
3D 프린팅 인장 시편의 파괴 거동에 미치는 적층 조건의 영향


Copyright © The Korean Society for Precision Engineering
This is an Open-Access article distributed under the terms of the Creative Commons Attribution Non-Commercial License (http://creativecommons.org/licenses/by-nc/3.0) which permits unrestricted non-commercial use, distribution, and reproduction in any medium, provided the original work is properly cited.
Abstract
Three-dimensional printing technology has technical limitations limited to the development of prototypes focusing on functional realization. Because of these limitations, there are problems such as mechanical strength and rigidity in entering the commercialization market. However, the industry is working to overcome these obstacles in the future and apply them directly to the field for mass production in the manufacturing process. In particular, research to secure physical properties such as mechanical strength, the major problem of 3D printing products, has been initiated in the automobile industry, aviation, and medical fields. Thus, this study focused on the mechanical strength required for commercialization of 3D printing technology. To achieve this goal, a tensile specimen was fabricated by an FDM (Fused Deposition Modeling) type 3D printer. Tensile specimens were produced of round bar type and the deposition direction, layer height, and printing speed of the layers were considered. Finally, the effects of variables for each printing condition on tensile strength and fracture behavior were compared and analyzed. Also, the fracture surface of the tensile specimen was observed to investigate the effect of the deposition direction on the fracture behavior.
Keywords:
Fused deposition modeling, Layer direction, Layer height, Printing speed, 3D printer키워드:
수지 압출 적층 방식, 레이어 방향, 적층 높이, 적층 속도, 3차원 프린터1. 서론
기계 산업 분야의 전통적인 제조 방법은 현재까지도 대부분이 뿌리산업에 기초하여 이루어지고 있다. 가장 많이 사용되는 대량 생산제조방식으로 주로 주조나 절삭 그리고 금형에 의한 사출 방법 등이 적용되고 있으며, 대부분의 생산은 이러한 방식에 의해 제조된다. 현재까지 뿌리산업에 기반한 생산제조방식은 4차 산업혁명 시대에 들어서면서 그 방식이 획기적으로 변화하기 시작하였으며, 주요 핵심기술인 사물인터넷(Internet of Things), 클라우드(Cloud), 빅데이터(Big Data), 모바일(Mobile), 인공지능(Artificial Intelligence) 등의 지능정보기술인 로봇, 3D 프린팅 등이 기존 주요 제조업의 생산·소비에서 혁명적 변화를 촉진할 것으로 예상된다. 특히, 인터넷, 3D 프린터 등 오픈소스 기반의 자동차 제작이 가능해지고 차량 디자인을 공유하여 3D 프린팅으로 시제품을 소비자가 직접 만드는 DIY 형태의 자동차 출현 가능하게 되었다.1 이러한 3D 프린팅 기술의 도래는 뿌리산업의 생산제조방식을 기반으로 한 절삭가공을 비롯하여 금형, 주형, 주조, 사출성형 등의 전통적인 생산제조방식에 급격한 변화를 가져왔으며 3D 프린터를 이용한 시제품 개발이 급격히 증가하고 있는 추세에 있다.
3D 프린팅 기술의 제조 방식 중 대표적이고 범용적인 기술로는 적층 방식이 가장 많이 시용되고 있으며 이는 다시 수지 압출 적층 방식(Extrusion Process), 광경화 적층 방식(Photo Curing Process), 레이저 소결 적층 방식(Laser Sintering Process), 잉크젯 적층 방식(Inkjet Printing Process)을 비롯 폴리젯 적층 방식(Polyjet Process), 박막 적층 방식(Lamination Process) 등으로 분류된다.2
이러한 적층 제조 방식들 중 본 연구에서 다루려고 하는 기술은 수지 압출 적층 방식의 3D 프린팅 기술이다.3 이 기술은 사출 금형에서 열가소성 및 열경화성 호퍼(Hopper)에 열을 가하는 것과 같이 3D 프린팅에서는 와이어(Wire) 형태의 가소성 수지 또는 왁스(Wax) 상태의 재료를 사출 헤드(Extrusion Head)에서 연속적으로 압출하여 형상을 제조하는 방법(Fused Deposition Modeling, FDM)이다.
그러나, 3D 프린팅 기술은 아직까지 기능 구현 위주의 시제품 개발에 국한하여 적용되는 기술적 한계를 가지고 있다. 이러한 문제로 인하여 상용화로 진입하기까지 기계적 강도 및 강성 등의 문제가 남아있으나 산업계에서는 향후 이러한 장애를 극복하고 생산 라인에서의 양산화를 위한 제품에 직접 적용하려는 연구가 진행 중에 있다.
특히, 3D 프린팅 제품의 가장 큰 문제인 기계적 강도 등의 물성을 확보하기 위한 연구는 자동차 산업을 비롯하여 항공, 의료 분야 등에서 시도되고 있으며 주로 3D 프린팅 적층 조건을 달리한4-7 강도 향상에 관한 연구가 활발히 진행 중에 있다.8-10
따라서 본 연구에서는 3D 프린팅 기술의 상용화를 위해 요구되는 기계적 강도에 초점을 두어 적층 조건에 따른 물성 평가에 주안점을 두었으며, 이를 달성하기 위하여 수지 압출 적층 방식으로 인장 시편을 제작, 적층 조건이 인장 강도 평가와 파단 거동에 미치는 영향을 조사하였다.
3D 프린팅 시편은 환봉 인장 시편으로 제작하였으며 제작 시 레이어의 적층 방향(Layer Direction) 및 적층 높이(Layer Height), 적층 속도를 고려하여 제작 후 각각의 프린팅 제작 조건에 대한 변수가 인장 강도와 파단 거동에 미치는 영향에 대하여 비교, 분석하였다.
2. 실험
2.1 재료
본 연구에서는 인장 시편을 제작하기 위하여 사용된 소재는 Sindoh사에서 생산된 PLA (Poly Lactic Acid) 재질의 FDM용 3D 프린팅 필라멘트로 Fig. 1에 나타난 바와 같이 ϕ 1.75 mm의 규격을 이용하였다.
PLA 소재는 옥수수의 전분을 이용하여 만든 친환경적 수지로 고온에서 상변화 시 유해요소 발생이 거의 없으며 수축률이 매우 적어 치수 변형이 없는 장점을 가지고 있으므로 FDM 방식의 3D 프린터용 필라멘트로 가장 널리 사용된다. Table 1은 인장 시편 제작을 위해 사용된 PLA 재질의 물성을 나타낸다.
2.2 시편 제작
인장 시편 제작을 위해 사용한 프린터는 Fig. 2와 같이 Sindoh사의 FDM 방식3D 프린터, 3DWOX-DP200 모델을 이용하였다.
인장 시편 제작을 위한 치수 규격은 ASTM E 8에 의거하여 Fig. 3과 같이 환봉 형태로 제작하였다.
인장 시편 제작 시 3D 프린팅 적층 조건이 인장 강도와 파괴 거동에 미치는 영향을 변화를 조사하기 위해 고려한 시편 제작 변수는 Table 2와 같다. 시편 제작을 위해 노즐의 사출 온도와 충진율을 각각 200oC와 100%로 모든 인장 시편에 대하여 동일하게 적용하였다.
적층 조건을 다르게 한 변수로 적층 방향, 적층 높이 그리고 적층 속도가 적용되었으며 적층 방향의 경우 Fig. 4(b)와 같이 시편의 X 방향과 Y 방향으로 레이어 적층 방향을 각각 달리하여 Fig. 4(a)와 같이 시편을 제작하였다.
각각의 적층 방향에 대하여 적층을 위한 레이어 높이를 0.2와 0.4 mm, 적층 속도는 15, 100, 200 mm/s 조건으로 총 12종의 시편을 제작하였다.
Fig. 5는 3D 프린터로 0.2와 0.4 mm로 각각 적층된 인장 시편의 레이어 높이를 확인하기 위하여 Bestec Vision사의 Xi-CAM 현미경을 사용하여 150배율에서 관찰한 결과로서 레이어 높이에 맞게 제작되었음을 확인할 수 있었다.
3. 실험 결과 및 분석
3.1 인장시험 결과
Fig. 7은 적층된 레이어 방향 및 높이가 각각 X 방향과 0.2 mm인 동일한 조건에서 적층 속도를 15, 100, 200 mm/s로 달리하여 제작된 시편의 인장 시편 거동을 나타낸다. 그 결과 적층 속도가 증가할수록 인장 강도와 연신율이 감소하는 것으로 나타났다.
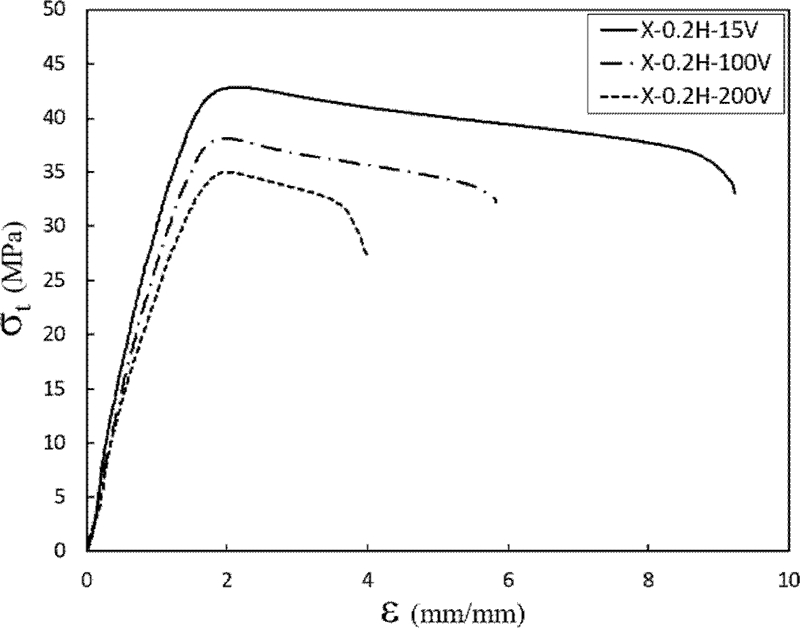
Comparison of tensile behavior at various printing speeds under X direction and layer height (0.2 mm)
Fig. 8의 레이어 방향과 적층이 동일하게 X 방향과 0.4 mm로 제작된 인장 시편의 경우 Fig. 7과 마찬가지로 적층 속도가 증가할수록 인장 강도와 연신율은 감소하는 경향을 나타내었다.
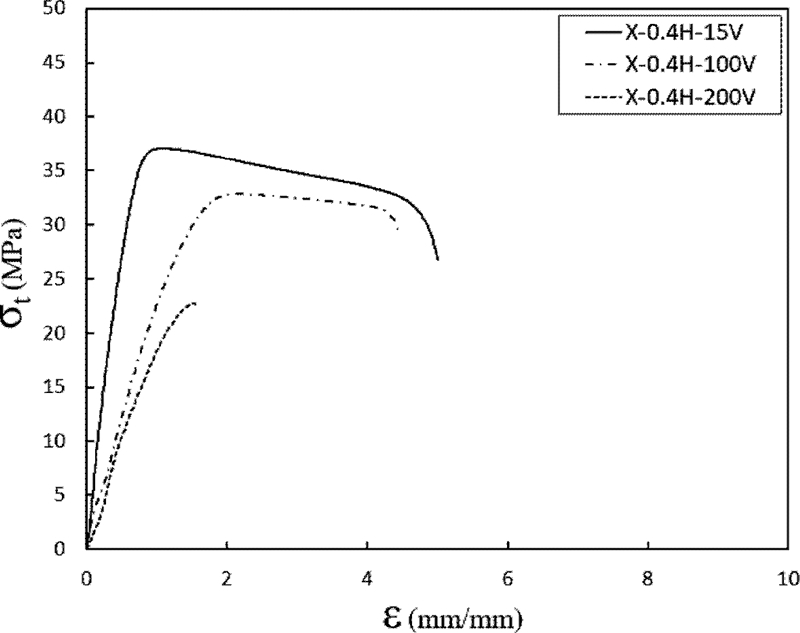
Comparison of tensile behavior at various printing speeds under X direction and layer height (0.4 mm)
Figs. 7과 8의 인장 거동 결과로부터 동일한 적층 방향과 레이어 높이에서는 적층 속도가 인장 강도와 연신율에 큰 영향을 미치는 중요 인자인 것으로 나타났으며, 적층 속도가 빠를수록 레이어 간의 결합력을 강화하는데 충분한 시간 확보의 부족 및 경계층에서 발생할 수 있는 기공(Void) 등을 발생시켜 강도 저하와 연신율의 감소에 영향을 미친 것으로 판단된다.
Figs. 9와 10은 동일한 적층 방향 X, 프린팅 속도, 즉 적층 속도 100과 200 mm/s 조건에 대하여 레이어의 적층 높이를 각각 0.2와 0.4 mm로 달리한 시편의 인장시험 결과를 보여준다.
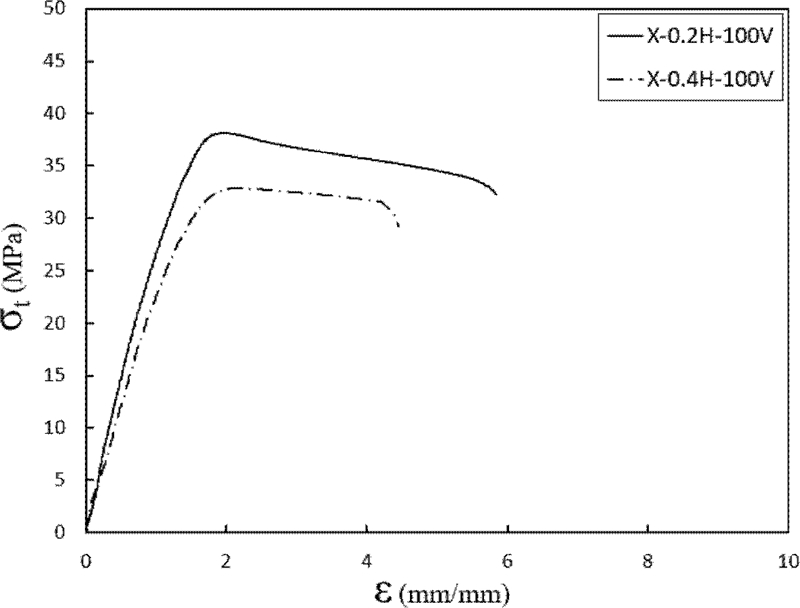
Comparison of tensile behavior at various layer height under X direction and printing speed (100 mm/s)
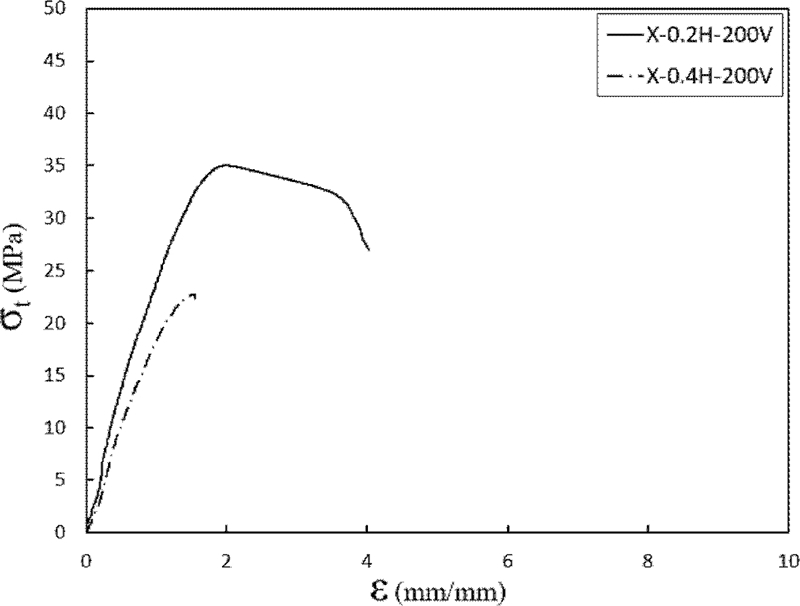
Comparison of tensile behavior at various layer height under X direction and printing speed (200 mm/s)
인장 거동은 각각의 적층 조건 100 및 200 mm/s의 속도와 관계없이 레이어 높이 0.4보다 0.2 mm의 경우가 인장 강도와 연신율이 증가한 경향을 나타내었다.
레이어의 적층 높이가 감소할수록 인장 강도가 증가한 원인은 0.4 mm 높이의 레이어로 제작된 시편에 비하여 상대적으로 증가된 레이어의 적층 수 및 면적에 외부 인장 하중에 대한 내부응력이 분배되어 시편의 인장 강도 증가에 기여를 하였다고 사료되며, 또한 연신율이 증가한 원인도 인장 방향으로 평행하게 적층된 개개의 레이어 가닥이 인장 시편의 역할을 하여 시편이 파단 시 상대적으로 많이 적층된 레이어의 수가 변형률의 증가에 기여를 하였으며, 이는 Park10의 연구 결과와도 일치하는 경향을 나타내었다. Fig. 11은 Y 방향으로 제작된 시편과의 인장 거동으로서 X 방향의 인장 거동과 동일한 경향을 나타내었는데 적층 높이가 0.2 mm로 동일한 조건에서 적층 속도가 증가할수록 인장 강도와 연신율이 현저하게 감소하는 결과를 나타내었다. 이는 적층 방향과 관계없이 적층 속도의 변화 역시 동일한 적층 높이 조건에서 적층 강도와 연신율에 영향을 미치는 변수인 것을 보여주는 결과이다. Fig. 12에 나타난 인장시험 결과 역시 동일한 적층 높이 조건에서 Fig. 11의 결과와 같은 경향을 나타내었다.
Y 방향의 적층에서 적층 속도의 증가는 앞서 기술한 Figs. 7과 8의 원인 고찰과 같이 레이어 간의 결합력 약화로 인해 생성된 경계층의 선결함이나 기공 등이 강도 저하와 연신율의 감소에 영향을 미친 것으로 판단된다. Figs. 11과 12의 결과로부터 동일한 적층 방향 Y, 각각의 적층 속도 100과 200 mm/s 조건에 대하여 적층 높이를 0.2와 0.4 mm로 달리한 시편의 인장시험 결과를 Figs. 13과 14에 나타내었다.
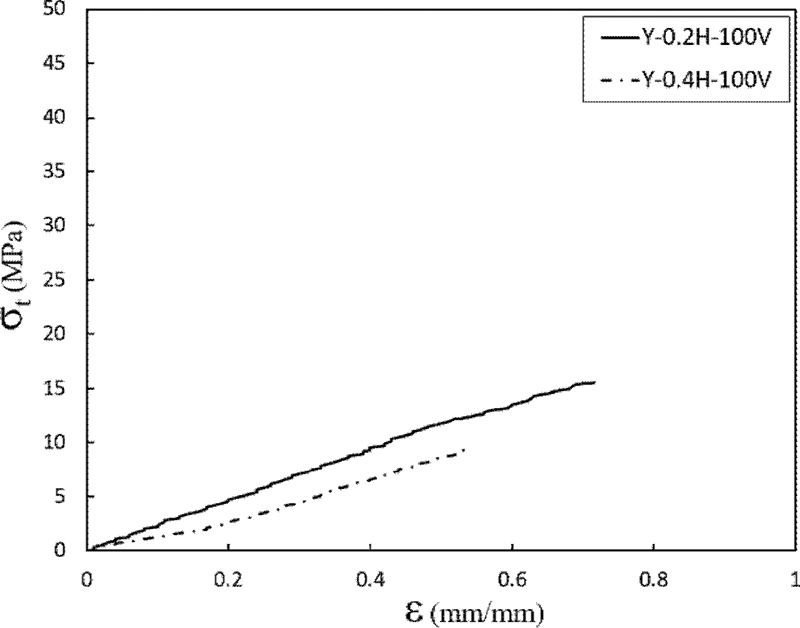
Comparison of tensile behavior at various layer height under Y direction and 100 mm/s printing speed
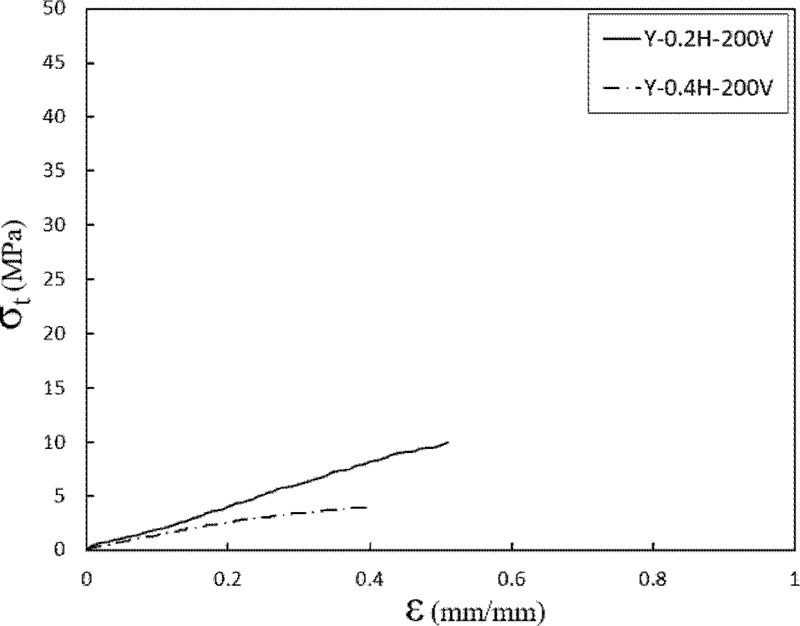
Comparison of tensile behavior at various layer height under Y direction and 200 mm/s printing speed
그 결과 동일한 적층 방향 Y에서도 X와 마찬가지로 적층 높이가 감소할수록 인장 강도는 증가하는 경향을 보였으며 연신율도 증가하는 경향을 나타내었다. 이러한 결과로부터 적층 높이 또한 시편의 인장 강도에 영향을 미치는 영향 인자인 것으로 판단된다.
적층 조건의 여러 변수 중 앞서 기술된 결과에서는 주로 적층 속도 그리고 적층 높이에 초점을 두어 분석을 하였다.
주요 인자 중 적층 방향이 인장 강도에 미치는 영향을 조사하기 위하여 Figs. 7과 8, 그리고 Figs. 11과 12의 인장시험 결과로부터 X 방향과 Y 방향의 적층 시편에 대한 인장시험 결과를 Figs. 14부터 19에 동일한 적층 높이와 속도 조건별로 나타내었다.
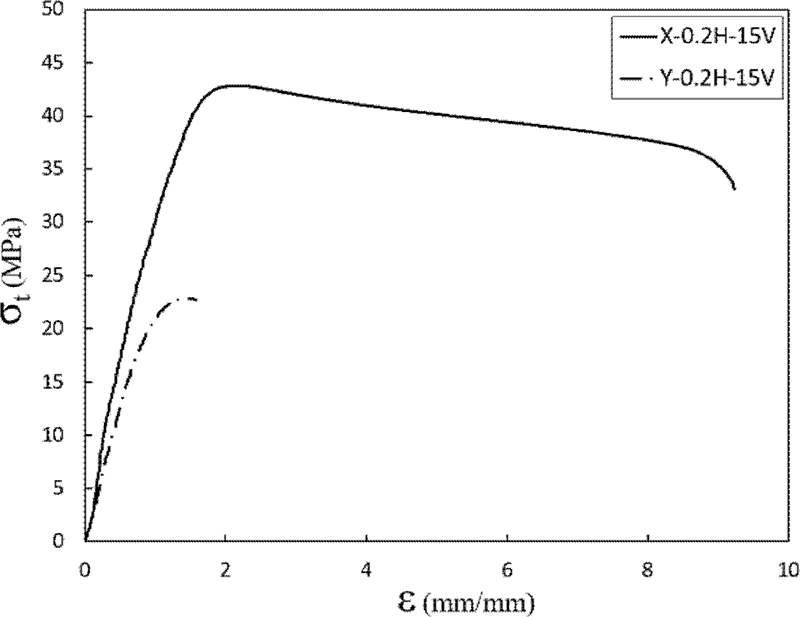
Comparison of tensile behavior at various layer direction under 0.2 mm layer height and 15 mm/s printing speed
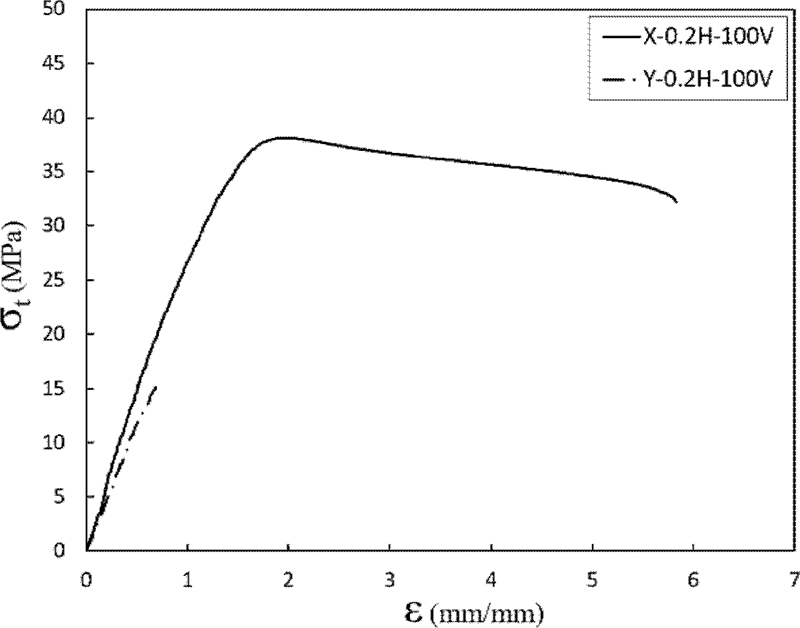
Comparison of tensile behavior at various layer direction under 0.2 mm layer height and 100 mm/s printing speed
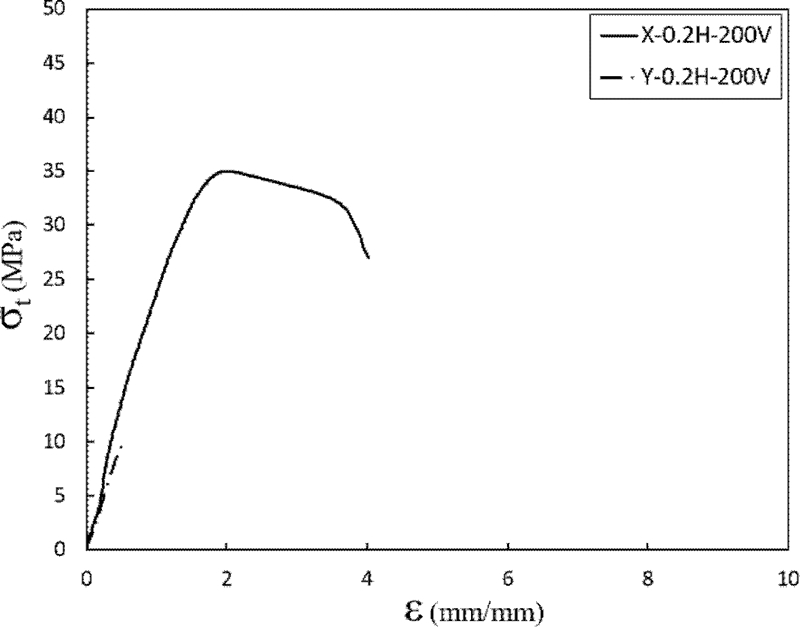
Comparison of tensile behavior at various layer direction under 0.2 mm layer height and 100 mm/s printing speed
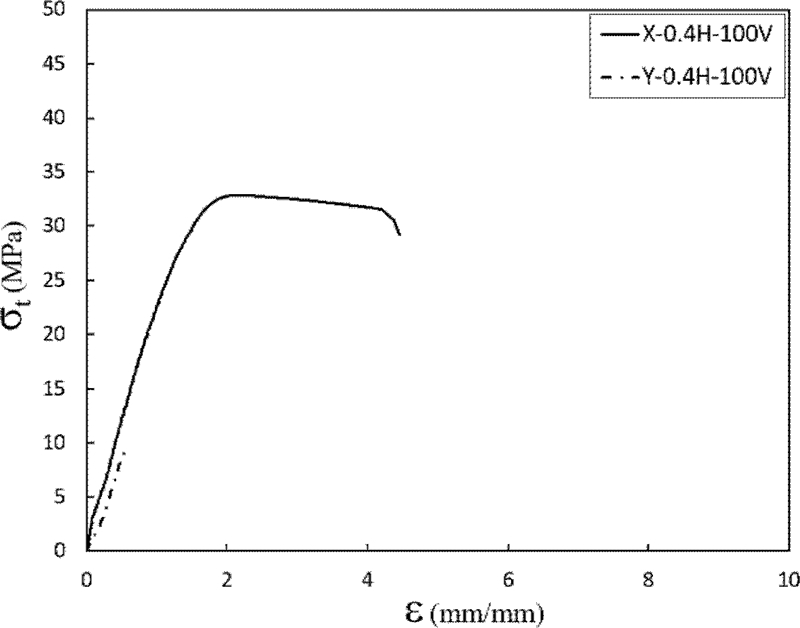
Comparison of tensile behavior at various layer direction under 0.2 mm layer height and 100 mm/s printing speed
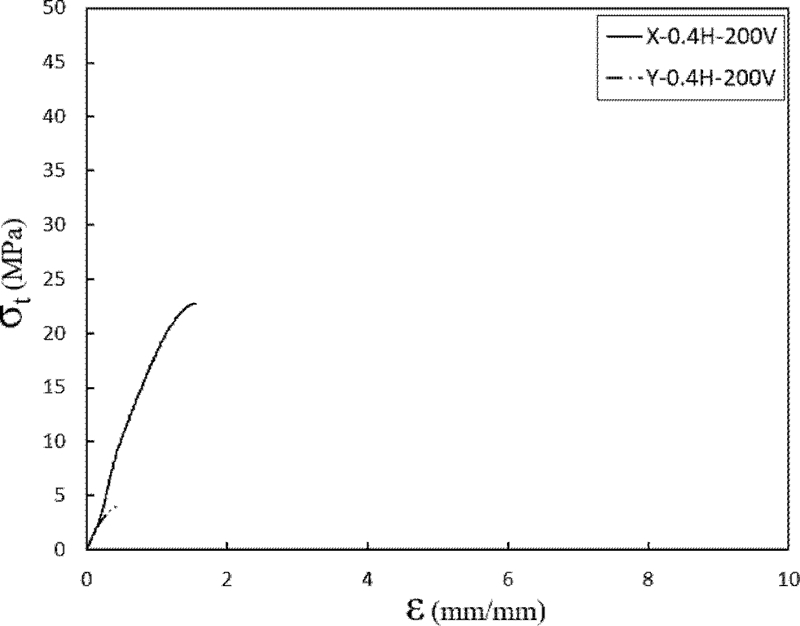
Comparison of tensile behavior at various layer direction under 0.2 mm layer height and 100 mm/s printing speed
그 결과 적층 방향이 인장 강도에 미치는 영향은 매우 뚜렷하게 나타났으며 연신율의 거동도 확연하게 차이가 남을 알 수 가 있다. 모든 결과에서 시편의 적층 높이 그리고 속도와 관계없이 X 방향의 기계적 인장 특성은 Y 방향의 인장 특성보다 매우 우수한 결과를 나타내었다. 이는 3D 프린팅으로 시험편을 적층할 경우 적층 방향에 따라 기계적 성질이 이방성을 가질것으로 예상되며 실제 본 연구의 인장실험 결과를 통해서도 입증된 것으로 나타났다.
결국 200 oC의 노즐을 통해 사출되어 적층되는 3D 프린팅 제품은 고온 및 고압 조건의 일반 사출성형 제품과 달리 적층 방향에 따른 레이어간 결합력에 따라 강도가 달라질 것이며 외부 하중이나 충격의 방향에 따라 이방성을 나타내게 된다.
이러한 이방성은 고압력의 사출성형 제품과 비교했을 때 레이어 층간 결합력이 떨어져서 이방성이 매우 커지게 된다. 파괴 역학에서 기본적으로 다루는 파괴 기구를 보면 부재에 인장 하중 부여 시 취성재료의 경우 축 방향에 수직한 방향으로 응력이 집중, 결함이 존재하는 곳에 균열(Micro Crack)이 발생하여 파괴가 발생하게 된다.
특히, Y 방향으로 적층된 부재의 경우 레이어 결합면에 대하여 수직으로 인장하중이 작용 시 레이어 적층 높이에 결합력의 크기의 차이만 있을 뿐 X 방향의 부재보다 파단이 용이하게 발생하게 된다. 이는 부재에 인장 하중 부여 시 파괴의 원인이 되는 균열이 Y 방향으로 발생, 적층된 부재의 레이어 층과 일치하며 발생된 균열은 레이어 층을 따라 평행하게 전파되어 파괴를 일으키게 된다. 이 파괴 결과는 비록 인장 하중에 의해 파괴가 발생하였지만 Y 방향으로 적층된 시편의 게이지부에 X 방향의 전단력에 의해 레이어 층간 평행 파괴가 일어나는 결과와 같은 파괴 양상을 나타내게 된다.
Figs. 14에서 19까지의 결과는 적층 속도, 적층 높이의 변화와 관계없이 X 방향과 Y 방향으로 적층된 시편의 인장시험 결과로서 Y 방향의 적층 시편은 상대적으로 매우 작은 인장 강도를 나타내고 있는데 이는 파괴역학적으로 다음과 같은 매우 중요한 결과를 내포한다. 이상의 결과로부터 3D 프린팅의 적층 방향이 외부 하중이 작용 시 작용 하중에 대하여 결합된, 즉 적층된 레이어 층이 하중 방향에 대하여 수직이면 레이어 층이 수평으로 적층된 시편의 탄성 한도 이내의 작은 응력 범위에서도 파괴가 발생할 것으로 예측되며 이는 본 연구의 Figs. 14부터 19의 인장 거동 결과를 통해서도 입증이 되었다. 이러한 연구 결과는 PLA 소재와 ABS 소재를 대상으로 3D 프린팅의 적층 변수별 연구를 진행한 연구 결과와도 일치하는 경향을 나타내었다.11,12 재료역학적으로 부재에 인장 하중 작용 시 파괴가 발생하는 각도가 축하중 방향에 대하여 90o에서 발생하므로 이 방향과 Y 방향의 적층면이 서로 일치하게 될 경우 파괴에 요구되는 응력은 낮아질 수 밖에 없으며 층간 박리가 쉽게 발생할 수 있다.
이와 반대로 X 방향으로 적층된 레이어를 따라 인장 하중이 평행하게 축 방향으로 작용할 경우 파괴의 원인이 되는 딤플이나 미소균열을 레이어의 내부에서 발생시키기 위하여 적층된 레이어 수만큼 높은 에너지를 필요로 하게 된다. 이는 일반적으로 금속 소재를 대상으로 인장시험 시 발생하는 파괴 거동과 같은 파괴 기구가 동일하게 적용되는 것과 같다고 볼 수 있다. 결국 3D 프린터에서 부품제조 시 기계적 강도에 가장 큰 영향을 미치는 핵심 인자는 적층 방향이며, 적층 높이와 적층 속도는 적층 방향을 중심으로 그 강도의 세기를 조절해주는 보조역할을 하는 변수임이 본 연구 결과에서 나타난 것으로 판단된다.
3.2 파괴 거동 및 파면 조사 결과
Fig. 20은 본 연구에 있어서 기계적 인장 강도에 가장 큰 영향을 미치는 핵심 인자인 적층 방향에 따른 파괴 거동을 Fig. 16의 파단된 인장 시편을 대상으로 조사한 결과이다. X 방향의 파면은 레이어가 외부 하중에 대하여 저항을 한 흔적이 파면에 관찰되었으며, 시편의 파단된 측면에서도 인장 하중에 대한 저항의 흔적으로 백화 현상이 나타난 것으로 조사되었다.
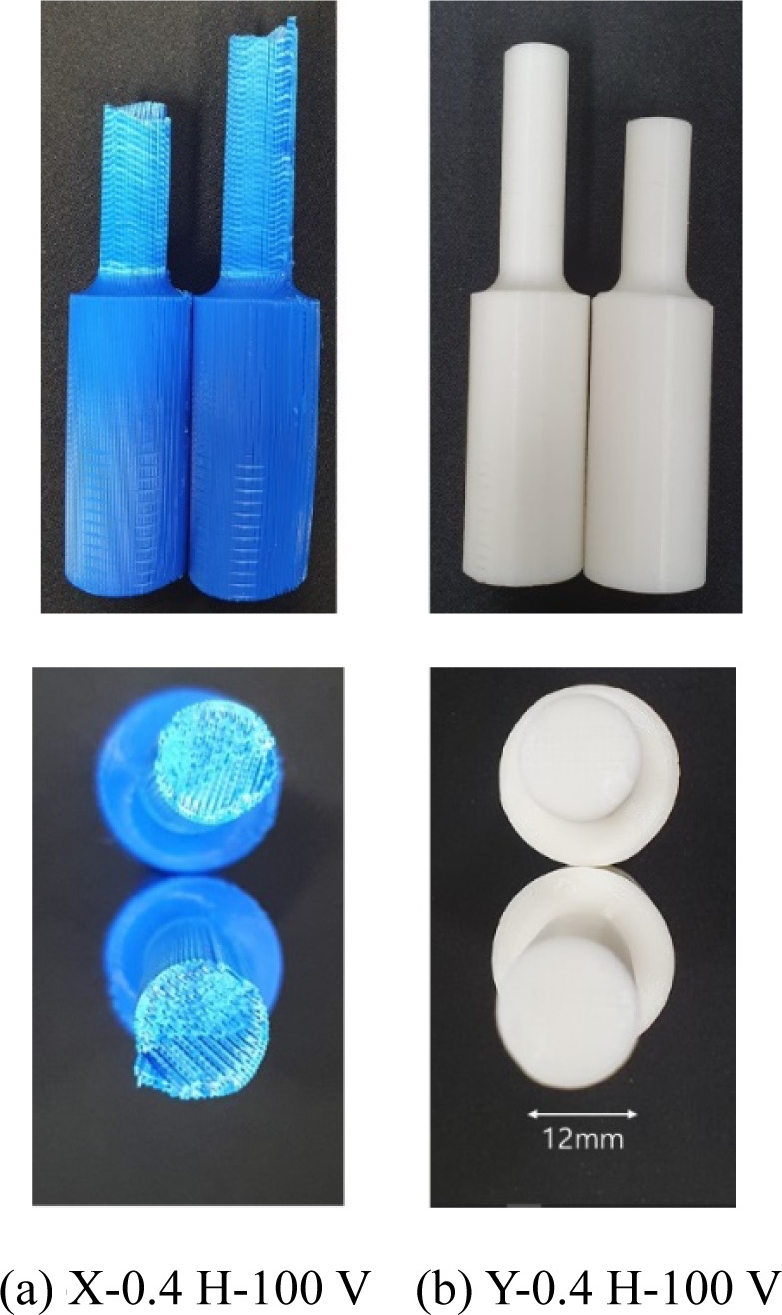
Comparison of fracture mode at various layer direction under 0.2 mm layer height and 100 mm/s printing speed
그러나, Y 방향으로 적층된 인장 시편의 파면은 매우 깔끔하게 전단되어있는 파면을 나타내었으며 시편의 측면 사진도 외부 하중에 대하여 변형된 흔적 없이 파단된 형태를 나타내었다.
Fig. 21은 Fig. 14의 인장시험 후 장착된 상태에서 파단된 모습을 촬영한 사진으로 X 방향의 레이어가 하중 방향에 대하여 연신되면서 45o 방향으로 슬립이 발생, 이와 함께 변형 저항의 증거로 백화 현상이 같이 일어나고 있음을 보여준다. 반면에 Y방향으로 적층된 시편은 거의 변형없이 취성 파괴되는 전형적인 파괴 양상을 나타내었다.
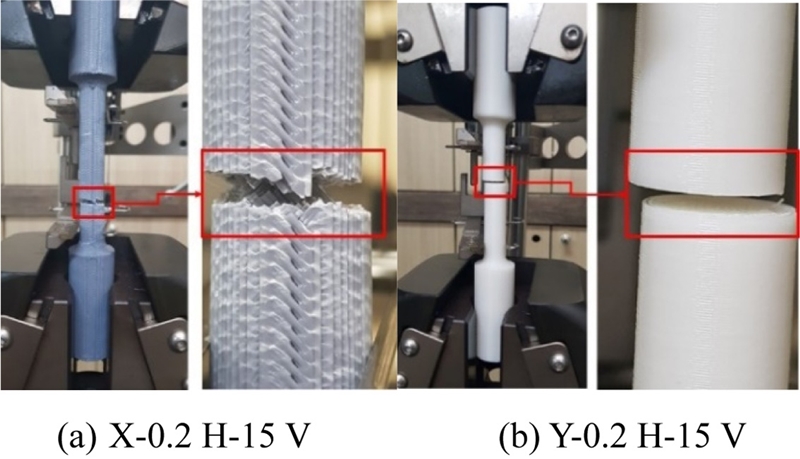
Comparison of fracture mode at various layer direction under 0.2 mm layer height and 100 mm/s printing speed
Fig. 22는 X 방향으로 0.4 mm의 레이어 높이 및 15 mm/s의 적층 속도로 제작된 시편의 인장시험 시 관찰된 시편의 파괴 거동을 단계별로 나타낸 사진이다. 무부하 시편 Fig. 22(1)에 대한 시험기의 변위가 증가할수록 시편 게이지 부위에 사진 Figs. 22(2)부터 22(6)까지 순서대로 변형으로 인한 백화 현상이 현저하게 집중되어 증가하다가 파단되는 것으로 나타났다.
이상과 같이 X 방향과 Y 방향의 적층 시편에 대한 파괴 거동을 조사한 결과 적층 방향은 파괴 모드에도 뚜렷한 파괴 형태의 차이에 영향을 미친 것으로 나타났다.
4. 결론
본 연구에서는 범용적으로 가장 많이 사용되는 수지 압출 적층 방식(FDM) 의한 3D 프린팅 기술의 향후 상용화를 위한 제품의 기계적 강도 확보 및 이에 미치는 영향 인자를 조사하기 위하여 3D 프린팅 적층 조건에 따라 인장시험을 수행한 결과 3D 프린팅 적층 조건의 여러 변수 중 적층 방향이 인장 강도에 가장 큰 영향을 미치는 핵심 인자로 나타났다. 그외 적층 높이와 적층 속도는 핵심 인자를 2차적으로 조절해주는 보조 인자인 것으로 조사되었다. 따라서, 향후 시제품을 비롯하여 상용화를 고려한 제품 등의 제조 시 외부 하중이 작용하는 방향을 고려하여 적층 조건을 주의 깊게 결정해야 할 것으로 사료된다.
NOMENCLATURE
X : | X axis deposition direction |
Y : | Y axis deposition direction |
H : | Layer height |
V : | Printing speed |
σt : | Tensile stress |
ε : | Strain |
Acknowledgments
본 연구는 오산대학교 2019년 교내학술연구지원에 의하여 이루어졌습니다.
References
- Ryu, B. K., “Impact and Implications of the Fourth Industrial Revolution on Korean Manufacturing,” Korea Institute for Industrial Economics & Trade, 1st Ed., p. 11, 2017.
-
Ahn, D. G., Lee, S. H., Kim, K. D., and Yang, D. Y., “Study on Rapid Manufacturing of 3D Functional Parts Combining VLM-ST Process and its RT Technology,” Transactions of Materials Processing, Vol. 11, No. 4, pp. 323-331, 2002.
[https://doi.org/10.5228/KSPP.2002.11.4.323]
-
Eom, S., Park, J., Jin, J., and Son, Y., “Feasibility Study on Dimensional Standard for Material Extrusion Type 3D Printed Structures,” Journal of the Korean Society for Precision Engineering, Vol. 37, No. 4, pp. 241-246, 2020.
[https://doi.org/10.7736/JKSPE.019.118]
-
Ahn, S. H., Montero, M., Odell, D., Roundy, S., and Wright, P. K., “Anisotropic Material Properties of Fused Deposition Modeling ABS,” Rapid Prototyping Journal, Vol. 8, No. 4, pp. 248-257, 2002.
[https://doi.org/10.1108/13552540210441166]
-
Bellehumeur, C., Li, L., Sun, Q., and Gu, P., “Modeling of Bond Formation between Polymer Filaments in the Fused Deposition Modeling Process,” Journal of Manufacturing Processes, Vol. 6, No. 2, pp. 170-178, 2004.
[https://doi.org/10.1016/S1526-6125(04)70071-7]
-
Sun, Q., Rizvi, G., Bellehumeur, C., and Gu, P., “Effect of Processing Conditions on the Bonding Quality of FDM Polymer Filaments,” Rapid Prototyping Journal, Vol. 14, No. 2, pp. 72-80, 2008.
[https://doi.org/10.1108/13552540810862028]
- Lee, S. H., Kim, M., Yun, E. G., and Lee, W. S., “Mold Technology with 3D Printing for Manufacturing of Porous Implant,” Journal of the Korea Society of Die & Mold Engineering, Vol. 11, No. 1, pp. 30-33, 2017.
- Ziemian, C., Cipoletti, D., Ziemian, S., Okwara, M., and Haile, K., “Monotonic and Cyclic Tensile Properties of ABS Components Fabricated by Additive Manufacturing,” Proc. of the Annual International Solid Freeform Fabrication Symposium, pp. 525-541, 2014.
-
Park, J. H., Park. S. J., Lee. K. H., and Lyu, M. Y., “A Study on the Deposition Strength of 3D Printed Specimen by Fused Deposition Modeling Process,” Proc. of the KSMTE Annual Spring Conference, p. 43, 2015.
[https://doi.org/10.7317/pk.2016.40.6.846]
- Park, S. J., Lee, J. E., Park, J. H., Lyu, M. Y., Lee., N. K., et al., “Comparison of Tensile Strength according to Raster Overlap in Fused Deposition Modeling Type 3D Printing,” Proc. of the KSMTE Annual Spring Conference, p. 189, 2016.
-
Park, S. J., Park, J. H., Lee, K. H., and Lyu, M. Y., “Deposition Strength of Specimens Manufactured Using Fused Deposition Modeling Type 3D Printer,” Polymer-Korea, Vol. 40, No. 6, pp. 846-851, 2016.
[https://doi.org/10.7317/pk.2016.40.6.846]
-
Kang, Y. G., Lee, T. W., and Shin, G. S., “The Influence of Experiment Variables on 3D Printing Using ABS Resin,” Journal of the Korean Society of Manufacturing Process Engineers, Vol. 16, No. 2, pp. 94-101, 2017.
[https://doi.org/10.14775/ksmpe.2017.16.2.094]
Professor in the Department of Mechanical Engineering, Osan University. His research interest is Fracture mechanics and Mechanical Design, its applications.
E-mail: kultra@osan.ac.kr