
직접 탄화수소 연료 적용을 위한 박막 고체산화물 연료전지 개발
Copyright © The Korean Society for Precision Engineering
This is an Open-Access article distributed under the terms of the Creative Commons Attribution Non-Commercial License (http://creativecommons.org/licenses/by-nc/3.0) which permits unrestricted non-commercial use, distribution, and reproduction in any medium, provided the original work is properly cited.
Abstract
Energy devices in modern society require high efficiency, carbon neutrality, and the capability of distributed power generation. A fuel cell is an energy conversion device, that satisfies all of these requirements. However, most fuel cells use hydrogen as a fuel, and more than half of hydrogen is currently produced through hydrocarbon reforming, resulting in significant energy loss. Additionally, the storage and supply of hydrogen require costly systems, and a large amount of energy is consumed during compression or liquidation processes. This paper develops a solid oxide fuel cell, that uses hydrocarbon directly as fuel to resolve this problem. A small amount of Ru is mixed with the Ni-based electrode, for the effective internal reforming of hydrocarbons. For rapid deposition of YSZ electrolytes, we developed a reactive sputtering process, using a DC power source. The developed thin-film solid oxide fuel cell, showed a performance of 76 mW/cm2 at 500oC using methane as fuel.
Keywords:
Solid oxide fuel cell, Hydrocarbon fuel, Sputter, Thin film키워드:
고체산화물 연료전지, 탄화수소 연료, 스퍼터, 박막1. 서론
현대 사회의 에너지 기술은 고효율, 탄소중립, 분산 발전을 구현하는 형태로 발전하고 있다. 연료전지는 이러한 요건들을 모두 만족하는 에너지 변환 장치로, 화학에너지를 전기에너지로 직접 변환하기 때문에 효율이 높고, 순수한 물만 배출하며 다양한 크기와 작동 온도로 설계가 가능하여 분산 발전에 적합하다[1-3]. 다만 연료전지의 연료로 가장 널리 사용되는 수소는 현재 절반 이상을 탄화수소 개질을 통해 생산하고 있으며 그 과정에서 상당한 에너지 손실이 발생한다[4]. 또한 보관 및 공급에 있어 액화 수소의 경우 극저온을 위해 고비용의 시스템 및 다량의 에너지가 소비되며 수소저장 합금의 경우 무게당 저장 비율이 5 wt% 내외로 효율이 떨어진다[5-6].
탄화수소는 수소보다 높은 에너지 밀도를 가지고 있으며 액화 및 보관이 쉽기 때문에 연료전지의 연로로 장점이 많지만 개질기를 통한 별도의 연료 처리 과정을 요구한다[7]. 개질기에 의해 추가된 시스템 부피 및 비용은 탄화수소의 높은 에너지 밀도의 장점을 상쇄하기 때문에 탄화수소가 가진 연료 측면에서의 이점을 백분 활용하기 위해서는 개질기 없이 직접 연료로 사용하는 것이 바람직하다[8-10]. 탄화수소가 연료전지 전극에서 내부 개질 반응이 이루어지기 위해서는 7-800oC 이상의 고온을 필요로 하며 고온의 폐열을 활용한 열병합 효율, 저렴한 촉매의 장점을 가지고 있다[2]. 이 온도에서는 탄화수소 연료를 개질기 없이 직접 사용할 수 있지만 고온 작동에 의한 연료전지 스택과 부가장치들의 내구성을 피하기 힘들기 때문에 5-600oC 부근으로 작동 온도를 낮추기 위한 노력들이 진행되고 있다[11]. 하지만 작동 온도의 감소는 전해질의 저항을 증가시키고 촉매 성능을 감소시키기 때문에 연료전지 구조 및 재료에 대한 대대적인 개선 없이는 성능 하락을 피할 수 없다[1]. 또한 메탄을 개질기 없이 직접 연료로 사용할 경우 전극에서 발생하는 수증기 개질 반응은 아래의 식(1)과 식(2)에 의해 흡열 반응이 지배적이기 때문에 7-800oC 이상의 높은 작동 온도를 요구한다[1].
(1) |
(2) |
SOFC의 나노기술 적용은 전해질의 두께를 획기적으로 줄이고 전극의 삼상계면을 극대화하여 작동 온도 감소에 의한 전극과 전해질의 저항 증가를 상쇄시킬 수 있다. 박막 전해질과 우수한 나노 구조의 전극을 제작하기 위해 다양한 반도체 공정들이 적용되었으며 큰 성능 하락 없이 4-600oC의 온도에서도 고체산화물 연료전지를 동작시킬 수 있다는 것이 다수의 연구 결과를 통해 증명되었다[12-15]. 다양한 반도체 공정 중 스퍼터는 증착 압력 조절을 통해 나노 전극을 위한 다공성 구조와 전해질을 위한 밀도 높은 박막을 모두 제작할 수 있으며 디스플레이와 같은 대면적 양산공정에 널리 적용되기 때문에 범용성과 상용성 측면에서 박막 고체산화물 제작에 가장 적합하다고 판단된다[12]. 또한 메탄을 내부 개질의 높은 반응 온도를 낮추기 위해 전극에 소량 혼합하는 귀금속(Ru, Rh, Pd, Pt, Ir)의 사용을 나노 촉매 적용을 통해 최소화할 수 있다.
따라서 본 연구에서는 탄화수소를 직접 연료로 사용하기 위한 박막 고체산화물 연료전지를 스퍼터를 통해 개발하였다. 특히 500oC의 낮은 온도에서도 활발한 내부 개질 반응을 촉진하기 위해 연료극 복합재 개발과 나노 구조 설계를 동시에 수행하였다. 또한 YSZ 전해질 제작에 있어 Y/Zr 금속 타겟과 DC 전원을 이용한 반응성 스퍼터링 공법을 개발하였다. RF 전원과 세라믹 타겟을 사용하는 기존 스퍼터링 공법 대비 공정 비용 및 시간을 크게 절감시킬 수 있다.
2. 실험 방법
2.1 기판
연료전지의 기판으로는 100 um 두께와 80 nm의 기공크기, 10%의 기공률을 가지고 있는 Anodized Aluminum Oxide (AAO)를 사용하였다. AAO는 사행도가 낮고 기공의 분포가 균일하기 때문에 연료의 확산이 활발하며 YSZ 전해질과의 열팽창계수가 유사하기 때문에 열팽창계수 차이에 의한 전해질의 크랙이나 박리를 효과적으로 방지할 수 있다.
2.2 음극
연료극은 기존의 Ni 기반 재료를 사용하되, 탄소의 침적을 방지하기 위해 Ru와 도핑된 CeO2를 소량 첨가하였다. 우선 스퍼터를 통해 AAO 기판 위에 30 nm의 Ru를 증착하였고 이후 Ni와 GDC를 Co-Sputtering하여 Ru가 증착된 AAO 기판 위에 Ni-GDC 복합 전극을 구성하였다. 비교군으로는 Ni 전극을 사용하였다. 자세한 증착 조건은 Table 1에 나타나 있다.
2.3 전해질
전해질은 1 um 두께의 YSZ를 제작하기 위해 Y/Zr 금속 타겟과 산소가 첨가된 아르곤을 이용한 반응성 스퍼터링 기법을 사용하였다. 200 W의 DC 전원이 Y/Zr 금속 합금 타겟에 인가되었으며 산소와 아르곤의 비율은 80 : 20, 스퍼터 내부의 압력은 증착 공정 동안 5 mtorr로 유지하였다.
2.4 양극
공기극 재료로는 저온에서도 촉매 활성도가 높은 Pt를 스퍼터를 통해 250 nm 두께로 증착하였다. 200W의 DC 전원을 인가하였으며 순수한 Ar 기체를 공급하였고 증착 압력은 50 mtorr를 유지하였다.
2.5 성능 측정
제작한 셀은 500oC에서 성능 측정을 진행하였으며 연료극에는 3%의 H2O가 포함된 CH4를 100 sccm의 유량으로 공급하였고 공기극에는 자연 대류를 통해 공기를 공급하였다. Solartron 1287 Electrochemical Interface와 1260 Impedance Analyzer가 전기화학 성능 측정에 이용되었다.
3. 실험 결과
탄화수소의 내부 개질 과정은 복잡한 촉매 반응을 포함하고 있기 때문에 신중한 연료극 재료 선정과 나노 구조 설계가 요구된다[8]. Ni는 메탄의 내부 개질에 효과적인 촉매이지만 탄소 침적의 문제가 있으며 상대적으로 높은 담지량을 요구하기 때문에 박막 고체산화물 연료전지의 개질 촉매로는 적합하지 않다. Ru는 상대적으로 적은 담지량에도 효과적으로 개질 반응을 나타내며 낮은 온도에서도 높은 개질률을 보인다[16]. 전극 제작에는 촉매의 분산도 및 반응 면적을 극대화하기 위해 스퍼터가 사용되었으며 7-800oC에 달하는 내부 개질 온도를 5-600oC로 낮추기 위해 우수한 개질 촉매인 Ru를 AAO와 Ni-GDC 연료극 사이에 30 nm 두께로 삽입하였다.
Fig. 1은 스퍼터를 통해 제작한 연료극을 나타낸다. 스퍼터와 같은 나노기술로 제작한 전극은 수-수십 nm의 매우 작은 입자 크기를 보여 연료전지의 TPB를 극대화할 수 있지만 Ostwald-Ripening에 의해 금속 입자가 고온에서 뭉쳐 내구성의 문제를 야기시킨다. 특히 Figs. 1(a)와 1(b)를 참고하면 순수한 Ni의 경우에 그 문제가 더 두드러지게 나타나는 것을 볼 수 있다. Ni에 GDC를 혼합한 경우 열처리 전 미세 구조는 순수한 Ni과 비교하여 큰 차이점을 발견할 수 없지만 600oC에서 열처리를 진행한 후에도 기공 구조가 유지되는 것을 발견할 수 있다. 금속에 소량의 산화물을 균일하게 분포시키면 분산강화(Dispersion Hardening)에 의해 산화물이 안정적인 Backbone 역할을 수행하여 금속의 응집을 방지한다. 본 연구에서도 동일한 원리에 의해 Ni의 응집이 방지되었으며 Pt의 고온 안정성을 확보하기 위해 GDC와 혼합 전극을 구성한 연구 사례에서도 이러한 경향성이 발견된다[17]. 또한 GDC는 탄화수소 연료의 개질 촉매로도 활용되며 Ni 표면에 침적되는 탄소를 방지하는 추가적인 효과가 있기 때문에 이러한 혼합 전극의 구성은 연료극의 성능 및 내구성을 크게 향상시킬 수 있다[18].
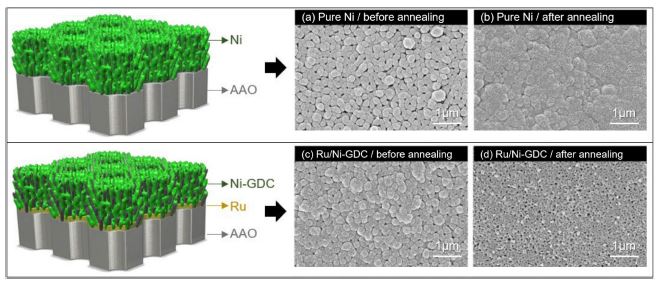
FE-SEM surface analysis of as deposited (a) Ni and (c) Ru/Ni-GDC anodes and 600oC, 1hour annealed (b) Ni and (d) Ru/Ni-GDC anodes
세라믹 전해질을 스퍼터로 제작하기 위해 YSZ 타겟과 RF 전원을 이용한 방식이 가장 보편적으로 사용되지만 YSZ의 높은 경도와 RF 전원의 고출력 시 발열 문제로 인해 증착률이 낮은 문제점이 발생한다. 본 연구에서는 증착률을 높이고 상대적으로 저렴한 DC 전원을 활용하기 위해 Y/Zr 합금의 반응성 스퍼터링으로 YSZ를 제작하였다. 반응성 스퍼터링은 Ar 기체에 산소나 질소를 소량 첨가하여 질화물, 산화물 박막을 제작하는 방식이다. 이 경우 산소를 추가하여 Y/Zr을 YSZ로 산화시켰으며 300 sccm의 총반응 기체 유량 중 80을 Ar로, 20%를 O2로 설정하여 공급하였다.
반응성 스퍼터링을 통해 증착된 YSZ 박막의 결정성을 확인하기 위한 XRD 분석이 Fig. 2에 나타나있다. XRD 분석을 통해 Y/Zr 금속의 Peak 성분이 발견되지 않았으며 (101), (002), (112), (211) 방향의 YSZ Peak이 발견되어 Polycrystalline YSZ 박막이 형성되었음을 알 수 있다. 또한 Table 2의 XPS 분석에서도 산소의 함량이 63% 이상 확보되어 금속 성분이 포함되지 않은 산화물 형태의 YSZ가 형성되었음을 확인하였다.
Fig. 3은 Ru/Ni-GDC 연료극과 반응성 스퍼터링으로 제작한 YSZ가 적용된 박막 고체산화물 연료전지의 구성과 단면을 나타낸다. 100의 AAO 위에 30의 Ru와 500 nm의 Ni-GDC 연료극을 Co-Sputtering 기법을 통해 증착하였으며 그 위에 1 μm의 YSZ 전해질을 DC 반응성 스퍼터링을 통해 적용하였다. 공기극은 상대적으로 낮아진 작동온도에서 오는 촉매 손실을 최소화하기 위해 촉매 활성도가 높은 Pt를 스퍼터링을 통해 제작하였다. 연료전지의 실험은 500oC에서 진행하였으며 H2와 CH4를 공급하여 연료에 따른 성능 차이를 확인하였다. H2 연료 조건에서 Pure Ni와 Ru/Ni-GDC 전극이 적용된 셀은 거의 동일한 OCV와 출력 밀도를 나타내었다. 하지만 Pure Ni 전극의 경우 CH4 연료에서 OCV가 뜨지 않았으며 이는 낮은 작동 온도와 500 nm의 낮은 Ni 담지량에 의한 것이라고 판단된다. 반면에 Ru/Ni-GDC가 적용된 셀의 경우 3%의 H2O로 가습된 CH4 연료에서 0.98 V의 OCV와 76 mW/cm2의 최대 전력 밀도를 나타내었다. 이는 소량의 Ru와 GDC가 부족한 Ni의 담지량에서 야기되는 CH4의 개질률을 크게 향상시킬 수 있다는 것을 의미한다. H2를 연료로 사용하였을 경우 OCV는 1.0 V, 최대 전력밀도는 87 mW/cm2로 CH4를 사용했을 때와 비교하여 약 10% 정도의 성능 차이를 보였다. 이는 기존 연구에서 보인 2-30%의 성능 차이[8-9]보다 월등히 개선된 수치로 본 연구에서 개발된 전극이 CH4의 내부 개질에 적합한 물질과 구조를 나타냄을 증명한다.
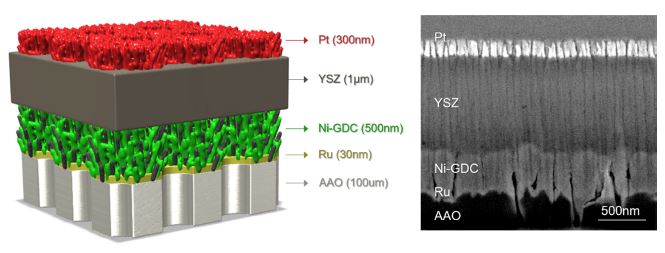
Illutration and FE-SEM analysis of thin film solid oxide fuel for direct ulilization of methane fuel
H2와 CH4 연료간 성능 차이의 원인을 분석하기 위해 EIS 분석을 수행하였다. Fig. 5를 참조하면 전해질의 저항은 두 경우 모두 0.56으로 동일하게 나타났지만 H2를 연료로 사용한 경우 3.8의 분극 저항을, CH4 연료를 사용한 경우 7.4 Ωcm2의 분극 저항을 나타내었다. 이때의 분극 저항은 화학 반응식의 반응 속도에 의해 결정되며 화학 반응이 빠를수록 분극 저항은 감소하고 반대로 화학 반응이 느릴수록 분극 저항은 증가한다. 메탄의 내부 개질 반응은 수소를 연료로 사용했을 때의 수소 산화 반응(HOR)인 H2+ O2- → H2O + 2e- 의 반응에 추가적으로 식(1)에서 소개한 CH4+ H2O(g) → CO + 3H2의 스팀 메탄 개질(SMR) 반응과 식(2)에서 소개한 CO + H2O(g) → CO2+ H2의 수성가스 전환 반응(Water Gas Shift Reaction)이 요구된다. 이 두 메탄의 내부 개질 반응은 수소의 산화보다 현저히 느리기 때문에 추가적인 분극 저항 상승을 초래한다[1].
4. 결론
본 연구에서는 탄화수소를 직접 연료로 사용하기 위한 Ru/Ni-GDC 전극과 값싸고 빠른 증착을 위한 DC 반응성 스퍼터링 YSZ 전해질 공정을 개발하여 박막 고체산화물 연료전지에 적용하였다. 제작된 박막 고체산화물 연료전지는 500oC의 낮은 온도에서도 원활한 내부 메탄 개질을 수행할 수 있었다. 직접 메탄 연료를 사용한 셀 테스트 환경에서 Pure Ni 전극이 적용된 셀은 OCV가 뜨지 않았던 것과는 대조적으로 Ru/Ni-GDC 전극이 적용된 셀에서는 약 1 V의 높은 OCV를 보였다. 또한 이 전극에서는 H2와 CH4를 연료로 사용하였을 때 각각 87, 76mW/cm2의 최대 전력 밀도를 보여 메탄의 느린 내부 개질에 의한 손실을 최소화하는데 성공하였다. 현재 보유한 장비의 문제로 Ru와 Ni-GDC 층을 분리하여 전극을 제작하였지만 추후 개선을 통해 Ru, Ni, GDC가 균일하게 혼합된 전극을 구성한다면 H2와 CH4 간의 성능 차이를 더 좁힐 수 있을 것이라 판단된다.
Acknowledgments
본 연구는 한국연구재단의 개인기초연구사업(No. 2020R1-G1A1014777)과 한국에너지기술평가원의 신재생 에너지핵심기술개발과제(No. 20213030030150)의 지원을 통해 수행하였습니다.
REFERENCES
-
O'hayre, R., Cha, S.-W., Colella, W., Prinz, F. B., (2016), Fuel cell fundamentals, John Wiley & Sons.
[https://doi.org/10.1002/9781119191766]
-
Minh, N. Q., (1993), Ceramic fuel cells, Journal of the American Ceramic Society, 76(3), 563-588.
[https://doi.org/10.1111/j.1151-2916.1993.tb03645.x]
-
Stambouli, A. B., Traversa, E., (2002), Solid oxide fuel cells (SOFCs): A review of an environmentally clean and efficient source of energy, Renewable and Sustainable Energy Reviews, 6(5), 433-455.
[https://doi.org/10.1016/S1364-0321(02)00014-X]
-
Barthélémy, H., Weber, M., Barbier, F., (2017), Hydrogen storage: Recent improvements and industrial perspectives, International Journal of Hydrogen Energy, 42(11), 7254-7262.
[https://doi.org/10.1016/j.ijhydene.2016.03.178]
-
Sakintuna, B., Lamari-Darkrim, F., Hirscher, M., (2007), Metal hydride materials for solid hydrogen storage: A review, International Journal of Hydrogen Energy, 32(9), 1121-1140.
[https://doi.org/10.1016/j.ijhydene.2006.11.022]
-
Rusman, N., Dahari, M., (2016), A review on the current progress of metal hydrides material for solid-state hydrogen storage applications, International Journal of Hydrogen Energy, 41(28), 12108-12126.
[https://doi.org/10.1016/j.ijhydene.2016.05.244]
-
Ghenciu, A. F., (2002), Review of fuel processing catalysts for hydrogen production in PEM fuel cell systems, Current Opinion in Solid State and Materials Science, 6(5), 389-399.
[https://doi.org/10.1016/S1359-0286(02)00108-0]
-
Park, S., Vohs, J. M., Gorte, R. J., (2000), Direct oxidation of hydrocarbons in a solid-oxide fuel cell, Nature, 404(6775), 265-267.
[https://doi.org/10.1038/35005040]
-
Murray, E. P., Tsai, T., Barnett, S. A., (1999), A direct-methane fuel cell with a ceria-based anode, Nature, 400(6745), 649-651.
[https://doi.org/10.1038/23220]
-
McIntosh, S., Gorte, R. J., (2004), Direct hydrocarbon solid oxide fuel cells, Chemical Reviews, 104(10), 4845-4866.
[https://doi.org/10.1021/cr020725g]
-
Wachsman, E. D., Lee, K. T., (2011), Lowering the temperature of solid oxide fuel cells, Science, 334(6058), 935-939.
[https://doi.org/10.1126/science.1204090]
-
Lee, Y. H., Ren, H., Wu, E. A., Fullerton, E. E., Meng, Y. S., Minh, N. Q., (2020), All-sputtered, superior power density thin-film solid oxide fuel cells with a novel nanofibrous ceramic cathode, Nano Letters, 20(5), 2943-2949.
[https://doi.org/10.1021/acs.nanolett.9b02344]
-
Chang, I., Ji, S., Park, J., Lee, M. H., Cha, S. W., (2015), Ultrathin YSZ coating on Pt cathode for high thermal stability and enhanced oxygen reduction reaction activity, Advanced Energy Materials, 5(10), 1402251.
[https://doi.org/10.1002/aenm.201402251]
-
An, H., Lee, H.-W., Kim, B.-K., Son, J.-W., Yoon, K. J., Kim, H., Shin, D., Ji, H.-I., Lee, J.-H., (2018), A 5 × 5 cm2 protonic ceramic fuel cell with a power density of 1.3 W cm-2 at 600oC, Nature Energy, 3(10), 870-875.
[https://doi.org/10.1038/s41560-018-0230-0]
-
Ren, H., Lee, Y. H., Wu, E. A., Chung, H., Meng, Y. S., Fullerton, E. E., Minh, N. Q., (2020), Nano-ceramic cathodes via co-sputtering of Gd-Ce alloy and lanthanum strontium cobaltite for low-temperature thin-film solid oxide fuel cells, ACS Applied Energy Materials, 3(9), 8135-8142.
[https://doi.org/10.1021/acsaem.0c01147]
-
Chen, Y., deGlee, B., Tang, Y., Wang, Z., Zhao, B., Wei, Y., Zhang, L., Yoo, S., Pei, K., Kim, J. H., (2018), A robust fuel cell operated on nearly dry methane at 500oC enabled by synergistic thermal catalysis and electrocatalysis, Nature Energy, 3(12), 1042-1050.
[https://doi.org/10.1038/s41560-018-0262-5]
-
Lee, Y. H., Cho, G. Y., Chang, I., Ji, S., Kim, Y. B., Cha, S. W., (2016), Platinum-based nanocomposite electrodes for low-temperature solid oxide fuel cells with extended lifetime, Journal of Power Sources, 307, 289-296.
[https://doi.org/10.1016/j.jpowsour.2015.12.089]
-
Lu, C., Worrell, W., Gorte, R., Vohs, J., (2003), SOFCs for direct oxidation of hydrocarbon fuels with samaria-doped ceria electrolyte, Journal of the Electrochemical Society, 150(3), A354.
[https://doi.org/10.1149/1.1553765]
Assistant Professor in the Department of Mechanical Engineering, Dankook University. He received his Ph.D. in Mechanical and Aerospace Engineering from Seoul National University. His research interest is fuel cells (LT-SOFCs) and their systems for power plants.
E-mail: guyoungcho@dankook.ac.kr
Assistant Professor in the School of Mechanical Engineering, University of Ulsan. He received his Ph.D. in Mechanical and Aerospace Engineering from Seoul National University. His research interest is the nanofabrication of solid oxide fuel cells.
E-mail: yhlee@ulsan.ac.kr