
전기자동차 모터의 채널 형상에 따른 냉각 성능 연구
Copyright © The Korean Society for Precision Engineering
This is an Open-Access article distributed under the terms of the Creative Commons Attribution Non-Commercial License (http://creativecommons.org/licenses/by-nc/3.0) which permits unrestricted non-commercial use, distribution, and reproduction in any medium, provided the original work is properly cited.
Abstract
This research investigated the cooling performance of the motor in electric vehicle depending on the shape of the cooling channel. The research, conducted numerically by FLUENT V20.1, focused on the numerical study of heat transfer coefficients to find an optimum design shape with high cooling performance. To compare the cooling performance, the temperatures in the coil and cooling channel were analyzed. As a result of forced convection, the average cooling channel velocity of Case 2 was 38% faster than Model N and 34% faster than Case 1. The maximum temperature of the cooling channel of Case 2 was 8.7% lower than Model N and 5.6% lower than Case 1. The minimum temperature of the coil of Case 2 was 2.7% lower than Model N and 4.3% lower than Case 1. The maximum temperature of the coil of Case 2 was 4.6% lower than Model N and 2.9% lower than Case 1. Ultimately, cooling channel of Case 2 showed the best cooling performance and improved driving performance for motor durability.
Keywords:
Electric vehicle, Drive motor, Virtual fluid dynamics, Cooling performance, Convection cooling, Cooling channel키워드:
전기자동차, 구동 모터, 가상 유체 역학, 냉각 성능, 대류 냉각, 냉각 채널1. 서론
최근 내연기관을 대체할 수 있는 전기자동차 연구개발이 활발하게 이루어지고 있으며 기존 내연기관 자동차로 인한 CO2, SO2, NOx 등의 유해가스가 각종 대기오염과 지구 온난화에 끼치는 영향을 막기 위해 미래형 자동차의 연구 방향은 전 세계적으로 온실가스 배출 저감, 기후변화 등에 집중되고 있다. 강화된 환경규제를 준수하고, 기계산업의 소형화, 자동화로 인해 고효율, 고출력의 전기 모터에 대한 연구 개발은 전기에너지를 사용할 미래의 인류 기술사회에서 필수적인 기술 해결 과제이다. 고출력 모터에 대한 요구가 증가하는 것은 모터가 사용되는 시스템의 발열량을 증가시키고, 이는 모터 성능 저하의 주요 요인이 된다.1 모터는 전기에너지를 기계에너지로 변환하여 동력 전달축을 회전시키고, 나머지 손실을 열에너지로 방출한다. 그러므로 고출력, 고효율 모터를 사용하기 위해 열관리시스템 기술이 필요하다. 냉각 및 방열 효과를 고려하여 모터를 설계하여 다양한 운전 및 환경조건에서 모터의 온도를 보다 낮게 유지시켜야 한다. 그러므로 열적인 측면에서 안정적으로 운용하기 위해서 효과적인 냉각 및 방열 설계가 필요하다.2 모터의 냉각 기술은 발생한 열을 냉각하여 모터를 안정적으로 운용할 수 있도록 하는 기술이다. 모터의 냉각 성능에서 중요한 요인은 코일의 온도를 감소시키는 것이다. 실제로 모터에서 코일의 발열량이 가장 많고, 코일의 온도에 따라 영구 자석의 성능인 자속 밀도를 결정하기 때문이다. 여기서 영구 자석은 Nd 계열의 희토류 영구 자석이며, 이는 높은 자속 밀도에 의한 높은 토크 밀도를 낼 수 있기 때문에 미래자동차, 모빌리티 및 가전 분야 등 다양한 분야에 사용되고 있다. 이때 Nd 계열 영구 자석은 높은 온도에서 영구 감자가 될 수 있는 Knee Point가 나타나 외부 자계에 의해 영구 감자가 나타날 수 있다.3 이는 영구 자석의 성능이 감소된다는 것을 의미한다.
냉각 성능이 우수한 핀을 가진 모터 하우징 설계, 워터 자켓유로 설계, 열전도성이 우수한 방열 소재, 열 저항을 최소화할 수 있는 접합 구조 등은 냉각을 위한 설계에 있어 주요 인자이다. 이에 관한 기존 연구들은 히트파이프를 부착한 구동 모터의 냉각 성능에 관한 연구,4 냉각핀 유무에 따른 열 유동해석을 통한 모터 하우징의 냉각 성능에 관한 연구,5 하이브리드 자동차용 모터 내부의 오일 냉각 시스템에 대한 연구,6 고출력 모터의 여러 냉각 방식인 공냉, 수냉 및 유냉에 대한 연구,7 냉각 채널의 감긴 횟수와 입-출구의 위치 및 개수에 따른 냉각 성능 연구,8 영구 자석 모터의 냉각 유로의 냉각수-공기 유량 변화 및 공냉 유로 형상 변화에 따른 냉각 성능에 대한 연구,9 전기모터 회전자 냉각 구조 연구 및 유동해석10 등이 있지만 실제 차량용 모터의 냉각 채널 형상에 따른 냉각 성능에 대한 연구는 거의 수행되지 않았다.
본 연구는 냉각 채널을 이용한 전기자동차 모터 내 강제 대류 냉각 시스템에서 냉각 채널의 형상을 변화시켜 기존 형상을 개선한 2가지 Case를 제시하고, 코일의 온도 및 주변 부품들의 온도 분포를 수치적으로 해석하여 냉각 채널의 형상별 냉각 성능을 비교하고, 성능이 우수한 냉각 채널의 형상을 설계하는 것이 이번 연구 목표이다.
2. 설계 및 수치해석
Fig. 1은 국내 완성차 업체 K사 전기자동차 모델 N에 탑재하는 구동 모터 사진이다. Fig. 2는 Fig. 1의 모델 N을 직접 분해 및 실측하여 CATIA V5 R21로 모델링한 CAD 형상을 렌더링한 사진이다. 동력 전달 축, UVW Connector, 코일의 양끝단 등 유동해석을 중점적으로 할 필요가 없는 부분은 단순화하여 3D 모델링을 하였다. Case별 냉각 채널의 형상만 변경하여 모델링하였고, 냉각 채널을 제외한 부품들은 모두 동일하다. Fig. 3은 CATIA V5 R21로 모델링한 3가지 냉각 채널의 형상을 ANSYS V20.1로 Import한 사진이다. Fig. 3(a)는 Fig. 2의 모델 N의 냉각 채널 형상이고, Figs. 3(b)와 3(c)는 Fig. 2의 냉각 채널 형상을 모티브로 삼아 동일한 질량 유량을 기준으로 기존 냉각 채널 내부 냉각수의 속도가 더 증가할 수 있는 형상을 자체적으로 개선 설계한 Case이다. Figs. 3(b)는 양쪽으로 U 형상의 채널을 나누어 배치한 것이고, 3(c)는 3(b)와 유사한 형상에서 U 채널의 내부를 세 갈래로 나누어 설계한 형상이다. Figs. 3(b)보다 3(c)의 U 형상의 냉각 채널의 개수가 많이 형성되어 있으며, 냉각 채널 각각의 단면적이 작다. Fig. 3의 3가지 냉각 채널 모두 앞부분이 냉각 채널의 입구이고, 뒷부분이 출구이다. Table 1은 CATIA V5 R21을 활용해 모델링한 하우징, 동력 전달 축, 회전자, 고정자, 영구 자석, 코일의 크기를 나타낸 것이다.
2.1 설계 조건
냉각 채널에서의 유체의 열전달 및 유동해석을 진행하기 위해 에너지 보존 법칙, 질량 보존 법칙, 운동량 보존 법칙을 ANSYS FLUENT V20.1로 비압축성 정상 상태 유동해석을 진행하였다. 냉각 채널의 내부 유동의 최대 레이놀즈 수는 6,800으로 계산되어 난류 유동해석을 진행하였다. 또한 유체 유동 경계층 흐름에 대한 계산의 정확성을 높이며 더 많은 계산을 하기 위해서 k-omega SST 모델을 사용하였다.
초기 조건은 주변의 공기의 온도를 상온인 25oC로 설정하였다. 냉각수의 온도는 실제 차량 운행 중일 때와 유사한 조건으로 해석을 수행하기 위해 65oC로 설정하였고, 실제 모터에서 사용하는 유량인 7 LPM을 질량 유량으로 환산하여 3가지 Case 모두 입구에서 질량 유량 0.15 kg/s로 설정하였다. 출구는 모두 대기압으로 가정하여 계기 압력 0 Pa을 설정하였다. 모터 내부의 코일에 일정 열 유속 조건을 열 경계 조건으로 사용하였다. Table 2는 열 및 유동해석을 위해 설정한 경계 조건들을 나타낸 것이다. 냉각수는 실제 사용되는 Ethylene Glycol을 선택하였고 하우징, 고정자, 코일, 회전자, 영구 자석, 동력 전달 축, Ethylene Glycol의 해석에 필요한 밀도, 비열, 열전도율, 점성 계수를 Table 3에 나열하였다.
2.2 격자 생성 및 의존도 Test
모터의 하우징, 냉각 채널, 고정자, 코일, 회전자, 영구 자석, 동력 전달 축을 ANSYS MESH를 이용하여 수치해석을 위한 격자를 생성하였다. 모터의 하우징 내부 냉각 채널의 형상에는 조밀한 격자가 중요하다. 또한 냉각 채널의 격자와 하우징, 고정자, 코일, 회전자, 영구 자석, 동력 전달 축의 격자가 이어져야 한다. 격자가 이어짐으로써 해석 진행에 있어 문제가 없도록 하였다. 500만개에서 2,300만개의 격자를 생성하여 코일의 최대온도를 비교하여 격자 의존도 검사를 진행하였다. 570만개 격자에서 Tmax가 135.72oC, 오차율이 1%, 856만개 격자에서 Tmax가 135.5oC, 오차율이 0.8%, 1,047만개 격자에서 Tmax가 135.25oC, 오차율이 0.4%, 1,381만개 격자에서 Tmax가 134.72oC, 1,669만 개 격자에서 Tmax가 134.6oC, 오차율이 0.1%, 1,932만개 격자에서 Tmax가 134.5oC, 오차율이 0.15%, 2,355만개 격자에서 Tmax가 134.44oC, 오차율이 0.2%로 나타나며 이를 Table 4에 정리하였다. 해석 시간과 수렴성을 고려하여 1,381만개의 격자를 선택하였고, 격자 의존도 검사 결과를 Fig. 4에 도시하였다. Fig. 1의 K사 모델 N과 Fig. 3에 나와있는 다른 두 가지 Case는 냉각 채널의 형상을 제외한 모든 부품들이 동일한 형상이다. 하우징, 회전자, 영구 자석, 동력 전달 축, 냉각 채널은 Tetra 격자로 설정하였다. 냉각 채널의 경우 벽면에서 속도 구배가 매우 크기 때문에 조밀한 격자를 위해 냉각 채널의 벽면에 Inflation을 사용하였다.
벽면에서의 격자 층수를 4층으로 설정, Growth Rate를 1.2로 설정하였고, 최대두께를 1 mm로 설정하였다. 냉각 채널의 Body Sizing으로 1 mm를 주었다. 고정자와 코일은 Hexa 격자를 사용하였고, Body Sizing으로 1.5 mm를 주었다. 하우징과 축은 10 mm, 영구 자석과 회전자는 5 mm로 Body Sizing을 주었다. K사 모델 N의 냉각 채널 격자 수는 488만개, 노드 수는 162만 개이다. 총 격자 수는 1,381만개, 노드 수는 385만개이다. Table 5는 Fig. 3의 모델 N과 Cases 1, 2의 격자 수와 노드 수를 표로 나타낸 것이다. Fig. 5는 K사의 모델 N의 모터 전체에 대한 격자의 형상이고 Fig. 6은 모델 N과 Cases 1과 2의 냉각 채널의 격자 형상이며 냉각 채널에서의 Y+는 0-20.0을 유지하였다.
3. 결과 및 고찰
본 연구에서는 전기자동차 모터의 형상을 단순화하고 ANSYS FLUENT V20.1을 활용하였다. Fig. 3에 제시한 K사의 모델 N과 Cases 1과 2를 냉각 채널의 형상만 변경하고 고정자, 코일, 회전자, 영구 자석, 축은 동일한 형상으로 강제 대류 상태에서 수치해석을 진행하였다. 3가지의 형상에 대하여 냉각 채널의 속도 분포, 온도 분포와 모터 하우징 내에 있는 코일의 온도 분포를 비교하여 냉각 성능이 가장 우수한 형상을 설계하기 위하여 유동해석을 진행하였다. 냉각 성능이 가장 우수한 냉각 채널의 형상과 코일을 찾기 위해 온도 분포가 가장 큰 코일 표면에 국소적인 지점을 선택 후 열전달 계수(h)를 구하여 냉각 채널과 코일의 냉각 성능을 비교 및 분석하여 냉각 성능이 가장 우수한 냉각 채널을 선정하였다. 해석의 신뢰성 확보를 위해 KISTI에서 Intel Xeon Phi 7250 1.4 GHz 모델 68 코어 96 GB, 6Ch per CPU의 성능을 가진 슈퍼컴퓨터를 사용하였다.
3.1 속도 분포
Figs. 7은 모터의 냉각 채널 형상별 속도 벡터 분포를 나타낸 그림이며, 7(a)는 K사의 모델 N, 7(b) 및 7(c)는 모델 N을 개선 설계한 형상의 냉각 채널 내부의 속도 벡터이다. Fig. 7(a)의 입구에서는 좁은 면적으로 인해 비교적 빠른 속도를 나타냈고, 냉각 채널 내부에서 단면적이 증가하여 속도가 감소하다 좁은 면적의 출구에서는 다시 속도가 증가하였다. 최고속도는 출구에서 2.017 m/s로 나타났고, 냉각 채널 전체의 평균속도는 0.496 m/s로 나타났다. Fig. 7(b)에서는 입구와 출구, 냉각 채널 내부에서 비교적 유사한 속도를 나타냈다. 최고속도는 U 형상에서 1.139m/s로 나타났고, 평균속도는 0.509 m/s로 나타났다. Fig. 7(c)에서 입구와 출구 속도는 유사하게 나타났고, 냉각 채널 내부에서는 각각의 면적이 작아 비교적 빠르게 나타났다. 최고속도는 Fig. 7(b)와 동일하게 U 형상에서 1.175 m/s로 나타났으며, 평균속도는 0.683 m/s로 나타났다. 3가지 냉각 채널 형상 중 냉각 채널의 개수가 가장 많고, 채널 각각의 단면적이 가장 좁은 Figs. 7(c)에서 가장 빠른 평균속도를 나타냈고, 7(a)에서 가장 느린 평균속도를 나타냈다. 평균속도는 Figs. 7(c)가 7(a)에 비해 37%, 7(b)에 비해 34% 빠르게 나타났다.
3.2 온도 분포
Fig. 8은 냉각 채널에서의 온도 분포를 나타낸 그림이다. 3가지 형상 모두 입구에서는 65oC로 가장 낮은 온도가 나타났고, 최고온도는 냉각 채널 출구 쪽에서 가장 냉각 성능이 떨어지는 코일에 인접한 냉각 채널 안쪽 벽면에서 모두 동일한 위치에서 나타났다. Fig. 8(a)에서 최고온도 101.32oC, 온도 편차 36.32oC로 나타났다. Fig. 8(b)에서 최고온도 98.07oC, 온도 편차 33.07oC로 나타났다. Fig. 8(c)에서 최고온도 92.53oC, 온도 편차 27.53oC로 나타났다. 최고온도 Figs. 8(c)가 8(a)에 비해 8.79oC, 8(b)에 비해 5.54oC 낮게 나타나 냉각 채널 내의 최고온도는 8(c)가 가장 낮게 나타났다.
Figs. 9는 8의 3가지의 냉각 채널을 통해 얻은 수치해석 결과에서 코일의 표면 온도를 나타내는 그림이다. 코일 표면의 최고 온도의 위치는 Figs. 9(a)부터 9(c) 모두 냉각 채널의 출구에 인접한 위치에서 나타났고, 최저온도의 위치는 냉각 채널의 입구에 인접한 위치에서 나타났다. Figs. 9(a)는 K사의 모델 N의 냉각 채널을 탑재한 코일의 표면 온도이고, 9(b)는 Case 1, 9(c)는 Case 2의 냉각 채널을 탑재한 코일 표면의 온도를 나타낸다. Fig. 9(a)에서 최저온도 117.24oC, 최고온도 134.72oC, 온도 편차 17.48oC로 나타났다. Fig. 9(b)에서 최저온도 119.22oC, 최고온도 132.35oC, 온도 편차 13.13oC로 나타났다. Fig. 9(c)에서 최저온도 114.1oC, 최고온도 128.52oC, 온도 편차 14.42oC로 나타났다. Figs. 9(a)는 최고온도와 온도 편차가 가장 높게 나타나 9(b)와 9(c)에 비해 냉각 성능이 가장 떨어지며, 9(c)의 최고온도는 9(a)에 비해 6.2oC, 9(b)에 비해 3.83oC 낮게 나타나 Fig. 9의 Case 2의 냉각 성능이 가장 우수하다고 할 수 있다.
Figs. 10은 9에 나와있는 코일 표면 온도 분포에서 냉각 성능이 취약하고, 온도 편차가 가장 큰 표면을 찾아 코일 표면 국소적 대각선 위치의 온도 분포를 나타낸 것이다.
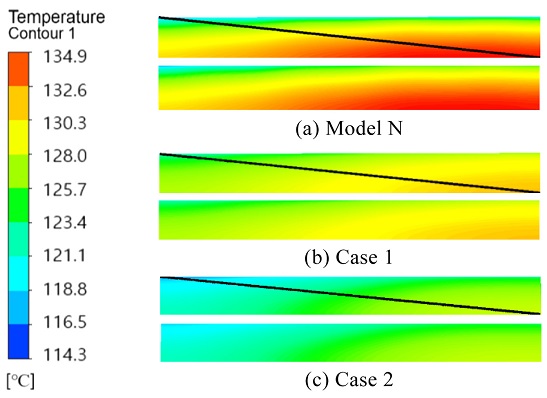
Temperature contours of diagonal position (R+) on the coil surface with maximum temperature deviation at three different cases of coil surface
3가지 형상의 냉각 채널에 대한 동일한 위치의 코일 표면에서 온도 편차가 대각선 방향으로 뚜렷하게 변화하여 대각선을 긋고, 11개 지점으로 나누어 온도 분포를 확인하였다. 각각의 코일의 표면에 따라 냉각 성능을 정량적으로 비교하기 위해 Nusselt 수를 계산하였다. Nusselt 수는 열전달 계수(h)의 무차원 파라미터로 대류 열전달에 대한 유체 내의 전도 열전달의 상대적인 비를 나타내는 무차원 파라미터이다.
코일 표면 중 냉각 성능이 취약하고 온도 편차가 가장 큰 지점을 범위로 설정하여 11개 지점의 국소적 위치(R)에서 Nusselt 수를 계산하여 냉각 성능을 비교했다. 국소적 위치(R)의 무차원 기준 길이(R+)를 식(1)을 통해 계산하여 나타냈다.
(1) |
식(1)의 R은 코일 표면의 대각선 위의 국소적 위치, L은 코일 위의 대각선 전체 길이이다.
(2) |
식(2)의 Tc는 모델N, Cases 1과 2의 국소적 위치 11개 지점에서의 코일 표면 온도이고 T2(min)는 3개의 코일 표면들 중 냉각 성능이 가장 우수하게 나타난 코일 표면(Case 2의 R+ = 0)의 온도이다.
Fig. 11은 냉각 성능이 가장 우수한 국소적 위치의 코일 표면(Case 2의 R+= 0)의 온도에 대하여 다른 코일 표면의 온도는 어느 정도 증가하였는지 한눈에 파악하기 위해 정량적으로 나타낸 그래프이다. 무차원의 기준 길이(R+)를 코일 표면의 좌측 상단(R+= 0)에서 시작하여 우측 하단(R+= 1)까지 0-1로 설정하였다. R+= 0은 냉각수가 냉각 채널로 유입되는 입구와 가장 근접한 코일 부분이고, R+ = 1은 냉각수가 냉각 채널 외부로 유출되는 냉각 채널 출구와 가장 근접한 코일 부분이다. Fig. 11을 보면 R+ = 1일 때 모델 N의 ΔT가 16oC, Case 1의 ΔT가 14oC, Case 2의 ΔT가 10oC로 모델 N에 비해 Case 1이 12.5%, Case 2가 37.5% 낮게 나타나 Case 2의 냉각 성능이 가장 우수한 것을 알 수 있다.
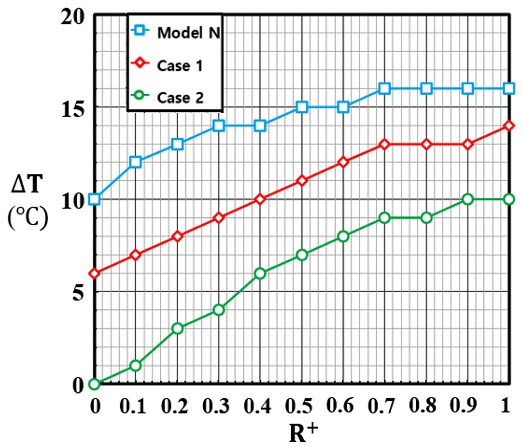
Temperature deviation of coil surface vs. dimensionless local positions of coil surface at three cases
Table 6은 Fig. 10의 코일 표면 위의 대각선상 온도 분포를 무차원 기준 길이(R+)의 위치에 해당하는 온도와 열전달 계수(h)를 수치적으로 계산하여 나타낸 표이다. Table 6에 나타나 있는 온도와 열전달 계수(h)를 통해 Nusselt 수로 나타내어 3가지 Case의 냉각 성능을 비교하였다.
Fig. 12는 온도 편차가 가장 큰 3가지의 코일 표면 위 대각선의 R+를 위치별로 Nusselt 수로 무차원화하여 레이놀즈 수(ReR)에 대한 냉각 정도를 한눈에 파악하기 위하여 정량적으로 나타낸 그래프이다. 3가지 코일 모두 레이놀즈 수가 증가할수록 Nusselt 수가 감소하여 냉각 성능이 떨어지는 것을 알 수 있다. Fig. 12의 그래프를 보면 동일한 레이놀즈 수에서 Nusselt 수를 비교해 본 결과 Case 2가 가장 큰 Nusselt 수를 가진다는 것을 알 수 있다. 최대 Nusselt 수를 기준(ReR = 0)으로 Case 2가 모델 N과 Case 1에 비해 각각 18.9, 11.4% 크며, 최소 Nusselt 수 기준으로 Case 2가 모델 N과 Case 1에 비해 각각 9.5, 6.4% 크게 나타나 Case 2의 냉각 채널의 냉각 성능이 가장 우수한 것을 알 수 있다.
4. 결론
본 연구는 현재 사용 중인 K사의 전기자동차 모델 N의 모터를 분해 및 실측하여 모델링 한 후 냉각 채널을 제외한 모든 부품은 동일하게 설계하고 새로운 2 가지 Case의 냉각 채널을 설계하였다. 모델 N과 2가지 Case의 냉각 채널과 코일에서의 속도 분포, 온도 분포를 수치적으로 해석 및 비교하여 가장 우수한 냉각 성능을 가지는 냉각 채널을 찾는 것에 초점을 두고 연구하였다. 코일 표면에서 온도 편차가 가장 큰 위치를 설정하고, 무차원 기준 길이(R+)에 따른 레이놀즈 수로 나타내어 각각 11개 지점에 나타난 온도 분포와 열전달 계수(h)를 통해 강제 대류 열전달에 의한 냉각 성능을 비교하기 위해 Nusselt 수를 계산하여 진행하였다. 이러한 연구의 결론을 다음과 같이 정리하였다.
(1) 동일한 질량 유량을 가지는 3가지 냉각 채널 중 Case 2의 냉각 채널 내부 냉각수의 평균 속도가 모델 N에 비해 37%, Case 1에 비해 34% 빠르게 나타났다.
(2) 냉각 채널에서의 온도를 비교해 보았을 때 냉각 채널 내부 냉각수의 평균 속도가 가장 빠른 Case 2의 냉각 채널의 최고온도가 모델 N에 비해 8.7%, Case 1에 비해 5.6% 낮게 나타났다.
(3) 모터의 출력을 유지 및 상승시키기 위해서는 냉각 채널에서의 강제 대류 냉각을 통해 코일에서 우수한 냉각 성능을 가져야 한다. 이번 연구를 통해 3가지 중 냉각 채널의 온도가 가장 낮은 Case 2의 냉각 성능(코일의 최대온도 기준)이 모델 N에 비해 4.6%, Case 1에 비해 2.9% 우수하다는 것을 알 수 있었고, 냉각 채널은 생산하는데 있어서 기술적 문제는 없는 것으로 판단한다.
(4) 본 연구를 기반으로 추후에는 전기자동차 모터의 냉각 채널은 Case 2를 기준으로 냉각 채널과 코일의 온도 외에도 코일을 둘러싸고 있는 에나멜 코팅까지 삽입하여 고정자, 코일, 에나멜, 회전자에서 열 변형이 발생하는지, 발생하면 어느 정도 발생하는지를 연구할 것이고, 열 변형을 최소화할 수 있는 냉각 채널과 코일의 형상을 보완하여 모터의 냉각 성능을 향상시킬 것이다.
REFERENCES
- Kang, D. H., “An Optimization on the Flow Passages of Outer Rotor Motors for Improving Cooling Performance,” M.Sc. Thesis, Hanyang University, 2015.
- Lee, J. H., Ha, M., Seo, K., and Park, Y., “Thermal Analysis of Electric Vehicle Motor Using CFD,” Proc. of the KSME Fall Annual Conference, pp. 2711-2714, 2010.
- Jin, C. S., “Estimation of Permanent Magnet Temperature of Permanent Magnet Motor,” Proc. of the Conference on the Korean Institute of Electrical Engineers, pp. 633-634, 2013.
- Lee, D. R., “Investigation of Cooling Performance of the Driving Motor Utilizing Heat Pipe,” Journal of the Korea Society for Power System Engineering, Vol. 10, No. 4, pp. 11-16, 2006.
- Seo, J. and Cho, C., “Study on the Change of Cooling Performance of Motor Housing for Automobile,” Proc. of the KSME Annual Conference, pp. 2170-2174, 2012.
-
Kim, J. S., Moon, J. W., Kwak, T. H., and Kang, T. G., “Numerical Investigation on an Oil Cooling System in the Motor for a Hybrid Vehicle,” Journal of Computational Fluids Engineering, Vol. 22, No. 3, pp. 86-94, 2017.
[https://doi.org/10.6112/kscfe.2017.22.3.086]
- Kang, Y. and Kim, D. K., “Comparative Study of Cooling Methods of Motor for Electric Vehicles,” Proc. of the KSME Annual Conference, p. 1646, 2019.
- Choi, H. J., “A Study on the Design Factor Analysis of Water Jacket for Improving the Cooling Performance of Motor,” M.Sc. Thesis, Konkuk University, 2021.
-
Nam, G. G., Joo, W. G., Son, S. W., Kim, J, H., Park, J. Y., et al., “A Numerical Study on the Cooling Channel of Permanent Magnet Motor,” The Korean Society for Fluid Machinery Journal of Fluid Machinery, Vol. 23, No. 2, pp. 35-41, 2020.
[https://doi.org/10.5293/kfma.2020.23.2.035]
- Lee, N. K., “Electric Motor Rotor Design to Improve Cooling Effect,” Proc. of the Spring Conference on the Korean Society of Automotive Engineers, pp. 1157-1158, 2017.
B.S. candidate in the School of Mechanical and Automotive Engineering, Catholic University of Daegu. His research interest is electric vehicle and future alternative energy.
E-mail: qkrtlahr12@cu.ac.kr
B.S. candidate in the School of Mechanical and Automotive Engineering, Catholic University of Daegu. His research interest is electric vehicle and future alternative energy.
E-mail: tjdghks7413@cu.ac.kr
B.S. candidate in the School of Mechanical and Automotive Engineering, Catholic University of Daegu. His research interest is electric vehicle and future alternative energy.
E-mail: alsrl3901@cu.ac.kr
M.S. candidate in the Graduate School of Mechanical Engineering, Sungkyunkwan University. His research interest is turbo machinery, future alternative energy, and aerospace engineering.
E-mail: sjh012@skku.edu
Professor in the School of Mechanical and Automotive Engineering, Catholic University of Daegu. His research interest is heat transfer, fluid engineering, and electric vehicle.
E-mail: dlee@cu.ac.kr