
식품 적층 제조 공정의 성형 시간 단축을 위한 이중 노즐 적용 연구
Copyright © The Korean Society for Precision Engineering
This is an Open-Access article distributed under the terms of the Creative Commons Attribution Non-Commercial License (http://creativecommons.org/licenses/by-nc/3.0) which permits unrestricted non-commercial use, distribution, and reproduction in any medium, provided the original work is properly cited.
Abstract
Additive manufacturing requires a relatively long time to fabricate complex three-dimensional (3D) structures or parts with more than one material. For additive manufacturing processes, production time and precision vary depending on the fabrication conditions. In this study, we developed a food additive manufacturing process of the material extrusion method type using a dual nozzle. In addition, we observed the change in the cross-sectional shape of the discharged food line according to each fabrication condition. By using a dual nozzle, the structure was fabricated under conditions of relatively high precision for the outer wall and relatively low precision for the infill, thereby shortening the production time. Through this process, it can be expected that the production time will be shortened in the food field, while the appearance will be of good quality.
Keywords:
Additive manufacturing, Food material, Dual nozzle, Material extrusion, Fabrication conditions키워드:
적층 제조, 식품 재료, 이중 노즐, 재료 압출, 성형 조건1. 서론
시제품 제작에 주로 적용되던 적층 제조 기술은 점차 이를 직접 제품 제작에 적용하는 것으로 범위가 확대되고 있다.1,2 이에 따라 다양한 형태의 제품을 제작할 수 있는 적층 제조 기술의 연구가 폭넓게 이루어지고 있다. 식품 분야에서도 다양한 적층 제조 공정 연구가 이루어지고 있다.3 식품 적층 제조 공정은 주로 노즐을 통해 재료를 밀어내는 재료 압출(Material Extrusion) 방식과 액체 원료를 분사하는 방식인 재료 분사(Material Jetting) 방식들이 적용되고 있다.3,4 특히 재료 압출 방식은 시스템이 상대적으로 단순하고, 사용 가능한 식재료의 범위가 넓기 때문에 식품을 재료로 하는 적층 제조 공정의 개발에 널리 사용되고 있다. 재료 압출 방식이 적용된 대표적인 상용화된 식품 적층 제조 장치는 WiiBoox, FoodBot S2, Createbot 등이 있으며, 모두 하나의 압출 헤드를 이용하여 초콜릿 등의 재료를 성형한다.5
한편, 재료 압출 방식에서는 성형 조건에 따라 제품을 제작하는 시간이 달라진다. Yang6 등은 재료 압출 방식의 적층 제조 공정을 이용하여 레몬 젤(Lemon Juice Gel)을 재료로 성형 조건 및 성형 조건에 따른 3차원 구조물의 제작 시간에 대해 연구하였다.6 또한 서로 다른 재료를 2개의 노즐로 각각 압출하여 성형된 제품의 물성치값을 조절하는 연구를 Lee7 등은 수행하였다.7 Park8 등은 두 가지의 초콜릿 재료를 케닉스 정적 믹서(Kenics Static Mixer)를 통해 혼합하여 압출하는 연구를 하였다.8
한편 성형되는 형상에 따라 압출되는 재료의 유랑을 다르게 할 경우 동일한 외관 형상 정밀도를 가지면서 제작속도를 향상시킬 수 있을 것으로 기대된다. 특히 다수의 노즐을 이용하고, 각각의 노즐에 서로 다른 성형 조건을 적용하면 제품의 외관 해상도를 유지하되 제작시간을 단축시킬 수 있을 것이다. 이에, 본 연구에서는 재료 압출 공정을 이용한 이중 노즐 기반의 식품 적층 제조 공정을 개발하였다. 그리고 식품 재료로서 초콜릿을 사용하여 각 성형 조건에 따라 압출되어 만들어지는 식재료 선의 단면 형상 변화를 관찰하고, 이를 기반으로 3차원 구조물 적층에 적합한 단면을 선정하였다. 그리고 노즐의 이송속도, 압출 유량 및 노즐과 기저판 사이의 거리에 따라 압출되는 재료의 선의 형상을 예측할 수 있는 수학적 모델을 제시하였다.
2. 식재료 성형을 위한 이중 노즐 적층 제조 시스템
Fig. 1은 본 연구에서 개발된 이중 노즐 적층 제조 시스템의 사진이다. x, y축은 스텝모터와 타이밍 벨트, z축은 스텝모터와 리드 스크류를 사용하여 구동되도록 하여 성형 정밀도와 시스템의 강성을 확보하였다. 또한 각 축에 리미트 스위치를 장착하여 성형 범위를 벗어나게 되면 자동으로 구동을 정지하도록 하였다. 재료 카트리지가 장착된 압출 헤드는 x축에 장착되어 있다. x, y 및 z축을 구동하기 위한 3개의 이송 모터와 재료를 각각 압출하기 위한 2개의 압출 모터는 독립적으로 제어되도록 하였다.
본 연구에서는 Fig. 2와 같이 모터와 헤드를 분리하여 관성에 의한 영향을 최소화하였다. 모터의 회전에 의한 동력은 플렉시블 샤프트를 통해 헤드에 부착된 리드 스크류에 전달되어 직선 운동으로 변환되어 카트리지를 가압한다. 그리고 압출 지연 현상을 개선하기 위해 재료는 압출 모터에 연결된 플렉시블 샤프트와 리드 스크류를 통해 재료가 압출된다.9 한편, 압출력을 향상시키기 위하여 3 : 5의 감속 기어가 모터와 플랙시블 샤프트 사이에 설치되어 있다.
본 연구에서는 초콜릿(초코데코펜, ㈜브레드가든)을 재료로 사용하였다. 초콜릿은 융점이 상대적으로 낮고, 구조물 성형 시 플라스틱과 같은 재료에 비해 점성이 매우 낮아 노즐에서 압출된 후 액체처럼 퍼지는 재료이다. 따라서 추후 유사한 성질의 재료에도 본 연구의 결과가 적용 가능할 것으로 판단된다.
한편, 초콜릿의 융점은 비교적 낮지만 온도 및 습도에 따라 재료의 유변학적인 특성이 변하기 때문에 온도를 일정하게 유지하는 것이 중요하다. 따라서 Fig. 3과 같이 카트리지를 둘러싸도록 가열부를 설치하여 일정한 온도의 재료가 압출되도록 하였다.10
3. 재료 압출 적층 제조 성형 특성
3.1 단면 형상 연구
재료 압출 방식의 적층 제조 공정에서 3차원 형상을 성형하기 위해서는 노즐로부터 압출되어 나온 재료의 단면 형상이 중요하다. 이에 본 연구에서는 재료인 초콜릿의 온도를 40oC로 일정하게 유지하면서 다양한 성형 조건(노즐의 이송속도, 노즐의 내경, 노즐 끝단과 이전 층 사이의 거리 등)에 따라 압출되어진 선의 단면 형상을 관찰하였다.
다양한 성형 조건에서 압출 성형된 재료의 단면들을 관찰한 결과 Table 1과 같이 크게 세 가지 형상으로 구분되었다. Table 1에서 Case A는 압출되어 나온 재료의 단면 형상이 반원 형상과 유사한 경우로서 실제 재료가 압출되어 만들어지는 형상의 단면 높이가 노즐과 기저판(Substrate) 사이의 거리인 SOD (Stand-Off Distance)보다 낮은 경우에 주로 나타난다. 이러한 반원 형태의 단면을 지속적으로 적층하게 되면 재료가 흘러내리게 되어 적층이 원활하게 되지 않는다. Case B는 압출되어 나온 재료의 단면 형상이 직사각형과 유사한 경우로서 재료의 단면 높이가 노즐과 기저판 사이의 거리와 대부분 일치한다. Case C는 재료의 단면 높이가 노즐과 기저판 사이의 거리보다 큰 경우로 재료가 과도하게 압출된 경우에 주로 나타난다. 이 경우는 적층할 때 단면의 높이 제어가 어렵게 된다. 따라서 직사각형 형태의 단면을 가지는 Case B가 3 차원 구조물을 적층하기에 가장 적합하다고 판단된다.
Case B의 단면의 폭이 W이고, 높이가 h인 직사각형이고, 압출되는 재료가 비압축성 유체라고 가정할 때 일정한 속도 VN으로 이송되는 노즐에서 재료가 일정한 유량 Q로 압출된다면 성형되는 재료의 폭 W는 식(1)과 같이 구할 수 있다. 따라서 식(1)을 이용하면 직사각형 단면이 만들어지는 성형 조건에서 성형되는 재료의 폭을 예측할 수 있다.
(1) |
식(1)로부터 계산된 값과 실제로 압출되어 성형된 재료의 단면 형상과 폭을 비교하기 위한 실험을 수행하였다. 노즐에서 압출되는 재료의 유량은 14.31 mm3/s, 그리고 노즐과 기저판 사이의 거리는 0.64 mm로 고정하고, 노즐의 이송속도를 300부터 1,000 mm/min까지 100 mm/min씩 증가시키면서 노즐에서 압출되어 성형된 재료의 단면 형상과 폭을 각각 관찰하였다.
Fig. 4는 노즐의 이송속도에 따라 압출된 재료의 폭을 식(1)을 이용한 계산 결과와 함께 비교한 그래프이다. Fig. 4에서 알 수 있듯이 노즐의 이송속도가 증가할수록 성형된 재료의 폭은 줄어들게 된다. 또한, 약 500 mm/min 이상의 노즐 이송속도에서는 실험 결과와 계산 결과가 어느 정도 일치한다. 하지만 노즐의 이송속도가 낮은 경우에는 실험 결과가 계산 결과와 일치하지 않는 경향을 보인다. 이는 재료의 점성에 비해 토출된 질량이 크기 때문에 높이 쌓이지 않고, 재료가 흘러내려 Case C와 같은 단면 형상이 만들어 진 것에 기인한 것으로 판단된다.
Fig. 5는 압출된 단면 형상이 직사각형을 갖는 조건인 유량 4.77 mm3/s, SOD 0.5 mm 그리고 노즐의 이송속도 750 mm/min인 성형 조건으로 성형된 원통 형상이다. 전체 층 수는 20이다. 압출된 재료의 단면 형상이 직사각형인 성형 조건에서 의도한 대로 제품이 성형된 것을 알 수 있다.
3.2 노즐 지름에 따른 성형 특성
재료가 압출되는 노즐의 지름에 따라서 압출 성형되는 재료의 폭이 달라질 것으로 예상되며, 각 경우에 따라 성형되는 제품의 해상도도 달라질 것이다. 이에 Table 1과 같이 서로 다른 지름을 갖는 노즐을 이용하여 재료를 압출 성형한 후 각각의 폭을 비교하였다.
Fig. 6은 Table 2의 성형 조건에 따라 성형된 재료의 폭을 측정한 값과 식(1)로부터 계산된 결과를 비교한 그래프이다. Fig. 6에서 선들은 식(1)로부터 계산된 값을 나타낸 것이고, 서로 다른 모양의 점들은 측정된 값을 나타낸다. Fig. 6에서 알 수 있듯이 측정된 값과 계산된 값이 유사한 경향을 가지는 것을 알 수 있다.
노즐 내경 0.97 mm의 경우, 압출 유량이 높으면서 노즐의 이송속도가 작으면, 측정값이 계산값보다 작은 것을 확인할 수 있었고, 이는 압출이 과도하여 Case C 형태의 단면을 가짐을 의미한다. 노즐 내경 0.47 mm의 경우는 측정값이 계산값과 일치하는 부분이 매우 적었다. 대부분 측정값이 계산값보다 높았고, 이는 대다수 반원 형태(Case A)의 단면을 가지는 것을 의미한다. 노즐 내경 0.78 mm의 경우는 계산값과 실험 결과가 대부분 일치하는 것을 확인할 수 있었다. 이는 직사각형 형태(Case B)의 단면을 가지는 것을 알 수 있다.
이를 바탕으로 계산값과 측정값이 유사한 즉, 적층이 용이한 직사각형 형태의 단면인 성형 조건들을 선정할 수 있다. Figs. 7은 6의 실험 결과에서 직사각형 단면을 가지는 결과만을 따로 정리한 것이다.
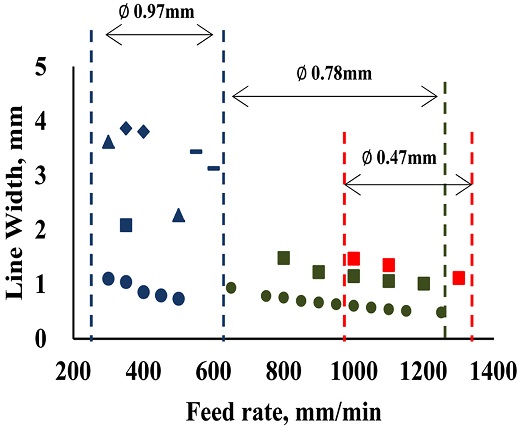
Experimental results of selected data from calculated data (○: 4.77 mm3/s, □: 9.54 mm3/s, △: 14.31 , ◇: 19.08 , ▬ : 23.85 )
이 결과를 이용하면 서로 다른 내경을 갖는 노즐로 다양한 폭을 가지는 재료를 압출하여 성형하는 것이 가능하다. 선정된 성형 조건들 중 가장 큰 값을 가지는 선폭은 3.865이고, 가장 작은 값을 가지는 선폭은 0.485 mm이다.
서로 다른 압출된 폭을 가진 재료의 성형 조건으로 성형된 형상의 해상도를 각각 비교하기 위해 가로 83, 세로 23.5 그리고 높이 5 mm의 동일한 3차원 구조물을 각각 성형하였다. Figs. 8(a)는 압출된 재료의 폭 3.865, 그리고 8(b)는 압출된 재료의 폭 0.788 mm로 구조물을 성형한 사진이다. Figs. 8(a)의 경우 압출되어 나오는 재료의 폭이 넓으므로 성형하는 과정에서 겹치는 부분이 생겨 해상도가 매우 떨어지는 반면 8(b)의 경우 비교적 뚜렷한 형상이 성형된 것을 확인할 수 있었다.
적층 제조 공정으로 제품을 성형할 때 외관 형상에 영향을 주지 않는 내부를 보다 빠르게 채워 성형하기 위해서는 제품의 외곽 형상과 내부를 성형할 때 각각 서로 다른 폭을 갖도록 재료를 압출하는 것이 유리할 것이다. 따라서 이를 확인하기 위해 구조물의 내부를 다른 성형 조건으로 성형하여 비교하였다. 출력 시간을 비교하기 위하여 각 변이 30 mm이고, 5 mm의 높이를 가지는 동일한 크기 및 형상의 구조물을 서로 다른 조건으로 성형하였다. Fig. 9(a)는 구조물의 내부 채움을 선정된 값 중 최대 선폭(3.865 mm)을 가지는 성형 조건으로, 구조물의 외벽은 최소 선폭(0.485 mm)을 가지는 성형 조건으로 이중 노즐을 이용하여 성형한 것이다. 성형 시간은 5분 25초이다. Fig. 9(b)는 구조물 전체를 최소 선폭인 0.485 mm로 성형한 것이다. 이 경우는 성형 시간이 17분 55초로 Fig. 9(a)에 비해 3.3배 정도의 성형 시간이 필요하다.
Fig. 9에서 알 수 있듯이 제품의 외관 형상에 영향을 주는 외부는 작은 폭을 갖는 성형 조건으로, 그리고 외관에 영향을 주지 않는 내부는 큰 폭을 갖는 성형 조건으로 성형하면 동일한 외관 형상을 가지면서도 성형속도를 크게 높일 수 있다.
한편, 본 연구에서는 초콜릿을 재료로 하였다. 초콜릿은 제조사에 따른 성분과 성형 공정에 따라서 재료의 특성과 맛 등이 달라질 가능성이 있다. 따라서 추후 연구를 통해 재료의 가열, 용융시간, 냉각속도 등과 같은 공정변수에 따른 재료의 물성 및 식감 등에 연구가 필요하다.
4. 결론
본 연구에서는 초콜릿을 재료로 한 듀얼 노즐 적층 제조 장치를 제작하고, 초콜릿을 재료로 3차원 구조물 성형에 있어서 필요한 성형 조건에 대한 연구를 수행하였다.
압출되어진 재료의 단면 형상을 관찰하였고, 성형된 선의 형상 중 사각형 단면을 가지는 것이 3차원 구조물을 성형하기에 적합함을 알 수 있었다. 이를 바탕으로 각 조건에 따라 압출된 재료의 폭을 예측할 수 있는 수학적 모델을 제시하였다. 또한, 실험을 통해 측정된 압출된 재료의 폭과 수학적 모델로부터 도출된 폭을 비교하여 적층하기에 용이한 조건들을 선정할 수 있다. 이중 노즐을 이용하여 외벽은 해상도가 상대적으로 높은 성형 조건으로, 내부는 해상도가 상대적으로 낮은 성형 조건으로 구조물을 성형하였을 때 성형 시간이 크게 단축된 것을 알 수 있었다. 본 연구 결과는 상대적으로 외관 형상이 중요한 식품 분야에서 성형 시간을 단축시킬 수 있을 것으로 기대된다.
NOMENCLATURE
DN : | Nozzle Diameter [mm] |
VN : | Nozzle Velocity [mm/min] |
Q : | Flow Rate [mm3/s] |
h : | Layer Height [mm] |
T : | Food Material Temperature [oC] |
W : | Line Width [mm] |
Acknowledgments
이 논문은 2021년 해양수산부 재원으로 한국해양과학기술진흥원의 지원을 받아 수행된 연구임(해역별 특성을 고려한 전통수산가공식품 개발 및 상품화).
REFERENCES
-
Attaran, M., “The Rise of 3-D Printing: The Advantages of Additive Manufacturing over Traditional Manufacturing,” Business Horizons, Vol. 60, No. 5, pp. 677-688, 2017.
[https://doi.org/10.1016/j.bushor.2017.05.011]
-
Oh, S. T., Lee, I. H., Kim, H. C., and Cho, H. Y., “Multi-Material Additive Manufacturing Process for 3-Dimensional Circuit Device Fabrication,” Journal of the Korean Society for Precision Engineering, Vol. 35, No. 3, pp. 349-354, 2018.
[https://doi.org/10.7736/KSPE.2018.35.3.349]
-
Liu, Z., Zhang, M., Bhandari, B., and Wang, Y., “3D Printing: Printing Precision and Application in Food Sector,” Trends in Food Science & Technology, Vol. 69, pp. 83-94, 2017.
[https://doi.org/10.1016/j.tifs.2017.08.018]
- Park, J. H. and Lee, I. H., “A Study on Extrusion Characteristics for Improving Fabrication Precision of Food 3D Printer,” Proc. of the Fall Conference on the Korean Society for Precision Engineering, p. 265 2019.
- 3DSOURCED, “The 10 Best Food 3D Printers 2021,” https://www.3dsourced.com/rankings/food-3d-printer/, (Accessed 20 OCTOBER 2021)
-
Yang, F., Zhang, M., Bhandari, B., and Liu, Y., “Investigation on Lemon Juice Gel as Food Material for 3D Printing and Optimization of Printing Parameters,” LWT-Food Science and Technology, Vol. 87, pp. 67-76, 2018.
[https://doi.org/10.1016/j.lwt.2017.08.054]
-
Lee, S., Shin, C., Jung, M., and Park, M., “Property Analysis of Multi-Material Specimen based on ME Type 3D Printer,” Journal of the Korean Society for Precision Engineering, Vol. 37, No. 3, pp. 231-238, 2020.
[https://doi.org/10.7736/JKSPE.019.122]
-
Park, M., Jeong, H., Moon, J., and Lim, J., “Development of a Material Mixing Extrusion Type Chocolate 3D Printer,” Journal of the Korean Society for Precision Engineering, Vol. 38, No. 2, pp. 145-151, 2021.
[https://doi.org/10.7736/JKSPE.020.089]
- Park, J., Kim, S., Lee, I., and Cho, H., “Improvement of Extrusion Performance for Food 3D Printing Using High-Viscosity Material,” Proc. of the Spring Conference on the Korean Society of Manufacturing Process Engineers, p. 175, 2018.
- Park, J. H., Kim, S. H., Chaima, F., and Lee, I. H., “Development of Cartridge Heating System for Food 3D Printer,” Proc. of the Annual Conference on the Korean Society of Mechanical Engineers, pp. 2763-2764, 2018.
B.Sc. candidate in the Department of Mechanical Engineering, Chungbuk National University. His research interest is manufacturing.
E-mail: baiks12@chungbuk.ac.kr
M.Sc. candidate in the Department of Mechanical Engineering, Chungbuk National University. His research interest is additive manufacturing.
E-mail: juho6269@naver.com
Ph.D. course in the Department of Seafood Science and Technology, Gyeongsang National University. His research interest is food-processing machine.
E-mail: sikang@gnu.ac.kr
Professor in the School of Mechanical Engineering, Chungbuk National University, Korea. He received his Ph.D in Mechanical Engineering from POSTECH. His research interests include additive manufacturing and its applications.
E-mail: anxanx@chungbuk.ac.kr