
유리렌즈 성형 금형에서 방열블록 형상에 따른 금형 가열부의 열전달 특성 연구
Copyright © The Korean Society for Precision Engineering
This is an Open-Access article distributed under the terms of the Creative Commons Attribution Non-Commercial License (http://creativecommons.org/licenses/by-nc/3.0) which permits unrestricted non-commercial use, distribution, and reproduction in any medium, provided the original work is properly cited.
Abstract
The purpose of this study is to propose a better contact surface pattern of a heat radiating block in a progressive GMP (Glass Molding Process) heating assembly. In this study, a simulation model based on FEM was developed to perform a thermal analysis for the heating assembly. It was verified by comparing experimental results. The temperature distribution on the heating block surface and heating energy consumption was analyzed with the change of contact surface pattern and area of a heat radiating block. The considered pattern on the contact surface was cross (+) and straight (-) shape. The contact area ratio was changed from 16 to 100%. The simulation results show that the heating energy consumption increased to reach a target temperature with the increase of contact area ratio. The straight-shaped patterns on a heat radiating block presented more uniform temperature distribution on the mold heating surface than the cross shaped surface, whereas it resulted in a slightly higher energy consumption of up to 9%. This study shows that the contact surface pattern on a heat dissipating block can control the temperature distribution on the mold heating surface.
Keywords:
Finite element analysis, Glass molding process, Heating energy consumption, Heat radiating block, Mold heating, Temperature distribution키워드:
유한요소해석, 유리 성형 공정, 가열 에너지 소비, 방열블록, 금형가열, 온도 분포1. 서론
최근 로봇, 자율주행, 안면 인식 등의 다양한 IT 분야에서 영상 데이터를 활용하는 기술 발전이 계속되고 있으며, 이러한 디지털 영상을 얻기 위한 디지털 카메라나 캠코더에 사용되는 초정밀 광학 렌즈의 수요가 증가하고 있다. 초정밀 광학 렌즈는 초고속 통신장치, 광학 기기에도 활용되므로 다양한 산업에서 그 수요가 꾸준히 발생하는 부품이다. 렌즈는 형상에 따라 다양한 종류가 존재하지만, 최근에는 촬영 이미지나 광통신 특성이 구면의 수차로 인해 저하되는 것을 방지할 수 있는 비구면 렌즈가 많이 사용되고 있다[1]. 유리 재질의 비구면 렌즈는 과거 절삭, 연삭과 같은 가공에 의해 제작되어 우수한 광학 성능을 갖고 있음에도 양산성이 크게 감소하는 문제가 있었다. 하지만 저융점 유리 소재의 개발과 초정밀 금형 제작이 가능하게 되면서 고온 고압의 조건에서 유리를 압축 성형하여 생산성을 높이는 GMP (Glass Molding Process) 공정이 많이 활용되고 있다[2]. GMP 공정에는 크게 다수의 캐비티를 갖는 금형을 질소로 충전된 챔버 내에서 가열, 압축, 냉각을 순차적으로 수행하는 일괄처리(Batch) 방식과 유리렌즈의 금형이 일정한 가열 온도와 프레스 압력으로 설정된 스테이지를 따라 이송하는 순차이송(Progressive) 방식이 있다. 일반적으로 좀 더 높은 생산성을 갖는 순차이송 방식의 GMP 공정이 많이 활용되고 있으며 이에 대한 기존의 연구가 존재한다.
기존의 연구를 살펴보면 비구면 형상오차를 일으키는 요인에 대해 분석하고 최적성형의 조건을 분석한 연구[3], 렌즈 성형 시스템 구축을 위해 금형의 열전달 효율 향상을 위한 설계기술 연구[4], GMP 공정에서 유리 표면 무결성을 분석하기 위해 가열시간에 따른 곡면 유리 표면 온도 분포와 응력 분포 변화를 예측하고, 실험을 통해 성형 온도가 유리 성형에 중요한 영향을 미치는 것을 확인한 연구[5], GMP 공정에 사용되는 금형의 열응력에 관한 연구[6], GMP 공정 과정에서 성형 대상 렌즈 재질의 최소 가열 시간과 프레스 과정 중 렌즈의 응력 분포를 예측한 연구[7] 등이 있다.
위에서 언급한 것과 같이 기존의 연구는 GMP 공정의 주목적인 렌즈의 성형과 관련된 금형 설계, 렌즈 성형 특성, 성형 조건 등에 대해 집중적으로 이루어졌음을 보여준다. 그러나 순차이송 GMP 공정을 구현하는 가열부 등의 장비는 렌즈성형을 구현하는 중요한 장치임에도 불구하고, 이에 대한 연구는 거의 이루어지지 않았음을 알 수 있다. 따라서 본 연구에서는 GMP 공정에서 각 스테이지의 온도 조건을 유지하도록 하는 가열 어셈블리에 대한 열해석을 수행하고자 하였다. 이를 위해 먼저 가열 어셈블리를 실험장치로 구현하고, 실험을 통해 얻은 데이터와 이를 유한요소법으로 모델링한 해석 결과를 비교하여 해석 모델을 검증하였다. 검증된 해석 모델을 활용하여 가열부와 냉각부 사이에 삽입되어 열전달 역할을 수행하는 방열블록이 가열 어셈블리의 온도 분포에 미치는 영향을 고찰하였다. 이를 위해 방열블록의 접촉부 형상과 접촉면적을 변경하며 시뮬레이션을 수행하였고, 이러한 형상 변화가 가열 접촉부의 온도 분포 균일도와 히터의 전기 에너지 소비에 미치는 영향을 분석하여 방열블록 형상설계에 유용한 정보를 제공하고자 하였다.
2. 가열 어셈블리 모델 및 실험
2.1 가열 어셈블리 구조
Fig. 1은 가열 어셈블리의 구조이다. 가열 어셈블리 순차이송방식의 GMP 공정을 구성하는 하나의 스테이지를 제공하며 Fig. 1의 가열블록 표면에 렌즈를 성형하는 금형이 놓이게 된다. 금형을 기준으로 상부와 하부에 독립적으로 가열 어셈블리가 대칭으로 존재하게 되며 상부에는 가압을 위한 장치가 추가로 설치된다. 렌즈의 성형을 온도 조건을 상하부 가열 어셈블리로 제어하고 가압 장치로 성형을 수행한다. 따라서 가열 어셈블리는 금형과 닿는 표면에서 균일한 온도 분포를 유지하면서도 온도 유지를 위한 전력의 소비는 되도록 작게 하는 것이 필요하다.
Fig. 1에서 가열 어셈블리는 크게 네 가지의 블록으로 구성되며 어셈블리 전체에 열량을 공급해주는 가열블록, 가열블록에서 다른 블록으로의 열전달을 조절하기 위한 방열블록, 가열 어셈블리를 구성하는 여러 개의 블록을 고정시켜주는 고정블록, 어셈블리를 냉각시키기 위한 냉각블록이 그것이다. 가열블록에는 6개의 카트리지 히터가 삽입되며 냉각블록 내부에는 ‘ㄹ’자의 냉각유로가 가공되어 있어 20°C의 냉각수가 흐른다.
방열블록은 가열 어셈블리에서 가열블록에서 발생된 열이 적절하게 냉각블록으로 전달되도록 하는 역할을 한다. 방열블록의 표면에는 형상이 존재하며 이러한 요철의 형상과 접촉면적에 따라 가열블록의 온도 분포 및 가열 시 필요한 전력량 등이 변화하게 된다. 본 연구에서는 이러한 방열블록의 형상의 영향을 고찰하고자 하였다.
이를 위해 현재 공정에서 사용되고 있는 Fig. 1의 (+)자형 방열블록을 기준으로 다양한 표면 패턴을 모델에 적용하고자 하였으며, 그 형상들은 Fig. 2에 제시되었다. 방열블록의 형상은 방열블록과 가열블록의 마주보는 전체 면적 대비 비율이 16%인 기존 (+)자형 방열블록 형상을 기준으로 접촉비율이 각각 2배와 3배인 32와 48%를 갖는 (+)자형 방열블록을 해석 모델에 적용하였다. 또한 방열블록의 가공성을 고려하여 (-)자형 패턴을 갖는 방열블록을 적용하였으며 접촉비율은 동일하게 16, 32, 48%로 설계하였다. 또한, 방열블록의 요철 유무에 따른 열전달 특성을 비교하기 위하여 패턴이 없는 접촉비율이 100%인 방열블록을 적용하여 해석을 수행하였다. Fig. 2에서 (+)는 (+)자형 패턴을, (-)는 (-)자형 패턴을 갖는 방열블록을 의미한다.
2.2 열전달 해석
GMP 렌즈 성형 장비를 구성하는 어셈블리의 온도 분포를 확인하기 위한 열전달 해석을 수행하였다. 열전달 해석은 ANSYS Workbench 2021 R1을 이용하여 과도열전달 해석(Transient Heat Transfer Analysis) 방법을 활용하여 수행되었다. 가열에 따른 물성치 변화는 다양한 자료의 값을 적용하였으며[8-10], 온도의 변화에 대한 재료의 상태량 변화도 해석 과정에서 고려되었다. 해석에서 사용된 주요 재료가 갖는 100°C 조건에서 물성치는 Table 1과 같다. STS310S는 가열블록과 방열블록에 사용되었으며, STS304는 고정블록과 냉각블록에 사용되었다. 실험용 챔버는 SM45C 재질을 적용하였다.
열전달 해석에서 실제 공정과 유사한 조건을 모델링하기 위해서는 공급된 히터의 열량, 질소와 냉각수의 온도와 대류 열전달계수, 각 블록간 접촉 열저항 등의 경계 조건을 고려해야 한다. 냉각 유로 내 대류 열전달계수는 식(1)의 원형관 내 난류 유동식인 Dittus-Bolter 방정식으로부터 계산되었다. 챔버 내 어셈블리에서 발생하는 자연대류의 대류 열전달계수는 수직면의 경우 Churchill and Chu [11]의 상관식(식(2))과 Lloyd and Lewandowski[12]에 의해 제시된 상관식(식 (3)과 식(4))을 사용하여 계산하였다. 도출된 경계 조건은 Table 2와 같으며, 기존 금형 온도 분포에 대한 연구[13,14]에서 제시된 범위인 5-20 W/m2·K 내에 포함 되는 값임을 확인하였다. 어셈블리를 구성하는 각 블록 사이의 접촉면에서 발생하는 열저항은 8 × 10−4 m2·K/W로 고려되었으며, 이 값은 Fig. 2의 16% 접촉면을 갖는 (+)자형 방열블록을 적용하여 수행된 가열 실험에서 정상 상태 조건의 가열블록 내부 한 지점의 측정 온도를 정확하게 예측하도록 해석 모델을 이용하여 계산된 값이다. 해당 열저항값은 Babu [15]가 제시한 Stainless Steel 재질의 접촉 열저항값인 2.74 × 10−4-26.10 × 10−4 m2·K/W의 범위에 존재하였다. Table 2는 검증 실험을 모사하기 위해 입력된 경계 조건을 보여준다.
(1) |
(2) |
(3) |
(4) |
2.3 실험 장치 및 조건
본 연구에서는 해석 모델의 경계 조건 도출과 시뮬레이션 결과를 검증하기 위한 실험 장치를 제작하였다. Figs. 3(a)와 3(b)는 실험용 챔버 외부 형태와 내부 가열 어셈블리를 보여준다. Fig. 3(c)는 장치 전체의 개념도이다. GMP 공정과 유사한 환경의 구현을 위해 챔버 내부에 질소를 주입하고 냉각수 순환을 위한 항온조 등이 연결되어 있음을 보여준다. Fig. 3(b)에서 보여주는 것과 같이 가열블록에는 K-Type의 열전대를 14 mm의 깊이로 삽입하였으며, 해당 위치의 측정된 온도와 동일 지점에 대한 시뮬레이션 예측 온도를 비교하여 해석 모델의 검증을 수행하였다. 실험에서 사용된 방열블록은 (+)자형 요철부를 가지며, 방열블록의 가열블록 및 고정블록과의 접촉비율은 16%이다.
실험 진행 중 실험용 챔버 내부에 질소를 주입하여 가열 어셈블리 및 내부 구조의 산화를 방지하였으며, 장치의 냉각을 위해 20°C의 냉각수를 2 L/min의 유량으로 공급하였다. 카트리지 히터는 가열을 위해 1.365 kW의 전력을 공급하였고, Fig. 3(b)의 측정 지점에서의 온도는 357°C에서 정상 상태에 도달하였다.
실험에서 사용한 측정 장치의 사양과 정확도는 Table 3에 제시되었다. 냉각유로의 입/출구 온도는 T-Type 열전대로 측정하였으며, 질소 온도 변화는 K-Type 열전대로 측정하였다. 냉각수와 챔버 내 질소의 압력 측정을 위해 정밀 압력계를 설치하였으며, 냉각수의 유량은 체적유량계로 측정하였다.
3. 해석 결과
3.1 해석 모델의 검증
Fig. 4는 해석 결과를 검증하기 위해 Fig. 3(b) 지점에서 측정된 가열블록 심부 온도와 동일 지점에서 열전달 해석을 결과를 비교한 그래프이다. Fig. 4가 보여주는 것과 같이 예측된 온도는 실험에서 측정된 온도와 비교하여 시간에 따른 온도가 계속하여 변하는 과도 상태에서 9.5°C 이내 정상 상태에서 2.9°C 이내의 오차를 보여 해석 모델이 실험의 측정온도를 정확히 예측하고 있음을 보여준다. 이때 정상 상태는 10분간 온도의 변화가 1°C 이내인 상태로 고려하였고, 정상 상태에서 측정된 가열블록 심부의 온도는 357.8°C, 예측된 온도는 360.7°C였다. 가열 중 온도가 상승하는 과도 상태에서 측정된 온도와 해석 모델의 예측 온도에는 약간의 차이가 발생하고 있다. 가열 과정에서 가열 블록을 구성하는 부품은 열변형량이 달라지며, 부품이 생산 공정에서 움직이지 않도록 고정되어 있어 수직 방향의 열변형량은 접촉 열저항값에 약간의 변화를 줄 것으로 예상된다. 해석 모델에서 고려된 열저항은 정상 상태 기준의 상수값이므로 가열 과정에서 실험과 해석 모델의 작은 차이가 과도 상태 온도 예측 오차의 원인으로 판단된다.
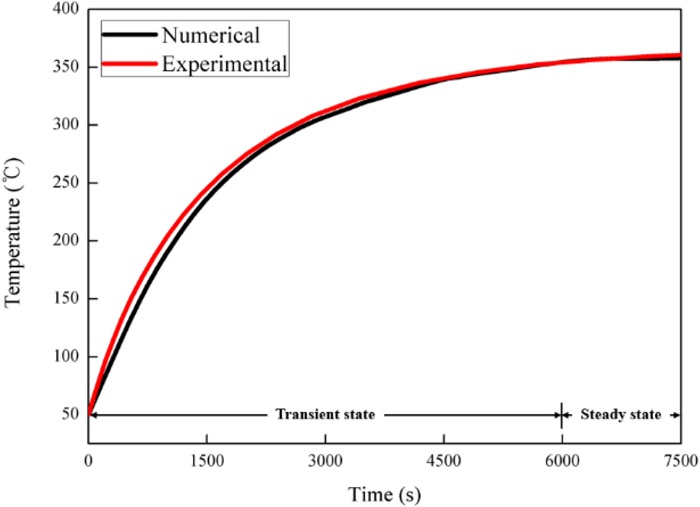
Temperature comparison between measurement and simulation results at the location of a heating block
Fig. 5는 해석 모델에 의한 가열 어셈블리의 온도 분포를 보여주고 있다. 냉각수가 흐르는 냉각블록의 온도가 가장 낮고, 히터가 장착된 가열블록의 온도가 가장 높음을 보여주고 있다. 가열블록과 고정블록 사이에 위치한 방열블록은 고온의 가열블록과 저온의 고정 및 냉각블록을 적절히 분리하는 역할을 한다. 이러한 분리를 통해 접촉부의 수직 방향으로 급격한 온도변화를 방지하여 가열블록 내부에서 비교적 균일한 온도 분포를 유지하도록 하며, 과도한 냉각으로 인해 히터가 필요 이상의 높은 전력을 소비하는 것을 막는다.
Fig. 5에서 가열블록이 상대적으로 낮은 온도를 갖는 부분은 Fig. 2의 (+)자형 방열블록이 가열블록과 접촉하는 면과 일치하고 있음을 확인할 수 있다. Figs. 5(a)와 5(b)는 각각 가열시작 후 1,500초와 7,500초 경과 후 가열 어셈블리의 전체적인 온도 분포를 보여준다. 시간의 경과에 따라 각 지점에서의 온도 절댓값에는 차이가 존재하지만 온도 분포의 경향에는 큰 차이가 없음을 알 수 있다. 따라서 가열이 진행되는 동안 유사한 온도분포를 가지면서 가열 어셈블리의 온도가 상승한다고 예상할 수 있다.
3.2 모델을 활용한 방열블록 형상에 따른 가열 특성과 소비 에너지 비교
전술한 것과 같이 GMP 공정에서는 가열에 필요한 전력량과 가열블록 윗면 금형과 접촉하는 부분에서의 고른 온도 분포가 중요하다. 본 연구에서는 Fig. 2에서 제시하였던 다양한 방열블록 형상과 접촉면적 조건에서 어셈블리의 열전달 특성에 대한 과도 열전달 해석을 수행하였으며 형상 변화가 필요 전력량과 온도 분포에 미치는 영향을 고찰하였다. 목표온도는 온도 측정부에서 약 577°C로 설정하였다[16]. 시뮬레이션 과정에서 가열블록의 온도가 목표온도에 도달하도록 히터에 공급되는 전력값을 조절하였다. Fig. 6은 목표온도에 도달하는데 필요한 전력값을 보여준다.
Fig. 6에서 보여주는 것과 같이 목표온도에 도달하기 위한 히터의 전력은 방열블록의 접촉면적에 크게 좌우됨을 알 수 있다. 이는 접촉면적이 증가할수록 접촉부의 열저항이 감소하여 가열블록의 히터에서 발생된 열이 냉각블록으로 원활하게 전달되기 때문이다. 필요 전력값을 좀더 세부적으로 살펴보면 접촉면적 비율이 16% 방열블록에서는 (-)자형이 (+)자형 형상에 비해 더 많은 전력을 필요로 한다 반면에 접촉면적 비율이 32, 48%인 경우 (+)자형 방열블록이 (-)자형 방열블록보다 높은 전력을 필요로 한다. 이론적으로 본다면 유사한 접촉면적을 갖는다면 필요 전력에는 큰 차이가 없어야 한다. 이러한 결과는 가열블록 전체의 온도 편차가 커지면서 발생한 것이다. 시뮬레이션 결과에 따르면 (+)자형 방열블록은 접촉면적의 비율이 높아짐에 따라 (-)자형 방열블록에 비해 가열블록 상부의 온도 편차가 증가하였다. 온도 편차가 증가하면 측정부의 온도는 가열블록 표면과 그 차이가 커져 원하는 가열 표면의 온도 제어가 어렵게 된다. 이는 따라서 정확한 표면 온도의 제어를 위해 가열블록의 고른 온도 분포가 중요함을 확인할 수 있으며, 되도록 표면에서 가까운 부위의 온도를 측정하거나 다수의 지점에서 온도를 측정하여 히터의 제어 입력변수로 활용해야 함을 보여준다.
Fig. 7은 가열블록에 다른 형상을 갖는 방열블록이 적용되는 경우 시간 경과에 따라 목표온도인 577°C에 도달하는 과정을 보여주고 있다. 전술한 것과 같이 방열블록의 접촉면적이 증가 할수록 목표온도에 도달하기 위한 전력은 커야 하므로 그 결과 방열블록에 패턴이 없는 경우(접촉면적 비율 100%)에 온도가 가장 급격하게 증가하고 있음을 알 수 있으며, 접촉면적의 비율이 낮아질수록 필요 전력과 승온속도가 감소하고 있음을 알 수 있다.
Fig. 8은 특정 온도에 도달하는 시점에서 히터가 소비한 전력량을 표시한 그래프이다. 가열블록이 400°C에 도달한 시점에서 히터의 전력 소비량은 접촉면적 비율이 100%인 경우를 제외하고는 큰 차이가 없음을 보여준다. 접촉면적 비율이 100%인 경우에는 목표온도에 도달하기 위해서 시간당 전력소비가 커 빠르게 온도상승이 이루어지지만 냉각블록으로 빠져나가는 열전달 역시 크기 때문에 특정 온도에 도달하기 위한 전력 소비량을 보면 패턴을 갖는 방열블록을 적용한 경우보다 크다는 것을 알 수 있다. 500°C에 도달한 조건에서는 소비 전력량이 접촉면적 비율이 48에서 16%로 감소함에 따라 역시 감소하고 있음을 보여주고 있으며 감소율은 (-)자형 방열블록에서 최대 9.0%, (+)자형 방열블록에서 최대 6.2%였다. 동일 접촉면적비를 갖는 경우 (+)자형 방열블록은 (-)자형 방열블록에 비해 3.8-8.7% 낮은 에너지를 소비하면서 500°C에 도달하는 결과를 보여주었다. 접촉면적이 동일한 경우에도 해당 조건에 도달하는 에너지 소비량이 다르다는 것은 접촉 부위에서 평균온도의 차이가 방열블록의 형상에 따라 다르기 때문이며, 이는 가열블록의 온도 분포가 방열블록의 형상에 영향을 받기 때문이다. 575°C에 도달하는 경우 정상 상태에 거의 가까워지기 때문에 도달하는 시간에서 큰 차이는 없게 된다. 그 결과 소비하는 전력량은 Fig. 6의 요구전력에 유사한 시간이 곱해지므로 575°C에 도달 시 소비 전력량은 요구전력과 유사한 경향을 갖게 된다.
3.3 방열블록 형상에 따른 가열블록 온도 분포 비교
방열블록의 형상은 가열블록의 온도 분포와 가열에 필요한 전력 소비량에 영향을 준다. 특히 가열블록 상부의 온도 분포균일도는 렌즈가 성형되는 금형과 직접 접촉하기 때문에 렌즈의 품질에도 매우 중요한 영향을 미친다. GMP 공정에서 활용되는 렌즈 성형용 원통형 금형의 지름을 120 mm라 가정하고, 가열블록 상부 표면의 120 mm 지름의 가상 원 내부 온도 분포를 해석결과를 활용하여 분석하였다. Fig. 9는 각 가열 시작 이후 시간에서 금형과 접촉하는 부분에서의 평균온도와 최대 및 최소온도값을 보여준다.
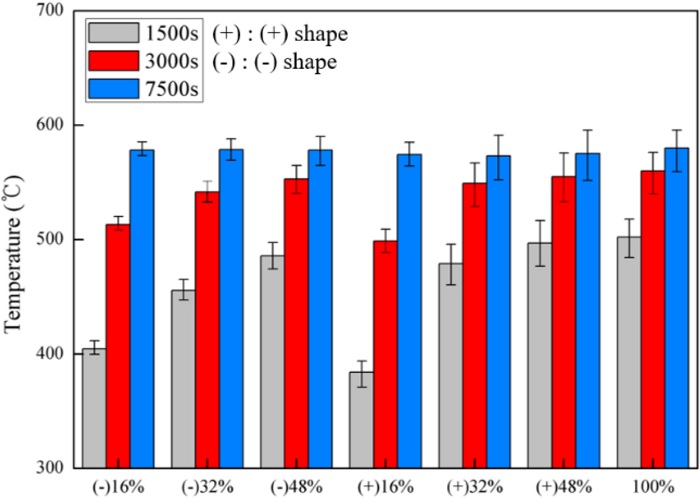
Heat radiating block pattern effect on heating block surface average, maximum and minimum temperature
Fig. 9에서 표면의 평균온도는 접촉면적의 비율이 증가함에 따라 커지지만 그 차이는 시간이 경과함에 따라 감소하고, 정상 상태에서는 거의 동일한 온도를 갖는다. 정상 상태인 7,500초 조건에서 분석된 표면에서의 최대온도와 최소온도의 차이는 (-)자형 방열블록의 경우 12.0-25.0°C, (+)자형 방열블록에서는 20.7-38.7°C의 범위를 보였으며, 접촉면적의 비율이 작을수록 최대온도와 최소온도 차는 감소하는 경향을 보였다. 패턴이 없는 방열블록에서 정상 상태 최대온도와 최소온도 차는 36.6°C였다. Table 4는 가열블록 표면의 지름 120 mm 가상 원 안쪽 영역에서 최대온도와 최소온도의 차이를 보여준다. 한 가지 흥미로운 점은 (+)자형 방열블록이 갖는 특징이다. Figs. 8과 9 그리고 Table 4에서의 결과를 보면 에너지 소비량을 감소시키는 측면에서는 (+)자형 방열블록이 장점을 가질 수 있으나 접촉면적비가 커지는 경우 오히려 패턴이 없는 방열블록보다 온도의 불균일도가 심해진다. 따라서 (+)자형 방열블록을 사용하는 경우 패턴의 형상 설계와 접촉면적비에 따라 가열 특성이 크게 달라짐을 알 수 있다.
Figs. 10(a)와 10(b)는 가열 시작 후 각각 3,000초와 7,500초 이후 시점에서 가열블록 표면의 온도 분포를 보여주고 있으며, 지름이 120 mm인 검은색 원 안쪽은 렌즈 성형을 위한 원통형 금형이 접촉하는 부분이다. 온도의 절댓값에서 차이가 존재하지만 각 시점에서 동일 방열블록 형상에 대해 온도 분포는 유사한 패턴을 보임을 알 수 있으며, 이는 가열 과정에서 표면의 온도 분포가 유지되며 온도가 상승한다는 것을 보여준다. 이러한 경향은 Table 4의 각 시점에서 최소온도와 최대온도의 차이가 거의 같다는 결과를 통해서도 확인이 가능하다.
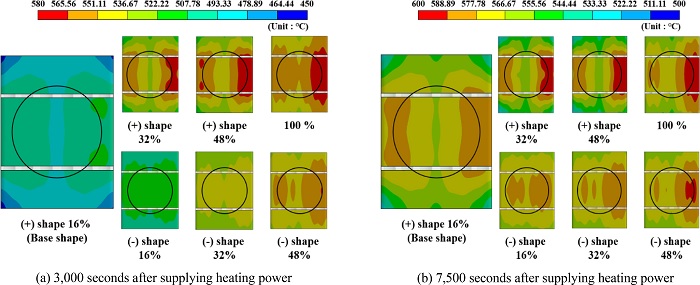
Temperature distribution contours at the heating block surface with different heat radiating block shapes
Fig. 10은 방열블록의 형상이 가열블록 표면에서 온도 분포에 상당한 영향을 미치고 있음을 보여준다. Figs. 2에 제시된 방열블록의 형상과 10의 온도 분포를 비교하여 보면 (+)자형 패턴을 갖는 경우 열이 방열블록의 모서리 근처와 가로, 세로의 중심선 부분으로 많이 전달된다. 따라서 Fig. 10에서 가열블록의 표면온도가 모서리 부분과 세로 중심선 부분에서 상대적으로 낮다는 것을 보여준다. 하지만 (-)자형 패턴의 방열블록의 경우에는 (+)자형 패턴의 방열블록에서 보이는 온도의 불균일 분포는 보이지 않고, 상대적으로 양호한 온도 균일 분포를 갖는다는 것일 알 수 있다. 모든 패턴에서 방열블록의 접촉면적비가 높을수록 표면에서 온도 균일도는 낮아지게 되는데 이는 방열블록을 통해 열전달이 커지면서 그 효과가 온도의 불균일 분포를 유도하기 때문으로 판단된다.
Fig. 11은 방열블록의 형상에 따른 가열 어셈블리에서 열유속 분포를 보여준다. (+)자형 패턴을 갖는 방열블록은 가열블록과 고정블록에 대한 접촉부가 모서리와 가로와 세로 방향 중심선 부분에 분포하므로 해당 부위에서 열유속이 집중적으로 발생하게 되며, 이러한 열유속의 분포는 가열블록 내부에서 온도가 불균일하게 분포하게 하는 원인이 된다. (-)자형 패턴의 경우에는 세로 방향으로 접촉부가 비교적 고르게 분포하기 때문에 동일한 면적비를 갖는 경우에도 (+)자형 패턴을 갖는 방열블록에 비해 집중된 열유속이 발생하지 않음을 알 수 있다. 방열블록의 접촉면적 비율이 높아지면 열유속은 감소하고, 열전달 발생 면적이 증가하고 있음을 Fig. 11을 통해 확인할 수 있다.
4. 요약 및 결론
본 연구에서는 유리렌즈 성형을 위한 GMP 공정용 가열 어셈블리에 대한 열해석을 수행하였다. 이를 위해 해석을 위한 모델을 개발하고 구축된 실험 장치의 측정값과 비교를 통해 모델을 검증하였다. 검증된 모델을 활용하여 가열블록과 고정블록을 사이에 위치하는 방열블록의 접촉 형상과 면적이 일정온도에 도달하기 위해 필요한 가열 에너지와 가열블록 표면의 온도 분포에 미치는 영향을 분석하였으며 이를 통해 얻어진 주요 결론은 다음과 같다.
(1) 목표온도에 도달하기 위한 히터의 요구 전력은 방열블록의 접촉면적의 증가에 따라 비례하였으며, 높은 발열에 의해 초기 온도 증가율 역시 높았다.
(2) 특정 온도에 도달하는데 필요한 소비 전력량은 패턴이 없은 방열블록에서 가장 높았으며, (+)자형 방열블록은 (-)자형 방열블록에 비해 동일한 접촉면적 비율에서 더 낮은 에너지 소비량을 보였으나 그 차이는 최대 9% 이내였다.
(3) 가열블록 표면에서 최대온도와 최소온도의 차이는 접촉면적 비율의 증가에 따라 증가하였으며 (-)자형 방열블록이 (+)자형 방열블록에 대해 더 낮은 온도 차이를 갖도록 하여 균일한 온도 분포 형성이 가능함을 보였다.
(4) (+)자형 방열블록은 일부 접촉면적 비율 조건에서 패턴이 없는 방열블록에 비해 더 높은 온도 불균일 분포를 보여주었다.
본 연구를 통해 방열블록은 가열블록의 온도 분포와 가열에 필요한 에너지 소비량을 결정하는 중요한 부품임을 확인하였으며, 접촉위치와 면적, 접촉부의 형상 설계를 통해 가열 표면의 온도 분포를 변화시킬 수 있음을 알 수 있었다. 이러한 방열블록의 특징을 파악한다면 다양한 응용분야에서 원하는 가열블록의 온도 분포 구현에 활용이 가능할 것으로 예상된다.
Acknowledgments
본 연구는 산업통상자원부의 재원으로 한국산업기술평가관리원(산업기술혁신사업, No. 20010775)의 지원으로 수행되었으며, 이에 감사드립니다.
REFERENCES
-
Park, K., Joo, W., (2008), Numerical evaluation of a plastic lens by coupling injection molding analysis with optical simulation, Japanese Journal of Applied Physics, 47(11R), 8402.
[https://doi.org/10.1143/JJAP.47.8402]
-
Zhou, T., Yan, J., Yoshihara, N., Kuriyagawa, T., (2010), Study on nonisothermal glass molding press for aspherical lens, Journal of Advanced Mechanical Design, Systems, and Manufacturing, 4(5), 806-815.
[https://doi.org/10.1299/jamdsm.4.806]
-
Jung, T.-S., Park, K.-S., Yoon, G.-S., (2011), A study on the optimal molding conditions for aspheric glass lenses in progressive GMP, Journal of the Korea Academia-Industrial Cooperation Society, 12(3), 1051-1057.
[https://doi.org/10.5762/KAIS.2011.12.3.1051]
- Kuk, K.-H., Kim, G.-S., Jung, D.-Y., (2011), Development of a convective sequential production system for aspheric lens, Journal of the Korean Society for Precision Engineering, 28(2), 202-210.
-
Zhang, Z., Yang, W., Ming, W., Yin, L., Liao, D., Zhang, G., (2021), Surface integrity analysis of ultra-thin glass molding process, Ceramics International, 47(21), 30584-30597.
[https://doi.org/10.1016/j.ceramint.2021.07.236]
- Lee, Y.-M., Chang, S.-H., Heo, Y.-M., Shin, K.-H., Yoon, G.-S., Jung, T.-S., (2008), Thermal stress analysis for an aspheric glass lens mold, Journal of the Korean Society for Precision Engineering, 25(12), 125-131.
-
Yan, J., Zhou, T., Masuda, J., Kuriyagawa, T., (2009), Modeling high-temperature glass molding process by coupling heat transfer and viscous deformation analysis, Precision Engineering, 33(2), 150-159.
[https://doi.org/10.1016/j.precisioneng.2008.05.005]
- The Enginnering Tool Box, Stainless steel AISI 310-Property.
-
Feli, S., Aalami Aaleagha, M., Foroutan, M., Borzabadi Farahani, E., (2012), Finite element simulation of welding sequences effect on residual stresses in multipass butt-welded stainless steel pipes, Journal of Pressure Vessel Technology, 134(1), 011209.
[https://doi.org/10.1115/1.4004571]
- MatWeb, JIS S45C steel, normalized.
-
Churchill, S. W., Chu, H. H., (1975), Correlating equations for laminar and turbulent free convection from a vertical plate, International Journal of Heat and Mass Transfer, 18(11), 1323-1329.
[https://doi.org/10.1016/0017-9310(75)90243-4]
-
Radziemska, E., Lewandowski, W., (2001), Heat transfer by natural convection from an isothermal downward-facing round plate in unlimited space, Applied Energy, 68(4), 347-366.
[https://doi.org/10.1016/S0306-2619(00)00061-1]
-
Oh, S. A., Ko, Y. B., Cha, B. S., Park, K., (2020), A study on thermal and flow characteristics of an injection mold using a detachable core module with embedded heating, Journal of the Korean Society for Precision Engineering, 37(5), 371-379.
[https://doi.org/10.7736/JKSPE.020.002]
-
Kim, J. H., Yi, D.-E., Jang, J. H., Lee, M. S., (2015), Deformation analysis considering thermal expansion of injection mold, Transactions of the Korean Society of Mechanical Engineers A, 39(9), 893-899.
[https://doi.org/10.3795/KSME-A.2015.39.9.893]
- Babu, K. N., (2015)., Thermal contact resistance: Experiments and simulation, M.Sc. Thesis, Chalmers University of Technology.
- Lee, Y. M., Chang, S. H., Heo, Y. M., Shin, G. H., Jung, T. S., Kim, D. S., (2007), A study on thermal deformation of the glass lens mold used in progressive GMP process through a thermal stress analysis, Proceedings of the Fall Conference on the Korean Society of Manufacturing Technology Engineers, 55-60.
M.Sc. candidate in the Department of Mechanical Design and Robot Engineering, Seoul National University of Science & Technology. Her research interest is experimental and numerical heat transfer.
E-mail: boromin116@gmail.com
CTO in R&D Center of Daeho Technology Korea Co., Ltd.. His research interest is thermoforming equipment and F. A. system.
E-mail: dongyean@daehoteck.co.kr
Professor in the Department of Mechanical System Design Engineering, Seoul National University of Science & Technology. His research interest is finite element analysis of manufacturing processes.
E-mail: kpark@seoultech.ac.kr
Professor in the Department of Mechanical System Design Engineering, Seoul National University of Science & Technology. His research interest is heat transfer and energy system analysis.
E-mail: cypark@seoultech.ac.kr