
기상측정을 통한 DED 출력물의 유연 후가공
Copyright © The Korean Society for Precision Engineering
This is an Open-Access article distributed under the terms of the Creative Commons Attribution Non-Commercial License (http://creativecommons.org/licenses/by-nc/3.0) which permits unrestricted non-commercial use, distribution, and reproduction in any medium, provided the original work is properly cited.
Abstract
The directed energy deposition (DED) process has been used for enhancement of the mechanical property, repair, and part manufacturing. Post-process machining is required due to the low quality of the DED printed part. Even if the part is printed under similar conditions, dimensional variations occur frequently due to the accumulation of small printing errors. Due to tool overfeeding and the occurrence of the non-cutting area due to this variation, the quality of the finished part is not guaranteed. Therefore, the post-process machining should be carried out considering the actual printed part shape. Herein, the flexible post-process machining is proposed by utilizing the shape information through the on-machine measurement (OMM) of DED printed parts. The process margin for machining the design shape is calculated through the OMM of the geometric dimension of the printed part. Feedrate (Override) and machining path of each printing parts are flexibly determined depending on the process margin. This technique is applied to the pocket shape part printed with STS 316L material, and the rough and finish machining conditions are established. Rough machining time was reduced by adjusting the feedrate flexibly. The final form of accuracy and surface roughness were achieved under 30 and 0.25 μm, respectively.
Keywords:
On-machine measurement, Post-process machining, Directed energy deposition, STS 316L, Flexible cutting condition키워드:
기상측정, 후가공, 직접 에너지 증착, 유연 가공 조건1. 서론
적층 제조(Additive Manufacturing)는 금속, 폴리머, 복합재 등 다양한 소재를 대상으로 광범위한 산업에서 활용되고 있으며, 시제품 제작 단계를 넘어서 실사용 부품을 출력하는 수준으로 발전되고 있다.1 최근 Boeing, Airbus사에서는 자사의 항공기 기체 부품을 출력하여 사용하는 등 부품의 신뢰도도 확보되어 더욱 많은 부품에 적용되고 있다.2,3 금속 소재 적층은 PBF (Powder Bed Fusion)와 DED 방식으로 많이 수행되며, 특히 DED 방식은 부품 보수, 기능 강화, 경사 소재 적층 등에 활용될 수 있는 장점이 있다.
DED 공정 출력물은 표면 조도 및 형상 정확도가 PBF 방식에 비해 낮고, 최종 부품으로 활용하기 위해서는 후가공이 필수적이다.4 DED 공정 출력물의 후가공은 출력 품질을 별도로 확인한 후 절삭 가공 장비를 활용하여 수행되며, 공작물 좌표계 설정 및 가공물 고정 등의 준비 과정이 다시 필요하고, 출력물의 형상 오차가 클 경우 보수 작업이 추가적으로 필요하게 된다. 출력 품질은 재현성을 보장하기 어려워 출력물 자체의 품질을 높여 최종 부품 가공에 들어가는 노력을 줄이고자 하는 다양한 연구가 진행되고 있다.
출력물의 공정 품질을 위해 파이로미터(Pyrometer), IR Camera, CCD Vision 등 다양한 센서 연계 공정제어 기술이 함께 적용되고 있다.5-7 Seo8는 레이저 출력 및 분말 공급량 조절을 통해 출력물의 높이 제어를 하더라도 적층 레이어가 누적될수록 형상 오차가 누적되는 것을 확인하였다. Chang9은 출력물의 형상 정도를 개선하기 위해 적절한 적층 경로를 생성하여 출력하였지만 모재로의 입열량이 과다해져 모재가 변형되는 등의 문제를 확인하였다. 따라서 이러한 출력물의 형상 오차로 후가공 전(前) 검사를 통한 가공 전략 수립이 필요하다.10
출력물의 형상 정보를 얻기 위해 3D 스캐너를 이용하거나, CMM (Coordinate Measuring Machine)을 활용하는 방법이 사용되고 있다.11-13 하지만 적층, 측정, 후가공에 이르는 공정이 각 공정기계에서 이루어지므로 생산성 측면에서 효율성을 향상시킬 필요가 있다. 따라서, Hybrid 3D 프린터에 기상측정(On-Machine Measurement) 기능을 탑재하여 3개의 공정을 단일 장비에서 수행하는 효율성 극대화 연구도 진행 중이다.14
본 논문에서는 DED 방식의 출력물을 터치프로브(Touch-Trigger Probe) 기반의 기상측정으로 출력 형상을 검사하고 효율적인 후가공을 위한 가공 조건을 유연하게 적용하는 방법을 제안한다. 터치프로브는 공작물 좌표계 설정 및 공작물의 좌표 데이터를 취득하기 위해 많이 활용되고 있는 기상측정 장치로 5축 이상 머시닝 센터에서는 필수적으로 활용되고 있다.15,16 2장에서는 기상측정을 활용하여 후가공 조건을 유연하게 설정하는 기술에 대하여 설명하고, 3장에서는 STS 316L 재료를 대상으로 정삭과 황삭의 조건을 벌크와 출력물 시편에 대한 비교 실험을 통해 도출한 결과를 소개한다. 4장에서는 3장에서 도출한 가공 조건을 적용하여 머시닝 센터에서 STS 316L DED 출력물의 측정과 가공 공정을 수행한 결과를 분석해서 제안한 방법의 유효성을 검증한다.
2. 기상측정을 활용한 유연 가공 조건 후가공
DED 출력물의 후가공 전 기상측정을 활용한 형상 측정 목적은 가공 잔량을 계산하여 가공 경로를 결정하고 가공 잔량을 고려한 유연한 가공속도로 총 가공 시간을 감소시키는데 있다. 출력물은 설계 형상을 최종적으로 얻기 위해 후가공을 고려하여 여유 레이어를 추가하거나 형상 스케일을 늘리는 등의 전략을 사용한다. 공정제어를 통한 출력을 하더라도 누적된 적층 오차 및 열변형 등으로 최종 출력 형상은 정확하게 예측하기 어렵다. 따라서, 후가공 경로 및 조건을 일정하게 적용하는 것은 비절삭부가 생기거나 과절입으로 인한 높은 가공 부하가 발생하는 등의 문제를 야기할 수 있다.
기상측정을 활용한 유연한 후가공 절차를 본 연구에서는 Fig. 1과 같이 제안한다. 먼저, 해당 소재와 공구에 대한 정삭(Finish Machining) 조건과 황삭(Rough Machining) 조건을 사전 실험을 통해 결정한다. 황삭 조건은 가공 잔량에 따라 유연하게 변동할 수 있도록 절입 깊이(Depth of Cut)에 따라 수립한다. 설계 형상으로부터 후가공이 되어야 하는 기하 형상(또는 중요 형상)을 결정하고 기상측정을 위한 경로를 설정한다.
출력이 완료된 가공물의 좌표데이터는 공작물 좌표계(또는 데이텀)에 대해 터치프로브로 취득한다. 이 측정데이터로부터 설계 형상과 실제 적층 형상과의 편차를 확인할 수 있고, 이 편차를 고려하여 결정된 가공 경로와 가공속도로 후가공을 실시한다.
2.1 출력물의 기상측정 경로 설정
출력물의 기상측정 경로는 사전에 작성한 Plane, Bore, Boss, Pocket, Web 측정과 같은 매크로에서 측정점을 설정하여 생성된다. 출력물의 형상을 판단하기 위한 측정점은 과적층 등에 의한 형상 오차가 주로 발생하는 코너 또는 Edge부에 가까운 위치로 선정하며 기본 공정 품질 및 적층 형상 크기에 따라서 Edge부에 측정점 추가가 필요하다. Web 형상 출력을 예로 들면, Fig. 2와 같이 출력물 좌표계{P}를 기준으로 높이(Height, H)에 대하여, 실적층 높이 H'은 p9-p12 측정 좌표데이터의 최소 Z 좌표로 결정한다. H에 대한 H'의 편차는 가공 잔량 ΔmH로 설정한다. 출력물의 높이가 설계 형상의 Web 높이보다 높을 경우 잔량에 따라서 사전에 설정한 가공 조건으로 반경 방향 절입이 많은 정면 밀링(Face Milling, F) 전략을 수립한다. 만약, 후가공 대상 높이가 설계 형상의 높이보다 낮을 경우 추가 적층을 필요로 하게 된다. Web의 폭(Width) 및 길이(Length)의 경우, p1, p3에 의한 적층물 길이(X좌표 차)와 p2, p4에 의한 적층물 길이 중 최소 길이를 Web의 설계 길이 L에 대한 실제 길이 L'으로 하여 가공 잔량 ΔmL이 계산되고, 중간 지점의 X좌표를 가공좌표계 {M}의 x원점으로 설정한다. 폭 W 또한 p5, p7 및 p6, p8의 측정 정보를 통하여 최소 폭 W'과 가공 잔량 ΔmW 및 가공좌표계 {M}의 y원점을 설정한다. 폭 및 길이 방향 형상은 공구축 방향 절입이 많은 측면 밀링(Side Milling, S)으로 가공하고, 가공 조건은 가공 잔량에 따라서 사전에 설정한 조건으로 결정된다. 정면 및 측면 밀링 형상 예시는 Fig. 3과 같다.
2.2 가공 잔량을 고려한 후가공 경로 생성 및 조건 수립
측정으로 얻은 좌표데이터를 이용해 설계 형상에 대한 출력물의 가공 잔량이 계산되면, 후가공 경로 생성 시에 잔량을 고려하여 가공 조건을 설정한다. Web 형상에서는 높이, 폭, 길이에 대한 각 가공 잔량 ΔmH, ΔmW, ΔmL이 식(1)과 같이 계산된다고 했을 때, 높이 방향의 가공 잔량 ΔmH은 식(2)로부터 황삭 횟수가 결정된다.
(1) |
(2) |
(3) |
여기서, da,R, da,F는 정면 밀링의 황삭 및 정삭 절입 깊이을 의미하고, dr,R, dr,F는 측면 밀링의 황삭 및 정삭 절입 깊이다. a1-a6는 측정된 가공 잔량으로부터 황삭 여부를 결정하고 황삭 절입 깊이를 조정하는 변수로 다음과 같이 계산한다. a3-a6도 측면 밀링 황삭 절입 깊이에 따라서 유사하게 적용한다.
정삭 조건은 정면 및 측면 밀링에서 사전 실험을 통해 가공물의 표면 조도를 평가하여 일정한 가공 조건으로 결정한다. 황삭의 경우 가공 잔량이 출력물의 적층 상태에 따라서 달라지기 때문에, 황삭 이송속도(frF)는 사전 실험을 통해 식(2)와 같이 같이 황삭 절입 깊이 조정변수(ak)를 변수로 하는 n차 다항식 모델로 모델링한 후 기상측정 결과에 따라서 결정한다.
(4) |
여기서, frF는 황삭 정면 밀링의 이송속도를 나타내며, 계산 모델을 통해 황삭 절입 깊이에 따라 계산할 수 있다. 측면 밀링 이송 속도(frS)도 동일하게 측정 결과에 따라 유연하게 이송속도를 적용할 수 있도록 모델링하였다.
3. 절삭 특성 확인 및 황/정삭 절삭 조건 수립
시편으로 사용할 재료는 오스테나이트계 스테인리스강인 STS 316L이다. 고인성, 가공 경화 현상 등의 성질로 대표적인 난삭재(難削材)로 알려져 있지만 높은 용접성과 적용 분야가 넓어 DED 공정에 많이 사용된다.17-20 적층 시편은 Maxrotec사의 DED 3D 프린터를 이용해 제작했고, 출력 조건은 Table 1에 나타내었다. 후가공 실험은 Table 2와 같이 터치프로브가 장착된 DMG Mori사의 5축 머시닝 센터에서 진행하였다. 벌크와 출력물의 가공성 비교평가 및 정삭 조건 수립을 위한 실험은 Fig. 4와 같이 공구동력계(Dynamometer), 조도측정기(Surface Roughness Meter), 공구현미경(Microscope)을 사용하여 실시하였다. 황삭 조건은 절입 깊이에 따른 최대 이송속도를 채터 현상을 고려하여 실험을 통해 수립하였다.
3.1 절삭 특성 확인 및 정삭 조건 결정
STS 316L 벌크, 출력물 시편을 동일 절삭 조건으로 가공해서 얻은 절삭력 및 표면 조도 데이터를 비교하여 출력물의 절삭 특성을 확인한다.
실험에 사용한 공구는 Table 3과 같이 TaeguTec사의 난삭재 가공용 초경 엔드밀을 사용했고, 스테인리스강 추천 절삭 조건을 참고하여 실험하였다.21 실험 조건은 스핀들 속도를 고정하고 날당 절입과 절입 깊이를 변동시켜 실시하였다. 두 종류의 시편으로부터 발생한 절삭력은 Fig. 6과 같이 날당 절입이 증가하고 절입 깊이가 커질수록 절삭력이 커지는 경향이었고, 출력물과 벌크 절삭력 데이터에서 최대 1.11 N의 편차를 보였다.
표면 조도는 Fig. 7과 같이 동일 가공 조건에서 출력물 시편에서 더 높게 측정되었다. 공구현미경으로 측정된 가공 표면 Fig. 8에서 출력물 시편의 표면이 유사한 절삭력에도 불구하고 전체적으로 스크래치 현상이 더 많이 발생하는 것을 확인하였다. 출력된 소재의 경도 및 표면 마찰이 높아짐에 따른 절삭 저항 및 절삭열 상승으로 인해 구성인선 생성이 촉진되어 출력물 시편의 표면 거칠기가 높은 것으로 추정된다. da = 0.1mm를 적용한 실험에서 측정된 표면 조도는 벌크 시편에 da = 0.2 mm 조건을 적용한 표면 조도와 유사했다. 따라서, 일반 소재와 유사한 표면 조도를 얻기 위해서는 다소 보수적인 가공 조건을 적용하는 것이 필요하다. 벌크 시편 가공 실험에서 얻은 Ra 0.25 μm의 표면 조도 가공 조건을 정삭 조건으로 설정하였다. 정면 밀링 조건은 da,F = 0.1 mm, dr,F = 5.0 mm, fr = 348 mm/min과 같고, 측면 밀링 조건은 da,F = 5.0 mm, dr,F = 0.1 mm, fr = 348 mm/min과 같이 설정하였다.
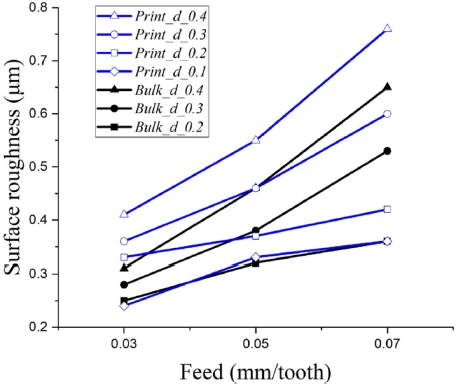
Surface roughness of the bulk and printed STS 316L test piece depending on depth of cut and feedrate
3.2 황삭속도 결정 모델 수립
황삭 조건은 같은 시간 내 많은 재료를 제거하기 위해 절입 깊이에 따른 최대 가공속도(이송속도)를 확인한다. 실험 조건은 Table 4와 같이 스핀들 속도를 고정한 후 절입 깊이(da, dr) 0.1부터 0.5 mm에서 날당 절입(Feed)을 0.03부터 0.17 mm/tooth까지 0.02씩 증가시키면서 채터가 발생하기 전 조건을 찾았다. 절입 깊이별 최종 황삭 가공속도는 채터 전 조건에서 Feed Override 조절을 통해 최대의 가공속도를 확인 및 결정하였다. 정면 밀링과 측면 밀링에서 채터 발생 조건은 동일했고, Table 5 및 Fig. 9와 같이 절입 깊이별 최대 이송속도를 도출 및 5차 다항식 모델로 적용하였다.
4. 기상측정을 활용한 유연 후가공 검증 실험
유연 후가공을 위한 기상측정 및 후가공 검증 실험은 STS 316L 재료를 DED 방식으로 출력한 Fig. 10과 같은 형상의 3개의 시편(A, B, C)을 대상으로 Fig. 11과 같이 실시하였다. 기상 측정을 위해 사용한 터치프로브의 성능은 Table 6과 같다. 사전에 작성한 측정 매크로에 의해 시편의 P1-P16 위치가 측정되었고, 좌표데이터로부터 높이(H), 폭(W), 길이(L)가 계산되었다.
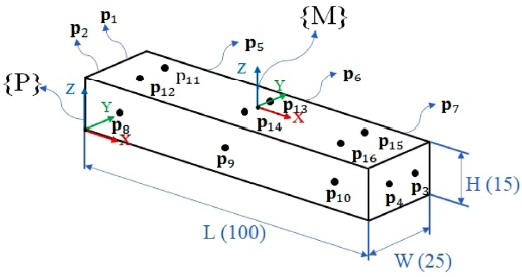
On-machine measurement points for determining post-process machining of the web shape DED printed test piece
측정으로 얻은 좌표데이터를 활용하여 계산한 시편들의 치수와 각 가공 잔량(ΔmH, ΔmW, ΔmL)은 Table 7과 같다. 각 가공 잔량별 황삭 절입 깊이(da,R, dr,R)는 Table 8과 같다. 가공 잔량에 따른 이송속도는 황삭 조건 시험을 통해 도출한 다항식 모델로 후가공 프로그램에 적용했다. B 시편의 ΔmW, ΔmL은 0.6mm를 초과하여 황삭 2회 적용이 필요했다.
도출한 조건을 적용하여 출력물을 후가공하여 Fig. 12와 같이 최종 시편을 얻었고, 최고, 치수와 표면 조도는 3차원 측정기와 조도 측정기를 활용하여 측정하였으며 Table 9와 같다. 후가공 후 시편의 형상 오차는 0.03 mm 이내로 장비의 이송정밀도 등의 성능 개선이 되면 더 줄어들 것으로 판단된다. 표면 조도는 사전에 목표했던 0.25 μm 이내로 가공됨을 확인했다. 최종적으로 A, B, C 시편의 거친 표면은 모두 제거되었음을 확인했다.
5. 결론
본 연구에서는 DED 공정 출력물의 효율적인 후가공을 위해 터치프로브 기반의 기상측정을 활용하여 가공 잔량 정보를 취득하고, 가공 잔량에 따른 유연한 가공 조건을 적용한 후가공 방법을 제안하였고 결론은 다음과 같다.
(1) 기상측정을 적용한 Web 형상의 DED 출력 부품의 기하형상 정보를 확인할 수 있었고, 설계 형상과의 비교를 통해 후가공 잔량을 정확하게 판단
(2) 가공 잔량을 파악하여 황삭 속도를 유연하게 적용할 수 있어 일정한 속도 가공에 비해 전체 가공 시간 및 과절입에 의한 공구 파손 등 방지 가능
(3) STS 316L 재료를 대상으로 적용하였고, 벌크와 출력물 시편에서 절삭력의 편차는 없었지만, 동일 조건에서 표면 품질은 적층 시편에서 더 거칠어 정삭 시 출력물 시편은 다소 보수적인 조건 적용 필요
(4) 적층과 절삭의 기능이 탑재된 하이브리드 DED 머신에 유연 가공 조건을 산출할 수 있는 기상측정 기능을 적용하면 STS 316L뿐 아니라 다양한 소재의 최종 부품 가공 시간이 효과적으로 단축 가능
(5) 3차원 곡면 형상에 적용할 경우에도 유사하게 Near-Net Shape과 최종 부품 형상을 고려하여 공구 절입 방향(반경 또는 축 방향)에 따라 가공 경로와 절삭속도를 유연 설정할 수 있으며, 적층물의 외곽 형상을 기상측정하여 각 방향의 실적층 Dimension을 평가 및 편차의 최솟값(내측 형상은 최댓값)을 산출하고 Feedrate을 가변할 수 있도록 후가공 CAM에 적용
NOMENCLATURE
pi : | On-machine measurement points (i = 1, …, n) |
{P} : | Print coordinate system |
{M} : | Workpiece coordinate system for post-process |
ΔmH, ΔmW, ΔmL : | Process margins f or height, width and length dimension, respectively |
dr,R, dr,F : | Radial depth of cut for rough and finish milling, respectively |
da,R, da,F : | Axial depth of cut for rough and finish milling, respectively |
frF, frS : | Feedrate for face and side milling, respectively |
ai : | Variables to determine the depth of cut of rough milling from on-machine measurement data (i = 1, …, 6) |
ci : | Coefficients of the n-th polynomial model for rough milling feedrate (i = 1, …, n) |
f : | Feed per tooth |
Acknowledgments
이 논문은 2020년도 산업통상자원부 및 과학기술정보통신부의 재원으로 한국산업기술평가관리원(No. 10053878)과 한국연구재단(No. NRF-2019R1A2C2088683)의 지원을 받아 수행된 연구임.
REFERENCES
- Campbell, I., Diegel, O., Kowen, J., and Wohlers, T., “Wohlers Report 2018: 3D Printing and Additive Manufacturing State of the Industry: Annual Worldwide Progress Report,” Wohlers Associates, 2018.
- BOEING, “Additive Manufacturing Insight.” https://www.boeing.com/features/innovation-quarterly/2019_q4/btj-additive-manufacturing.page, (Accessed 23 NOVEMBER 2020)
- Airbus, “Printing the Future: Airbus Expands its Applications of the Revolutionary Additive Layer Manufacturing Process,” https://www.airbus.com/newsroom/news/en/2014/03/printing-the-future-airbus-expands-its-applications-of-the-revolutionary-additive-layer-manufacturing-process.html, (Accessed 23 NOVEMBER 2020)
-
Kim, S. and Chun, C., “Trend of DED Type Additive Manufacturing Technology for Titanium,” Journal of Welding and Joining, Vol. 35, No. 4, pp. 23-28, 2017.
[https://doi.org/10.5781/JWJ.2017.35.4.4]
- CLAMIR, “Closed-Loop Laser Power Control System for Cladding and Laser Metal Deposition Processes.” https://www.clamir.com/en/specifications-2/, (Accessed 23 NOVEMBER 2020)
- FLIR, “Fixed Thermal Cameras,” https://www.flir.com/browse/industrial/fixed-thermal-cameras/, (Accessed 23 NOVEMBER 2020)
- NIT, “Imaging Applications,” https://new-imaging-technologies.com/applications/, (Accessed 9 NOVEMBER 2020)
- Seo, J., Yoon, H., Lee, K., and Shim, D., “Study on Effects of Direct Laser Melting Process Parameters on Deposition Characteristics of AlSi12 Powders,” Transactions of Materials Processing, Vol. 27, No. 5, pp. 314-322, 2018.
-
Choi, J. and Chang, Y., “Characteristics of Laser Aided Direct Metal/Material Deposition Process for Tool Steel,” International Journal of Machine Tools and Manufacture, Vol. 45, Nos. 4-5, pp. 597-607, 2005.
[https://doi.org/10.1016/j.ijmachtools.2004.08.014]
-
Flynn, J. M., Shokrani, A., Newman, S. T., and Dhokia, V., “Hybrid Additive and Subtractive Machine Tools-Research and Industrial Developments,” International Journal of Machine Tools and Manufacture, Vol. 101, pp. 79-101, 2016.
[https://doi.org/10.1016/j.ijmachtools.2015.11.007]
-
Mandić, M., Galeta, T., Raos, P., and Jugović, V., “Dimensional Accuracy of Camera Casing Models 3D Printed on Mcor IRIS: A Case Study,” Advances in Production Engineering & Management, Vol. 11, No. 4, pp. 324-332, 2016.
[https://doi.org/10.14743/apem2016.4.230]
-
Newton, L., Senin, N., Gomez, C., Danzl, R., Helmli, F., et al., “Areal Topography Measurement of Metal Additive Surfaces Using Focus Variation Microscopy,” Additive Manufacturing, Vol. 25, pp. 365-389, 2019.
[https://doi.org/10.1016/j.addma.2018.11.013]
- SIEMENS, “Automate Quality Control with a Data-Driven Process,” https://www.plm.automation.siemens.com/global/ko/products/manufacturing-planning/part-quality-control.html, (Accessed 23 NOVEMBER 2020)
- Lee, H., Lee, D., Park, M., Lee, K and Yang, S., “An On-Machine Measurement Technique for Efficient Machining of an Additive Manufactured Workpiece on a Hybrid Metal 3D Printer,” Proc. of the KSPE Autumn Conference, p. 169, 2019.
- HEIDENHAIN, “Touch Probes for Machine Tools,” https://www.heidenhain.com/en_US/products/touch-probes/, (Accessed 9 NOVEMBER 2020)
- MARPOSS, “Touch Probe Line,” https://www.marposs.com/eng/product/touch-probe-line, (Accessed 23 NOVEMBER 2020)
-
Lee, K. S., Lee, J. K., Song, K. O., and Park, J. H., “Study on Effect of Mechanical Machining and Heat Treatment on Surface Residual Stress of TP316L Stainless Steel,” Transactions of the Korean Society of Mechanical Engineers A, Vol. 35, No. 5, pp. 453-458, 2011.
[https://doi.org/10.3795/KSME-A.2011.35.5.453]
-
Kang, M. C., Ye, D. H., and Go, G. H., “International Development Trend and Technical Issues of Metal Additive Manufacturing,” Journal of Welding and Joining, Vol. 34, No. 4, pp. 9-16, 2016.
[https://doi.org/10.5781/JWJ.2016.34.4.9]
-
Park, E. K., Hong, S. M., Park, J. J., Lee, M. K., Rhee, C. K., et al., “Dispersion Behaviors of Y2 O3 Particles into Aisi 316L Stainless Steel by Using Laser Cladding Technology,” Journal of Korean Powder Metallurgy Institute, Vol. 20, No. 4, pp. 269-274, 2013.
[https://doi.org/10.4150/KPMI.2013.20.4.269]
-
Hwang, J. H., Shin, S. S., Jung, G. I., Kim, S. W., and Kim, H. D., “A Study on the Characteristics of Laser Deposition Surface and Cross-Section for Metal Powder,” Journal of Welding and Joining, Vol. 34, No. 4, pp. 17-22, 2016.
[https://doi.org/10.5781/JWJ.2016.34.4.17]
- TaeguTec, “Solid End Mills.” https://www.taegutec.com/pages/publications/cutting-tools-catalogs/, (Accessed 23 NOVEMBER 2020)
Senior Researcher in the Korea Institute of Industrial Technology. His research interest is machine tool metrology and metal 3D printing.
E-mail: hhlee84@kitech.re.kr
Master course student in the School of Mechanical Engineering, Kyungpook National University. His research interest is intelligent manufacturing systems and CAD/CAM.
E-mail: msparker8@knu.ac.kr
Ph.D. Director of R&D Center, Maxrotec Co., Ltd.. His research interest is metal 3D printing.
E-mail: dmlee@maxrotec.com
Professor in the School of Mechanical Engineering, Kyungpook National University. His research interest is intelligent manufacturing systems and CAD/CAM.
E-mail: syang@knu.ac.kr