
슬롯 다이 코팅 균일도 평가를 위한 실용적인 중량계측 기반 유량 측정 방법
Copyright © The Korean Society for Precision Engineering
This is an Open-Access article distributed under the terms of the Creative Commons Attribution Non-Commercial License (http://creativecommons.org/licenses/by-nc/3.0) which permits unrestricted non-commercial use, distribution, and reproduction in any medium, provided the original work is properly cited.
Abstract
Slot-die coating is a method of coating a wide layer of thin film on a substrate. It has the advantages of large-area coating with high reproducibility and uniform thickness. For this reason, it has been widely applied in various industrial manufacturing fields. To secure higher coating uniformity under various coating conditions, estimating and controlling the flow rate of the coating solution discharged to the substrate is crucial. In this study, a practical gravimetric flow rate measurement method for slot-die coating uniformity evaluation has been introduced. The gravimetric method is a technique for accurately and quickly estimating the flow rate through the mass change over time using a precision weighing balance. We analyzed the measurement principle and errors caused by fluid mechanics such as hydrodynamic force or capillary force. The dynamic properties based on fluid viscosity were also evaluated for flow rates from 5 to 50 μL/s. The repeatability of the fabricated measurement system was ~1.5 μL/s. Finally, it was confirmed that the settling time for high-viscosity fluid could be advanced by 56.4% through multi-step feedforward control.
Keywords:
Slot-die coating, Gravimetric method, Flow meter, Coating uniformity키워드:
슬롯 다이 코팅, 중량계측법, 유량계, 코팅 균일도1. 서론
슬롯 다이 코팅(Slot-Die Coating)은 높은 종횡비를 가진 슬롯 다이에 코팅액을 토출하여 기판위에 넓은 층의 박막을 코팅 할 수 있는 방법이다[1]. 넓이 제한 없는 대면적 코팅 특성, 균일한 두께 코팅을 통한 높은 재현성으로 인해 슬롯 다이 코팅은 태양광 전지, 리튬 이온 배터리, 유기 발광 다이오드 장치 등 다양한 제조 공정에 활용되고 있다[2-4]. 최근 슬롯 다이 코팅은 롤투롤(Roll-to-Roll) 공정과 같이 연속적인 코팅뿐만 아니라 대형 디스플레이 제조 공정 등에서 토출이 불연속적인 코팅에도 사용되고 있다[5-6].
Fig. 1과 같이 슬롯 다이 코팅에서 코팅의 균일도는 코팅의 진행 방향(Coating Direction)과 그 방향과 수직인 슬롯 다이에 나란한 방향(Cross Coating Direction) 두 방향의 균일도 모두 중요하다. 따라서 시편의 길이가 유한한 불연속적인 코팅에서 슬롯 다이 코팅을 이용하여 균일한 코팅을 수행하기 위해서는 펌프의 유량 제어, 다이와 시편 사이의 갭 그리고 슬롯 다이의 이동 속도를 각각 제어할 필요가 있다.
그 중 유량 제어 시스템의 경우, 슬롯 다이 코팅은 전계량(Pre-Metered) 방식이지만 코팅 액의 점도와 이동 유로의 탄성 및 다이 내부 유로의 특성에 따라 노즐로부터 토출되는 유량은 펌프의 명령과 동적 특성이 달라진다[7]. 또한 유량 제어 시스템이 복잡하고 코팅을 설명하기 위한 모델이 난해하기 때문에, 코팅액의 점도, 시편의 크기와 표면 상태를 고려하여 현장에서 작업자의 Trial and Error 방법으로 각 파라미터를 설정하는 실정이다.
따라서 불연속적인 코팅에서 코팅의 진행 방향 균일도를 향상시키기 위해 유량을 정확하게 예측 또는 계측할 필요가 있다. 유량을 측정하는 방법은 유량계를 이용하는 방법이 일반적이지만 슬롯 다이 내부에 유량계를 설치하기는 거의 불가능하다. 이를 해결하기 위해 코팅액에 입자를 넣고 이를 추적하여 유량을 측정하는 입자 영상 유속계 방법과 코팅된 기판을 건조시킨 후 코팅 두께를 직접 측정하는 방법이 제안되었다[8-9]. 그러나 기존의 방법들은 많은 시간과 비용이 들며, 측정 과정 중 코팅 두께에 영향을 줄 수 있는 요인들이 존재한다.
본 논문에서는 슬롯 다이 코팅에 적용하기 위한 코팅 노즐의 출구의 유량을 측정하는 중량계측법(Gravimetric Method) 기반 유량 측정 시스템에 대해서 소개한다. 중량계측법은 정밀한 저울을 이용하여 시간에 따른 중량 변화를 통해 정확하면서도 빠르게 유량을 추정하는 기법이다[10-13]. 개발된 유량 측정 시스템은 정밀 저울을 이용하여 최소 수 μL/sec에서 수천 μL/sec의 유량 측정이 가능하며, 점도에 따른 유량의 동적 특성을 평가할 수 있다.
2. Gravimetric Flow Meter
2.1 유량 측정 시스템
유량의 측정은 토출된 유체의 무게를 측정하는 것으로부터 시작된다. 무게 측정은 전자기력 보상 방식의 정밀 저울을 이용하는데, 이 방식은 측정하고자 하는 대상의 무게 Fg로 인해 기울어짐이 발생할 때 저울을 평형상태로 위치시키는 영위법(Null Method)을 통해 무게를 도출한다[14-15]. Fig. 2는 간략화된 저울의 형태와 유량 측정 시스템을 보여준다. 유연기구 메커니즘으로 제작된 레버의 끝에 위치한 위치 센서는 레버가 원점에서부터 얼마나 기울어졌는지를 측정하고, 기울어진 변위만큼 전자기 구동기가 피드백 제어를 통해 평형 상태로 보상한다. 이때 보상되는 전자기력으로부터 물체의 질량 ml을 도출한다.
(1) |
여기에서 g는 중력가속도, Kf는 전자기 구동기의 힘 상수이며, 전자기 구동기에 인가되는 전류 I를 통해 보상되는 힘을 구할 수 있다.
유량 측정 시스템에서는 물체가 놓이는 곳에 유체가 담기는 저수통(Reservoir) 형태의 Weighing Pan을 설치하고 그 상부에 유체가 토출되는 노즐을 위치시킨다. 만약 유체가 비압축성이라면 토출되는 유체의 부피 Vl는 유체의 질량과 해당 유체의 밀도 ρ로 도출되며 유체의 부피를 수치 미분을 통해 유체의 유량 Ql을 최종적으로 도출할 수 있다.
(2) |
(3) |
Fig. 3은 제작된 유량 측정 시스템이다. 유연기구 메커니즘은 변위 증폭비 3.64 : 1을 가진 레버 메커니즘이며, 기계적 민감도 증가를 위해 Flexure Pivot의 두께는 0.1 mm로 제작하였다. 위치 센서의 경우 Photodiode (PD)에 수광 되는 빛의 세기를 통해 변위를 측정하도록 자체 설계한 센서이며, 분해능은 약 2 nm이다[16]. 또한 보조 변위 센서로서 선형 엔코더(Ti20KD, Renishaw)를 사용하였다. 무게 보상을 위해 사용된 선형 보이스 코일 모터(Voice Coil Motor, VCM)는 힘 상수 3.9 N/A를 지닌 모터를 사용하였다(AVM24-10, Akribis).
유체를 토출하는 펌프는 지름 22.5 mm 크기의 30 mL의 시린지(Syringe)와 시린지 펌프(Legato 110, KD Scientific)를 사용하였다. 효용성 검증을 위해 외경 1.47 mm, 내경 1.069 mm의 Needle 노즐(17 Gauge, Hamilton)을 사용하였다. 샘플링 주기는 0.1 msec이며 유량 데이터는 노이즈 저감을 위해 버퍼사이즈 5,000, 표준 편차 0.1의 가우시안(Gaussian) 필터를 적용하였다. 최종적으로 설계한 유량 측정 시스템은 약 1 mg의 분해능과 0.28초의 안정화 시간을 가진다.
2.2 유체 거동에 의한 오차 분석 및 저감
본 논문에서 웨잉팬에 일정량의 미리 유체를 담아두고 노즐 끝단을 유체 내부에 위치시킨 다음 토출을 하는 방식을 적용하였다. 이러한 중량계측 기반 유량 측정에서는 유체의 특성에 의해 발생하는 힘들에 의해 측정 오차가 발생할 수 있다. 그 중 주요인은 Fig. 4와 같이 크게 부력(Buoyancy Force), 모세관 힘(Capillary Force), 그리고 동유체력(Hydrodynamic Force)을 들 수 있다[11,17]. 노즐이 유체에 잠김 부분만큼 발생하는 부력에 의해 발생하는 질량 mb은 식(4)와 같다.
(4) |
이 때 L은 노즐의 잠긴 깊이이며, Do와 Di는 노즐의 외경과 내경이다. 함침된 노즐 내부의 유체의 경우 대기압 수준 이하의 압력이기 때문에 이때의 질량 mbL 또한 식(5)와 같이 영향을 미친다.
(5) |
모세관 힘에 의해 발생하는 질량 mc은 노즐의 외경, 유체의 표면장력 γ (N/m), 그리고 노즐과 유체사이의 접촉각 θ (o)과 관계가 있으며, 이는 식(6)과 같다.
(6) |
마지막으로 동유체력에 의해 발생하는 질량 md은 유체의 질량유량 과 충격속도 ui의 곱과 같으며 식(7)과 같다.
(7) |
충격속도 ui는 베르누이의 법칙에 따라서 식(8)과 같이 표현된다.
(8) |
un은 초기 속도이며, hi는 충격 높이이다. 앞서 설명한 세 가지 요인들에 의해 발생되는 오차 Δml은 다음과 같다.
(9) |
부력에 의한 질량과 동유체력에 의한 질량은 측정 질량 값을 증가시키고, 모세관 현상에 의한 질량은 반대로 이를 감소시키며, 이 오차는 식(1)에서 측정되는 질량에 반영된다.
그러나 유량은 시간에 따른 질량 변화이다. 유량에 비해 큰 저수통으로 인하여 높이의 변화도 크지 않고 균일한 노즐 표면 및 형상으로 인하여 유체의 표면 장력과 접촉각은 크게 변동되지 않을 거라 판단된다. 따라서 모세관 힘에 의한 질량은 유량에 큰 영향을 미치지 않을 것이다. 또한 부력에 의한 질량의 경우 높이 L의 변화에 따라서 유량 값에 영향을 줄 수 있지만 수 μL/sec의 유량 수준에서는 유의미한 변화가 없다. 하지만 유체의 속도에 의한 동유체력은 수식에 의해 보정되거나 이를 줄일 수 있는 방법이 필요하다.
Fig. 5에 도시한 것처럼 유체를 빈 웨잉팬에 Drop하는 방법은 동유체력에 의해 초기 유량이 과도하게 측정되는 경향이 있다. 반면에 유체 내부로 토출하는 방식은 이러한 과도한 응답이 제거되었으며 이는 토출되는 유체가 담긴 유체 내부로 확산되면서 충격 속도 ui가 느려지기 때문으로 생각된다.
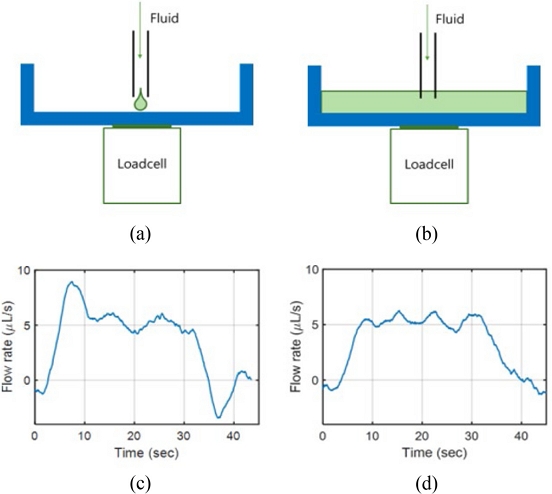
Nozzle setup for (a) Fluid drop (b) Immersed discharge, the measured flow rate in case of (c) Fluid drop, and (d) Immersed discharge
다음으로 충분한 글리세롤 유체를 웨잉팬에 담아둔 상태에서 노즐과 웨잉팬 바닥 사이의 간격을 0.2, 0.4, 0.6 mm로 변경하면서 유량을 측정하였다. 측정은 10회 반복 측정을 하였으며, 유량이 안정화되고 10초 데이터의 각각 평균의 표준편차를 이용하여 비교하였다. 그 결과 Fig. 6과 같이 노즐과 웨잉팬의 거리가 멀수록 표준편차는 감소하였다. 이는 앞의 Fig. 5의 설명과 마찬가지로 유체가 토출될 때 노즐의 끝과 웨잉팬의 거리가 멀어질수록 중력 방향으로의 유속이 느려지기 때문에 좀 더 안정적인 측정이 가능한 것으로 보인다. 최종적으로 노즐과 웨잉팬의 바닥과의 간격은 0.6 mm 이상으로 설정하였다.
2.3 선형성 평가
우선 점도에 따라 시스템의 선형성에 대한 실험을 진행하였다. 5에서 50 μL/s까지 유체의 유량을 5 μL/s 간격으로 측정하였으며 물과 저점도 유체인 글리세롤과 고점도 유체인 실리콘 레진을 각 유량마다 5회씩 실험하였다. 세 유체의 특성은 Table 1과 같다. 측정 데이터는 안정화된 후 10초의 데이터를 평균하고 1차 선형 피팅을 통해 기울기 값을 산출하였다. Fig. 7에 도시된 바와 같이 물을 통해 유량계의 선형성 평가한 결과 측정 기울기는 0.9051이며 결정계수 R2는 0.9997로 매우 선형적인 결과가 나타났다. 글리세롤과 실리콘 레진도 비슷하게 높은 선형성을 보였다. 다만 점도가 높아질수록 유량의 불확도로 인해 결정계수가 낮아진다. 펌프 지시 유량과는 약 10%의 오차를 보이는데, 시린지의 단면 크기에 대한 오차와 시린지 펌프의 불확도로 인해 발생한 오차로 볼 수 있다.
3. 유체 및 펌프 특성 평가 및 유량 제어
3.1 점도에 따른 유량의 동적 특성
Fig. 8은 펌프 유량 50 μL/s로 총 5회 토출하여 유량을 시간에 따라 도시한 그래프이다. 각 유체의 평균 유량, 유량 반복도(Repeatability) 및 안정화 시간은 Table 2에 나타내었다. 5초부터 35초까지 30초간 펌프를 동작하였을 때, 각 유체의 평균 유량은 앞서 2.3절에서 살펴본 바와 같이 비슷한 수준으로 측정되었다. 다만 점도가 증가할수록 각 측정 간 유량의 반복도는 증가하였으며, 물과 실리콘 레진의 유량 반복도는 약 8배 이상 차이가 났다. 그 이유는 유체 토출 시 유체 점도가 커질수록 시린지 모터에 가해지는 부하가 증가하여 모터의 운동 성능에 미약한 변동이 생기기 때문으로 생각된다. 또한 점도가 증가하면 유연한 튜브의 내벽에 가해지는 압력도 증가하므로, 이에 따라 튜브의 팽창으로 인한 유량 변동도 원인이 될 수 있다. 마지막으로 점도가 증가할수록 유동의 저항이 커져 유량이 안정화되기까지의 시간이 증가함을 알 수 있다.
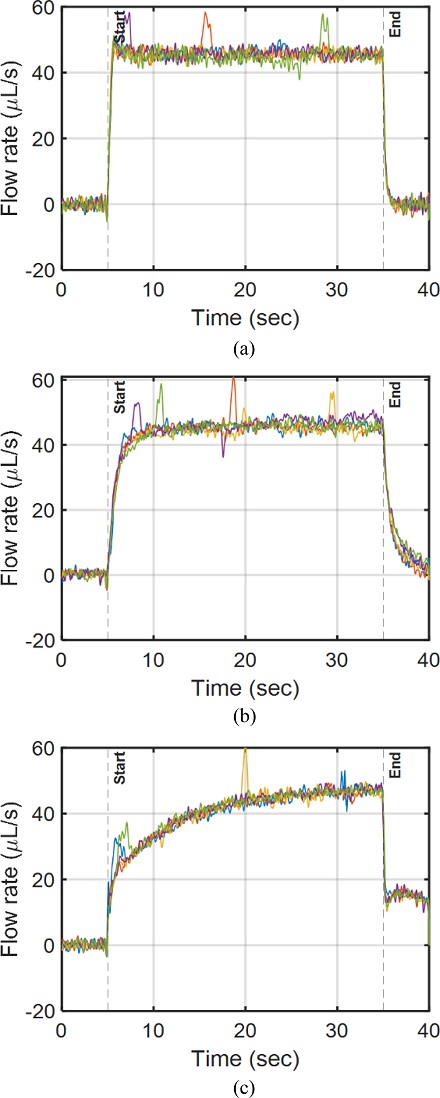
Measured flow rates of (a) Water, (b) Glycerol, and (c) Silicone resin in case of 50 μL/s pump command
3.2 펌프 유량 변동에 따른 토출 유량
코팅 시 펌프로부터 반복적인 유량의 변동이 발생할 경우를 모사하기 위하여 글리세롤에 대해 평균 유량 50 μL/s을 기준으로 최대 70, 최소 30 μL/s으로 주파수 0.25 Hz의 유량 변동을 주었다. Fig. 9에 측정결과를 도시하였다. 글리세롤의 경우, 앞 절에서 살펴본 바와 같이 유체 점도에 의해 수 초의 응답시간을 가지지만 펌프 유량의 변동과 일치하여 측정됨을 관측할 수 있었다.
3.3 균일 토출을 위한 유량의 앞먹임 제어
앞선 실험 결과처럼 점도가 높은 액체를 토출할 때 긴 안정화 시간으로 인하여 코팅 초반부의 코팅 균일도 확보가 어렵게 된다. 따라서 이 절에서는 유량 측정 시스템을 이용하여 고점도 유체 토출 시 과도응답 구간을 줄이고 안정화 시간을 앞당기는 것을 목적으로 유량 명령을 제어하는 방법을 검토한다. 실험에 앞서 시린지 펌프 및 실리콘 레신 유체 토출을 간단히 1차 시스템으로 모델링 하였다. Fig. 8(c)에서 실리콘 레진의 응답은 시정수 약 3.3초를 가진다. Fig. 10(a)에서와 같이 모델은 실제 응답과 비슷한 안정화 시간을 가짐을 알 수 있다. 이를 바탕으로 시정수의 2배인 7초간의 펌프 명령을 단계적으로 변화시키면서 안정화 시간이 최소화되는 앞먹임 명령값을 Trial and Error로 찾았으며 그 결과는 Fig. 10(b)에 도시하였다.
최종적으로 앞먹임 제어를 하지 않았을 때 안정화 시간보다 앞먹임 제어 시 안정화 시간은 7.8초로 기존 스텝 명령 대비 56.4% 개선할 수 있었으며, 점도가 약 5배 낮은 글리세롤과 비슷한 안정화 시간을 가졌다.
더불어 Fig. 10(a)를 보면 토출 종료 시 유체의 관성으로 인해 펌프 명령 종료 후에 잔여 토출 유량이 발생하게 된다. 이를 개선하기 위해 토출 종료 시 시린지 펌프의 흡입을 통해 잔여 토출 유량을 최소화하도록 하였으며 Fig. 10(b)와 같이 0에 가까운 유량을 가지도록 할 수 있었다.
4. 결론
본 논문에서는 코팅 노즐의 출구에서 유량을 측정하기 위해 중량계측법을 이용하였다. 실험실에서 제작된 유량 측정 시스템을 통해 점도와 상관없이 5-50 μL/s까지 측정 구간에서도 매우 선형적인 측정이 가능하였다. 최종적으로 유량을 앞먹임 제어함으로서 고점도 유체와 시린지 펌프에서 안정화 시간을 약 56% 감소시켰으며 종료 시 잔여 토출 유량을 최소화시켰다. 이는 코팅 시 코팅 초기 과도 응답 부분과 코팅 종료 시 원하는 유량 토출을 통해 품질 향상을 기대할 수 있다.
본 논문에서는 수 μL/s 수준의 유량일 경우 부력과 모세관 힘에 의한 영향이 무시할 만한 수준이라 가정하였지만, 실제로는 수위 상승에 따라 유량에 영향을 줄 수 있으므로 이는 추후 정량적으로 분석되어야 할 필요가 있다. 또한 본 유량 측정시스템은 펌프와 노즐 자체가 코팅 방향으로 균일도에 영향을 어떻게 주는 지만 평가할 수 있으며 실제 코팅 시 기판과 유체의 상호작용에 의한 영향은 예측 또는 평가하기 어렵다.
추후 연구에서는 Fig. 11과 같이 상용 정밀 저울과 토출부가 높은 종횡비를 가진 슬롯 다이 노즐이 장착된 유량 측정 시스템을 개발하고 이를 평가할 계획이다. 또한 보다 정밀한 펌프를 사용하여 모터 운동 성능 변동에 의한 영향을 최소화하고자 한다.
NOMENCLATURE
D : | Outer Diameter of the Nozzle |
Di : | Inner Diameter of the Nozzle |
Fg : | Gravitational Force of the Weighing Object |
g : | Gravitational Acceleration |
hi : | Impact Height |
I : | Current Applied to Voice Coil Motor |
Kf : | Force Constant of the Voice Coil Motor |
L : | Insertion Depth of the Nozzle |
ml : | Fluid Mass |
mb : | Mass from the Buoyancy Effect |
mbL : | Liquid Mass inside the Nozzle below the Atmospheric Pressure Level |
mc : | Mass from the Capillary Force Effect |
md : | Mass from the Hydrodynamic Force Effect |
: | Mass Flow Rate |
Ql : | Volume Flow Rate |
t : | Measured Time |
Vl : | Volume of the Fluid |
γ : | Surface Tension |
θ : | Contact Angle between the Fluid and the Nozzle |
ρ : | Density of the Fluid |
ui : | Normal Impact Velocity of the Fluid |
un : | Initial Velocity of the Falling Fluid |
Δml : | Measurement Error of the Fluid Mass |
Acknowledgments
This work was supported by the Technology Innovation Program (No. 20014812), funded by the Ministry of Trade, Industry & Energy (MOTIE, Republic of Korea).
REFERENCES
- Beguin, A. E., (1951), Method of coating strip material, US2681294A.
-
Larsen-Olsen, T. T., Andreasen, B., Andersen, T. R., Böttiger, A. P., Bundgaard, E., Norrman, K., Andreasen, J. W., Jørgensen, M., Krebs, F. C., (2012), Simultaneous multilayer formation of the polymer solar cell stack using roll-to-roll double slot-die coating from water, Solar Energy Materials and Solar Cells, 97, 22-27.
[https://doi.org/10.1016/j.solmat.2011.08.026]
-
Schmitt, M., Scharfer, P., Schabel, W., (2014), Slot die coating of lithium-ion battery electrodes: Investigations on edge effect issues for stripe and pattern coatings, Journal of Coatings Technology and Research, 11(1), 57-63.
[https://doi.org/10.1007/s11998-013-9498-y]
-
Sandström, A., Dam, H. F., Krebs, F. C., Edman, L., (2012), Ambient fabrication of flexible and large-area organic light-emitting devices using slot-die coating, Nature Communications, 3(1), 1-5.
[https://doi.org/10.1038/ncomms2002]
-
Schmitt, M., Diehm, R., Scharfer, P., Schabel, W., (2015), An experimental and analytical study on intermittent slot die coating of viscoelastic battery slurries, Journal of Coatings Technology and Research, 12(5), 927-938.
[https://doi.org/10.1007/s11998-015-9717-9]
-
Tan, P., Diao, S., Huang, T., Yang, Z., Zhou, H., Zhang, Y., (2020), Mechanism and control of the trailing edge in intermittent slot die coating, Industrial & Engineering Chemistry Research, 59(35), 15758-15767.
[https://doi.org/10.1021/acs.iecr.0c02743]
-
Ding, X., Liu, J., Harris, T. A., (2016), A review of the operating limits in slot die coating processes, AIChE Journal, 62(7), 2508-2524.
[https://doi.org/10.1002/aic.15268]
-
Meng, K., Wang, X., Chen, Q., (2011), Fluid flow in coat-hanger die of melt blowing process: Comparison of numerical simulations and experimental measurements, Textile Research Journal, 81(16), 1686-1693.
[https://doi.org/10.1177/0040517511402130]
-
Park, J., Shin, K., Lee, C., (2015), Improvement of cross-machine directional thickness deviation for uniform pressure-sensitive adhesive layer in roll-to-roll slot-die coating process, International Journal of Precision Engineering and Manufacturing, 16(5), 937-943.
[https://doi.org/10.1007/s12541-015-0122-1]
-
Bissig, H., Petter, H. T., Lucas, P., Batista, E., Filipe, E., Almeida, N., Ribeiro, L. F., Gala, J., Martins, R., Savanier, B., (2015), Primary standards for measuring flow rates from 100 nl/min to 1 ml/min–gravimetric principle, Biomedical Engineering/Biomedizinische Technik, 60(4), 301-316.
[https://doi.org/10.1515/bmt-2014-0145]
-
Doihara, R., Shimada, T., Cheong, K.-H., Terao, Y., (2016), Liquid low-flow calibration rig using syringe pump and weighing tank system, Flow Measurement and Instrumentation, 50, 90-101.
[https://doi.org/10.1016/j.flowmeasinst.2016.06.014]
-
Doihara, R., Shimada, T., Cheong, K.-H., Furuichi, N., (2021), Weighing system with low evaporation error for liquid microflow down to 1 mg/min, Flow Measurement and Instrumentation, 81, 102030.
[https://doi.org/10.1016/j.flowmeasinst.2021.102030]
-
Lee, S. H., Kang, W., Chun, S., (2018), Dynamic behavior analysis of drug delivery devices using a dynamic gravimetric method, Flow Measurement and Instrumentation, 62, 105-112.
[https://doi.org/10.1016/j.flowmeasinst.2018.03.009]
-
Gläser, M., Borys, M., (2009), Precision mass measurements, Reports on Progress in Physics, 72(12), 126101.
[https://doi.org/10.1088/0034-4885/72/12/126101]
-
Marangoni, R. R., Rahneberg, I., Hilbrunner, F., Theska, R., Fröhlich, T., (2017), Analysis of weighing cells based on the principle of electromagnetic force compensation, Measurement Science and Technology, 28(7), 075101.
[https://doi.org/10.1088/1361-6501/aa6bcd]
-
Bae, J. H., Yoon, K. T., Lim, H. H., Choi, Y. M., (2021), Development of an optical position sensor for high-precision electromagnetic force compensation balance, Journal of the Korean Society for Precision Engineering, 38(8), 567-574.
[https://doi.org/10.7736/JKSPE.021.031]
- Aguilera, J., (2011), Dynamic weighing calibration method for liquid flowmeters-A new approach, Universitätsbibliothek Ilmenau.
Ph.D. Student in the Department of Mechanical Engineering, Ajou University. His research interest is novel instrumentation systems, actuator design, and biomechanical wearable devices.
E-mail: majesty17@ajou.ac.kr
M.S. in the Department of Mechanical Engineering, Ajou University. His research interest is high-precision machines and optical sensors.
E-mail: dmcj421@ajou.ac.kr
Associate Professor in the Department of Mechanical Engineering, Ajou University. His research interest is high-precision machines, mass metrology and wearable mechatronics.
E-mail: ymanchoi@ajou.ac.kr