
압출적층형 3차원 프린터의 고온 압출부 설계를 위한 열-구조 연계 수치해석
Copyright © The Korean Society for Precision Engineering
This is an Open-Access article distributed under the terms of the Creative Commons Attribution Non-Commercial License (http://creativecommons.org/licenses/by-nc/3.0) which permits unrestricted non-commercial use, distribution, and reproduction in any medium, provided the original work is properly cited.
Abstract
This study aims at developing a high temperature extruder for an FDM (Fused Deposition Modeling) type 3D printer that uses engineering thermoplastic filaments. An extruder is a key part of an FDM type printer, in which a filament moves to a heating block and is extruded through a nozzle with a specific diameter. For an appropriate extrusion, the filament should be heated above its softening temperature. Specifically, the filament should not be melted nor softened before it reaches the heating block for appropriate delivery. Hence, the extruder temperature should be carefully controlled to ensure its heating capability as well as its proper delivery. To meet these requirements, thermal-structural finite element (FE) analyses were performed for the prediction of the distributions of temperature and thermal stress. Various extruder designs were then considered to maximize the temperature difference between the nozzle and delivery parts, as well as to ensure structural safety.
Keywords:
3D printing, Fused deposition modeling, Extruder, Finite element method, Thermal-structural coupled analysis키워드:
3차원 프린팅, 압출적층 조형, 압출부, 유한요소법, 열-구조 연계해석1. 서론
3차원 프린팅 공정은 원하는 입체형상을 제작하기 위해 3차원 형상을 다수개의 2차원 단면으로 분할(Slicing)하고, 2차원 단면을 순차적으로 적층하여 원하는 형상을 제조하는 공정이다. 3차원 프린팅은 과거 시작품 제작이나 2차공정을 위한 패턴으로 활용되며 쾌속 조형(Rapid Prototyping)으로 명명되었으나,1 최근 기술의 발전에 따라 제품의 직접 제조에 활용됨으로써 적층 제조(Additive Manufacturing) 공정으로 불리운다.2
3차원 프린터는 광중합(Photo-Polymerization) 방식, 재료 압출(Material Extrusion) 방식, 접착제 분사(Binder Jetting) 방식, 재료 분사(Material Jetting) 방식, 분말적층 용융(Powder Bed Fusion) 방식, 고에너지 직접조사(Direct Energy Deposition) 방식, 박판 적층(Sheet Lamination) 방식의 7가지 방식으로 구분된다.3 이중 재료압출 방식 프린터는 열가소성 고분자 필라멘트를 가열하여 직경 1 mm 이하의 노즐을 통해 압출함으로써 적층하는 방식으로, 1992년 미국 Stratasys사에서 압출 적층(Fused Deposition Modeling, FDM) 방식으로 명명하여 상용화하였다.4 이후 개방형 소스 3차원 프린터 개발 프로젝트인 RepRap (Replicating Rapid-Prototyper) 프로젝트 등의 영향으로 현재 저가 개인용 프린터의 대다수를 차지하고 있다.5
압출적층형 개인용 프린터의 경우 대부분 PLA (Polylactic Acid)나 ABS (Acrylonitrile Butadiene Styrene)와 같은 범용 열가소성 고분자 필라멘트를 원재료로 사용한다.6 상기 범용 플라스틱은 기계적 강도와 내열성이 취약하여 시제품 검증이나 모형 제작에는 활용이 가능한 반면 내구성, 내열성 등이 요구되는 기능성 부품을 직접 제조하기에는 한계가 있다. 이러한 한계를 극복하기 위해 일부 산업용 프린터에서 PC (Polycarbonate), PEI (Polyetherimide) 등의 엔지니어링/슈퍼엔지니어링 플라스틱 프린팅 기능을 지원하고 있는데,7 상기 엔지니어링/슈퍼엔지니어링 플라스틱은 융점이 높아 고온 압출부의 적용이 필수적이다.
압출적층형 프린터에서 압출부는 필라멘트 소재가 이송되는 이송부와 노즐을 통해 일정 직경으로 출력되는 출력부로 구성되는데,8 이때 이송부에서는 소재가 고체 상태로 원활히 이송되면서 출력부에서 소재가 용융되어 토출되도록 하기 위한 적절한 온도조건의 설정이 필요하다.9 본 연구에서는 엔지니어링/슈퍼엔지니어링 플라스틱 프린팅을 위한 고온 압출부를 개발하고자 하며, 특히 압출부의 열적 특성을 수치해석적으로 고찰하고자 한다. 이를 위해 기존 제품 압출부의 열적 특성을 수치해석을 통해 분석하고, 이를 토대로 고온 압출부 제작시 출력단에서 소재의 융점 이상의 온도를 유지하면서도 이송부 내부에서는 용융이 발생하지 않도록 압출부를 설계하고 수치해석을 통해 검증하고자 한다.
2. 프린터 압출부의 열특성 수치해석
2.1 프린터 압출부의 설계 개요
압출적층형 3차원 프린터 압출부의 열특성 분석을 위해 영국 E3D 社의 E3D V6모델을 선정하였다.10 Fig. 1에 E3D V6모델 압출부의 사진 및 단면도를 도시하였다. 압출부는 크게 하단의 가열부(Heat Block)와 상단의 방열부(Heat Sink)로 구분되며, 배럴(Barrel)을 사용하여 연결되어 있다. Table 1에 각 요소별 재료의 주요 물성을 비교하였다.11
가열부에는 히터가 삽입되어 노즐을 가열해주며, 직경 0.4 mm인 노즐을 통해 필라멘트 소재를 용융시켜 압출하는 역할을 수행한다. 방열부는 다수개의 핀을 통해 열을 방출하는 역할을 수행하며, 내부에 내경 2 mm의 테플론 튜브가 삽입되어 직경 1.75 mm인 필라멘트를 원활하게 이송시키는 역할을 한다.
배럴의 양쪽 끝단에 나사산이 형성되어 각각 가열부와 방열부에 조립되며, 중앙부의 두께를 국부적으로 감소(0.5 mm)시켜 가열부에서 방열부로의 열전달을 감소시키는 열차단(Heat Break) 역할을 수행하도록 설계되어 있다(Fig. 1 참조).
2.2 프린터 압출부의 열-구조 연계해석
상기 압출부의 열특성을 예측하기 위해 열-구조 연계 유한요소해석을 실시하였다. 우선 가열부와 방열부에서의 온도분포를 예측하기 위해 열전달 해석을 수행하고, 열차단부에서의 응력 집중으로 인한 배럴부의 안전성 여부를 판단하기 위한 구조해석을 수행하였다.
Fig. 2에 열-구조 연계해석을 위한 경계조건을 도시하였다. 해석은 대칭성을 고려하여 모델의 1/2에 대해 수행하였고, ANSYS Workbench를 사용하였다. 열전달 해석을 위해서는 히터가 삽입되는 원통면의 온도를 260oC로 고정하였고, 외측면에는 상온(22oC)에서의 대류열전달 계수(5 W/m2-K)를 적용하였다. 초기온도는 22oC로 설정하였고, 부품간의 열접촉 저항을 고려하기 위해 접촉면에 1000W/m2-K의 열접촉 전도도를 부여하였다.12 구조해석을 위해서는 압출부 상면의 변위(Z 방향) 및 대칭면 수직변위를 구속하였고, 열전달 해석으로부터 얻어진 온도분포를 열하중으로 부과하였다. 또한 출력 과정에서 외부하중 작용에 의한 배럴부의 안전성 여부를 판단하기 위해 노즐 끝단에 10 N의 하중을 횡방향(-Y 방향)으로 부과하였다. 각 부품의 기계적, 열적 물성은 Table 1에 제시된 값을 사용하였으며, 부품간 접촉부의 수직변위를 구속하였다.
Fig. 3에 열전달 해석 결과를 도시하였다. Fig. 3(a)는 정상상태 도달 시점의 온도분포이며, 가열부는 전반적으로 220oC 이상의 온도를, 방열부는 80oC 이하의 온도를 보임을 확인할 수 있었다. 이러한 온도의 변화는 배럴부에서 급격히 발생되는 것으로 확인되었는데, 배럴부 최하단과 최상단 온도가 각각 233oC, 77oC에 해당하여 156oC의 온도차이를 보였으며, 이러한 경향은 Fig. 3(c)에 도시한 열화상카메라 측정 결과와 유사함을 확인할 수 있었다.
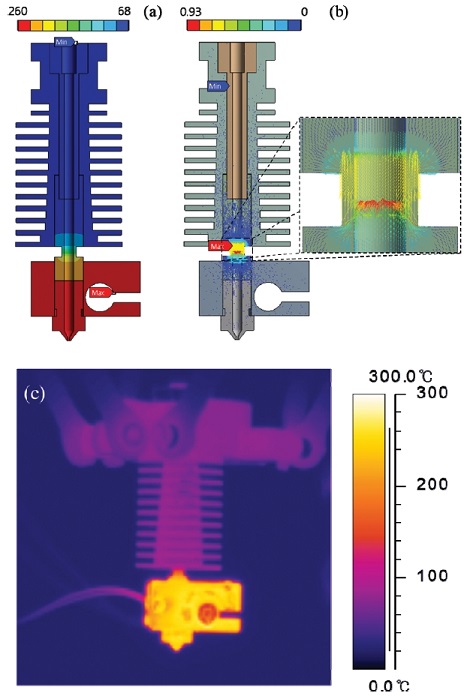
Thermal FE analysis results: (a) Temperature (unit: oC), (b) Heat flux (unit: W/mm2), (c) Measured temperature distribution (unit: C)13
배럴부에서의 국부적인 온도 변화의 원인을 고찰하기 위해 대칭면에서의 열속(Heat Flux) 분포를 Fig. 3(b)에 도시하였으며, 중앙에서의 단면감소부에서 열속이 집중되어 온도구배가 급증한 것으로 확인되었다. 즉 배럴 중앙부의 두께를 국부적으로 감소(잔여 두께 0.5 mm)시킴으로써 열을 효과적으로 차단할 수 있는 것으로 판단된다.
Fig. 4에 구조해석 결과를 도시하였다. Fig. 4(a)는 순수 열응력 분포이며, 배럴부 하단 조립부에서 최대응력(SS303: 287, AA6061: 217 MPa)이 발생하였다. 이는 배럴부 재료인 SS303과 가열블록 재료인 AA6061간의 열팽창계수 차이로 인한 응력이며, 각각 재료의 항복응력(SS303: 415 MPa, AA6061: 370 MPa) 이하의 값으로 나타났다. 10 N의 하중이 추가로 부과된 경우(Fig. 4(b))의 최대응력은 SS303이 305, AA6061이 268 MPa까지 증가하는 것으로 나타났다. 해당 위치는 접촉부위로 파손 위험은 적은 반면 두께가 얇아 파손 위험이 높은 배럴 중앙 열차단부(구간 B-B’)에서도 국부적으로 응력이 집중되는 것으로 나타났다. 최대응력은 268 MPa로 항복응력 이하로 나타나 안전한 것으로 판단되나, 국부적으로 응력이 집중되는 점을 감안할 때 하중 증가시 소성변형이 발생할 우려가 있어 추가적이 고찰이 필요한 것으로 판단된다.
2.3 열차단부 두께에 따른 열특성 비교
열차단부에서 발생되는 국부적인 응력 집중 현상을 추가적으로 고찰하기 위해 열차단부의 두께를 변화시키며 해석을 수행하였다. 열차단부 두께는 기존 두께(0.5 mm)에서 1.5 mm까지 0.25 mm씩 증가시키며 해석을 수행하였다.
Fig. 5(a)에 열차단부 두께에 따른 배럴 내측면(Fig. 4(b)의 경로 A-A’)의 온도분포를 그래프로 비교하였다. 배럴부 하단(A 지점) 온도는 전반적으로 240oC 내외에서 시작하여 서서히 감소하다 열차단부가 시작되는 5 mm 지점에서 기울기가 증가하며, 이후 열차단부가 끝나는 7 mm 지점에서 기울기가 다시 감소함을 알 수 있다. 열차단부에서의 온도 강하는 두께 0.5, 0.75 mm인 경우 급격하게 나타났으며, 두께가 1 mm 이상인 경우는 상대적으로 온도 강하가 완만한 점을 알 수 있다. 또한 본 해석의 기준 필라멘트인 ABS 수지의 유리전이 온도가 110oC인 점을 감안할 때, 배럴부 상단 내측에서 필라멘트의 연화를 방지하기 위한 열차단부의 두께는 1 mm 이하로 유지해야 할 것으로 판단된다.
Fig. 5(b)에 열차단부 두께에 따른 열차단부 외측면(Fig. 4(b)의 경로 B-B’)의 등가응력 분포를 그래프로 비교하였다. 전반적으로 열차단부 상단(B’ 지점)에서 최대 응력이 발생하였으며, 열차단부 두께가 증가할수록 응력이 감소됨을 알 수 있다. 특히 두께가 0.5 mm인 경우(268 MPa)와 두께가 0.75 mm인 경우(169 MPa)간의 편차가 가장 크게 나타남을 알 수 있는데, 상기 결과로부터 두께 0.75 mm인 경우가 열차단 효과 및 구조적 안전성을 종합적으로 고려할 때 가장 우수함을 알 수 있다.
3. 고온 압출부의 설계 및 열특성 수치해석
3.1 고온 압출부의 설계 및 해석
2장에서 기술한 압출부는 필라멘트의 원활한 이송을 위해 내부에 테플론 관(Teflon Tube)이 삽입되는 구조이다. 상기 테플론 관의 허용 온도는 250oC로 2장에서 사용한 온도경계조건(ABS 필라멘트 기준, 히터온도 260oC)에서 최대 150oC의 온도를 보여 연화가 발생하지 않는 것으로 나타났다. 그러나 가열온도가 300oC 이상인 엔지니어링/슈퍼엔지니어링 플라스틱 필라멘트를 사용할 경우에는 테플론이 연화되어 원활한 필라멘트 이송이 이루어지지 않을 가능성이 있다.
본 연구에서는 엔지니어링/슈퍼엔지니어링 플라스틱의 고온 압출을 위해 테플론을 사용하지 않고 금속 재질로 필라멘트 이송경로를 형성하도록 설계를 변경하였다. Fig. 6에 금속관을 삽입한 고온 압출부의 형상을 도시하였으며, 이때 금속관은 상대적으로 열전도율이 낮은 스테인레스강(SS 303)으로 사용하였다. 금속관의 외경은 4 mm, 내경은 2 mm로 설계하였고, 결과적으로 관의 두께는 1 mm에 해당한다.
Fig. 7에 열전달 해석 결과를 도시하였다. Fig. 7(a)는 정상상태 도달 시점의 온도분포이며, 방열부의 최소온도가 90.4oC로 나타나 Fig. 3(a)의 해석결과(최소온도 68oC)에 비해 22oC 정도 높게 나타났다. 또한 최대 열유속(0.33W/mm2)도 Fig. 3(b)의 해석결과(최대 열유속 0.93 W/mm2)의 35% 수준으로 나타났다. 이는 스테인레스 강관의 열전도도(16.3 W/m-K)가 테플론(0.35 W/m-K) 보다 높고 별도의 열차단부가 없기 때문으로 분석된다.
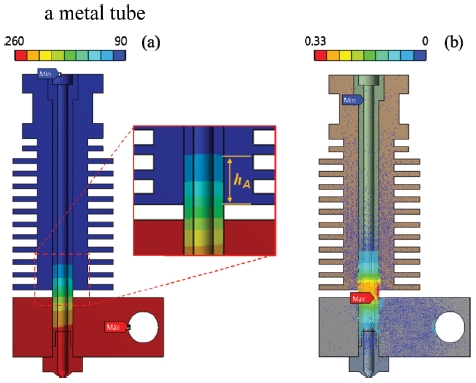
Analysis results for high temperature extruder: (a) Temperature (unit: oC), (b) Heat flux (unit: W/mm2)
또한 금속관 내부에서 필라멘트의 연화 발생 가능성을 정량적으로 비교하기 위해 금속관 내측의 온도가 필라멘트의 유리전이 온도(110oC) 이상으로 나타내는 구간에 대해 Fig. 7(a)의 확대도에 도시한 바와 같이 방열부 바닥면을 기준으로 고온구간 범위(hA)를 정의하여 비교하였다. Fig. 7(a)의 경우 고온구역이 5.0 mm로 나타나 Fig. 3(a)에 도시한 기존 노즐의 해석결과(2.54 mm)에 비해 고온구간이 증가함을 알 수 있다.
3.2 금속관 두께에 따른 열특성 수치해석
금속관 두께에 따른 열특성 고찰을 위해 두께를 0.5 mm에서 1.75 mm까지 0.25 mm씩 증가시키며 해석을 수행하였다. 두께 변화시 관의 내경은 2 mm로 고정시킨 상태에서 외경을 변화시켰으며, 이에 상응하도록 방열부의 내경을 변화시켰다. 두께에 따른 열차단 효과와 구조적 안전성을 위해 열-구조 연계해석을 수행하였으며, 해석 조건은 2.2절과 동일하게 설정하였다.
Fig. 8(a)에 금속관 두께에 따른 내측면(Fig. 6의 경로 C-C’)의 온도분포를 그래프로 비교하였다. 방열부 하단(C 지점)을 기준으로 5 mm까지는 온도는 빠른 속도로 감소하다 점차적으로 완만해지며 10 mm 지점 이후 균일해짐을 알 수 있다. ABS 수지의 유리전이 온도가 110oC인 점을 감안할 때, 필라멘트의 연화를 방지하기 위해 두께를 1 mm 이하로 유지해야 할 것으로 판단된다.
Fig. 8(b)에 금속관 두께에 따른 외측면(Fig. 6의 경로 D-D’)의 등가응력 분포를 비교하였다. 해당 경로는 크게 가열부 삽입부(0-2 mm), 연결부(2-3.9 mm), 방열부 삽입부(3.9-5.8 mm)의 3 구간으로 구분할 수 있는데, 두께가 0.5 mm인 경우를 제외하면 대부분 방열부 경계부분(3.9 mm 지점)에서 최대 응력이 발생함을 알 수 있다. 반면 두께 0.5 mm인 경우 연결부(2 mm 지점)에서 최대 응력(178 MPa)이 발생하여 구조적으로 취약함을 확인할 수 있었다.
Table 2에 금속관 두께에 따른 경로 C-C’에서의 온도편차(ΔTC), 경로 D-D’에서의 최대등가응력(smax), 고온구역 범위(hA)를 종합적으로 비교하였다. 두께가 0.75, 1.0 mm일 경우 고온구역 범위가 5 mm 이하로 온도차단 효과가 높으면서도 응력이 크게 감소되어 구조적 안전성을 보장할 수 있음을 알 수 있었다. 반면 두께가 1.5 mm 이상인 경우에는 내측면 전체가 110oC 이상으로 나타나 필라멘트가 이송중 연화될 것으로 판단된다.
3.3 방열핀 개수에 따른 열특성 수치해석
Fig. 6에 도시한 바와 같이 방열부에 11개의 방열 핀(Fin)이 형성되어 가열부로부터 전달되는 열을 방출하는 역할을 한다. 핀의 개수가 많을수록 방열효과가 우수하나, 방열부의 길이가 길어져 공간에 제약을 받는 문제가 발생한다. 본 연구에서는 압출부의 열전달 해석을 통해 방열부 핀의 개수에 따른 방열효과에 대해 고찰하고자 한다. 이를 위해 핀 개수를 감소시키면서 열전달 해석을 수행하여 방열효과의 변화를 비교하였다. 이때 금속관 두께는 3.2절의 결과를 바탕으로 1.0 mm로 설정하였으며, 경계조건은 앞서 수행한 열전달 해석과 동일하게 부여하였다.
Fig. 9에 핀의 개수에 따른 정상상태 온도분포를 비교하였고, 전반적으로 핀의 개수가 줄어들수록 방열부의 온도가 상승함을 알 수 있다. Table 3에 각각의 경우에 대한 경로 C-C’에서의 온도를 정량적으로 비교하였다. 결과를 보면 핀이 6개 이하인 경우에는 방열부 내측면의 최소 온도(115.8oC)가 ABS 소재의 유리전이 온도(110oC) 이상으로 상승하여 필라멘트의 원활한 이송이 어려워질 것으로 판단된다. 상기 결과로부터 핀의 개수는 8개 이상으로 유지되어야 할 것으로 판단되며, 핀의 개수를 8개로 유지할 경우 방열부의 길이는 기존 설계안(11개의 핀) 대비 7.5 mm 정도 감소될 수 있는 것으로 나타났다.
3.4 필라멘트 재료에 따른 열특성 수치해석
상기 결과를 토대로 필라멘트 재료를 변경시키며 열-구조 연계해석을 실시하였다. 기존의 ABS 이외에 엔지니어링 플라스틱인 Polycarbonate (PC), 슈퍼엔지니어링 플라스틱인 Polyetherimide (PEI)을 사용하여 프린팅을 수행하는 것으로 가정하고 해석을 진행하였다. 해석시 PC와 PEI의 유리전이 온도(Tg)를 감안하여 각각의 압출부 가열 온도(Tm)를 300oC와 350oC로 설정하였다.14 모든 경우에 대해 금속관의 두께는 1.0 mm로, 핀의 개수는 8개로 설정하였다.
Fig. 10에 3가지 수지에 대한 온도분포 결과를 비교하였다. 각각의 경우 청색으로 표현되는 범위를 최소온도에서 유리전이온도(PC: 150oC, PEI: 218oC) 사이로 설정하였고, 따라서 방열부 내에서 청색 이외의 색깔로 표시되는 부분은 고온구간으로 볼 수 있다. 결과를 보면 PC와 PEI의 경우 가열 온도가 높음에도 불구하고 수지의 유리전이 온도가 높아 고온구간의 범위가 오히려 감소함을 알 수 있다.
Table 4에 해석결과를 정량적으로 비교하였다. 각각의 경우 방열부 내측의 온도편차(ΔTC)는 유사한 수준으로 나타난 반면 고온구간 범위는 ABS에 비해 PC와 PEI가 오히려 감소되어 제안된 금속관 압출부의 설계사양을 적용할 때 필라멘트의 고착현상 없이 원활이 소재의 이송 및 프린팅이 가능할 것으로 판단된다. 한편 ABS 수지의 경우 최대응력이 87.6 MPa로 나타나 11개의 핀을 적용한 3.2절의 결과(90.5 MPa)에 비해 소폭 감소하였는데, 이는 핀의 개수 감소에 따른 온도 증가로 인해 열응력이 증가하는 효과와 핀의 길이가 짧아짐에 따른 굽힘모멘트 감소가 복합적으로 작용한 결과로 판단된다. PC, PEI의 경우도 전반적으로 90 MPa 이하의 최대응력을 보여 주어진 범위 내에서 안전하게 사용할 수 있을 것으로 판단된다.
4. 결론
본 연구에서는 엔지니어링/슈퍼엔지니어링 플라스틱 프린팅을 위한 고온 압출부 개발을 목적으로 열-구조 연계 수치해석을 실시하였으며, 아래와 같은 결론을 도출하였다.
(1) 기존 제품을 대상으로 열-구조 연계해석을 수행한 결과 열차단부 두께를 감소시킬수록 온도 구배가 크게 나타나 열차단 효과가 향상되는 반면 응력집중이 크게 나타나 적정 두께(0.75 mm)의 설정이 필요함을 확인하였다.
(2) 고온 출력을 위한 급속관 압출부를 설계하고 수치해석을 수행한 결과 0.75-1.0 mm 범위의 두께에서 온도차단 효과가 높으면서도 구조적 안전성을 보장할 수 있음을 알 수 있었다.
(3) 방열핀 개수에 따른 해석을 수행한 결과 핀의 개수를 기존 11개에서 8까지 감소할 수 있으며, 이때 방열부의 길이는 기존 설계안 대비 7.5 mm 정도 감소될 수 있는 것으로 확인되었다.
(4) 확정된 설계사양(금속관 두께 1 mm, 8핀)을 적용하여 수지의 종류를 엔지니어링 플라스틱(PC), 슈퍼엔지니어링 플라스틱(PEI)으로 확대하여 수치해석을 수행한 결과 온도차단 효과 및 구조적 안전성을 보장할 수 있는 것으로 확인되었다.
상기 결과를 종합하였을 때 본 연구에서 수치해석을 통해 확정한 설계안으로 엔지니어링/슈퍼엔지니어링 플라스틱 필라멘트의 프린팅이 가능할 것으로 판단되며, 이를 반영하여 고강도/고내열성 제품 제작이 가능한 산업용 압출적층형 프린터 개발에 활용하고자 한다.
NOMENCLATURE
E : | Elastic modulus |
ν : | Poisson’s ratio |
a : | Thermal expansion coefficient |
k : | Thermal conductivity |
Tg : | Glass transition temperature of polymer |
Tm : | Heating temperature of the extruder |
hA : | Length of the high temperature region |
Acknowledgments
본 논문은 본 연구는 산업통상자원부 산업기술혁신사업(장비연계형 3D 프린팅 소재 기술개발사업, 과제번호: 10062348)의 지원으로 수행된 결과로 관계자 여러분께 감사드립니다. 또한 압출부 제작과 실험에 도움을 주신 전자부품연구원의 홍영규 박사님과 임태현 연구원께 감사드립니다.
REFERENCES
- Ahn, D. G. and Yang, D. Y., “Principle of Rapid Prototyping and Its Trends,” J. Korean Soc. Precis. Eng., Vol. 22, No. 10, pp. 7-16, 2005.
-
Campbell, I., Bourell, D. and Gibson, I., “Additive Manufacturing: Rapid Prototyping Comes of Age,” Rapid Prototyping Journal, Vol. 18, No. 4, pp. 255-258, 2012.
[https://doi.org/10.1108/13552541211231563]
- Stampfl, J. and Hatzenbichler, M., “Additive Manufacturing Technologies,” Springer, 2010.
-
Turner, B. N. and Gold, S. A., “A Review of Melt Extrusion Additive Manufacturing Processes: I. Process Design and Modeling,” Rapid Prototyping Journal, Vol. 20, No. 3, pp. 192-204, 2014.
[https://doi.org/10.1108/RPJ-01-2013-0012]
-
Jones, R., Haufe, P., Sells, E., Iravani, P., Olliver, V., et al., “RepRap - The Replicating Rapid Prototyper,” Robotica, Vol. 29, No. 1, pp. 177-191, 2011.
[https://doi.org/10.1017/S026357471000069X]
-
Turner, B. N. and Gold, S. A., “A Review of Melt Extrusion Additive Manufacturing Processes: II. Materials, Dimensional Accuracy, and Surface Roughness,” Rapid Prototyping Journal, Vol. 21, No. 3, pp. 250-261, 2015.
[https://doi.org/10.1108/RPJ-02-2013-0017]
- Fischer, F., “Thermoplastics: The Best Choice for 3D Printing,” Stratasys, 2011.
- Kwon, S. H., Kim, M. K., Lee, I. H., and Cho, H. Y., “Fabrication Characteristics of Extruded Material for FDM Nozzle Shape,” Proc. of KSPE Spring Conference, pp. 33-34, 2016.
-
Kim, K. E., Park, K., and Lee, C., “A Study on Development of Three-Dimensional Chocolate Printer,” J. Korean Soc. Precis. Eng., Vol. 34, No. 4, pp. 293-298, 2017.
[https://doi.org/10.7736/KSPE.2017.34.4.293]
- E3D-Online Limited, https://e3d-online.com/v6, (Accessed 9 FEB 2018)
- Lee, H. J., Shin, D. Y., Lim, T. H., Hong, Y. K., and Park, K., “Finite Element Analysis of Thermal Characteristics of Extruder of FDM 3D Printer,” Proc. of KSPE Autumn Conference, p. 76, 2017.
- Bejan, A. and Kraus, A. D., “Heat Transfer Handbook,” John Wiley & Sons, 2003.
- Lim, T. H. and Hong, Y. K., “Development of Full-Metal High-Temperature Extruder for Engineering Plastic 3D Printing,” Proc. of KSPE Autumn Conference, pp. 73-74, 2017.
- Stratasys, http://www.stratasys.com/materials/fdm, (Accessed 9 FEB 2018)