예측을 위한 모니터링 시스템의 개발 사례 중에는 가공 정보로부터의 표면 형상 예측과, 가공 중의 모니터링을 통한 센서 신호를 반영한 표면 형상의 재구성 과정에서 가상 가공 기술의 개념이 보여지는 경우도 있는데, 한 연구에서는 측정된 절삭력을 바탕으로 가공된 형상의 편차를 재구성하는 방식의 모델 기반의 형상편차 모니터링 기술을 구현하였다.46
Kovac et al.7은 정삭 밀링에서 표면 가공에 대한 가공 파라미터의 영향을 조사하였다. 인공 지능 도구를 사용하여 표면 거칠기를 모델링하는 접근 방식을 시도하였으며, 퍼지 논리와 회귀 분석을 사용하여 경험적 모델을 개발하였다. 이들 모델에 의해 예측된 표면 거칠기 값을 비교한 결과는 제안된 시스템이 회귀 분석과 같은 기존 접근법과 비교할 때 제품 프로파일의 정확성을 크게 높일 수 있음을 보여주었다. 이를 통해 퍼지 논리 모델링 기법이 건식 가공에서 표면 거칠기 예측에 효과적으로 사용될 수 있음을 나타내었다.
3.4 절삭 메커니즘 규명
티타늄 합금과 탄소섬유강화플라스틱(Carbon Fiber Reinforced Plastic, CFRP)과 같은 절삭성이 취약한 고기능성 소재들은 가공 효율을 높이는 것이 가장 중요하다. 이러한 고기능성 난삭소재들을 대상으로 한 모니터링의 목적도 가공 메커니즘의 이해를 돕기 위한 정보의 확보 차원으로 접근하는 측면이 있다.
CFRP 밀링에 대한 한 연구는 절삭 온도를 열전쌍(Thermocouple)과 적외선 열화상 카메라로 관찰하여 공정과의 상관관계를 분석하여 가공 성능을 향상시킬 수 있는 공정 조건을 판단하였다.47 CFRP 가공 관련 다른 연구는 헬리컬 밀링공정에서 CFRP 공작물의 온도 분포를 조사하기 위한 열전달 모델을 개발하였다. 헬리컬 밀링의 특성에 따라 두 종류의 열원을 제시하였으며, 그 기하학적 모양은 반원형 호와 선으로 모델링하였다. 해석에 기초하여, 단열 경계조건을 갖는 CFRP 공작물에서의 열전달의 비정상상태 3차원 지배방정식을 제안하였으며, 해석 결과는 실험을 통한 온도 측정 결과와 일치하여 개발된 열전달 모델이 절삭 조건을 최적화하고 CFRP 공작물의 열 손상을 억제하는 데에 활용될 수 있음을 보였다.48 Feng et al.49은 Ti-6Al-4V 티타늄 합금 박막 벽체의 수직 밀링 중에 발생하는 채터 현상을 X 방향 밀링 힘 신호, 표면 토포그래피 및 재생성 채터의 예측 이론을 기반으로 검증 하였다. Sun et al.50은 반 인공 열전쌍(Semi-Artificial Thermo Couple)에 의한 절삭 온도와 절삭 조건의 관계를 조사하였다. 실험을 통해 절삭 온도와 절삭력은 동일한 변동 특성을 가지며 절삭 공정의 모니터링과 분석을 위해 서로 보완할 수 있음을 보였다.
공정 메커니즘을 이해하는 데에는 온도 센서뿐 아니라 AE 센서도 이용되는데, AE 센서의 신호가 절삭 및 칩형성 과정에 대한 영향을 파악하기에 적합한 것으로 보고되고 있다. 선반 가공공정 중에 생성 된 AE 신호를 측정하여 가공 작업 상태를 예측한 연구에서는 실험을 통해 칩 형성 과정, 칩 유형 및 전단 각 모두가 AE 신호에 현저한 영향을 미침을 확인하였다.51
Segreto et al.52은 C45 탄소강에서 수행한 가공 실험에서 센서 융합을 통해 가공칩의 형태 분류 및 바람직하지 않은 칩 유형을 식별하였다.
3.5 장비 상태 감지
가공 장비의 상태를 파악하는 것은 가공공정의 안전과 신뢰성을 확보하는 차원에서 가장 기본적으로 수행되어야 하는 일이다. O'Driscoll et al.53은 지능형 에너지 센서를 이용한 장비 상태 감지에 대한 연구를 소개하였다.
가공 장비의 결함 여부는 장비에서 발생하는 진동 신호를 취득하여 분석하는 방식으로 모니터링 시스템이 구성되기도 하는데, 장비의 다양한 구조물들로부터 발생하는 진동 신호들 중에서 가공공정에 영향을 끼칠 수 있는 신호를 선별해 내고, 이로부터 장비의 결함 유형을 판단하기 위한 분석 기법의 개발이 중요하다. 진동 신호 바탕의 회전 기계의 고장 진단 방법을 연구한 한 사례는 수정된 유전과 알고리즘과 SVM (Support Vector Machine)을 사용하여 다양한 오류 패턴을 분류할 수 있음을 보여준다.54 가공장비의 효율적인 제어를 위하여 절삭력을 모니터링 하는 사례도 보고 되었다.55
4. 기계 가공공정 모니터링을 위한 센서
센서는 모니터링 시스템에서 분석 대상이 되는 신호를 출력하는 장치로써 필요에 따라 다양한 종류의 센서가 사용된다. 한 가지 종류의 센서만으로 모니터링 시스템이 구성되기도 하고, 때로는 여러 종류의 센서를 함께 사용하기도 한다.
Fig. 3은 본 논문에서 참고문헌으로 사용한 논문들에서 주로 사용한 센서를 조사한 것이다. 여러 종류의 센서를 함께 사용한 경우에는 각각의 센서에 대하여 모두 사용한 것으로 가산하여 나타내었다. 조사 결과 힘(절삭력)을 측정하기 위한 센서가 가장 많이 사용되었다. 이 결과에는 단순히 일반적으로 많이 사용되는 공구동력계를 사용한 경우만이 아니라, 절삭력을 측정하기 위하여 특별한 장치 구성을 한 경우도 포함되어 있다. 그 다음으로 많이 사용된 센서는 진동을 측정하기 위한 센서이다. 그 뒤를 잇는 것이 이미지를 측정하기 위한 센서인데 여기에는 현미경과 비전시스템, 프로파일 측정 장치 등과 같이 형상을 직접 관찰하기 위한 장치를 사용한 경우를 모두 포함하였다. 기타로 변위를 측정하기 위한 센서, 공작 기계의 엔코더, 회전수를 계측하기 위한 타코미터 등이 사용되기도 한다.
4장의 이어지는 내용에서는 각 센서 별로 모니터링 시스템에서의 활용 사례와 함께 새로운 형태의 센서 개발과 관련된 연구들을 소개한다.
4.1 힘 센서
힘 센서는 절삭공정의 모니터링에서 매우 중요한 위치를 차지하고 있다. 힘 센서는 가공 중의 절삭 부하의 감지에 민감하게 반응하여 공정의 변화를 실시간으로 파악하기에 유용한 데이터를 출력하여 준다. 힘 센서는 공정의 변화를 시계열(Time Domain) 신호의 크기나 파형의 변화로 파악할 수 있을 만큼 민감하여 비교적 직관적인 감지가 가능하면서도 신호의 진동 성분에 대한 분석을 통하여 보다 변별력 있는 결과를 얻을 수 있다. 이러한 특징으로 인하여 다른 종류의 센서를 이용한 모니터링 시스템의 구현이나 새로운 센서의 개발에 있어서 힘 센서는 성능의 검증을 위한 비교 기준으로서 역할을 한다.
일반적인 힘 센서는 형태적인 특징으로 인해 가공공정 중에 움직임이 없는 부분(밀링 가공에서는 소재, 선반 가공에서는 공구)에 주로 설치하게 되는데, 설치의 용이성이 낮음으로 인하여 사용이 제한되기도 한다. 근래에는 모니터링 시스템에 힘 센서의 적용성을 높이고 보다 효과적인 데이터 취득을 위하여 스핀들에 설치하는 형태 등의 다양한 방향으로의 힘 센서 개발을 위한 연구들이 이루어지고 있다.
밀링공정에서 스핀들에 설치되어 절삭 부하를 감지할 수 있는 형태의 센서 개발들로는 다음과 같은 사례들이 있다. 압전 재료를 이용하여 스핀들에서 토크의 변화를 감지하여 공정을 모니터링할 수 있는 형태의 센서 시제품을 시험되기도 하였고,56 Fig. 4와 같이 원형의 다이아프램 구조를 갖는 형태로 3축의 힘과 3축의 모멘트를 측정할 수 있는 센서도 고안되었다.57 또한 밀링 및 드릴링 공정을 위한 스트레인게이지 기반의 무선 회전식 동력계의 연구개발 사례도 있다. 이 회전형 공구 동력계는 최대 3000 N의 절삭력과 5000 rpm의 회전을 측정할 수 있으며, 모니터링 신호를 무선 통신으로 취득할 수 있다.58 다른 사례로 변위 센서를 스핀들에 내장하여 밀링공정에서 이를 이용하여 절삭 부하를 정밀하게 모니터링 하기도 하였다.59
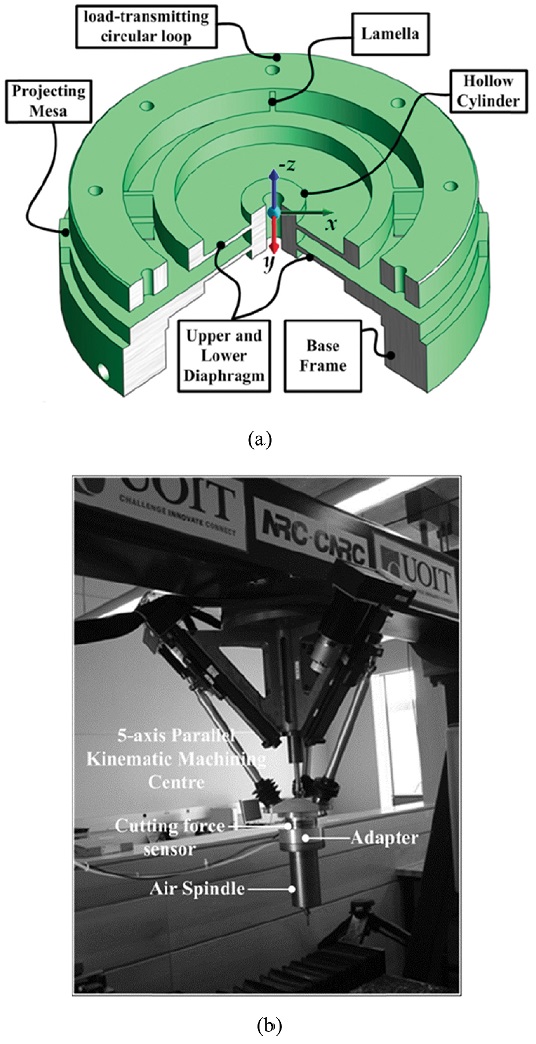
A sensor system for cutting force measurement: (a) 3D Model of the monolithic elastic element structure, (b) Experimental setup for implementing the sensor system for cutting force measurement57 (Adapted from Ref. 57 on the basis of open access)
선반공정에서 공구측에 설치하는 형태로의 센서 개발로는 다음과 같은 사례들이 있다. Fig. 5와 같이 선반 가공용 공구의 홀더 형태를 갖추고 동시에 3축의 힘의 변화를 모니터링 할 수 있는 스트레인 게이지 기반의 센서가 고안되었으며,60 선반용 공구의 인서트 하단부에 압전 필름을 삽입하여 가공 시의 절삭력을 측정할 수 있는 센서도 개발되었다.61 공구 측면에 표면 탄성파 센서(Surface Acoustic Wave, SAW)를 부착하여 절삭력을 감지하는 연구 사례도 발견되었다.62
4.2 가속도 센서
진동 신호는 시스템 상태 변화의 영향을 잘 보여주는 특징으로 인해 모니터링 시스템의 구현에 있어서 매우 다양하게 이용된다. 공구마모와 채터의 감지뿐만 아니라 장비 고장 진단을 위한 모니터링 시스템의 구현에 있어서도 직접적인 감시의 대상이 된다.54
진동 신호는 주로 가속도 센서를 이용하여 측정이 되는데, 가속도 센서는 비교적 크기가 작아 설치의 용이성이 높은 편이고, 시스템 변화를 파악할 수 있는 시간에 따른 진동의 크기와 파형 데이터를 출력해 준다. 이러한 특성으로 인해 많은 연구들에서 시스템의 진동 신호를 모니터링 하기 위하여 가속도 센서를 사용하고 있다. 진동 신호를 이용한 모니터링 시스템의 구현에서는 절삭공정 중에 진동을 발생시키는 가공 장비의 구성 요소가 다양함으로 신호의 변별력과 활용도를 높이기 위한 분석 기법의 개발에 많은 역량이 투입되는 특징이 있다.
최근에는 공작기계 업체들이 가속도 센서를 장비 안에 내장하도록 하고, 분석 솔루션을 함께 제공하면서, 사용자가 장비의 상태를 모니터링할 수 있게 하여 장비를 보호하고 생산성 및 제품의 품질을 향상시키는 데에 도움이 되도록 하고 있다.
4.3 온도 센서
칩의 생성이나 공구의 마모 등과 같은 절삭공정에 대한 메커니즘을 분석하는데 있어서 공정 온도는 중요한 정보 중의 하나이다. 공정 온도의 관찰은 센서의 직접 접촉에 의해서 관찰하거나 적외선 관찰 장치를 통한 비접촉식 관찰을 통해서할 수 있다.63
가공 소재에 열전쌍을 설치하는 경우에는 가공 진행에서의 연속적인 데이터의 수집에 한계가 있다. 절삭 공구에 근접한 위치에 열전쌍을 설치하는 것은 공간적인 제약으로 인하여 쉽지 않으나 근래에 매우 작은 크기의 열전쌍을 설치해서 온도 데이터를 취득하여 분석하는 사례가 발생하고 있다. Sugita et al.64은 절삭 공구의 경사면에 마이크로 급의 온도 센서 어레이를 설치하고, 의료용 어플리케이션으로서 MC 나일론 공작물을 가공하면서 절삭 온도를 측정하였다. Kerrigan et al.65은 밀링 공구의 홀더 속에 내장되는 형태로 온도 측정이 가능한 무선 센서(Wireless Integrated Thermocouple, WIT)를 고안하여 실험을 통해 성능을 검증하였다. 절삭 인서트에 내장할 수 있는 박막 열전대(Thin Film Thermocouples, TFTCs)의 개발도 보고되었다.66
4.4 이미지 센서
대부분의 경우 이미지 센서는 오프라인에서 공구마모를 직접적으로 측정하기 위하여 사용되며, 다른 센서 신호들의 분석을 통해 예측한 공구의 마모 정도를 비교하기 위한 기준 데이터를 제공하는 역할을 한다.67,68
Zhang et al.69은 머신 비전을 기반으로 한 온라인 공구마모 측정 방법을 연구하였는데, 보다 정확한 결과를 얻기 위해 마모 모서리 지점의 정밀도를 높이기 위해 서브 픽셀 정밀도를 갖는 마모 모서리 지점의 정확한 검출 알고리즘을 제안하였다. 실험을 통해 제안 된 공구마모 온라인 측정 방법이 현미경의 수작업 측정 정밀도보다 더 정밀함을 보였다.
이미지 센서 기반의 비전시스템은 일반적인 모니터링 시스템에서는 온라인 모니터링에 적용되는데 어려움이 있으나, 다축 밀링이나 드릴링 머신에서의 공구 충돌 감지 분야에서는 스핀들과 공구의 움직임을 실시간으로 파악하여 안전한 공구의 경로 생성에 기여하는 방식으로 온라인 모니터링 시스템에서 사용되거나, 실시간으로 가공되는 제품의 표면을 관찰하여 공구마모를 파악하는 방식의 온라인 모니터링 시스템으로 사용되는 사례가 있다.28,70
4.5 음향방출 센서
음향방출 센서는 고주파수 대역의 신호를 감지할 수 있는 센서로서 많은 연구자들의 관심을 받아 왔다. 높은 대역의 신호를 취득하기 위한 높은 샘플링 속도와 그로 인해 발생하는 많은 데이터로 인해 그동안은 실시간 신호처리에 제약이 있어 왔다. 그러나, 최근 고속 DAQ 가격이 낮아지고 고속컴퓨팅 장치와 소프트웨어의 발달로 인해 앞으로의 활용이 더욱 주목된다. 다만, 고주파수 대역 신호와 물리적 현상과의 상관관계가 일반적으로 결정되지 않아 공구와 소재의 접촉 감지 등과 같은 특수한 용도에만 넓게 활용되고 범용적 사용에는 다소 한계가 있어왔다. 그럼에도, 많은 연구자들이 음향방출 센서를 이용한 다양한 성공사례를 지속적으로 발표하고 있어, 향후 다양한 적용 사례가 보고될 것으로 기대된다.
Bhuiyan et al.71은 음향방출 및 진동 특성은 공구 상태 이외에도 선삭가공의 다양한 현상을 모니터링 하는 데 탁월한 성과를 나타냄을 보고하였다. 음향방출 센서와 진동 센서를 결합하여 공구마모, 공구 파손, 칩 형성, 칩 파손, 공작 기계 진동, 기계 진동, 공작물 표면 거칠기 등을 설명하였다. 다수의 음향방출 센서를 사용하여 모니터링 시스템을 구축한 사례도 있는데, 로터리 커터 기반의 가공 작업 모니터링을 위해 3개의 음향방출 센서를 이용한 다중 센서 데이터 융합 프레임 워크가 제안되었다.72
4.6 새로운 센서
기존에 사용되지 않던 새로운 센서의 출현은 모니터링의 가능성을 더욱 넓혀준다는 측면에서 긍정적인 효과가 있다. Sadilek et al.73은 절삭 공구의 인서트에 임피던스 레이어를 구성하여 가공 실험이 진행되는 동안의 전기 저항의 변화를 측정하여 공구마모의 지표로 활용하였다. 임피던스 층의 너비는 공구 측면 마모의 허용치에 해당하는 수준으로 제작되었다. 임피던스 레이어에 마모가 진행되면 전기 저항이 증가하게 되며, 최종적으로 임피던스 레이어가 모두 사라지게 되면 저항 신호가 사라지고, 이것은 공구가 마모 한계에 다다랐음을 나타나게 된다.
센서 자체가 새로운 것은 아니지만, 공작 기계의 구성부품에 모니터링 목적의 신호 출력을 위한 새로운 형태의 시도를 한 사례로써, 마이크로 스트레인 게이지를 내장한 형태의 Z-Slide 구조를 가지는 스핀들을 고안하면서 센서의 진폭을 하드웨어적으로 증가시킬 수 있는 노치 효과에 대하여 논의한 연구도 발견되었다.74
5. 결론
기계 가공공정 모니터링 시스템의 구축이라는 행위는 결국 공정의 최적화를 위한 감각 기관의 구성이라는 관점에서 볼 수 있다. 관찰의 대상이 공구의 마모나 파손일 수도, 또는 채터나 가공면의 품질일 수도 있을 것이나, 최적화라는 것은 결국 기계 가공공정 간의 문제 발생을 최소화하면서 제품의 품질과 생산성을 극대화할 수 있는 공정 파라미터를 결정하기 위한 행위이다. 여러 센서 등을 이용한 일련의 모니터링 행위는 이러한 최적화를 위한 감각기관을 구성하기 위한 것이며, 하나의 목적을 달성하기 위하여 단일 감각기관을 이용하기도 하고, 한 종류의 감각 기관을 복수개로 이용하기도 하며, 여러 종류의 감각기관을 이용하기도 한다.
모니터링 시스템의 성능을 향상시키고 구축의 자유도를 높이기 위해서는 이러한 감각기관인 센서의 활용성을 높이기 위한 노력이 필수적이다. 학계에서는 장치 내부에 센서를 탑재하는 형태로 스핀들이나 공구 및 그 주변 장치들의 기능을 지능화하는 연구들이 활발하게 이루어지고 있다. 그리고, 무선 센서의 사용도 센서의 활용성을 높이기 위한 하나의 접근법으로 보이며, 가공 시에 시스템에서 발생하는 진동을 이용하여 에너지를 수확(Energy Harvesting)하는 기술은 이러한 무선 센서의 활용성 향상에 도움이 될 것으로 보인다.75
최근에 출시되는 절삭가공 장비들은 Fig. 6에 나타낸 바와 같이 장치 내부에 다양한 센서를 탑재하고 이를 활용한 소프트웨어 솔루션까지 함께 제공하고 있다.
센서의 설치 용이성을 높이기 위한 또 하나의 기류로 센서의 소형화와 적은 비용으로 효과를 낼 수 있는 형태의 센서 개발을 들 수 있다. 이는 설치 공간과 비용의 제약을 낮추어 모니터링을 위한 적극적인 센서의 사용을 가능하게 한다.
다른 하나의 접근 방식으로 장치의 최소화를 통한 모니터링 시스템 구축이다. 이것은 부가적인 센서를 사용하지 않고, 기존의 공작 기계에서 얻을 수 있는 파워나 엔코더 신호 등과 같은 데이터를 이용하여 공정 상태를 모니터링 하려는 시도이다.
센서를 사용하거나 사용하지 않거나, 공통적으로 신호의 변별력을 높이고 예측의 정확성을 높일 수 있는 각 공정에 적합한 분석 방법을 찾아내기 위해 수많은 연구자들이 지속적으로 노력하고 있다. 모니터링 시스템의 구축과 관련된 모든 연구는 사실 적합한 분석 방법을 찾기 위한 것이라고 해도 무방할 정도로 많은 역량이 집중되고 있고, 다양한 방법이 시도되고 있다.
컴퓨터 및 소프트웨어 기술의 발전으로 대용량의 데이터에 대한 복잡한 연산이 가능해진 시점에서, 최근 이러한 분석 방법에 인공지능을 적용하거나, Fig. 7과 같이 가상환경에서의 시스템 분석을 통해 가공현상을 예측하고 이러한 것들을 통합된 하나의 시스템으로 구축하려는 사례들이 생겨나고 있다. 새롭게 출현하는 고성능 소재 의 기계 가공 등과 같이 지속적으로 요구되는 공정환경의 변화에 대응하는 모니터링시스템의 개발에 있어서 이러한 인공지능 및 가상 기술의 적용은 모니터링 시스템의 성능 향상에 기여할 것으로 예상된다.
Acknowledgments
본 논문은 산업통상자원부 산업기술 개발사업의 자금지원으로 작성되었으며 이에 감사드립니다(10052978).
REFERENCES
-
Byrne, G., Dornfeld, D., Inasaki, I., König, W., and Teti, R., “Tool Condition Monitoring(TCM) – The Status of Research and Industrial Application,” CIRP Annals, Vol. 44, No. 2, pp. 541-567, 1995.
[https://doi.org/10.1016/S0007-8506(07)60503-4]
- Töshoff, H. H. and Inasaki, I., “Sensors in Manufacturing,” Wiley-VCH Verlag GmbH, ISBN 3-527-29558-5, 2001.
-
Teti, R., Jemielniak, K., O’Donnell, G., and Dornfeld, D., “Advanced Monitoring of Machining Operations,” CIRP Annals, Vol. 59, No. 2, pp. 717-739, 2010.
[https://doi.org/10.1016/j.cirp.2010.05.010]
-
Ridwan, F. and Xu, X., “Advanced CNC System with In-Process Feed-Rate Optimisation,” Robotics and Computer-Integrated Manufacturing, Vol. 29, No. 3, pp. 12-20, 2013.
[https://doi.org/10.1016/j.rcim.2012.04.008]
-
Tapoglou, N., Mehnen, J., Vlachou, A., Doukas, M., Milas, N., et al., “Cloud-Based Platform for Optimal Machining Parameter Selection Based on Function Blocks and Real-Time Monitoring,” Journal of Manufacturing Science and Engineering, Vol. 137, No. 4, Paper No. 040909, 2015.
[https://doi.org/10.1115/1.4029806]
-
Li, Y., Liu, C., Hao, X., Gao, J. X., and Maropoulos, P. G., “Responsive Fixture Design Using Dynamic Product Inspection and Monitoring Technologies for the Precision Machining of Large-Scale Aerospace Parts,” CIRP Annals, Vol. 64, No. 1, pp. 173-176, 2015.
[https://doi.org/10.1016/j.cirp.2015.04.025]
-
Kovac, P., Rodic, D., Pucovsky, V., Savkovic, B., and Gostimirovic, M., “Application of Fuzzy Logic and Regression Analysis for Modeling Surface Roughness in Face Milliing,” Journal of Intelligent Manufacturing, Vol. 24, No. 4, pp. 755-762, 2013.
[https://doi.org/10.1007/s10845-012-0623-z]
-
Tapoglou, N., Mehnen, J., Vlachou, A., Doukas, M., Milas, N., et al., “Cloud-Based Platform for Optimal Machining Parameter Selection Based on Function Blocks and Real-Time Monitoring,” Journal of Manufacturing Science and Engineering, Vol. 137, No. 4, Paper No. 040909, 2015.
[https://doi.org/10.1115/1.4029806]
-
Mourtzis, D., Vlachou, E., Xanthopoulos, N., Givehchi, M., and Wang, L., “Cloud-Based Adaptive Process Planning Considering Availability and Capabilities of Machine Tools,” Journal of Manufacturing Systems, Vol. 39, pp. 1-8, 2016.
[https://doi.org/10.1016/j.jmsy.2016.01.003]
-
Lamraoui, M., Barakat, M., Thomas, M., and Badaoui, M. E., “Chatter Detection in Milling Machines by Neural Network Classification and Feature Selection,” Journal of Vibration and Control, Vol. 21, No. 7, pp. 1251-1266, 2015.
[https://doi.org/10.1177/1077546313493919]
-
Bustillo, A. and Rodríguez, J. J., “Online Breakage Detection of Multitooth Tools Using Classifier Ensembles for Imbalanced Data,” International Journal of Systems Science, Vol. 45, No. 12, pp. 2590-2602, 2014.
[https://doi.org/10.1080/00207721.2013.775378]
-
Wang, J., Xie, J., Zhao, R., Zhang, L., and Duan, L., “Multisensory Fusion Based Virtual Tool Wear Sensing for Ubiquitous Manufacturing,” Robotics and Computer-Integrated Manufacturing, Vol. 45, pp. 47-58, 2017.
[https://doi.org/10.1016/j.rcim.2016.05.010]
-
Wang, G., Yang, Y., Zhang, Y., and Xie, Q., “Vibration Sensor Based Tool Condition Monitoring Using ν Support Vector Machine and Locality Preserving Projection,” Sensors and Actuators A: Physical, Vol. 209, pp. 24-32, 2014.
[https://doi.org/10.1016/j.sna.2014.01.004]
-
Wang, G., Yang, Y., Xie, Q., and Zhang, Y., “Force Based Tool Wear Monitoring System for Milling Process Based on Relevance Vector Machine,” Advances in Engineering Software, Vol. 71, pp. 46-51, 2014.
[https://doi.org/10.1016/j.advengsoft.2014.02.002]
-
Wang, G., Qian, L., and Guo, Z., “Continuous Tool Wear Prediction Based on Gaussian Mixture Regression Model,” International Journal of Advanced Manufacturing Technology, Vol. 66, Nos. 9-12, pp. 1921-1929, 2013.
[https://doi.org/10.1007/s00170-012-4470-z]
-
Nouri, M., Fussell, B. K., Ziniti, B. L., and Linder, E., “Real-Time Tool Wear Monitoring in Milling Using a Cutting Condition Independent Method,” International Journal of Machine Tools and Manufacture, Vol. 89, pp. 1-13, 2015.
[https://doi.org/10.1016/j.ijmachtools.2014.10.011]
-
Liu, T.-I., Song, S.-D., Liu, G., and Wu, Z., “Online Monitoring and Measurements of Tool Wear for Precision Turning of Stainless Steel Parts,” International Journal of Advanced Manufacturing Technology, Vol. 65, Nos. 9-12, pp. 1397-1407, 2013.
[https://doi.org/10.1007/s00170-012-4265-2]
-
Wang, G., Guo, Z., and Yang, Y., “Force Sensor Based Online Tool Wear Monitoring Using Distributed Gaussian ARTMAP Network,” Sensors and Actuators A: Physical, Vol. 192, pp. 111-118, 2013.
[https://doi.org/10.1016/j.sna.2012.12.029]
-
Karandikar, J., McLeay, T., Turner, S., and Schmitz, T., “Tool Wear Monitoring Using Naive Bayes Classifiers,” International Journal of Advanced Manufacturing Technology, Vol. 77, Nos. 9-12, pp. 1613-1626, 2015.
[https://doi.org/10.1007/s00170-014-6560-6]
-
Wang, G., Yang, Y., and Li, Z., “Force Sensor Based Tool Condition Monitoring Using a Heterogeneous Ensemble Learning Model,” Sensors, Vol. 14, No. 11, pp. 21588-21602, 2014.
[https://doi.org/10.3390/s141121588]
-
Ritou, M., Garnier, S., Furet, B., and Hascoët, J.-Y., “Angular Approach Combined to Mechanical Model for Tool Breakage Detection by Eddy Current Sensors,” Mechanical Systems and Signal Processing, Vol. 44, Nos. 1-2, pp. 211-220, 2014.
[https://doi.org/10.1016/j.ymssp.2013.02.004]
- Antić, A., Šimunović, G., Šarić, T., Milošević, M., and Ficko, M., “A Model of Tool Wear Monitoring System for Turning,” Tehnicki Vjesnik/Technical Gazette, Vol. 20, No. 2, pp. 247-254, 2013.
-
Aghdam, B., Vahdati, M., and Sadeghi, M., “Vibration-Based Estimation of Tool Major Flank Wear in a Turning Process Using ARMA Models,” International Journal of Advanced Manufacturing Technology, Vol. 76, Nos. 9-12, pp. 1631-1642, 2015.
[https://doi.org/10.1007/s00170-014-6296-3]
-
Li, W., Fu, P., and Cao, W., “Study on Feature Selection and Identification Method of Tool Wear States Based on SVM,” International Journal on Smart Sensing & Intelligent Systems, Vol. 6, No. 2, pp. 448-465, 2013.
[https://doi.org/10.21307/ijssis-2017-549]
-
Maia, L. H. A., Abrao, A. M., Vasconcelos, W. L., Sales, W. F., and Machado, A. R., “A New Approach for Detection of Wear Mechanisms and Determination of Tool Life in Turning Using Acoustic Emission,” Tribology International, Vol. 92, pp. 519-532, 2015.
[https://doi.org/10.1016/j.triboint.2015.07.024]
-
Downey, J. and Raghavendra, R., “Comparison and Analysis of Audible Sound Energy Emissions during Single Point Machining of HSTS with PVD TiCN Cutter Insert Across Full Tool Life,” Wear, Vol. 313, Nos. 1-2, pp. 53-62, 2014.
[https://doi.org/10.1016/j.wear.2014.02.004]
-
Hung, C.-W. and Lu, M.-C., “Model Development for Tool Wear Effect on ae Signal Generation in Micromilling,” International Journal of Advanced Manufacturing Technology, Vol. 66, No. 9-12, pp. 1845-1858, 2013.
[https://doi.org/10.1007/s00170-012-4464-x]
-
Bhat, N. N., Dutta, S., Vashisth, T., Pal, S., Pal, S. K., et al., “Tool Condition Monitoring by SVM Classification of Machined Surface Images in Turning,” International Journal of Advanced Manufacturing Technology, Vol. 83, Nos. 9-12, pp. 1487-1502, 2016.
[https://doi.org/10.1007/s00170-015-7441-3]
-
Čerče, L., Pušavec, F., and Kopač, J., “A New Approach to Spatial Tool Wear Analysis and Monitoring,” Strojniški Vestnik-Journal of Mechanical Engineering, Vol. 61, No. 9, pp. 489-497, 2015.
[https://doi.org/10.5545/sv-jme.2015.2512]
-
Stavropoulos, P., Papacharalampopoulos, A., Vasiliadis, E., and Chryssolouris, G., “Tool Wear Predictability Estimation in Milling Based on Multi-Sensorial Data,” International Journal of Advanced Manufacturing Technology, Vol. 82, Nos. 1-4, pp. 509-521, 2016.
[https://doi.org/10.1007/s00170-015-7317-6]
-
Tönissen, S., Koike, R., Kakinuma, Y., Aoyama, T., and Klocke, F., “Monitoring of Tool Collision in Drilling by Disturbance Observer,” CIRP Journal of Manufacturing Science and Technology, Vol. 7, No. 3, pp. 274-282, 2014.
[https://doi.org/10.1016/j.cirpj.2014.05.004]
-
Drouillet, C., Karandikar, J., Nath, C., Journeaux, A.-C., El Mansori, M., et al., “Tool Life Predictions in Milling Using Spindle Power with the Neural Network Technique,” Journal of Manufacturing Processes, Vol. 22, pp. 161-168, 2016.
[https://doi.org/10.1016/j.jmapro.2016.03.010]
-
Cao, H., Lei, Y., and He, Z., “Chatter Identification in End Milling Process Using Wavelet Packets and Hilbert–Huang Transform,” International Journal of Machine Tools and Manufacture, Vol. 69, pp. 11-19, 2013.
[https://doi.org/10.1016/j.ijmachtools.2013.02.007]
-
Huang, P., Li, J., Sun, J., and Zhou, J., “Vibration Analysis in Milling Titanium Alloy Based on Signal Processing of Cutting Force,” International Journal of Advanced Manufacturing Technology, Vol. 64, Nos. 5-8, pp. 613-621, 2013.
[https://doi.org/10.1007/s00170-012-4039-x]
-
Cao, H., Zhou, K., and Chen, X., “Chatter Identification in End Milling Process Based on EEMD and Nonlinear Dimensionless Indicators,” International Journal of Machine Tools and Manufacture, Vol. 92, pp. 52-59, 2015.
[https://doi.org/10.1016/j.ijmachtools.2015.03.002]
-
Lamraoui, M., Thomas, M., El Badaoui, M., and Girardin, F., “Indicators for Monitoring Chatter in Milling Based on Instantaneous Angular Speeds,” Mechanical Systems and Signal Processing, Vol. 44, Nos. 1-2, pp. 72-85, 2014.
[https://doi.org/10.1016/j.ymssp.2013.05.002]
-
Grossi, N., Scippa, A., Sallese, L., Sato, R., and Campatelli, G., “Spindle Speed Ramp-Up Test: A Novel Experimental Approach for Chatter Stability Detection,” International Journal of Machine Tools and Manufacture, Vol. 89, pp. 221-230, 2015.
[https://doi.org/10.1016/j.ijmachtools.2014.11.013]
-
Dos Santos, R. G. and Coelho, R. T., “A Contribution to Improve the Accuracy of Chatter Prediction in Machine Tools Using the Stability Lobe Diagram,” Journal of Manufacturing Science and Engineering, Vol. 136, No. 2, Paper No. 021005, 2014.
[https://doi.org/10.1115/1.4025514]
-
Frumusanu, G. R., Constantin, I. C., Marinescu, V., and Epureanu, A., “Development of a Stability Intelligent Control System for Turning,” International Journal of Advanced Manufacturing Technology, Vol. 64, Nos. 5-8, pp. 643-657, 2013.
[https://doi.org/10.1007/s00170-012-4074-7]
-
Moradi, H., Vossoughi, G., Movahhedy, M. R., and Salarieh, H., “Suppression of Nonlinear Regenerative Chatter in Milling Process via Robust Optimal Control,” Journal of Process Control, Vol. 23, No. 5, pp. 631-648, 2013.
[https://doi.org/10.1016/j.jprocont.2013.02.006]
-
Ma, L., Melkote, S. N., and Castle, J. B., “A Model-Based Computationally Efficient Method for On-Line Detection of Chatter in Milling,” Journal of Manufacturing Science and Engineering, Vol. 135, No. 3, Paper No. 031007, 2013.
[https://doi.org/10.1115/1.4023716]
-
Filippov, A., Nikonov, A. Y., Rubtsov, V., Dmitriev, A. I., and Tarasov, S. Y., “Vibration and Acoustic Emission Monitoring the Stability of Peakless Tool Turning: Experiment and Modeling,” Journal of Materials Processing Technology, Vol. 246, pp. 224-234, 2017.
[https://doi.org/10.1016/j.jmatprotec.2017.03.030]
-
Jeyakumar, S., Marimuthu, K., and Ramachandran, T., “Prediction of Cutting Force, Tool Wear and Surface Roughness of Al6061/SiC Composite for End Milling Operations Using RSM,” Journal of Mechanical Science and Technology, Vol. 27, No. 9, pp. 2813-2822, 2013.
[https://doi.org/10.1007/s12206-013-0729-z]
-
Balasundaram, M. K. and Ratnam, M. M., “In-Process Measurement of Surface Roughness Using Machine Vision with Sub-Pixel Edge Detection in Finish Turning,” Int. J. Precis. Eng. Manuf., Vol. 15, No. 11, pp. 2239-2249, 2014.
[https://doi.org/10.1007/s12541-014-0587-3]
-
Albertelli, P., Goletti, M., Torta, M., Salehi, M., and Monno, M., “Model-Based Broadband Estimation of Cutting Forces and Tool Vibration in Milling through In-Process Indirect Multiple-Sensors Measurements,” International Journal of Advanced Manufacturing Technology, Vol. 82, Nos. 5-8, pp. 779-796, 2016.
[https://doi.org/10.1007/s00170-015-7402-x]
-
Krüger, M. and Denkena, B., “A Model-Based Approach for Monitoring of Shape Deviations in Peripheral Milling,” International Journal of Advanced Manufacturing Technology, Vol. 67, Nos. 9-12, pp. 2537-2550, 2013.
[https://doi.org/10.1007/s00170-012-4672-4]
-
Yashiro, T., Ogawa, T., and Sasahara, H., “Temperature Measurement of Cutting Tool and Machined Surface Layer in Milling of CFRP,” International Journal of Machine Tools and Manufacture, Vol. 70, pp. 63-69, 2013.
[https://doi.org/10.1016/j.ijmachtools.2013.03.009]
-
Liu, J., Chen, G., Ji, C., Qin, X., Li, H., et al., “An Investigation of Workpiece Temperature Variation of Helical Milling for Carbon Fiber Reinforced Plastics (CFRP),” International Journal of Machine Tools and Manufacture, Vol. 86, pp. 89-103, 2014.
[https://doi.org/10.1016/j.ijmachtools.2014.06.008]
-
Feng, J., Sun, Z., Jiang, Z., and Yang, L., “Identification of Chatter in Milling of Ti-6Al-4V Titanium Alloy Thin-Walled Workpieces Based on Cutting Force Signals and Surface Topography,” International Journal of Advanced Manufacturing Technology, Vol. 82, Nos. 9-12, pp. 1909-1920, 2016.
[https://doi.org/10.1007/s00170-015-7509-0]
-
Sun, Y., Sun, J., Li, J., and Xiong, Q., “An Experimental Investigation of the Influence of Cutting Parameters on Cutting Temperature in Milling Ti6Al4V by Applying Semi-Artificial Thermocouple,” International Journal of Advanced Manufacturing Technology, Vol. 70, Nos. 5-8, pp. 765-773, 2014.
[https://doi.org/10.1007/s00170-013-5294-1]
-
Hase, A., Wada, M., Koga, T., and Mishina, H., “The Relationship between Acoustic Emission Signals and Cutting Phenomena in Turning Process,” International Journal of Advanced Manufacturing Technology, Vol. 70, Nos. 5-8, pp. 947-955, 2014.
[https://doi.org/10.1007/s00170-013-5335-9]
-
Segreto, T., Simeone, A., and Teti, R., “Principal Component Analysis for Feature Extraction and NN Pattern Recognition in Sensor Monitoring of Chip Form during Turning,” CIRP Journal of Manufacturing Science and Technology, Vol. 7, No. 3, pp. 202-209, 2014.
[https://doi.org/10.1016/j.cirpj.2014.04.005]
-
O'Driscoll, E., Kelly, K., and O'Donnell, G. E., “Intelligent Energy Based Status Identification as a Platform for Improvement of Machine Tool Efficiency and Effectiveness,” Journal of Cleaner Production, Vol. 105, pp. 184-195, 2015.
[https://doi.org/10.1016/j.jclepro.2015.01.058]
-
Lu, L., Yan, J., and de Silva, C. W., “Dominant Feature Selection for the Fault Diagnosis of Rotary Machines Using Modified Genetic Algorithm and Empirical Mode Decomposition,” Journal of Sound and Vibration, Vol. 344, pp. 464-483, 2015.
[https://doi.org/10.1016/j.jsv.2015.01.037]
-
Yamada, Y. and Kakinuma, Y., “Sensorless Cutting Force Estimation for Full-Closed Controlled Ball-Screw-Driven Stage,” International Journal of Advanced Manufacturing Technology, Vol. 87, Nos. 9-12, pp. 3337-3348, 2016.
[https://doi.org/10.1007/s00170-016-8710-5]
-
Tansel, I. N., Demetgul, M., Bickraj, K., Kaya, B., and Ozcelik, B., “Basic Computational Tools and Mechanical Hardware for Torque-Based Diagnostic of Machining Operations,” Journal of Intelligent Manufacturing, Vol. 24, No. 1, pp. 147-161, 2013.
[https://doi.org/10.1007/s10845-011-0550-4]
-
Liang, Q., Zhang, D., Coppola, G., Mao, J., Sun, W., et al., “Design and Analysis of a Sensor System for Cutting Force Measurement in Machining Processes,” Sensors, Vol. 16, No. 1, p. 70, 2016.
[https://doi.org/10.3390/s16010070]
-
Rizal, M., Ghani, J. A., Nuawi, M. Z., and Haron, C. H. C., “Development and Testing of an Integrated Rotating Dynamometer on Tool Holder for Milling Process,” Mechanical Systems and Signal Processing, Vol. 52, pp. 559-576, 2015.
[https://doi.org/10.1016/j.ymssp.2014.07.017]
-
Sarhan, A. A. and Matsubara, A., “Investigation about the Characterization of Machine Tool Spindle Stiffness for Intelligent CNC End Milling,” Robotics and Computer-Integrated Manufacturing, Vol. 34, pp. 133-139, 2015.
[https://doi.org/10.1016/j.rcim.2014.12.001]
-
Zhao, Y., Zhao, Y., Liang, S., and Zhou, G., “A High Performance Sensor for Triaxial Cutting Force Measurement in Turning,” Sensors, Vol. 15, No. 4, pp. 7969-7984, 2015.
[https://doi.org/10.3390/s150407969]
-
Wang, C., Rakowski, R., and Cheng, K., “Design and Analysis of a Piezoelectric Film Embedded Smart Cutting Tool,” Proceedings of the Institution of Mechanical Engineers, Part B: Journal of Engineering Manufacture, Vol. 227, No. 2, pp. 254-260, 2013.
[https://doi.org/10.1177/0954405412462785]
-
Wang, C., Cheng, K., Chen, X., Minton, T., and Rakowski, R., “Design of an Instrumented Smart Cutting Tool and Its Implementation and Application Perspectives,” Smart Materials and Structures, Vol. 23, No. 3, Paper No. 035019, 2014.
[https://doi.org/10.1088/0964-1726/23/3/035019]
-
Liang, L., Xu, H., and Ke, Z., “An Improved Three-Dimensional Inverse Heat Conduction Procedure to Determine the Tool-Chip Interface Temperature in Dry Turning,” International Journal of Thermal Sciences, Vol. 64, pp. 152-161, 2013.
[https://doi.org/10.1016/j.ijthermalsci.2012.08.012]
-
Sugita, N., Ishii, K., Furusho, T., Harada, K., and Mitsuishi, M., “Cutting Temperature Measurement by a Micro-Sensor Array Integrated on the Rake Face of a Cutting Tool,” CIRP Annals, Vol. 64, No. 1, pp. 77-80, 2015.
[https://doi.org/10.1016/j.cirp.2015.04.079]
-
Kerrigan, K. and O'Donnell, G. E., “Temperature Measurement in CFRP Milling Using a Wireless Tool-Integrated Process Monitoring Sensor,” International Journal of Automotive Technology, Vol. 7, No. 6, pp. 742-750, 2013.
[https://doi.org/10.20965/ijat.2013.p0742]
-
Li, L., Li, B., Li, X., and Ehmann, K. F., “Experimental Investigation of Hard Turning Mechanisms by PCBN Tooling Embedded Micro Thin Film Thermocouples,” Journal of Manufacturing Science and Engineering, Vol. 135, No. 4, Paper No. 041012, 2013.
[https://doi.org/10.1115/1.4023722]
-
Wang, J., Wang, P., and Gao, R. X., “Enhanced Particle Filter for Tool Wear Prediction,” Journal of Manufacturing Systems, Vol. 36, pp. 35-45, 2015.
[https://doi.org/10.1016/j.jmsy.2015.03.005]
-
Wang, G., Liu, C., Cui, Y., and Feng, X., “Tool Wear Monitoring Based on Cointegration Modelling of Multisensory Information,” International Journal of Computer Integrated Manufacturing, Vol. 27, No. 5, pp. 479-487, 2014.
[https://doi.org/10.1080/0951192X.2013.814162]
-
Zhang, C. and Zhang, J., “On-Line Tool Wear Measurement for Ball-End Milling Cutter Based on Machine Vision,” Computers in Industry, Vol. 64, No. 6, pp. 708-719, 2013.
[https://doi.org/10.1016/j.compind.2013.03.010]
-
Ahmad, R. and Plapper, P., “Generation of Safe Tool-Path for 2.5D Milling/Drilling Machine-Tool Using 3D ToF Sensor,” CIRP Journal of Manufacturing Science and Technology, Vol. 10, pp. 84-91, 2015.
[https://doi.org/10.1016/j.cirpj.2015.04.003]
-
Bhuiyan, M., Choudhury, I., and Dahari, M., “Monitoring the Tool Wear, Surface Roughness and Chip Formation Occurrences Using Multiple Sensors in Turning,” Journal of Manufacturing Systems, Vol. 33, No. 4, pp. 476-487, 2014.
[https://doi.org/10.1016/j.jmsy.2014.04.005]
-
Duro, J. A., Padget, J. A., Bowen, C. R., Kim, H. A., and Nassehi, A., “Multi-Sensor Data Fusion Framework for CNC Machining Monitoring,” Mechanical Systems and Signal Processing, Vol. 66, pp. 505-520, 2016.
[https://doi.org/10.1016/j.ymssp.2015.04.019]
- Sadílek, M., Kratochvíl, J., Petrů, J., Čep, R., Zlámal, T., et al., “Cutting Tool Wear Monitoring with the Use of Impedance Layers,” Tehnicki Vjesnik, Vol. 21, No. 3, pp. 639-644, 2014.
-
Denkena, B., Litwinski, K., Brouwer, D., and Boujnah, H., “Design and Analysis of a Prototypical Sensory Z-Slide for Machine Tools,” Production Engineering, Vol. 7, No. 1, pp. 9-14, 2013.
[https://doi.org/10.1007/s11740-012-0419-1]
-
Ostasevicius, V., Markevicius, V., Jurenas, V., Zilys, M., Cepenas, M., et al., “Cutting Tool Vibration Energy Harvesting for Wireless Sensors Applications,” Sensors and Actuators A: Physical, Vol. 233, pp. 310-318, 2015.
[https://doi.org/10.1016/j.sna.2015.07.014]