
온간 굽힘 성형에서 시간을 고려한 마그네슘 합금 판재(AZ31B)의 스프링백 특성 분석
Copyright © The Korean Society for Precision Engineering
This is an Open-Access article distributed under the terms of the Creative Commons Attribution Non-Commercial License (http://creativecommons.org/licenses/by-nc/3.0) which permits unrestricted non-commercial use, distribution, and reproduction in any medium, provided the original work is properly cited.
Abstract
The purpose of this study was to investigate the springback behavior of magnesium alloy (AZ31B) at high temperature with respect to the holding time in the die-set. The changes of microstructure in the springback during V-Bending were analyzed. The springback of the magnesium alloy sheet showed a tendency to decrease as the forming temperature and the retention time in the die increase. In the microstructure analysis, there was minimal change in the microstructure at room temperature, while at high temperature the microstructure changed markedly. The increasing material holding time in die has been shown to reduce springback from internal energy reduction because of recrystallization and grain growth at high temperature.
Keywords:
Magnesium alloy sheet, Spring-back, Warm forming, Time-dependent, Microstructure키워드:
AZ31B, 스프링백, 온간 성형, 시간-의존성, 미세 구조1. 서론
마그네슘 합금 소재는 비중 1.74로 철의 4배, 알루미늄 1.5배로 기존 철강 재료에 대비 우수한 비강도, 비강성과 같은 기계적 특성이 뛰어난 소재로써 반도체, 디스플레이, 항공우주 및 자동차 부품 등과 같은 중량하가 요구되는 다양한 분야에서 사용되고 있다.1 하지만 마그네슘 합금은 상온에서 낮은 연신율을 가짐으로써 성형성이 좋지 않고 낮은 탄성 계수 및 높은 유동 응력으로 인해 스프링백이 심하게 발생한다. 이러한 문제를 해결하기 위해 성형 온도를 증가시킴으로써 소재의 연신율을 증가시키고 유동 응력을 낮추어 스프링백을 감소시켜 성형성을 향상시키는 온간 성형 방법을 주로 사용하고 있다. 또한 스프링백을 감소시키기 위해 성형 후 금형 내 소재의 유지 시간을 증가시키는 방법을 사용한다. 기존 마그네슘 합금 판재의 온간 굽힘 성형과 성형 후 금형 내 소재의 유지 시간에 따른 스프링백 거동에 관한 연구는 다음과 같다.
Wang2 등은 V굽힘 성형에서 펀치 반지름 및 성형 온도에 따른 마그네슘 합금 판재의 스프링백을 측정하였다. 또한 결과 시편의 미세 구조를 관찰함으로써 스프링백 거동을 분석하였다. Hama3 등은 마그네슘 합금 판재를 사용하여 2D-Draw 굽힘 공정에서 블랭크 하중 및 성형 온도에 따른 스프링백 특성을 조사하였다. Zhang4 등은 마그네슘 합금 판재의 성형성을 평가하기 위해 다양한 성형 온도에서 LDR (Limit Drawing Ratio, 한계 연신율) 및 LDH (Limit Drawing Hight, 한계 돔 높이) 실험을 수행하였다. Li5 등은 마그네슘 합금 판재(AZ31B)를 상온 3점 굽힘 공정을 통해 금형 내 소재의 유지 시간에 따른 스프링백 변화 경향을 분석하였다. Kim6 등은 응력 완화가 스프링백에 미치는 영향을 알아보기 위해 마그네슘 합금 판재를 사용하여 온간에서 3점 굽힘 시험을 진행하였다.
현재 마그네슘 합금 판재의 크리프 특성과 소성 변형에 관한 연구가 많이 진행되었으나 크리프 특성과 소성 변형의 관계에 관한 연구는 부족한 실정이다. 따라서 본 연구에서는 L굽힘, V굽힘 온간 공정에서 마그네슘 합금 소재의 금형 내 소재의 유지 시간에 따른 스프링백 특성을 실험적으로 분석하였다. 또한 이에 따른 결과를 미세 구조 관찰을 통해 스프링백 변화 특성을 분석하였다.
2. 실험 방법
2.1 재료 특성
본 연구에서 사용한 판재로는 마그네슘 합금 판재 AZ31B이다. 상온에서 AZ31B의 기계적 물성치는 Table 1과 같으며 온도에 대한 응력-변형률 그래프는 Fig. 1과 같다.
마그네슘 합금 판재의 경우 성형 온도에 따라 유동 응력의 차이가 크게 나타나기 때문에 판재의 온간 굽힘 성형 시 상온과는 다른 성형 형상을 나타낸다.
본 연구에서는 위와 같은 기계적 물성을 갖는 마그네슘 합금 판재를 이용하여 L굽힘 및 V굽힘 시편을 압연 방향(R.D.)으로 제작하였다. 상온에서 마그네슘 합금 판재의 기계적 물성치는 Table 1과 같으며, 시편의 사진과 규격은 Fig. 2와 Table 2와 같다.
2.2 L굽힘 및 V굽힘 금형
L-형상과 V-형상의 판재 성형을 위한 금형을 제작하였으며 제작한 금형의 그림은 Fig. 3과 같다. 금형 소재의 경우 온간 및 열간 성형 공정에서 많이 사용되는 SKD-61과 SKD-11 합금을 사용하였다. L굽힘 금형의 경우, 다이 및 펀치의 폭을 50 mm, 다이의 코너 반경은 6 mm, 펀치의 코너 반경은 3mm로 제작하였다. V굽힘 금형의 경우, 다이 및 펀치의 폭은 50mm로 같으며, 펀치의 코너 반경과 펀치 어깨부의 반경은 6mm로 제작하였다. 또한 카트리지 히터를 삽입하기 위해 금형의 펀치, 다이, 홀더(L굽힘)에 각각 홀을 제작하였다.
2.3 실험 조건
V굽힘 성형 시 펀치 스트로크가 어느 일정 값 이상 내려가면 펀치의 성형부와 어깨부가 접촉되는 3점 접촉 현상이 발생한다.7이 현상이 발생하는 스트로크부터 소재는 스프링고 현상이 발생하며 이후 보터밍으로 인해 스프링백이 크게 발생하지 않는다. 본 연구에서는 스프링백 현상이 큰 3점 접촉 전 스트로크(23.3 mm)까지 성형 후 온도별 금형 내 소재의 유지 시간에 따른 스프링백 변화를 측정하였다. 금형의 온도는 온도 제어 장치를 사용하여 목표 온도(상온, 100, 150, 200, 250°C)를 유지하였으며, 소재의 끝 부에 K-Type Thermocouple을 부착하여 소재의 온도를 측정하였다. 소재와 금형의 온도가 목표 온도에 도달한 후 실험을 진행하였다. 금형 내 소재의 유지 시간은 0-1000초로 실험을 진행하였다. 각 공정의 스프링백 정의는 다음 식(1)과 같이 결정하였다.
(1) |
여기서 Δθ는 스프링백, θs는 성형 후 하사점(금형 내 소재의 유지 시간 0초)에서 소재의 각도, θf는 하사점에서 금형 내 소재의 유지 시간(0-1000초) 경과 후 상사점에서 소재의 각도이다. 소재의 스프링백 측정 시 금형에서 소재를 제거하고 냉각 후 소재의 각도를 측정하였다. 각 공정의 스프링백(Δθ) 정의의 도식적인 그림은 Figs. 4와 5와 같다. 본 연구에서 진행된 L굽힘 및 V굽힘 실험에서는 성형 온도 및 금형 내에 소재의 유지 시간에 따라 스프링백(Δθ) 값을 측정하여 마그네슘 합금 판재의 스프링백 변화 경향성을 분석하였다.
성형 시 소재와 금형의 온도를 유지하였다. Fig. 6은 성형 전,후 중심으로부터 소재의 길이 방향에 따른 온도 변화를 나타낸다. Fig. 6과 같이 성형 전후의 소성 영역의 온도 차는 10°C 미만으로 스프링백 결과에 크게 영향을 미치지 않는다. 이를 통해 성형 시 변화하는 소재의 온도는 결과값에 크게 영향을 미치지 않는다는 것을 알 수 있다.
2.4 미세 구조 관찰
본 연구에서는 마그네슘 합금 판재의 변형 특성, 온도, 금형 내 소재의 유지 시간 증가에 따른 미세 구조 변화에 대해 분석하였다. V굽힘 실험으로 성형이된 시편을 자른 후에 콜드 마운팅을 진행했다. 마운팅된 샘플을 SIC 및 알루미나 분말을 사용하여 연마를 진행하였다. 이후 입자를 관찰하기 위해 부식액(4.2 g Picric Acid, 70 ml Ethanol, 10 ml Distilled Water and 75 ml Acetic Acid)을 사용하여 에칭을 진행하였다. 최종적으로 광학현미경을 사용하여 에칭된 시편의 미세 구조 관찰을 진행하였다. 미세 구조 관찰 부위는 Fig. 7과 같다.
굽힘 변형에서는 소재의 중립축을 기준으로 압축 응력을 받는 영역과 인장 응력을 받는 영역으로 나뉘게 된다. 본 연구에서는 중립축을 기준으로 다른 변형 경로를 갖는 영역을 나누어 미세 구조 관찰을 진행하였다. 결정립 크기는 ASTM 표준 규격 E112에 해당하는 Linear Intercept Method에 의해 측정되었다. 그리고 시간에 대해 결정립의 변화를 측정하기 위해 금형 유지 시간에 따라 미세 구조를 측정 후 비교하였다.
3. 온도 및 금형 내 소재의 유지 시간 증가에 따른 L굽힘 및 V굽힘 실험 결과
3.1 성형 온도에 따른 스프링백 결과
성형 시 펀치의 하사점에서 소재의 초기 각도(θs)는 L굽힘 시 90.39°, V굽힘 시 90.5°로 측정됐다. 금형 내 소재의 유지 시간 0초일 때 성형 온도에 따른 L굽힘과 V굽힘 소재의 최종 각도를 Fig. 8에 나타냈다.
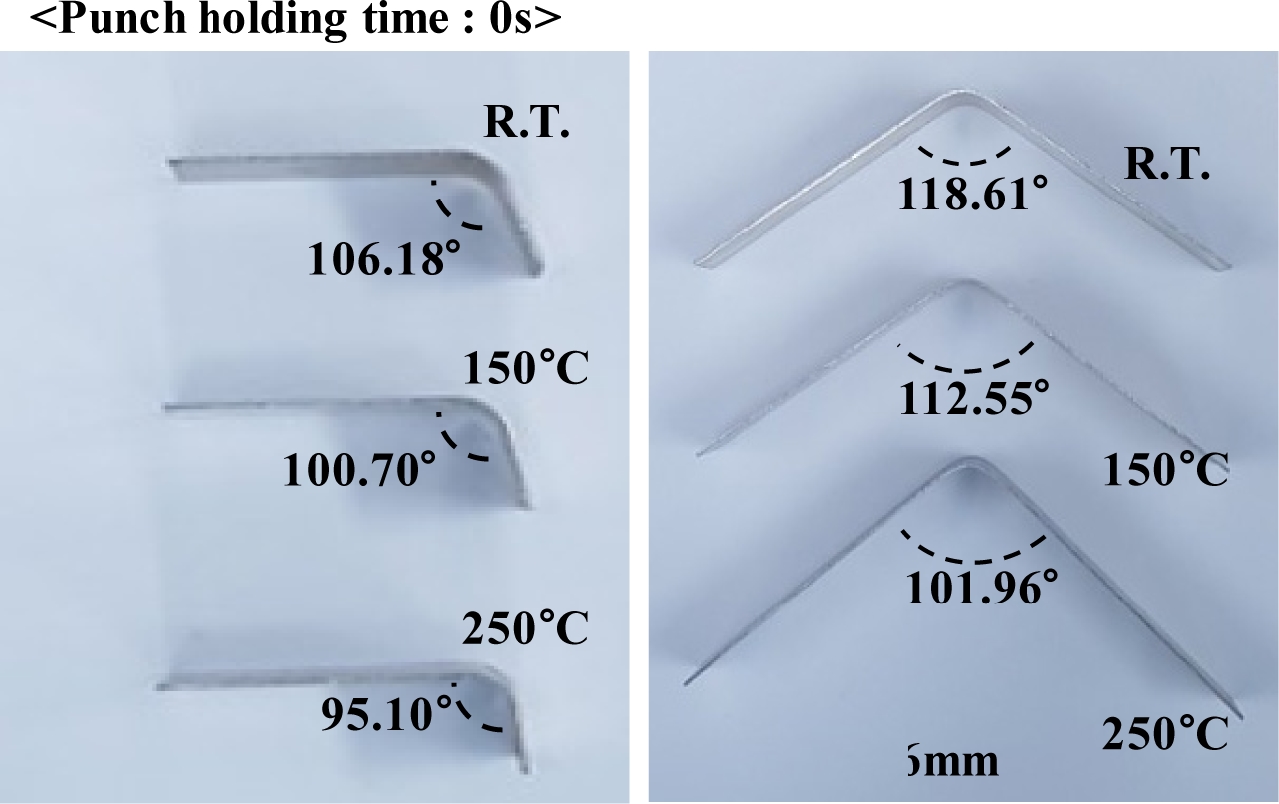
Material shape of (a) L-bending and (b) V-bending according to temperature at punch holding time 0 s
L굽힘의 경우 상온에서 스프링백(Δθ) 15.79°, 250°C에서 스프링백(Δθ) 4.71°로 11.08° 크게 감소하였다. V굽힘의 경우 상온에서 스프링백(Δθ) 28.11°, 250°C에서 스프링백(Δθ) 11.46°로 스프링백이 감소하였다. 이를 통해 성형 온도가 증가함에 따라 유동 응력이 감소하여 스프링백 또한 감소함을 알 수 있다. 스프링백은 마그네슘 합금의 재결정 온도로 알려진 150°C 이후 크게 감소하였다. 또한 V-bending 시 250°C에서 급격하게 스프링백이 감소하는 것을 알 수 있다. 이 이유는 성형 온도가 증가하면서 AZ31B의 가공경화지수 n값이 감소하고, 이로 인해 국부적인 소성 변형량이 증가해 스프링백이 급격하게 감소하기 때문이다.
온도가 증가함에 따라 스프링백이 감소한 이유는 스프링백이 재료의 탄성 계수와 항복 응력의 영향을 받기 때문이다. 탄성계수는 온도의 변화에 따라 크게 변하지 않는 반면, AZ31B의 항복 응력은 온도의 증가에 따라 크게 감소한다.8 성형 온도가 스프링백에 미치는 영향에 대한 결과는 마그네슘 합금에 대한 이전 연구와 같은 결과를 보이는 것을 알 수 있다.9
성형 온도가 증가함에 따른 V굽힘 스프링백 감소의 원인을 미세 구조 관찰을 통해 정성적으로 분석하였다. 미세 구조 관찰 결과는 Fig. 10과 같다.
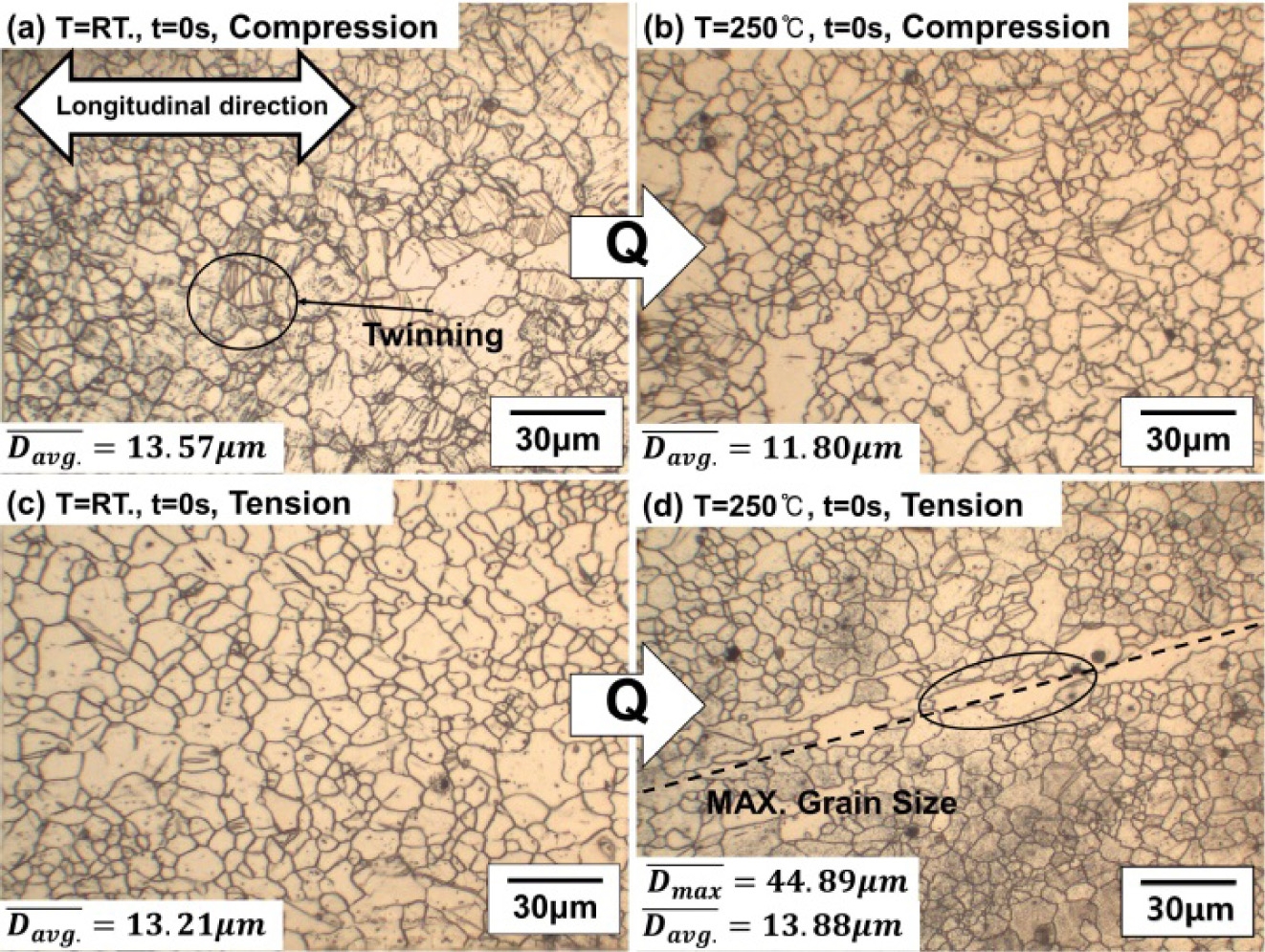
The microstructure of AZ31B after V-bending process at (a) R.T., Compression zone, (b) R.T., Tension zone, (c) 250°C, Compression zone and (d) 250°C, Tension zone
성형 온도 상온(Figs. 10(a), 10(c))의 경우, 압축 응력을 받는 영역(Fig. 10(a))에서 결정립계 사이로 쌍정(Twinning)이 많이 발생하는 반면에 인장 응력을 받는 영역(Fig. 10(c))에서는 쌍정이 거의 발생하지 않았다. 이를 통해 마그네슘 합금은 압축 변형에서 쌍정에 지배를 받는 것을 알 수 있다. 반면에 250°C의 V굽힘 실험 미세 구조 결과의 경우, 상온 압축 응력을 받는 영역(Fig. 10(a))에서 발생한 쌍정이 250°C 압축 응력을 받는 영역(Fig. 10(b))에서 발생하지 않았다.
상온 인장 응력을 받는 영역의 결정립 크기는 13.21 μm, 250°C에서 인장 응력을 받는 영역의 결정립 크기는 13.88 μm부터 최대 44.89 μm로 최대 31.86 μm 차이를 갖는다. 여기서 250°C인장 영역에서의 평균 결정립 크기와 최대 결정립 크기의 차이가 심한 이유는 재결정이 생김으로써 작은 결정립들이 많이 생기면서 비교적 낮아진 임계 슬립 응력으로 인해 결정립의 모양이 하중을 받는 방향으로 변화하였기 때문이다.
또한 250°C에서 새로운 결정이 생기는 현상인 재결정, 결정립 성장이 발생하면서 내부에너지 감소함을 알 수 있다. 이로 인해 재료의 굽힘 변형 시 발생한 스프링백(Δθ)이 성형 온도가 증가할수록 감소함을 알 수 있다.
3.2 금형 내 소재의 유지 시간 증가에 따른 스프링백 결과
성형 온도 150°C에서 금형 내 소재의 유지 시간이 증가함에 따른 L굽힘과 V굽힘 소재의 최종 각도는 다음 Fig. 11과 같다.
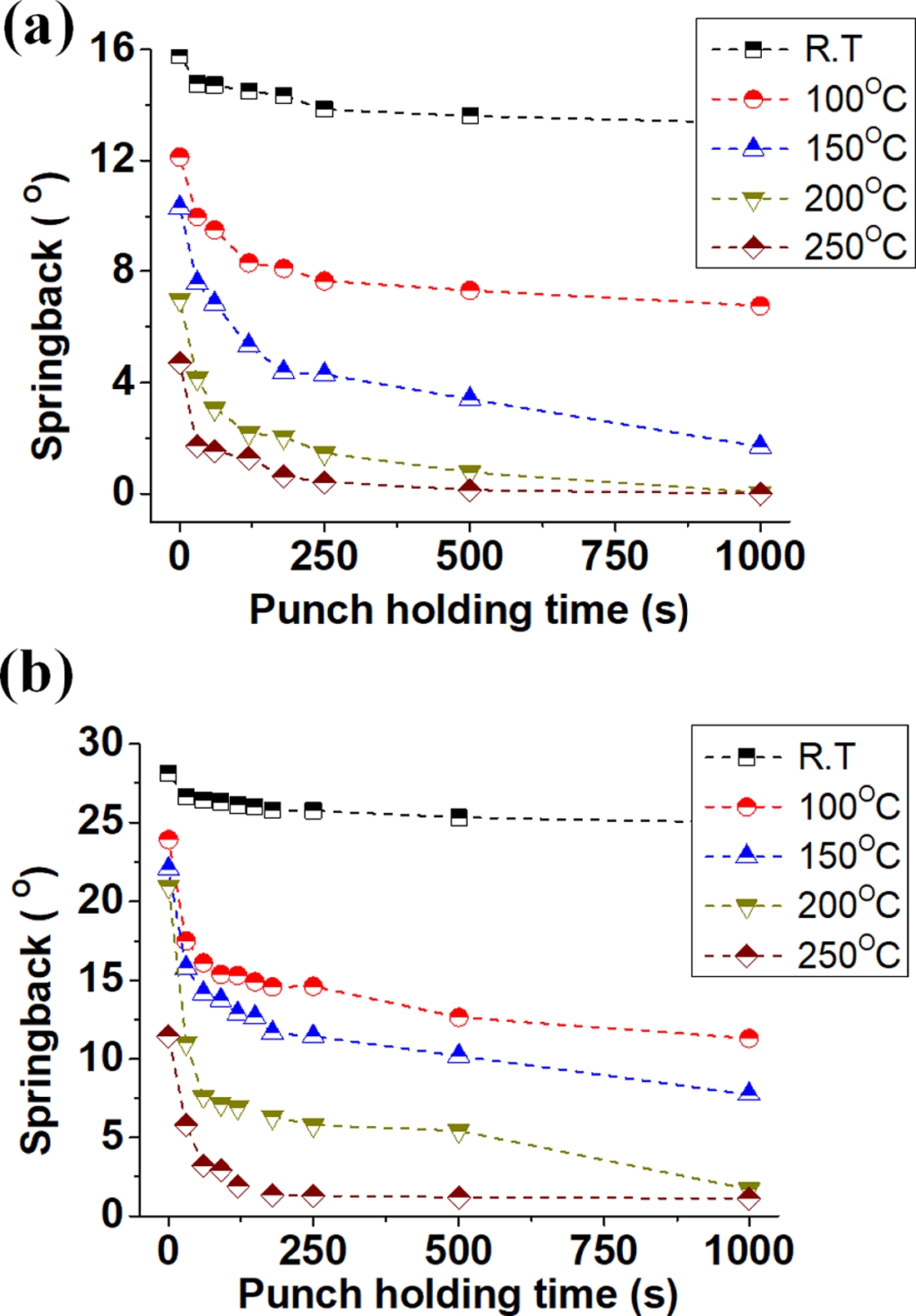
The springback of (a) L-bending process and (b) V-bending according to punch holding time and temperature
성형 온도 150°C에서 L굽힘의 경우, 금형 내 소재의 유지 시간이 0초 일 때 스프링백(Δθ)은 10.31°, 1000초 일 때 1.7°로 8.61° 감소하였다. 또한 마그네슘 합금의 재결정 온도 150°C 이상부터 금형 내 소재의 유지 시간이 1000초 일 때 스프링백(Δθ)이 2° 미만으로 크게 감소하였다. V 굽힘의 경우, 성형 온도 150°C에서 금형 내 소재의 유지 시간이 0초 일 때 스프링백(Δθ)은 20.05°, 1000초 일 때 7.76°로 12.29° 감소하였다.
각각의 성형 온도에서 금형 내 소재의 유지 시간 증가에 따른 L굽힘 및 V굽힘의 스프링백(Δθ) 결과는Fig. 11과 같다. 금형 내 소재의 유지 시간이 증가함에 따라 스프링백(Δθ)이 감소함을 확인하였다. 또한 L굽힘과 V굽힘 두 공정 모두 금형 내 소재의 유지 시간이 250초 안에 스프링백(Δθ)이 일정값으로 수렴하는 경향을 보였다.
성형 온도 상온과 250°C에서 마그네슘 합금 판재의 금형 내 소재의 유지 시간에 따른 스프링백 변화 원인을 미세 구조 관찰을 통해 정성적으로 분석하였다. 성형 온도 상온에서 금형 내 소재 유지 시간이 증가함에 따른 인장 영역과 압축 영역에서의 미세 구조는 Fig. 13과 같다.
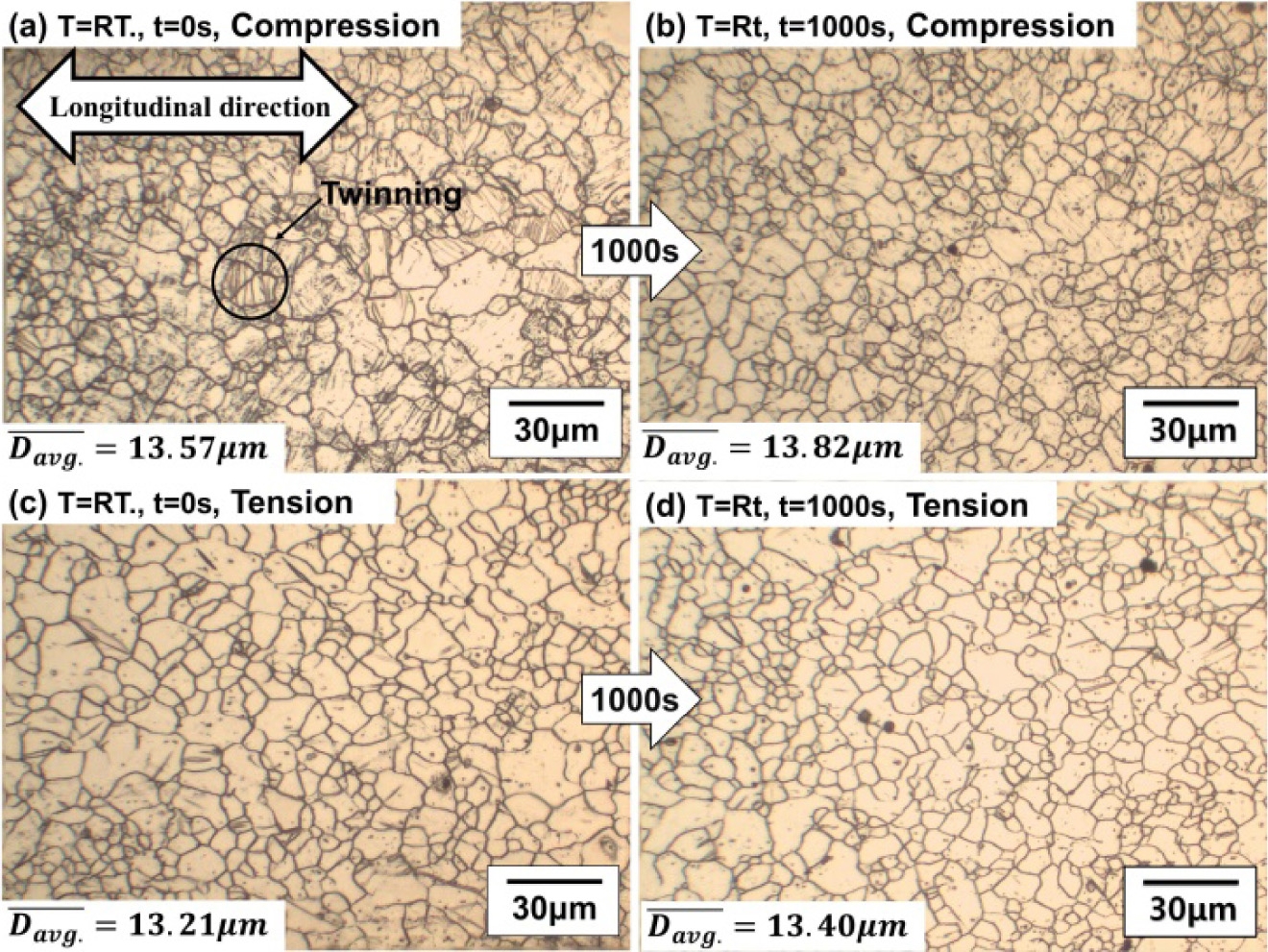
The microstructure of AZ31B after V-bending process according to material holding time (a) 0 s, Compression zone, (b) 1000 s, Compression zone, (c) 0 s, Tension zone and (d) 1000 s, Tension zone in room temperature
상온에서 V굽힘 성형 시 압축 응력을 받는 영역의 평균 결정 크기는 금형 내 소재의 유지 시간 0 s (Fig. 13(a))일 때 13.57 μm, 1000 s (Fig. 13(b))일 때 13.82 μm로 유지 시간에 따라 0.25 μm차이를 보인다. 또한 압축 응력을 받는 영역에서 금형 내 소재의 유지 시간이 0 s일 때와 1000 s일 때 쌍정, 결정립 크기는 큰 차이를 보이지 않는다.
인장 응력을 받는 영역에서 또한 금형 내 소재의 유지 시간이 0 s (Fig. 13(b))일 때와 1000 s (Fig. 13(b))일 때 결정 크기 차이 0.19 μm로 차이가 크게 나지 않는 것을 알 수 있다. 이와 같은 결과는 상온에서 V굽힘 성형 시 응력 완화의 영향이 크지 않다는 것을 알 수 있으며 금형 내 소재의 유지 시간이 증가함에 따른 스프링백 감소량 또한 3.12°로 본 연구에서 진행한 성형 온도 중 스프링백 변화량이 가장 적게 발생함을 알 수 있다.
Fig. 14는 250°C에서 금형 내 소재의 유지 시간이 증가함에 따른 미세 구조 변화 결과이다.
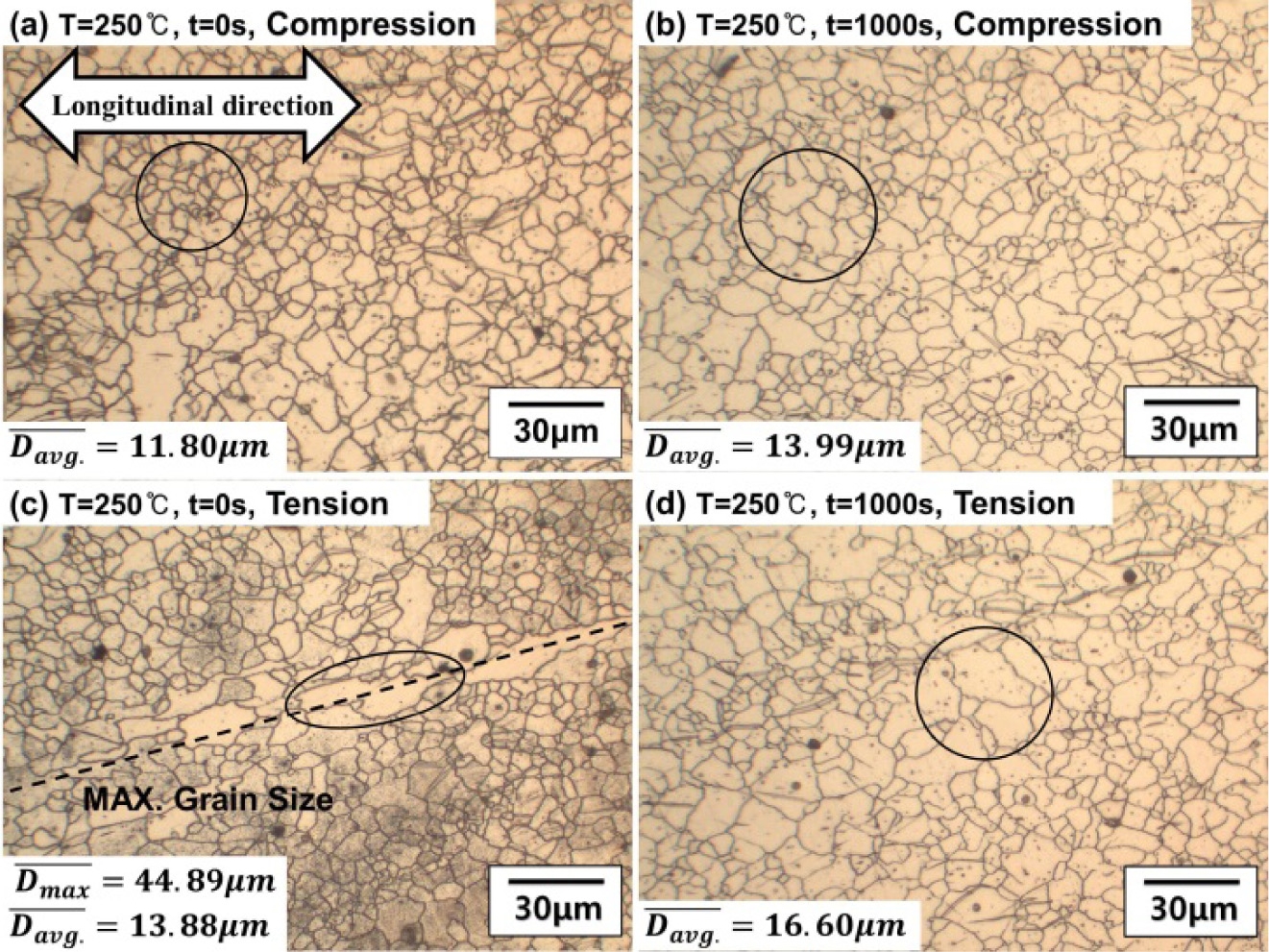
The microstructure of AZ31B after V-bending process according to material holding time (a) 0 s, Compression zone, (b) 1000 s, Compression zone, (c) 0 s, Tension zone and (d) 1000 s, Tension zone in 250°C
압축 응력을 받는 영역에서 금형 내 소재의 유지 시간이 0 s (Fig. 14(a))일 때 11.80 μm, 1000 s (Fig. 14(b))일 때 13.99 μm로 2.19 μm 커졌으며, 인장 응력을 받는 영역 또한 0 s (Fig. 13(c))일 때 13.88 μm, 1000 s (Fig. 14(d))일 때 16.60 μm로 2.72 μm 결정립 크기가 증가하였다. 이 결과를 통해 압축 응력을 받는 영역과 인장 응력을 받는 영역 모두 재결정 과정, 결정립 성장 과정을 거쳐 평균 결정 크기가 커진 것을 알 수 있다. 이러한 이유로 소재가 변형 시 쌓였던 내부 응력이 재결정 및 결정 성장으로 인해 풀리게 됨으로써 굽힘 성형 시 발생한 소재의 스프링백이 감소함을 알 수 있다.
4. 고찰
L굽힘과 V굽힘에서 모두 금형 내 소재의 유지 시간이 증가함에 따라 스프링백이 감소하였다. 이 결과는 온간 성형에서 금형 내 유지 시간이 증가함에 따라 마그네슘 합금 판재에서 재결정 및 회복으로 인한 응력 완화가 발생하였다.10 이는 소재의 소성 변형에서 발생한 잔류 응력이 온간에서 나타나는 회복과 재결정 과정을 거치며 감소하였기 때문이다. Fig. 14에서와 같이 시간이 증가함에 따라 새로운 결정이 생기고, 생성된 결정립이 성장하면서 잔류 응력이 제거된다.
특히 Fig. 12에서 0-250초 구간에 스프링백 변화량이 크게 발생하였다. 재결정에 의한 응력 완화가 발생하는 과정에서, 금형 내 유지 초기 시간에 대부분의 응력이 제거되는 것을 확인할 수 있었다. 이와 유사한 결과는 마그네슘 합금 판재의 크리프에서도 관찰할 수 있다. 소성 변형이 발생하는 높은 응력 상태에서 마그네슘 합금은 매우 높은 크리프 속도를 보인다. 특히 고온에서 1차 크리프에 비해 2차 크리프가 지배적으로 발생한다. 이는 마그네슘 합금의 경우 고온에서 임계 슬립 전단 응력이 낮아지면서 낮은 크리프 저항력을 초래하기 때문이다. 요구되는 응력에서 2차 크리프 속도의 경우 주로 전위 이동에 대한 장애물에 의해 결정이 된다. 즉, 고온으로 갈수록 비교적 전위의 이동이 쉬워 크리프 변형 속도에 대한 저항이 약해지기 때문이다.
위의 결과를 바탕으로 볼 때, 마그네슘 합금의 온간 성형에서 기존 연구와 달리 금형 내 소재의 유지 시간이 스프링백 감소에 큰 영향을 주는 것을 확인할 수 있다. 특히 250초 동안 금형 내 소재를 유지한 경우 발생한 스프링백의 80% 이상이 제거되는 것을 확인할 수 있었다. 따라서 실제 성형 공정에서도 이와 같은 금형 내 유지 시간을 고려하여 성형 공정을 설계 해야 하는 것을 알 수 있었다.
5. 결론
본 논문에서는 금형 내 소재의 유지 시간을 고려하여 온간 굽힘 성형 시 마그네슘 합금 판재의 스프링백 경향을 확인하였으며, 이 결과에 대해 미세 구조 관찰을 통해 분석하였다. 연구 결과는 다음과 같다.
AZ31B의 L굽힘 및 V굽힘 실험을 통해 성형 온도가 증가함에 따라 감소하는 유동 응력 차이가 소재의 최종 형상에 미치는 영향을 확인하였다. 온간 성형 시 최종 소재의 각도는 상온에 대비하여 L굽힘의 경우 70%, V굽힘의 경우 59% 감소하였다. 이는 성형 온도가 증가함에 따라 감소한 탄성 계수에 대비해 유동 응력의 감소가 크기 때문에 스프링백이 감소함을 알 수 있다.
AZ31B의 L굽힘 및 V굽힘 실험을 통해 금형 내 소재의 유지 시간이 소재의 스프링백에 미치는 영향을 확인하였다. 금형 내 소재의 유지 시간이 증가함에 따라 최종 소재의 각도는 상온에 대비하여 L굽힘의 경우 99%, V굽힘의 경우 95% 감소하였다. 이는 소재의 재결정 발생 및 쌍정의 사라짐에 따라 응력 완화가 발생해 굽힘 변형된 소재에 남아있던 응력이 풀림으로써 스프링백이 감소함을 알 수 있다.
NOMENCLATURE
∆θ : | Spring-back |
θf : | The workpiece angle after forming |
θs : | The workpiece angle after holding time in die |
Davg. : | Average grain size |
Acknowledgments
본 연구는 정부의 재원으로 한국연구재단의 지원을 받아 수행되었습니다(No. NRF-2017R1C1B5017648).
References
-
Friedrich, H. and Schumann, S., “Research for a “New Age of Magnesium,” in the Automotive Industry,” Journal of Materials Processing Technology, Vol. 117, No. 3, pp. 276-281, 2001.
[https://doi.org/10.1016/S0924-0136(01)00780-4]
-
Wang, L., Huang, G., Zhang, H., Wang, Y., and Yin, L., “Evolution of Springback and Neutral Layer of AZ31B Magnesium Alloy V-Bending under Warm Forming Conditions,” Journal of Materials Processing Technology, Vol. 213, No. 6, pp. 844-850, 2013.
[https://doi.org/10.1016/j.jmatprotec.2013.01.005]
-
Hama, T., Kariyazaki, Y., Ochi, K., Fujimoto, H., and Takuda, H., “Springback Characteristics of Magnesium Alloy Sheet AZ31B in Draw-Bending,” Materials Transactions, Vol. 51, No. 4, pp. 685-693, 2010.
[https://doi.org/10.2320/matertrans.P-M2010803]
-
Zhang, K., Yin, D., and Wu, D., “Formability of AZ31 Magnesium Alloy Sheets at Warm Working Conditions,” International Journal of Machine Tools and Manufacture, Vol. 46, No. 11, pp. 1276-1280, 2006.
[https://doi.org/10.1016/j.ijmachtools.2006.01.014]
-
Li, B., McClelland, Z., Horstemeyer, S., Aslam, I., Wang, P., et al., “Time Dependent Springback of a Magnesium Alloy,” Materials & Design, Vol. 66, pp. 575-580, 2015.
[https://doi.org/10.1016/j.matdes.2014.03.035]
- Kim, J., Kim, D., Lee, Y., and Lee, M., “Stress Relaxation and Springback of Magnesium Alloy Sheets,” Proc. of the Spring Conference on the Korean Society of Precision Engineering, pp. 1387-1388, 2013.
- Kim, H., Yu, J., and Lee, C., “Study on the Deformation Characteristics of AZ31B Sheets in V-Bending and Effect of Bottoming Process,” Transactions of Materials Processing, Vol. 27, No. 3, pp. 139-144, 2018.
-
Nguyen, N. T., Seo, O. S., Lee, C. A., Lee, M. G., Kim, J. H., et al., “Mechanical Behavior of AZ31B Mg Alloy Sheets under Monotonic and Cyclic Loadings at Room and Moderately Elevated Temperatures,” Materials, Vol. 7, No. 2, pp. 1271-1295, 2014.
[https://doi.org/10.3390/ma7021271]
-
Chen, F. K. and Huang, T. B., “Formability of Stamping Magnesium-Alloy AZ31 Sheets,” Journal of Materials Processing Technology, Vol. 142, No. 3, pp. 643-647, 2003.
[https://doi.org/10.1016/S0924-0136(03)00684-8]
-
Lee, J. H., Lee, J. U., Kim, S. H., Song, S. W., Lee, C. S., et al., “Dynamic Recrystallization Behavior and Microstructural Evolution of Mg Alloy AZ31 through High-Speed Rolling,” Journal of Materials Science & Technology, Vol. 34, No. 10, pp. 1747-1755, 2018.
[https://doi.org/10.1016/j.jmst.2018.03.002]
He is graduate student in department of product design and manufacturing engineering in Seoul national university of Science and Technology.
E-mail: jhyu9109@seoultech.ac.kr
Assistant professor in the department of product design and manufacturing engineering, Seoul National University of Science and Technology. His research interests include simulation and development of the metal forming process and lightweight materials.
E-mail: cwlee@seoultech.ac.kr