
절삭신호를 이용한 탄소섬유복합재(CFRP) 라우팅 가공면 특성 분석
Copyright © The Korean Society for Precision Engineering
This is an Open-Access article distributed under the terms of the Creative Commons Attribution Non-Commercial License (http://creativecommons.org/licenses/by-nc/3.0) which permits unrestricted non-commercial use, distribution, and reproduction in any medium, provided the original work is properly cited.
Abstract
Carbon Fiber Reinforced Plastics (CFRP) is an encouraging material for aerospace and automotive industries due to its light weight and high strength. Aerospace parts require precise dimensional tolerance and high machined surface quality for safety and reliability. Routing process is needed to produce satisfactory dimensional accuracy of CFRP parts. Machining defects of routing process are related to the cutting mode with respect to cutting angle and bonding strength between carbon fibers and polymer matrix. When the polymer matrix is transformed from polymer to amorphous state, bonding strength is declined. Therefore, cutting temperature is a critical parameter for CFRP machining process because glass transient temperature is relatively low. In this paper, cutting temperature was measured using thermal imaging camera. Machined surface roughness and maximum fiber pull-out depth were analyzed with respect to feed, spindle speed, and laminate structure.
Keywords:
Carbon fiber reinforced plastics, Cutting temperature, Surface roughness, Cutting surface, Machining defect, Fiber pull-out키워드:
탄소섬유복합재, 가공온도, 표면거칠기, 절삭표면, 가공결함, 뜯김1. 서론
탄소섬유복합재(Carbon Fiber Reinforced Plastics, CFRP)는 탄소섬유(Carbon Fiber)와 플라스틱 수지(Polymer Matrix)로 이루어진 복합소재로써, 일반적으로 사용되는 강철(Steel) 소재에 비해 인장강도는 약 2배 높은 반면, 밀도는 25% 이하로써 기계적 성질이 우수하고 무게는 가벼운 특징을 가지고 있다.1 항공기, 자동차등 수송산업에서 글로벌 환경규제에 따른 경량화 요구가 증가하면서 이러한 탄소섬유복합재의 고강도, 경량 특성으로 수송산업에서 탄소섬유복합재 부품 사용이 급속하게 증가하고 있다.2
탄소섬유복합소재 부품은 제조된 탄소섬유와 플라스틱 수지를 함침, 경화(Curing)하여 복합재를 만들고, 제조된 복합재를 원하는 형상과 크기로 가공하는 라우팅(Routing) 공정을 통하여 제품의 외형을 완성한다.
탄소섬유복합재는 기계적 성질이 우수하지만 여러 방향의 탄소섬유가 적층되어 있는 구조를 가지고 있어서 외형을 가공하는 라우팅 가공 공정의 경우, 섬유 각도에 따라 다양한 절삭모드가 존재하고 적층되어 있는 섬유의 방향에 따라 다양한 결함이 나타나는데,3 금속소재 가공에서 나타나는 결함과는 다른 형태인 섬유 뜯김(Fiber Pull-Out), 미절삭 섬유(Uncut Fiber), 박리(Delamination) 등의 결함이 나타난다.4 탄소섬유복합재는 항공, 자동차 등 수송산업의 경량 부품으로 사용이 증가하고 있는데 수송산업의 특성상 제품의 안전을 위해 부품의 정밀도, 가공품질 등이 중요하기 때문에 라우팅 가공 중 발생하는 결함을 줄이는 공정기술 개발이 필요하다.5
탄소섬유복합재는 플라스틱 수지에 의해 탄소섬유들이 결합하고 있는 형태로써, 가공 중 결함은 섬유와 수지의 결합력과 관계가 있다. 탄소섬유복합재를 구성하고 있는 플라스틱 수지는 일반적으로 200°C 전후에서 폴리머(Polymer)의 결합고리가 파괴되면서 강성이 감소하는 유리전이온도(Glass Transition Temperature, Tg)가 존재한다.6 가공 중 발생하는 가공 열에 의해 가공 면이 유리전이 온도까지 올라가면, 플라스틱 수지의 강성이 낮아지면서 플라스틱 수지와 섬유 사이의 결합력이 약해진다.7 섬유와 플라스틱 수지의 약해진 결합력으로 가공 중 발생하는 절삭력에 의해 섬유의 굽힙(Bending)이나 박리(Delamination) 등이 증가할 수 있으며, 이는 미절삭 섬유나 섬유 뜯김과 같은 결함을 발생시켜 가공 면의 품질을 저하시킨다.8 따라서 고품질 탄소섬유복합재 부품 생산을 위해서는 온도에 민감한 탄소섬유복합재의 소재 특성을 고려하여 라우팅 가공 조건에 따른 가공 면의 온도를 모니터링하여 유리전이 온도 이하에서 생산성과 품질을 얻을 수 있는 가공조건을 찾는 것이 중요하다. 가공 시 발생하는 가공 표면에서의 온도를 측정하기 위해서는 열전대를 이용하는 방법이 있으나, 이는 시편 준비에 많은 시간이 소요되고 가공 중에 가공 표면의 온도 변화를 실시간으로 확인하기 어려워, 열화상 카메라를 이용한 비접촉 온도 측정 방식을 제안하였으며, 열화상 카메라의 변수를 조정하여 열전대의 경우와 최대 2°C 이내의 온도 측정 오차를 확보하였다.
본 논문에서는 항공용 탄소섬유복합재의 라우팅 가공 중 발생하는 온도를 열화상 카메라를 이용하여 비접촉식 방식으로 측정하고, 가공조건(Spindle Speed, Feed)에 따라 가공온도와 라우팅 가공면의 표면거칠기 및 섬유 뜯김 깊이를 분석하였다.
2. 실험 및 탄소섬유복합재 소재 구성
Fig. 1(a)는 가공면에서의 온도를 측정하기 위한 실험 장치의 구성과 가공 중 발생하는 온도를 열화상 카메라를 이용하여 측정하는 모습을 보여주며, Fig. 1(b)는 비접촉 열화상 카메라의 측정 오차 값을 보여준다. 본 실험에서는 라우팅 가공과 가공 온도 측정을 위하여 3축 머시닝센터(Hyundai WIA, F600B)에서 직경 10 mm의 PCD 코팅 공구를 사용하였고, 공구는 YG1의 GUF39 모델이며, 나선각(Helix Angle) 15도, 4날로 이루어져 있다. 가공 중 발생하는 온도를 실시간으로 확인하기 위하여 비 접촉식 방식인 열화상 카메라를 이용하여 가공면의 온도를 측정할 수 있도록 측정 장치를 만들어 사용하였다. 탄소섬유복합재의 표면특성을 반영하여 정확한 온도를 측정하기 위해 실험 전 접촉식 열전대(Thermo-Couple)와 열화상 카메라의 측정 온도를 비교 후, 열화상 카메라의 방사율을 조정하였고,9 그 결과 Fig. 1(b)와 같이 접촉식 열전대 측정값과 비교 시 측정오차가 최대 2°C 이하의 안정된 값을 얻었다. 가공 중 발생하는 온도는 공구의 위치에서 5 mm 떨어진 지점에서의 온도를 측정하였다. 실험에 사용한 탄소섬유복합재는 국내 항공산업에서 부품 생산에 사용하고 있는 두께 5.7 mm의 소재를 사용하였다. 탄소섬유복합재의 적층 구조는 Fig. 2와 같다. 표면은 우븐(Woven) 층으로 이루어져있고, 우븐 층 아래 [-45° / 90° / -45° / 0° / 45° / 90° / 45° / 0° / 0° / 45° / -45° / 90° / -45°]s 구조로 탄소섬유가 적층되어 있다. 탄소섬유복합재는 T1000급 탄소섬유로 구성되어 있으며, 플라스틱 수지는 에폭시 소재이다. 탄소섬유 복합재는 탄소섬유 프리프레그(Prepreg)를 각도 별로 적층한 후 오토클래이브(Autoclave) 공정으로 경화한 소재이다.
본 연구에서는 라우팅 가공변수 중 공구의 이송속도(Feed)와 주축회전수(Spindle Speed)에 따른 가공온도와 가공면의 결함을 분석하였으며, 이를 위해 이송속도는 0.01 mm/rev부터 0.2 mm/rev까지, 주축회전수는 4,000 pm부터 18,000 pm까지 변화하면서 실험하였다. 실험에 사용된 탄소섬유복합재의 특성, 공구, 라우팅 가공 실험조건은 Table 1에 정리하였다.
3. 결과 및 토의
이송속도와 주축회전수에 따라 가공 면의 온도를 측정하였으며, Figs. 3(a)와 3(b)는 각각 이송속도와 주축회전수에 따른 가공면의 온도를 보여준다. Fig. 3(a)를 보면, 이송속도가 가장 낮은 조건(0.01 m/rev)에서 가공 면의 온도가 128°C로 가장 높았으며, 이송속도가 증가할수록 가공 면의 온도는 점차 낮아지는 것을 알 수 있다. 이는 이송속도가 증가하면 단위 절삭량이 증가하면서 탄소섬유복합재의 절삭에 의한 열량은 증가하지만, 동일한 가공거리(500 m)에 대한 전체 가공시간이 감소하면서, 마찰열이 감소했기 때문이다. 가공 중 발생하는 온도는 소재의 Tg값보다 낮아 가공 중 발생하는 열에 의한 폴리머 소재의 물성변화는 무시할 수 있음을 알 수 있다. Fig. 3(b)를 보면 주축회전수가 증가함에 따라 가공면의 온도가 낮아지는 것을 알 수 있다. 이는 이송속도에 따른 실험 결과와 유사하게 주축회전수가 증가하면서 이송속도가 증가하고, 이에 따라 전체 가공시간이 감소하였기 때문이다.
라우팅 가공면의 품질을 분석하기 위해 공초점 현미경(3D Laser Scanning Confocal Microscope, KEYENCE VK-X200KA)을 이용하여 표면 형상, 표면거칠기, 섬유 뜯김의 최대 깊이를 측정하였다. Fig. 4는 이송속도에 따른 가공 면의 형상, 표면 거칠기(Ra), 최대 섬유 뜯김의 깊이를 보여준다. 가공 면의 표면 형상(Surface Image)에서 적색 원으로 표시한 지점이 섬유 뜯김 결함이 최대로 발생한 곳이다. 표면 형상 이미지를 보면 최상단에 우븐층 있고 적층 순서대로 각각의 가공단면의 형상이 각도에 따라 다르게 구분되는 것을 알 수 있다. 이는 섬유의 각도에 따라 가공 모드가 달라지기 때문이다.3 공구의 이송속도가 증가하면 표면 거칠기도 증가하였으며, 표면 거칠기 값은 이송속도의 변화에 비례하는 것을 알 수 있다. 이는 이송속도가 증가함에 따라 공구 하나의 날에 의해 절삭되는 칩(Chip) 두께가 증가하고, 이에 따라 한번에 절삭되는 탄소섬유의 수와 탄소섬유 굽힘(Fiber Bending) 효과가 증가했기 때문이다.3 가공 면의 결함 형상을 보면 낮은 이송속도 영역에서는 적층된 탄소섬유의 각도(0°, 45°, 90°, -45°)별 발생하는 결함의 깊이 차이가 작고, 국부적으로 깊게 파이는 섬유 뜯김이 발생하는 영역도 높은 이송속도에 비해 적음을 알 수 있다. 또한 높은 이송속도 조건에서는 적층된 탄소섬유의 각도가 -45°인 층에서 다른 각도를 가지는 층과 비교하여 상대적으로 깊고 많은 결함이 발생했음을 알 수 있다. 이는 높은 이송속도 영역에서 공구 하나의 날에 의해 절삭되는 양이 증가하면서 탄소섬유 굽힘이 증가하여 섬유 뜯김도 증가하기 때문이다. 이송속도가 변화하면서 섬유 각도 -45°인 층 외에 다른 각도(0°, 45°, 90°)를 가지는 층에서의 결함은 상대적으로 증가하지 않음을 알 수 있었다.
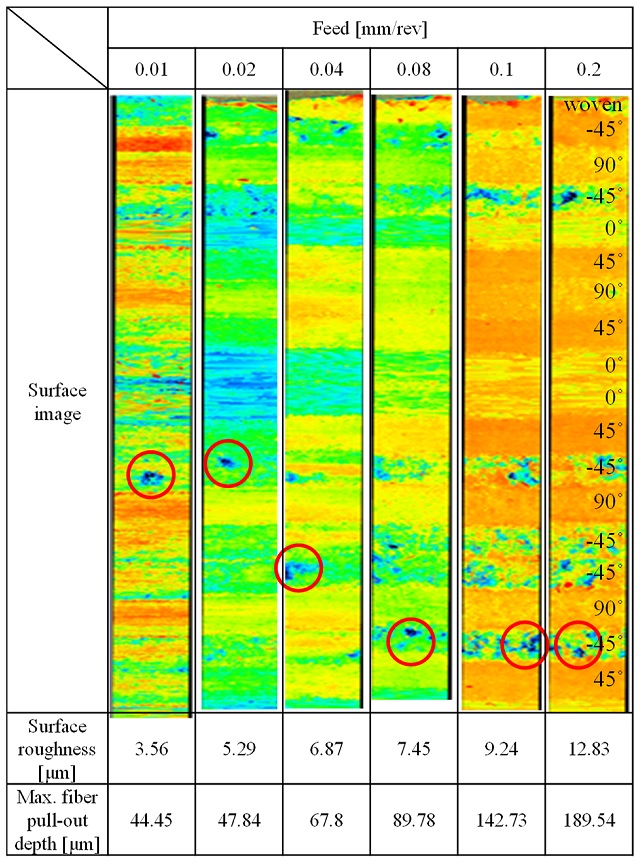
Machined surface quality (image, surface roughness and maximum fiber pull-out depth) w.r.t the routing feed
Fig. 5는 주축회전수에 따른 가공 면 측정 결과를 보여준다. 이송속도에 따른 가공 결과와 유사하게, 주축회전수가 증가하면서 표면거칠기가 증가하였고, 섬유뜯김의 최대 깊이도 증가하였다. 적층된 탄소섬유의 각도에 따른 결함의 형태를 보면 탄소 섬유의 각도가 -45°인 층에서 결함이 많이 발생했으나, 섬유 뜯김의 최대 깊이는 이송속도에 따른 결과와 비교해서 상대적으로 증가 폭이 적었다. 이는 동일한 이송속도(0.04 mm/rev)을 유지하며 주축회전수를 증가시켜 주축회전수 증가에 따른 섬유 굽힘 량 변화가 적었기 때문이다. 하지만, 전체 가공 면의 표면 거칠기는 주축 회전수 증가 시에는 섬유 뜯김의 최대 깊이와 비교하여 그 증가 폭이 컸다. 이는 섬유뜯김이 최대로 발생한 -45° 영역 외에 다른 층에서도 결함이 증가했기 때문이다. 따라서 주축회전수가 증가하는 경우에는 -45° 영역에서 국부적으로 발생하는 섬유 굽힘 결함보다는, 0°, 45°, 90°등 다른 층에서 절삭속도 증가에 의한 다양한 모드의 결함이 동시에 증가한 것으로 예상된다.3
4. 결론
탄소섬유복합재 라우팅 공정에서 이송속도와 주축회전수에 따른 가공 면의 온도를 측정하고, 가공 면 표면형상, 표면거칠기, 섬유 뜯김의 최대 깊이를 분석하였다. 가공 면 온도는 라우팅 가공시 이송속도와 주축회전수가 증가하면서 감소하였다. 이는 이송속도가 증가하면서 단위 절삭량이 증가하여 이때 발생하는 열량은 증가하지만, 전체 가공시간이 감소하여 온도 증가 폭이 감소하기 때문이다. 주축회전수가 증가하면 가공 면의 온도도 감소하였는데, 결과로 가공 면의 온도는 절삭량과 절삭 속도보다 가공 중에 발생하는 마찰열에 의한 영향이 크다는 것을 알 수 있었으며, 결론적으로 가공시간을 줄이는 것이 가공 열에 의한 결함을 최소화하는 방법 중의 하나임을 알 수 있었다.
탄소섬유복합재는 탄소섬유 방향에 따라 다양한 절삭모드가 있는데, 라우팅 가공에서는 절삭방향과 탄소섬유의 각도가 -45°를 이루는 층에서 섬유 굽힘에 의한 결함 개수와 깊이가 증가하였다. 따라서 라우팅 가공면의 가공품질 향상을 위해서는 적층각도 -45°에서 섬유 굽힘 현상을 줄이는 것이 중요함을 알 수 있다. 이송속도가 증가하면 섬유 굽힘에 의한 섬유 뜯김 결함이 증가하는 것을 실험적으로 분석하였으며, 주축회전수가 증가할 경우에는 섬유 각도가 -45°인 층의 섬유 뜯김 결함 외에 다양한 모드의 결함이 발생하여 가공 면의 표면 거칠기가 높아지는 것을 알 수 있었다.
탄소섬유복합재의 라우팅 가공 시 이송속도와 주축회전수가 증가할 경우 다양한 모드의 결함이 발생하여 가공 면의 품질이 저하되므로, 실제 항공 산업에서 고품질의 탄소섬유복합재 부품을 생산하기 위해서는 가공 품질을 유지하면서 생산성을 향상시키기 위한 가공공정 최적화에 대한 연구가 필요하다.
Acknowledgments
본 연구는 산업통상자원부의 기계산업핵심기술개발 사업의 일환으로 수행하였습니다(No. 10053248, 과제명: 탄소섬유복합재(CFRP) 가공시스템 개발).
REFERENCES
- Kennametal, “Composite Machining Guide,” https://www.kennametal.com/content/dam/kennametal/kennametal/common/Resources/Catalogs-Literature/Metalworking/Composite_material_machining_guide_Aerospace.pdf, (Accessed 25 SEP 2017)
-
Kim, H.-Y., Kim, T.-G., Lee, S.-W., Yoon, H.-S., Kyung, D.-S., et al., “Development of Manufacturing System Package for CFRP Machining,” J. Korean Soc. Precis. Eng., Vol. 33, No. 6, pp. 431-438, 2016.
[https://doi.org/10.7736/KSPE.2016.33.6.431]
-
Che, D., Saxena, I., Han, P., Guo, P., and Ehmann, K. F., “Machining of Carbon Fiber Reinforced Plastics/Polymers: A Literature Review,” Journal of Manufacturing Science and Engineering, Vol. 136, No. 3, Paper No. 034001, 2014.
[https://doi.org/10.1115/1.4026526]
-
El-Hofy, M. H., Soo, S. L., Aspinwall, D. K., Sim, W. M., Pearson, D., et al., “Factors Affecting Workpiece Surface Integrity in Slotting of CFRP,” Procedia Engineering, Vol. 19, pp. 94-99, 2011.
[https://doi.org/10.1016/j.proeng.2011.11.085]
-
Fernández-Pérez, J., Cantero, J. L., Díaz-Álvarez, J., and Miguélez, M. H, “Influence of Cutting Parameters on Tool Wear and Hole Quality in Composite Aerospace Components Drilling,” Composite Structures, Vol. 178, pp. 157-161, 2017.
[https://doi.org/10.1016/j.compstruct.2017.06.043]
- Merino-Pérez, J., Ayvar-Soberanis, S., Merson, E., and Hodzic, A., “The Influence of Heat during Short Ageing Periods on the Mechanical Properties of CFRP Composites,” Proc. of 16th European Conference on Composite Materials, 2014.
-
Michels., J., Widmann, R., Czaderski, C., Allahvirdizadeh, R., and Motavalli, M., “Glass Transition Evaluation of Commercially Available Epoxy Resins Used for Civil Engineering Applications,” Composites Part B: Engineering, Vol. 77, pp. 484-493, 2015.
[https://doi.org/10.1016/j.compositesb.2015.03.053]
-
Wang., C.-Y., Chen, Y.-H., An, Q.-L., Cai, X.-J., Ming, W.-W., et al., “Drilling Temperature and Hole Quality in Drilling of CFRP/Aluminum Stacks Using Diamond Coated Drill,” Int. J. Precis. Eng. Manuf., Vol. 16, No. 8, pp. 1689-1697, 2015.
[https://doi.org/10.1007/s12541-015-0222-y]
- FLIR, “Thermal Imaging Guidebook for Industrial Applications,” http://www.flirmedia.com/MMC/THG/Brochures/T820264/T820264_EN.pdf, (Accessed 22 SEP 2017)