
전기자동차 매립형 영구자석 동기 전동기의 토크 리플 및 토크를 고려한 로터 및 영구자석 설계
Copyright © The Korean Society for Precision Engineering
This is an Open-Access article distributed under the terms of the Creative Commons Attribution Non-Commercial License (http://creativecommons.org/licenses/by-nc/3.0) which permits unrestricted non-commercial use, distribution, and reproduction in any medium, provided the original work is properly cited.
Abstract
The aim of this research was to investigate the torque performance of the motor in an electric vehicle depending on the rotor shape and air gap. The research focused on numerical comparison of torque performance of new rotors based on the average torque and torque ripple rate, which appeared according to the number and placement of permanent magnets. This research was numerically analyzed by MAXWELL V21.1. Average torque values in cases 1, 2, and 3 were increased, but vibration and noise in cases 1 and 3 were increased as the torque ripple rate increased. Considering the average torque and torque ripple rate, the torque performance of case 2 was the most optimal. Compared with Model N, the average torque of case 2 was increased by 9.1% and the torque ripple rate was reduced by 1.5%. The torque performance according to the size of air gap was compared with the basic model of case 2, which showed the best performance. An air gap of 0.7 mm applied to Model N showed the best torque performance. An additional magnet on case 2 and air gap of 0.7 mm provided the best torque performance and improved the driving motor performance for motor durability.
Keywords:
Electric vehicle, Drive motor, IPMSM, Torque ripple, Rotor, Stator키워드:
전기자동차, 구동 모터, 매립형 영구자석 동기 전동기, 토크 리플, 회전자, 고정자1. 서론
최근 환경 오염, 지구 온난화 등의 문제로 인해 경량화, 소형화, 고출력, 고효율 전동기에 대한 관심이 증가하고 있고, 국내외 기술력을 가진 기업들의 전기자동차 시장에 대한 경쟁이 치열해짐으로써 전기자동차 성능의 획기적인 향상이 기대되고 있다. 영구자석 동기 전동기는 고효율과 고출력을 갖기 때문에 가정이나 산업기기 등 여러 분야에서 많이 사용되고 있다. 전기자동차 구동용 영구자석 동기 전동기는 높은 단위 전류당 출력 밀도 및 토크를 요구하기 때문에 고효율, 고출력 밀도, 높은 토크 등의 개발 목표를 가지고 있다. 매립형 영구자석 동기 전동기는 로터 영구자석의 형상과 크기, 매립 형태에 따라 전동기의 특성에 차이가 발생하게 된다. 고속 운전 시 높은 안정성을 가지고 릴럭턴스 토크를 이용해 높은 출력을 낼 수 있으며, 구조적으로 다양한 로터 형상의 설계가 가능하다는 장점이 있다.1 그러나 고속 회전에 따른 소음 및 진동의 증가, 기계적 손실과 마모로 인한 수명 단축, 고성능 감속기 개발에 의한 비용 증가, 도체의 주파수에 따라 저항이 증가되고, 결과적으로 동손을 증가시켜 전동기의 효율 저하와 고발열을 유발하는 것이 단점이다. 이러한 단점을 해결하기 위해 높은 토크를 가지지만 토크 리플, 코깅 토크를 저감시킨 고효율 전동기의 기술 개발은 필수적이다.
이에 관한 기존 연구들은 릴럭턴스 토크와 마그네틱 토크의 조합에 따른 약 자속 영역 특성 분석 후 비대칭 배리어 설계를 통해 약 자속 영역에서 높은 토크를 설계하는 연구,2 IPM 전동기의 코깅 토크 저감을 위한 연구, 단위 전류당 토크 밀도 증가를 위해 로터 형상을 설계하는 연구,3 코깅 토크 및 구동 토크 리플 저감을 목적으로 한 노치와 배리어 설치와 로터 형상이 변위의 특성에 미치는 영향에 대한 연구,4 로터 표면에 노치를 설치하여 공극에서 자속밀도 분포를 변화시키고, 토크 리플 및 코깅 토크의 크기 변화를 확인하고 노치의 크기가 코깅 토크에 미치는 영향에 대한 연구,5 로터 영구자석의 두께 및 오프셋 반지름을 설계 변수로 한 전류각 특성해석에 대한 연구,6 레저 선박에 장착되는 매립형 영구자석 동기 전동기의 로터 극수를 변경하여 높은 효율의 모델을 찾는 연구7 등이 있지만 실제 로터의 형상과 영구자석 배열을 변경시켜 토크를 향상시키는 연구는 많이 수행되지 않았다.
본 연구는 현재 출시되어있는 K사의 완성차 모델 N과 C사의 모델 B에 탑재되는 전동기의 전자기 해석을 통해 토크 성능이 우수하고, 토크 리플이 낮게 나타나는 전동기를 기준 형상으로 설정하고, 로터의 내부 설계 형상을 변경하여 전자기 해석 전용 소프트웨어 ANSYS MAXWELL을 활용하여 전동기의 토크를 수치적으로 해석 후 비교하였다.
본 연구의 기술적 의의는 토크 밀도를 향상시키며 토크 리플을 감소시켜 소형화와 경량화를 추구하는 최근 전기자동차 모터 기술 트렌드에 맞는 성능이 우수한 로터와 내부 영구자석을 설계하는 것이 목표이다.
Fig. 1은 본 연구를 수행한 미래에너지 연구실에서 보유한 전기자동차 모델 N과 모델 B에 탑재되는 전동기의 형상이다. Fig. 2는 전동기 내부 요소 부품들의 실제 형상이며 좌측이 모델 N, 우측이 모델 B의 부품들이다. Figs. 2(a)와 2(b)는 코일과 스테이터가 조립되어있는 형상이며, 2(c)는 로터, 영구자석, 동력 전달축이 조립되어있는 형상이다. Fig. 2(d)는 로터의 단면 형상으로 로터, 영구자석과 배리어(엔지니어링 플라스틱)로 구성되어 있다. 모델 N과 B의 전동기 내부 로터, 스테이터, 영구자석, 코일의 치수와 개수를 Tables 1과 2에 도시하였다.
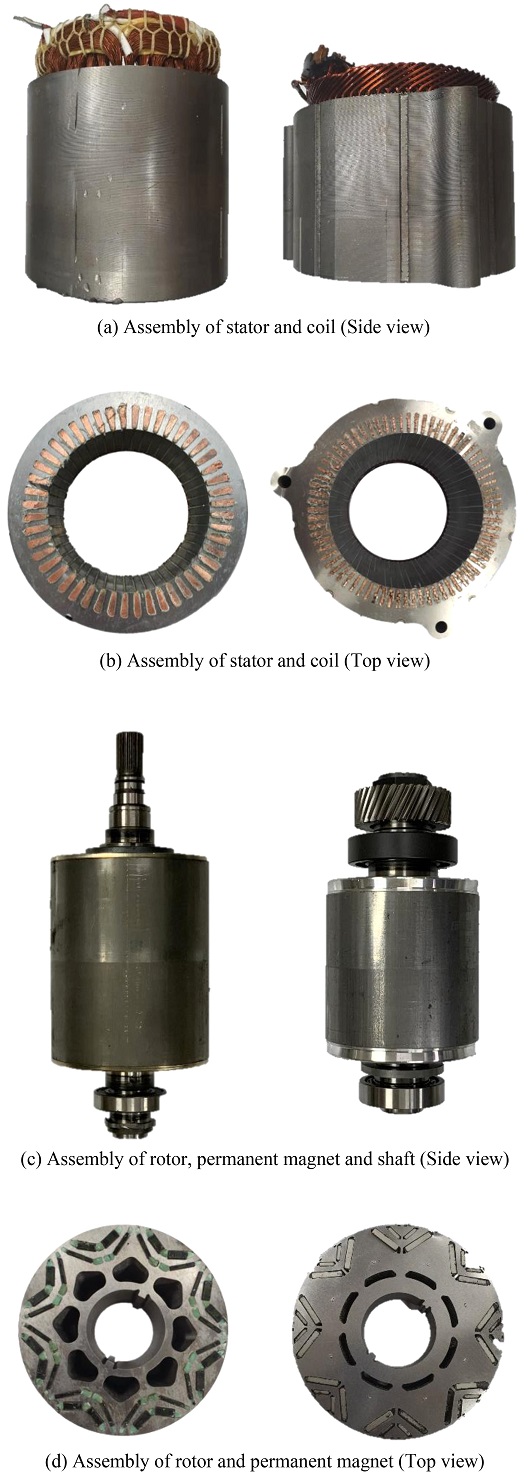
Actual photograph of direct tear-down stator and rotor parts of electric motor model N (Left) and B (Right)
2. 전동기 작동 원리
전동기는 하우징, 스테이터, 코일, 로터, 영구자석, 동력 전달축으로 구성되어있다. 전동기에 전압이 가해지지 않더라도 전동기 내부에는 영구자석으로 인해 자기장이 형성되어 있으며(Magnetostatic State: 정자기 상태) 전동기 시동을 위해 전압 또는 전류를 가하면 로터 내부의 코일에는 전류가 흐르게 되며 암페어의 법칙에 의해 전류에 의한 자기장을 형성하게 된다(Transient State: 과도 상태). 형성된 자기장과 영구자석에 의해 형성된 자기장 간의 힘이 중첩되어 전동기의 동력 전달축을 회전시키는데 이때의 회전력이 전동기의 토크 발생의 포텐셜이다.8 전동기에서 발생되는 토크는 주기적인 파형을 가지기 때문에 토크의 진동을 유발하고, 이는 전동기 내 회전하는 로터의 진동과 소음에 영향을 주는 토크 리플이 나타난다.
3. 로터 형상 설계
본 연구에서는 모델 N과 모델 B 전동기를 직접 분해(Tear-Down) 및 실측하여 스테이터, 코일, 로터, 영구자석을 AUTOCAD를 활용하여 모델링한 후 두 모델의 토크 성능을 비교하여 성능이 우수한 전동기를 선정하였다.
Fig. 3은 모델 N과 B의 스테이터, 코일, 로터, 영구자석의 실제 형상을 AUTOCAD를 활용하여 2D로 나타낸 것이다. Fig. 4는 전자기 해석 전용 ANSYS MAXWELL을 활용해 모델 N과 모델 B의 정자기 상태에서 자기장 세기를 나타낸 것이다. 모델 N의 정자기 상태에서 최대 자기장 세기는 3.8580 [T]로 나타났으며 모델 B의 최대 자기장 세기는 6.9172 [T]로 나타났다. Fig. 5는 모델 N과 모델 B의 과도 상태에서의 토크 성능 곡선이다. 모델 N의 최대 토크는 385, 최소 토크 362, 평균 토크 375 [N·m]로 나타났으며 토크 리플률은 6.1%로 나타났다. 모델 B의 최대 토크는 330, 최소 토크 295, 평균 토크 311 [N·m]로 나타났으며 토크 리플률은 11.2%로 나타났다. 모델 N이 모델 B에 비해 평균 토크는 20.5% 높게 나타났으며 토크 리플률은 5.1%P 낮게 나타나 모델 N이 모델 B에 비해 우수한 토크 성능을 가지는 것을 확인하였다.
전동기의 토크에 영향을 미치는 인자들은 영구자석의 위치, 개수, 종류, 영구자석이 이루고 있는 각도, 코일이 삽입되는 스테이터 내부 슬롯의 형상, 코일의 권선 방식, 코일의 형상, 영구자석과 코일 사이의 거리, 코일의 종류, 로터와 스테이터 사이 공극의 크기 등 수많은 인자들이 존재한다.
본 연구에서는 모델 B에 비해 높은 토크와 낮은 토크 리플을 가진 모델 N의 전동기 형상을 기준으로 영구자석과 코일 사이의 거리, 영구자석의 개수와 배열, 로터와 스테이터 사이 공극의 크기를 기반으로 Case Study를 진행하여 토크와 토크 리플을 비교하였다.
Fig. 6(a)는 모델 N의 스테이터, 코일, 로터, 영구자석의 형상을 AUTOCAD를 활용하여 2D로 나타낸 것이다. Fig. 6(b)는 모델 N의 조건과 모두 동일하게 설정하였고, 영구자석과 코일 사이의 거리를 줄이기 위해 모든 영구자석을 로터 외곽으로 1.5 mm 이동하여 설계한 것이다. 모델 N에서는 영구자석이 2 Layer로 배열되어 있는데 Figs. 6(c)는 영구자석의 배열을 3 Layer로 설계하였고, 6(d)는 6(b)와 동일한 방법을 사용하여 Case 2의 영구자석을 외곽으로 1.5 mm 이동하여 설계하였다.
4. 결과 및 고찰
본 연구에서는 모델 N의 전동기와 3개의 개선 설계 유형을 AUTOCAD로 2D 모델링을 진행한 후 ANSYS MAXWELL 프로그램을 활용하여 전자기 해석을 진행하였으며 토크와 토크 리플을 비교하여 성능이 가장 우수한 설계 유형을 선정하였고, 스테이터와 로터 사이의 공극 크기에 따른 토크와 토크 리플을 비교하여 최적의 공극을 선정하였다.
4.1 설계 유형별 정자기 상태 해석
본 연구에서는 모델 N의 전동기를 포함하여 총 4가지 설계 유형의 정자기 상태 해석을 진행하였다. Fig. 7은 정자기 상태 해석 결과를 그림으로 나타낸 것이다. 모델 N의 정자기 상태에서의 자기장 최대 세기는 3.8580 [T]로 나타났으며, Cases 1은 4.2193 [T], 2는 3.1372 [T], 3은 4.6731 [T]로 나타나 최댓값은 3에서 나타났다. 정자기 상태에서 자기장의 최대 세기는 Case 3이 모델 N의 전동기보다 21.1% 크게 나타났다.
4.2 설계 유형별 과도 상태 해석
본 연구에서는 모델 N의 전동기를 포함하여 총 4가지 설계 유형의 과도 상태 해석을 진행하였고, 해석을 진행할 때 로터의 회전수는 모델 N의 공식 제원에 명시된 최대 출력과 최대 토크에 근거하여 3,626 RPM으로 모두 동일하게 설정하였다. Fig. 8은 설계 유형별 과도 상태에서의 토크 성능 곡선을 그래프로 나타낸 것이다.
토크 리플은 로터가 회전함에 따라 출력 토크의 주기적인 증가 또는 감소를 의미하며 전동기 설계에 있어 중요한 인자 중 하나이고, 토크 리플률은 최대 토크, 최소 토크, 평균 토크에 의해 결정되며 토크 리플률이 커질수록 소음 및 진동 문제를 야기하여 전동기 수명 저감의 원인이 된다.
(1) |
식(1)의 TR은 토크 리플률, Tmax는 전동기의 최대 토크, Tmin은 최소 토크, Tavg는 평균 토크를 말한다.
K사 모델 N의 공식 제원에 제시된 전동기의 최대 토크는 395 [N·m]이다. 본 연구에서 해석한 모델 N의 최대 토크는 385 [N·m]로 나타나 모델 N의 공식 제원과 오차율이 2.5% 이내가 되어 해석의 신뢰성을 검증할 수 있었다.
모델 N, Cases 1부터 3의 최대 토크는 각각 385, 484, 421, 474 [N·m]이고, 최소 토크는 362, 386, 402, 406 [N·m], 평균 토크는 375, 431, 409, 441 [N·m]로 나타났으며 토크 리플률은 6.1, 22.7, 4.6, 15.4%로 나타났다.
(2) |
식(2)에서의 T+는 모델 N에 대한 평균 토크 증가율을 정량적으로 나타내며 Tavg(C)는 Cases별 평균 토크, TN은 모델 N의 전동기 평균 토크를 나타낸다.
토크 성능 해석을 통해 평균 토크와 토크 리플을 비교해보았을 때 기존 모델 N에 비해 Cases 1과 3의 평균 토크가 각각 14.9, 17.6%로 크게 증가하였지만 토크 리플률은 각각 16.6, 9.3%P 증가하여 진동 및 소음 문제를 야기할 수 있어 성능이 우수한 설계 유형이라고 할 수 없다. Case 2의 평균 토크는 모델 N에 비해 9.1% 증가하였고, 토크 리플률은 1.5%P 감소하여 성능이 가장 우수한 설계 유형이라고 판단된다. 모델 N을 포함하여 총 4가지 설계 유형의 데이터와 식(1)과 식(2)를 적용한 결과값을 Table 3에 정리하였다.
4.3 공극별 토크 해석
IPMSM(매립형 영구자석 동기 전동기)은 로터의 형상에 따라 토크가 발생되는 특성이 다르기 때문에 스테이터와 로터 사이의 공극 크기에 따른 4가지 설계 유형의 토크 성능을 분석하였으며, 본 연구에서 토크 성능이 가장 우수하다고 판단되는 Case 2(공극 0.7 mm)의 설계 형태에서 공극을 0.5, 0.9, 1.1 mm로 설계한 3가지 설계 유형의 과도 상태 해석을 추가적으로 진행하여 Case 2(공극 0.7 mm)와 비교하였다.
Figs. 9는 모델 N 전동기 조립체의 공극을 보여주는 실제 사진이며, 10은 정자기 상태에서의 공극별 자기장을 나타내는 그림이다. 0.5, 0.7, 0.9, 1.1 mm에서 최대 자기장은 각각 2.9318, 3.1372, 3.2802, 3.4708 [T]로 나타났다. Fig. 11은 과도 상태에서의 공극별 토크 성능 해석을 나타낸 것이다. 공극 0.5, 0.7, 0.9, 1.1 mm에서 최대 토크는 각각 456, 421, 378, 313 [N·m]이고, 최소 토크는 410, 402, 357, 298 [N·m], 평균 토크는 428, 409, 368, 305 [N·m], 토크 리플률은 10.7, 4.6, 5.7, 4.9%로 나타났다.
(3) |
식(3)에서의 T+는 Case 2에 대한 평균 토크 증가율을 정량적으로 나타내며, Tavg(A)는 공극별 평균 토크, T0.7은 공극이 0.7 mm인 Case 2의 평균 토크를 나타낸다.
토크 성능 해석을 통해 평균 토크와 토크 리플률을 비교해보았을 때 로터와 스테이터 사이의 공극이 0.9, 1.1 mm인 설계 유형은 Case 2(공극 0.7 mm)보다 평균 토크가 각각 10.0, 25.4% 낮게 나타났고, 공극이 0.5 mm인 설계 유형은 Case 2(공극 0.7 mm)보다 평균 토크는 4.6% 높게 나타났지만 토크 리플률도 6.1%P 높게 나타났다. 공극을 다르게 설계한 4가지 설계 유형의 해석 결과를 Table 4에 정리하였다.
Case 2의 공극별 토크 및 전압과 토크 리플률을 한눈에 비교하기 위해 Fig. 12에 그래프로 나타내었다. 공극이 작을수록 누설 리액턴스를 감소시켜 출력 토크 및 전압이 높게 나타났고, 토크 리플률은 공극 0.7 mm에서 가장 낮게 나타났다. 토크 리플률이 높으면 기계적인 불완전성에 의해 발생되는 저주파로 인해 진동 및 소음이 커져 전동기의 내구성 감소에 영향을 미치며 운전자의 조향 핸들에 진동이 전달되어 조종 안정성이 저하될 수 있기 때문에9 공극 0.5 mm에 비해 토크가 낮지만 토크 리플률도 낮아 안정된 토크 수치를 가지는 공극 0.7 mm를 최적의 공극으로 선정하였다. 완성차 업체 K사 및 1차 협력 업체 G사의 전동기 또한 공극 0.7 mm로 본 연구의 해석 결과와 일치하여 해석 결과에 신뢰성이 있다고 판단된다.
5. 결론
본 연구에서는 현재 출시되어있는 완성차 업체 K사 모델 N과 C사 모델 B의 토크 성능을 비교한 후 토크 성능이 우수한 모델 N의 전동기 형상을 기준으로 영구자석과 코일 사이의 거리, 영구자석의 개수와 배열을 변경하여 3가지 설계 유형을 설계하였다. 소형화와 경량화를 목표로 토크와 토크 리플률을 모델 N의 전동기와 비교하여 성능이 가장 우수한 전동기 형상인 Case 2를 선정하였다. 추가적으로 성능이 가장 우수하다고 판단되는 Case 2의 스테이터와 로터 사이 공극을 0.5, 0.9, 1.1 mm로 설정한 3가지 설계 유형을 모델링한 후 기존 0.7 mm를 포함하여 총 4가지 설계 유형에 대해 과도 상태 해석을 진행하여 토크와 토크 리플률을 비교하고 토크 성능이 가장 우수한 공극을 확인하였다.
(1) 모델 N과 로터 내부 설계 Geometry를 변경한 3가지 설계 유형을 과도 상태 해석을 통해 수치적으로 비교하였다. 모델 N에 비해 Cases 1부터 3의 평균 토크는 각각 14.9, 9.1, 17.6% 증가하였고, 토크 리플률은 각각 6.0, -1.5, 9.3%P 증가하였다. Cases 1과 3은 토크가 증가했지만 토크 리플률도 함께 증가해 진동 및 소음 문제를 야기할 수 있으므로 토크는 증가하고, 토크 리플률은 감소한 Case 2를 가장 성능이 우수한 Case로 선정하였다.
(2) 성능이 가장 우수한 Case 2(공극 0.7 mm)를 기준으로 로터와 스테이터 사이의 공극의 크기를 0.5, 0.9, 1.1 mm를 추가로 설계하여 과도 상태 해석을 진행한 후 수치적으로 비교하였을 때 평균 토크는 각각 4.6, -10, -25.4% 증가하였고, 토크 리플률은 각각 6.1, 1.1, 0.3%P 증가하여 Case 2의 공극인 0.7 mm를 가장 성능이 우수한 공극으로 선정하였다.
(3) 최종적으로 로터 내부 영구자석의 개수를 늘리고, 2 Layer에서 3 Layer로 바꾸어 설계하는 것(Case 2)이 성능이 가장 우수하고, 최적의 공극은 0.7 mm로 판단된다. 추후에는 본 연구 범위를 확장하여 영구자석이 이루고 있는 각도, 코일이 삽입되는 스테이터 내부 슬롯의 형상, 코일의 종류를 달리하는 등 다양한 접근을 통해 분석하여 높은 토크 밀도와 낮은 토크 리플을 가지는 고성능 전동기를 구현하는 방안을 연구할 것이다.
REFERENCES
- Lee, S. J., “Torque Characteristics of IPMSM according to the Rotor Shape,” Proc. of the Summer Conference on the Korean Society of Electrical Engineers, pp. 728-729, 2015.
-
Lee, K. D., “Shape Design Method for High Torque in the Flux-Weakening Range of the IPMSM,” The Transactions of Korean Institute of Electrical Engineers, Vol. 64, No. 4, pp. 629-633, 2015.
[https://doi.org/10.5370/KIEE.2015.64.4.629]
- Kim, H. W., “A Study on the Inductance Variation according to the Rotor Shape in IPMSM,” Proc. of the Spring Conference on the Korean Society of Electrical Engineers, pp. 274-276, 2009.
- Park, K. W., “The Displacement Property by the Radial Force considering Rotor Shape of IPMSM (3),” Proc. of the Autumn Conference on the Korean Society of Electrical Engineers, pp. 220-223, 2012.
- Hong, S. Y., “The Effects of Rotor Shape of IPMSM on Cogging Torque Characteristics,” Proc. of the Summer Conference on the Korean Society of Electrical Engineers, pp. 764-765, 2016.
- Park, H. I., “Rotor Design of High-speed Interior Permanent Magnet Synchronous Motor with Ferrite Permanent Magnet,” Proc. of the Autumn Conference on the Korean Society of Electrical Engineers, pp. 42-44, 2015.
- Han, J. H., “IPMSM Characteristic Comparison Regarding the Rotor Pole Number,” Proc. of the Summer Conference on the Korean Society of Electrical Engineers, pp. 635-636, 2013.
-
Park, H. J., “Design of DC Small Motor Fixings and Rotors for Torque Improvement,” Journal of the Korean Society for Precision Engineering, Vol. 36, No. 11, pp.1039-1042, 2019.
[https://doi.org/10.7736/KSPE.2019.36.11.1039]
- Oh, S. A., “Level Set Based Shape Optimization of Surface-Mounted Permanent Magnet Motor for Minimizing Torque Ripple,” M.S. Thesis, Hanyang University, 2013.
B.S. candidate in the School of Mechanical and Automotive Engineering, Catholic University of Daegu. His research interest is electric vehicle and future alternative energy.
E-mail: tjdghks7413@cu.ac.kr
B.S. candidate in the School of Mechanical and Automotive Engineering, Catholic University of Daegu. His research interest is electric vehicle and future alternative energy.
E-mail: qkrtlahr12@cu.ac.kr
B.S. candidate in the School of Mechanical and Automotive Engineering, Catholic University of Daegu. His research interest is electric vehicle and future alternative energy.
E-mail: alsrl3901@cu.ac.kr
M.S. candidate in the Graduate School of Mechanical Engineering, Sungkyunkwan University. His research interest is turbo machinery, future alternative energy, and aerospace engineering.
E-mail: sjh012@skku.edu
Professor in the School of Mechanical and Automotive Engineering, Catholic University of Daegu. His research interest is heat transfer, fluid engineering, and electric vehicle.
E-mail: dlee@cu.ac.kr