
전극 레이저 절단에서 전극의 두께가 절단 품질에 미치는 영향
Copyright © The Korean Society for Precision Engineering
This is an Open-Access article distributed under the terms of the Creative Commons Attribution Non-Commercial License (http://creativecommons.org/licenses/by-nc/3.0) which permits unrestricted non-commercial use, distribution, and reproduction in any medium, provided the original work is properly cited.
Abstract
Many countries are trying to overcome global warming due to greenhouse gas emissions, such as CO2. In particular, the regulation on CO2 emissions of internal combustion engine vehicles has become strictly important. Thus, the automobile companies are putting more effort for improving the manufacturing of the battery, which is the main power supply of electrical vehicles. In the electrode cutting process, laser cutting has been actively discussed to solve problems originating from the conventional electrode cutting processes. However, there is a lack of research considering the effect of thickness of the active material on laser cutting. In this paper, the effect of thickness of the active material on laser cutting of electrodes is analyzed. First, the cut electrodes are observed through a scanning electron microscope (SEM). Next, the kerf width and clearance width of the electrodes are measured and compared at the same laser parameter. The kerf width and clearance width of relatively thick electrodes are narrowly formed. Finally, the cutting quality of the electrode is compared. A uniform cut edge is observed as the scanning speed increases.
Keywords:
Lithium-ion battery, Laser cutting, Thickness of electrodes, Cut edge quality키워드:
리튬이온 배터리, 레이저 절단, 전극의 두께, 절단 품질1. 서론
오늘날 인류는 다양한 환경문제에 직면하였으며, CO2와 같은 온실가스 배출로 인한 지구 온난화 문제를 극복하기 위해 많은 노력을 기울이고 있다. 특히, 전 세계적으로 CO2 배출을 줄이기 위하여 화석연료 사용 규제를 강화하고 있다. 그에 따라, 화석연료를 대체할 에너지원에 대한 관심이 증가하고 있다.1,2 대체 에너지원 중 하나인 리튬이온 배터리(Lithium-Ion Battery)는 1991년 처음으로 상용화된 후 기술의 발달로 현재는 스마트폰, 무선제품, 전기자동차 등에 사용되며 인류의 삶에 깊숙이 자리 잡고 있다. 다양한 분야에 리튬이온 배터리가 사용되는 이유는 다른 2차 전지에 비해 가볍고, 용량이 높고, 긴 사이클 수명과 안정성을 갖고 있기 때문이다.3 그럼에도 불구하고 기존의 리튬이온 배터리의 성능 한계를 극복하고, 효율적이고 높은 신뢰성의 공정 라인을 구축하기 위하여 많은 노력을 하고 있다.4 리튬이온 배터리의 공정은 전극제작 공정(Electrode Manufacturing Process), 조립 공정(Assembly Process), 활성화 공정(Formation Process)으로 분류된다.5 전극제작 공정은 활물질, 도전재, 바인더를 섞어 집전체에 코팅하여 전극을 만드는 공정이며, 조립 공정은 제작된 전극을 절단하고, 분리막과 함께 적층하여 전해액을 주입하여 밀봉하는 단계이며, 활성화 공정은 배터리제작의 마무리 단계로 배터리를 안정화하는 단계이다.
현재 전극제작 공정에서 전극 물질의 특성을 개선시켜 배터리 성능을 향상시키려는 연구는 활발이 진행되고 있지만 그에 비해 조립 공정에서 배터리 성능을 개선하려는 연구는 상대적으로 적다. 특히, 조립 공정에서 전극의 절단 공정은 배터리 안정성과 밀접한 관계를 보여준다. 예를 들어, 전극 절단 후 전극에 버(Burr)와 같은 결함은 배터리 조립 후에 분리막을 손상시켜 배터리 수명을 감소시키며, 더 나아가 폭발을 초래한다. 전극의 절단은 대부분 Die Cutting, Rotary Knife Cutting으로 진행된다. 그러나, 위에 언급된 기계적 절단들은 시간이 지남에 따라 공구가 마모되어 전극 절단 중 결함을 발생시킬 확률이 증가한다.6 이러한 문제를 해결하기 위하여 레이저 절단은 좋은 대안 중 하나이다. 레이저는 비접촉식 공정으로 공구의 마모로 인한 절단 품질 문제를 발생시키지 않으며, 다양한 크기의 전극을 유연하게 절단할 수 있다.7 따라서, 기존 전극절단 공정을 대체하기 위한 연구들이 진행됐다.8-12 그러나, 레이저 가공 시 전극의 두께가 절단 품질에 미치는 영향에 대한 연구는 부족하다. 본 연구는 동일한 성분과 두께의 집전체(Current Collector)에 활물질(Active Material)의 코팅 두께에 차이를 두어 전극의 두께가 레이저 가공에서 절단 품질에 미치는 영향을 알아보기 위한 실험을 진행하였다. 레이저 절단된 전극은 주사전자현미경을 통해 관찰되었으며, 분석을 위해 절단폭(Kerf Width), Clearance Width, 절단 품질을 주요 인자로 선택하였다. 절단폭은 레이저를 통해 전극 절단이 가능한 가공 조건을 얻기 위해 분석된다. 또한, 전극 절단 후에 과도한 Clearance Width와 전극의 결함은 배터리 조립 후 분리막을 손상시키거나, 전기화학적 반응을 할 수 있는 활물질의 양이 감소하여 배터리 성능을 감소시킨다. 그러므로 Clearance Width와 절단 품질에 대한 분석이 진행되었다.
2. 실험 설계
2.1 전극 제작 및 레이저 절단 방법
실험에 사용된 전극의 슬러리는 LiFePO4, Polyvinylidene Fluoride, Super C65를 중량비율로 각각 9 : 0.5 : 0.5로 섞어 제작하였다. 제작된 슬러리는 20 μm의 두께의 알루미늄 포일에 코팅되었다. 각각 슬러리의 코팅 두께는 37과 85 μm으로 상이하며, Table 1에 주요사항을 제시하였다. 코팅 후에 전극은 120oC의 오븐에서 2시간 동안 건조하였다. 건조된 전극을 각각 약 20% 압축한 후 다시 120oC에서 12시간 동안 건조하였으며 전극의 최종 두께는 상용되는 LiFePO4 Cathode의 두께와 비슷한 86 μm와 그보다 더 얇은 51 μm로 설정했다. 모든 과정은 드라이 룸에서 진행되었다. 본 논문에서 51 μm의 두께를 갖는 전극을 E51와 86 μm의 두께를 갖는 전극을 E86으로 정의하였다.
Fig. 1은 실험에 사용된 레이저 시스템을 모식도로 표현하였다. 단일모드 광섬유 레이저(IPG YLM-200/2000-QCW)는 최대 출력 250W이며, 1070 nm의 파장을 갖고 있다. 레이저의 빔 품질인수는 1.05, 렌즈와 시편표면 사이의 거리는 100 mm이며, 이때 초점 크기(Spot Size)는 약 23 μm이다. 레이저 빔은 3DGalvo-Scanner를 통해 제어되었다. 본 실험에서 설정된 레이저 출력(Power)은 150 W이며, 레이저 조사속도(Scanning Speed)는 500-5,000 mm/s (500 mm/s 간격)의 범위로 진행했다. 실험이 수행될 때 전극이 움직이지 않게 클램핑(Clamping) 장비를 통해 고정하였으며, 폭 30mm의 전극이 완전히 절단되는 것을 방지하여 20 mm의 길이로 절단하였다.
3. 실험 결과 및 고찰
3.1 절단폭(Kerf Width)
Fig. 3은 레이저 출력 150 W에서 E51와 E86의 조사 속도에 따른 절단폭을 보여준다. Fig. 3을 보면, E51와 E86는 활물질의 두께와 상관없이 조사 속도가 증가함에 따라 절단폭이 감소하였다. 그리고 E51는 500에서 5,000 mm/s까지 절단되었지만, E86는 4,500 mm/s부터 절단되지 않고 부분적인 절단이 관찰되었다. 형성된 절단폭을 각각 측정하였을 때, E51의 평균 절단폭은 500 mm/s에서 최대 약 65 μm이며, 5,000 mm/s에서 최소 약 18 μm으로 측정되었다. E86은 평균 절단폭은 500 mm/s에서 최대 약 30 μm, 4,000mm/s에서 최소 약 12 μm으로 E56의 절단폭보다 상대적으로 좁게 형성되었다. 이러한 결과는 레이저 빔의 부피에너지(Volume Energy)와 전극과 레이저 빔이 상호 작용 시, 발생되는 다중 반사 현상을 통해 설명될 수 있으며, 부피 에너지는 식(1)과 같이 정의한다.
(1) |
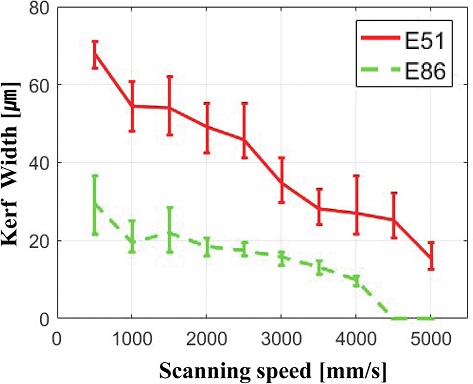
Comparison of kerf width of 51 μm-thick electrodes (E51) and 86 μm-thick electrodes (E86) at the laser power of 150 W
먼저, 동일한 레이저 가공 조건에서 상대적으로 두꺼운 활물질을 제거하기 위해서 더 높은 부피에너지가 소모된다. 이후 두꺼운 전극의 집전체는 상대적으로 낮은 에너지의 빔과 상호 작용하기 때문에 절단폭이 좁게 형성된 것으로 판단된다. 또한, 얇은 전극을 절단될 때, 두꺼운 전극의 활물질보다 얇은 전극의 활물질이 먼저 제거되기 때문에 집전체와 레이저 빔의 상호 작용 시간이 길어진다. 따라서, 다중반사가 증가하였으며, 결과적으로 절단폭이 증가했다고 추측된다. 즉, 실험 결과를 통해 활물질의 두께가 절단폭에 미치는 영향을 확인할 수 있었다.
3.2 Clearance Width
Fig. 4는 150W에서 조사 속도에 따른 E51와 E86의 Clearance Width의 변화를 보여준다. 절단폭과 동일하게 조사 속도가 증가할수록 감소하는 경향이 나타났다. 그리고 코팅 두께가 얇은 E51의 Clearance Width가 상대적 넓게 형성되었고, E86의 Clearance Width는 상대적 좁게 형성되었다. E51의 평균 Clearance Width는 약 10-21 μm의 범위로 형성되었다. 반면, E86의 평균 Clearance Width는 4-13 μm로 상대적으로 좁게 형성되었다. 상대적으로 얇은 전극의 Clearance Width가 넓은 이유는 절단폭이 넓게 형성되는 메커니즘과 동일하게 추측할 수 있다. 동일한 레이저 가공 조건에서 상대적으로 얇은 활물질을 제거할 때 소모되는 부피에너지는 낮다. 즉, 두꺼운 활물질을 제거한 빔보다 높은 부피에너지의 빔이 집전체와 상호 작용을 하며, 이때 알루미늄 포일에 다중 반사된 빔이 Clearance Width를 증가시킨다고 추측된다. 따라서 동일한 레이저 가공 조건에서 전극의 코팅 두께가 Clearance Width에 영향을 미치는 것을 확인하였으며, 전극의 두께에 따라 레이저 가공 조건을 조절하면 Clearance Width를 조절 가능한 것으로 나타났다.
3.3 절단 품질
Fig. 5는 레이저 절단된 E51와 E86를 주사전자현미경으로 촬영한 사진이다. Fig. 5(a)에서 E51의 절단면을 관찰하였을 때 500-5,000 mm/s까지 상대적으로 균일한 절단폭과 Clearance Width가 관찰되지 않았다. 반면, Fig. 5(b)를 보았을 때, E86은 2,000-4,000 mm/s의 조사 속도에서 균일한 절단폭과 Clearance Width를 형성하였다. 두 전극에서 관찰된 균일하지 못한 절단폭 형성의 원인 중 하나는 절단된 후, 집전체가 재응고(Re-Solidification)될 때 반동압력(Recoil Pressure)에 의해 균일한 용융풀을 유지하지 못하기 때문이다. 그리고 4,500과 5,000 mm/s에서 부분적으로 절단되었지만 활물질이 제거된 폭은 4,000 mm/s보다 넓었다. 레이저 빔이 활물질을 제거한 후 집전체와 반응할 때, 집전체를 제거하기 위해 필요한 부피에너지보다 낮아 부분적으로 절단되었으며, 부분적으로 절단된 영역에서 레이저 빔의 다중반사가 증가하여 활물질의 제거폭이 증가한 것으로 추측된다.
4. 결론
본 논문은 단일모드 광섬유 레이저에 의한 절단 가공 시 전극의 두께가 절단 품질에 미치는 영향을 분석한 결과 다음과 같은 결론을 얻을 수 있었다.
(1) 레이저 절단 시 활물질의 코팅 두께와 상관없이 조사 속도가 증가할 때, 절단폭과 Clearance Width가 감소하였다. 따라서, 조사 속도는 전극의 레이저 절단 시 절단폭과 Clearance Width에 영향을 준다는 것으로 나타났다.
(2) 전극의 레이저 절단에서 활물질의 코팅 두께에 따른 영향이 뚜렷하게 관찰되었으며, 동일한 가공변수에서 상대적으로 두꺼운 코팅 두께를 갖은 전극의 절단폭과 Clearance Width가 좁게 형성되었다.
(3) 절단 품질을 관찰하였을 때, 상대적으로 활물질의 두께가 얇은 E51에서 불균일한 절단폭과 Clearance Width가 관찰되었고, 상대적으로 두꺼운 E86은 조사 속도가 증가함에 따라 균일한 절단폭과 Clearance Width가 형성되었다. 따라서, 활물질의 코팅 두께가 균일한 절단면을 형성하는데 영향을 미쳤다.
(4) 전극 절단 공정에서 레이저 가공 적용 시 레이저 가공 조건뿐만 아니라 전극의 두께에 대한 영향도 고려되어야 한다.
Acknowledgments
The research described herein was sponsored by the National Research Foundation of Korea (No. NRF-2019R1A2C1089644) grant funded by the Korean government (MSIP; Ministry of Science, ICT & Future planning). The opinions expressed in this paper is those of the authors and do not necessarily reflect the views of the sponsors.
REFERENCES
-
Zubi, G., Dufo-López, R., Carvalho, M., and Pasaoglu, G., “The Lithium-Ion Battery: State of the Art and Future Perspectives,” Renewable and Sustainable Energy Reviews, Vol. 89, pp. 292-308, 2018.
[https://doi.org/10.1016/j.rser.2018.03.002]
-
Tomaszewska, A., Chu, Z., Feng, X., O'Kane, S., Liu, X., et al., “Lithium-Ion Battery Fast Charging: A Review,” eTransportation, Vol. 1, Paper No. 100011, 2019.
[https://doi.org/10.1016/j.etran.2019.100011]
-
Yang, Y. S., Hwang, C. Y., and Yoo, Y. T., “T-Joint Welding Characteristics of Multi-Thin Plate Dissimilar Thickness of SS41 of Automobile Battery by Using Nd: YAG Laser,” Journal of the Korean Society for Precision Engineering, Vol. 29, No. 10, pp. 1078-1088, 2012.
[https://doi.org/10.7736/KSPE.2012.29.10.1078]
-
Kronthaler, M. R., Schloegl, F., Kurfer, J., Wiedenmann, R., Zaeh, M., et al., “Laser Cutting in the Production of Lithium Ion Cells,” Physics Procedia, Vol. 39, pp. 213-224, 2012.
[https://doi.org/10.1016/j.phpro.2012.10.032]
-
Väyrynen, A. and Salminen, J., “Lithium Ion Battery Production,” The Journal of Chemical Thermodynamics, Vol. 46, pp. 80-85, 2012.
[https://doi.org/10.1016/j.jct.2011.09.005]
-
Lee, D. and Mazumder, J., “Effects of Momentum Transfer on Sizing of Current Collectors for Lithium-Ion Batteries during Laser Cutting,” Optics & Laser Technology, Vol. 99, pp. 315-325, 2018.
[https://doi.org/10.1016/j.optlastec.2017.09.016]
- Ahn, D. G., Kim, M. S., Park, H. J., and Yoo, Y. T., “Influence of Process Parameters on the Surface Roughness and the Striation Formation of the Cut Section for the Case of Cutting of CSP 1 N Sheet Using High Power CW Nd: YAG Laser,” Journal of the Korean Society for Precision Engineering, Vol. 23, No. 7, pp. 30-38, 2006.
-
Lutey, A. H., Fortunato, A., Carmignato, S., and Fiorini, M., “High Speed Pulsed Laser Cutting of LiCoO2 Li-Ion Battery Electrodes,” Optics & Laser Technology, Vol. 94, pp. 90-96, 2017.
[https://doi.org/10.1016/j.optlastec.2017.03.022]
-
Lutey, A. H., Fortunato, A., Carmignato, S., Ascari, A., Liverani, E., et al., “Quality and Productivity Considerations for Laser Cutting of LiFePO4 and LiNiMnCoO2 Battery Electrodes,” Procedia CIRP, Vol. 42, pp. 433-438, 2016.
[https://doi.org/10.1016/j.procir.2016.02.227]
-
Lee, D., Patwa, R., Herfurth, H., and Mazumder, J., “Parameter Optimization for High Speed Remote Laser Cutting of Electrodes for Lithium-Ion Batteries,” Journal of Laser Applications, Vol. 28, No. 2, Paper No. 022006, 2016.
[https://doi.org/10.2351/1.4942044]
-
Lee, D., “Investigation of Physical Phenomena and Cutting Efficiency for Laser Cutting on Anode for Li-Ion Batteries,” Applied Sciences, Vol. 8, No. 2, p. 266, 2018.
[https://doi.org/10.3390/app8020266]
-
Lutey, A. H., Fortunato, A., Ascari, A., Carmignato, S., and Leone, C., “Laser Cutting of Lithium Iron Phosphate Battery Electrodes: Characterization of Process Efficiency and Quality,” Optics & Laser Technology, Vol. 65, pp. 164-174, 2015.
[https://doi.org/10.1016/j.optlastec.2014.07.023]
M.S. candidate in the Department of Future Convergence Engineering at Kongju National University. His research interest includes laser processing on lithium-ion battery manufacturing. Currently, his primary research is in electrode laser cutting, electrode laser structuring, and Li metal processing for achieving high-performance battery.
E-mail: dongkyu5610@gmail.com
He graduated Ph.D in Mechanical Engineering at the University of Michigan- ANN Arbor in 2011 and 2012. Currently, he is an associate professor in the Department of Mechanical and Automotive Engineering at Kongju National University. His research interest is to understand multi-physical phenomena during laser material processing of composite materials such as lithium-ion batteries, electrical passive components, and PCB. Furthermore, his research interest is to fabricate biomaterials using laser ablation.
E-mail: ldkkinka@kongju.ac.kr