
고속 메니스커스 솔루션 시어링 코팅 가시화 장치를 이용한 페로브스카이트 결정화
Copyright © The Korean Society for Precision Engineering
This is an Open-Access article distributed under the terms of the Creative Commons Attribution Non-Commercial License (http://creativecommons.org/licenses/by-nc/3.0) which permits unrestricted non-commercial use, distribution, and reproduction in any medium, provided the original work is properly cited.
Abstract
Among the types of new and renewable energy, perovskite solar cells, which are next-generation solar cells, are capable of a solution process at a low temperature of 200oC or less, and have the advantages of high efficiency and low cost; hence, many studies have been conducted. Research has been performed on perovskite solar cells mainly produced using spin coating, but they have a disadvantage of occurrence of pinholes and cracks when fabricated over a large area, reducing the uniformity and density of the thin film. For the production of large-area perovskite solar cells, research is underway using solution shearing process technology among printed electronic process technologies, and most of the processes have been carried out at low speeds. This is due to the size of the crystal, which is one of the most important factors of high efficiency of the solar cell. When printing at high speed for mass production, the size of the crystal is reduced, resulting in charge loss and lower efficiency, making it difficult to apply the roll-to-roll process. In this study, to apply the roll-to-roll process for mass production, perovskite crystallization experiments were performed under high-speed conditions and crystal size changes according to meniscus stability.
Keywords:
Meniscus, Perovskite, Visualization, High-speed process, Crystallization, Perovskite solar cell키워드:
메니스커스, 페로브스카이트, 가시화, 고속 공정, 결정화, 페로브스카이트 태양전지1. 서론
환경오염의 문제가 대두되어 신재생 에너지에 대한 연구가 각광받고 있다. 신재생 에너지 중 실리콘 태양전지의 경우 고효율과 긴 수명을 가지지만 고가의 재료와 공정으로 인한 단가가 높다는 단점을 가지고 있어 이를 대체할 차세대 태양전지에 대한 연구가 진행 중이다. 페로브스카이트 물질은 200oC 이하의 저온 용액 공정이 가능하며, 저가의 재료를 사용하고, 이전의 실리콘 태양전지와 비슷한 효율을 가지고 있다. 또한 저가 설비로 공정이 가능하며 높은 광 흡수계수와 낮은 엑시톤 결합에너지를 가진다는 장점을 가지고 있어 다양한 연구 분야인 유기 발광 다이오드(Organic Light-Emitting Diode, OLED), 유기태양전지(Organic Photovoltaic, OPV) 등 제작에 활용되고 있다.
고효율 페로브스카이트 태양전지 제작 시 페로브스카이트의 큰 결정립 사이즈를 얻기 위해 저속의 공정 조건에서 제작이 이루어지고 있다. 고속의 공정 조건에서 제작이 이루어질 경우 페로브스카이트 결정립의 크기가 감소하는 현상이 발생되는데, 작은 크기의 결정립은 전자 손실을 유발시키고, 이는 태양전지의 저효율을 초래한다.1 이러한 문제들로 인해 양산화를 위한 롤투롤(Roll-to-Roll) 적용에 어려움을 겪고 있다. 이러한 어려움을 해결하기 위해 고속 공정 적용에 관한 많은 연구들이 나오고 있다. 솔루션 시어링 코팅 공정을 이용한 연구에서는 0.1-5.0 mm/s의 공정 속도에서 진행하였고,2 그라비아 코팅(Gravure Coating)을 이용한 연구에서는 18 mm/s에서 공정을 진행하였다.3 또한 다른 연구팀에서는 기판 온도에 따른 결정립 성장 변화에 대한 연구를 진행하였으며, 이때 기판 온도는 25-150oC에서 공정을 진행하였다.4 이와 같이 현재 페로브스카이트의 연구 중 가장 높은 효율을 보여주고 있고, 최근 많은 연구들이 나오고 있는 메니스커스를 이용한 솔루션 시어링 코팅을 적용하여 페로브스카이트 태양전지의 흡광층을 고속 공정에 적용이 가능한 공정 조건을 확립하였다. 메니스커스 솔루션시어링 코팅 공정은 박막 형성에 표면 거칠기가 매우 우수하다는 장점을 가지고 있으며 다층구조를 갖는 태양전지 제작에 하부층의 영향을 주지 않는다.
2. 이론
2.1 페로브스카이트 태양전지
페로브스카이트(Perovskite) 결정은 ABX3 구조를 가지며 A와 B는 양이온, X는 결합하고 있는 음이온이다. 페로브스카이트는 구성된 원자에 따라 다양한 종류를 가지고 있다. 대표적으로 태양전지에 사용되는 페로브스카이트 종류로는 CH3NH3PbI3 (MAPbI3)와 HC(NH2)2PbI3 (FAPbI3)를 들 수 있다.5
페로브스카이트 물질은 저온 용액 공정이 가능하다는 가장 큰 장점을 가지고 있어 저가 공정으로 고효율의 소자를 제작할 수 있다. 대부분의 페로브스카이트 용액 공정은 스핀 코팅(Spin Coating) 방식을 이용해 많은 연구가 진행된다. 하지만 스핀 코팅 공정 기술을 이용하여 대면적 코팅을 할 경우 핀홀과 균열이 발생해 박막의 낮은 균일성과 조밀도를 유발하며, 양산화를 위한 연속 공정이 불가능하다는 단점을 가지고 있다.6 또한 인쇄하고자 하는 용액을 기판에 떨어트려 코팅하는 방식으로 용액의 손실이 크다는 단점을 가지고 있다. 이러한 단점을 보완하고 대면적 페로브스카이트 태양전지를 제작하기 위해 인쇄 전자 공정 기술이 떠오르고 있다. 하지만 페로브스카이트 물질 특성상 빠른 속도로 박막을 제작할 경우 Fig. 1과 같이 결정립의 크기가 감소하는 경향이 발생되고, 이에 따라 저효율을 초래한다. 이러한 특성으로 인하여 양산화를 위한 롤투롤 공정 적용의 어려움을 가지고 있어 이를 해결할 수 있는 공정 조건을 확립하는 연구가 필요하다.
2.2 솔루션 시어링 코팅(Shearing Solution Coating)
Fig. 2와 같이 솔루션 시어링 코팅은 기판(Subatrate)과 블레이드(Blade) 사이의 간격에 용액을 주입하여 코팅하는 방식이다. 이 부분에서 모세관 현상이 발생되어 형성된 메니스커스를 이용하여 코팅하는 기술이다. 대면적 코팅이 가능하며, 원하는 패턴과 양을 조절할 수 있다는 장점을 가지고 있다. 본 공정의 변수는 기판과 블레이드 사이의 간격(Gap), 블레이드 각도(Blade Angle), 인쇄 속도(Coating Speed)와 이전 솔루션 시어링 공정과는 다른 기판 온도(Hot Substrate)가 있으며 이러한 다양한 공정 변수를 이용하여 다양한 공정 연구가 진행 중이다.
소량의 재료를 사용하기 때문에 재료 손실이 적으며 균일한 대면적의 박막을 제작할 수 있다. 높은 공정 효율과 생산성을 가질 수 있다는 장점을 가지고 있다.7 또한 롤투롤 공정에 적용하기 전 시제품 제작 공정 연구를 진행할 수 있다.
2.3 솔루션 시어링 코팅에 적용된 유체역학 이론
솔루션 시어링 코터는 기판과 블레이드 사이에 발생된 모세관현상에 의한 메니스커스를 이용한 장비이다. 공정 중 메니스커스 형상은 박막 코팅 중 가장 중요한 인자이므로 메니스커스 형상 제어 연구가 필요하다. 메니스커스에는 다음과 같이 다양한 유체역학 이론이 적용된다.
Fig. 3에서 메니스커스에는 모세관 현상(Capillary Flow), 마랑고니 유동(Marangoni Flow), 쿠에트 유동(Couette Flow)과 레일리 버나드 대류(Rayleigh-Bénard Convection)가 적용되어 있다. 모세관 현상 액체 속에 모세관을 넣었을 때 관내에 액면이 외부의 자유 표면보다 높거나 낮아지는 현상으로 응집력과 부착력에 의해 발생되며 이때 메니스커스가 형성된다.8 이때 형성된 메니스커스는 가장 먼저 공기와 접촉하는 부분으로 대부분의 증발이 발생하는 부분이다. 증발이 일어나면 질량 손실을 유발되고, 이때 액체-액체 또는 액체-기체 사이의 표면장력 변화에 의해 발생되는 액체 운동을 의미하는 마랑고니 유동 이 질량 손실을 보충하기 위해 발생된다.9,10 또한 고정된 기판과 운동을 하는 상판(블레이드) 사이의 전구체 용액은 전단력을 생성하는데 이는 쿠에트 유동흐름을 의미하는 전단 구동 유체 운동을 유도한다. 쿠에트 유동은 일정한 속도로 상대운동을 하는 평행한 두 평면 사이에서 점성유체에 의해 발생된 정상층 흐름을 의미한다.11
연구에 사용된 장비의 경우 기판의 온도도 제어할 수 있는 장비다. 기판에 온도를 가하게 되면 기판과 주입된 용액의 온도 차이에 의해 레일리-버나드 대류(Rayleigh-Benard Convection)가 발생된다. 이 대류는 자연 대류의 한 유형으로, 가열된 유체의 수평층에서 발생된다. 이때 유체는 Bénard 세포라고 알려진 규칙적인 패턴을 가지는 세포를 형성하게 된다. 또한 온도차가 증가할 경우 더 큰 대류가 형성되고 세포의 크기가 증가한다.12
또한 이러한 유체의 유동에 의해 커피링 효과가 발생된다. 커피링 효과는 미세입자를 포함하는 액체가 증발할 때 입자들이 가장자리에 쌓이는 원리로 발생한다. 이는 액적의 중심부보다 가장자리에서 증발이 활발하게 일어나게 되어 발생된 질량 손실을 보충하기 위해 중심부에서 가장자리로 유동이 발생된다. 발생된 유동에 의해 액체 속에 포함된 입자들 또한 이동해 가장자리에 쌓이게 되어 증발 후 가장자리의 색이 중심부보다 진해지는 현상이 발생된다. 이는 균일한 박막을 제작하는 데에 좋지 않은 영향을 끼친다.
3. 실험 방법
3.1 실험 장치 및 재료
메니스커스 솔루션 시어링 코팅(Meniscus Solution Shearing Coating, MSSC)을 이용하여 페로브스카이트 태양전지의 흡광층의 박막 특성과 메니스커스 안정성에 따른 결정립 크기에 대한 연구를 하였다. 기존 MSSC 장비는 저속(-5.0 mm/s)으로만 공정이 가능했고, 기판 온도를 가할 수 없었다. 기존 장비를 수정하여 기판 온도와 고속 모터를 장착한 메니스커스 솔루션 시어링 코팅 장비를 이용하여 공정 연구를 진행하였다. 기존 장비의 경우 5 mm/s가 가장 빠른 속도였지만 연구에 사용된 장비는 최고 30 mm/s로 추후 롤투롤 공정에 적용이 가능하도록 수정하였다. 또한 메니스커스 형상의 안정성를 확인하기 위해 Fig. 4에서 볼 수 있듯이 CCD 카메라를 부착하여 코팅 중 실시간으로 메니스커스 형상을 확인하였다.
태양전지의 흡광층(Absorption Layer)에는 다양한 연구분야에 적용되고 있는 페로브스카이트 물질 중 MAPbI3 (Methylammonium Lead Iodide, CH3NH3PbI3)를 사용하였다. 30wt%의 Dimethly Sulfoxide (DMSO, Aldrich, 99.9%)와 Gamma Butyrolactone (GBL, Aldrich, 99.9%)를 7 : 3의 비율로 용액을 제조한 후, 24시간 교반하였다. 기판은 Bare Glass를 사용하였고, 초음파세척기로 Acetone에 담궈 20분 정도 세척한 후 가열된 IPA (Isopropayl Alcohol)에 15분가량 세척 후 오븐에서 건조를 진행하였다. 그 후, 20분 동안 UV 처리하여 유기물을 제거하여 2차 세척을 진행하였다.
3.2 실험 내용
고속의 조건에서도 큰 크기의 결정립을 가지는 흡광층 제작을 위한 연구를 진행하였다. MSSC의 공정 변수는 블레이드 각도, 기판 온도(Substrate Temperature), 인쇄 속도와 기판과 블레이드 사이의 간격(Gap)을 변수로 설정하였다.
다양한 변수를 이용하여 박막의 두께, 결정립의 크기와 메니스커스 안정성에 따른 결정립 크기에 대한 연구를 수행하였다. 박막 두께 측정은 알파스텝(α-Step)을 이용하였다. 알파스텝은 탐침이 피측정물 표면을 긁어 두께를 전기적 시그널로 증폭하여 기록 및 측정하는 방식으로 비교적 간단한 방법이다. 두께 변화를 확인하기 위해 기판 온도는 상온, 블레이드 각도는 3o로 고정한 후 인쇄 속도와 기판과 블레이드 사이의 간격을 변수로 두어 공정을 진행하였다. 인쇄 속도는 6부터 7 mm/s 간격으로 증가시키고, 기판과 블레이드 사이의 간격은 100과 200 μm의 조건으로 인쇄하였다. p-i-n 구조의 페로브스카이트 태양전지 흡광층의 보편적인 두께는 300-450 nm로 350 nm의 두께를 목표로 설정하였다. 흡광층 두께는 Fig. 5와 같은 측정 결과를 얻었다. 인쇄 속도가 증가함에 따라 두께가 감소하는 경향을 확인하였다. 이는 용매가 박막에 머무르는 시간이 감소하고, 증발속도가 증가해 도출된 결과라고 예상한다. 위의 결과를 통해 인쇄속도는 27, 20 mm/s의 순서로 350 nm와 근접한 값을 보였다.
페로브스카이트 태양전지의 효율에 가장 큰 영향을 주는 요인은 페로브스카이트 결정립의 크기이다. 결정립 크기는 빛의 굴절을 이용항 확대 관찰 장치인 광학 현미경(Optical Microscope, OM)을 이용하여 측정하였다. 페로브스카이트 물질을 인쇄한 후 열처리 또는 추가적인 안티 솔벤트 공정을 통해 박막이 형성된다. 이때 결정립이 형성되고, 크기에 따라 전자와 정공이 이동할 때 발생되는 전하 손실량이 결정된다. 이러한 결정립의 크기는 인쇄 속도가 증가함에 따라 감소하는 경향을 보였다. 결정립의 크기가 클수록 Shunt 저항이 증가하고 직렬 저항이 감소한다. 입자 크기는 페로브스카이트 태양전지에서 더 높은 효율을 갖기 위한 중요한 매개변수이다. 중요한 매개변수임에 불구하고 많은 연구들은 저속 공정 연구에 못 미치고 있다. 양산화를 위한 롤투롤 적용에 어려움을 겪고 있다. 고속 공정에도 큰 사이즈의 Grain 사이즈를 갖는 박막 제작을 위한 연구를 진행하였다. 기판 온도는 상온, 블레이드 각도는 3o로 고정한 후 앞서 언급한 조건과 같이 인쇄 속도는 6부터 7 mm/s 간격으로 증가시키고, 기판과 블레이드 사이의 간격은 100과 200 μm의 조건으로 인쇄하였다. 결정립 형성은 빛의 굴절을 이용한 확대 관찰 장치인 광학현미경을 이용하여 측정하였다. Fig. 6에서 볼 수 있듯이 인쇄 속도가 급격하게 증가하여도 결정립이 크게 성장하지 않는 경향을 확인하였다.
Fig. 7의 CCD 카메라를 통해 촬영된 메니스커스는 초점이 잘 잡힌 안정한 형상을 보였지만 기판의 온도를 상온에서 고정한 후 인쇄 속도를 증가시켰을 때 결정립이 형성되지 않는 것을 확인하였다. 이러한 결과는 결정립의 성장은 증발 직후 일어나는데 인쇄 속도가 너무 빨라 결정립이 형성될 시간이 부족해 이러한 경향을 보인 것이라고 예상할 수 있다.
기판 온도에 따라 증발이 변화하고, 이에 따른 박막 두께 변화가 발생한다. 기판 온도에 따라 인쇄된 흡광층 박막의 두께 변화를 박막 두께 측정기(α-Step)을 이용하여 측정했다. 먼저 블레이드 각도는 3o로 고정한 후 기판 온도는 50에서 150oC, 인쇄 속도는 6부터 7 mm/s 간격으로 증가시켜 27 mm/s속도로 진행하였다. 블레이드와 기판 사이의 간격은 100과 200 μm의 공정 조건으로 페로브스카이트 박막을 인쇄하였다. Fig. 8과 같은 결과를 얻었으며 같은 인쇄 속도와 갭의 공정 조건에서 기판 온도가 증가함에 따라 박막의 두께가 감소하는 것을 확인하였다. 기판 온도가 증가함에 따라 증발 속도가 빨라져 박막의 두께가 감소하는 것이라고 예상할 수 있다. Fig. 9는 150oC에서 용매가 증발되는 모습을 CCD 카메라를 이용하여 촬영한 것으로 이를 통해 기판의 온도가 증가함에 따라 두께가 감소하는 경향을 설명할 수 있다.
인쇄 속도가 증가함에 따라 증발 후 결정립의 성장이 될 만한 충분한 시간이 충족되지 않아 성장이 이뤄지지 않았다. 이를 해결하기 위해 기판 온도를 가했을 때 성장된 결정립 크기 변화에 대해 확인하였다. 공정 조건은 앞의 실험과 동일하게 진행하였다.
Fig. 10에서 50oC의 기판 온도에서의 결정립 형상을 보면 20 mm/s 미만의 속도에서는 결정립 성장이 이루어지지 않았다. 20 mm/s 이상의 속도에서는 비교적으로 결정립이 성장되는 경향을 보였지만 완벽한 페로브스카이트 결정립이 형성되지 않았다. 100oC의 기판 온도에서의 시료는 50oC의 조건에서 보다 느린 속도에서 결정립이 성장되었지만 크기가 매우 작아 고효율 페로브스카이트 태양전지에 적용하기에는 어렵다. 마지막 조건인 150oC의 가판 온도에서는 이전 조건과 비교했을 때 13 mm/s 이하에서도 결정립이 형성되었으며, 고속인 20 mm/s 이상의 기 판 온도에서도 결정립이 형성되었다. 유체역학 이론 중 상하부의 온도차에 따라 형성된 대류에 의해 규칙을 가지는 결정립을 형성한다는 레일리-버나드 대류 이론에 의해 설명이 가능하다. 이 이론은 온도차가 증가하면 형성되는 결정립의 크기가 증가한다는 것을 포함한다.
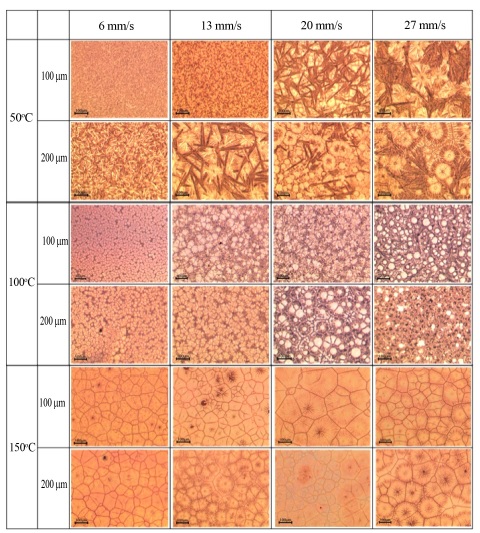
Variation of the grain formation according to the coating speed and substrate temperature (Scale bar: 100 μm)
150oC의 기판 온도와 주입된 용액의 온도차가 이전 온도에 비해 증가하였고, 따라서 이전 조건에서 형성된 결정립보다 큰 크기의 결정립이 형성된 것이라고 예상한다. 이전의 페로브스카이트 태양전지 흡광층의 연구에서 보편적으로 사용된 인쇄 속도 1-5 mm/s보다 약 4배의 인쇄 속도에서도 큰 페로브스카이트 결정립 크기를 갖는 150oC의 기판 온도, 20 mm/s의 인쇄 속도와 100 μm의 갭을 최적 공정 조건으로 확립하였다.
각 결과들의 결정립의 크기를 비교하기 위해 최적 공정 조건을 기준으로 기판 온도별 결정립 크기를 광학현미경을 통해 측정하여 비교했다. 측정 결과는 Fig. 11과 같으며, 기판 온도가 증가함에 따라 결정립 크기가 증가하는 경향을 확인할 수 있다.
메니스커스 솔루션 시어링 코팅 기술은 메니스커스를 이용한 방식으로 메니스커스 형상에 따라 결정립 변화에 대한 실험을 진행하였다. 앞서 언급한 바와 같이 메니스커스는 블레이드와 기판 사이의 간격에 형성된다. 이때 간격이 증가할수록 용액이 머무르는 표면적이 감소하게 된다. 이에 따라 용액은 안정한 상태를 유지하기 위해 덩어리가 되는 현상인 응집이 발생된다. Fig. 12(b)와 같이 응집된 메니스커스를 불안정한 메니스커스라 칭하였다. 또한 CCD 카메라의 초점은 블레이드 끝단으로 설정되어 있기 때문에 초점을 통해 안정성을 판단하였다.
인쇄 속도, 기판 온도와 기판과 블레이드 사이의 간격은 확립된 최적 공정 조건으로 진행하고, 블레이드 각도를 변수로 두었다. 메니스커스 솔루션 시어링 코팅에 보편적으로 사용되는 각도는 3-5o이지만, 메니스커스 형상 변화를 확인하기 위해 10o까지 공정을 진행하였다.
Fig. 13은 블레이드 각도에 따른 결정립 변화와 CCD 카메라를 통해 촬영된 메니스커스 이미지이다. 각도를 극한으로 9o까지 증가시켰을 때 메니스커스는 안정하게 형성되었으며 페로브스카이트 결정립 또한 고속임에도 불구하고 형성되는 것을 확인하였다. 비록 최적 공정 조건인 3o의 블레이드 각도일 때보다는 살짝 감소하는 경향을 보였지만 결정립이 형성되는 것을 확인할 수 있었다. 이를 통해 각도가 증가함에 따라 결정립의 크기에 영향을 끼쳐 미세하게 감소하는 경향을 확인하였다.
다음으로는 메니스커스 안정성에 따른 결정립 변화에 대해 확인해보았다. 이때의 공정 조건은 인쇄 속도와 기판 온도는 20 mm/s와 150oC로 고정한 후 블레이드와 기판 사이의 간격과 블레이드 각도를 변수로 두어 진행하였다. 메니스커스를 이용한 공정 기술이라는 점을 고려해 Fig. 12(b)와 같이 메니스커스의 형상이 안정적으로 되어 있지 않고, 용액의 응집 현상이 발생하게 되면 인쇄된 박막에 영향을 줄 것이라는 가정을 두고 수행하였다. 이를 위해 블레이드 각도와 기판과 블레이드 사이의 간격을 극단적으로 키워 그때의 이미지를 촬영하고, 그에 따른 결정 립 크기 변화를 확인하였다. Fig. 14는 CCD 카메라를 통해 인쇄 중 메니스커스 형상을 촬영한 결과이다. 블레이드 각도를 10o로 증가시켜 코팅하였을 때 100 μm의 Gap에서는 용액의 응집현상이 발생되지 않고 코팅이 진행되었다. 하지만 이보다 큰 500 μm의 Gap에서는 Fig. 12(b)와 같이 용액의 응집 현상이 발생해 CCD 카메라상에 초점이 잡히지 않은 것을 확인할 수 있다. 응집 현상이 발생한 상태로 즉, 불안정한 메니스커스를 유지한 후 박막을 인쇄할 경우 Fig. 12의 오른쪽 하단의 그림처럼 박막이 균일하게 인쇄되지 않고 원하는 패턴의 박막을 제조할 수 없다.
불안정한 메니스커스 형상을 유지한 후 150oC의 기판 온도와 20 mm/s의 인쇄 속도에서 박막을 코팅한 결과 안정한 메니스커스 형상보다 불안정한 메니스커스 형상을 유지한 후 인쇄된 페로브스카이트의 결정립의 형상과 크기는 Fig. 15에서 볼 수 있듯이 크기가 점차 감소하고 결정립의 질의 상대적으로 좋지 않은 경향을 확인하였다.
4. 결론
메니스커스를 이용한 솔루션 시어링 공정을 이용하여 페로브스카이트 태양전지의 흡광층 공정 연구로서 추후 롤투롤 공정 적용을 위한 고속 공정 연구를 진행하였다. 메니스커스 솔루션 시어링 코팅의 공정 변수인 인쇄 속도, 기판 온도, 블레이드 각도와 기판과 블레이드 사이의 간격에 따라 흡광층에 쓰이는 페로브스카이트의 결정립 성장의 변화를 확인하였다. 동일한 메니스커스 솔루션시어링 코팅 공정을 적용한 이전 연구에서는 1-3 mm/s 속도로 연구를 진행한 바가 있다. 인쇄 속도는 이전 연구1의 저속 공정과는 상반된 속도로 6-27 mm/s의 고속에서 공정연구를 진행하였다. 그 결과 두께는 인쇄 속도가 증가함에 따라 감소하는 경향을 확인하였다. 이는 인쇄 속도가 증가함에 따라 증발률이 증가하고, 용액이 박막에 머무르는 시간이 감소하는 이유로 설명할 수 있다.
본 연구의 핵심인 페로브스카이 물질의 결정이 크고, 고를수록 전자가 잘 이동할 수 있어 태양전지 효율이 높아지기 때문에 페로브스카이트의 결정립 크기 변화를 확인하기 위해 인쇄 속도와 기판 온도에 따라 변화를 확인하였다. 저온의 기판 온도와 저속의 공정에서 보다 고온의 기판 온도와 고속의 공정 조건에서 페로브스카이트 박막을 제작하였을 때 비슷한 결정립을 얻을 수 있었으며, 결정립이 활발하게 성장되는 것을 확인하였다. 결정립 성장은 증발 직후 발생하게 되는데 고온의 기판 온도에서 증발이 더 활발하게 발생되기 때문에 이러한 경향을 보인 것이라고 예측할 수 있다.
또한 메니스커스를 이용한 솔루션 시어링 코팅 장비를 이용하여 박막을 제조하기 때문에 메니스커스의 형상에 따라 박막에 미치는 영향을 확인하기 위해 다양한 블레이드 각도에서 공정을 진행하였다. 그 결과 블레이드 각도를 3-10o까지 증가시켜 공정을 진행한 결과 결정립이 성장되는 것을 확인하였지만 결정립의 크기가 감소하는 것을 확인하였다. 또한 10o의 블레이드 각도와 500 μm의 블레이드와 기판 사이의 간격의 조건에서는 용액의 응집 현상이 발생되어 불안정한 메니스커스 형상을 확인하였으며, 이에 따라 이전에 가장 큰 결정립을 얻은 공정 조건인 150oC의 기판 온도와 20 mm/s의 인쇄 속도에서 박막을 제작하여 결정립의 크기를 비교한 결과 크기가 감소하는 경향을 확인하였다.
롤투롤 공정의 평균 속도는 3 m/min이다. 실험에서 조건이 확립된 속도는 20 mm/s (1.2 m/min)로 약 1.8 m/min 정도 차이를 가지고 있다. 이 차이는 공정 변수 중 인쇄 속도를 증가시키고 기판 온도를 조절함으로서 충분히 좁혀질 것이라고 예상한다. 연구에 사용된 장비는 Sheet Type으로 Lab Scale로 롤투롤 공정으로 상용화하기 위해 시제품 제작을 위한 조건 확립하는 장비로 적합하다. 연구를 통한 최적 공정을 도출해 페로브스카이트 태양전지 소자의 적용한다면 고효율 대면적 페로브스카이트 태양전지의 양산화가 가능할 것이다.
Acknowledgments
This research was supported by Basic Science Research Program through the National Research Foundation of Korea (NRF) funded by the Ministry of Education (No. 2018R1A6A1A03026005). This research was supported by the research fund of Hanbat National University.
REFERENCES
-
Kim, K. M., Lee, H. A., and Kim, D. S., “Study on Optimization of Meniscus Solution Shearing Coating Process for Fabrication of Large Area Perovskite Solar Cell,” Journal of the Korean Society for Precision Engineering, Vol. 37, No. 6, pp. 443-449, 2020.
[https://doi.org/10.7736/JKSPE.019.164]
-
Kim, M. K., Lee, H. S., Pae, S. R., Kim, D.-J., Lee, J.-Y., et al., “Effects of Temperature and Coating Speed on the Morphology of Solution-Sheared Halide Perovskite Thin-Films,” Journal of Materials Chemistry A, Vol. 6, No. 48, pp. 24911-24919, 2018.
[https://doi.org/10.1039/C8TA08565J]
-
Kim, Y. Y., Yang, T.-Y., Suhonen, R., Kemppainen, A., Hwang, K., et al., “Roll-to-Roll Gravure-Printed Flexible Perovskite Solar Cells Using Eco-Friendly Antisolvent Bathing with Wide Processing Window,” Nature Communications, Vol. 11, No. 1, pp. 1-11, 2020.
[https://doi.org/10.1038/s41467-020-18940-5]
-
Zhong, Y., Munir, R., Li, J., Tang, M.-C., Niazi, M. R., et al., “Blade-Coated Hybrid Perovskite Solar Cells with Efficiency > 17%: An in Situ Investigation,” ACS Energy Letters, Vol. 3, No. 5, pp. 1078-1085, 2018.
[https://doi.org/10.1021/acsenergylett.8b00428]
-
Lee, J.-W. and Park, N.-G, “Perovskite Solar Cell,” Vacuum Magazine, Vol. 1, No. 4, pp. 10-13, 2014.
[https://doi.org/10.5757/vacmag.1.4.10]
- Yang, T. Y., Joong, J. N., Seo, J. W., and Noh, J. H., “Perovskite Solar Process Technology,” Journal of the Korean Institute of Electrical and Electronic Material Engineers, Vol. 29, No. 9, pp. 22-34, 2016.
- Choe, J., Song, J., Jeong, J., Chung, C.-H., Kim, J., et al., “The Influence of Process Variables on the Thin Film Growth of Metal-Halide Perovskites by the Solution Shear Coating,” Journal of the Korean Institute of Surface Engineering, Vol. 52, No. 1, pp. 6-15, 2019.
-
Nguyen, T. A., Nguyen, A. V., Hampton, M. A., Xu, Z. P., Huang, L., et al., “Theoretical and Experimental Analysis of Droplet Evaporation on Solid Surfaces,” Chemical Engineering Science, Vol. 69, No. 1, pp. 522-529, 2012.
[https://doi.org/10.1016/j.ces.2011.11.009]
- Kim, J. Y., Rie, D. H., Park, J. H., and Choi, G. K., “A Study of Heat Transfer Enhancement by Temperature Driven Marangoni Convection,” Korean Journal of Air-Conditioning and Refrigeration Engineering, Vol. 15, No. 10, pp. 795-801, 2003.
-
Zhang, Z., Peng, B., Ji, X., Pei, K., and Chan, P. K. L., “Marangoni-Effect-Assisted Bar-Coating Method for High-Quality Organic Crystals with Compressive and Tensile Strains,” Advanced Functional Materials, Vol. 27, No. 37, Paper No. 1703443, 2017.
[https://doi.org/10.1002/adfm.201703443]
-
Dai, X., Deng, Y., Van Brackle, C. H., and Huang, J., “Meniscus Fabrication of Halide Perovskite Thin Films at High Throughput for Large Area and Low-Cost Solar Panels,” International Journal of Extreme Manufacturing, Vol. 1, No. 2, Paper No. 022004, 2019.
[https://doi.org/10.1088/2631-7990/ab263e]
-
Deng, Y., Wang, Q., Yuan, Y., and Huang, J., “Vividly Colorful Hybrid Perovskite Solar Cells by Doctor-Blade Coating with Perovskite Photonic Nanostructures,” Materials Horizons, Vol. 2, No. 6, pp. 578-583, 2015.
[https://doi.org/10.1039/C5MH00126A]
The Master’s course in the Department of Creative Convergence, Hanbat National University. Her research interest is printed electronics and perovskite solar cell.
E-mail: dlwlgom@naver.com
Ph.D. course in the Department of Creative Convergence, Hanbat National University. Her research interest is printed electronics.
E-mail: hyunah@hanbat.ac.kr
Professor in the Department of Creative Convergence, Hanbat National University. His research interest is 4D printing.
E-mail: kds671@hanbat.ac.kr