
루테늄과 사마리아 도핑된 세리아의 서멧 구조 스퍼터 박막의 조성 비율 변화에 따른 스크래치 특성
Copyright © The Korean Society for Precision Engineering
This is an Open-Access article distributed under the terms of the Creative Commons Attribution Non-Commercial License (http://creativecommons.org/licenses/by-nc/3.0) which permits unrestricted non-commercial use, distribution, and reproduction in any medium, provided the original work is properly cited.
Abstract
Interest in the use of thin film of Ruthenium-Samaria doped ceria cermet (Ru-SDC) as anode in solid oxide fuel cells is increasing due to its high oxygen storage capacity and high chemical and thermal stability. To have enough structural integrity between sputtered Ru-SDC films and underlying substrates, good adhesion property is required. In this work, scratch resistance and failure mode for Ru-SDC films with various SDC composition were investigated using a scratch test method employing linearly increasing load from 1 to 50 N using a 200 μm radius Rockwell C indenter. Scratched surfaces were examined with a field emission scanning electron microscope. Chemical compositions in scratch tracks were analyzed by energy dispersive X-Ray spectroscopy. Critical loads for films with different SDC ratios were assessed and associated failure modes were identified. The highest scratch resistance among tested film compositions was the one that contained 50% of SDC. Failure modes of tested films regardless of the ratio of SDC were identified to be the initiation of tensile cracks with rapid increase of friction coefficient followed by chipping, and eventually the generation of a severe crack network.
Keywords:
Scratch test, Critical load, Surface damage, Failure mode, Ruthenium and Samaria doped ceria키워드:
스크래치 시험, 임계하중, 표면 파손, 파손 모드, 루테늄과 사마리아가 도핑된 세리아1. 서론
루테늄은 탄화수소 연료를 분해하는데 효율적이고, 높은 융점(2,334oC)을 가진 금속으로 탄화수소 연료를 사용하는 고체 산화물 연료전지의 연료극에 널리 이용되고 있는 물질이다[1-4]. 세리아 물질은 Ce4+와 Ce3+ 간의 산화환원 반응이 잘 일어나고, 산소 공극을 이용한 산소 저장 능력(Oxygen Storage Capacity, OSC)이 높다.
또한, 도핑된 세리아 물질은 도핑되는 물질의 이온 형태가 3가 원소(Sm3+, Gd3+)인 경우 산소 이온의 전도율이 높아지고, 4가 원소 물질(Zr4+와 Hf 4+)인 경우 OSC와 열적 내구성이 좋아지는 특성을 가진다[5]. 이러한 성질을 이용해 최근 세리아 물질은 전기화학적 전극에서 촉매로 널리 쓰이고 있다[6-8]. 금속과 세라믹 물질의 합성물(서멧 구조)은 금속의 조대화 현상(Coarsening)을 억제하여 전극 구조로 널리 사용되고 있다. 서멧 구조는 두 물질의 특성을 동시에 가지며 조성 비율에 따라 물질의 특성을 달리할 수 있는 장점이 있다. 메탄의 건식 개질 반응에서 우수한 전기화학적 촉매반응성을 가진 루테늄의 성질과 활발한 산소교환반응을 통해 금속 전극 표면에서 탄화수소의 산화반응에 참여하는 도핑된 세리아의 특성을 이용한 연구가 진행되었고, 이를 통해 루테늄과 도핑된 세리아의 서멧 구조는 탄화수소 촉매물질로 널리 알려져 있다[9-12]. 루테늄과 도핑된 세리아의 서멧 구조를 가진 박막을 제조하기 위해 물리적 기상 증착법(Physical Vapor Deposition) 중 스퍼터링 공정을 이용하는 연구가 진행되었다[13,14]. 한편, 증착된 박막이 가져야 할 중요한 성능으로 모재와의 충분한 접합력(Adhesion Strength)과 박막층 내부의 우수한 응착력(Cohesive Strength)을 고려해야 하는데 고체연료전지 분야의 박막에 대해 이러한 성능에 대한 연구는 진행된 바가 거의 없다. 모재와 박막층의 접합 성능에 대한 평가를 위해 스크래치 시험법(Scratch Test)이 널리 활용하고 있다. 스크래치 시험법은 다이아몬드 압입자를 사용하여 수직 하중을 선형적으로 증가시키며 시편 표면을 스크래치하며 이동할 때 표면에 발생하는 균열과 파손 모드를 규명하는 시험법이다. 특히 균열과 파손의 발생 과정을 조사하여 모재와 박막층의 접합 성능과 박막층 내부의 스크래치 저항 성능을 임계하중(Critical Load)이란 기준척도값으로 설명한다[15,16].
본 연구에서는 루테늄과 사마리아가 도핑된 세리아 서멧 구조의 조성 비율을 변화시켜 스퍼터링 공정으로 제조한 네 가지 종류의 박막들을 대상으로 매크로 스케일(Macro-Scale)에서의 스크래치 시험을 통해 박막층 조성 변화에 따른 스크래치 저항 성능을 비교평가하고, 각 박막층의 파손 거동을 파악하고자 하였다[17-20].
2. 연구 방법 및 내용
2.1 시편
루테늄과 도핑된 세리아의 서멧 구조 박막은 500 μm 두께의 N-Type SiO2 (100) 기판에 DC/RF 마그네트론 스퍼터링(KVS-2000, Korea Vacuum Tech) 공정을 이용하여 제조하였다. Ru(99.9%, RND Korea)와 Samaria Doped Ceria (SDC, Kurt J. Lesker Company; 15 mol%) 타겟을 사용하였고 SDC의 함유율을 변화시키며 네 종류의 박막을 제조하였다. 제조한 네 종류의 박막은 SDC 함유율이 부피 비율로 각각 0, 10, 50과 100 vol%이며 편의상 각각 Ru-SDC 0, Ru-SDC 10, Ru-SDC 50과 Ru-SDC 100으로 표기하였다.
DC와 RF 스퍼터링 파워는 7 mTorr의 Ar 분위기에서 Ru-SDC 0는 각각 28과 0W, Ru-SDC 10 은 각각 28과 20W, Ru-SDC 50은 각각 28과 60W 그리고 Ru-SDC 100 은 각각 0과 60W로 조절하였다. 제조한 박막들의 두께와 미세구조는 고분해능 주사전자현미경(Hitachi, SU8010, HR-SEM)을 사용해 분석하였으며 배율 15만배로 촬영한 박막의 단면 사진을 Fig. 1에 제시하였다. Ru-SDC 50을 제외한 모든 박막들은 스퍼터링 증착의 특성인 기둥 구조(Columnar Structure)를 가지고 있다. Ru-SDC 0과 Ru-SDC 10의 단면을 보면 기둥구조가 확연하게 관측된다. Ru-SDC 100의 경우엔 Ru-SDC 0과 Ru-SDC 10에 비해 기둥 구조 입자의 크기도 현저히 크고 기둥 구조가 아닌 조대한 입자가 혼재하고 있다. 따라서 Ru-SDC 100은 박막층이 조밀하지 않아 박막 내부의 응착력이 다른 박막에 비해 상대적으로 낮을 것이며 이것이 스크래치 저항성과 밀접히 연계될 것으로 예측된다. 반면에 Ru-SDC 50 박막은 다른 세 박막과는 달리 기둥구조가 거의 형상되지 않았으며 박막의 구조가 매우 조밀하여 다른 박막에 비해 상대적으로 높은 스크래치 저항성을 보일 것으로 예측된다. 박막의 두께는 84-105 nm로 박막 간에 약간의 두께 차이가 있으며 특히 Ru-SDC 10과 Ru-SDC 50의 두께 차이가 약 19 nm로 측정되었다. 스크래치 시험에서 균열의 발생은 박막 표면에서 시작하며 임계하중은 박막층 전체의 파손보다는 균열이 발생하기 시작하는 하중과 관계가 있다. 따라서 두께의 영향보다는 박막층의 조밀성이 더 중요하며 Ru-SDC 50의 조밀성이 Ru-SDC 10보다 매우 우수하기 때문에 Ru-SDC 50의 스크래치 저항 성능이 월등히 좋을 것임을 예측할 수 있다. 증착된 박막의 화학적 조성 분석을 위해 X선 광전자분광기(X-Ray Photoelectron Spectroscopy, XPS; K-Alpha+; ThermoFisher Scientific)를 이용하였다. Fig. 2는 XPS를 통해 측정한 Ru-SDC 샘플별 화학적 조성 분석 결과이다. Ru 3D 피크와 Ce 3D 피크를 측정하였다. Ru-SDC 100과 Ru-SDC 50에 비해서 Ru-SDC 10은 SDC가 부분적으로 환원되었음을 알 수 있다. Ru-SDC 100 샘플에서는 Ru 피크가 검출되지 않았고, Ru-SDC 0에서는 Ce 피크가 검출되지 않아 각각 제조 목적대로 Ru와 Ce로만 구성된 박막임을 확인하였다.
2.2 스크래치 시험
증착된 박막의 접합 특성과 파손 모드는 Universal Mechanical Tester (UMT, Bruker, USA)를 이용해 매크로 스케일에서 스크래치 시험을 통해 평가하였다. Fig. 3은 본 연구에서 사용된 UMT 장비의 스크래치 시험 모듈의 개략도를 나타낸 것이다. 모든 시험은 선단 반경 200 μm인 원추형 로크웰 C 다이아몬드 압입자를 사용해 스크래치 거리 3 mm (스크래치 속도 16.7 μm/sec)에 대해 수직 하중을 1에서 50 N까지 선형적으로 증가시키며 실시하였다. 이때 접촉면에 작용하는 최대접촉압력은 Hertzian 접촉이론을 적용한 결과, 하중 50 N에서 약 15.25 GPa로 계산되었다. 각 스크래치 시험 사이의 간격은 이미 생성된 스크래치 트랙으로부터의 영향을 방지하기 위해 압입자의 반경의 약 10배 간격을 두고 진행하였고, 결과의 신뢰성과 재현성을 파악하기 위해 모든 시편에서 5번의 스크래치 시험을 진행하였다. 스크래치 시험 후 스크래치 트랙의 파손 모드는 전계방사형 주사전자현미경(FE-SEM, JEOL, JSM-6700F)을 이용해 관찰하였고, 스크래치 트랙의 손상부의 화학적 조성을 분석하기 위해 에너지 분산 분광기(EDS, NORAN-System-Six, THERMO Ltd.)를 이용하였다.
3. 시험 및 고찰
3.1 3D-Profiler를 이용한 표면 분석 결과
증착된 박막의 표면 거칠기 분석을 위해 3D-Profiler (Bruker, Dektak-XTA)를 이용하였다. 각 시편마다 세 군데 다른 위치에서 50 × 50 μm 면적을 측정하였으며, RMS (Root-Mean-Square) 거칠기인 Rq값의 평균을 구하였다. 측정 결과는 Fig. 4에 제시한 바와 같이 Ru-SDC 0, 10, 50과 100의 Rq 값의 평균은 각각 1.24, 1.59, 1.56과 1.26 nm로 측정되어 선단반경 200 μm인 다이아몬드 압입자의 스케일을 고려할 때 시편들의 표면거칠기가 스크래치 시험 결과에 미치는 영향은 무시할 정도로 작다.
3.2 스크래치 시험 결과
각 박막들의 스크래치 시험 결과로 스크래치 거리(선형적 하중 증가)에 따른 마찰계수 변화와 스크래치 트랙에 대한 광학현미경 사진을 Fig. 5에 함께 제시하였다. 다섯 번의 시험 결과가 모두 유사한 결과를 보여 본 시험이 신뢰성 있는 결과를 제시함을 확인하였다. 임계하중은 마찰계수가 급격히 변하거나 다른 유형을 보이기 시작하는 시점에 해당하는 하중일 가능성이 매우 크나 스크래치 트랙을 광학현미경과 FE-SEM으로 추가 분석하여 균열이 처음 발생하는 위치에 해당하는 하중으로 지정한다. Fig. 5에는 임계하중의 위치를 마찰계수 변화값 위에 붉은 화살표로 표시하였으며, 각 트랙에 발생하는 탄성변형 구간과 소성변형 구간을 각 그림의 전자현미경 사진 상부에 각각 푸른색 화살표와 붉은색 화살표로 각각 표시하였다. 탄성변형 구간은 압입자가 지나간 후 압입자에 의해 눌러진 표면이 탄성 복원되는 구간이다. 이 구간에선 압입자와의 마찰접촉에 의해 형성된 미세한 미끄럼 흔적만이 광학현미경 사진상에 검출되며 SEM 관찰에서도 미세한 미끄럼 흔적만이 흐리게 보인다. 소성 변형 구간은 압입자에 의해 눌러진 표면이 압입자가 지나간 후에 복원되지 않는 구간으로서 광학현미경 사진상에 비교적 선명한 검은 흔적으로 관측된다. 마찰계수의 변화를 살펴보면 각 박막의 파손 이전의 마찰계수의 평균은 각각 0.29, 0.14, 0.10, 0.08로 계산되어 시편의 SDC 부피 비율이 0에서 100%로 증가함에 따라 마찰계수가 감소하였다. 따라서 증착층 내의 SDC의 함유량의 변화가 마찰계수 감소 경향과 직접적인 싱관관계가 있음을 알 수 있다. 스크래치 트랙에 대한 광학현미경 사진은 각 박막의 파손 모드와 임계하중을 결정하기엔 해상도가 충분치 않으나 대체적인 스크래치 거동을 파악하는 데에는 도움이 된다. Ru-SDC 10과 Ru-SDC 100 박막의 스크래치 흔적을 보면 표면층의 탄성변형 구간이 매우 짧았고 소성변형 구간으로 급격히 전환하였으며, 특히 임계하중이 작아 이 두 박막의 스크래치 저항성이 Ru-SDC 00과 Ru-SDC 50에 비해 현저히 떨어짐을 알 수 있다. 각 박막의 임계하중의 변화는 증착층의 SDC 함유 비율이 증가할 때 마찰계수가 감소하는 것과는 달리 SDC 함유율에 직접적으로 비례하지 않았다. Fig. 1의 박막 단면을 보면 Ru-SDC 100과 Ru-SDC 10 박막의 조밀성이 다른 두 박막보다 낮아 이것이 작은 임계하중을 보인 주요 원인으로 작용한 것으로 판단된다. 특히 Ru-SDC 50 박막은 상당히 조밀한 구조를 가지고 있어 가장 큰 임계하중을 보이고 있는 것으로 판단된다.
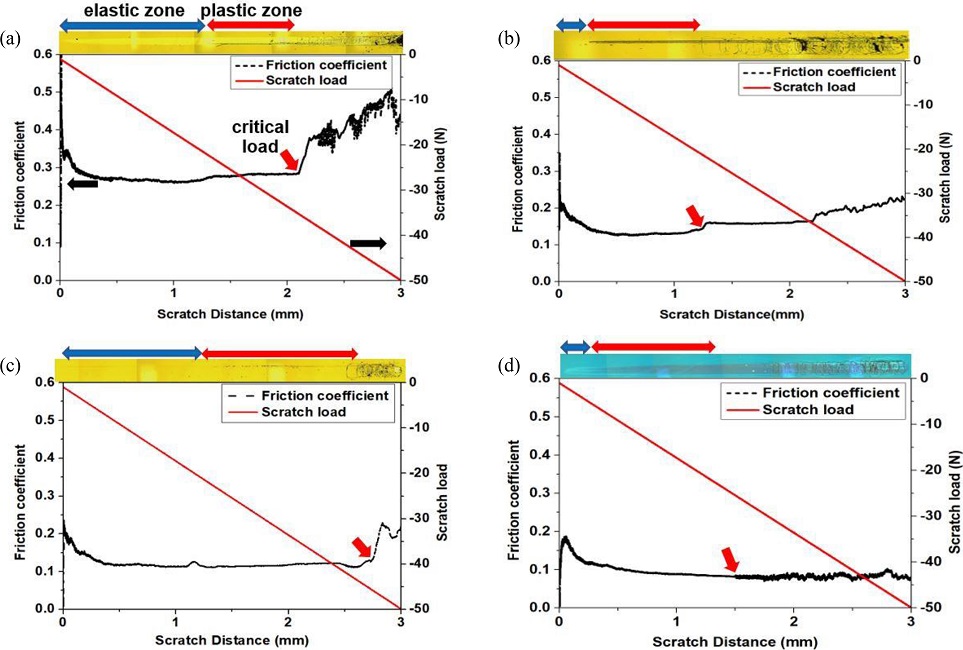
Optical images of scratch tracks and friction coefficient with linear scratch load for (a) Ru-SDC 0, (b) Ru-SDC 10, (c) Ru-SDC 50, and (d) Ru-SDC 100
스크래치 트랙에 대한 FE-SEM을 이용한 분석은 임계하중의 결정과 파손 모드의 규명에 필수적이다. Fig. 6은 각 박막의 스크래치 트랙에 대해 균열이 시작하는 지점부터 균열의 성장과 전파, 박막 일부분의 탈착(Chipping-Off)이 발생하는 과정을 보여주는 FE-SEM 사진이다. 스크래치 표면의 마찰계수의 변화와 FE-SEM을 통해 종합해 분석한 결과에 의하면 SDC 조성 비율과 관계없이 모든 박막이 동일하게 마찰계수가 급격하게 변화하는 하중에서 박막 표면에서 인장균열(Tensile Crack)이 시작되었다. 이때의 하중을 임계하중으로 정의하며 이 하중이 시편 박막의 스크래치 저항 성능을 대변하게 된다. Ru-SDC 0, 10, 50과 100의 임계하중은 각각 35.8, 21.5, 45.4와 26.7 N으로 Ru-SDC 50이 가장 높은 임계하중을 보이고 있다. 이는 Fig. 1과 관련해 앞에서 기술한 바와 같이 Ru-SDC 50이 다른 세 박막보다 월등히 조밀한 구조를 가지고 있어 기공성이 매우 낮아 균열 생성이 다른 박막들보다 높은 하중에서 발생하는 것으로 보인다. Fig. 6을 보면 모든 Ru-SDC 박막의 균열 유형은 크게 두 가지로서, 헤르쯔균열(Hertz Crack)과 컨포멀균열(Conformal Crack)이 발생하고 있다. 두 균열 모두 박막 표면에 작용하는 인장응력의 세기가 커짐에 따라 이로 인해 발생하는 균열(Tensile Cracks)로 분류되긴 하나 생성 메카니즘은 서로 다르다. 헤르쯔균열은 압입자의 뒷부분(Trailing Edge)에 발생하는 반경 방향 인장응력(Tensile Radial Stress)에 의해 균열이 표면에서 발생하여 하중에 증가됨에 따라 박막 내부로 퍼져 내려가게 된다. 스크래치 트랙 표면에는 Fig. 6에 표시한 것과 같이 압입자 진행 반대 방향으로 돌출하는 원호(Circular Arc) 형상의 균열이 발생한다. 스크래치가 계속 진행되어 하중이 증가하게 되면 균열의 발생 빈도와 크기도 증가하게 되고 각 균열들이 서로 만나 네트워크(Crack Network)를 형상하게 된다. 균열이 더욱 심해지면 박막을 관통해 기판 경계면(Through-Thickness Cracks)까지 도달하여 칩핑(Chipping)이 발생하게 되며 박막 일부가 기판에서 탈착하게 된다. 컨포멀균열은 압입자 앞쪽에 있는 박막의 표면부 일부가 압입자의 진행에 의해 밀려 휘어지고 이때 발생하는 인장응력에 의해 Fig. 6에 “Conformal Cracks”으로 표시한 바와 같이 균열의 형태가 압입자 진행 방향으로 돌출하는 원호 형상을 띤다. 스크래치 트랙상의 균열과 균열 네크워크 그리고 칩핑이 발생했을 때의 해당 부위의 화학조성은 EDS 분석을 통해 확인할 수 있다.
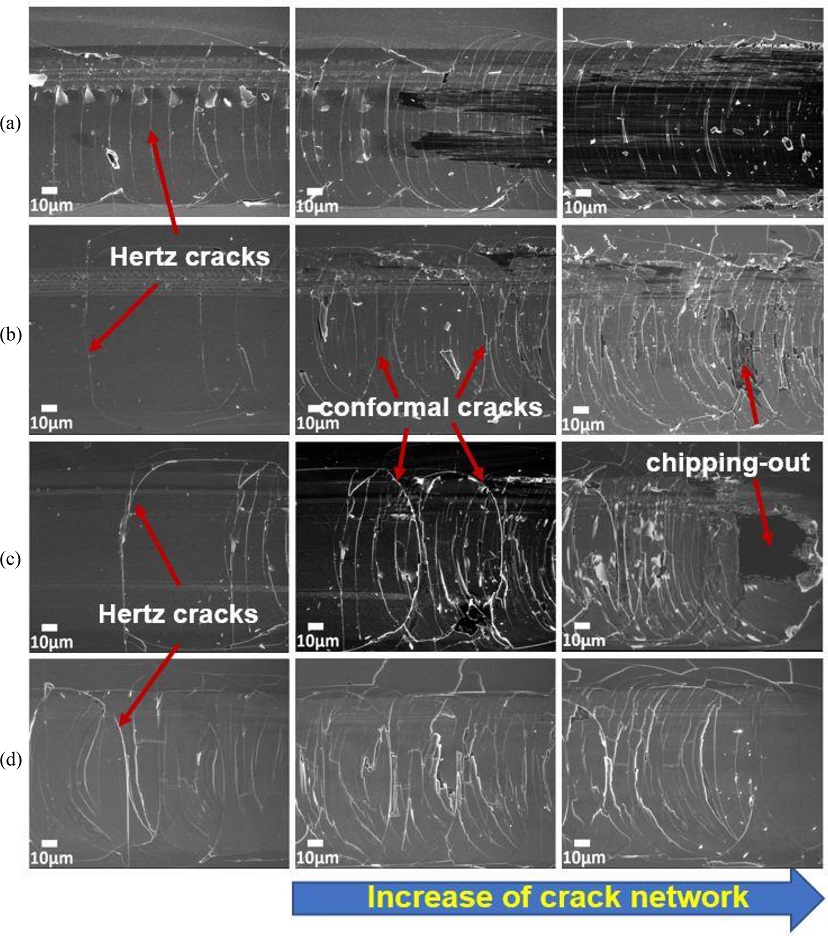
FE-SEM images of scratch tracks after initiation of cracks (a) Ru-SDC 0, (b) Ru-SDC 10, (c) Ru-SDC 50, and (d) Ru-SDC 100
Fig. 7에는 Ru-SDC-50 박막에 발생한 균열 네트워크와 칩핑을 고배율로 소개하였다. 다른 박막들에서도 거의 동일한 형태로 박막 일부가 파손되는 것을 관찰할 수 있었다. Ru-SDC 50 박막의 스크래치 트랙에서 대표적인 부위 네 군데에 대한 EDS 분석 결과를 Fig. 8에 소개하였다. 칩핑이 발생한 부위인 Point 1, 균열들이 교차하며 표면에 추가 손상이 감지된 Point 2, 균열이 발생하기 이전의 손상 없는 부분인 Point 3과 헤르쯔균열이 잘 발달해 있는 Point 4 지역에서 분석을 실시하였다. 칩핑이 발생한 Point 1 부분에서는 Fig. 7(b)에 예시된 것처럼 박막 일부가 제거되어 기판이 드러났기 때문에 기판의 주성분인 Si의 비율(81.90 Atomic %)이 인장균열이 일어나기 전인 Point 3의 68.87%보다 매우 높게 검출되었고, 박막층의 성분 원소들(Ru, Ce, Sm)의 비율 또한 감소한 것을 확인할 수 있었다. Point 2에서는 박막의 두께 일부가 제거되어 단순히 헤르쯔균열만 발생한 Point 4에 비해 Si의 비율이 높으며 이는 기판과 박막의 계면까지 균열이 전파하지 않고, 박막층의 내부에서 파손되어 두께의 일부가 손실된 응착파손(Cohesive Failure)으로 분류할 수 있다.
4. 결론
본 연구에서는 루테늄과 사마리아가 도핑된 세리아(SDC) 서멧 구조 박막(Ru-SDC)을 대상으로 박막층 조성 변화에 따른 스크래치 저항 성능을 비교평가하고 파손 모드를 규명하고자 하였다. FE-SEM을 이용한 박막층의 단면 관찰, 스크래치 거리에 따른 마찰계수 변화와 임계하중의 측정을 통해 사마리아가 도핑된 세리아의 부피 비율이 50%인 박막의 스크래치 저항 성능이 가장 우수함을 알 수 있어 특정한 조성 비율에서 서멧 구조의 응착 특성이 향상됨을 밝힐 수 있었다. 한편 박막의 SDC 조성 비율의 증가는 마찰계수 감소에 직접적으로 기여하였다. 스크래치 트랙에 대한 FE-SEM 분석을 통해 본 연구에서 조사한 모든 박막 시편의 파손 모드는 압입자 뒷부분에 발생하는 인장응력에 의한 헤르쯔균열이 먼저 시작하고 뒤이어 압입자 앞 쪽에서 발생하는 인장응력에 의한 컨포멀균열이 추가되며 하중의 지속적 증가는 균열 밀도의 증가와 균열의 전파를 통해 균열네트워크를 형성하게 되고 기판까지 균열이 침투한 경우 박막이 칩핑되어 기판에서 기판에서 탈착하는 파손 모드로 진행됨을 규명하였다.
루데늄과 사마리아가 도핑된 세리아의 특정한 조성 비율에서 우수한 응착 특성을 가짐을 보인 본 연구 결과와 나노스케일 박막에 대한 스크래치 시험법의 적용은 향후 고체연료전지 분야의 박막 개발 연구에 좋은 자료로서 활용될 것으로 기대된다.
Acknowledgments
이 연구는 서울과학기술대학교 교내 학술연구 지원비로 수행되었습니다.
REFERENCES
-
Hei, M., Chen, H., Yi, J., Lin, Y., Lin, Y., et al., (1998). CO2-reforming of methane on transition metal surfaces. Surface Science, 417(1), 82-96.
[https://doi.org/10.1016/S0039-6028(98)00663-3]
-
Qin, D., & Lapszewicz, J., (1994). Study of mixed steam and CO2 reforming of CH4 to syngas on MgO-supported metals. Catalysis Today, 21(2-3), 551-560.
[https://doi.org/10.1016/0920-5861(94)80179-7]
-
Bebelis, S., Neophytides, S., Kotsionopoulos, N., Triantafyllopoulos, N., Colomer, M., et al., (2006). Methane oxidation on composite ruthenium electrodes in YSZ cells. Solid State Ionics, 177(19-25), 2087-2091.
[https://doi.org/10.1016/j.ssi.2006.02.014]
-
Hibino, T., Hashimoto, A., Yano, M., Suzuki, M., & Sano, M., (2003). Ru-catalyzed anode materials for direct hydrocarbon SOFCs. Electrochimica Acta, 48(17), 2531-2537.
[https://doi.org/10.1016/S0013-4686(03)00296-2]
-
Kim, K., Yoo, J. D., Lee, S., Bae, M., Bae, J., et al., (2017). A simple descriptor to rapidly screen Co oxidation activity on rare-earth metal-doped CeO2: From experiment to first-principles. ACS Applied Materials & Interfaces, 9(18), 15449-15458.
[https://doi.org/10.1021/acsami.7b01844]
-
Mosqueda, B., Toyir, J., Kaddouri, A., & Gélin, P., (2009). Steam reforming of methane under water deficient conditions over gadolinium-doped ceria. Applied Catalysis B: Environmental, 88(3-4), 361-367.
[https://doi.org/10.1016/j.apcatb.2008.11.003]
-
Kašpar, J., Fornasiero, P., & Graziani, M., (1999). Use of CeO2-based oxides in the three-way catalysis. Catalysis Today, 50(2), 285-298.
[https://doi.org/10.1016/S0920-5861(98)00510-0]
-
Murray, E. P., Tsai, T., & Barnett, S. A., (1999). A direct-methane fuel cell with a ceria-based anode. Nature, 400(6745), 649-651.
[https://doi.org/10.1038/23220]
-
Lim, Y., Lee, H., Hong, S., & Kim, Y.-B., (2019). Co-sputtered nanocomposite nickel cermet anode for high-performance low-temperature solid oxide fuel cells. Journal of Power Sources, 412, 160-169.
[https://doi.org/10.1016/j.jpowsour.2018.11.025]
-
Dharini, T., Kuppusami, P., Panda, P., Ramaseshan, R., & Kirubaharan, A. K., (2020). Nanomechanical behaviour of Ni-YSZ nanocomposite coatings on superalloy 690 as diffusion barrier coatings for nuclear applications. Ceramics International, 46(15), 24183-24193.
[https://doi.org/10.1016/j.ceramint.2020.06.198]
-
Liu, Z., Zhang, F., Rui, N., Li, X., Lin, L., et al., (2019). Highly active ceria-supported Ru catalyst for the dry reforming of methane: In situ identification of Ruδ+-Ce3+ interactions for enhanced conversion. ACS Catalysis, 9(4), 3349-3359.
[https://doi.org/10.1021/acscatal.8b05162]
-
Ruiz Puigdollers, A., Schlexer, P., Tosoni, S., & Pacchioni, G., (2017). Increasing oxide reducibility: The role of metal/oxide interfaces in the formation of oxygen vacancies. ACS Catalysis, 7(10), 6493-6513.
[https://doi.org/10.1021/acscatal.7b01913]
-
Takagi, Y., Adam, S., & Ramanathan, S., (2012). Nanostructured ruthenium-gadolinia-doped ceria composite anodes for thin film solid oxide fuel cells. Journal of Power Sources, 217, 543-553.
[https://doi.org/10.1016/j.jpowsour.2012.06.060]
-
Kim, H. J., Kil, M. J., Lee, J., Yang, B. C., Go, D., et al., (2021). Ru/Samaria-doped ceria gradient cermet anode for direct-methane solid oxide fuel cell. Applied Surface Science, 538, 148105.
[https://doi.org/10.1016/j.apsusc.2020.148105]
-
Bull, S., & Rickerby, D., (1990). New developments in the modelling of the hardness and scratch adhesion of thin films. Surface and Coatings Technology, 42(2), 149-164.
[https://doi.org/10.1016/0257-8972(90)90121-R]
-
Perry, A. (1981). The adhesion of chemically vapour-deposited hard coatings to steel the scratch test. Thin Solid Films, 78(1), 77-94.
[https://doi.org/10.1016/0040-6090(81)90419-3]
-
Lee, H., Coutu, R. A., Mall, S., & Leedy, K. D., (2006). Characterization of metal and metal alloy films as contact materials in MEMS switches. Journal of Micromechanics and Microengineering, 16(3), 557.
[https://doi.org/10.1088/0960-1317/16/3/011]
-
Hartmanová, M., Navrátil, V., Buršíková, V., Kundracik, F., & Mansilla, C., (2011). Effect of crystallographic structure on electrical and mechanical characteristics of Sm2O3-doped CeO2 films. Russian Journal of Electrochemistry, 47(5), 505-516.
[https://doi.org/10.1134/S1023193511050041]
-
Singh, J., & Wolfe, D. E., (2005). Review nano and macro-structured component fabrication by electron beam-physical vapor deposition (EB-PVD). Journal of Materials Science, 40(1), 1-26.
[https://doi.org/10.1007/s10853-005-5682-5]
-
Amirzada, M. R., Tatzel, A., Viereck, V., & Hillmer, H., (2016). Surface roughness analysis of SiO2 for PECVD, PVD and IBD on different substrates. Applied Nanoscience, 6(2), 215-222.
[https://doi.org/10.1007/s13204-015-0432-8]
B.Sc. in the Department of Manufacturing Systems and Design Engineering, Seoul National University of Science & Technology. His research interest is tribololgy.
E-mail: jkid959thie@gmail.com
Ph.D. candidate in the Department of Nano-Bio Engineering, Seoul National University of Science & Technology. His research interest is SOFC/ALD.
E-mail: hyongjunekim@seoultech.ac.kr
Professor in the Department of Manufacturing Systems and Design Engineering, Seoul National University of Science & Technology. His research interest is SOFC/ALD.
E-mail: jihwanan@seoultech.ac.kr
Professor in the Department of Manufacturing Systems and Design Engineering, Seoul National University of Science & Technology. His current interest is scanning probe microscopy and the evaluation of tribological and mechanical properties of nanoscale thin films.
E-mail: hsahn@seoultech.ac.kr