
Laser EDM Hybrid Micro Machining of CFRP
Copyright © The Korean Society for Precision Engineering
This is an Open-Access article distributed under the terms of the Creative Commons Attribution Non-Commercial License (http://creativecommons.org/licenses/by-nc/3.0) which permits unrestricted non-commercial use, distribution, and reproduction in any medium, provided the original work is properly cited.
Abstract
CFRP (Carbon Fiber Reinforced Plastic) is a composite material formed using carbon fibers and epoxy resin matrices. It has low productivity and suffers from machining defects during precision machining. Laser machining of CFRP is associated with the problem of heat damage to the epoxy resin. EDM of CFRP can process various shapes with a shaped tool, however it has a lower material removal rate compared to laser, and the non-conductive epoxy resin layer on the surface must be removed before EDM processing. In this study, we have proposed a laser EDM hybrid machining in which CFRP was pre-processed with a laser and then post-processed by EDM. The laser pre-processing conditions were selected by adjusting the laser power and the number of repetitions to minimize thermal damage. According to EDM conditions, the size of the thermal damage area occurring in the epoxy resin, the change in the side gap, and the change in the processing time were investigated. Using the hybrid processing, micro-holes with a diameter of 150 μm were machined, and square-shaped micro-holes were also machined. To improve productivity, a multi-tool capable of processing four square shapes was manufactured, and multi-processing was performed.
Keywords:
CFRP, Laser machining, EDM, Hybrid machining, Multi-processing, Multi-tool키워드:
탄소섬유강화플라스틱, 레이저가공, 방전가공, 복합가공, 멀티가공, 멀티전극1. Introduction
CFRP (Carbon Fiber Reinforced Plastic) is a composite material using carbon fibers and epoxy resin matrices. It is widely used in various industries such as aviation, automobiles, ships, sports, medical, electronics, robotics, and defense. It has been in the spotlight for its excellent properties such as light weight, high strength, high elasticity, abrasion resistance, and fatigue characteristics [1]. However, precision machining of CFRP is difficult due to the heterogeneous properties of carbon fiber and epoxy resin. Defects such as delamination, fiber pull out, burrs, uncut fiber and thermal damage are easy to occur during cutting such as drilling and milling, and high tool wear is also a problem [1-3]. Various non-conventional machining methods are also being used in CFRP processing. Among them, laser machining is capable of processing CFRP from a large area to a small area without considering tool wear and cutting force [4]. For precise micro-shapes, picosecond pulses are used [5], and good shape processing is also possible even with nanosecond pulses [6]. The author also studied micro machining of CFRP using nanosecond pulses [7]. However, there is a problem in that extensive thermal damage occurs to the heat-sensitive epoxy resin during laser processing of CFRP [3].
CFRP machining using EDM can process various shapes depending on the shape of the tool electrode. Since EDM is a non-contact machining resulting in almost no cutting force, so precise shape machining without delamination or burr is possible [8]. For micro machining, it is possible to make micro holes in CFRP using EDM [9]. However, EDM is generally slower than laser machining. There is a problem that the non-conductive epoxy resin layer on the surface of the CFRP must be removed before EDM processing [10]. To make up for the shortcomings of EDM of CFRP and increase productivity, a hybrid machining of drilling and EDM deburring was researched [11]. However, this process was not applied to make various shapes other than the circular hole shape.
In this study, the hybrid machining of CFRP using laser and EDM was proposed. After pre-processing with a laser to minimize thermal damage, post-processing with EDM was performed to machine the micro-shape. By using EDM tools with various shapes, not only circular but also square shaped micro-holes were machined. In addition, multi-processing using multi-tool was attempted to improve productivity.
2. Experimental Set Up
In this experiment, Ytterbium Pulsed Fiber Laser (K2 Fiber 20, K2 Laser System, Korea) with a wavelength of 1,064 nm was used. It is adjustable from 10-95% based on the maximum power of 20 W, the maximum frequency is 200 kHz, and the maximum scan speed is 3,000 mm/s. EDM machine was manufactured in the laboratory. It has XYZ axis with the tool rotation, and uses an RC type EDM power. The EDM tool was made of tungsten carbide with a diameter of 0.5 mm, and was manufactured to various shaped microelectrodes through WEDG. As the dielectric fluid, EDM oil (EDM OIL 100, Universal Oils, Korea) was used. For a multi-processing, SS304 with a diameter of 1.0 mm was used as a multi-tool electrode, and deionized water was used as the dielectric fluid. The CFRP specimen is plain woven type and has a thickness of 0.5 mm (Muhan Carbon, Korea).
3. Feasibility Test of Laser EDM Hybrid Machining
In Fig. 1 shows the machined rectangular shape by hybrid process with pre-processing by laser and post-processing by EDM. Laser processing conditions were 95% power, 20 kHz frequency, 600 mm/s scan speed, and 800 repetitions. For EDM, a square tool with a side of 310 μm was used, and 120 V and 94 nF were used. After laser pre-processing, the size of the square shape was 265 μm on the front side and 132 μm on the back side. After EDM post-processing, the size of the square shape was 353 μm on the front side and 343 μm on the back side. After EDM, the overall size increased due to the size of the square tool (310 μm), but the taper was decreased from 14.9 degrees after laser to 1.1 degrees after EDM. So a square shape with almost no taper could be processed. However, after laser machining, thermal damage occurred widely around the machined area, which could not be removed even after EDM. Therefore, it is necessary to reduce the laser thermal damage area in order to produce a precise shape after EDM.
4. Results and Discussion
4.1 Laser Pre-Processing
In order to reduce the wide thermal damage in the laser pre-processing step, the laser power and the number of repetitions were reduced. Fig. 2(a) shows a case of 50% laser power and 10 repetitions. Although the wide and deeply damaged areas were reduced, a large area was still thermally damaged. Fig. 2(b) shows a case of 30% laser power and 5 repetitions, and it shows that there is very little thermal damage around the machined area. A very small thermally damaged area is not a problem since it is included in the machining area of EDM post processing. Although the amount of laser processing in the depth direction was relatively small, 30% power and 5 repetitions were selected as laser conditions because wide and deep thermal damage could not be removed even after EDM. Fig. 2(c) shows the result of processing a rectangular shape under the conditions of 30% power and 5 repetitions.
4.2 EDM Post-Processing
Fig. 3 shows the result of EDM post-processing of a circular shape after laser pre-processing. In the laser pre-processing, a circular shape was machined with 30% power and 5 repetitions. The EDM tool size is 233 μm. As shown in Fig. 3(a), under the EDM conditions of 120 V and 10 nF, thermal damage occurred in which the epoxy resin melted widely in the carbon fiber direction due to the heat generated during EDM. In Fig. 3(b), slight thermal damage occurred around the hole on the back side. As shown in Figs. 3(c) and 3(d), under the EDM conditions of 90 V and 10 nF, the discharge energy was relatively small, so it was possible to machine a shape with a very small thermal damage area around the machined hole after EDM post-processing.
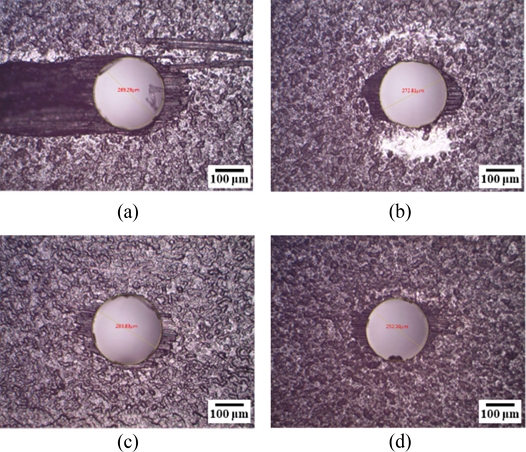
Machined holes by laser EDM hybrid process with different EDM conditions: 120 V, 10 nF (a) Front view, (b) Backside view; 90 V, 10 nF (c) Front view, (d) Backside view
To analyze the size of thermal damage after EDM post-processing, the thermal damage area ratio was calculated as follows.
In the case of 120 V and 10 nF in Fig. 3(a), the thermal damage area ratio is larger than in the case of 90 V and 10 nF in Fig. 3(c).
Fig. 4 shows the thermal damage area ratio according to voltage in EDM post-processing. In this case, the capacitor is 10 nF, and the tool size is 233 μm. As the voltage increases, the thermal damage area ratio increases. Fig. 5 shows the thermal damage area ratio according to the capacitor in EDM post-processing. In this case, the voltage is 100 V and the tool size is 215 μm. As the capacitor increases, the thermal damage area ratio also increases. That is, if the discharge energy increases, more heat is generated during EDM, so the thermal damage area increases.
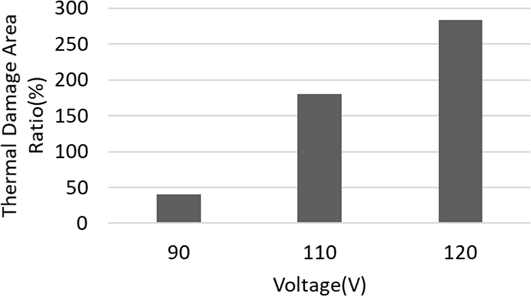
Thermal damage area ratio according to voltage in EDM post-processing (capacitor: 10 nF, tool size: 233 μm)
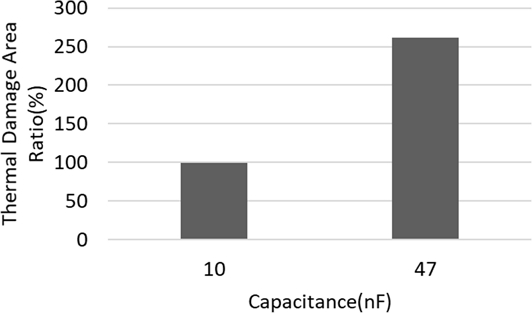
Thermal damage area ratio according to capacitance in EDM post-processing (voltage: 100 V, tool size: 215 μm)
Fig. 6 shows the machining time and the side gap according to the voltage in EDM post-processing. In this case, the capacitor is 10 nF and the tool size is 233 μm. When the voltage was 90 V, the side gap was the smallest at 25 μm. In the case of 90 V and 110 V, the machining time was almost the same, and in the case of 120 V, the shortest machining time was 13 minutes.
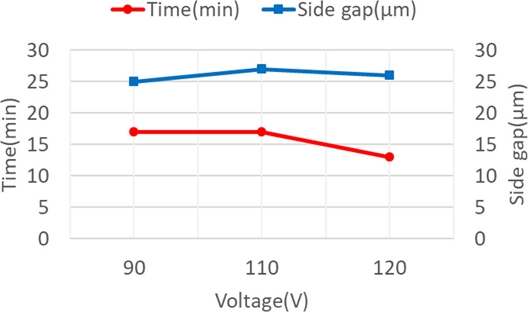
Machining time and side gap according to voltage in EDM porst-processing (capacitance: 10 nF, tool size: 233 μm)
Fig. 7 shows the micro holes with a diameter of 150 μm by using hybrid machining. In the laser pre-processing step, it was processed to a size of 100 μm. In the EDM post-processing step, conditions of 100 V and 5 nF were used, and the tool size was 125 μm. The EDM machining time was 9 minutes, and it was observed that the epoxy resin was slightly melted around the machined holes after EDM.
4.3 Square Shape Machining
In this experiment, a rectangular shape was machined as shown in Fig. 8. In the laser pre-processing, a square shape was processed. Then, EDM post-processing was performed using a square tool with a side of 210 μm. In this case, EDM conditions were 100 V and 10 nF. The tool can be rotated when machining a circular shape, but it is impossible to rotate the tool when machining a square shape. Therefore, the removal of debris and the supply of dielectric fluid in the machining area were relatively difficult, so the machining time was increased to 41 minutes. The size of the machined rectangle is 247 μm on one side. After EDM post-processing, the epoxy resin melted in the direction of carbon fiber on the front side. This is because the thermal damage is increased due to the prolonged machining time and unstable machining environment caused by non-rotation of the tool.
4.4 Multi-Processing Using Multi-Tool
In order to improve productivity, a multi-tool capable of processing four square shapes was manufactured, and multi-processing was performed using this multi-tool in EDM post-processing. A SS304 shaft with 1mm diameter was used to fabricate four rectangular multi-tools using wire electrodes. As shown in Fig. 9, the outer four sides were machined to make a rectangle (steps 1 to 4). Then, by machining in to a cross shape (steps 5 to 6), four square multi-tools are completed. In this case, EDM conditions were 125 V and 97 nF, and the total processing time was 97 minutes. The length of one side of the rectangle is 140 μm. Fig. 10 shows the multi-tool after being used for CFRP multi-processing, and it can be seen that the tool tip is worn out.
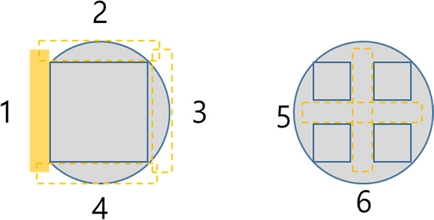
Fabrication procedure of multi-tool (outer four sides machining: steps 1 to 4, cross shape machining: steps 5 to 6)
In EDM post-processing using multi-tool, since the discharge gap is not controlled for each hole during discharge, machining stability and efficiency may be reduced. Increased machining area and no tool rotation also reduce machining stability. Using the multi-tool, there were many electrical shorts between tool and workpiece, and the machining did not proceed well in the depth direction. Therefore, the amount of machining in laser pre-processing was increased in order to reduce the amount of machining in EDM post-processing. As laser conditions, 80% power and 200 repetitions were used, and the size of the processed shape was reduced by repeatedly irradiating one point. A total of 4 holes were pre-machined with a laser according to the size of the multi-tool. As shown in Fig. 11(a), after laser pre-processing, thermal damage occurred around the machined area. In EDM post-processing, 125 V and 47 nF was used because of the large machining area of multi-processing. Deionized water was used as a dielectric fluid. The EDM machining time was 14 minutes. Figs. 11(b) and 11(c) shows the front and back sides after EDM post-processing. In conclusion, multi-processing is possible, but the machining shape accuracy is not high. Further research is needed to improve machining shape accuracy in multi-processing.
5. Conclusion
In this paper, micro machining of CFRP using laser and EDM was studied. In the laser pre-processing step, thermal damage was minimized by controlling the laser power and the number of repetitions. As a result of the experiment, the conditions of 30% power and 5 repetitions were selected. In the EDM post-processing, the size of the thermal damage occurring in the epoxy resin, the change in the side gap, and the change in the machining time were investigated according to the EDM conditions. The thermal damage size was analyzed through the thermal damage area ratio. In the case of high discharge energy, thermal damage occurred widely around the machined area after EDM post-processing. When the discharge energy is reduced, it is possible to machine the shape with little to no thermal damage after EDM post-processing (ex. 90 V and 10 nF). By using the hybrid machining, micro-holes with a diameter of 150 μm were machined, and a square-shaped hole with a side length of 247 μm was also machined. To improve productivity, multi-processing that can process 4 square shapes was tested. In order to increase the machining stability and efficiency of EDM in multi-processing, the amount of laser pre-machining was increased and the amount of EDM post-machining was reduced. As a result, four square holes were machined by multi-processing. But, the machining shape accuracy was not high, so further research on improving machining shape accuracy is needed.
Acknowledgments
This research was supported by Basic Science Research Program through the National Research Foundation of Korea (NRF) funded by the Ministry of Education (NRF-2017R1D1A1B03032887).
REFERENCES
-
Che, D., Saxena, I., Han, P., Guo, P., Ehmann, K. F., (2014), Machining of carbon fiber reinforced plastics/polymers: A literature review, Journal of Manufacturing Science and Engineering, 136(3), 034001.
[https://doi.org/10.1115/1.4026526]
-
Gang, M. G., Kim, G., Shin, K., Jeong, A., Kim, H. Y., Kim, C. H., Lee, S. W., Kim, T. G., (2018), Mechanical cutting process trends for difficult-to-cut materials-A review, Journal of the Korean Society for Precision Engineering, 35(3), 253-267.
[https://doi.org/10.7736/KSPE.2018.35.3.253]
-
Kim, K. B., Seo, J. H., Kim, T. G., Jun, M. B. G., Jeong, Y. H., (2020), Comparative analysis and monitoring of tool wear in carbon fiber reinforced plastics drilling, Journal of the Korean Society for Precision Engineering, 37(11), 813-818.
[https://doi.org/10.7736/JKSPE.020.091]
-
Goeke, A., Emmelmann, C., (2010), Influence of laser cutting parameters on CFRP part quality, Physics Procedia, 5, 253-258.
[https://doi.org/10.1016/j.phpro.2010.08.051]
-
Wolynski, A., Herrmann, T., Mucha, P., Haloui, H., L’huillier, J., (2011), Laser ablation of CFRP using picosecond laser pulses at different wavelengths from UV to IR, Physics Procedia, 12, 292-301.
[https://doi.org/10.1016/j.phpro.2011.03.136]
-
Jaeschke, P., Stolberg, K., Bastick, S., Ziolkowski, E., Roehner, M., Suttmann, O., Overmeyer, L., (2014), Cutting and drilling of carbon fiber reinforced plastics (CFRP) by 70W short pulse nanosecond laser, High-Power Laser Materials Processing: Lasers, Beam Delivery, Diagnostics, and Applications III, 159, 89630S.
[https://doi.org/10.1117/12.2036086]
-
Chung, D. K., Park, J. S., Kim, K. H., (2019), Micro machining of CFRP using nanosecond pulsed fiber laser, Journal of the Korean Society for Precision Engineering, 36(9), 783-791.
[https://doi.org/10.7736/KSPE.2019.36.9.783]
-
Lau, W., Wang, M., Lee, W. B., (1990), Electrical discharge machining of carbon fibre composite materials, International Journal of Machine Tools and Manufacture, 30(2), 297-308.
[https://doi.org/10.1016/0890-6955(90)90138-9]
-
Kumar, R., Agrawal, P. K., Singh, I., (2018), Fabrication of micro holes in CFRP laminates using EDM, Journal of Manufacturing Processes, 31, 859-866.
[https://doi.org/10.1016/j.jmapro.2018.01.011]
-
Teicher, U., Müller, S., Münzner, J., Nestler, A., (2013), Micro-EDM of carbon fibre-reinforced plastics, Procedia Cirp, 6, 320-325.
[https://doi.org/10.1016/j.procir.2013.03.092]
- Islam, M. M., Li, C. P., Won, S. J., Ko, T. J., (2017), A deburring strategy in drilled hole of CFRP composites using EDM process, Journal of Alloys and Compounds, 703, 477-485.
Associate Professor in School of Robot and Automation Engineering, Dongyang Mirae University. His research interests are micro machining and non-conventional machining.
E-mail: dkchung@dongyang.ac.kr
B.Sc. in School of Robot and Automation Engineering, Dongyang Mirae University. His research interest is micro machining.
E-mail: gkscksgh93@naver.com
B.Sc. in School of Robot and Automation Engineering, Dongyang Mirae University. His research interest is micro machining.
E-mail: cj45jin@naver.com
B.Sc. in School of Robot and Automation Engineering, Dongyang Mirae University. His research interest is micro machining.
E-mail: wnstj5067@naver.com