
3차원 회로장치 제작을 위한 다중재료 복합 부가가공 공정
Copyright © The Korean Society for Precision Engineering
This is an Open-Access article distributed under the terms of the Creative Commons Attribution Non-Commercial License (http://creativecommons.org/licenses/by-nc/3.0) which permits unrestricted non-commercial use, distribution, and reproduction in any medium, provided the original work is properly cited.
Abstract
Recently, various attempts have been made to apply the additive manufacturing technology directly to fabricate a product. In this regards, the industry is focusing on the multi-material additive manufacturing technology that can processes multiple materials simultaneously. This study is about the fabrication of a 3-dimensional circuit device (3DCD), based on the multi-material additive manufacturing technology, which is combination of the material extrusion and the direct writing processes. The multi-material additive manufacturing system was developed based on the commercial multi-head FDM system. In addition, a contact type nozzle for the dispensing of the conductive material in the direct writing process is proposed. The 3-dimensional circuit device in which circuit elements are arranged on several layers was fabricated successfully, based on the presented multi-material additive manufacturing system.
Keywords:
Additive manufacturing, Multi-material, 3-dimensional circuit device, Material extrusion, Direct writing키워드:
부가가공, 다중재료, 3차원 회로장치, 재료압출, 직접주사1. 서론
부가가공(Additive Manufacturing) 기술은 절삭가공에 비해서 제품을 쉽게 제작할 수 있는 특징을 가지고 있다. 하지만 일반적으로 부가가공 기술은 성형공정에 따라서 한 가지 혹은 유사한 성질을 갖는 재료만 사용이 가능하다. 따라서 기존에는 부가가공기술이 실제 사용 가능한 제품의 제작 보다는 주로 시제품 제작에 적용되어 왔으나,1 최근 들어 이를 직접 제품제작에 적용하는 것에 대한 관심이 증가되고 있다. 특히 다양한 특성을 갖는 재료를 동시에 성형할 수 있는 부가가공 기술은 별도의 부착이나 조립 공정을 필요로 하지 않기 때문에 제품제작에 직접 적용할 수 있을 것으로 기대된다.
다양한 부가가공 기술 중 FDM (Fused Deposition Modeling) 공정과 FFF (Fused Filament Fabrication) 공정은 재료압출 (Material Extrusion) 기술의 하나로서, 필라멘트 형상의 열 가소성 수지 재료를 녹여 압출함과 동시에 압출 노즐의 위치를 제어하여 3차원 형상을 제작한다. 이 공정은 시스템이 비교적 간단하고 재료를 쉽게 구할 수 있기 때문에 널리 사용되고 있다. 한편, 액체재료를 이용하는 직접주사(Direct Writing) 기술은 재료가 토출되는 노즐의 위치를 제어하여 원하는 패턴을 성형할 수 있다.2,3 따라서 액체상태의 전도성 재료를 직접주사 기술로 토출하여 전자회로를 구성하는 것이 가능할 것으로 기대된다.4 FDM/FFF 공정에 많이 사용되는 재료는 ABS 및 PLA로서 비전도성 재료이다. 따라서 비전도성 재료를 사용하는 FDM/FFF 공정과 전도성 재료를 사용하는 직접주사 기술을 융합한 다중재료 복합 부가가공 공정을 적용하면 전자회로의 제작이 가능할 것으로 기대된다. 이는 평면형태만 가능한 기존의 PCB (Printed Circuit Board)와는 다르게 3차원으로 회로를 구성 할 수 있다는 특징을 갖는다.5-9
본 연구는 FDM/FFF 공정과 직접주사 기술이 융합된 다중재료복합 부가가공 공정 개발을 통해 3차원 회로장치(3-Dimensional Circuit Device, 3DCD)를 제작하는 것에 대한 것이다. 본 연구를 통해서 3차원 회로장치 제작에 적용할 수 있는 FDM/FFF 공정과 직접주사 기술이 융합된 다중재료 복합 부가가공 공정을 제안하고, 이를 구현하기 위한 시스템을 개발하였다. 또한 직접주사 기술에서 전도성 재료의 토출을 위한 접촉식 개폐형 노즐을 제안하였다. 개발된 다중재료 복합 부가가공 시스템을 이용하여 여러 층에 회로소자가 배열된3차원 회로장치를 성공적으로 제작하였다.
2. 다중재료 복합 부가가공 시스템
2.1 다중재료 복합 부가가공 공정
Fig. 1은 3차원 회로장치 성형을 위해 본 연구에서 제안하는 다중재료 복합 부가가공 공정의 모식도이다. 구체적인 공정은 다음과 같으며, (2)-(4)의 공정을 반복하여 최종적으로 3차원 회로장치를 제작할 수 있다.
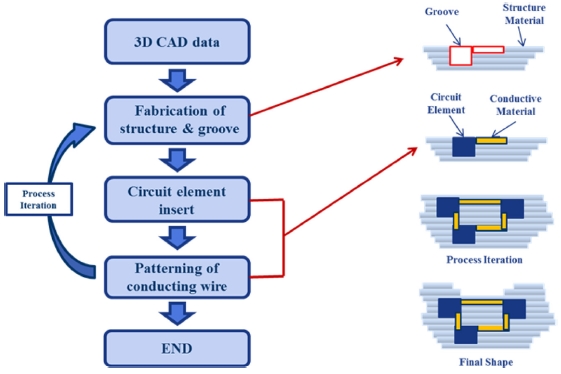
Schematic drawing of multi-material additive manufacturing process for 3-dimensional circuit device fabrication
(1) CAD 데이터 제작: CAD 소프트웨어를 이용하여 전체적인 구조물을 설계한다. FDM/FFF 공정으로 제작되는 구조물은 3차원 회로장치의 형상을 구성할 뿐만 아니라 절연체 역할을 동시에 하게 된다. 만들어진 CAD 데이터에는 회로소자의 삽입 및 회로도선 성형을 위한 홈이 3차원으로 배치된다.
(2) 구조물 성형: CAD 데이터에 따라 FDM/FFF 공정의 재료압출 헤드를 통해서 재료가 압출되어 구조물이 층층이 성형된다. 이때 회로소자의 삽입 또는 도선이 성형될 단면의 성형이 완료되면 재료압출 헤드의 동작을 정지시킨다.
(3) 회로소자 삽입 및 도선 성형: 만들어진 구조물 단면의 홈에 회로소자를 삽입한다. 또한 직접주사 장치를 이용하여 전도성재료를 토출 하여 회도선을 성형하고 적절한 방법으로 경화시킨다. 이를 통해 회로소자들은 전기적으로 연결된다.
(4) 구조물 성형 및 회로소자의 층 방향 연결: 회로소자가 삽입되고 회로도선의 성형이 완료되면 다음 홈이 위치하는 단면까지 구조물을 계속 성형한다. 한편 3차원 회로장치의 회로소자는 여러 단면에 배열될 수 있으며 따라서 단면들 사이의 전기적 연결도 필요하다. 이를 위해서 필요한 곳에 수직방향의 구멍형상을 CAD 모델에 만들고, 만들어진 구멍에 전도성 핀을 삽입하거나 액체상태의 전도성 재료를 주입 후 경화시킨다. 본 연구에서는 전도성 재료로 만들어진 핀을 구멍에 삽입하여 단면들 사이의 전기적 연결을 가능하게 하였다.
2.2 다중재료 복합 부가가공 시스템
Fig. 2는 3차원 회로장치 제작을 위해 본 연구에서 개발된 다중 재료 복합 부가가공 시스템의 사진이다. 이 시스템은 오픈 소스 기반의 상용 FDM/FFF 장비인 BFB-300010을 개조하여 제작되었다. 이 장비는 최대 100 × 100 × 200 mm 크기의 구조물을 성형할 수 있으며, 지름 0.5 mm의 열가소성 수지 압출 헤드가 2개 장착된 다중헤드 시스템이다. 본 연구에서는 열가소성수지 압출 헤드 하나를 제거하고 여기에 직접주사 헤드를 장착하여 다중재료 헤드(Multi-Material Head)를 제작하였다. 따라서 구조물의 제작 시에는 열가소성 수지 압출 헤드를 통해서 재료가 공급되며, 회로도선의 성형이 필요한 곳에는 직접주사헤드를 통해서 재료가 공급된다. 실험에 사용된 열가소성 수지는 ABS 이며, 전도성 재료는 Elcoat P-100(CANS 사)이다. Elcoat P-100은 바인더와 전도성 입자가 혼합된 액체상태의 재료로서 상온에서 경화가 가능하기 때문에 별도의 가열 경화 공정이 필요하지 않다.
다중재료 헤드는 X-축 스테이지에 부착되며, X-축 스테이지는 Y-축 스테이지에 부착되어 있기 때문에 X-Y 평면에서 이송된다. 한편 Z-축 스테이지에는 조형판이 부착되어 있으며, 조형판의 위치제어를 통해 성형되는 구조물의 적층두께가 결정된다. 한편 BFB-3000에서 제거된 압출헤드의 구동을 위한 제어신호를 다중 재료 토출 헤드의 동작을 위한 스텝모터 제어신호로 이용하였으며, 나머지 제어시스템과 제어 소프트웨어는 그대로 이용하였다. 제어시스템에서 작성된 G 코드에 의해서 구동 시스템, 열가소성 수지 압출 헤드 및 직접주사헤드가 동작된다. 따라서 G 코드에는 구조물의 성형정보뿐만 아니라 전도성 재료의 성형정보 또한 포함된다.
Fig. 3(a)는 열가소성수지 압출헤드와 직접주사헤드가 통합된 다중재료 헤드의 사진이다. 열가소성수지 압출헤드는 내부에 위치한 스텝모터의 회전에 의해서 재료가 가열노즐로 공급되어 용융 압출된다. 한편, 본 연구에서는 전도성재료의 토출을 위해 직접주사헤드를 제작하고 이를 다중재료 헤드에 장착하였다. Fig. 3(b)의 직접주사헤드 스텝모터가 회전하면 스텝모터의 축에 타이밍벨트 시스템으로 연결된 LM 나사(LM Screw)가 회전하여 압축부(Pressing Part)가 직선 이송되고 압축부는 주사기의 피스톤을 밀어주어 주사기 내부의 전도성재료가 토출 된다.11 한편, 주사기에 의해 토출 되는 전도성 재료의 정밀한 유량제어와 토크의 증가를 위해서 전체 감속비가 1 : 20.25인 두 개의 타이밍벨트로 감속하였다.
한편, 직접주사헤드에서 토출 되는 전도성재료의 유량(Q, mm3/min)은 식(1)과 같이 계산된다.
(1) |
여기서 D는 주사기의 내경(mm), R은 스텝모터의 회전수(rpm), s는 타이밍벨트 시스템에 의한 감속비, 그리고 L은 LM 나사의 리드(mm)이다.
제작된 직접주사헤드의 성능을 평가하기 위해서 스텝 모터의 회전속도를 4-12 rpm으로 2 rpm씩 증가시키면서 주사기에서 토출 되는 액체재료의 유량측정 실험을 수행하였다. 내경 20 mm인 주사기에 증류수를 주입하고 각 모터의 회전속도에서 1시간동안 토출된 증류수의 질량을 측정하여 유량을 계산하였다. 한편, LM 나사의 리드는 2 mm이다. Fig. 4는 실험결과를 식(1)을 이용한 계산결과와 함께 비교한 것이다. Fig. 4에서 알 수 있듯이 모터의 회전속도에 따라 토출 되는 액체의 유량은 계산결과와 잘 일치하며 선형적으로 비례하는 것을 알 수 있다. 따라서 직접주사시스템의 적절한 유량제어가 가능하다.
2.3 접촉식 개폐형 노즐
직접주사장치는 토출부에 지름이 작은 노즐을 장착하여 토출되는 액체가 일정한 선폭을 갖도록 하는 것이 일반적이다.5,7 한편, 본 연구에서 개발된 다중재료 복합 부가가공 시스템은 고온의 열가소성수지 압출헤드와 직접주사헤드가 하나의 헤드에 함께 장착되어 있다. 따라서 압출헤드에서 발생하는 열은 인접한 직접주사헤드에 전달되며, 따라서 직접주사헤드 노즐 출구의 전도성재료가 열에 의해 경화되어 막히는 현상이 발생한다. 또한 가압장치를 이용해서 액체상태 전도성재료를 토출 할 때 시작과 끝 지점에서 선폭이 일정하지 않은 현상이 발생하는 경우가 많다. 이에 본 연구에서는 기저판과 접촉에 의해서만 열려 액체상태의 전도성 재료가 토출되는 개폐형 노즐을 개발하여 이를 직접주사헤드의 주사기에 부착하였다(Fig. 5).
Fig. 5(a) 우측 그림과 같이 노즐 팁이 기저판에 닿지 않으면 노즐 내부와 노즐 팁의 개폐부는 스프링에 의해서 밀착되어 닫힌 상태가 유지된다. 한편 Fig. 5(b)와 같이 노즐 팁이 기저판에 닿게 되면 밀착부가 열리게 되어 내부의 전도성재료가 노즐 팁을 타고 흘러내리게 된다.12 이때 전도성 재료가 토출 되는 기저판의 표면이 고르지 않아 노즐 팁의 상하 움직임이 생기더라도 노즐 내부에서 전도성 재료가 흘러나오는 단면은 항상 일정하게 유지되기 때문에 항상 일정한 유량이 흘러내리게 된다. 한편 노즐 팁의 끝부분은 기저판의 손상을 방지하기 위해서 원형으로 제작되었으며, 스프링 정수는 1 N/mm이다.
3. 다중재료 복합 부가가공 공정에서 전도성 재료의 토출 성형 특성
FDM/FFF 공정은 가열 압출된 열가소성 수지로 단면을 만들기 때문에 상대적으로 표면 거칠기가 좋지 않다. 또한 Fig. 6(a)와 같이 재료를 절약하고 공정시간을 단축하기 위해서 단면을 모두 채우지 않고 그물망 형태로 성형하는 것이 일반적이다. 따라서 여기에 회로를 구성하기 위한 전도성 재료가 토출 되면 재료의 일부가 스며들게 되어 전기적 단선의 원인이 될 수 있다.
FDM/FFF 공정에서 용융 압출된 열가소성수지는 노즐 끝단과 기저판 사이에서 적층두께만큼 압착된다. 따라서 압출량이 같을 때 적층두께가 작게 되면 압착된 재료의 폭이 더 넓어지게 된다. Fig. 6(b)는 적층두께를 Fig. 6(a)의 반인 125 μm로 하였을 때 만들어진 구조물 단면의 광학현미경 및 전자현미경 사진이다. 이 경우 압착된 재료의 폭이 넓어지게 되어 그물망 형태가 없어지게 되어 주사된 액체상태의 전도성 재료가 스며들지 않게 된다. 따라서 구조물 재료 성형을 위한 공정변수를 전도성재료가 스며들지 않도록 설정하여 틈새가 없는 면이 성형되어야만 전기적인 결선이 원활하게 이루어질 수 있음을 알 수 있다. 한편, Fig. 6의 구조물들은 층 두께를 제외하고는 BFB-3000 구동소프트웨어의 기본 설정을 변경 없이 동일하게 적용하여 성형되었다.
직접주사 공정을 통해서 토출 되어 경화된 전도성 재료가 전기적으로 안정된 도선의 기능을 수행하려면 일정한 선폭을 갖도록 해야 한다. 토출 성형된 액체재료의 선폭은 노즐의 이송속도와 주사유량에 따라서 달라지는 것으로 알려져 있다.13 따라서 본 연구에서는 노즐이 부착된 직접주사 헤드의 이송속도와 전도성 재료의 주사유량에 따른 전도성재료의 선폭을 파악하는 실험을 수행하였다. Fig. 7은 직접주사 헤드의 이송속도를 10-25 mm/sec로 5 mm/sec씩 증가시키고, 전도성 재료 토출의 유량을 15.08, 22.62, 30.16 및 37.7 ml/hr로 변화시키면서 성형된 전도성 재료의 선폭을 광학현미경으로 관측한 결과를 정리한 그래프이다. Fig. 7에서 알 수 있듯이 노즐의 이송속도가 15mm/s일 때 토출유량에 따라 성형되는 전도성 재료의 선폭 변화가 가장 선형적인 결과를 보인다.
다중재료 복합 부가가공 공정으로 제작되는 3차원 회로장치에서 도선은 구조물 내부 단면에 성형되게 되며, 그 위에 FDM/FFF 공정으로 계속해서 구조물이 성형된다. 이때 구조물의 단면에 액체상태의 전도성 재료를 토출 성형하는 것은 두 가지 방법이 가능하다. 첫 번째는 단면에 홈을 성형하고 여기에 전도성 재료를 토출하는 것으로서, 전도성 재료의 선폭제어가 쉬우나 전도성 재료를 토출하는 노즐의 경로제어가 좀 더 정밀해야 한다. 두 번째는 홈을 성형하지 않고 구조물 단면에 직접 전도성 재료를 토출 성형하는 것으로서, 구조물 설계가 용이하지만 선폭제어가 상대적으로 어렵다.14 이에 적합한 토출 성형전략을 파악하기 위한 실험적 연구를 수행하였다.
즉, Figs. 8(a)와 8(b)의 위쪽 그림들과 같이 단면에 폭 1 mm 깊이 0.5 mm의 홈이 성형된 단면과 홈이 성형되지 않은 단면을 가진 구조물을 각각 제작하였다. 이때 전도성 재료가 구조물 내부로 스며드는 것을 방지하기 위해서 층 두께는 125 μm로 하였다. 그리고 여기에 전도성재료를 토출 하여 도선을 성형한 후 다시 그 위에 구조물을 한층 더 성형한 시편을 각각 제작하였다. 제작된 시편에 성형된 각 도선의 양 끝에 만들어진 단자에 디지털 멀티미터를 연결하여 전기적 결선을 파악하였다. Fig. 8(a) 아래 사진은 홈이 성형된 단면에 도선을 성형한 시편이다. 측정 결과 모든 단자들의 전기적 결선이 양호하였다. Fig. 8(b) 아래 사진은 홈이 성형되지 않은 단면 위에 도선을 성형한 시편의 사진이다. 측정 결과 4-4’ 단자가 전기적으로 연결되지 않았으며 3-4’은 합선이 되었다. 또한 일부 표면이 손상되어 도선재료가 시편 표면에 나타난 것이 관측되었다. 이는 직접주사공정으로 성형된 회로도선 위에 높은 온도를 갖는 열가소성 수지 재료가 압출되면서 회로도선이 손상된 것에 기인한다. 이상의 결과로 FDM/FFF 공정 기반의 다중재료 복합 부가가공 공정에서 액체상태의 전도성 재료를 토출하여 도선을 성형하기 위해서는 단면에 홈을 포함한 구조물을 제작하는 것이 유리함을 알 수 있다.
4. 3차원 회로장치의 제작
개발된 다중재료 복합 부가가공 시스템을 이용해서 단일 공정으로 스위치의 동작에 의해 멜로디가 재생되는 3차원 회로장치를 제작하였다. 제작된 3차원 회로장치는 회로이며. Fig. 9는 회로도이며, 본 연구에서는 이를 분석하여 3차원 형태로 재구성하였다.
Fig. 10은 제작된 3차원 회로장치의 각 단면에 회로소자와 도선이 성형된 것과 완성된 장치의 사진이다. 전체 구조물은 모두 200개의 층으로 구성되며, 5개의 단면에 회로소자가 삽입되고 도선이 성형되었다. 회로소자와 단면이 삽입될 각 단면에 해당되는 층의 제작이 끝나면 장치를 일시 정지시켰다. 장치가 정지되면 성형된 홈들에 회로소자를 삽입하고 도선을 성형한 후 다시 장치를 동작시켜 전체 구조물을 제작하였다. 또한 회로소자가 삽입된 각 단면들 사이에서 수직방향의 전기적 연결을 위해 원형 단면을 가진 구멍 형상을 만들고, 여기에 전도성을 갖는 핀을 삽입하였다. 한편, 제작 속도를 높이기 위해서 회로소자와 도선이 삽입되는 단면에 해당하는 층 구조물의 적층두께는 125 μm로 설정하였으며, 이를 제외한 다른 층들의 적층두께는 250 μm로 하였다. 직접주사 헤드의 이송속도는 15 mm/s이고 전도성 재료의 주사유량은 30.16 ml/hr이다. 제작된 3차원 멜로디 회로는 커넥터를 통해서 스피커와 전원이 연결된 후 정상적으로 동작하였다.
5. 결론
본 연구에서는 FDM/FFF 공정과 직접주사공정이 통합된 다중재료 복합 부가가공 공정을 제안하고 및 이를 구현하기 위한 시스템을 제작하였다. 또한 액체상태의 전도성 재료를 토출하기 위한 직접주사장치에 개폐형 노즐을 개발하여 적용함으로써 액체재료가 원활히 토출 되도록 하였다. 회로도선이 성형되는 단면에서는 액체상태의 전도성재료가 경화된 후 단선이 일어나지 않도록 면이 모두 채워지도록 성형되어야 한다. 또한 전도성재료가 성형되는 홈을 성형하고 여기에 전도성재료를 토출하여 고온의 열가소성수지에 의해서 도선이 손상되는 것을 방지해야 한다. 개발된 공정장치를 이용해서 5개의 단면에 회로소자가 배열된 3차원 멜로디 회로장치를 성공적으로 제작하였다.
Acknowledgments
이 논문은 이공분야 기초연구사업(과제번호: NRF-2016R1D1A1B03936016) 및 2015년도 충북대학교 학술연구지원사업의 교내연구비 지원으로 연구되었습니다.
REFERENCES
- Bourell, D., Beaman, J., Marcus, H., and Barlow, J., “Solid Freeform Fabrication an Advanced Manufacturing Approach,” Proc. of the Solid Freeform Fabricaiton Symposium, pp. 1-7, 1990.
-
Vunnam, S., Ankireddy, K., Kellar, J., and Cross, W., “Surface Modification of Indium Tin Oxide for Direct Writing of Silver Nanoparticulate Ink Micropatterns,” Thin Solid Films, Vol. 531, pp. 294-301, 2013.
[https://doi.org/10.1016/j.tsf.2013.01.047]
-
Church, K. H., Fore, C., and Feeley, T., “Commercial Applications and Review for Direct Write Technologies,” MRS Online Proceedings Library Archive, Vol. 624, 2000.
[https://doi.org/10.1557/PROC-624-3]
-
Zhang, Y., Liu, C., and Whalley, D., “Direct-Write Techniques for Maskless Production of Microelectronics: A Review of Current State-of-the-Art Technologies,” Proc. of International Conference on Electronic Packaging Technology & High Density Packaging, pp. 497-503, 2009.
[https://doi.org/10.1109/ICEPT.2009.5270702]
-
Lee, I. H., Kim, H.-C., and Cho, H. Y., “Development of Hybrid Fused Deposition Modeling System for Three-Dimensional Circuit Device Fabrication,” Transactions of the Korean Society of Mechanical Engineers A, Vol. 38, No. 8, pp. 869-874, 2014.
[https://doi.org/10.3795/KSME-A.2014.38.8.869]
-
Lee, J., Kim, H.-C., Choi, J.-W., and Lee, I. H., “A Review on 3D Printed Smart Devices for 4D Printing,” Int. J. Precis. Eng. Manuf.-Green Tech., Vol. 4, No. 3, pp. 373-383, 2017.
[https://doi.org/10.1007/s40684-017-0042-x]
-
Jang, S. H., Oh, S. T., Lee, I. H., Kim, H.-C., and Cho, H. Y., “3-Dimensional Circuit Device Fabrication Process Using Stereolithography and Direct Writing,” Int. J. Precis. Eng. Manuf., Vol. 16, No. 7, pp. 1361-1367, 2015.
[https://doi.org/10.1007/s12541-015-0179-x]
-
Lopes, A. J., Lee, I. H., MacDonald, E., Quintana, R., and Wicker, R., “Laser Curing of Silver-Based Conductive Inks for in Situ 3D Structural Electronics Fabrication in Stereolithography,” Journal of Materials Processing Technology, Vol. 214, No. 9, pp. 1935-1945, 2014.
[https://doi.org/10.1016/j.jmatprotec.2014.04.009]
- Kim, H. C., Yun, H. Y., Lim, S. G., and Lee, I. H., “Fabrication of 3D-Printed Circuit Device Using Direct-Write Technology,” Proc. of Institute of Control Robotics and Systems International Conference, pp. 1964-1968, 2015.
- 3D Systems, “BFB-3000 Set Up and Operation Manual,” https://www.3dsystems.com, (Accessed 19 FEB 2018)
- Lee, I. H., Kim, H.-C., and Oh, S. T., “3D Printer Head for Three Dimension Production Comprised of Multi Material,” KOR Patent, 101736568, 2017.
- Lee, I. H. and Oh, S. T., “Liquid Discharging Nozzle,” KOR Patent, 101736567, 2017.
-
Jung, H. J., Lee, I. H., Kim, H. C., and Cho, H. Y, “Characteristics of Surface Lamination according to Nozzle Position in Liquid Direct Writing SFF,” Journal of the Korean Society of Manufacturing Process Engineers, Vol. 13 No. 2, pp. 41-48, 2014.
[https://doi.org/10.14775/ksmpe.2014.13.2.041]
- Jang, S. H., “Three Dimensional Circuit Board Fabrication Process using Stereolithography and Direct Writing,” M.Sc. Thesis, Chungbuk National University, 2014.