
다결정 다이아몬드를 이용한 초경합금의 마이크로 핀 가공
Copyright © The Korean Society for Precision Engineering
This is an Open-Access article distributed under the terms of the Creative Commons Attribution Non-Commercial License (http://creativecommons.org/licenses/by-nc/3.0) which permits unrestricted non-commercial use, distribution, and reproduction in any medium, provided the original work is properly cited.
Abstract
Micro tool fabrication is crucial in micro machining. Wire electro-discharge grinding (WEDG) is one of the popular methods applied to fabricate micro tools used for micro electrical discharge machining (EDM), electrochemical machining (ECM), and ultrasonic machining (USM). WEDG can machine micro tools or features regardless of workpiece hardness. In WEDG, however, the machining speed is relatively low and the discharge gap control is not easy. In this study, the micro mechanical machining using the polycrystalline diamond is introduced to fabricate the micro cylindrical tool or micro pin of the tungsten carbide. This method demonstrates the possibility of applying ductile machining of tungsten carbide without brittle fracture or cracks. This paper compared the machining characteristics such as material removal rate and surface roughness with the PCD-mechanical machining and WEDG.
Keywords:
Micro pin, Polycrystalline diamond, Mechanical machining, Wire electro-discharge grinding, Tungsten carbide키워드:
미세 핀, 다결정 다이아몬드, 기계가공, 와이어 방전 연삭, 초경합금1. 서론
최근 IT-디스플레이 산업과 고정밀 기계 부품산업에서 초정밀 몰드 및 다이의 수요가 높아지면서 고경도 난삭재의 미세 형상 가공이 중요해지고 있다.1 제품의 높은 정밀도와 생산성에 부합하기 위해 사용되는 소재가 초경합금이나 인코넬 등의 고경도 난삭재로 점차 바뀌고 있어 미세 형상 가공의 난이도가 매우 높아지고 있다. 고경도 소재의 미세 형상 가공 기술로 레이저가공, 절삭가공, 방전가공, 전해가공, 연삭가공 등 다양한 종류의 기술이 소개되어 있으며 많은 연구가 되고 있다.2,3 레이저 가공의 경우 레이저 광원을 이용하는 방법이지만, 절삭, 방전가공, 전해가공 등은 공구를 사용하는 가공법이므로 이들 방법으로 미세 형상 가공을 위해서는 미세한 공구 제작이 필수적이다.4,5 미세 공구는 크기가 작아지면 작아질수록 허용할 수 있는 절삭력이나 하중이 줄어들게 되어 가능한 높은 강도와 경도를 지닌 공구 재료가 필요하게 된다. 절삭이나 연삭과 같은 접촉식 가공뿐만 아니라 방전, 전해가공과 같이 비접촉 가공에서도 실제 공정에서는 공구가 가공물에 접촉하는 경우가 빈번히 발생하므로 높은 경도의 초경합금이 많이 사용되어 왔다. 초경합금을 수십 또는 수백 마이크로미터 크기의 공구로 쉽게 가공할 수 있는 방법으로 다양한 기술이 개발되어왔다. Masuzawa는 와이어 가이드에 방전 와이어를 이송시켜 와이어의 진동을 최대한 억제시킨 상태에서 미세 공구를 제작하는 방법으로 초경합금 등에 직경 50 μm 이하의 공구를 제작한 바가 있으며 이를 와이어 방전 연삭(Wire Electro-Discharge Grinding, WEDG)라 명명하였다.6 이 방법은 와이어 방전가공의 일종으로, 마이크로 가공에서 필요한 미세 공구를 제작하는 방법 중 가장 많이 사용되고 있다. 또한 Mohri 등은 와이어 대신 금속 판전극을 이용하여 방전가공으로 미세 실린더 형상의 공구를 제작하였다.7 Kunieda는 전해액을 분사하여 가공물 재료의 전해 용출을 일으키는 일종의 전해가공법으로 미세 공구 형상을 제작한 예가 있다.8 Ohmori는 연삭기술을 이용하여 수십 마이크로의 실린더나 각형의 초경합금 미세 공구를 제작한 바가 있다.9,10 이와 같이 미세 가공에 필요한 정밀한 미세 공구를 보다 효율적으로 제작하기 위해 다양한 가공법이 연구되어왔다. 한편 다결정 다이아몬드(Poly Crystalline Diamond, PCD)는 단결정 다이아몬드보다 경도는 떨어지지만 초경합금보다 높은 경도를 지니고 있어 PCD를 밀링 공구로 제작하여 초경합금 가공에 쓰일 수 있다. Suzuki 등은 PCD로 마이크로 밀링 공구를 제작하여 글래스 몰딩을 위한 초경합금 금형을 제작하였으며, Nakamoto는 초경합금 가공에서 PCD 공구의 마모 및 가공 품질에 대해 연구하였다.11,12
본 논문에서는 미세 공구 형상을 가공하기 위해 방전가공 처리한 PCD를 공구로 사용하여 초경합금에 미세 핀 형상을 가공하였으며, 기존 WEDG 방법과 재료제거율(Material Removal Rate, MRR)과 가공 표면을 비교 분석하였다.
2. 실험 방법
본 연구에서는 초경합금 재질의 미세 핀 형상 가공을 위해 기존 연삭(Grinding)과 유사한 방법을 사용하였다. Fig. 1(a)는 앞서 설명한 와이어 방전 연삭(WEDG)과 본 논문에서 사용한 미세 핀 가공 방법을 비교한 그림이다. 와이어가 주행하는 상태에서 가공물 재료(Workpiece)가 회전하면서 아래로 이송하면 와이어와 가공물 사이에 방전이 발생하여 가공되는 원리이다. Fig. 1(b)는 본 논문에서 사용한 방법을 나타낸 것으로서 초경합금과 같은 고경도 소재를 가공하기 위한 공구로서 PCD를 사용하였으며 이 PCD 공구의 표면은 미리 방전가공으로 거칠게 만들었다. 즉 방전가공으로 PCD 소재를 가공하여 방전흔(Crater)으로 표면을 거칠게 만들었다. 이러한 거친 표면의 돌기는 하나 하나가 미세한 절삭날 역할을 하게 된다. 가공물을 회전시키면서 PCD쪽으로 이송시키면 결과적으로 PCD 표면에 절삭날이 여러 개가 존재하기 때문에 가공물이 조금씩 제거된다. 즉, 연삭휠이 고정되어 있고 가공물이 회전하여 가공되는 연삭 공정과 동일하다고 볼 수 있다. 이 방법은 PCD 표면에 절삭날이 많아 가공 효율이 높으며, 상대적으로 공구 마모가 적고 가공물 표면 조도를 높일 수 있는 장점이 있다. 또한 트루잉(Truing)이나 드레싱(Dressing)을 미세 방전가공으로 할 수 있어 쉽게 거친 표면을 재생시킬 수 있는 장점이 있다.
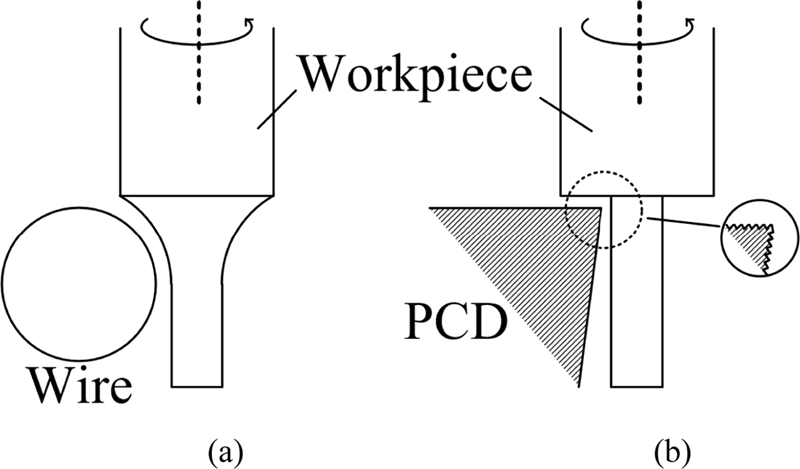
Schematic diagram of (a) Wire electro-discharge grinding (WEDG) and (b) PCD mechanical machining for micro circular pin
Fig. 2(a)는 PCD를 이용한 미세 핀 가공의 개략도이며, Fig. 2(b)는 실제 핀 가공에 사용한 PCD의 SEM 사진이다. 사진에서 볼 수 있듯이 모서리 부분이 선삭 공구와 달리 날카롭지 않으며 대신 방전가공으로 생긴 방전흔으로 인해 거친 것을 알 수 있다. 전술하였듯이 이러한 거친 요철이 연삭공구와 비슷한 역할을 하는 것으로 판단된다. 또한 절삭이 일어나는 모서리는 90°의 각도를 이루도록 가공하였다.
Fig. 3(a)는 PCD를 이용하여 초경합금에 지름 650 μm의 핀 형상을 가공한 SEM 사진이며, Fig. 3(b)는 광학 사진이다. 가공물인 초경합금은 텅스텐 카바이드 입자 크기는 0.2 μm이며, 코발트(Co)를 17%를 포함하고 있다. 가공 조건으로 초경합금 재료(Rod)를 30,000 rpm으로 회전시켰으며, 반경 방향 절입량은 5 μm, 이송속도는 20 μm/s으로 가공하였다. Fig. 3(c)는 가공 표면의 SEM 사진이며 초경합금의 탄화 텅스텐(WC) 입자가 절단된 것을 관찰할 수 있어 초경합금이 취성 재질임에도 불구하고 연성 모드(Ductile Mode)로 가공된 것을 확인할 수 있다. 고경도 취성 재료인 초경합금이 우수한 표면 품질로 무리 없이 가공할 수 있음을 확인하였으며 가공 조건에 따라 재료제거율과 표면 조도를 측정하여 기존 와이어 방전 연삭 방법과 비교하였다.
3. PCD 연삭가공과 방전가공과의 비교
3.1 재료제거율
PCD를 이용한 기계가공과 와이어 방전 연삭의 재료제거율을 비교하였다. 초경합금 환봉을 회전 런아웃을 제거하기 위해 지름 400 μm으로 가공한 후, 동일한 절입량으로 PCD 기계가공과 와이어 방전 연삭으로 가공하였다.
초경합금의 회전속도는 30,000 rpm으로 설정하였으며, 반경 반향 절입량(Depth of Cut, DOC)은 10 μm로 설정하였다. 기계가공의 경우 이송속도를 30에서 150 μm/s로 변화시켰다. 이송속도가 높아질수록 진동이 발생하는 것이 관찰되었으며 PCD의 고정 방법, 초경합금 환봉 크기에 따른 강성, 절입량, 이송속도에 따라 달라질 것으로 판단된다. WEDG의 경우 인가전압 100V, 축전용량 2000 pF으로 가공하였으며 이송속도는 1-5 μm/s으로 설정하였으나 방전가공 특성상 가공 중에 발생하는 단락 및 지연 등으로 인해 실제 가공속도는 0.76 μm/s으로 측정되었다. 방전가공에서 축전용량을 크게 하면 가공속도는 증가할 수 있으나 표면 품질이 매우 저하가 되고, 형상 정밀도 측면에서 불리하기 때문에 본 실험에서는 2,000 pF의 축전용량을 사용하였다.
Table 1은 PCD를 이용한 기계가공의 가공 조건이며, Table 2는 와이어 방전 연삭의 가공 조건을 나타낸다. Table 1에서 볼 수 있듯이 기계가공의 재료제거율이 와이어 방전 연삭보다 30에서 150배 이상 높은 것을 볼 수 있다. 하지만 이는 절입량이 10 μm인 경우에만 한하며 수치적으로 단순 비교하기엔 무리가 있다. 기계가공의 경우 절입량이 100 μm 이상 커지게 되면 진동이나 공구 마모 및 파손 등으로 이어질 가능성이 크지만 방전가공은 비접촉 가공이므로 절입량을 크게 할 수 있어 절대적인 값은 가공 조건에 따라 달라질 여지가 많다. 다만, 초정밀 마이크로 가공에서는 기본적으로 절입량이 크지 않고 재료제거량도 작기 때문에 이 경우 PCD 기계가공이 생산성이 훨씬 높을 것으로 판단된다. 또한 Table 1에서 볼 수 있듯이 회전당 이송량(Feed per Revolution)이 수십에서 수백 나노미터에 불과하여 높은 표면 조도와 안정적인 가공을 기대할 수 있다
3.2 가공 표면
초경합금을 Tables 1과 2의 조건으로 가공한 후 표면 거칠기를 비교하였다. Fig. 4(a)는 방전가공으로 가공한 가공 표면이며, 사진과 같이 대략 지름 10 μm의 방전흔으로 덮여있는 것을 볼 수 있다. 방전흔의 크기는 방전에너지, 즉 사용된 인가전압과 축전용량에 따라 달라지며 가공 방식이나 가공물의 회전 유무 등에 따라 모양이 달라질 수 있다. Fig. 4(b)는 방전가공 표면 형상을 공초점 현미경(OLS-5000, Olympus Corp.)을 사용하여 측정한 결과이며 표면 조도는 0.319 μm (Ra)로 측정되었다.
Fig. 5(a)는 PCD를 이용하여 가공한 표면의 SEM 사진이다. 취성재료임에도 불구하고 절삭흔(Cutting Mark)이 관찰되어 연성 모드로 가공된 것을 알 수 있으며 절삭흔의 간격은 이송속도에 비례하여 관찰되었다. Fig. 5(a)에서 볼 수 있듯이 부분적으로 균일하지 못한 표면도 존재하였으며 이는 가공 시 발생하는 진동으로 인한 것으로 보인다. 미세 형상 가공에서 필연적으로 가공물의 강성이 매우 낮을 수 밖에 없으므로 적절한 가공 조건의 선정이 중요하며 추가적인 연구가 필요하다. Fig. 5(b)는 가공 표면 형상을 측정한 결과이며 표면 조도는 Ra 0.096 μm로 방전가공 표면보다 우수한 것으로 나타났다.
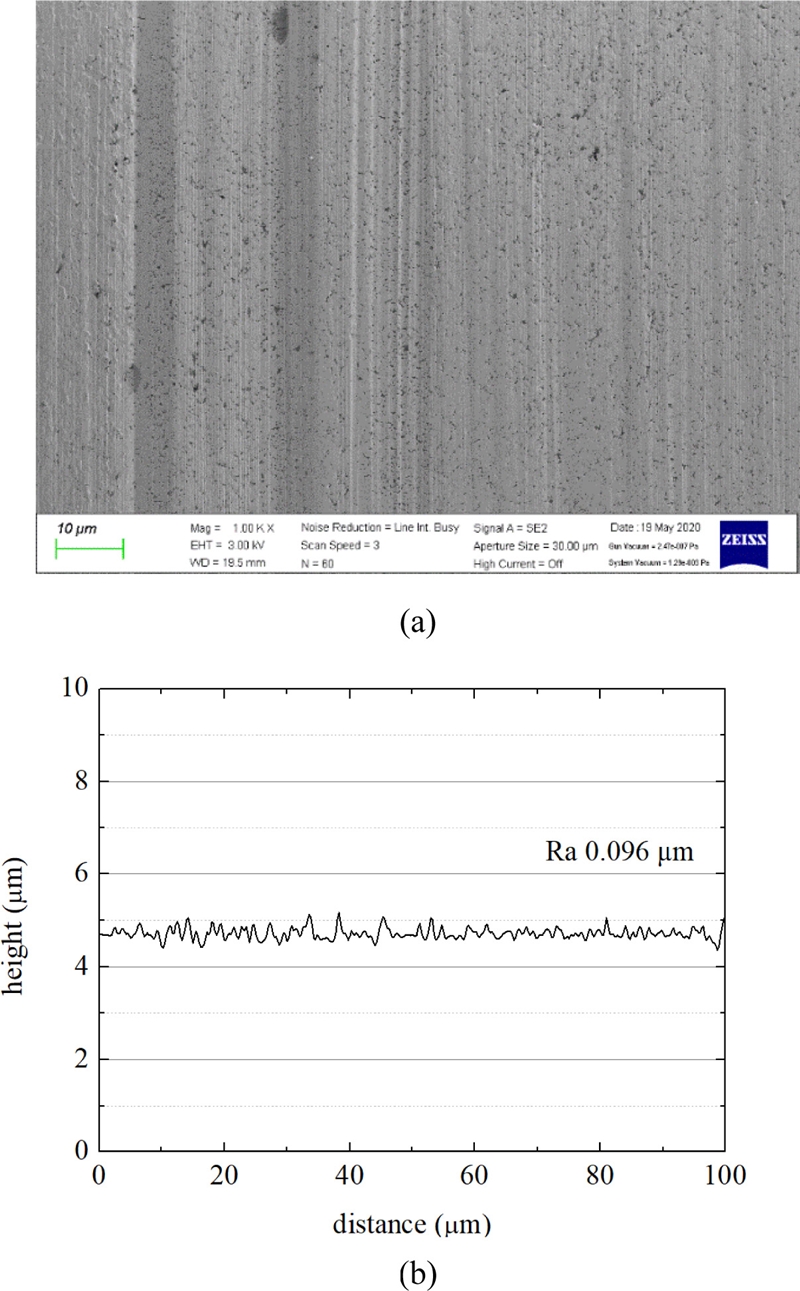
(a) SEM image of mechanical machined surface (Feedrate 30 μm/s, DOC 10 μm, 30,000 rpm) and (b) Surface profile
Fig. 6(a)는 PCD 기계가공을 이용하여 초경합금에 지름 380 μm의 미세 핀 형상을 가공한 예이며 전체적으로 방전가공에 비해 비교적 높은 표면 품질과 진직도를 보이고 있다. Fig. 6(b)는 다단 형상의 원형 핀을 가공한 예이며, 가공 길이와 절입량을 제어하여 4단의 형상을 가공하였다. 형상 프로파일에서 알 수 있듯이 PCD의 모서리나 옆면뿐만 아니라 윗면에서도 가공이 일어난 것을 확인할 수 있다. 가장 작은 부분의 지름은 약 50 μm로서 초경합금을 기계적 가공으로 수십 마이크로미터까지 가공할 수 있음을 보이고 있다.
4. 결론
본 연구에서는 초경합금의 미세 핀 형상을 제작하기 위해 다결정 다이아몬드(PCD)를 공구로 사용한 기계적 가공 가능성에 대해 연구하였다. 고경도 취성재료인 초경합금을 가공하기 위해 이보다 높은 경도의 PCD를 사용하였으며 방전가공으로 PCD 표면에 방전흔을 만들어 이를 절삭날로 사용하였다. 이 방전흔으로 초경합금이 크랙이나 취성파괴 없이 연성 모드로 가공됨을 보였다. 기본적으로 선삭과 비슷한 공정이나 공구의 거친 면으로 재료를 제거하는 것이므로 결과적으로 연삭 공정이라 할 수 있으며 표면 조도가 우수한 특징을 보였다. 일반적으로 초경합금의 미세 공구나 미세 핀 형상을 가공할 때 많이 사용하는 와이어 방전 연삭 또는 와이어 방전가공의 재료제거율과 표면 거칠기를 비교하였으며 10 μm의 반경 방향 절입량에서 방전가공보다 수십배 이상 높은 가공 속도를 보였으며 표면 조도도 우수한 것으로 나타났다. 와이어 방전 연삭은 초경합금과 같이 높은 경도의 재료도 쉽게 가공할 수 있는 장점이 있으나, 가공물과 와이어 사이의 간극 제어가 쉽지 않다. 특히 표면 조도 향상을 위해 방전 에너지를 줄이는 경우 단락이 빈번하게 발생하여 가공 효율이 떨어지며 절입량이 많은 경우에도 마찬가지 문제가 발생한다. 이에 반해 PCD 기계가공은 가공 공정이 비교적 단순하여 미세 공구 제작에 쉽게 적용할 수 있을 것으로 판단된다. PCD를 이용한 기계 가공 시 절삭력 측정은 가공물 파손, 가공 속도 최적화 등에 매우 중요하며 PCD의 마모 또한 매우 중요한 요소이므로 이에 대한 추가 연구가 수행될 예정이다.
Acknowledgments
이 연구는 2020년도 산업통상자원부 및 산업기술평가관리원(KEIT) 연구비 지원에 의한 연구임(No. 20010984).
REFERENCES
-
Masuzawa, T., “State of the Art of Micromachining,” CIRP Annals, Vol. 49, No. 2, pp. 473-488, 2000.
[https://doi.org/10.1016/S0007-8506(07)63451-9]
-
Rajurkar, K. P., Levy, G., Malshe, A., Sundaram, M. M., McGeough, J., et al., “Micro and Nano Machining by Electro-Physical and Chemical Processes,” CIRP Annals, Vol. 55, No. 2, pp. 643-666, 2006.
[https://doi.org/10.1016/j.cirp.2006.10.002]
-
Lee, P. A, Nam, E., and Kim, B. H., “The State of the Art in Electrochemical Micro Machining Technologies,” Journal of the Korean Society for Precision Engineering, Vol. 35, No. 3, pp. 229-239, 2018.
[https://doi.org/10.7736/KSPE.2018.35.3.229]
-
Chung, D. K., Park, J. S., and Kim, K. H., “Micro Machining of CFRP Using Nanosecond Pulsed Fiber Laser,” Journal of the Korean Society for Precision Engineering, Vol. 36, No. 9, pp. 783-791, 2019.
[https://doi.org/10.7736/KSPE.2019.36.9.783]
-
Na, Y. and Kim, B. H., “Effect of Vibration and Machining Area in the Fabrication of Micro Tool by Reverse EDM,” Journal of the Korean Society for Precision Engineering, Vol. 36, No. 2, pp. 169-175, 2019.
[https://doi.org/10.7736/KSPE.2019.36.2.169]
-
Masuzawa, T., Fujino, M., Kobayashi, K., Suzuki, T., and Kinoshita, N., “Wire Electro-Discharge Grinding for Micro-Machining,” CIRP Annals, Vol. 34, No. 1, pp. 431-434, 1985.
[https://doi.org/10.1016/S0007-8506(07)61805-8]
-
Mohri, N. and Tani, T., “Micro-Pin Electrodes Formation by Micro-Scanning EDM Process,” CIRP Annals, Vol. 55, No. 1, pp. 175-178, 2006.
[https://doi.org/10.1016/S0007-8506(07)60392-8]
-
Miyoshi, K. and Kunieda, M., “Fabrication of Micro Rods of Cemented Carbide by Electrolyte Jet Turning,” Procedia CIRP, Vol. 42, pp. 373-378, 2016.
[https://doi.org/10.1016/j.procir.2016.02.201]
-
Ohmori, H., Katahira, K., Uehara, Y., Watanabe, Y., and Lin, W., “Improvement of Mechanical Strength of Micro Tools by Controlling Surface Characteristics,” CIRP Annals, Vol. 52, No. 1, pp. 467-470, 2003.
[https://doi.org/10.1016/S0007-8506(07)60627-1]
-
Onikura, H., Ohnishi, O., Take, Y., and Kobayashi, A., “Fabrication of Micro Carbide Tools by Ultrasonic Vibration Grinding,” CIRP Annals, Vol. 49, No. 1, pp. 257-260, 2000.
[https://doi.org/10.1016/S0007-8506(07)62941-2]
-
Suzuki, H., Moriwaki, T., Yamamoto, Y., and Goto, Y., “Precision Cutting of Aspherical Ceramic Molds with Micro PCD Milling Tool,” CIRP Annals, Vol. 56, No. 1, pp. 131-134, 2007.
[https://doi.org/10.1016/j.cirp.2007.05.033]
-
Nakamoto, K., Katahira, K., Ohmori, H., Yamazaki, K., and Aoyama, T., “A Study on the Quality of Micro-Machined Surfaces on Tungsten Carbide Generated by PCD Micro End-Milling,” CIRP Annals, Vol1, No. 1, pp. 567-570, 2012.
[https://doi.org/10.1016/j.cirp.2012.03.112]
Undergraduate student in the School of Mechanical Engineering, Soongsil University. Her research interest is micro machining.
E-mail: qkrwndk123@soongsil.ac.kr
M.S. student in the department of Mechanical Engineering, Graduate School, Soongsil University, Korea. His research interest is micro machining.
E-mail: lus223@soongsil.ac.kr
Professor in the School of Mechanical engineering, Soongsil University. His research topics are micro mechanical and non-conventional machining processes.
E-mail: bhkim@ssu.ac.kr