
원뿔 컵 형상의 점진적 판재 성형 공정에서 형상에 따른 단면 형상의 변형 특성 분석
Copyright © The Korean Society for Precision Engineering
This is an Open-Access article distributed under the terms of the Creative Commons Attribution Non-Commercial License (http://creativecommons.org/licenses/by-nc/3.0) which permits unrestricted non-commercial use, distribution, and reproduction in any medium, provided the original work is properly cited.
Abstract
Incremental sheet metal forming can be used to manufacture various products without the punch and die set. However, it is difficult to manufacture the desired shape due to section deflection and springback of the sheet. Section deflection is caused by the force of the blank holder for fixing the sheet and the tool for forming the sheet. In this study, we analyzed the characteristics of the section deflection according to the geometries of the circular cup shapes in the sheet incremental forming process. The section deflection increased with an increase in the entering radius and forming angle in the section deflection region. However, section deflection was constant according to the exit radius. In addition, the secondary forming process for reducing the shape error was introduced. The secondary incremental forming process was conducted in the opposite direction. Characteristics of the shape error according to the entering depth of the tool among the forming parameters for reducing the shape error of the cup shape were analyzed. The springback in the cup-shape was reduced by the additional forming process with an optimum entering depth of the tool.
Keywords:
Incremental sheet metal forming, Section deflection, 2nd Incremental forming process키워드:
점진적 판재 성형, 단면변형, 2차 점진적 성형 공정1. 서론
4차 산업시대로 접어들며 자동차 산업과 같은 제조업계는 고객 요구의 다변화에 대응하기 위해 오랫동안 유연 생산을 확대하고 있다. 유연 생산 시스템은 다품종 소량 생산에 적합한 유연성을 갖는 제조 시스템을 말한다. 최근에는 대량 생산과 고정 설비로 대변되는 화학, 기계 등 전통 산업에서도 생존 차원에서 도입하고 있다.
점진적 판재 성형은 이러한 유연 생산 시스템에 적합한 성형공법이다. 이 성형 기술은 공구와 소재의 접촉으로 소재에 작은 변형을 누적시켜 목적 형상을 제작할 수 있는 성형 기술이다.1 일반적으로 판재 성형을 하기 위해서는 다이와 펀치가 필요하다. 하지만 점진적 판재 성형은 CNC 가공기에 둥근 원형 공구를 장착해 성형할 수 있어 금형 제작이 필요 없다. 또한 X, Y, Z축으로 표현 가능한 3차원 공구 경로와 작은 원형의 공구를 이용하여 어떠한 제품도 성형할 수 있는 장점이 있다. 따라서 기존의 성형 기술보다 성형성이 좋아 제작할 수 있는 제품의 범위가 상대적으로 넓다.2 이에 따라 Jeswiet et al.,3 Park et al.,4은 점진적 판재 성형에서 소재와 공구 경로의 성형 공정변수에 따른 성형 한계선도(FLD), 표면 거칠기 등 성형성 및 소재의 특성에 관하여 비교 분석하였다. 하지만 점진적 판재 성형에서는 성형 중에 발생하는 형상 오차와 성형 후에 발생하는 형상 오차가 존재한다.5 성형 중에는 판재를 성형하기 위한 공구의 가압하는 힘과 판재를 고정하기 위한 블랭크 홀더의 힘으로 판재에 굽힘 변형이 발생하여 단면변형이 발생한다.6 성형 후에는 판재의 탄성 회복으로 인한 소재의 스커트부에서 스프링백이 발생한다. Fig. 1은 성형 후 발생하는 단면변형과 스프링백의 실험 결과이다.
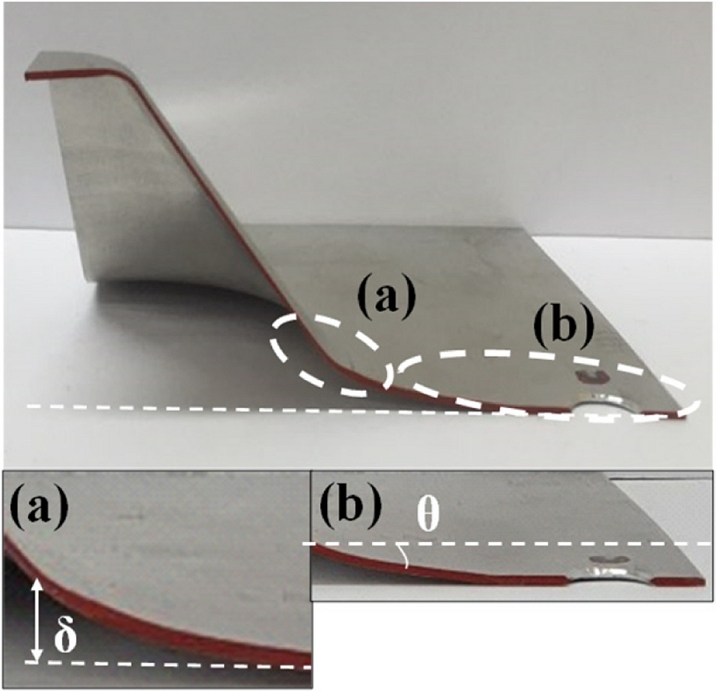
Shape errors in the single point incremental forming process (a) Section deflection (δ) and (b) Skirt spring back (θ)
Jung et al.7은 점진적 성형에서 발생하는 형상 오차를 줄이기 위해 2차 점진 성형을 통한 형상 저감 공정을 개발하였다. 2차 점진적 성형 공정은 Fig. 2에서와 같이 일반적인 점진적 판재 성형 후, 소재를 180o 회전하여 단면변형이 발생한 구역을 추가로 성형한다. 이에 따라 형상 오차 중 단면변형 및 스커트부의 스프링백을 감소하여 형상 오차를 저감하는 방법이다. 일반적인 점진적 판재 성형을 1차 점진 성형, 형상 오차를 저감하는 점진적 판재 성형을 2차 점진 성형이라 하였다.7
본 연구에서는 먼저 원뿔 컵 형상의 성형 공정에서 제작하고자 하는 형상에 따른 단면 형상의 변형을 측정하였다. 원뿔 컵형상을 성형하기 위한 성형 공정변수 중 진입 반지름, 이탈 반지름, 성형 각도에 따른 단면변형의 특성을 비교 분석하였다. 더 나아가 여기서 발생한 형상 오차를 감소시키기 위한 2차 점진 성형의 연구를 진행하였다. 원뿔 컵 형상의 형상 오차를 저감하기 위한 성형 공정변수 중 공구의 진입 깊이에 따른 형상 오차의 특성을 비교 분석하였다.
2. 실험 소재
2.1 재료의 인장 시험
본 연구의 실험 소재는 알루미늄(Al5052)을 사용하였다. 소재의 기계적 물성을 도출하기 위해 인장 시험을 진행하였다. 본 시험을 진행하기 위해 200 ton 유압식 만능재료시험기를 사용하였다. 위의 재료시험기의 크로스 헤드 속도를 5mm/min으로 변위를 제어하였다. 인장 시편은 KS B0801-13호 규격에 입각한 시편을 사용하였다. 시편의 표점 거리는 50, 너비는 12.5, 두께는 1 mm이다. 인장 시험을 측정하기 위해 3D-DIC (ATOS Core Optical 3D Scanner)를 사용하였다. 위의 실험 측정 장비를 사용하여 프레임의 속도를 5Hz로 제어하였다. 인장 시험 장치는 Fig. 3과 같다.
2.2 인장 시험 결과
Fig. 4는 표점 거리에서 소재의 응력-변형률 선도이다. 위의 선도에서는 톱니 형태의 특이한 응력 진동이 발생한다. 이와 같은 현상을 PLC 효과(Portevin-Le Chatelier Effect)라 한다.8 Table 1은 위의 선도로 도출한 Al5052의 기계적 물성이다. 항복 강도는 167.8 MPa이다. 알루미늄은 뚜렷한 항복점을 보이지 않는 특징이 있다. 이에 따라 항복 강도는 탄성 구간에서 0.2% 오프셋하여 정의하였다.
3. 원뿔 컵 형상의 점진적 판재 성형 공정
3.1 실험 장치
시편의 크기는 150 × 150 mm이며 두께는 1mm이다. 실제시편에서 성형 가능한 크기는 블랭크 홀더의 너비를 제외한 100 × 100 mm이다. 시편의 형상과 규격의 개략도는 Fig. 5와 같다.
점진적 판재 성형의 실험을 진행하기 위해 CNC 가공기, 공구, 블랭크 홀더를 사용하였다. CNC 가공기는 X, Y, Z축으로 제어되며 Z축 방향으로 베드가 이동한다. Fig. 6은 본 실험에서의 실험 장치이다. 8 mm의 공구를 사용하였고 150 × 150 mm인 블랭크 홀더를 사용하였다. 윤활유는 순수 오일과 첨가제가 추가된 내연 기관용 오일(SAE 5W-30)을 사용하였다.
3.2 실험 조건
본 실험에서 사용된 이송 속도는 2,000 mm/min, 공구 각 속도는 200 rpm이다. 2차 점진 성형에서는 적절한 이송 속도와 공구 각 속도를 사용하지 않으면 파단이 발생한다,9,10 본 연구에서는 점진적 판재 성형의 성형 공정변수의 영향에 대해서만 분석하였다.
점진적 판재 성형에서 원뿔 컵 형상을 성형하기 위한 공구 경로는 Fig. 7과 같다. 위의 공구 경로는 진입 반지름(Rin), 이탈 반지름(Rout), 성형 각도(θh), 1회전당 수직 거리(Δz)의 공정변수로 제어한다. 점진적 판재 성형에서 디스크 형상을 성형하기 위한 공구 경로는 Fig. 8과 같다. 디스크 형상의 공구 경로는 원뿔 컵 형상의 단면변형이 발생한 구역을 추가로 가공하여 형상 오차를 저감할 수 있다. 위의 공구 경로는 진입 반지름, 이탈 반지름, 공구의 진입 깊이(ZD), 1회전당 수직 거리의 공정변수로 제어한다.
공구의 진입 깊이는 형상 오차를 저감하기 위한 본 연구에서 제안한 공정변수이다. 공구의 진입 깊이는 XY 평면을 기준으로 정의하였다. XY 평면은 원뿔 컵 형상을 성형한 후에 시편을 180° 회전한 바닥부이다. 즉 공구의 진입 위치부터 XY 평면까지의 거리가 공구의 진입 깊이이다.
제품 성형 후 형상 측정은 3D-DIC를 사용하여 시편을 스캔하였다. 스캔 시 시편의 측정 범위는 시편 끝단의 중심점을 기준점으로 하여 시편의 윗면을 측정하였다.
4. 원뿔 컵 형상의 성형 공정변수에 따른 점진적 판재 성형의 실험
4.1 실험 조건
원뿔 컵 형상의 성형 공정변수 중 진입 반지름, 이탈 반지름, 성형 각도에 따른 단면변형의 특성을 파악하였다. Table 2(a)는 이탈 반지름에서 30, 20, 10 mm의 변수를 갖는 실험 조건이다. Table 2(b)는 진입 반지름에서 40, 35, 30, 25 mm의 변수를 갖는 실험 조건이다. Table 2(c)는 성형 각도에서 60, 55, 50, 45°의 변수를 갖는 실험 조건이다. 위의 실험 조건으로 각각의 변수에 따른 단면변형의 특성을 파악할 수 있다. 모든 실험 조건에서 1회전당 수직 거리는 0.3 mm로 고정하였다.
4.2 측정 방법
Fig. 9는 원뿔 컵 형상의 성형 공정변수에 따른 단면변형의 특성을 파악하기 위한 측정 방법의 개략도이다. 기준면은 시편을 뒤집었을 때 최상단의 면이다. 위의 면은 점진적 판재 성형에서 성형의 영향을 가장 받지 않는 지역이기 때문에 기준면으로 정의하였다. 성형 높이(h)는 위의 기준면으로부터 시편의 윗면까지의 높이이다. 단면변형의 발생 지역은 원뿔 컵 형상을 성형하기 위해 공구가 시편에 최초로 접촉하는 지점의 윗면부터 블랭크 홀더까지의 거리이다. 위의 지역은 공구가 시편에 접촉하지 않는 지역이다. 따라서 단면변형이 발생하는 지역으로 판단하기에 적합하다.
4.3 이탈 반지름(Rout)에 따른 실험 결과
Fig. 10은 이탈 반지름값 10, 20, 30 mm에 따른 실험 결과이다. 중심축으로부터 거리와 성형 높이의 관계로 이탈 반지름에 따른 단면 형상은 Fig. 11과 같다. 위의 단면 형상은 시편의 압연 방향이다.
이탈 반지름에 따른 단면변형의 특성을 파악하기 위해 이탈 반지름과 성형 높이의 관계를 Fig. 12와 같이 나타내었다. 그 결과 이탈 반지름에 따라 형상 오차가 큰 차이를 보이지 않았다.
4.4 진입 반지름(Rin)에 따른 실험 결과
Fig. 13은 진입 반지름값 40, 35, 30, 25 mm에 따른 실험 결과이다. 중심축으로부터 거리와 성형 높이의 관계로 진입 반지름에 따른 단면 형상은 Fig. 14와 같다. 위의 단면 형상은 시편의 압연 방향이다. 단면변형의 발생 지역은 진입 반지름에 따라 다르다. 따라서 단면변형의 발생 지역을 중심축으로부터 40과 50 mm 사이의 거리로 정의하였다. 이 지역에서 성형 높이로 단면변형의 영향을 확인하였다.
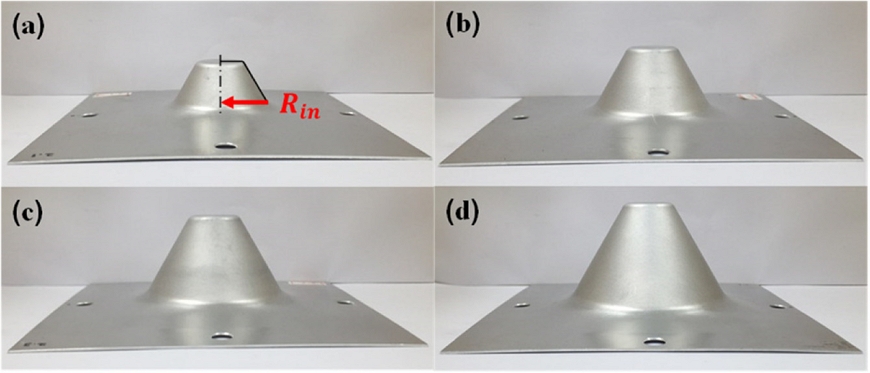
Experiment results of incremental forming of cup shape when Rin is (a) 40 (b) 35 (c) 30 and (d) 25 mm
진입 반지름에 따른 단면변형의 특성을 파악하기 위해 진입 반지름과 성형 높이의 관계를 Fig. 15에 나타내었다. 그 결과 진입 반지름이 증가함에 따라 단면변형이 크게 발생하는 것을 확인할 수 있었다. 따라서 진입 반지름이 증가함에 따라 형상 오차가 증가함을 알 수 있다
4.5 성형 각도(θh)에 따른 실험 결과
Fig. 16은 성형 각도 값 60, 55, 50, 45o에 따른 실험 결과이다. 중심축으로부터 거리와 성형 높이의 관계로 성형 각도에 따른 단면 형상은 Fig. 17과 같다. 위의 단면 형상은 시편의 압연 방향이다. 단면변형의 발생 지역은 중심축으로부터 40과 50mm 사이의 거리이다. 이 지역에서의 성형 높이로 단면변형의 영향을 확인하였다. 그 결과 성형 각도에 따라 성형 높이의 차이가 발생하였다.
성형 각도에 따른 단면변형의 특성을 파악하기 위해 성형 각도와 성형 높이의 관계를 Fig. 18에 나타내었다. 그 결과 진입 반지름에 따른 실험 결과와 유사한 결과를 도출하였다. 성형 각도가 증가함에 따라 단면변형이 크게 발생하는 것을 확인할 수 있었다. 따라서 성형 각도가 증가함에 따라 형상 오차가 증가함을 알 수 있다.
5. 원뿔 컵 형상의 형상 오차를 저감하는 성형 공정변수에 따른 2차 점진적 성형 공정의 실험
5.1 실험 조건
본 실험은 원뿔 컵 형상을 성형하기 위한 1차 점진 성형과 디스크 형상을 성형하기 위한 2차 점진 성형으로 진행하였다. 2차 점진 성형에서는 1차 점진 성형 후 소재를 180o 회전하여 성형하지만 1차 점진 성형과 동일한 좌표계를 이용한다. 2차 점진 성형 공정을 적용함으로써 원뿔 컵 형상에서 형상 오차의 저감 가능성을 분석하였다.
본 연구에서는 1차 점진 성형의 형상은 고정하고 2차 점진 성형에서 공구의 진입 깊이에 따른 형상 오차의 특성을 파악하였다. Table 3(a)는 1차 점진 성형의 실험 조건이다. Table 3(b)는 2차 점진 성형의 실험 조건으로 공구의 진입 깊이가 공정변수이다. 위의 조건으로 공구 진입 깊이에 따른 스커트부에서 발생하는 스프링백(θ)의 영향을 확인하였다.
2차 점진 성형의 진입 반지름은 블랭크 홀더의 너비를 제외한 소재의 반너비에서 공구의 반경과 여유 공차인 1 mm를 제외한 45 mm이다.
또한 2차 점진 성형의 이탈 반지름은 1차 점진 성형의 진입 반지름에 공구의 반경을 추가한 39 mm이다.
5.2 측정 방법
Fig. 19는 공구의 진입 깊이에 따른 형상 오차의 특성을 파악하기 위한 측정 방법의 개략도이다. 형상 측정의 기준면은 시편을 뒤집었을 때 최상단의 면이다. 성형 높이는 위의 기준면으로부터 시편의 윗면까지의 높이이다. 스커트부의 스프링백은 2차 점진 성형에서 공구가 시편에 최초로 접촉하는 지점과 끝점의 사이각으로 정의하였다.
5.3 실험 결과
Fig. 20은 1차 점진 성형만 진행한 시편과 2차 점진 성형에서 공구의 진입 깊이에 따른 실험 결과이다. 중심축으로부터 거리와 성형 높이의 관계로 공구의 진입 깊이 에 따른 단면 형상은 Fig. 21과 같다. 위의 단면 형상은 시편의 압연 방향이다. 그 결과 공구의 진입 깊이가 증가함에 따라 스커트부의 스프링백이 감소하는 것을 확인할 수 있다.
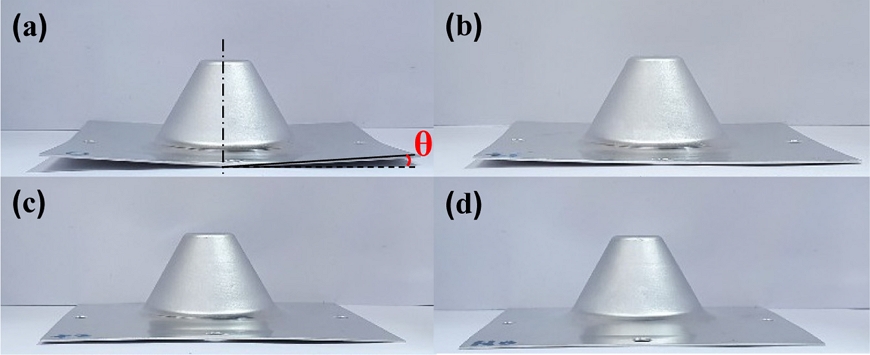
Experimental results in 1st+2nd incremental forming when ZD is (a) 0 (b) 1 (c) 2 mm and (d) 1st incremental forming
Fig. 22는 공구의 진입 깊이와 스커트부의 스프링백의 관계이다. 여기에서 공구의 진입 깊이와 스프링백 각도의 관계를 식(1)과 같이 3차식으로 피팅하였다. 그리고 이 식(1)을 통해 스프링백의 각도를 최소화할 수 있는 공구의 진입 깊이를 도출하였다.
(1) |
식(1)에서 θ = 0o일 때 공구의 진입 깊이 ZD= 1.63 mm를 도출할 수 있다.
1차 점진 성형 후 스커트부의 스프링백 각도는 -5.82o이다. 또한 2차 점진 성형에서 공구의 진입 깊이가 1.63mm일 때 스커트부의 스프링백 각도는 0.17o이다. 따라서 2차 점진적 성형 공정을 통해 스커트부의 스프링백 감소를 확인하였다. 중심축으로부터 거리와 성형 높이의 관계로 1차 점진 성형과 2차 점진 성형의 단면 형상은 Fig. 23과 같다.
6. 고찰
원뿔 컵 형상의 성형 공정변수 중 진입 반지름을 제외한 다른 공정변수를 고정하면 이는 원뿔 컵 형상의 성형 높이를 제어하는 것과 같다. 이에 따라 Fig. 12에서 이탈 반지름에 따라 형상 오차가 뚜렷하게 나타나지 않으므로 성형 높이에 따라 형상 오차가 일정하다는 것을 알 수 있다.
하지만 진입 반지름과 성형 각도(θh)는 공구가 판재에 접촉하는 위치에 의해 결정된다. Fig. 15에서 진입 반지름에 따라, Fig. 18에서 성형 각도에 따라 형상 오차의 차이를 보였다. 따라서 점진적 판재 성형에서 성형 시 발생하는 단면변형은 성형 중에 발생하는 것보다 공구와 판재가 최초로 접촉하는 위치에서 발생한다는 것을 알 수 있다.
점진 성형 공정에서는 컵 형상의 성형 각도가 증가함에 따라 소성 변형율이 증가한다.3 따라서 성형 각도가 증가함에 따라 성형품의 형상 오차 및 스프링백이 증가하는 것으로 분석할 수 있다. 이탈 반지름(성형 높이)는 컵 형상 벽면에서 일정한 소성 변형율이 발생하므로 형상 오차는 동일한 것을 알 수 있다. 진입 반지름이 큰 경우 재료의 바깥쪽에서부터 변형이 발생하여 소재의 변형량이 더 많다. 따라서 이 경우에도 재료의 형상 변형이 증가한다.
이와 같은 형상 오차를 저감하기 위해 2차 점진적 성형 공정을 적용하였고 형상 오차의 저감에 효과적인 것을 확인하였다.
본 연구에서는 형상 오차를 저감하기 위한 2차 점진 성형에서 최적 공구의 깊이를 도출하여 스커트부의 스프링백을 저감하였다.
하지만 2차 점진 성형 후에도 Fig. 21과 같이 중심축으로부터 35와 39 mm사이의 거리에서 발생하는 단면변형을 저감하기에는 한계가 있다. 위의 거리는 공구의 반경이며 더이상 진입 시에는 성형품을 파손할 수 있기 때문이다.
또한 2차 점진 성형 후에는 Fig. 23과 같이 스커트부의 위치가 CAD Data보다 높아진다. 이에 따라 원뿔 컵 형상의 최종 성형 높이의 차이가 발생하게 된다. 현재 이와 관련한 연구를 진행하고 있다.
7. 결론
본 연구에서는 알루미늄(Al5052) 판재를 이용한 점진적 판재 성형에서 성형 공정변수에 따른 원뿔 컵 형상의 형상 오차 및 특성을 비교 분석하였다. 연구 결과는 다음과 같다.
(1) 원뿔 컵 형상의 성형 공정변수에 따라 단면변형이 발생하는 특성을 파악하였다. 성형 공정변수 중 진입 반지름과 성형 각도가 증가함에 따라 형상 오차가 증가한다. 하지만 이탈 반지름은 일정한 형상 오차가 발생한다.
(2) 원뿔 컵 형상의 형상 오차를 저감하는 성형 공정변수 중 공구의 진입 깊이에 따른 스커트부의 스프링백의 특성을 파악하였다. 공구의 진입 깊이가 증가함에 따라 스커트부의 스프링백이 감소한다. 따라서 3차 다항식을 통해 최적 공구의 진입 깊이 값을 도출하여 형상 오차를 저감할 수 있음을 알 수 있다.
NOMENCLATURE
Rin : | Enter radius |
Rout : | Exit radius |
θh : | Forming angle |
Δz : | Step down size |
ZD : | Entering depth of tool |
H : | Forming height |
Θ : | Spring back angle in skirt region |
Δ : | Region of section deflection |
Acknowledgments
본 연구는 서울과학기술대학교 교내연구비의 지원으로 수행되었습니다.
References
-
Emmens, W., Sebastiani, G., and Van Den Boogaard, A. H., “The Technology of Incremental Sheet Forming-A Brief Review of the History,” Journal of Materials Processing Technology, Vol. 210, No. 8, pp. 981-997, 2010.
[https://doi.org/10.1016/j.jmatprotec.2010.02.014]
-
Yang, D. Y., Bambach, M., Cao, J., Duflou, J., Groche, P., et al., “Flexibility in Metal Forming,” CIRP Annals, Vol. 67, No. 2, pp. 743-765, 2018.
[https://doi.org/10.1016/j.cirp.2018.05.004]
-
Jeswiet, J., Micari, F., Hirt, G., Bramley, A., Duflou, J., et al., “Asymmetric Single Point Incremental Forming of Sheet Metal,” CIRP Annals, Vol. 54, No. 2, pp. 88-114, 2005.
[https://doi.org/10.1016/S0007-8506(07)60021-3]
-
Kim, Y. and Park, J., “Effect of Process Parameters on Formability in Incremental Forming of Sheet Metal,” Journal of Materials Processing Technology, Vols. 130-131, pp. 42-46, 2002.
[https://doi.org/10.1016/S0924-0136(02)00788-4]
-
Bambach, M., Araghi, B. T., and Hirt, G., “Strategies to Improve the Geometric Accuracy in Asymmetric Single Point Incremental Forming,” Production Engineering, Vol. 3, No. 2, pp. 145-156, 2009.
[https://doi.org/10.1007/s11740-009-0150-8]
-
Kopac, J. and Kampus, Z., “Incremental Sheet Metal Forming on CNC Milling Machine-Tool,” Journal of Materials Processing Technology, Vols. 162-163, pp. 622-628, 2005.
[https://doi.org/10.1016/j.jmatprotec.2005.02.160]
- Jung, K. S., You, J. H., Chung, W. J., and Lee, C. W., “Incremental Forming Method and Incremental Forming Apparatus,” KR Patent, 10-2018-0172398, 2018.
-
Nguyen, V. T., Kwon, S. J., Kwon, O. H., and Kim, Y. S., “Mechanical Properties Identification of Sheet Metals by 2D-Digital Image Correlation Method,” Procedia Engineering, Vol. 184, pp. 381-389, 2017.
[https://doi.org/10.1016/j.proeng.2017.04.108]
-
Hamilton, K. and Jeswiet, J., “Single Point Incremental Forming at High Feed Rates and Rotational Speeds: Surface and Structural Consequences,” CIRP Annals, Vol. 59, No. 1, pp. 311-314, 2010.
[https://doi.org/10.1016/j.cirp.2010.03.016]
- Jung, K. S., Chung, W. J., and Lee, C. W., “A Study on the Cross-Sectional Shape of Incremental Sheet Forming according to the Forming Process,” Proc. of the Korean Society for Technology of Plasticity Conference, p. 82, 2018.
Kyu-Seok Jung received M.E. degree in department of mechanical design and manufacturing engineering in Seoul national university of Science and Technology.
E-mail: ksjung@seoultech.ac.kr
Jae-Hyeong Yu received M.E degree in department of mechanical design and manufacturing engineering in Seoul national university of Science and Technology.
E-mail: jhyu9190@Seoultech.ac.kr
Professor in the department of mechanical system and design engineering, Seoul National University of Science and Technology. His research interests include simulation (FEM) and sheet metal forming.
E-mail: wjchung@seoultech.ac.kr
Assistant professor in the department of mechanical system and design engineering, Seoul National University of Science and Technology. His research interests include simulation and development of the metal forming process and lightweight materials.
E-mail: cwlee@seoultech.ac.kr