
방전 가공과 마이크로 편심 공구전극을 이용한 미세 기둥 어레이 가공
Copyright © The Korean Society for Precision Engineering
This is an Open-Access article distributed under the terms of the Creative Commons Attribution Non-Commercial License (http://creativecommons.org/licenses/by-nc/3.0) which permits unrestricted non-commercial use, distribution, and reproduction in any medium, provided the original work is properly cited.
Abstract
The fabrication of a micro column array using micro EDM (Electrical Discharge Machining) and eccentric tools was presented. With the eccentric tools, micro columns can be easily machined only by feeding the tool vertically, as is the case in mechanical drilling. Moreover, the tool electrode rotates very fast, which is helpful to flush dielectric fluid in the EDM. In this paper, four eccentric tools were machined, and a micro column was machined in a few minutes. Finally, a hundred micro columns with 200-300 μm in a diameter were machined on a metal plate. In this study, vibration-assisted EDM was introduced to improve the machining rate in the fabrication of eccentric tools. Also, the design parameters of eccentric tools were discussed.
Keywords:
Micromachining, Electrical discharge machining, Eccentric tool, Micro column키워드:
미세가공, 방전가공, 편심 공구, 미세 기둥1. 서론
최근 기계전자 및 의료, 바이오 산업의 발달에 따라 기계 부품의 초미세화, 고정밀화가 요구되고 있으며 이러한 고정밀 미세 부품 가공을 위한 가공 기술 수요도 크게 증가하고 있다.1 미세 부품에서 필요한 기본적인 형상은 주로 미세 구멍, 미세 축, 기둥 그리고 미세 홈 등이 있다. 이러한 기본 형상을 보다 정밀하게 또는 보다 높은 생산성으로 제작하기 위해 기존 절삭가공 기술뿐만 아니라 다양한 특수 가공 기술이 많이 연구되고 있다. 미세 구멍이나 미세 홈 가공의 경우 마이크로 드릴링, 밀링, 방전 가공, 레이저 가공 등의 기술이 연구되고 있다. 또한 다양한 소재에 가공하기 위해, 가공정밀도를 높이기 위해, 그리고 가공 속도를 높이기 위해 연구가 되고 있다.1
미세 핀 또는 기둥은 미세 회전부품의 회전축이나 구멍 가공을 위한 마이크로 펀칭 공구, 미세 형상 부품을 위한 금형, 미세 바늘 어레이(Micro Needle Array) 등으로 쓰일 수 있다. 하지만, 마이크로 미터 크기의 핀이나 기둥 형상을 위한 가공기술이 소개된 적이 있지만, 구멍이나 홈 가공 기술에 비해 연구가 부족한 실정이다.2-4 본 논문에서는 미세 기둥 가공을 위한 방전 가공 기술에서, 보다 생산성을 높이고 공정을 단순화시키기 위해 편심공구전극을 이용한 연구를 수행하였다.
2. 미세 기둥 형상 가공
2.1 기존 미세 기둥 형상 가공 기술
미세 기둥 형상을 가공하기 위한 방법 중 하나로 마이크로 밀링 기술이 있다.5 이는 회전하는 미세 밀링 공구를 원형 경로를 따라 이송 시키면서, 동시에 아래로 이송 시켜 미세 원형 기둥 형상을 제작하는 방법이다. 기계적 밀링 가공의 경우 버(Burr)가 발생하고 가공형상크기가 작으면 작을수록 버 발생이 형상정밀도에 악영향을 미치게 된다. 또한 미세 기둥 형상의 크기가 마이크로미터 단위 정도로 작아지게 되면 절삭력에 의해 가공 형상이 변형되거나 파손이 될 수 있으며 가공물의 강도가 높은 경우 공구가 파손될 수 있는 문제가 있다. 따라서 가공 속도를 높이는데 한계가 있으며, 기둥 형상 치수나 가공물 재료 선정에 제한이 있다. 이러한 한계로 인해 공구 이송을 정밀하게 제어하여 가공량(공구의 절입량)을 매우 작게 하여 가공하게 된다.
한편 방전 가공은 전도성 가공물과 공구 전극 사이에 전압을 인가하여 발생하는 스파크 열로 재료를 가공하는 기술이며, 가공물의 강도나 경도에 무관하게 가공할 수 있는 장점이 있다. 따라서 마이크로 밀링 가공과 마찬가지로 공구 전극을 X, Y 방향으로 이송시키며 가공하는 방전 밀링(EDM Milling)으로 금속 소재에 미세기둥형상을 가공할 수 있다. 하지만 방전 가공 특성 상 공구전극과 가공물이 닿으면 방전이 일어나지 않기 때문에 전극과 가공물 사이의 일정한 간극을 유지해야 하며 방전 전류의 피드백을 바탕으로 한 정밀한 위치 제어가 필요하다.6
마이크로 밀링가공이나 방전 밀링과 같이 공구를 이송 시켜 원형기둥형상을 가공하는 경우, 원형 경로를 따라 공구를 이송 시키기 위해 공구 위치를 X, Y방향으로 동시에 제어 해야하고, 그와 동시에 Z방향으로도 위치 제어를 해야 한다. 하지만 크기가 수 십에서 수 백 마이크로미터인 미세 기둥 형상의 경우 매우 정밀한 위치 제어가 필요하나, 동시 제어를 해야 하는 축이 많아지면 정밀 제어가 어려워지고 또한 공구의 이송 속도를 높이는 데에도 한계가 있다. 따라서 가공하고자 하는 기둥 형상의 개수가 많으면, 가공 효율이 매우 낮은 문제가 있다.
2.2 편심공구을 이용한 가공
일반적으로 미세 기둥 형상을 가공할 때에는 Fig. 1(a)와 같이 밀링 공구를 원형으로 이송하여 가공한다. 하지만 이는 Z방향의 공구 이송 제어뿐만 아니라 추가적인 X-Y방향의 이송제어가 필요하다. 하지만 Fig. 1(b)와 같이 공구의 위치가 공구회전중심에서 일정 거리만큼 떨어져 있는 편심공구를 이용하면 추가적인 X-Y이송제어가 필요 없이, 단순히 공구를 회전시킴으로써 고속의 원형이송운동을 얻을 수 있다. 이를 이용하면 기존 X-Y방향 이송제어방법보다 훨씬 빠르게 공구를 이송 시킬 수 있으며 Z방향 이송만으로 미세기둥형상을 가공할 수 있다. 이를 이용하면 Fig. 2와 같이 단순 방전 드릴링 공정으로 다수의 3차원 기둥 형상을 가공할 수 있다.
3. 실험 장치
Fig. 3(a)는 편심공구를 이용한 미세 방전 가공 시스템을 나타내고 있다. 가공시스템은 X-Y-Z 이송기구와 스핀들로 이루어져 있고, 방전가공 회로, 방전 수조와 가공물에 진동을 부가할 수 있는 진동부가장치로 이루어져 있다. 방전 가공에서의 진동부가는 방전가공의 효율을 높일 수 있다.7 Fig. 3(b)는 방전 회로를 나타내고 있으며 파워서플라이, 저항, 콘덴서로 RC 회로를 구성하였다. 이 회로에서 방전 전류를 측정하여 가공 상태를 파악할 수 있으며 공구 전극 이송제어의 피드백 신호로 이용하였다. 공구전극의 재료는 초경합금(WC-Co)을 사용하였으며 역방전에서 쓰인 금속판은 구리, 미세 기둥을 가공한 재료는 황동과 스테인리스강(STS304)이 쓰였다.
4. 미세 편심공구 제작
편심공구전극를 이용한 미세 기둥형상 가공은 두 부분으로 나뉠 수 있다. 첫 번째는 편심공구전극 제작이며, 두 번째는 이를 이용한 미세 기둥 가공이다.
먼저 편심공구전극은 기본적으로 역방전가공(Reverse EDM)을 이용하여 제작하였다.9 Fig. 4와 같이 방전드릴링으로 금속판에 구멍을 가공한 뒤 이 금속판을 공구로 이용하여 전극재료에 다시 미세 공구를 방전가공(역방전)하는 방법이다. 이 때 공구재료의 회전 중심에서 일정거리만큼 편심을 주어 가공한다.
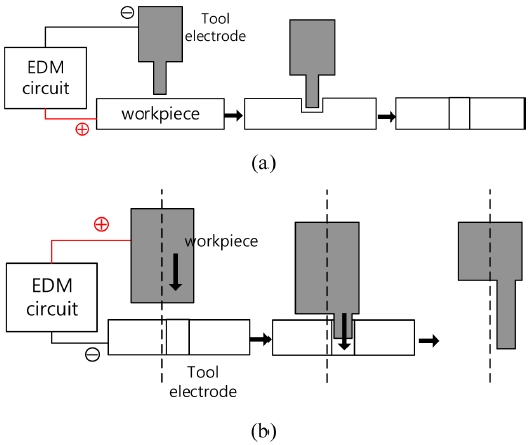
Process for eccentric micro tool electrodes (a) Machining of micro hole (b) Fabrication of an eccentric tool9
미세 구멍 가공에서는 공구전극이 회전할 수 있기 때문에 쉽게 절연액 순환에 문제가 없으나, 역방전의 경우 편심위치에 공구를 제작하기 때문에 공구전극을 회전할 수 없다. 따라서 절연액의 순환이 어려워지며 방전 가공에서 절연액이 잘 순환되지 않으면, 가공 부스러기가 배출되지 못해 가공 효율이 급격히 떨어지게 된다.4 이를 해결하기 위해 방전 수조 밑에 진동부가 장치를 설치하여 역방전시 진동을 부가하여 절연액을 순환시키고자 하였다.7
편심공구의 치수는 미세기둥의 크기와 기둥과 기둥사이의 간격 등을 고려하여 결정하여야 한다. Fig. 5는 미세 기둥과 공구 치수 그리고 기둥 피치와의 관계를 나타낸다. Fig. 5(a)에서 검은 실선으로 나타낸 원은 가공된 미세 기둥이며, 검은 점선으로 나타낸 원은 편심 공구를 나타내고 있다. 편심 공구가 회전하면서 소재를 가공하면 검은 실선의 원형 기둥이 가공된다.
Fig. 5(a)와 같이 기둥을 최대한 촘촘히 배치하는 경우, 공구가 옆 기둥에 닿아서는 안 되므로 다음과 같은 관계식을 구할 수 있다.
(1) |
여기서 dc는 기둥의 지름, dt는 공구의 지름을 나타낸다.
미세 기둥을 Fig. 5(b)와 같이 어레이로 가공하는 경우 기둥과 기둥 사이의 피치 거리(p)는 다음 식으로 표현할 수 있다.
(2) |
여기서 g는 기둥과 기둥 사이의 가공되지 않은 영역(여기서는 미가공 영역이라 칭함)의 폭을 나타낸다.
미가공 영역은 최대한 없애야 하므로 g는 가능한 작아지도록 공구와 기둥 지름, 그리고 피치 거리를 조절해야한다. 따라서 식(1)을 식(2)에 대입하고, 미가공영역(g)를 구하면 다음과 같다.
(3) |
따라서 미가공영역(g)을 없애기 위해서(g < 0) 식(3)을 정리하면, 다음 식(4)를 구할 수 있다. 즉 공구 지름(dt)이 기둥 지름(dc)의 70%보다 크면 미가공 영역을 없앨 수 있다.
(4) |
이 식에서는 방전 가공에서의 간극 거리(Discharge Gap)와 공구의 측면 마모량은 고려되지 않았으나, 실제 가공에서는 이를 고려할 필요가 있다.
또한 방전가공에서는 공구의 마모가 발생하기 때문에 가공량을 고려해 편심공구의 개수와 길이를 정해야 한다. 본 연구에서는 4개의 실린더형 공구가 달려있는 편심공구를 제작하였다. Fig. 6는 역방전으로 가공한 초경합금(WC-Co)재료의 편심공구 전극을 보이고 있다. 실린더형 공구 4개를 회전중심에서 150 μm 만큼 떨어진 지점에 가공하였다. 방전가공으로 구리판에 4개의 구멍을 가공한 뒤 역방전으로 공구를 제작하였다. 또한 가공효율을 향상시키기 위해 구리판에 진동을 부가하였으며 Table 1에 그 가공조건을 나타내었다. Fig. 7은 편심공구 제작시 진동없이 가공했을 때와 진동을 부가했을 때의 공구이송을 나타낸 것이다. 그래프에서 볼 수 있듯이 길이 2000 μm의 공구전극을 가공할 때 진동이 없는 경우, 90분 정도의 시간이 소요되나, 진동을 부가하는 경우 그 가공시간을 50% 이상(40분 소요) 단축시킬 수 있었다.
5. 미세 기둥 가공
5.1 황동과 스테인리스강의 미세 기둥 가공
방전 가공은 가공 중에 가공물뿐만 아니라 공구전극도 같이 가공되어 마모가 상당히 발생하는 공정이다. 미세 기둥을 가공하기 위한 편심공구도 마찬가지로 마모가 발생하며 이로 인해 최종 가공물의 형상에도 영향을 미치게 된다. 가공속도나 공구마모량은 방전가공의 전기적 가공 조건, 공구 재료나 가공물 재료의 열적 특성에 따라 달라진다. Fig. 8은 황동(Brass)과 스테인리스 강(STS304)에 미세 기둥을 가공한 예이며 가공 조건은 Table 2와 같다. 가공 시간은 황동은 약 90 초, 스테인리스 강은 약 8분 정도 소요되었다. 스테인리스 강의 경우 축방향공구의 마모는 50 μm로 황동가공에서의 15 μm보다 크게 측정되었으며, 사진에서 볼 수 있듯이 가공된 기둥의 길이도 마모량에 비례하여 짧게 가공된 것을 볼 수 있다. 이는 소재의 높은 융점 등으로 방전 가공 특성이 좋지 못하기 때문이다.7 또한 스테인리스 강에 가공된 형상을 보면 상대적으로 둥글게 움푹 패인 바닥을 볼 수 있으며 이는 공구 길이 방향 뿐만 아니라 측면에서도 마모가 크다는 것을 보이고 있다. 이로 인해 가공이 계속되면 기둥의 형상 정밀도에도 영향을 끼칠 수 있다. 이를 해결하기 위해서는 가공시간 단축과 마모량 감소를 위해 진동부가 방전이나 초경합금이 아닌 흑연 또는 텅스텐 재질의 공구 재료 선택이 필요할 것으로 판단된다.
5.2 미세 기둥 어레이 가공
앞서 설명한 편심공구를 이용한 가공방법으로 미세 기둥 어레이를 제작하였다. Fig. 9는 5 × 5의 25개 미세 기둥을 가공한 예이다. 기둥 한 개 당 가공시간은 1-2분 내외이며, 전체 가공시간은 대략 40분 정도 소요되었다. 가공시간은 가전압이나 축전용량 등으로 달라질 수 있다.
5.3 미가공영역
Fig. 10(a)은 10 × 10의 100개의 미세 기둥을 가공한 예이다. 한편 식(1)과 식(2)에서 기둥 사이의 피치거리를 너무 크게 하면 미가공영역(g > 0)이 남게 된다. Fig. 10(b)와 같이 피치거리가 큰 경우(630 μm) 기둥과 기둥 사이에 미가공 영역이 뾰족한 바늘 형태로 남게 되는 것을 알 수 있다. Fig. 11은 미세 기둥의 피치거리를 조절하여 미가공영역을 줄인 가공예이다.
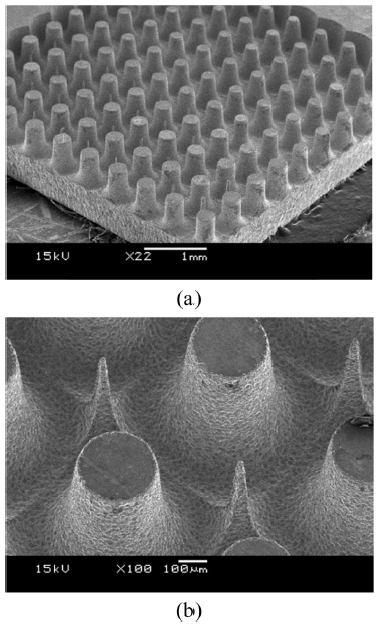
Micro column array machined on a brass steel plate: 10 × 10, 100 cylindrical columns, pitch 630 μm (a) isometric view, (b) enlarged view of a micro column and under-cut area
미가공영역은 피치거리에 의해서도 좌우되지만, 방전 가공 특성성 공구의 마모도 미가공영역에 영향을 미치게 된다. 미가공영역이 수직기둥이 아니라 테이퍼가 심한 형태를 띄는것도 편심공구의 마모에 기인한 것이다.
Fig. 12는 기둥어레이를 가공한 뒤의 편심공구의 사진이며, 공구 측면 방향과 축방향으로 마모가 발생된 것을 볼 수 있다. Figs. 10(a)나 11의 기둥형상을 자세히 보면 가공횟수가 증가하면서 테이퍼 형상이 조금씩 심해지는 것을 볼 수 있다. 이는 공구의 축방향, 횡방향 마모비가 조금씩 달라진다는 것을 의미한다. 따라서 형상정밀도를 높이기 위해서는 공구 마모를 줄이거나 마모된 공구형상을 재생시키는 방법 등에 대한 추가적인 연구가 필요하다.1,6
6. 결론
미세 기둥 형상 어레이를 가공하기 위해서 미세 편심공구전극을 제작하였다. 기존 마이크로밀링 또는 방전밀링의 경우 공구를 미세 기둥형상만큼 원형으로 이송시키면서 수직방향으로 이송시켜야 하므로 X-Y-Z의 3축으로 정밀하게 제어해야한다. 하지만 편심공구를 적용하면 드릴링처럼 수직방향으로 공구를 이송하기만 하면 미세 원형 기둥을 쉽게 가공할 수 있다. 더욱이 방전밀링의 경우 전극과 가공물 사이에 절연액을 순환시킬 필요가 있지만 편심공구전극의 경우 빠른 속도로 원형으로 이송하기 있기 때문에 절연액 순환이 원활하며 결과적으로 가공속도를 향상시킬 수 있다. 하지만 방전 가공의 특성상 공구전극의 마모가 발생하며 그로 인해 미세 기둥의 테이퍼형상과 기둥 사이에 뾰족한 형태의 미가공영역이 남는 것을 확인할 수 있었다. 추후 공구전극의 마모를 최소화시키기 위해 녹는점이 높은 텅스텐 재료의 공구를 사용하거나 방전가공의 전기적 조건 등에 대한 추가적인 연구가 필요하다.
편심공구는 방전 가공뿐만 아니라 다른 마이크로 절삭 공정에서 공구로써도 이용될 수 있으므로 다양한 소재와 형상 제작에 응용될 수 있으며 현재 관련 연구가 진행 중에 있다. 고경도금속, 세라믹, 고강도유리 등의 소재에 제작된 지름 10-100 μm 크기의 미세 기둥 형상은 의료분야의 미세 바늘 어레이(Micro Needle Array), 미세 금속 핀, 마이크로 베어링의 롤러, 미세 구조물 조립(Micro Assembly)를 위한 고정축, 회전축 등으로 활용될 수 있다.
Acknowledgments
이 논문은 2015년도 정부(교육부)의 재원으로 한국연구재단의 지원을 받아 수행된 기초연구사업임(No. NRF-2015R1D1A1A01060646).
REFERENCES
-
Masuzawa, T., “State of the Art of Micromachining,” CIRP Annals-Manufacturing Technology, Vol. 49, No. 2, pp. 473-488, 2000.
[https://doi.org/10.1016/S0007-8506(07)63451-9]
-
Masuzawa, T., Fujino, M., Kobayashi, K., Suzuki, T., and Kinoshita, N., “Wire Electro-Discharge Grinding for Micro-Machining,” CIRP Annals-Manufacturing Technology, Vol. 34, No. 1, pp. 431-434, 1985.
[https://doi.org/10.1016/S0007-8506(07)61805-8]
-
Masuzawa, T., Yamaguchi, M., and Fujino, M., “Surface Finishing of Micropins Produced by WEDG,” CIRP Annals-Manufacturing Technology, Vol. 54, No. 1, pp. 171-174, 2006.
[https://doi.org/10.1016/S0007-8506(07)60076-6]
-
Masuzawa, T., Tsukamoto, J., and Fujino, M., “Drilling of Deep Microholes by EDM,” CIRP Annals-Manufacturing Technology, Vol. 38, No. 1, pp. 195-198, 1989.
[https://doi.org/10.1016/S0007-8506(07)62683-3]
-
Bang, Y.-B., Lee, K.-M., and Oh, S., “5-Axis Micro Milling Machine for Machining Micro Parts,” International Journal of Advanced Manufacturing Technology, Vol. 25, Nos. 9-10, pp. 888-894, 2005.
[https://doi.org/10.1007/s00170-003-1950-1]
-
Shin, H. S., Park, M. S., Kim, B. H., and Chu, C. N., “Recent Researches in Micro Electrical Machining,” Int. J. Precis. Eng. Manuf., Vol. 12, No. 2, pp. 371-380, 2011.
[https://doi.org/10.1007/s12541-011-0049-0]
-
Lee, P. A., Kim, Y., and Kim, B. H., “Effect of Low Frequency Vibration on Micro EDM Drilling,” Int. J. Precis. Eng. Manuf., Vol. 16, No. 13, pp. 2617-2622, 2015.
[https://doi.org/10.1007/s12541-015-0335-3]
-
Shin, H. S., Kim, B. H., Park, M. S., and Chu, C. N., “Surface Finishing of Micro-EDM Holes Using Deionized Water,” Journal of Micromechanics and Microengineering, Vol. 19, No. 4, Paper No. 045025, 2009.
[https://doi.org/10.1088/0960-1317/19/4/045025]
-
Kim, B. H., Park, B. J., and Chu, C. N., “Fabrication of Multiple Electrodes by Reverse EDM and Their Application in Micro ECM,” Journal of Micromechanics and Microengineering, Vol. 16 No. 4, pp. 843-850, 2006.
[https://doi.org/10.1088/0960-1317/16/4/022]