
압전 페인트 센서를 활용한 구조물 모니터링 최신 기술 동향
Copyright © The Korean Society for Precision Engineering
This is an Open-Access article distributed under the terms of the Creative Commons Attribution Non-Commercial License (http://creativecommons.org/licenses/by-nc/3.0) which permits unrestricted non-commercial use, distribution, and reproduction in any medium, provided the original work is properly cited.
Abstract
Recently, large-scale accidents caused by minor damage from fatigue failure and impact on structures have been frequently reported. Therefore, a real-time damage monitoring system of structures is considered to be one of the most important technologies to ensure safety in various types of research. The piezoelectric sensor, which has an advantage of converting deformation of a structure into an electrical signal without using an additional power source, has been reported as one of the most suitable methods for real-time monitoring systems. This review aims to describe the structural monitoring system utilizing piezoelectric paint sensors. First, we present the concept of a piezoelectric paint sensor with the advantages of flexibility and piezoelectric performance. Then, factors affecting the performance of the piezoelectric paint sensor are introduced. Finally, an overview of piezoelectric paint sensors for structural monitoring, such as vibration detection and impact monitoring, are provided. The state-of-the-art of the application of the piezoelectric sensor is also introduced, providing feasibility in industrial fields.
Keywords:
Piezoelectric composite, Sensor, Sensitivity, Vibration detection, Impact detection, Structure monitoring키워드:
압전 복합재, 센서, 민감도, 진동감지, 충격감지, 구조물 모니터링1. 서론
기술의 발전에 따른 다양한 재료와 형태의 구조물들이 설계되고 제작되며, 이를 이용하는 사용자 역시 증가하고 있다. 하지만 반복하중에 의한 교각의 피로파괴, 외부이물손상(Foreign Object Debris, FOD)에 의한 항공기 파손, 자갈도상의 손상으로 발생하는 비산물에 의한 철도 파손 등의 다양한 구조물에서의 반복하중에 의한 피로파괴와 순간적인 충격에 의해 일어나는 작은 손상에 의한 대형사고가 빈번히 발생하면서 구조물의 안전성이 강조되고 있다. 구조물에서의 대형사고는 이를 이용하는 사용자에게 큰 피해를 입힐 수 있으므로 구조물에 가해지는 피해를 예측하고 감지하여 예상되는 피해 정도와 위치를 파악하고 효과적인 유지 및 보수 작업을 진행하려는 연구가 계속되고 있다.1-8 하지만 대부분의 구조물의 경우 크기가 매우 크기 때문에 인력이 투자되어 일일이 파손 여부를 확인하는 것은 비효율적일 뿐 아니라, 미처 발견하지 못한 파손이 존재할 수 있다. 이에 따라 구조물에 가해지는 손상을 실시간으로 모니터링하여 구조물의 안전성을 확보할 수 있는 센서를 개발하는 연구가 진행되고 있다.
이 중 압전 효과를 이용한 센서는 비대칭 결정 구조를 갖는 특정 물질에서 인장, 압축 등의 기계적 에너지를 가하면 결정구조가 변형되며 전기적 신호가 발생하므로 외부의 진동 및 충격 등에 의한 신호를 전기적으로 감지하여 구조물의 실시간 모니터링이 가능하기 때문에 많은 분야에서 이를 활용하는 방안을 연구 중이다.9 기존에 구조물의 모니터링에 주로 사용되고 있는 것은 티탄산 지르콘산 연(PZT), 티탄산 바륨(BaTiO3) 등의 압전세라믹 소재이다. 압전 세라믹 소재는 실온에서 안정적이고 높은 압전 성능을 가지고 있기 때문에 모니터링 센서뿐만 아니라폐에너지원에서 에너지를 추출할 수 있는 에너지 하베스팅에서도 주로 활용하고 있다.10 하지만, 압전 세라믹 소재는 취성이 강하기 때문에 외부 충격이나 진동이 심하면 내구성의 문제가 발생할 수 있고, 낮은 가공성으로 인해 곡면에서의 활용이 힘들며, 넓은 면적에서 활용하기에는 무게가 다소 무겁기 때문에 복잡한 형상의 대면적 모니터링은 쉽지 않다. 반면, 압전 고분자 수지인 불화비닐리덴수지(Polyvinylidene Fluoride, PVDF), 삼불화에틸렌-불화비닐리덴수지(Poly (Vinylidene Fluoride-Trifluoroethylene), P(VDF-TrFE)) 등은 유연하며 가벼운 압전 소재이기 때문에 부착되는 표면의 형상에 구애받지 않고 활용이 가능하지만, 온도에 따라 압전 효과의 변화가 크기 때문에 활용가능한 온도 구간이 좁다는 단점이 있다.11,12 따라서 압전 세라믹 소재와 압전 고분자 수지의 장단점을 보강, 보완하기 위해 다양한 연구가 진행되고 있다.
압전 고분자 수지 중에서 압전 페인트는 압전 세라믹 분말과 합성 수지를 혼합하여 만든 복합 소재로, 압전 세라믹 소재의 안정적인 압전 성능과 합성 수지의 유연성 및 넓은 활용성의 장점을 모두 활용할 수 있다. 압전 페인트에서의 압전 성능은 PZT,13-19,21-28 BaTiO3 20,29뿐 아니라 산화아연(ZnO)30 등의 압전세라믹 필러에서 오기 때문에 폴리우레탄,19 에폭시,13,14,17,18,21-28 상용 아크릴 페인트,15,16,19 PVDF29,30 등 다양한 합성 수지를 사용하여 센서의 성능을 조절하고, 다양한 요구사항을 충족할 수 있다.
또한, 페인트의 특성상 필름의 형태뿐 아니라 분사 가능한 스프레이의 형태로도 제작이 가능하기 때문에 대면적 표면에 쉽게 도포할 수 있으며, 별도의 추가적인 장치 없이 상용 페인트를 대신하여 활용이 가능하기 때문에 구조물의 실시간 모니터링에 압전 페인트를 스마트 센서로 활용하려는 기술이 연구되고 있다.
따라서, 압전 페인트를 이용한 구조물의 모니터링을 위한 센서는 산업계 전반으로 유용하게 활용할 수 있으므로 압전 페인트 센서에 대한 소개와 최신 기술의 동향을 본 논문을 통해 소개하고자 한다. 먼저, 압전 페인트 센서와 센서의 성능을 결정하는 요인들에 대해 소개하고, 구조물의 모니터링에서 중요한 요소인 진동 감지와 충돌 감지를 위한 압전 페인트 센서로 구분하여 현재까지의 연구 동향을 소개하고자 한다.
2. 압전 페인트 센서
압전 페인트 센서는 압전 페인트를 이용하여 구조물의 변형을 감지할 수 있는 센서이다. 압전 페인트 센서는 압전 세라믹에 합성 수지가 섞였기 때문에 변형에 따른 신호가 압전 세라믹 센서에 비해 다소 감소하지만 신호를 검출하는데 지장이 없어 많은 논문에서 센서로서 역할이 가능하다고 보고되었다. 또한 Fig. 1에서 볼 수 있듯이 압전 페인트 센서는 페인트 소재의 장점인 대면적 적용성과 경량성이라는 큰 강점을 활용하기 때문에 대형 구조물의 실시간 모니터링에 활용이 가능하다.
압전 페인트 센서를 제작하기 위해서는 압전 페인트에 전극을 부착하고, 높은 전계를 가해 분극 상태로 만든 후 모니터링하고자 하는 구조물에 도포하는 과정을 거친다. 이때 전극은 전도성 물질을 사용하면 되므로 알루미늄 등의 금속 구조물과 맞닿는 하부 전극의 경우 별도의 전극을 붙이지 않고, 구조물 그 자체를 전극으로 사용하기도 한다.
한편, 분극 상태로 만들기 위해 가해지는 전계는 매우 강하기 때문에 너무 높은 전계 또는 긴 시간 분극화를 진행하면 절연파괴(Dielectric Breakdown)가 발생하여 센서로서 활용이 불가능하게 된다. 또한, 사용되는 압전 필러 및 합성수지의 종류에 따라 분극 조건이 달라지므로 압전 페인트 센서의 성능을 결정하는 주요 요인으로 분극 전계의 전압, 적용 시간 및 주위 온도와 같은 분극 조건을 꼽는다.23,33
이 외에도 압전 페인트 센서의 성능을 결정하는 요인은 압전 페인트 내의 압전 필러의 함량, 페인트 센서 층의 두께,14 압전 필러의 종류,29 전극의 종류19 등이 있다. 압전 페인트 내의 압전 세라믹의 함량이 높아질수록 대체적으로 높은 분극 전계에서 분극화가 가능하기 때문에 분극 특성과 압전 성능이 개선되지만 압전 세라믹의 성질이 강해져 취성이 강해지고 무거워지게 된다.
압전 페인트 센서를 사용하면서 경우에 따라 보다 더 높은 신호를 검출해야 할 경우에는 압전 세라믹 계열의 압전 필러를 첨가하여 압전 성능을 개선한다. 이때 사용하는 압전 필러의 종류, 농도, 종횡비(Aspect Ratio) 및 방향성에 따라 압전 성능이 개선된다. 특히, 압전 필러의 종횡비를 늘리게 되면 내부의 필러 네트워크를 강한 이방성 구조로 만들어 압전 효과를 크게 향상시키는 효과가 보고된 바 있다.29
압전 페인트 센서를 제작할 때 사용하는 전극에 따라서도 출력성능이 변화할 수 있다. 앞서 언급한 것처럼 금속 구조물의 경우 하부 전극은 별도의 전극 없이 구조물에 부착함으로써 금속 구조물이 전극의 역할을 하게 된다. 하지만 상부 전극의 경우는 사용할 수 있는 전극이 한정적인데, 대표적으로 금, 은 페인트, 니켈 코팅 등이 있다. 금을 활용하는 것은 전기적, 기계적인 측면에서 우수하나, 가격적인 측면에서 상업적으로 활용하기 어렵다는 단점이 있다. 따라서 상업적으로 이용하는 것을 고려할 경우 은 페인트와 니켈 코팅을 선호하는데, 니켈 코팅은 에어로졸 형태로 존재해서 구조물의 모양과 관계없이 사용할 수 있으며, 금방 마르기 때문에 활용하기 쉽다는 장점이 있다. 은 페인트 역시 금방 마르지만 니켈 코팅에 비해 다소 느리고, 브러쉬로 처리하기 때문에 두께 면에서 정교하지 않고 부착이 잘 되지 않지만, 후처리가 가능하여 니켈 코팅에 비해 좁은 영역에서 고르게 코팅을 할 때 사용한다. 하지만 니켈 코팅과 은 페인트는 순도 100%에 가까운 증착 형식이 아닌 혼합물을 분사하거나 바르기 때문에 혼합되어 있는 다른 성분이 압전 페인트와 반응하여 표면의 형태를 변화시키고, 압전 성질을 변형시키기 때문에 신중한 선택이 필요하다.19
이처럼 압전 페인트 센서의 성능을 결정하는 다양한 요인들은 대체적으로 상호 연관되어 있다. 따라서, 각 요인 간의 상호 연관성을 파악하여 최적의 조건을 찾거나 압전 페인트 센서의 성능을 예측하는 것에 대한 연구가 진행중이다.22
3. 압전 페인트 센서의 구조물 모니터링
3.1 진동 감지를 위한 압전 페인트 센서
진동 감지를 위한 압전 페인트 센서는 대부분 빔 형태의 구조물에 센서를 부착하여 구조물에 진동을 가해 발생하는 전기 신호 및 전류와 구조물의 변형률을 비교하여 외부의 기계적 외력 발생을 감지한다. Fig. 2는 압전 페인트 센서의 이러한 특성을 보여주기 위해 X자 빔에 인장력과 수축력을 동시에 가했을 때의 변형률과 전기적 변위를 나타낸 것이다. 구조물의 양끝단에 다른 힘이 가해지면서 빔의 구조에 변형이 일어나지만, 결과적으로 압전 페인트 센서가 부착된 곳에서의 두 힘이 상쇄되어 변형은 발생하지 않아 신호가 발생하지 않는 것을 확인할 수 있다. 이를 통해 발생하는 신호 및 전류는 압전 페인트 센서가 부착된 곳의 인장과 수축을 모두 고려한 총 변형률의 합에 비례하는 것을 알 수 있다.15 또한, 압전 페인트 센서의 진동 감지 성능은 진동의 주파수와는 상호 독립적이기 때문에 넓은 주파수 영역과 다양한 형태의 진동을 감지할 수 있다.16,17
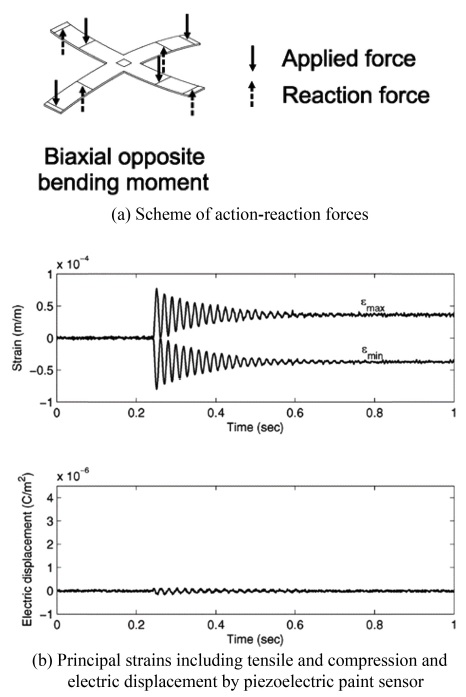
Comparison of principal strains and electric displacement by piezoelectric paint sensor15 (Accessed from Ref. 15 with permission)
특히, 압전 페인트 센서에 여러 개의 전극을 설치하면, 단순 진동 감지 뿐만 아니라 센서의 파손 여부도 확인할 수 있다. Fig. 3(a)와 같이 압전 페인트 센서가 피로파괴에 의해 완전히 손상된 경우를 가정하여 센서를 완전히 가르는 파열이 발생했을 때의 신호를 그렇지 않을 때와 비교하면 압전 효과에 의해 파괴의 유무에 관계없이 신호가 발생하지만, 피로파괴가 발생한 경우 두 전극 사이의 신호의 크기와 위상 모두 차이가 있는 것 을 확인할 수 있었다. 이때, 발생한 신호를 정상화하기 위해 Damage Index를 다음 식(1)과 같이 설정하였다.
(1) |
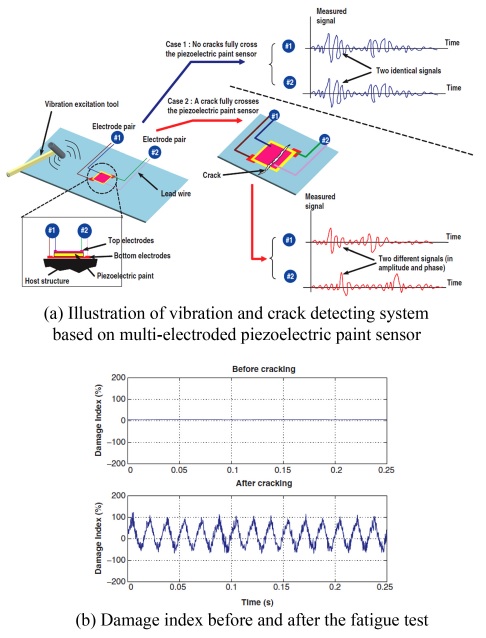
Vibration monitoring and damage sensing based on piezoelectric paint sensor17,18 (Accessed from Refs. 17 and 18 with permission)
x1과 x2는 두 전극에서 발생한 신호, RMS 값은 각 신호의 실효값을 의미한다. 파괴가 발생하지 않은 경우 두 전극에서 발생한 신호가 동일하기 때문에 Fig. 3(b)와 같이 Damage Index가 모든 시간에서 0을 나타내지만, 파괴가 발생한 경우 두 신호의 차이가 발생하기 때문에 시간에 따라 변하는 값을 찾을 수 있다.17,18
진동 감지를 위한 압전 페인트 센서의 민감도를 측정하기 위해선 직접 센서를 제작하여 힘을 가해 나오는 전류를 측정해야 한다는 번거로움이 있다. 이를 해결하고자 압전 페인트 센서의 민감도를 다양한 변수를 통해 수식화하여 센서를 제작하지 않고도 성능을 예측할 수 있는 연구 또한 진행 중이다. PZT와 상용 아크릴 페인트를 혼합하여 만든 압전 페인트 센서의 경우 다음 식(2)와 같은 식으로 민감도를 예측할 수 있다.
(2) |
S는 민감도, tp는 분극 시간이며, a, B, C는 각각 분극 전계, PZT wt%, 필름 두께와 관련된 상수이다. Fig. 4에서 볼 수 있듯이, 해당 실험식은 압전 페인트 센서의 민감도가 분극 시간 10초까지 급증하는 현상을 보여주고 있으며(Fig. 4(a)), 압전 페인트 내의 PZT wt% 및 분극 전계가 증가함에 따라 민감도가 증가함을 밝히고 있다(Fig. 4(b)). 하지만 상용 아크릴 페인트 대신 에폭시를 사용하게 되면 압전 페인트 센서 내 압전 세라믹의 비율이 높을수록 높은 분극 전계에서 절연 파괴가 발생하는데, 이는 위의 식(2)와는 전혀 다른 경향을 보이기 때문에 사용하는 물질에 따라서 압전 페인트 센서의 민감도와 관련한 식이 변화함을 알 수 있다.16
3.2 충격 감지를 위한 압전 페인트 센서
충격은 단기적으로 구조물의 파손뿐 아니라 장기적으로 피로 파괴를 일으킬 수 있기 때문에 충격을 감지하고, 해당 부분을 가능한 빨리 점검해야 안전성을 확보할 수 있다. 이러한 관점에서 충격을 감지하는 것은 구조물의 유지 및 보수에 큰 역할을 하기 때문에 충격과 충격이 가해진 위치를 감지할 수 있는 센서가 활용되어야 한다.
압전 페인트 센서는 가해지는 충격에너지에 비례하여 전기 신호 및 전류가 발생하여 센서가 완전 파단이 일어나지 않는 한 얼마나 강한 충격이 가해졌는지 파악할 수 있다. 또한, 충격 지점에서 멀어질수록 발생하는 응답이 감소하기 때문에 충격 위치를 비교적 쉽게 감지할 수 있다.20,21,26,27,32
한편, 충격 감지를 위한 압전 페인트 센서의 민감도는 진동감지와는 다르게 순간적인 힘이 가해지기 때문에 구조물의 명확한 변형률을 측정하는데 어려움이 있다. 따라서, 충격 감지를 위한 압전 페인트 민감도는 다음 식(3)과 같이 정의하여 정량화 하였다.31,32
(3) |
충격 감지를 위한 압전 페인트 센서는 완전 파단이 일어나지 않는 한 압전 성능이 다소 감소할 수는 있어도 제거되지 않기 때문에 장기간 활용이 가능하다. 이런 장점으로 인해 몇 년 단위로 중정비를 하는 항공우주 및 철도 분야에서 압전 페인트 센서의 활용 가능성이 높다. 특히, 철도 분야에서는 한국의 온도차가 심한 사계절을 지나면서 구조물의 열 피로에 의한 손상도 고려해야 한다. Fig. 5는 열 순환 주기를 다르게 하여 열 피로가 센서에 어떤 영향을 미치는지 분석하고 이를 1 : 1 스케일 모형에 적용한 예시이다. 각 시편의 열 순환 주기 정보는 Table 1에 정리되어 있다. 1 사이클은 -40 - 70oC의 온도 변화를 가지며, 100 사이클당 1년으로 가정하였다. 실험 결과 센서의 민감도는 다소 감소하지만 약 5년 후에도 여전히 충격 위치를 감지하는 것이 가능하다는 것을 보였다(Fig. 5(a)).
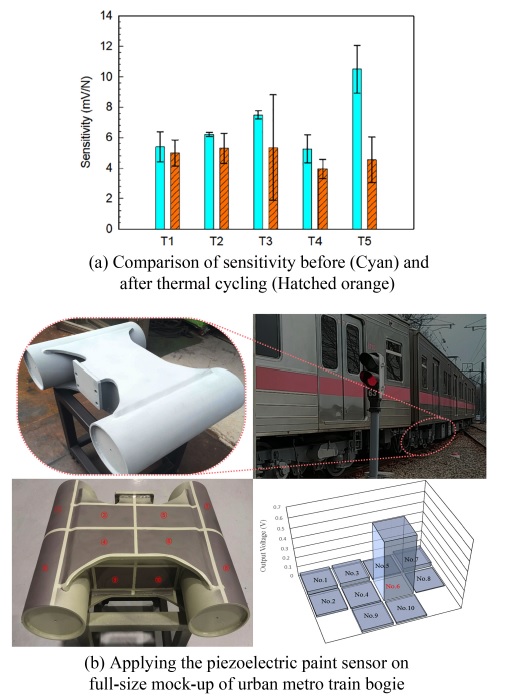
Sensitivity changes and experimental setup of piezoelectric paint at thermal fatigue condition21 (Accessed from Ref. 21 with permission)

Specimen groups according to the number of thermal cycles at Fig. 5(a)21 (Accessed from Ref. 21 with permission)
이는 열차의 중정비 주기인 3, 4년 이상에서도 센서가 정상적으로 작동하는 것을 의미하며 이를 활용하여 Fig. 5(b)에서와 같이 실제 전동차 하부 대차의 일부 구조물 중 곡면과 평면이 조합된 복잡한 구조의 1 : 1 스케일 모형에 압전 페인트 센서를 적용하여 충격 감지에 대한 실험을 진행하여 실제 열차의 적용 가능성을 검증하였다.21,31
압전 페인트 센서의 성능을 개선하기 위해 앞서 말한 압전 페인트의 압전 성능을 향상시키는 압전 필러 외에도 센서의 전기적 특성을 개선하기 위해 탄소나노튜브(Carbon Nanotube, CNT) 등 다양한 첨가제를 추가하는 연구도 진행 중이다. 특히 CNT는 전기전도도가 매우 우수하여 Fig. 6(a)에서 볼 수 있듯이 CNT를 소량 첨가한 경우와 그렇지 않은 경우와 비교했을 때 전기적 특성이 개선되어 전반적으로 민감도가 상승하게 된다.
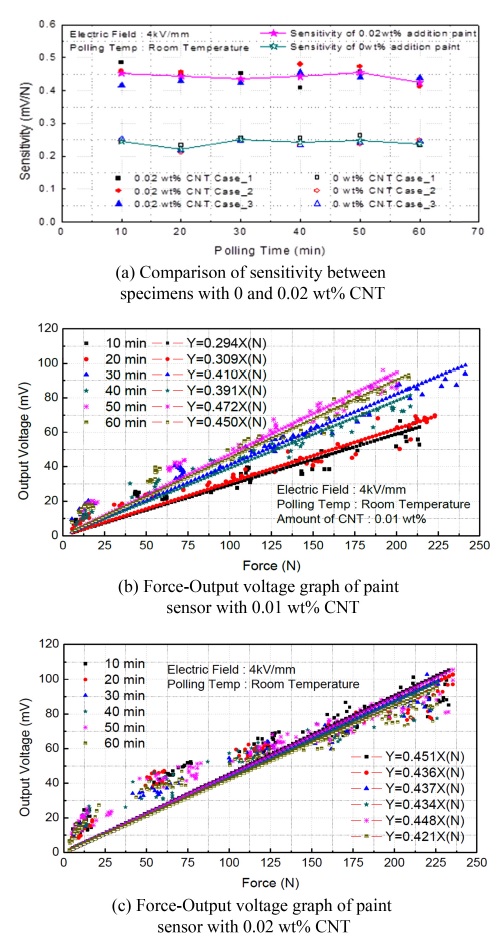
Sensitivity of sensors for impact detection at various CNT wt% conditions24 (Accessed from Ref. 24 on the basis of OA)
하지만 Figs. 6(b)와 6(c)에서 CNT wt%의 차이에 따라 민감도의 성능 경향성이 다르기 때문에 향후 CNT wt%와 분극 조건과의 상관관계를 통해 최적의 조건에 관한 연구가 요구된다.24
Fig. 7(a)는 비강도가 높아 구조물의 뼈대에 사용되는 유리섬유와 다양한 형태의 곡면에 도포가 가능한 압전 페인트 센서를 혼합하여 제작한 스마트 복합재의 모식도이다. 제작된 스마트 복합재는 유리섬유의 강성을 기반으로 비강도가 좋은 구조물을 만들 수 있으며 동시에 압전 페인트 센서에 의해 충격을 감지하는 센서로 작용한다.
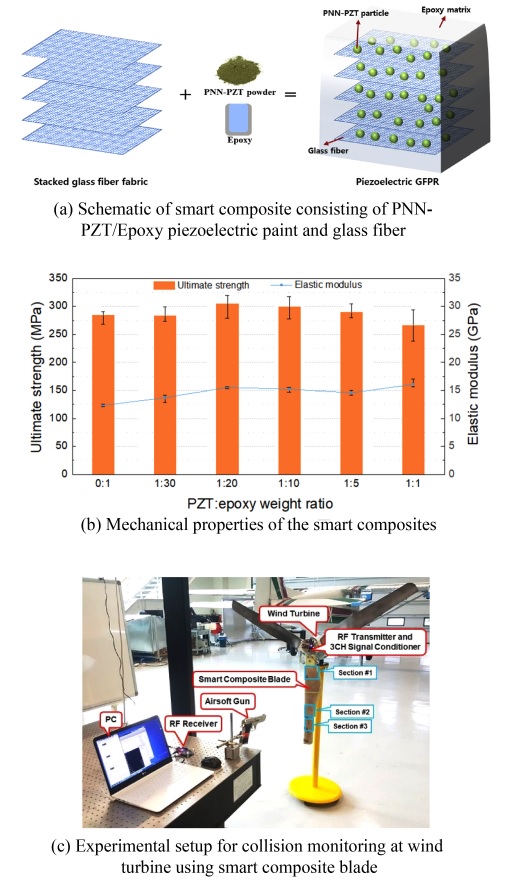
Properties and experimental setup of smart composite consisting of piezoelectric paint and glass fiber25,26 (Accessed from Refs. 25 and 26 with permission)
또한, 유리섬유가 센서에 가해지는 충격을 일부 흡수하여 센서의 내충격성이 강화되고, Figs. 7(b)에서 볼 수 있듯이 압전 페인트 센서의 유무가 스마트 복합재의 기계적 성질에 큰 영향을 미치지 않기 때문에 풍력발전기, 항공기 동체 등 비강도와 내충격성을 요하는 구조물에 활용될 수 있으며, 7(c)에서 보듯이 스마트 복합재를 이용하여 풍력발전기의 블레이드의 충격위치와 정도를 측정하여 실제 구조물에 활용하기 위한 실험이 진행 중이다.25,26
4. 결론
본 논문에서는 구조물의 실시간 모니터링에 활용할 수 있는 압전 페인트 센서에 대해서 소개하고, 진동 감지와 충격 감지에서 활용 가능한 압전 페인트 센서의 최근 연구 동향을 요약하였다. 압전 페인트 센서는 압전 성능을 갖는 압전 세라믹과 다양한 합성 수지로 이루어져 각기 다른 성능을 보이기 때문에, 사용하는 성분과 조건을 조절하여 원하는 성능의 센서를 제작할 수 있다. 뿐만 아니라 압전 페인트 센서는 상용 페인트를 대체할 수 있을 정도로 사용하기 쉽고, 추가 전원 없이 진동과 충격을 감지하여 항공우주, 철도, 건축물 등의 구조물의 안전성을 확보할 수 있는 방안이 될 수 있다. 압전 재료를 활용하는 센서의 특성상 진동 및 충격과 같은 동적 상태 변화에 대한 측정은 가능하지만, 전기적 신호를 이용하기 때문에 노이즈와 비슷한 크기의 미세 진동 및 충격 또는 정적 상태의 변화는 감지하는 것이 다소 어렵다. 하지만 향후 압전 필러의 효과적인 내부구조 생성 및 효율적인 분극 방법 등을 통해 센서의 민감도를 보완할 수 있다면 보다 넓은 적용성을 확보할 수 있을 것이다. 또한, 압전 페인트 센서는 여러 전극을 단순히 연결하여 신호를 비교하는 것으로 손상 여부를 확인할 수 있고 손상된 곳에 동일 센서를 덧바르는 것으로 보완이 가능하다는 등의 장점이 있으므로 대형 구조물의 실시간 모니터링을 가능하게 하는 중요한 인자로 앞으로도 활발히 연구될 것으로 보인다.
Acknowledgments
이 출판물은 2020년도 한국항공대학교 교비지원 연구비에 의하여 지원된 연구의 결과임.
REFERENCES
- Richard, H., Fulland, M., Sander, M., and Kullmer, G., “Examples of Fatigue Crack Growth in Real Structures,” CP2006, pp. 1-13, 2013.
- Lim, J., “Fatigue Life Estimation of an Aircraft Lug considering Model Uncertainty,” Proc. of the Conference of Korean Society for Aeronautical & Space Sciences, pp. 792-796, 2011.
- Kim, T., Kim, W., and Shin, H., “Fatigue Damage of Reinforced Concrete Bridge Columns Subjected to Cyclic Load,” Proc. of the Korea Concrete Institute Conference, pp. 99-104, 2002.
-
Jeon, H. K., Park, C. K., Seo, J. W., and Jeon, C. S., “A Study on Impact Testing of a Rolling-Stock Windscreen,” Journal of the Korean Society for Railway, Vol. 16, No. 5, pp. 365-371, 2013.
[https://doi.org/10.7782/JKSR.2013.16.5.365]
- Garcia, A. J., Lee, J. M., and Kim, D. S., “Convolutional Neural Network-Based Foreign Object Debris (FOD) Detection System,” Proc. of the Symposium of the Korean Institute of communications and Information Sciences, pp. 597-598, 2021.
-
Peters, J., Boyce, B., Thompson, A., Ritchie, R., and Roder, O., “Role of Foreign-Object Damage on Thresholds for High-Cycle Fatigue in Ti-6Al-4V,” Metallurgical and Materials Transactions A, Vol. 31, No. 6, pp. 1571-1583, 2000.
[https://doi.org/10.1007/s11661-000-0167-2]
-
Liu, Y. and Mahadevan, S., “Fatigue Limit Prediction of Notched Components Using Short Crack Growth Theory and an Asymptotic Interpolation Method,” Engineering Fracture Mechanics, Vol. 76, No. 15, pp. 2317-2331, 2009.
[https://doi.org/10.1016/j.engfracmech.2008.06.006]
-
Brighenti, R. and Carpinteri, A., “Surface Cracks in Fatigued Structural Components: A Review,” Fatigue & Fracture of Engineering Materials & Structures, Vol. 36, No. 12, pp. 1209-1222, 2013.
[https://doi.org/10.1111/ffe.12100]
-
Curie, J. and Curie, P., “Développement par compression de l'électricité polaire dans les cristaux hémièdres à faces inclinées,” Bulletin de minéralogie, Vol. 3, No. 4, pp. 90-93, 1880.
[https://doi.org/10.3406/bulmi.1880.1564]
-
Hwang, H.-Y., “Feasibility Study of the Damage Monitoring for Composite Materials by the Piezoelectric Method,” Transactions of the Korean Society of Mechanical Engineers A, Vol. 32, No. 11, pp. 918-923, 2008.
[https://doi.org/10.3795/KSME-A.2008.32.11.918]
-
Ueberschlag, P., “PVDF Piezoelectric Polymer,” Sensor review, Vol. 21, No. 2, pp. 118-126, 2001.
[https://doi.org/10.1108/02602280110388315]
-
Luo, H. and Hanagud, S., “PVDF Film Sensor and its Applications in Damage Detection,” Journal of Aerospace Engineering, Vol. 12, No. 1, pp. 23-30, 1999.
[https://doi.org/10.1061/(ASCE)0893-1321(1999)12:1(23)]
-
Egusa, S. and Iwasawa, N., “Piezoelectric Paints: Preparation and Application as Built-in Vibration Sensors of Structural Materials,” Journal of Materials Science, Vol. 28, No. 6, pp. 1667-1672, 1993.
[https://doi.org/10.1007/BF00363366]
-
Egusa, S. and Iwasawa, N., “Thickness Dependence of the Poling and Current-Voltage Characteristics of Paint Films Made Up of Lead Zirconate Titanate Ceramic Powder and Epoxy Resin,” Journal of Applied Physics, Vol. 78, No. 10, pp. 6060-6070, 1995.
[https://doi.org/10.1063/1.360546]
-
Payo, I. and Hale, J. M., “Dynamic Characterization of Piezoelectric Paint Sensors under Biaxial Strain,” Sensors and Actuators A: Physical, Vol. 163, No. 1, pp. 150-158, 2010.
[https://doi.org/10.1016/j.sna.2010.08.005]
-
Payo, I. and Hale, J., “Sensitivity Analysis of Piezoelectric Paint Sensors Made Up of PZT Ceramic Powder and Water-Based Acrylic Polymer,” Sensors and Actuators A: Physical, Vol. 168, No. 1, pp. 77-89, 2011.
[https://doi.org/10.1016/j.sna.2011.04.008]
-
Zhang, Y., “In Situ Fatigue Crack Detection Using Piezoelectric Paint Sensor,” Journal of Intelligent Material Systems and Structures, Vol. 17, No. 10, pp. 843-852, 2006.
[https://doi.org/10.1177/1045389X06059957]
- Zhang, Y., “Piezoelectric Paint Sensor for Nondestructive Structural Condition Monitoring,” Proc. of the SEM X International Congress and Exposition on Experimental and Applied Mechanics, pp. 7-10, 2004.
-
White, J., De Poumeyrol, B., Hale, J., and Stephenson, R., “Piezoelectric Paint: Ceramic-Polymer Composites for Vibration Sensors,” Journal of Materials Science, Vol. 39, No. 9, pp. 3105-3114, 2004.
[https://doi.org/10.1023/B:JMSC.0000025839.98785.b9]
-
Capsal, J.-F., David, C., Dantras, E., and Lacabanne, C., “Piezoelectric Sensing Coating for Real Time Impact Detection and Location on Aircraft Structures,” Smart Materials and Structures, Vol. 21, No. 5, Paper No. 055021, 2012.
[https://doi.org/10.1088/0964-1726/21/5/055021]
-
Choi, K., Hwang, M.-Y., Kang, D., Kang, M., Ahn, D., et al., “Impact Monitoring Characteristics of Piezoelectric Paint Sensor by Thermal Fatigue Analysis for Railroad Vehicle Applications,” Structural Health Monitoring, Vol. 19, No. 6, pp. 1951-1962, 2020.
[https://doi.org/10.1177/1475921720902274]
-
Han, D.-H. and Kang, L.-H., “Piezoelectric Characteristics of PNN-PZT/Epoxy Paint Sensor according to the Poling Conditions,” Sensors and Actuators A: Physical, Vol. 269, pp. 419-426, 2018.
[https://doi.org/10.1016/j.sna.2017.12.005]
-
Han, D.-H. and Kang, L.-H., “Piezoelectric Properties of Paint Sensor according to Piezoelectric Materials,” Functional Composites and Structures, Vol. 2, No. 2, Paper No. 025002, 2020.
[https://doi.org/10.1088/2631-6331/ab90e1]
- Hwang, M., Kang. M., Kang, L., “A Study on Piezoelectric Characteristic Changes of PNN-PZT/CNT/Epoxy Paint Sensor for Impact Monitoring of Aerospace Structures,” Proc. of the Conference on the Korean Society for Aeronautical & Space Science, pp. 101-104, 2015.
-
Kang, S.-H., Kang, M., and Kang, L.-H., “Piezoelectric Smart Composite Blades for Collision Monitoring: Measurement of Mechanical Properties and Impact Sensitivity,” Composite Structures, Vol. 202, pp. 1295-1307, 2018.
[https://doi.org/10.1016/j.compstruct.2018.06.065]
-
Hwang, M. Y. and Kang, L.-H., “Characteristics and Fabrication of Piezoelectric GFRP Using Smart Resin Prepreg for Detecting Impact Signals,” Composites Science and Technology, Vol. 167, pp. 224-233, 2018.
[https://doi.org/10.1016/j.compscitech.2018.08.002]
-
Park, S.-B., Han, D.-H., and Kang, L.-H., “Impact Signal Monitoring of a Composite Structure Using Piezoelectric Paint Sensor,” Composites Research, Vol. 27, No. 4, pp. 141-145, 2014.
[https://doi.org/10.7234/composres.2014.27.4.141]
-
Han, D.-H., Park, S.-B., and Kang, L.-H., “Sensitivity Measurement of the Piezoelectric Paint Sensor according to the Poling Electric Field,” Composites Research, Vol. 27, No. 4, pp. 146-151, 2014.
[https://doi.org/10.7234/composres.2014.27.4.146]
-
Choi, W., Choi, K., Yang, G., Kim, J. C., and Yu, C., “Improving Piezoelectric Performance of Lead-Free Polymer Composites with High Aspect Ratio BaTiO3 Nanowires,” Polymer Testing, Vol. 53, pp. 143-148, 2016.
[https://doi.org/10.1016/j.polymertesting.2016.05.018]
-
Choi, K., Choi, W., Yu, C., and Park, Y. T., “Enhanced Piezoelectric Behavior of PVDF Nanocomposite by AC Dielectrophoresis Alignment of ZnO Nanowires,” Journal of Nanomaterials, Vol. 2017, Paper No. 6590121, 2017.
[https://doi.org/10.1155/2017/6590121]
-
Choi, K., Kang, D., Park, S.-B., and Kang, L.-H., “A Study on Impact Monitoring Using a Piezoelectric Paint Sensor,” Journal of the Korean Society for Nondestructive Testing, Vol. 35, No. 5, pp. 349-357, 2015.
[https://doi.org/10.7779/JKSNT.2015.35.5.349]
-
Park, S.-B., Han, D.-H., and Kang, L.-H., “Investigation of Impact Detection Characteristics of Piezoelectric Paint according to Boundary Conditions,” Transactions of the Korean Society of Mechanical Engineers A, Vol. 38, No. 12, pp. 1335-1343, 2014.
[https://doi.org/10.3795/KSME-A.2014.38.12.1335]
-
Han, D.-H., Park, S.-B., and Kang, L.-H., “Study on Piezoelectric Characteristics of Piezoelectric Paint Sensor according to Poling Time,” Transactions of the Korean Society of Mechanical Engineers A, Vol. 38, No. 10, pp. 1069-1074, 2014.
[https://doi.org/10.3795/KSME-A.2014.38.10.1069]
Undergraduate Student in the School of Aerospace and Mechanical Engineering, Korea Aerospace University. His research interest is energy harvesting materials.
E-mail: phjin1216@kau.kr
Professor in the School of Aerospace and Mechanical Engineering, Korea Aerospace University. His research interest is energy harvesters and self-powered sensors based on thermoelectric/piezoelectric/triboelectric effects.
E-mail: kwchoi@kau.ac.kr