
금속 나노 입자-고분자 복합체로 코팅된 3D 미세 격자의 압축 거동 분석
Copyright © The Korean Society for Precision Engineering
This i an Open-Access article distributed under the terms of the Creative Commons Attribution Non-Commercial License (http://creativecommons.org/licenses/by-nc/3.0) which permits unrestricted non-commercial use, distribution, and reproduction in any medium, provided the original work is properly cited.
Abstract
Microlattice is well known as an efficient structure having a low density which maintains mechanical properties, so microlattice is being applied to the structural design of lightweight material in many industrial fields. In this study, we proposed a core-shell microlattice structure by the conformal coating of a metal nanoparticle-polymer composite in order to enhance the mechanical properties of polymeric microlattice printed by light-based 3D printing method. Polymeric architected microlattice was fabricated using digital light printing, which enabled the printing of complex structures with good surface smoothness. Then, the polymeric microlattice was conformally coated with aluminum nanoparticle-polymer composites. To investigate the effect of the metal nanoparticle-polymer composite coating on the mechanical properties of the microlattice, we studied the compressive behavior of cubic and octet-truss microlattices. As a result, we confirmed that both compressive strength and toughness of the two types of microlattices were effectively increased by coating with aluminum nanoparticle-polymer composites.
Keywords:
Microlattice, Composites coating, Compression strength, Toughness키워드:
미세 격자 구조, 복합체 코팅, 압축 강도, 인성1. 서론
미세 격자 구조는 단위 부피당 낮은 밀도를 가지고 있는 초경량 구조로 우수한 기계적 특성으로 많은 산업 분야에서 경량화를 위한 구조 설계에 적용되고 있다. 그 중 항공 우주 산업, 자동차 산업 등 다양한 분야에서 내부 구조의 샌드위치 패널에 경량화 및 안전성을 가지기 위해 다양한 격자 구조 제작 방법을 연구하고 있다.1-5 기존의 기계 가공 방법으로 복잡한 형상의 미세 격자 구조를 제작하는 것은 생산 시간 및 가공에 제약이 많아 최근에는 3D 프린팅을 이용한 제조 방법에 관한 연구가 활발히 진행되고 있다.5,6
3D 프린팅 방법은 크게 압출 적층 방식(Extrusion Process), 광경화성 적층 방식(Photo Curing Process), 레이저 소결 적층 방식(Laser Sintering Process) 등이 있다. 압출 적층 방식 중 하나인 FDM 방식은 여러 가지 재료를 사용할 수 있다는 장점이 있지만, Overhang 구조 제작을 위해서는 지지체가 필요하며 마이크로미터 단위의 크기를 제작할 수 없다는 한계로 인해 다양한 형상의 미세 격자 구조를 제작하는 데에는 부적합하다.7-9 광경화성 적층 방식에는 SLA, DLP 방식이 있으며, 이들은 레이저 빔이나 자외선을 이용해 광경화성 폴리머를 경화시켜 적층하는 방식을 사용한다. 두 방식 모두 마이크로미터 단위의 물체를 높은 정밀도로 출력하여 미세 격자 구조를 제작할 수 있고, DLP 방식은 공정 속도가 빠르다는 장점이 있다. 하지만 사용 가능한 재료가 광경화성 폴리머에만 국한된다는 한계로 인해 광범위하게 적용하기에는 기계적 특성이 부족하다는 단점이 있다.9,10 레이저 소결 적층 방식 중 SLM 방식은 레이저 빔에 의한 열에너지를 이용해 금속 분말을 녹여 제작하는 방식으로 우수한 품질의 금속 미세 격자 구조를 제작할 수 있다는 장점이 있지만, 공정 시간이 느리고, 돌출된 형상이나 수평 구조물은 제작하지 못한다는 단점이 있어 제작할 수 있는 격자 구조의 종류가 한정적이다.11 반면에 EBM 방식은 다양한 격자 구조를 제작할 수 있다는 장점이 있다. 하지만 표면 조도가 좋지 않고, 알루미늄, 아연, 마그네슘 기반 재료에는 적합하지 않다.
본 연구에서는 DLP 방식을 이용하여 복잡한 형상의 폴리머 미세 격자 구조를 제작하고, 금속 나노입자-폴리머 복합체 코팅을 수행하여 기계적 특성을 향상하고자 한다. 본 연구를 위해서 격자 구조의 크기, 각도 등에 영향을 받지 않고, 표면 조도가 좋으며 공정 속도가 빠른 광중합 방식의 DLP 3D 프린팅을 이용해 미세 격자 구조를 제작하고 알루미늄 나노입자-폴리머 복합체 코팅제를 이용해 격자 구조에 코팅한다. 이러한 방법은 금속 나노입자의 종류에 상관없이 미세 격자 구조의 표면에 균일하게 코팅할 수 있기 때문에, 다양한 복합 물질의 미세 격자 구조를 형성할 수 있게 한다. 위와 같은 방법으로 표면은 금속 나노입자-폴리머 복합체이며 내부는 폴리머인 복합소재 미세 격자 구조를 제작하여 폴리머 소재의 미세 격자 구조와 압축 특성을 비교하고 분석하였다.
2. 시편 제작
2.1 설계
격자 구조는 굽힘이 지배적인 입방(Cubic) 구조와 신축이 지배적인 옥텟-트러스(Octet-Truss) 구조로, 서로 다른 특성을 가진 2가지 구조로 선정하였다.12 Fig. 1(a)와 같이 한 변의 길이(a)가 2.5이고, 두께(t)가 0.3 mm인 정육면체 단위 셀로 구성된 20 × 20 × 10 mm 크기인 격자 구조를 설계하였다. Fig. 1(b)와 같이 두 가지 격자 구조의 크기와 두께는 동일하다.
2.2 DLP 3D 프린팅
설계된 2가지 격자 구조는 DLP 3D Printer (IM2, Carima, South Korea)와 광경화성 레진(OCLEAR Resin, XYZprinting, Taiwan)을 사용하여 제작되었다. 제작한 결과는 Fig. 2와 같다.
2.3 코팅
금속 나노입자-폴리머 복합체 코팅제의 금속 종류는 가벼우면서도 단단한 알루미늄으로 선정하였다. 코팅제에는 핵산(2.4 g, n-Hexane, 96.0%, South Korea), 무수 에탄올(4.8 g, Ethyl Alcohol Anhydrous, 99.9%, South Korea)의 혼합 용매에 광경화성 레진(0.8 g, OCLEAR Resin, XYZprinting, Taiwan)을 용해시킨 후, 알루미늄 나노 파우더(0.8 g, Al 99.9%, 40 nm, Metal Basis, US Research Nanomaterials)를 첨가하였으며, 이를 교반기를 이용해 2시간 이상 섞어서 알루미늄 나노입자-폴리머 복합체 코팅제를 제작하였다.13
코팅 효율을 높이기 위해 제작한 격자 구조의 표면을 친수성으로 개질하기 위해서 미세 격자 구조를 회전시켜가며 윗면, 아랫면을 각각 300 s씩 UV-Ozone 처리를 하였다.14
앞서 제작한 복합체 코팅제를 사용하여 Dip Coating 방법으로 알루미늄 나노입자-폴리머 복합체 코팅을 수행하였다. 제작한 코팅제에 미세 격자 구조가 충분히 담길 정도로 침지시킨 후 약 30 s 이후 격자 구조를 천천히 꺼낸다.
마지막으로 코팅된 격자 구조를 건조하기 위해 후경화를 진행한다. UV 후경화 장비(CL300pro, Carima, South Korea)를 이용해 앞뒤로 5분간 후경화하여 알루미늄 나노입자-폴리머 복합체가 코팅된 격자 구조를 Fig. 4와 같이 제작하였다.
3. 결과
3.1 코팅된 양의 측정
격자 구조에 코팅이 얼마나 되었는지를 확인하기 위해 알루미늄 나노입자-폴리머 복합체 코팅 전후의 질량을 측정하여 비교하였다. 코팅에 따라 증가한 질량을 측정한 결과, Fig. 5와 같이 입방 구조는 11, 옥텟-트러스 구조는 44 mg으로 옥텟-트러스 구조가 입방 구조보다 4배 더 커지는 것을 확인하였다. 옥텟-트러스 구조의 표면적(8,343 mm2)은 입방 구조의 표면적(2,199 mm2) 보다 크고, 이는 코팅이 가능한 면적이 약 3.8배 넓어 코팅되는 양이 더 많음을 의미한다. 따라서 알루미늄 나노입자-폴리머 복합체를 코팅했을 때 옥텟-트러스 구조의 질량이 더 많이 증가하게 된다.
3.2 압축 시험
알루미늄 나노입자-폴리머 복합체 코팅으로 인한 금속 미세 격자의 기계적 특성 변화를 알아보기 위해 압축 시험을 진행하였다. Fig. 6과 같이 시험기의 용량이 50 ton인 만능 시험기(RB-305, R&B, South Korea)를 사용해 2 mm/min의 시험 속도로 압축 시험을 진행하여 압축 강도와 인성을 측정하였다.
정확한 데이터를 위해 각 5번의 반복 실험을 시행하여 최댓값과 최솟값을 제외한 3개 데이터의 평균을 구해 결괏값을 얻었다.
Fig. 7은 알루미늄 나노입자-폴리머 복합체를 코팅하기 전과 후의 입방 구조에 대한 응력-변형률 그래프이다. 입방 구조는 4개의 Cycle을 가지는데, 이 Cycle이 뜻하는 것을 분석하고자 압축 시험 중인 격자 구조를 동영상 촬영하여 동영상과 그래프를 비교하였다.
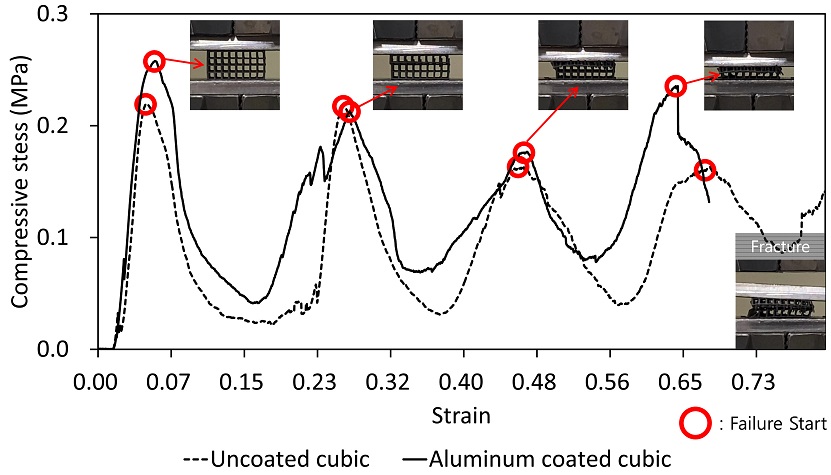
Compression test result graph of cubic structure before and after aluminum nanoparticles-polymer composites coating
비교 결과, 입방 구조는 층마다 세로축의 구조물에서 파단이 발생하는 것을 알 수 있다. 따라서 입방 구조의 세로축이 휘어지면서 파단이 시작되는 지점과 굴곡의 마루 부분이 일치하고, 한 층의 세로축이 완전히 부서져 다음 층으로 넘어가는 부분인 파단이 끝나는 지점은 굴곡의 골 부분과 일치한다. 이는 굴곡의 마루는 파단이 시작되는, 골은 파단이 끝나는 지점이며, 입방 구조에서는 한 번의 파단이 발생할 때 하나의 Cycle이 발생함을 의미한다. 또한 입방 구조는 세로축의 파단이 발생하면서 압축되기 때문에 압축 시험이 끝난 후에도 원래의 형상으로 회복되지 않는다.
알루미늄 나노입자-폴리머 복합체를 코팅하기 전과 후에 대해 입방 구조의 압축 시험 결과를 비교한 결과 코팅 전후의 입방 구조 모두 4개의 굴곡을 가진다는 점과 압축 시험 시 세로축의 파단으로 인해 굴곡이 생긴다는 점이 동일하다는 것을 알 수 있다. 이를 통해 알루미늄 나노입자-폴리머 복합체를 코팅한 입방 구조가 압축될 때의 파단 특성은 코팅하기 전과 같다고 판단할 수 있다. 코팅한 후 달라진 점은 첫 번째 파단이 발생하기까지의 응력이 코팅하기 전보다 11.1% 증가하여 압축 강도와 인성이 증가한다.
Fig. 8은 알루미늄 나노입자-폴리머 복합체를 코팅하기 전과 후의 옥텟-트러스 구조에 대한 응력-변형률 그래프이다. 옥텟-트러스 구조는 입방 구조와 달리 첫 번째 작은 굴곡 이후부터는 거의 굴곡이 없는 그래프를 가진다.
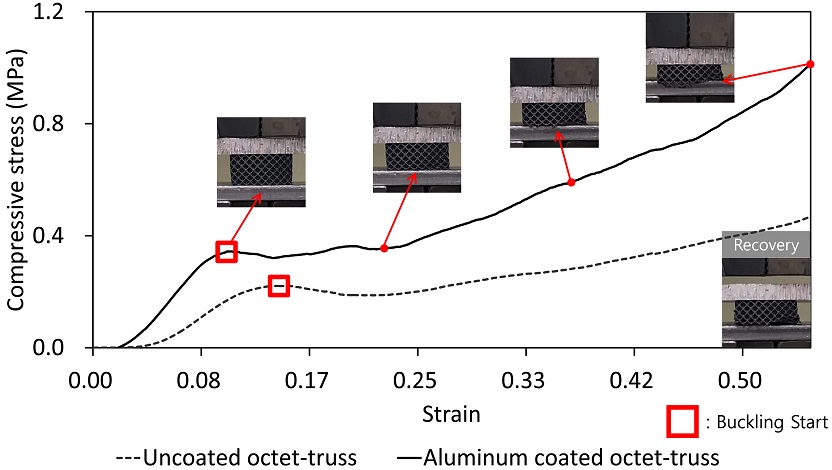
Compression test result graph of octet-truss structure before and after aluminum nanoparticles-polymer composites coating
압축 시험 중인 격자 구조를 관찰하면 입방 구조와는 달리 옥텟-트러스 구조는 시편의 하단 부분부터 층마다 좌굴이 일어나면서 압축이 되었다. 파단은 처음 좌굴이 발생하는 시편의 하단 부분에서 발생하였고, 그 이후에는 좌굴만 발생한다. 이를 통해 첫 번째 굴곡은 파단이 발생한 것이고, 그 이후부터 좌굴이 발생하여 그래프가 굴곡이 거의 없는 곡선의 형태를 나타내는 것이다. 압축 시험이 끝난 후의 옥텟-트러스 구조를 보았을 때 처음 파단이 발생한 지점 외에 좌굴이 발생한 지점은 다시 회복되었지만, 파단이 발생한 지점은 입방 구조와 같이 회복되지 않는다. 이 특성 때문에 옥텟-트러스 구조는 압축 시험이 끝난 후에 원래의 형상으로 좌굴이 일어난 부분에 한해서 회복이 가능하다.
알루미늄 나노입자-폴리머 복합체를 코팅하기 전과 후의 옥텟-트러스 구조는 첫 번째 굴곡 이후엔 굴곡이 거의 없다는 점과 상단 부분부터 좌굴이 발생한다는 점, 압축 시험 이후 회복이 가능하다는 점이 동일하다. 또한 입방 구조와 동일하게 코팅으로 인해 파단이 발생하기까지의 압축 응력이 57.4% 증가하여 압축 강도와 인성이 증가함을 알 수 있다.
압축 시험 결과를 이용해 압축 강도의 크기를 정량적으로 비교하기 위해 각 격자 구조의 압축 시험 결과 중 첫 번째 파단 시작 지점의 압축 응력을 압축 강도로 선정하였다. Fig. 9에서 보여주는 바와 같이 2가지 격자 구조 모두 알루미늄 나노입자-폴리머 복합체 코팅을 하였을 때, 압축 강도가 증가하는 것을 알 수 있다. 코팅하기 전의 압축 강도는 입방과 옥텟-트러스가 비슷하지만, 코팅 이후 압축 강도는 확연히 차이가 나는데, 이것은 옥텟-트러스에 비해 4배 많은 나노입자-폴리머 복합체 코팅이 이루어졌기 때문이라고 판단된다.
압축 시험 결과에서 그래프의 아래 면적이 인성을 의미하며 각 격자 구조의 인성 크기를 정량적으로 비교하기 위해 입방 구조의 첫 번째 파단이 끝나는 지점까지의 변형률 값(0.17)을 기준으로 응력-변형률 그래프의 하단 부분 면적을 계산하여 인성으로 정의하고 그 값을 비교하였다. Fig. 10에서 이를 보여주고 있으며 알루미늄 나노입자-폴리머 복합체를 코팅함에 따라 입방 구조, 옥텟-트러스 구조 모두 인성이 증가하는 것을 확인하였고, 코팅에 따른 인성의 증가량은 입방 구조의 4 kJ/m3에 비해 옥텟-트러스 구조가 18 kJ/m3으로 400% 이상 크게 증가한다. 이렇게 옥텟-트러스에서 인성이 크게 증가하는 것은 압축 시험에서 파단이 아닌 좌굴이 발생할 때 나노입자-폴리머 복합체 코팅에 의한 효과가 더욱 커지기 때문이라고 판단한다.
4. 결론
본 연구에서는 DLP 3D 프린팅을 통해 제작된 미세 격자에 금속 나노입자-폴리머 복합체 코팅을 적용한 복합소재의 격자 구조를 제작하는 공정을 제안하고, 압축 시험을 통해 그 효과를 확인하였다. 이를 요약하면 본 연구의 결과는 다음과 같다.
(1) 알루미늄 나노 파우더를 이용한 금속 나노입자-폴리머 복합체 코팅제 제작이 가능하고, 이를 이용하여 광경화성 폴리머 소재 격자 구조에 코팅이 가능함을 확인하였다.
(2) 압축 시험 결과를 확인하였을 때 입방, 옥텟-트러스 두 가지 구조 모두 코팅 전과 코팅 후의 좌굴 및 파단되는 현상은 같게 나타났고, 압축강도와 인성의 크기가 달라지는 것을 확인하였다. 즉, 단위 격자 구조의 형상에 따라 외력에 의해 파단이 될지 변형이 될지 정해지게 된다.
(3) 압축 강도를 비교한 결과, 입방, 옥텟-트러스 두 가지 구조 모두 알루미늄 나노입자-폴리머 복합체를 코팅하였을 때 압축 강도가 증가하였다. 두 구조 모두 코팅하기 전의 압축 강도의 크기는 유사하지만, 알루미늄 나노입자-폴리머 복합체 코팅을 통해 증가한 압축 강도의 크기를 비교해 보면 옥텟-트러스가 입방 구조보다 860% 이상 더 많이 증가하여 알루미늄 나노입자-폴리머 복합체 코팅 후의 압축 강도는 옥텟-트러스가 훨씬 크게 측정되었다.
(4) 인성을 비교한 결과 두 가지 구조 모두 알루미늄 나노입자-폴리머 복합체를 코팅하였을 때 인성이 증가하였다. 코팅하기 전후 모두 옥텟-트러스가 컸고, 코팅에 따라 증가한 인성의 크기 또한 옥텟-트러스가 입방 구조에 비해 4배 이상 더 컸다.
본 연구에서 제시한 복합소재의 미세 격자 구조 제조 방식을 통해 기계적 물성을 증가시킬 수 있음을 확인하였고 금속 나노 입자-폴리머 복합체 코팅제의 종류에 따라 충분히 산업 전반에 활용될 수 있을 것으로 기대한다.
NOMENCLATURE
3D : | 3 Dimension |
FDM : | Fused Deposition Modeling |
SLA : | Stereo Lithography Apparatus |
DLP : | Digital Light Process |
SLM : | Selected Laser Melting |
EBM : | Electron Beam Melting |
Acknowledgments
이 논문은 2021-2022년도 창원대학교 자율연구과제 연구비 지원으로 수행된 연구 결과임.
REFERENCES
-
Ushijima, K., Cantwell, W., and Chen, D., “Prediction of the Mechanical Properties of Micro-Lattice Structures Subjected to Multi-Axial Loading,” International Journal of Mechanical Sciences, Vol. 68, pp. 47-55, 2013.
[https://doi.org/10.1016/j.ijmecsci.2012.12.017]
-
Rashed, M., Ashraf, M., Mines, R., and Hazell, P. J., “Metallic Microlattice Materials: A Current State of the Art on Manufacturing, Mechanical Properties and Applications,” Materials & Design, Vol. 95, pp. 518-533, 2016.
[https://doi.org/10.1016/j.matdes.2016.01.146]
-
Banhart, J., “Manufacture, Characterisation and Application of Cellular Metals and Metal Foams,” Progress in Materials Science, Vol. 46, No. 6, pp. 559-632, 2001.
[https://doi.org/10.1016/S0079-6425(00)00002-5]
-
Mines, R., “On the Characterisation of Foam and Micro-Lattice Materials Used in Sandwich Construction,” Strain, Vol. 44, No. 1, pp. 71-83, 2008.
[https://doi.org/10.1111/j.1475-1305.2008.00399.x]
-
Wadley, H. N., “Cellular Metals Manufacturing,” Advanced Engineering Materials, Vol. 4, No. 10, pp. 726-733, 2002.
[https://doi.org/10.1002/1527-2648(20021014)4:10<726::AID-ADEM726>3.0.CO;2-Y]
-
Wadley, H. N., Fleck, N. A., and Evans, A. G., “Fabrication and Structural Performance of Periodic Cellular Metal Sandwich Structures,” Composites Science and Technology, Vol. 63, No. 16, pp. 2331-2343, 2003.
[https://doi.org/10.1016/S0266-3538(03)00266-5]
-
Choi, J. W. and Kim, H. C., “3D Printing Technologies-A Review,” Journal of the Korean Society of Manufacturing Process Engineers, Vol. 14, No. 3, pp. 1-8, 2015.
[https://doi.org/10.14775/ksmpe.2015.14.3.001]
- Paek, S., “Introduction of 3D Printing Technology & Applications,” Korean Industrial Chemistry News, Vol. 18, No. 1, pp. 2-10, 2015.
-
Stansbury, J. W. and Idacavage, M. J., “3D Printing with Polymers: Challenges among Expanding Options and Opportunities,” Dental Materials, Vol. 32, No. 1, pp. 54-64, 2016.
[https://doi.org/10.1016/j.dental.2015.09.018]
-
Quan, H., Zhang, T., Xu, H., Luo, S., Nie, J., et al., “Photo-Curing 3D Printing Technique and Its Challenges,” Bioactive Materials, Vol. 5, No. 1, pp. 110-115, 2020.
[https://doi.org/10.1016/j.bioactmat.2019.12.003]
-
Rehme, O. and Emmelmann, C., “Rapid Manufacturing of Lattice Structures with Selective Laser Melting,” Proc. of the Laser-Based Micropackaging on International Society for Optics and Photonics, Vol. 6107, 2006.
[https://doi.org/10.1117/12.645848]
-
Ashby, M. F., “The Properties of Foams and Lattices,” Philosophical Transactions of the Royal Society A: Mathematical, Physical and Engineering Sciences, Vol. 364, No. 1838, pp. 15-30, 2006.
[https://doi.org/10.1098/rsta.2005.1678]
-
Wang, Y., Huang, Z., Gurney, R. S., and Liu, D., “Superhydrophobic and Photocatalytic PDMS/TiO2 Coatings with Environmental Stability and Multifunctionality,” Colloids and Surfaces A: Physicochemical and Engineering Aspects, Vol. 561, pp. 101-108, 2019.
[https://doi.org/10.1016/j.colsurfa.2018.10.054]
-
Wang, H., Yu, B., Jiang, S., Jiang, L., and Qian, L., “UV/Ozone-Assisted Tribochemistry-Induced Nanofabrication on Si (100) Surfaces,” RSC Advances, Vol. 7, No. 63, pp. 39651-39656, 2017.
[https://doi.org/10.1039/C7RA07198A]
M.Sc. candidate in the Department of Smart Manufacturing Engineering, Changwon National University. Her research interests are 3D printing and nano-micro technology.
E-mail: qkrtjflakr@changwon.ac.kr
Ph.D. candidate in the Department of Mechanical Engineering, Changwon National University. His research interests are machine and nano-micro technology.
E-mail: haho0109@naver.com
He is an Assistant Professor in the Department of Smart Manufacturing and Department of Mechanical Engineering, Changwon National University. His research focuses on the development of a variety of advanced manufacturing with functional materials for energy, environmental, and biological applications.
E-mail: kimseok@changwon.ac.kr
He is a Professor in the Department of Mechanical Engineering, Changwon National University. His research interests are imprint process, super-hydrophobic and precision manufacturing system.
E-mail: ytcho@changwon.ac.kr