
PCD 공구를 이용한 초경합금의 V자형 미세 채널 가공
Copyright © The Korean Society for Precision Engineering
This is an Open-Access article distributed under the terms of the Creative Commons Attribution Non-Commercial License (http://creativecommons.org/licenses/by-nc/3.0) which permits unrestricted non-commercial use, distribution, and reproduction in any medium, provided the original work is properly cited.
Abstract
Microchannels machining can be used to make micro molds for microfluidic chips. The fluid flow in the channel can be controlled, by changing the cross sectional shape of the channel. V-shaped channels with a specific angle are not easily made with the etching process. This study presents the mechanical machining of microchannels of V-shaped cross section, on cemented carbide (WC-Co). In this study, to reduce tool wear in the process of machining, the micro conical tool was fabricated using polycrystalline diamond (PCD). The tool wear of the conical tool and form accuracy of channels, were investigated during V-shaped microchannel machining.
Keywords:
Micro channel, Cemented carbide, Micro tool, Micro machining, Wire electro-discharge grinding키워드:
미세 채널, 초경합금, 미세 공구, 미세 가공, 와이어 방전 연삭1. 서론
바이오 의료 진단이나 약물의 화학적 분석 및 합성 등에서 널리 이용되고 있는 미세 유체 디바이스(Microfluidic Devices)는 유체가 이동하는 미세 채널이나 홈, 구멍 등이 복잡하게 구성되어 있다[1,2]. 미세 유체 디바이스의 미세 채널에서 발생하는 관성 집중(Inertial Focusing) 현상은 미세 유체의 이동, 혼합, 집중 및 분리 등에 응용될 수 있으며, 이와 같은 현상은 채널의 단면 형상에 많은 영향을 받는다[3]. 특히, 삼각형 단면의 미세채널은 관성 집중 현상을 효과적으로 조작하는데 용이하며 작은 크기의 입자를 높은 효율로 집중시킬 수 있어 채널 병렬화에 적합한 단면 형상이다[4-6]. 따라서 입자의 혼합, 분리 등을 효율적으로 제어하기 위해 임의의 경사각을 갖는 삼각형 단면의 채널을 제작할 필요성이 있다.
에칭(Etching)은 미세 채널 형상 가공에 많이 사용하는 방법 중 하나이다. 에칭을 이용하면 실리콘 웨이퍼나 유리 재료에 마이크로나 나노 크기의 채널을 쉽게 가공할 수 있다[7,8]. 하지만 에칭을 이용한 가공 방법은 특정 각도의 경사면만 가공할 수 있다는 단점이 있다.
펨토초 레이저(Femtosecond Laser) 가공은 유리와 같은 취성 재료에 크랙 발생 없이 빠른 속도로 미세 채널을 가공할 수 있다[9]. 하지만 이 방법은 비용이 비싸고 채널 단면 형상의 정밀도가 떨어진다는 단점이 있다.
미세 공구를 이용한 기계적 가공은 상대적으로 우수한 표면 조도와 높은 치수 정밀도를 가진 가공 방법이다. 특히 특정한 각도를 가진 공구를 사용함으로써 다양한 채널 형상을 가공할 수 있다[1]. 채널 형상이 가공된 초경합금은 폴리머나 유리 소재의 미세 칩 제작을 위한 몰드로 사용될 수 있다. 초경합금은 다른 금속재료에 비해 취성(Brittleness)이 높기 때문에 기계적 가공에서 버(Burr)의 발생이 거의 없고 깨끗한 가공면을 얻을 수 있다[10]. 다만 초경합금의 경도가 매우 높기 때문에 공구의 파손이나 마모가 크게 발생하며, 이를 해결하기 위해 다이아몬드 소재의 공구 제작이 필요하다[11-13]. 최근, 다결정 다이아몬드(Polycrystalline Diamond, PCD) 공구를 이용한 초경합금의 미세 형상 가공에 대한 연구가 보고되었다. Nakamoto 등은 와이어 방전 가공(Wire Electrical Discharge Machining, WEDM)을 이용하여 제작한 PCD 밀링 공구로 초경합금에 사각 단면의 미세 홈을 가공하였다[11]. 가공 길이에 따른 공구 마모량 증가와 마모로 인한 표면 조도 변화를 관찰하였다. Fujita 등은 PCD 다이싱 블레이드(Dicing Blade)를 이용하여 초경합금에 폭 20 μm, 깊이 1 mm와 50 μm의 미세 홈 어레이를 가공하였으며 블레이드의 마모를 포함한 가공 특성에 대해 연구하였다[12].
본 연구에서는 초경합금에 V자형 미세 채널을 가공하기 위해 원뿔형 PCD 공구를 제작하였으며 초경합금 가공 시 가공 길이에 따른 공구 마모와 그로 인한 채널의 형상 오차에 대해 분석하였다.
2. 실험 방법
Fig. 1은 실험에서 사용된 가공 시스템의 모습을 나타낸 사진이다. 가공 시스템은 3축으로 구성된 스테이지로 정밀 이송이 가능하며, 최대 60,000 rpm의 스핀들을 장착하였다. 본 연구에서는 공구 재료로서 PCD 소재를 사용하였으며 와이어 방전 연삭(Wire Electro Discharge Grinding, WEDG)을 이용하여 미세 공구를 제작하였다[14-17]. 와이어 방전 연삭 시스템은 모터, 롤러, 보빈, 와이어 가이드로 구성하였다. 와이어 전극으로는 직경 200 μm의 황동 와이어를 사용하였고, 와이어 가이드의 마모를 줄이기 위해 알루미나 소재의 와이어 가이드를 사용하였다[18]. Fig. 1과 같이 공구를 제작하기 위한 방전 연삭 시스템 바로 옆에 가공물을 부착하여 공구 제작 후 바로 채널 가공을 수행하였다.
Fig. 2는 PCD 미세 공구 제작 과정을 나타낸 그림이다. 와이어 방전 연삭은 방전 시 발생하는 열로 재료를 제거하기 때문에 정밀한 치수 제어를 위해서 낮은 소재 제거율(Material Removal Rate, MRR)로 가공할 필요가 있다. 원뿔형 미세 공구는 황삭(Roughing)과 정삭(Finishing) 과정을 거쳐 제작하였다. 지름 1 mm의 PCD 환봉을 제작하고자 하는 공구 각도에 맞춰 원통형 형상으로 황삭 가공하였다. 정삭은 미세 공구를 원뿔형으로 만들기 위해 각 축의 모터를 제어하여 필요한 각도의 원뿔형 공구를 제작하였다. 방전 가공을 이용한 미세 공구 제작에서 와이어를 공구 아래쪽에서 위쪽 방향으로 이송하는 경우, 약 10 μm 이하의 날카로운 공구 끝부분에서 방전 집중 현상으로 인해 끝이 뭉툭하게 가공되는 현상이 발생할 수 있다. 따라서 정삭 가공 시, 공구 끝에 과다 방전 집중을 피하기 위해서 공구의 위쪽에서 아래쪽 방향으로 와이어를 이송시켜 공구를 제작하였다.
Fig. 3은 와이어 방전 연삭으로 제작한 미세 공구의 SEM 사진이다. 평균 입자 크기 1 μm의 다결정 다이아몬드를 사용하였으며 와이어를 일정 각도로 이동시켜 60도의 경사각을 갖는 공구를 제작하였다. 방전 가공 조건으로 인가전압은 100 V, 축전 용량은 1,000 pF을 사용하였으며 날 끝 반경은 약 5 μm 내외이다[19,20].
본 실험에서 사용된 가공물 재료는 초경합금이며, 기계적 성질은 Table 1에 나타내었다.
3. 실험 결과
3.1 V자형 미세 채널 가공
앞서 제작한 PCD 미세 공구를 이용하여 Fig. 4(a)와 같이 초경합금에 V자형 미세 채널을 가공하였다. 미세 공구 표면에 방전 가공으로 생긴 방전흔(Crater)이 절삭날 또는 연삭 입자 역할을 하며, 공구의 고속 회전을 통한 연삭 가공 형태로 재료를 제거한다. 가공물의 표면에서부터 공구를 깊이 방향으로 5 μm씩 절입시키며 초경합금을 가공하였고, 이를 12번 반복하여 최종적으로 60 μm 깊이의 채널을 가공하였다. 미세 채널의 가공 조건은 Table 2에 표시하였다. 알루미늄이나 스테인리스 강의 가공에서는 일반적으로 모서리 부분에 많은 버가 발생하지만 초경합금의 경우 재료의 취성 성질로 인해 버(Burr)가 관찰되지 않았으며 치핑(Chipping)도 발생하지 않았다. 이는 정밀한 미세몰드 제작에 큰 장점이 된다. 다만 초경합금은 매우 높은 경도를 지니기 때문에 다른 금속에 비해 공구 마모가 크게 발생하며, 그로 인해 대략 10 μm 폭의 평평한 바닥면이 형성되었다. Fig. 4(b)는 가공된 미세 채널의 3차원 형상을 나타내며 공초점 현미경(OLS-5000, Olympus Co., Japan)으로 측정하였다.
3.2 가공 특성
원뿔형 PCD 공구를 이용하여 초경합금에 지그재그 형태의 미세 채널을 가공하였다. 공구 마모를 고려하여, 황삭으로 깊이 50 μm의 미세 채널을 제작한 뒤, 와이어 방전 연삭 장치에서 공구를 재가공(Dressing)하였다. 그다음 깊이 방향으로 5 μm씩 절입시키며 2회 정삭 가공하여 총깊이 60 μm의 채널을 제작하였다. Figs. 5(a)와 5(b)는 미세 채널의 전체적인 모습과 채널 모서리 부분을 확대한 사진이다. 채널의 크기는 가로 800, 세로 600 μm이며 채널의 총길이는 3.2 mm이다. 바닥면의 폭은 공구의 마모로 인해 대략 12.28 μm으로 측정되었다. 초경합금의 높은 경도로 인해 가공 길이가 늘어남에 따라 공구 마모 발생은 크게 증가했고, 미세 채널의 시작점에 비해 끝점의 바닥면은 대략 10 μm 이상 증가했다. 또한 바닥면의 표면 거칠기가 증가하였고 채널 벽면의 거칠기가 증가하였다. 가공 도중에 와이어 방전 연삭으로 공구를 재가공할 수 있기 때문에 공구 마모로 인한 문제는 줄일 수 있을 것으로 보여 추가적인 연구가 필요하다. Fig. 5(c)는 가공한 채널의 단면 프로파일을 나타낸 것이다. 공구 마모로 인해 미세 채널의 바닥면이 평평한 형상으로 가공된 것을 확인할 수 있다.
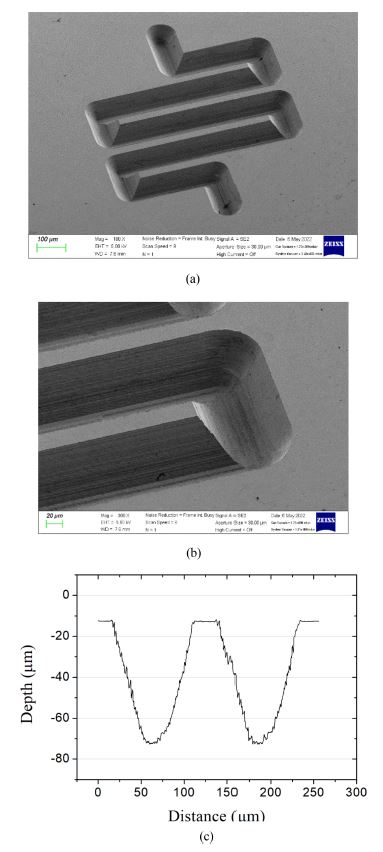
V-shaped microchannel machined on cemented carbide (a) SEM image, (b) Enlarged view, and (c) Cross-sectional profile of channels
Fig. 6(a)는 V자형 채널 벽면의 절삭흔을 확대한 사진이다. 초경합금 입자가 가공된 것을 확인할 수 있으나 공구 마모로 인해 그 면이 매끄럽지 못한 것을 알 수 있다. Fig. 6(b)는 V자형 미세채널의 바닥면을 확대한 사진이다. 바닥면의 경우 공구의 절삭 속도가 매우 작고, 공구 마모가 가장 심한 곳이므로 절삭보다는 바닥을 문지르면서 가공이 된 것이 보인다. 바닥면의 표면 거칠기(Surface Roughness)는 약 0.060 μm Ra로 측정되었다.
3.3 공구 마모 특성
초경합금의 기계적 가공 시, 가공 길이에 따라 발생하는 원뿔형 PCD 공구 마모를 확인하였다. 가공 길이를 1,000, 2,400, 10,000 μm로 설정하여 공구 끝과 가공된 채널을 관찰하였다. 공구 마모는 공구의 SEM 사진과 가공된 채널의 바닥면 너비를 측정하여 확인하였다. 가공 길이 1,000에서는 바닥면 너비가 대략 10 μm로 초기 공구 날 끝 반지름을 고려하면 마모가 거의 발생하지 않았다. Fig. 7은 가공 길이 2,400과 10,000 μm에서의 PCD 공구 끝의 SEM 사진이다. Fig. 7(a)와 같이 가공 길이 2,400 μm에서 공구의 바닥면과 옆면에서 기계적 마찰로 인한 공구의 부분적 파손과 공구 마모가 발생했음을 확인할 수 있다. 가공 길이 10,000 μm에서는 Fig. 7(b)와 같이 공구 마모가 크게 발생하였으며, 날 끝의 형태가 평평하게 변한 것을 알 수 있다.
Figs. 8(a)와 8(b)는 가공 길이 2,500과 10,000 μm에서의 채널 단면 사진이다. 가공 길이가 증가할수록 공구 끝의 마모로 인해 채널 바닥면의 너비가 증가하는 것을 확인할 수 있다. Fig. 9는 가공 길이에 따른 바닥면 너비의 변화를 그래프로 나타낸 것이다. 가공 길이가 증가함에 따라 바닥면 너비가 증가하여, 가공 길이 10,000에서 바닥면 너비는 23.5 μm로 확인하였다. 높은 경도의 초경합금 가공에서는 공구 마모가 심하게 발생하고 이러한 공구 마모는 채널 형상 정밀도에 부정적인 영향을 미치기 때문에 채널 가공 도중에 공구를 재가공하는 방식을 고려할 수 있다.
4. 결론
본 연구에서는 와이어 방전 연삭으로 다결정 다이아몬드 소재의 원뿔형 미세 공구를 제작하여 초경합금에 미세 채널을 가공하였다. 공구 표면에 방전 가공으로 생긴 미세한 돌기로, 특별한 절삭날이 없이 초경합금을 가공할 수 있는 것을 확인하였으며 초경합금의 취성 성질로 인해 버가 없는 깨끗한 모서리를 얻을 수 있었다. 가공 길이에 따라 공구 끝부분의 마모가 증가하는 것을 확인할 수 있으며 대략 가공 길이가 10 mm 일 때, 공구 끝의 폭이 10에서 25 μm로 증가하는 것을 확인하였다. 이는 공구 끝의 절삭 속도가 매우 낮기 때문이며 공구 회전 속도, 이송 속도, 절입량에 따라 달라질 수 있기 때문에 추가적인 연구가 필요하다. 마모된 공구는 가공 시스템에 장착된 와이어 방전 연삭 장치로 다시 재가공할 수 있으며 가공 영역이 매우 작기 때문에 재가공 시간도 수 분 정도로 오래 걸리지 않는다. 따라서 공구의 재가공 공정을 효율적으로 적용하여 보다 높은 형상 정밀도와 표면 품질의 초경합금을 가공할 수 있을 것으로 판단된다.
Acknowledgments
이 연구는 2020년도 산업통상자원부 및 산업기술평가관리원(KEIT) 연구비 지원에 의한 연구임(No. 20010984).
REFERENCES
-
Hwang, J., Cho, Y. H., Park, M. S., Kim, B. H., (2019), Microchannel fabrication on glass materials for microfluidic devices, International Journal of Precision Engineering and Manufacturing, 20(3), 479-495.
[https://doi.org/10.1007/s12541-019-00103-2]
-
Kim, C. M., Kim, G. M., (2022), Development of multilayered droplet splitting microfluidic system for preparation of microdroplet, Journal of the Korean Society for Precision Engineering, 39(6), 425-431.
[https://doi.org/10.7736/JKSPE.022.015]
-
Amini, H., Lee, W., Di Carlo, D., (2014), Inertial microfluidic physics, Lab on a Chip, 14(15), 2739-2761.
[https://doi.org/10.1039/c4lc00128a]
-
Kim, J.-A., Lee, J., Wu, C., Nam, S., Di Carlo, D., Lee, W., (2016), Inertial focusing in non-rectangular cross-section microchannels and manipulation of accessible focusing positions, Lab on a Chip, 16(6), 992-1001.
[https://doi.org/10.1039/C5LC01100K]
-
Mukherjee, P., Wang, X., Zhou, J., Papautsky, I., (2019), Single stream inertial focusing in low aspect-ratio triangular microchannels, Lab on a Chip, 19(1), 147-157.
[https://doi.org/10.1039/C8LC00973B]
-
Tang, W., Fan, N., Yang, J., Li, Z., Zhu, L., Jiang, D., Shi, J., Xiang, N., (2019), Elasto-inertial particle focusing in 3D-printed microchannels with unconventional cross sections, Microfluidics and Nanofluidics, 23(3), 1-10.
[https://doi.org/10.1007/s10404-019-2205-2]
-
Xu, B.-Y., Yan, X.-N., Zhang, J.-D., Xu, J.-J., Chen, H.-Y., (2012), Glass etching to bridge micro- and nanofluidics, Lab on a Chip, 12(2), 381-386.
[https://doi.org/10.1039/C1LC20741E]
-
Lee, D.-K., Kwon, J. Y., Cho, Y. H., (2019), Fabrication of microfluidic channels with various cross-sectional shapes using anisotropic etching of Si and self-alignment, Applied Physics A, 125(5), 1-7.
[https://doi.org/10.1007/s00339-019-2600-2]
-
Bulushev, E., Bessmeltsev, V., Dostovalov, A., Goloshevsky, N., Wolf, A., (2016), High-speed and crack-free direct-writing of microchannels on glass by an IR femtosecond laser, Optics and Lasers in Engineering, 79, 39-47.
[https://doi.org/10.1016/j.optlaseng.2015.11.004]
-
Wu, X., Li, L., He, N., Zhao, G., Shen, J., (2019), Investigation on the surface formation mechanism in micro milling of cemented carbide, International Journal of Refractory Metals and Hard Materials, 78, 61-67.
[https://doi.org/10.1016/j.ijrmhm.2018.09.001]
-
Nakamoto, K., Katahira, K., Ohmori, H., Yamazaki, K., Aoyama, T., (2012), A study on the quality of micro-machined surfaces on tungsten carbide generated by PCD micro end-milling, CIRP annals, 61(1), 567-570.
[https://doi.org/10.1016/j.cirp.2012.03.112]
-
Fujita, T., Izumi, Y., Watanabe, J., (2019), Ultra-fine grooving technology with high aspect ratio for cemented carbide by PCD (poly-crystalline diamond) blade, Precision Engineering, 55, 381-389.
[https://doi.org/10.1016/j.precisioneng.2018.10.006]
-
Park, J. A., Lee, U. S., Kim, B. H., (2020), Micro pin fabrication of tungsten carbide using polycrystalline diamond, Journal of the Korean Society for Precision Engineering, 37(11), 791-796.
[https://doi.org/10.7736/JKSPE.020.085]
-
Masuzawa, T., Fujino, M., Kobayashi, K., Suzuki, T., Kinoshita, N., (1985), Wire electro-discharge grinding for micro-machining, CIRP Annals, 34(1), 431-434.
[https://doi.org/10.1016/S0007-8506(07)61805-8]
-
Lee, E. S., Yang, C. Y., Lee, J. H., Kim, B. H., (2021), Micro drilling of single crystal SiC using polycrystalline diamond tool, Journal of the Korean Society for Precision Engineering, 38(7), 471-478.
[https://doi.org/10.7736/JKSPE.021.013]
- Doan, C. X., Kim, B.-H., Chung, D.-K., Chu, C.-N., (2011), Fabrication of PCD micro tool and its hybrid micro machining, Journal of the Korean Society for Precision Engineering, 28(6), 694-700.
-
Moon, I. Y., Kim, B. H., (2013), Micro machining of titanium alloy using polycrystalline diamond tools, Journal of the Korean Society for Precision Engineering, 30(3), 284-291.
[https://doi.org/10.7736/KSPE.2013.30.3.284]
-
Na, Y., Kim, B. H., (2019), Effect of vibration and machining area in the fabrication of micro tool by reverse EDM, Journal of the Korean Society for Precision Engineering, 36(2), 169-175.
[https://doi.org/10.7736/KSPE.2019.36.2.169]
-
Lee, P. A., Kim, Y., Kim, B. H., (2015), Effect of low frequency vibration on micro EDM drilling, International Journal of Precision Engineering and Manufacturing, 16(13), 2617-2622.
[https://doi.org/10.1007/s12541-015-0335-3]
-
Park, J. W., Chung, D. K., Kim, B. H., Ok, J. G., Kim, W. J., Kim, Y. H., Chu, C. N., (2012), Wire electrical discharge machining of carbon nanofiber mats for field emission, International Journal of Precision Engineering and Manufacturing, 13(4), 593-599.
[https://doi.org/10.1007/s12541-012-0076-5]
M.S. student in the Department of Mechanical Engineering, Soongsil University. His research interest is micro machining.
E-mail: daebosim@soongsil.ac.kr
M.S. student in the Department of Mechanical Engineering, Soongsil University. His research interest is micro machining.
E-mail: cyyangmech@soongsil.ac.kr
Professor in the School of Mechanical engineering, Soongsil University. His research topics are micro mechanical and non-conventional machining processes.
E-mail: bhkim@ssu.ac.kr