
탑코팅된 그레이트바의 고온산화, 부식, 내마모 특성 평가
Copyright © The Korean Society for Precision Engineering
This is an Open-Access article distributed under the terms of the Creative Commons Attribution Non-Commercial License (http://creativecommons.org/licenses/by-nc/3.0) which permits unrestricted non-commercial use, distribution, and reproduction in any medium, provided the original work is properly cited.
Abstract
Grate Bars used in the sintering process of steel companies are exposed to high temperatures, oxidation and abrasive environments. To extend the lifetime of the Grate Bar, surface coating was applied to enhance performance at high temperatures and reinforce abrasion resistance. To evaluate mechanical and chemical properties of these coatings, various tests such as abrasion resistance testing and high temperature oxidation testing were conducted. Based on results of the tests, selection of applicable coating materials and techniques were obtained in the field.
Keywords:
Grate bar, Coating, Thermal barrier, Abrasion wear, Thermal stress, Durability키워드:
그레이트바, 코팅, 열차폐, 마모, 열응력, 내구성1. 서론
철강산업은 우리나라의 기간산업을 이루고 있는 핵심분야이며 세계적인 경쟁력을 가지고 있다. 철강 제품을 생산하기 위해서는 다양한 공정을 거치게 되는데, 철광석을 원료로 하여 강을 만드는 일관제철소의 경우 소결과정(Sintering Process)을 반드시 거치게 된다. 소결과정은 철광석을 용광로에 투입하기 전 단계에서 지름 6 mm정도의 구 모양으로 된 철광석을 코크스와 혼합하여 덩어리 모양의 괴석으로 만드는 과정이다. 이러한 소결을 위하여 소결대차가 사용되고 소결대차의 밑바닥에 위치하는 부품이 그레이트바(Grate Bar)이다. 그레이트바는 600-800°C정도의 고온과 산화, 부식, 마모 등 열악한 환경조건에서 사용되기 때문에 수 개월 단위로 교체되는 부품이다. 부식에 의한 크랙, 산화, 마모 등의 현상이 심하게 나타나기 때문에 기계적, 화학적 성능이 급격히 감소한다. 본 연구에서는 이러한 그레이트바의 수명을 연장시키기 위하여 표면에 금속합금 코팅을 수행하였다. 열차단, 산화부식, 내마모 등의 특성을 향상시킬 수 있는 금속합금 재료로 코팅을 수행하였으며,1-5 그 코팅막의 성능을 평가하기 위하여 다양한 시험을 수행하였다.
표면 코팅에 의해서 터빈, 항공, 일반 산업부품 등의 열차단, 마모, 부식 성능향상을 위한 기존 연구가 많이 발표 되었다.6-10 표면을 강화하기 위한 대표적인 방법으로 현재까지 많이 적용되고 있는 것은 침탄법, 질화법, 고주파경화법, 쇼트피닝법 등의 방법이 있다. 그러나 이러한 것은 표면의 기계적 특성을 강화하기 위한 방법이며, 표면의 다양한 화학적, 기계적, 열적 특성을 향상시키기 위해서는 그 요구사항에 적합한 새로운 코팅층을 형성하는 것이 가장 적합하다. 플라즈마 용사에 의한 표면 코팅은 이러한 요구 조건에 적합한 코팅층을 형성하는 가장 좋은 방법중의 하나인 것이 기존의 연구를 통하여 증명되었다.11,12 본연구에서도 이러한 코팅층을 형성하기 위하여 용사 방법을 적용하였다.
그레이트바의 내구성 향상을 위한 코팅층의 필수 요구사항은 내열성 향상을 위한 열차폐(Thermal Barrier) 기능과 내마모성이다. 이러한 조건을 고려하여 본 연구에서는 4가지 재료를 선택하여 코팅을 수행한 다음 성능 시험을 수행하였다. 시험결과의 검토를 통하여 현장 적용가능성과 그 유효성을 검증하였다.
2. 그레이트바
그레이트바는 고로를 사용하는 제철소에서 소결과정 중에 사용되는 부품이며 주기적으로 교체되는 소모품이다. 그레이트바의 수명을 늘려 교체주기를 늘리면 생산성, 비용, 효율 등 모든 면에서 많은 경제적 이익이 발생한다.
2.1 사용환경 및 조건
그레이트바는 사용환경이 매우 열악할 뿐만 아니라, 표면에서 철광석과 코크스가 함께 소결되면서 고열이 발생한다.
Fig. 1에 그레이트바의 사용구조를 도식적으로 나타내었다. 이 그림에서 알 수 있는 바와 같이, 그레이트바의 하부에서는 상부의 소결 연소를 가속화 하기 위해서 속도 10-15 m/s정도의 속도로 공기를 빨아 들이고 있다. 철광석이 그레이트바 위에 탑재되고, 분리되는 과정에서 그레이트바는 표면에 충격을 받는다. 그레이트바의 사용환경은 코크스의 연소열과 고속의 바람에 의해 고온 산화가 매우 촉진되는 환경이며 또한 입자의 충돌로 인한 표면 충격을 받는다.
소결대차에 장착된 그레이트바 위에 철광석과 코크스가 약 80 cm 높이로 쌓여서 연소되며 이때 발생하는 연소열이 그레이트 바의 표면에 직접적으로 접촉하게 된다. 그레이트바는 약 28%의 Cr을 함유하고 있는 고크롬강이며 오스테나이트계 내열강이다. 그러나 이러한 내열강이라도 고온에서 고속의 공기와 접촉하기 때문에 산화가 급격히 발생한다. 현재 사용되고 있는 그레이트바의 성분을 Table 1에 나타내었다.
Fig. 2는 실제 제철공장에서 사용되고 있는 그레이트바를 나타낸다. 그레이트바의 교체주기는 운전 조건 및 상황에 따라 상이하지만 대략 수개월에서 최대 1.5년 정도이다. Fig. 2의 좌측 상단의 그림은 그레이트바가 소결대차에 장착된 모습이다. 그레이트바의 교체주기는 생산비용과 연관된다.
위에서 언급한 바와 같이, 그레이트바는 혹독한 고온 산화 분위기에 노출되어 있다. Fig. 3은 그레이트바의 사용 전후의 형상을 나타낸다. 사용된 그레이트바는 표면 부식에 상당히 진행된 것을 알 수 있다. 철광석과 코크스가 혼합되어 연소하는 반응의 화학식은 다음과 같다.
(1) |
2.2 시험시편 제작
그레이트바의 수명연장을 위한 표면코팅 재료로 Mo alloy, Ni-Cr alloy, Cr-Si alloy, Ni-WC alloy 등 4가지 재료를 선택하였다. 고내열성 특성을 구현하기 위해서는 무엇보다도 재료의 선택이 가장 중요하다. 코팅 재료의 고온산화 특성, 내마모 특성이 우수해야 한다. 코팅의 방법 및 내용에 대해서는 참고문헌 13의 내용과 동일한 방법을 사용하였다. 코팅의 두께는 0.3mm로 하였다. 고온 특성이 가장 우수한 것은 세라믹 재료이나 취성에 매우 약하다.
다양한 시험을 수행하기 위하여 다수의 시험편을 제작하였다. 시험편은 기존에 현장에서 사용되는 그레이트바를 절단하여 시험편을 제작하였다. 시험 시편을 제작함에 있어서 가공으로 인한 열변형 및 열 영향으로 인한 물성의 변화를 최소화하기 위하여 와이어커팅(Wire Cutting) 방법으로 제작하였다. 3D 치수가 40 mm (H) × 40 mm (V) × 10 mm (T)인 육면체 시편을 제작하였다.
육면체 시편은 부식시험을 위한 샘플용으로 제작되었다. 고온 산화 시험을 위해서 분말 형태의 재료가 준비되었다. 내마모 시험은 디스크 형태의 시편으로 수행되었다. 내마모 시험은 크게 핀-디스크 방식과, 볼-디스크 방식으로 나누어지는데 두 방법 모두 거의 흡사한 방법으로 마모량을 측정한다. 디스크 시편의 사이즈는 Ø 60 mm, Thickness = 13 mm이다. 이 사이즈는 ASTM D3702 (Standard test method for wear rate and coefficient of friction of materials in self lubricated rubbing contact using thrust washer testing machine)의 표준 마모시험 기준의 사이즈이다.
3. 성능 시험
그레이트바의 고온, 부식 및 내마모 특성 등을 명확하게 규명하기 위하여 다양한 성능시험을 수행하였다.
Fig. 6에 나타낸 바와 같이, 성능시험은 본 연구에서 개발한 4종류의 금속합금으로 코팅된 시편과 순수한 그레이트바 시편 1종류를 포함하여 총 5 종류의 시편을 사용하여 시험을 수행하였다. 성능시험의 객관성을 부여하기 위하여 공인 인증된 시험방법을 통해서 수행하였다.
3.1 고온산화 시험
고온 산화 시험은 고온에서 금속 혹은 비금속 재료의 산화량을 측정하는 것으로써 재료가 산화되면 산소와 결합하는 무게가 증가한다. 이러한 무게 측정의 변화로 고온에서 재료의 산화도 정도를 측정하는 표준적인 방법이다. 시험은 Fig. 7에 나타낸 바와 같이 Rigoku TG120 실험장치를 사용하여 수행하였다. 고온산화 시험은 알루미나 노를 이용하였으며 가열온도는 최대 1000°C로 하였다. 대기 중에서의 산화시험을 실시하였으며 10°C/min의 속도로 온도를 상승하여 1000°C까지 온도를 상승하는데 약 100분 정도 시간이 소요되었다. 산화가 지속되어 일정한 정상상태가 되었다고 판단이 될 때 시험을 중지하였으며 시험 중지 시간은 대략 500분을 기준으로 정하였다. 산화 시험 후, 산화 정도를 평가하기 위해 무게변화를 측정하였다.
총 5개의 시료를 시험하였으며 그것은 기본이 되는 (1) Grate Bar (Cr alloy), (2) Mo alloy, (3) Ni-Cr alloy, (4) Cr-Si alloy, (5) Ni-WC alloy 이다.
시험 결과는 1000°C까지 온도를 상승시키면서 무게 증분(Weight Gain)과 열흐름(Heat Flow)을 측정하였다. 열흐름은 센서에서 발생되는 출력신호인 마이크로 볼트(μV)의 값으로 관찰할 수 있다. 시료의 무게는 20 mg을 사용하였고 산화되는 양이 거의 정상상태를 보일 때까지 시험을 수행하였다. 시험용 분말입자의 크기는 수 μm에서 수십 μm까지의 분포이다. 모든 재료는 고온에서 산소와 결합하는 특성이 다르다.
현재 사용되고 있는 그레이트바는 크롬 28%정도 함유하고 있는 고크롬강이며 Fig. 8(a)에서 보는 바와 같이 600-700°C부터 산화되기 시작하며, 시험시작 후 100-200분 정도에 산화가 급격히 진행되어 안정화(정상상태) 되어 간다. 산화량은 1000°C 500분 정도에서 약 3 mg정도로 비교적 안정적인 상태를 나타낸다. Mo 합금의 경우는 약 800°C에서 산화량이 최고 6.5 mg정도로 높게 나타났으며 전부 시험 시작 100분 이하의 시간에서 산화가 급격히 발생하고, 100분 이상의 시간에서는 완전 연소되어 무게가 감소한다. Ni-Cr 합금의 경우는 시험시작 약 100분에서 400분 정도의 시간영역에서 대부분의 산화가 급속히 진행되고 정상상태에 이른다. 최대 산화량은 1000°C에서 500분 정도의 시간에서 산화량으로 인한 무게가 증가가 약 11 mg정도이다. Cr-Si 합금 코팅재는 약 1000°C 가까운 온도에서 산화가 시작되어 급격히 산화되고, 시험 시작 후 약 500분 정도의 시간에서 약 2 mg정도 산화로 무게가 증가하였다. Ni-WC 합금 코팅재의 경우는 비교적 낮은 온도에서 산화가 시작되기는 하지만 이것은 불순물일 가능성이 높으며 1000°C 500분 정도의 환경에 노출 되었을 때 산화로 인한 무게증가가 약 1.5 mg정도이다. 위의 실험결과를 토대로 고온 산화 환경에서 가장 작은 산화량을 보이는 우수한 제품은 Ni-WC 합금재료인 것으로 나타났다. 다음으로 우수한 내고온-산화 특성을 가지는 금속합금은 Cr-Si 합금으로 같은 환경조건에서 약 2.0 mg정도 산화로 인한 무게 증가가 나타났다.
3.2 염수부식 시험
그레이트바는 사용도중 다양한 화학적 반응에 의하여 부식이 발생한다. 부식이 발생하면 내구성이 급격히 저하되며 표면 크랙의 원인을 제공하는 핵심 인자이다. 부식시험은 열악한 환경조건에서 부식에 대한 저항성을 평가하기 위하여 사용하며 산업현장의 목적에 따라서 다양한 부식시험 기준을 사용한다. 본 연구에서는 앞 절에서 제시한 5가지 재료에 대하여 염수 부식시험을 수행하여 부식에 대한 재료의 저항성을 평가하였다. 실험 장치 구성, 비용, 기술적 한계 등 다양한 어려움 때문에 본 연구에서는 염수 부식 환경에서의 시험을 통하여 간접적인 방법으로 부식에 대한 저항 특성을 규명하였다. 염수부식 시험은 KS D ISO 14993:2003 염수분무 시험기준을 적용하였다.
시험 조건은 Table 2에 제시된 시험기준에 따라 총 21 사이클 동안 시험을 수행하였다. 염수분무, 건조, 습윤의 순서대로 시험을 수행하였으며, 염수농도는 50 g ± 5 g/L NaCl 용액을 사용하였다.
부식시험의 결과는 육안으로 판단하여 결정하였다. 염수부식 시험의 결과를 Fig. 10에 나타내었다. 그림에서 ① 코팅되지 않은 그레이트바, ② Mo 합금이 코팅된 그레이트바, ③ Ni-Cr 합금이 코팅된 그레이트바, ④ Cr-Si 합금이 코팅된 그레이트바, ⑤ Ni-WC 합금이 코팅된 그레이트바 이다. 육안으로 판단한 결과 Mo 합금이 코팅된 그레이트바가 부식에 가장 취약한 것으로 나타났다.

Salt water corrosion test results (①Grate Bar, ②Mo alloy coating, ③Ni-Cr alloy coating, ④Cr-Si alloy coating, ⑤Ni-WC alloy coating)
부식환경에 대한 우수한 저항특성을 가지는 코팅재료는 Cr-Si 합금, Ni-WC 합금이며, 거의 부식이 진행되지 않았다.
3.3 내마모 시험
마모시험은 외부의 마찰, 충돌 등에 의해 표면의 마모 및 접착량 등을 측정하는 시험이다. 내마모 시험은 표면의 경도와 매우 밀접한 관계를 가지고 있다. 표면의 경도가 높을수록 마모에 대한 저항력이 크다. 내마모 시험은 ASTM D3702와 G0099 등에 명시되어 있다. 내마모 시험은 핀-디스크 형식과, 볼-디스크 형식의 두 가지가 주로 사용된다. Fig. 11은 본 연구에서 사용한 볼-디스크 형식의 장치를 나타낸다.
Fig. 5는 내마모 시험편의 사이즈를 나타낸다. 이 시편의 사이즈는 ASTM G0099에 정의되어 있다. 총 5 개의 시편에 대해서 내마모 시험을 수행하였다. 3.2절의 염수 부식시험에서와 같은 순서로 후보 재료들을 1번에서 5번까지 부여하여 시험을 수행하였다. 내마모 시험을 수행한 후의 시편의 형상을 Fig. 12에 나타내었다. 내마모 시험의 성능은 중앙에 패인 원형자국의 깊이로 나타내며, 이 데이터는 실시간으로 시험을 수행하면서 획득한다. 내마모 시험에서는 10 kg의 하중을 지르코늄 볼에 가하였고 이러한 지르코늄 볼이 원형 디스크에 마모를 일으키면서 마찰 혹은 접착에 의한 마모량을 깊이로 나타낸다. 마모 깊이는 시험장치에 부착된 다이얼 게이지에 의해서 실시간 자동적으로 측정된다. 마모의 깊이는 마모시험이 수행되면서 점점 깊어진다.
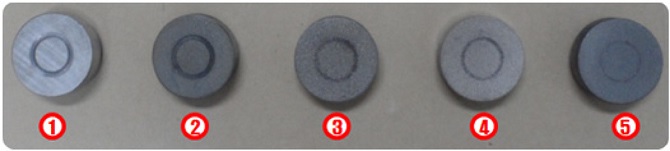
Wear test results (①Grate Bar, ②Mo alloy coating, ③Ni-Cr alloy coating, ④Cr-Si alloy coating, ⑤Ni-WC alloy coating)
마모량의 정량적인 수치인 마모 깊이는 가해진 하중과 마모시간에 의존한다. 본 연구에서는 마모시험을 32,700초 (약 9시간)동안 수행하였다. Fig. 12는 마모 시험의 결과를 나타낸다.
Table 3은 최대 마모량의 깊이를 정량적 수치로 나타낸 값이다. 코팅되지 않은 그레이트바 재료의 시편은 최대 마모 깊이가 약 1.3 mm정도이며, Mo 합금이 코팅된 시편의 경우는 1.1 mm, Ni-Cr 합금이 코팅된 경우는 0.7 mm, Cr-Si 합금이 코팅된 경우는 0.6 mm, Ni-WC 합금이 코팅된 경우는 0.4 mm정도로 나타났다. 전반적인 마모 시험의 수치로 볼 때 마모에 가장 강한 코팅재료는 Ni-WC 합금 코팅인 것으로 확인되었다. 그레이트바 재료 자체적으로도 매우 우수한 내마모 특성을 가지고 있지만 코팅된 재료의 경우는 훨씬 더 우수한 성능을 나타낸다
4. 결론
제철소의 소결과정에 사용되는 부품인 그레이트바는 600-800°C정도의 고온, 산화, 부식, 마모 등 열악한 환경에서 사용되고 있다. 본 연구에서는 이러한 가혹한 환경에서 사용되고 있는 그레이트바의 수명을 연장하기 위하여 금속재 합금 코팅 재료 4가지를 선정하였다. 순수한 그레이트바 재료와 선정된 4가지 재료로 코팅된 시편에 대하여 고온산화, 내마모, 염수부식시험을 수행하였다. 고온산화 시험에서는 Ni-WC 합금코팅재가 우수한 성능을 나타내었고, 염수부식시험에서는 Cr-Si, Ni-WC 합금 코팅재가 매우 우수하였다. 내마모 시험에서는 전반적으로 선택된 코팅재들이 우수한 내마모 특성을 나타내었으며 Grate Bar < Mo alloy < Ni-Cr alloy < Cr-Si alloy < Ni-WC alloy 의 순으로 성능이 우수함이 입증되었다. 고온 산화를 제외한 내마모, 내부식 시험은 상온에서 시험이 수행되었다. 600-800°C 정도의 고온에서는 어느 정도 편차는 있겠지만 상온의 경향이 비슷하게 유지될 것으로 예상된다.
Acknowledgments
본 연구는 미래창조과학부 2015 연구개발특구육성사업(과제번호: ACC-2015-DGI-00546)의 지원으로 수행되었으며 이에 감사드립니다.
REFERENCES
-
Koo, J. M. and Seok, C. S., “Design Technique for Improving the Durability of Top Coating for Thermal Barrier of Gas Turbine,” J. Korean Soc. Precis. Eng., Vol. 31, No. 1, pp. 15-20, 2014.
[https://doi.org/10.7736/KSPE.2014.31.1.15]
-
Koo, J. M., Lee, S. Y., and Seok, C. S., “Top Coating Design Technique for Thermal Barrier of Gas Turbine,” J. Korean Soc. Precis. Eng., Vol. 30, No. 8, pp. 802-808, 2013.
[https://doi.org/10.7736/KSPE.2013.30.8.802]
-
Cao, X. Q., Vassen, R., and Stoever, D., “Ceramic Materials for Thermal Barrier Coatings,” Journal of the European Ceramic Society, Vol. 24, No. 1, pp. 1-10, 2004.
[https://doi.org/10.1016/S0955-2219(03)00129-8]
-
Gell, M., Xie, L. H., Jordan, E. P., and Padture, N., “Mechanisms of Spallation of Solution Precursor Plasma Spray Thermal Barrier Coatings,” Journal of Surface and Coating Technology, Vols. 188-189, pp. 101-106, 2004.
[https://doi.org/10.1016/j.surfcoat.2004.08.004]
-
Wolf, W., Schulz, R., Savoie, S., Bolfarini, C., Kiminami, C. S., et al., “Structural Mechanical and Thermal Charaterization of an Al-Co-Fe-Cr Alloy for Wear and Thermal Barrier Coating Applications,” Surface and Coatings Technology, Vol. 319, No. 15, pp. 241-248, 2017.
[https://doi.org/10.1016/j.surfcoat.2017.03.066]
-
Bolelli, G., Cannillo, V., Lusvarghi, L., and Manfredini, T., “Wear Behavior of Thermally Sprayed Ceramic Oxide Coating,” Journal of Wear, Vol. 261, No. 11, pp. 1298-1315, 2006.
[https://doi.org/10.1016/j.wear.2006.03.023]
-
Cernuschi, F., Lorenzoni, L., Capelli, S. K., Markocsan, N., Menuey, J., et al., “Solid Particle Erosion of Thermal Spray and Physical Vapor Deposition Thermal Barrier Coatings,” Journal of the Wear, Vol. 271, No. 11, pp. 2909-2981, 2011.
[https://doi.org/10.1016/j.wear.2011.06.013]
-
Daroonparvar, M., Yajid, M. A. M., Yusof, N. M., Farahany, S., Hussain, M. S., et al., “Improvement of Thermally Grown Oxide Layer in Thermal Barrier Coating Systems, with Nano Alumina as Third Layer,” Transactions of Nonferrous Metals Society of China, Vol. 23, No. 5, pp. 1322-1333. 2013.
[https://doi.org/10.1016/S1003-6326(13)62600-X]
-
Tolpygo, V. K. and Clarke, D. R., “Morphological Evolution of Thermal Barrier Coatings Induced by Cyclic Oxidation,” Journal of the Surface and Coatings Technology, Vol. 163, pp. 81-86, 2003.
[https://doi.org/10.1016/S0257-8972(02)00595-9]
-
Shanmugavelayutham, G. and Kobayashi, A., “Mechanical Properties and Oxidation Behavior of Plasma Sprayed Functionally Graded Zirconia-alumina Thermal Barrier Coatings,” Journal of Materials Chemistry and Physics, Vol. 103, No. 2, pp. 283-289, 2007.
[https://doi.org/10.1016/j.matchemphys.2007.02.066]
-
Bumgardner, C., Croom, B., and Li, X., “High-Temperature Delamination Mechanisms of Thermal Barrier Coatings: In-Situ Digital Image Correlation and Finite Element Analyses,” Acta Materialia, Vol. 128, pp. 54-63, 2017.
[https://doi.org/10.1016/j.actamat.2017.01.061]
-
Kyaw, S., Jones, A., Jepson, M. A. E., and Thomson, R. C., “Effects of Three-Dimensional Coating Interfaces on Thermo-Mechanical Stress Within Plasma Spray Thermal Barrier Coatings,” Materials and Design, Vol. 125, No. 5, pp. 189-204, 2017.
[https://doi.org/10.1016/j.matdes.2017.03.067]
-
Lee, D. G. and Cho, H. K., “Morphological Observation on Tribological Characteristic of Thermal Spray Coated Steel-Bar,” Transactions of the Korean Society of Mechanical Engineers A, Vol. 38, No. 5, pp. 559-566, 2014.
[https://doi.org/10.3795/KSME-A.2014.38.5.559]